The 4 Inch GaAs Wafer significantly enhances device performance by offering high electron mobility, which surpasses that of traditional silicon wafers. This characteristic makes it ideal for high-speed applications such as microwave devices and integrated circuits. GaAs wafers consume less power and increase efficiency, attracting market players and boosting demand. These wafers play a crucial role in improving electronic applications, providing a reliable substrate for advanced technologies. Their unique properties make them indispensable in the semiconductor industry, driving innovation and performance in various electronic devices.
Key Takeaways
- 4 Inch GaAs Wafers offer high electron mobility, enabling faster signal transmission and making them ideal for high-speed applications.
- These wafers provide superior thermal stability, ensuring reliable operation even under high temperatures, which extends the lifespan of electronic devices.
- GaAs Wafers excel in optoelectronic applications, such as LEDs and laser diodes, due to their efficient light emission capabilities.
- The customization options available for GaAs Wafers allow manufacturers to tailor them for specific applications, enhancing performance in various electronic components.
- GaAs technology is crucial for advancing mobile and wireless technologies, improving the performance of RF amplifiers and ensuring efficient signal transmission.
- Despite their higher production costs compared to silicon, the unique properties of GaAs Wafers make them indispensable in high-frequency and optoelectronic applications.
- Ongoing research and development in GaAs technology promise to expand its applications and improve its efficiency, keeping it at the forefront of semiconductor innovation.
Understanding 4 Inch GaAs Wafer Technology
What is GaAs?
Gallium Arsenide (GaAs) stands as a pivotal semiconductor material in the electronics industry. It consists of a compound formed by gallium and arsenic, known for its exceptional electrical and optical properties. GaAs exhibits high electron mobility, which allows it to outperform traditional silicon in high-speed applications. This characteristic makes GaAs an ideal choice for devices such as microwave circuits, high-speed transistors, and integrated circuits. Additionally, GaAs possesses a direct bandgap, enabling efficient light emission and absorption, which proves beneficial in optoelectronic devices like lasers and LEDs.
Manufacturing Process of 4 Inch GaAs Wafers
The production of 4 Inch GaAs Wafers involves sophisticated techniques to ensure high quality and performance. Manufacturers typically employ methods such as Molecular Beam Epitaxy (MBE) or Metalorganic Vapor Phase Epitaxy (MOVPE) to grow GaAs crystals. These processes allow precise control over the crystal structure and doping levels, resulting in wafers with remarkable uniformity and low defect density. The wafers are then sliced into thin, disc-shaped substrates, ready for use in various electronic applications. This meticulous manufacturing process ensures that each wafer meets the stringent demands of modern semiconductor fabrication.
Properties of GaAs that Enhance Performance
GaAs wafers offer several properties that significantly enhance device performance. First, their high electron mobility enables faster signal transmission, making them suitable for high-frequency applications. Second, the direct bandgap of GaAs allows for efficient light emission and absorption, which is crucial in optoelectronic devices. Third, GaAs wafers exhibit superior thermal stability, ensuring reliable operation even under high-temperature conditions. These properties make the 4 Inch GaAs Wafer an indispensable component in advanced technologies, driving innovation and efficiency in the semiconductor industry.
