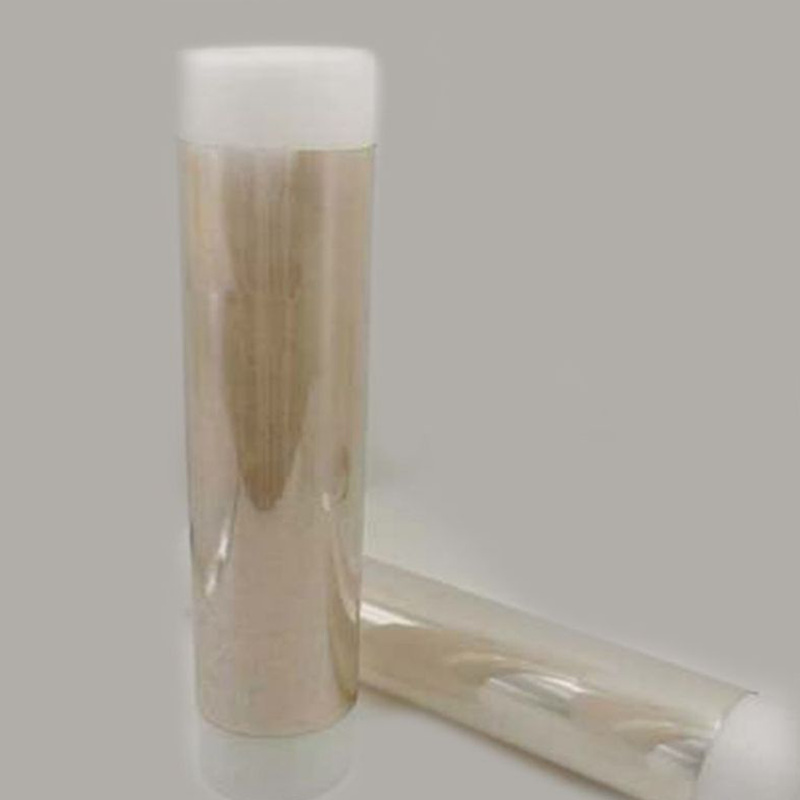
The proton exchange membrane is a critical element in fuel cell technology, acting as the central component that facilitates the efficient transformation of chemical energy into electrical energy. Integral parts of this system include the proton exchange membrane itself, the catalyst coated membrane, gas diffusion layers, and bipolar plates. Each component plays a significant role in ensuring the performance and dependability of the fuel cell. Gaining a deeper understanding of these elements is crucial for advancing clean energy innovations, particularly as the global demand for proton exchange membrane fuel cells continues to expand rapidly in the years ahead.
Key Takeaways
- The proton exchange membrane is essential for fuel cell operation, allowing protons to pass while blocking electrons, which is crucial for generating electricity.
- High-quality membranes enhance fuel cell efficiency by minimizing energy losses and resisting degradation, making ongoing research in membrane technology vital.
- Gas diffusion layers ensure even distribution of gases and manage water levels, preventing flooding and maintaining optimal performance in fuel cells.
- Bipolar plates play a dual role in guiding gas flow and conducting electricity, highlighting the importance of material choice and design in their effectiveness.
- Recent advancements in materials and designs, such as non-platinum catalysts and composite membranes, are driving down costs and improving the durability of PEM fuel cells.
- Understanding the synergy between the components of a fuel cell is key to appreciating how they work together to achieve maximum efficiency and reliability.
- As demand for clean energy solutions grows, innovations in proton exchange membrane technology will continue to play a crucial role in shaping a sustainable energy future.
Overview of the Proton Exchange Membrane
What is a Proton Exchange Membrane?
A proton exchange membrane serves as the core of a fuel cell. This thin, polymeric material acts as an electrolyte, enabling the movement of protons while blocking electrons. Positioned between the anode and cathode, it ensures that protons generated during the reaction at the anode pass through to the cathode. This selective permeability is essential for maintaining the electrochemical process that powers the fuel cell.
The membrane’s unique properties stem from its material composition. Most proton exchange membranes are made from perfluorosulfonic acid polymers, which combine high proton conductivity with chemical stability. These materials allow the membrane to perform efficiently under the demanding conditions of a fuel cell. By understanding the structure and function of this component, you can appreciate its role in advancing clean energy technologies.