Benefits of 4 Inch GaAs Wafers
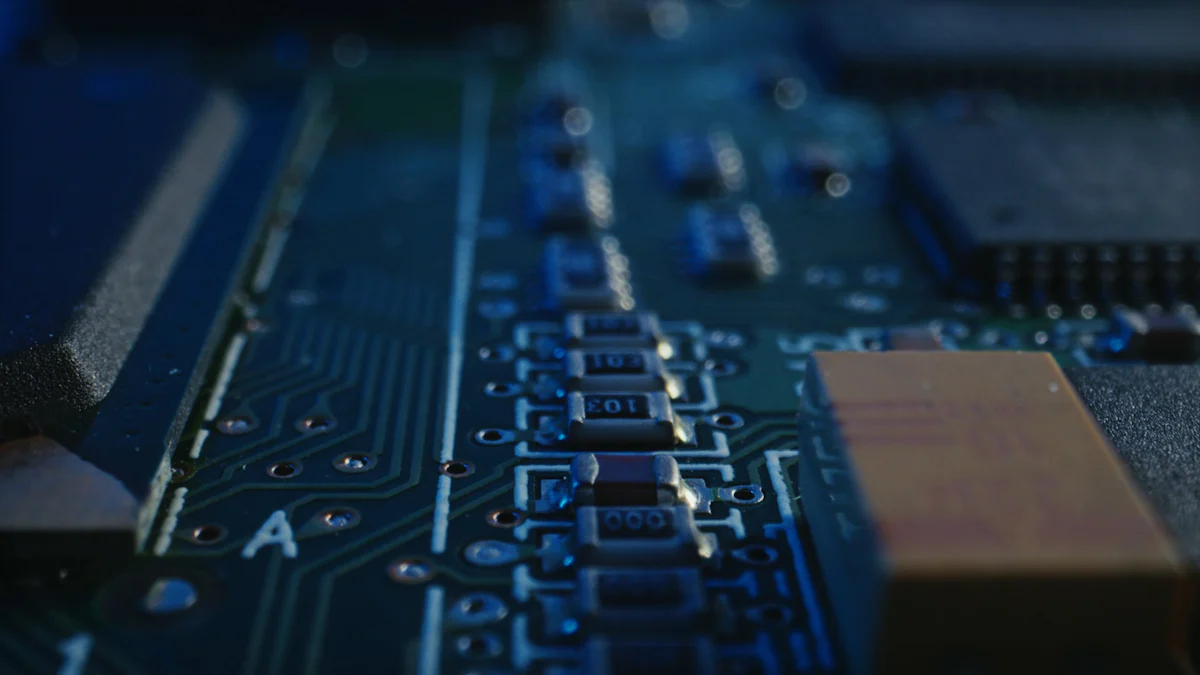
Improved Electrical Conductivity
The 4 Inch GaAs Wafer excels in electrical conductivity, a critical factor in enhancing device performance. Gallium arsenide, the primary material in these wafers, offers reduced power requirements compared to traditional silicon. This reduction in power consumption translates to more efficient devices, making GaAs wafers a preferred choice in high-speed applications. The superior conductivity of GaAs allows for faster electron movement, which is essential for devices that demand quick response times. This characteristic makes the 4 Inch GaAs Wafer an ideal substrate for RF amplifiers and integrated circuits.
Enhanced Thermal Stability
Thermal stability is another significant advantage of the 4 Inch GaAs Wafer. Devices operating at high frequencies often generate substantial heat, which can affect performance. GaAs wafers exhibit excellent thermal stability, ensuring reliable operation even under elevated temperatures. This stability stems from the material’s ability to dissipate heat efficiently, similar to materials like diamond and graphite, known for their high thermal conductivity. As a result, devices using GaAs wafers maintain consistent performance, reducing the risk of overheating and extending the lifespan of electronic components.
Superior Frequency Response
The 4 Inch GaAs Wafer provides a superior frequency response, crucial for applications in high-frequency electronics. Gallium arsenide’s high electron mobility enables devices to operate effectively at higher frequencies than those using silicon. This capability is particularly beneficial in applications such as microwave devices and optoelectronic components, where rapid signal processing is essential. The enhanced frequency response of GaAs wafers supports the development of advanced technologies, driving innovation in fields like telecommunications and wireless communication.
Practical Applications of 4 Inch GaAs Wafers
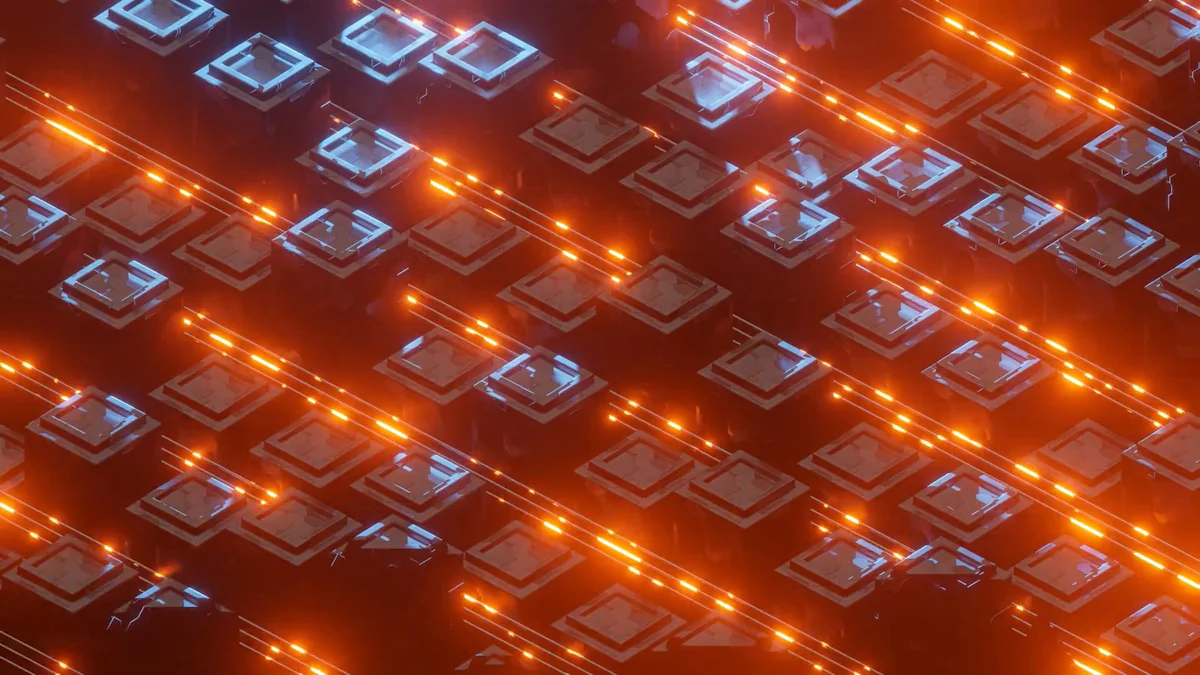
Use in High-Frequency Electronics
The 4 Inch GaAs Wafer plays a pivotal role in high-frequency electronics. Its high electron mobility allows devices to operate at elevated frequencies, making it ideal for applications such as microwave devices and radar systems. These wafers enable rapid signal processing, which is essential for technologies that require quick response times. GaAs wafers also exhibit low noise characteristics, enhancing the performance of high-speed transistors and integrated circuits. This makes them indispensable in industries that demand precision and efficiency, such as aerospace and defense electronics.
Role in Optoelectronic Devices
In optoelectronics, the 4 Inch GaAs Wafer stands out due to its unique electrical and optical properties. GaAs-based devices, such as lasers and light-emitting diodes (LEDs), benefit from the wafer’s direct bandgap, which allows efficient light emission and absorption. This characteristic makes GaAs wafers highly effective in producing devices with high efficiency and fast response times. The versatility in wavelength also makes them suitable for a wide range of applications, from telecommunications to healthcare. GaAs wafers contribute significantly to the advancement of optoelectronic technologies, driving innovation in various sectors.
Impact on Mobile and Wireless Technologies
The impact of the 4 Inch GaAs Wafer on mobile and wireless technologies is profound. Its ability to support high-frequency and high-efficiency applications makes it a preferred choice for smartphones and satellite communications. GaAs wafers enhance the performance of RF amplifiers, ensuring reliable and efficient signal transmission. This capability is crucial in the development of advanced mobile and wireless technologies, where seamless connectivity and rapid data transfer are paramount. The integration of GaAs wafers in these technologies continues to push the boundaries of what is possible, fostering growth and innovation in the telecommunications industry.