Role of the Proton Exchange Membrane in Fuel Cells
The proton exchange membrane plays a pivotal role in the operation of fuel cells. It facilitates the transport of protons from the anode to the cathode, a process critical for generating electricity. At the same time, it prevents the mixing of hydrogen and oxygen gases, ensuring the reaction occurs in a controlled manner.
This membrane also supports the overall efficiency of the fuel cell. By maintaining separation between the reactants and enabling the flow of protons, it helps sustain the electrochemical reactions. Without this component, the fuel cell would fail to produce a steady and reliable flow of electricity. Its role highlights the importance of precision engineering in fuel cell design.
Importance of the Proton Exchange Membrane for Efficiency
The efficiency of a fuel cell depends heavily on the performance of the proton exchange membrane. A high-quality membrane minimizes energy losses by conducting protons effectively while resisting degradation. This ensures that the fuel cell operates at optimal levels over extended periods.
Advancements in membrane technology have further enhanced efficiency. Researchers have developed materials with improved proton conductivity and durability, addressing challenges such as chemical degradation and mechanical stress. These innovations not only boost the performance of individual fuel cells but also contribute to the broader adoption of fuel cell technology in various applications.
Understanding the importance of the proton exchange membrane allows you to see how this component drives the efficiency and reliability of fuel cells. As the demand for clean energy solutions grows, the development of advanced membranes will remain a key focus for researchers and engineers.
The Membrane and Its Function
Material Composition of the Membrane
The material composition of a proton exchange membrane determines its performance and durability. Most membranes are made from perfluorosulfonic acid (PFSA) polymers. These polymers combine high proton conductivity with excellent chemical and thermal stability. This unique combination allows the membrane to function effectively under the demanding conditions of a fuel cell.
PFSA membranes have a structure that includes a hydrophobic backbone and hydrophilic side chains. The hydrophilic regions create pathways for proton transport, while the hydrophobic backbone provides mechanical strength. This design ensures that the membrane can conduct protons efficiently while maintaining its structural integrity.
In recent years, researchers have explored alternative materials to improve membrane performance. Some of these include hydrocarbon-based polymers and composite membranes. These innovations aim to enhance conductivity, reduce costs, and increase resistance to degradation. By understanding the material composition, you can appreciate how these membranes support the operation of fuel cells in various industries.
Proton Transport Mechanism
The proton transport mechanism is the core function of a proton exchange membrane. When hydrogen gas enters the fuel cell, it splits into protons and electrons at the anode. The membrane allows only the protons to pass through to the cathode, while the electrons travel through an external circuit, generating electricity.
Proton movement occurs through a process called “hopping” or the Grotthuss mechanism. In this process, protons jump between water molecules within the membrane’s hydrophilic channels. The efficiency of this transport depends on the membrane’s hydration level. A well-hydrated membrane ensures smooth proton flow, which directly impacts the fuel cell’s performance.
Maintaining optimal hydration is critical for the membrane’s function. Too much water can flood the membrane, while too little can reduce conductivity. Advanced designs and materials aim to balance these factors, ensuring consistent and efficient proton transport.
Challenges in Membrane Durability
Durability remains one of the biggest challenges for proton exchange membranes. Over time, exposure to high temperatures, humidity, and reactive chemicals can degrade the membrane. This degradation reduces its ability to conduct protons and maintain structural integrity.
Chemical degradation often occurs due to the formation of reactive oxygen species during the fuel cell’s operation. These species attack the membrane’s polymer structure, leading to cracks and reduced performance. Mechanical stress, caused by repeated expansion and contraction during hydration cycles, also contributes to wear and tear.
To address these challenges, researchers focus on developing more robust materials. Innovations include reinforcing membranes with nanoparticles and creating hybrid structures that combine the strengths of different materials. These advancements aim to extend the lifespan of membranes, making fuel cells more reliable and cost-effective.
Understanding these challenges highlights the importance of ongoing research in membrane technology. As you explore the potential of fuel cells, recognizing the efforts to improve durability can give you a deeper appreciation for this critical component.