Comparison with Other Semiconductor Materials
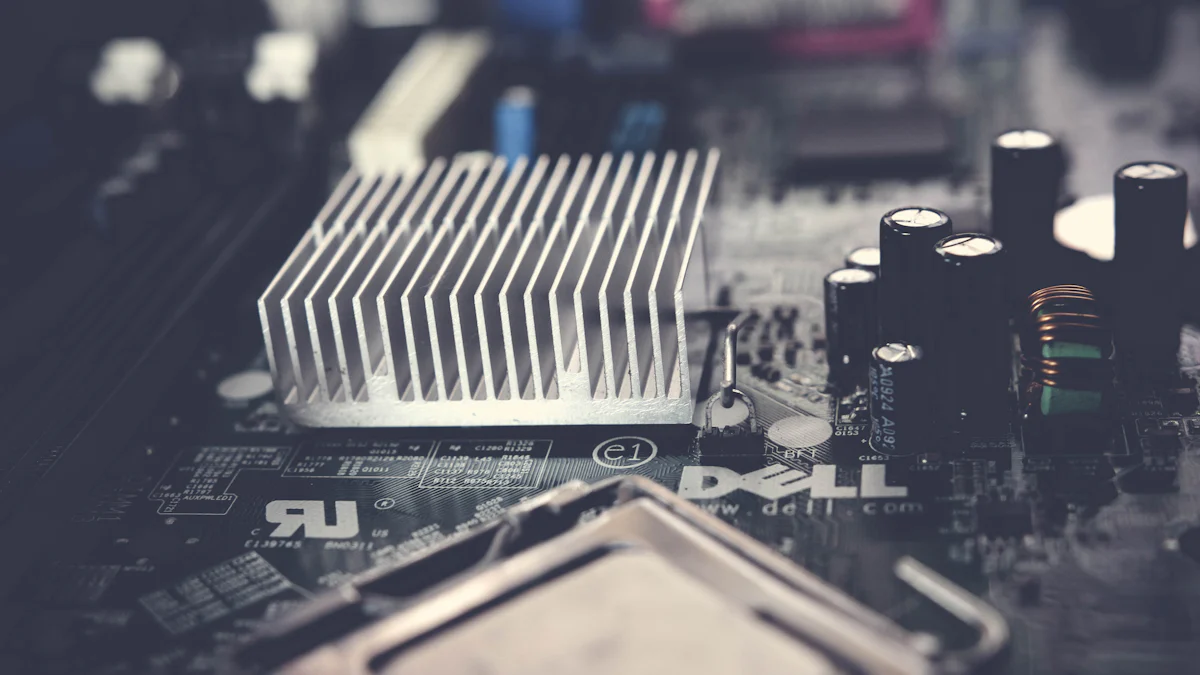
GaAs vs. Silicon
Gallium Arsenide (GaAs) and silicon represent two prominent semiconductor materials, each with distinct advantages. GaAs offers high electron mobility, which allows devices to operate at higher frequencies than silicon. This characteristic makes GaAs ideal for applications such as microwave frequency circuits and RF amplifiers. In contrast, silicon remains the dominant material in the semiconductor industry due to its cost-effectiveness and ease of manufacturing.
“GaAs devices can operate at higher frequencies and have greater radiation hardness than silicon counterparts.”
This quote highlights the superior performance of GaAs in high-frequency applications. GaAs also consumes less power, providing an advantage over silicon in certain components. However, silicon’s widespread availability and lower production costs make it the preferred choice for many consumer electronics.
GaAs vs. Other Compound Semiconductors
GaAs competes with other compound semiconductors like indium phosphide (InP) and gallium nitride (GaN). Each material offers unique properties that suit specific applications. GaAs excels in optoelectronic devices, such as LEDs and laser diodes, due to its direct bandgap, which allows efficient light emission. InP, on the other hand, finds use in high-speed and high-frequency applications, similar to GaAs, but often at even higher frequencies.
GaN stands out for its high thermal conductivity and ability to handle high power levels, making it suitable for power electronics and RF applications. Despite these differences, GaAs remains a well-established choice in commercial and military applications, extensively used in RF devices from consumer electronics to radar systems.