Catalyst Layers in Proton Exchange Membranes
Role in Electrochemical Reactions
Catalyst layers play a vital role in the electrochemical reactions within proton exchange membrane (PEM) fuel cells. These layers, located on both the anode and cathode sides of the membrane, facilitate the chemical reactions that generate electricity. At the anode, the catalyst splits hydrogen molecules into protons and electrons. The protons pass through the membrane, while the electrons travel through an external circuit, creating an electric current. On the cathode side, the catalyst enables the combination of protons, electrons, and oxygen to form water, which is the only byproduct.
Without these catalyst layers, the reactions would occur too slowly to produce usable energy. The efficiency of the fuel cell depends heavily on the performance of these layers. By accelerating the reactions, the catalyst layers ensure that the fuel cell operates effectively, providing a steady and reliable power output.
Materials Used in Catalyst Layers
The materials used in catalyst layers significantly impact their performance. Platinum and platinum alloys are the most common choices due to their excellent catalytic properties. These materials efficiently facilitate the reactions at both the anode and cathode. However, the high cost of platinum has driven researchers to explore alternative materials.
In recent years, hybrid composite materials have gained attention. For example, Nafion®-based membranes combined with other components have shown promise in improving the efficiency of catalyst layers. These composites enhance the interaction between the catalyst and the ionomer, which is essential for effective proton transport. By optimizing the composition of the catalyst layers, researchers aim to reduce costs while maintaining high performance.
The choice of materials also affects the durability of the catalyst layers. Advanced materials resist degradation, ensuring that the fuel cell remains functional over extended periods. Understanding the materials used in these layers helps you appreciate their role in advancing PEM fuel cell technology.
Innovations in Catalyst Design
Innovations in catalyst design have transformed the performance of PEM fuel cells. Researchers have focused on developing novel catalysts and optimizing the structure of the catalyst layers. For instance, studies have highlighted the importance of understanding how the structure of these layers affects fuel cell performance. By refining the arrangement of materials within the layers, engineers can improve the distribution of reactants and enhance overall efficiency.
One significant advancement involves the use of nanoparticles in catalyst layers. These tiny particles increase the surface area available for reactions, boosting the activity of the catalyst. Additionally, hybrid designs that combine different materials have shown potential in reducing costs and improving durability. For example, combining platinum with less expensive metals creates alloys that retain high catalytic activity while lowering material expenses.
The integration of molecular dynamics simulations has also contributed to progress in catalyst design. These simulations allow researchers to predict how changes in composition and structure will impact performance. By leveraging these tools, scientists can develop more efficient and cost-effective catalyst layers, paving the way for broader adoption of PEM fuel cells.
Innovations in this field demonstrate the ongoing efforts to enhance the functionality of catalyst layers. As you explore the potential of fuel cells, recognizing these advancements provides insight into how technology continues to evolve to meet the growing demand for clean energy solutions.
Gas Diffusion Layers and Their Role
Structure and Function of Gas Diffusion Layers
Gas diffusion layers (GDLs) serve as a vital component in proton exchange membrane fuel cells. These layers, positioned between the catalyst layer and the bipolar plates, perform multiple essential functions. Structurally, GDLs are typically made from porous carbon-based materials. This porous design allows them to facilitate the movement of gases, ensuring that hydrogen and oxygen reach the catalyst layers efficiently.
The GDLs also act as a conduit for electrons generated during the electrochemical reaction. By collecting and transferring these electrons to the external circuit, they contribute directly to the generation of electricity. Additionally, the porous structure aids in managing water and heat produced during the reaction, preventing flooding and overheating within the fuel cell. Without GDLs, the fuel cell would struggle to maintain consistent performance.
Importance in Gas Distribution
The distribution of gases within the fuel cell relies heavily on the gas diffusion layers. These layers ensure that hydrogen and oxygen are evenly delivered to the catalyst surfaces. Uneven gas distribution can lead to inefficiencies, reducing the overall performance of the fuel cell.
GDLs achieve this by balancing the flow of gases across the entire surface of the catalyst layer. Their porous nature allows gases to diffuse uniformly, even under varying operating conditions. This uniformity ensures that the electrochemical reactions occur consistently, maximizing the energy output of the fuel cell. By understanding the role of GDLs in gas distribution, you can appreciate how they enhance the reliability and efficiency of fuel cells.
Water Management in Gas Diffusion Layers
Water management is another critical function of gas diffusion layers. During the operation of a fuel cell, water forms as a byproduct of the reaction at the cathode. While some water is necessary to maintain the hydration of the proton exchange membrane, excess water can flood the catalyst layers and hinder gas flow.
GDLs help regulate water levels by facilitating its removal through their porous structure. They balance hydrophilic and hydrophobic properties to ensure that water is effectively evacuated without drying out the membrane. This balance is crucial for maintaining optimal proton conductivity and preventing performance degradation.
Research has highlighted the importance of capillary pressure and hydrophilic porosity in GDLs for effective water management. These characteristics enable the layers to handle water efficiently, even under high humidity or varying load conditions. By managing water effectively, GDLs contribute to the long-term stability and performance of the fuel cell.
Bipolar Plates in Proton Exchange Membranes
Role in Gas Flow and Electrical Conductivity
Bipolar plates serve as a crucial component in proton exchange membrane (PEM) fuel cells. These plates manage the flow of gases, ensuring that hydrogen and oxygen reach the respective electrodes efficiently. By guiding these gases through well-designed flow channels, bipolar plates maintain consistent reactant distribution, which is essential for the electrochemical reactions within the cell.
In addition to gas flow management, bipolar plates play a key role in electrical conductivity. They collect the electrons generated during the reaction at the anode and transfer them to the external circuit. This process enables the generation of electricity. Furthermore, the plates connect individual cells in a fuel cell stack, allowing the current to flow seamlessly between them. Without bipolar plates, the fuel cell would fail to deliver the required power output.
The dual functionality of gas flow regulation and electrical conduction highlights the importance of bipolar plates in maintaining the performance and reliability of PEM fuel cells.
Materials and Design of Bipolar Plates
The choice of materials for bipolar plates directly impacts their performance and durability. Common materials include metals, carbon-based composites, and graphite. Each material offers unique advantages. For instance, metals like stainless steel provide excellent electrical conductivity and mechanical strength. However, they require protective coatings to prevent corrosion in the fuel cell’s harsh environment.
Carbon-based composites and graphite plates are lightweight and chemically stable, making them ideal for long-term use. These materials also exhibit high thermal conductivity, which helps manage the heat generated during fuel cell operation. Despite these benefits, their brittleness can pose challenges in certain applications.
The design of bipolar plates also plays a significant role in their effectiveness. Flow channel configurations, such as serpentine, parallel, and pinhole designs, influence gas distribution and pressure drops within the cell. Advanced computational fluid dynamics (CFD) techniques have enabled engineers to optimize these designs, ensuring uniform gas flow and minimizing energy losses.
“Innovative flow field layouts, such as modified serpentine channels with bypass pathways, have been shown to alleviate pressure drops and enhance overall efficiency.”
By selecting the right materials and refining the design, you can ensure that bipolar plates meet the demanding requirements of PEM fuel cells.
Challenges in Bipolar Plate Development
Developing bipolar plates involves addressing several challenges. One major issue is achieving a balance between durability and weight. Since bipolar plates account for a significant portion of the fuel cell’s mass, lightweight materials are preferred. However, these materials must also withstand the mechanical stresses and temperature fluctuations experienced during operation.
Corrosion resistance is another critical factor. The plates operate in highly oxidative and reductive environments, which can degrade their surfaces over time. Protective coatings and advanced material treatments aim to mitigate this issue, but they can increase production costs.
Structural integrity poses additional challenges. Bipolar plates must remain leak-proof to prevent gas crossover and maintain the fuel cell’s efficiency. Vibration and thermal cycling can compromise their structural toughness, leading to potential failures.
Despite these obstacles, ongoing research continues to drive innovation. Engineers are exploring hybrid materials and novel fabrication techniques to enhance the performance of bipolar plates. By overcoming these challenges, you can contribute to the advancement of PEM fuel cell technology and its adoption in clean energy solutions.
How the Parts Work Together in a Fuel Cell
The Electrochemical Process in PEM Fuel Cells
In a proton exchange membrane (PEM) fuel cell, the electrochemical process transforms chemical energy into electrical energy. This process begins at the anode, where hydrogen gas splits into protons and electrons. The catalyst layer facilitates this reaction by lowering the energy barrier, ensuring the reaction occurs efficiently. The protons pass through the proton exchange membrane to the cathode, while the electrons travel through an external circuit, generating electricity.