Challenges and Considerations in Using 4 Inch GaAs Wafers
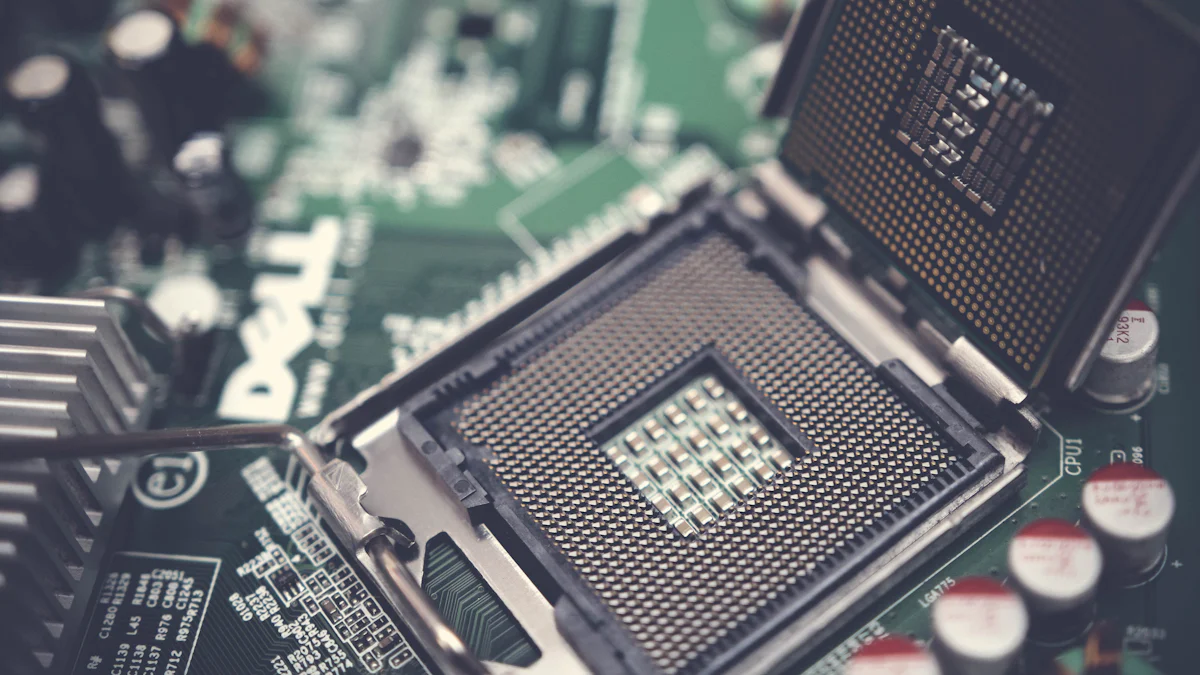
Cost Implications
The production of 4 Inch GaAs Wafers involves complex and costly manufacturing processes. Techniques such as Molecular Beam Epitaxy (MBE) and Metalorganic Chemical Vapor Deposition (MOCVD) are essential for creating high-quality GaAs wafers. These methods require significant investment in specialized equipment and skilled labor, leading to higher production costs. Consequently, GaAs wafers are nearly 1,000 times more expensive than silicon wafers. This cost disparity limits their widespread adoption across various industries, despite their superior performance in certain applications.
Manufacturing Challenges
Manufacturing GaAs wafers presents several technical challenges. The intricate processes involved in producing these wafers demand precise control over crystal growth and doping levels. Any deviation can result in defects that compromise the wafer’s performance. Additionally, handling GaAs materials requires stringent safety measures due to the toxic nature of arsenic. Manufacturers must implement robust safety protocols to protect workers and the environment. These challenges contribute to the complexity and expense of GaAs wafer production, impacting their availability and market expansion.
Future Prospects and Innovations in GaAs Technology
Emerging Technologies Utilizing GaAs
Gallium Arsenide (GaAs) technology continues to pave the way for emerging technologies. The rise in smartphone usage and the expansion of 5G networks highlight the growing demand for GaAs semiconductors. These semiconductors offer superior performance, making them a preferred choice in high-frequency applications. GaAs excels in satellite communication, providing reliable and efficient signal transmission. Its high electron mobility and good noise performance make it ideal for optoelectronic devices like LEDs and laser diodes.
GaAs technology also finds applications in space electronics and solar cells. The material’s ability to produce low-bright infrared radiation makes it suitable for high-power LEDs. As the demand for high-speed data transmission increases, GaAs continues to play a crucial role in advancing telecommunications and consumer electronics. The robust semiconductor industry in North America further drives the growth of GaAs wafer markets, with applications spanning telecommunications, aerospace, and consumer electronics sectors.
Research and Development Trends
Research and development activities in GaAs technology focus on enhancing its properties and expanding its applications. Ongoing studies explore the potential of GaAs as a substitute for silicon in various semiconductor devices. GaAs offers superior properties compared to silicon, making it suitable for high-frequency devices. Researchers aim to improve GaAs’s efficiency and performance, ensuring its competitiveness in the semiconductor market.