At the cathode, oxygen reacts with the incoming protons and electrons to form water. This reaction, also catalyzed by the catalyst layer, completes the electrochemical cycle. The gas diffusion layers ensure that hydrogen and oxygen gases reach the catalyst layers evenly, while the bipolar plates guide the flow of gases and collect the generated electricity. Each component contributes to the seamless operation of the fuel cell, ensuring a steady power output.
“The highly random and delicate structure of catalyst layers, ranging from nanometers to micrometers, plays a critical role in enhancing reaction rates and reducing activation energy,” as highlighted in studies on PEM fuel cell performance.
Interaction Between Components
The interaction between the components of a PEM fuel cell is essential for its functionality. The proton exchange membrane acts as the central element, connecting the anode and cathode while allowing only protons to pass through. The catalyst layers on either side of the membrane accelerate the reactions, ensuring efficient energy conversion. Gas diffusion layers distribute reactants evenly across the catalyst surfaces, preventing inefficiencies caused by uneven gas flow.
Bipolar plates link individual cells in a fuel cell stack, enabling the transfer of electrons and maintaining structural integrity. Their flow field designs optimize gas distribution and minimize pressure drops, enhancing overall performance. Research has shown that optimal flow field designs in bipolar plates significantly improve fuel cell efficiency. This synergy between components ensures that the fuel cell operates reliably under varying conditions.
Importance of Component Synergy for Efficiency
The efficiency of a PEM fuel cell depends on the synergy between its components. Each part must perform its role effectively while complementing the others. For instance, the proton exchange membrane must maintain high proton conductivity without allowing gas crossover. At the same time, the catalyst layers must facilitate reactions efficiently, while the gas diffusion layers manage water and gas distribution.
When these components work together seamlessly, the fuel cell achieves maximum efficiency. Innovations in material design and structural optimization have further enhanced this synergy. For example, the integration of nanoparticles in catalyst layers increases surface area, boosting reaction rates. Similarly, advancements in bipolar plate materials and designs have improved durability and conductivity.
Understanding how these parts interact helps you appreciate the complexity and precision of PEM fuel cell technology. This synergy not only drives efficiency but also ensures the long-term reliability of the fuel cell, making it a cornerstone of clean energy solutions.
Challenges and Advancements in Proton Exchange Membrane Technology
Key Challenges in PEM Technology
Proton exchange membrane (PEM) technology faces several challenges that impact its widespread adoption. One of the most significant hurdles is the high cost of production. The reliance on platinum for catalyst layers contributes heavily to this expense. Platinum, being a rare and expensive material, increases the overall cost of PEM fuel cells, making them less accessible for commercial applications.
Durability also presents a major challenge. PEM fuel cells operate under harsh conditions, including high temperatures, humidity, and exposure to reactive chemicals. These factors can degrade the membrane and other components over time, reducing their efficiency and lifespan. For instance, reactive oxygen species formed during operation can attack the membrane’s polymer structure, leading to performance issues.
Water management within the fuel cell adds another layer of complexity. Maintaining the right balance of hydration is critical for optimal proton conductivity. Excess water can flood the system, while insufficient hydration can dry out the membrane, both of which hinder performance. Engineers must design systems that effectively manage water levels to ensure consistent operation.
Recent Advancements in Materials and Design
Recent advancements in PEM technology have addressed many of these challenges, paving the way for more efficient and cost-effective fuel cells. One notable innovation involves the development of alternative catalyst materials. Researchers have explored non-platinum catalysts, such as nickel-based alloys and carbon-supported catalysts, to reduce costs without compromising performance. These alternatives have made PEM fuel cells more affordable for broader applications.
Material improvements in membranes have also played a crucial role. New composite membranes combine perfluorosulfonic acid polymers with other materials to enhance durability and conductivity. These membranes resist chemical degradation and mechanical stress, ensuring longer operational lifespans. Additionally, hybrid designs that incorporate nanoparticles have improved proton transport efficiency, further boosting fuel cell performance.
Advances in the design of bipolar plates have contributed significantly to the technology’s evolution. Engineers have optimized flow field patterns to ensure uniform gas distribution and minimize pressure drops. For example, modified serpentine channels with bypass pathways have enhanced gas flow and reduced energy losses. These innovations demonstrate how thoughtful design can improve both efficiency and reliability.