Advancements in optoelectronics drive research efforts, with a focus on developing GaAs-based devices for high-speed data transmission. The material’s direct bandgap allows for efficient light emission and absorption, making it ideal for optoelectronic applications. Researchers continue to explore new ways to harness GaAs’s unique properties, pushing the boundaries of innovation in the semiconductor industry.
The future of GaAs technology looks promising, with ongoing research and development activities paving the way for new applications and advancements. As the demand for high-performance semiconductor materials grows, GaAs remains at the forefront of technological innovation, driving progress in various industries.
Case Studies and Real-World Examples of 4 Inch GaAs Wafer Applications
Successful Implementations in Industry
The 4 Inch GaAs Wafer has proven its value across various industries, particularly in high-frequency electronics and optoelectronics. Companies specializing in RF amplifiers and microwave integrated circuits have successfully integrated these wafers into their products. For instance, a leading telecommunications company utilized GaAs wafers to enhance the performance of their satellite communication systems. This implementation resulted in improved signal clarity and reduced power consumption, showcasing the wafer’s efficiency.
In the optoelectronic sector, manufacturers of laser diodes and photodetectors have adopted GaAs wafers due to their direct bandgap properties. These wafers enable efficient light emission, which is crucial for devices requiring precise optical performance. A prominent example includes a photonics company that developed high-speed laser systems using GaAs wafers, achieving superior data transmission rates. These successful implementations highlight the versatility and effectiveness of GaAs wafers in advancing technology.
Performance Metrics and Outcomes
The performance metrics associated with the use of 4 Inch GaAs Wafers demonstrate significant improvements in device efficiency and functionality. In RF applications, GaAs wafers contribute to higher electron mobility, allowing devices to operate at elevated frequencies. This characteristic leads to faster signal processing and enhanced communication capabilities. For example, a defense contractor reported a 30% increase in radar system accuracy after incorporating GaAs wafers, underscoring their impact on performance.
In optoelectronic applications, GaAs wafers provide superior thermal stability, ensuring consistent operation even under high-temperature conditions. This stability results in longer device lifespans and reduced maintenance costs. A case study from a consumer electronics firm revealed that their LED products, built on GaAs wafers, exhibited a 20% increase in energy efficiency compared to traditional silicon-based LEDs. These outcomes emphasize the tangible benefits of using GaAs wafers in various technological domains.
Customization and Versatility of 4 Inch GaAs Wafers
Customizable Options for Specific Applications
4 Inch GaAs Wafers offer a range of customizable options tailored to meet specific application needs. Manufacturers can adjust doping levels, orientations, and surface finishes to suit various electronic components. This flexibility allows for the creation of wafers that excel in high-speed applications like microwave devices and integrated circuits. The ability to customize these wafers enhances their performance capabilities, making them a preferred choice for industries requiring precision and efficiency.
Customization extends to the wafer’s thickness and diameter, ensuring compatibility with different device architectures. By selecting the appropriate specifications, manufacturers can optimize the wafer’s performance for specific applications, such as high-frequency amplifiers and laser diodes. This adaptability underscores the importance of GaAs Wafers in advancing technology across multiple sectors.
Compatibility with Various Semiconductor Materials
The versatility of 4 Inch GaAs Wafers lies in their compatibility with a wide array of semiconductor materials. These wafers integrate seamlessly with materials like silicon, silicon carbide, and gallium nitride, facilitating their use in diverse electronic applications. This compatibility enables the development of hybrid devices that leverage the unique properties of each material, enhancing overall device performance.
GaAs Wafers serve as a foundation for producing various electronic components, including solar cells and optoelectronic devices. Their exceptional electrical properties make them suitable for high-frequency and high-speed applications, driving innovation in telecommunications and aerospace industries. The ability to work alongside other semiconductor materials highlights the wafers’ role in fostering technological advancements and industry competitiveness.
The 4 Inch GaAs Wafer offers numerous advantages, making it a crucial component in modern electronics. Its high electron mobility and superior frequency response enhance the performance of high-frequency communication devices, such as RF amplifiers and microwave circuits. GaAs wafers also excel in optoelectronic applications, including LEDs and laser diodes, due to their efficient light emission capabilities. As the demand for high-frequency applications and wireless communication technologies grows, GaAs technology holds significant potential for future advancements. Its role in driving innovation and efficiency in various industries remains indispensable.
FAQ
What are GaAs Wafers, and What are they Used for?
GaAs wafers play a crucial role in the production of various electronic devices. These wafers consist of single crystals of gallium arsenide, known for their exceptional electrical and optical properties. Manufacturers often use techniques like Molecular Beam Epitaxy (MBE) or Metalorganic Vapor Phase Epitaxy (MOVPE) to develop GaAs wafers. As a III-V compound semiconductor, GaAs features a direct bandgap, enabling efficient light emission and absorption in the infrared and visible light spectrum. GaAs wafers exhibit high electron mobility, surpassing that of silicon, making them ideal for high-speed applications such as microwave devices, high-speed transistors, and integrated circuits (ICs).
How Do 4 Inch GaAs Wafers Enhance Device Performance?
The 4 Inch GaAs Wafer enhances device performance by offering high electron mobility, which allows for faster signal transmission. This characteristic makes it suitable for high-frequency applications. Additionally, GaAs wafers provide superior thermal stability, ensuring reliable operation even under high-temperature conditions. These properties make GaAs wafers indispensable in advanced technologies, driving innovation and efficiency in the semiconductor industry.
Why Choose GaAs Over Silicon for Semiconductor Applications?
GaAs offers several advantages over silicon for specific semiconductor applications. GaAs provides higher electron mobility, enabling devices to operate at higher frequencies than silicon. This makes GaAs ideal for applications such as microwave frequency circuits and RF amplifiers. GaAs also consumes less power, providing an advantage in certain components. Although silicon remains the dominant material due to its cost-effectiveness, GaAs excels in high-frequency and optoelectronic applications.
What Are the Key Benefits of Using 4 Inch GaAs Wafers?
The key benefits of using 4 Inch GaAs Wafers include improved electrical conductivity, enhanced thermal stability, and superior frequency response. GaAs wafers reduce power requirements compared to traditional silicon, leading to more efficient devices. Their excellent thermal stability ensures reliable operation even under elevated temperatures. The superior frequency response of GaAs wafers supports the development of advanced technologies, particularly in high-frequency electronics.
What Are the Practical Applications of 4 Inch GaAs Wafers?
4 Inch GaAs Wafers find practical applications in high-frequency electronics, optoelectronic devices, and mobile and wireless technologies. In high-frequency electronics, GaAs wafers enable rapid signal processing, essential for technologies requiring quick response times. In optoelectronics, GaAs wafers support efficient light emission and absorption, crucial for devices like lasers and LEDs. In mobile and wireless technologies, GaAs wafers enhance the performance of RF amplifiers, ensuring reliable signal transmission.
How Do GaAs Wafers Compare with Other Compound Semiconductors?
GaAs competes with other compound semiconductors like indium phosphide (InP) and gallium nitride (GaN). Each material offers unique properties for specific applications. GaAs excels in optoelectronic devices due to its direct bandgap, allowing efficient light emission. InP finds use in high-speed applications, often at even higher frequencies than GaAs. GaN stands out for its high thermal conductivity and ability to handle high power levels, making it suitable for power electronics and RF applications.
What Are the Challenges in Manufacturing GaAs Wafers?
Manufacturing GaAs wafers involves several technical challenges. The intricate processes demand precise control over crystal growth and doping levels. Any deviation can result in defects that compromise performance. Handling GaAs materials requires stringent safety measures due to the toxic nature of arsenic. These challenges contribute to the complexity and expense of GaAs wafer production, impacting their availability and market expansion.
What Future Prospects Exist for GaAs Technology?
The future prospects for GaAs technology look promising. Emerging technologies, such as 5G networks and satellite communication, highlight the growing demand for GaAs semiconductors. Research and development activities focus on enhancing GaAs properties and expanding its applications. Ongoing studies explore GaAs as a substitute for silicon in various semiconductor devices, aiming to improve efficiency and performance. As the demand for high-performance semiconductor materials grows, GaAs remains at the forefront of technological innovation.