“The late 1980s and early 1990s marked a turning point for PEM fuel cells, as pivotal innovations drove down costs and made their development more realistic.” This period laid the foundation for the advancements we see today, highlighting the importance of continuous research and development.
Future Directions for PEM Fuel Cells
The future of PEM fuel cells looks promising, with ongoing research focusing on overcoming current limitations and expanding their applications. One key area of exploration involves further reducing costs. Scientists are working to develop catalysts that use earth-abundant materials, eliminating the need for expensive platinum. These efforts aim to make PEM fuel cells more commercially viable.
Durability improvements remain a priority. Researchers are investigating advanced coatings and reinforcement techniques to protect membranes and other components from degradation. For instance, integrating nanoparticles into membranes has shown potential in enhancing both durability and conductivity. These innovations will ensure that PEM fuel cells can operate reliably over extended periods.
Expanding the range of applications is another exciting direction. PEM fuel cells are already used in transportation, portable power, and stationary energy systems. Future advancements could enable their use in more demanding environments, such as aerospace and marine industries. The versatility of PEM technology makes it a strong candidate for addressing diverse energy needs.
As you look ahead, the potential of PEM fuel cells to revolutionize clean energy solutions becomes increasingly clear. By addressing challenges and embracing advancements, this technology will continue to play a vital role in shaping a sustainable future.
Understanding the main parts of a proton exchange membrane reveals their essential roles in fuel cell operation. Each component, from the membrane to the bipolar plates, contributes to the seamless conversion of chemical energy into electricity. Their synergy ensures efficiency and reliability, making fuel cells a powerful clean energy solution.
Advancements in materials and design continue to push the boundaries of PEM technology. Researchers focus on creating cost-effective and durable components, paving the way for broader applications. As these innovations evolve, you can expect PEM fuel cells to play a transformative role in shaping a sustainable energy future.
FAQ
What are proton exchange membranes primarily used for?
Proton exchange membranes are primarily used in PEM fuel cells. These fuel cells power various applications in industries such as aerospace, automotive, and energy. You can find them in electric vehicles, backup power systems, and even military equipment due to their efficiency and reliability.
What is the essential function of a proton exchange membrane in a fuel cell?
The proton exchange membrane performs two critical tasks in a fuel cell. It separates the reactants, ensuring hydrogen and oxygen do not mix, and it transports protons from the anode to the cathode. At the same time, it blocks electrons, forcing them to travel through an external circuit to generate electricity.
What is the significance of the proton exchange membrane in PEM fuel cells?
The proton exchange membrane is the heart of PEM fuel cells. It allows only protons to pass through while blocking electrons. This selective movement creates an electric current, which powers devices, vehicles, or even homes. Without this membrane, the fuel cell would not function efficiently.
How are PEM fuel cells being engineered to improve longevity?
Engineers are developing advanced materials for proton exchange membranes to improve the durability of PEM fuel cells. These materials resist chemical degradation and withstand high temperatures and mechanical stresses. As a result, these innovations extend the lifespan of fuel cells, making them more reliable for long-term use.
Why is water management important in PEM fuel cells?
Water management is crucial because water forms as a byproduct during the fuel cell’s operation. The proton exchange membrane requires proper hydration to conduct protons effectively. However, excess water can flood the system, while insufficient water can dry out the membrane. Effective water management ensures consistent performance and prevents damage.
What materials are commonly used in proton exchange membranes?
Most proton exchange membranes are made from perfluorosulfonic acid (PFSA) polymers. These materials combine high proton conductivity with excellent chemical and thermal stability. Researchers are also exploring alternative materials, such as hydrocarbon-based polymers, to enhance performance and reduce costs.
How do gas diffusion layers support the function of proton exchange membranes?
Gas diffusion layers (GDLs) play a supportive role by distributing hydrogen and oxygen gases evenly across the catalyst layers. They also manage water levels and transfer electrons to the external circuit. This ensures that the proton exchange membrane operates efficiently under varying conditions.
What advancements have been made in catalyst layers for PEM fuel cells?
Recent advancements include the use of nanoparticles and hybrid materials in catalyst layers. These innovations increase the surface area for reactions, improving efficiency. Additionally, researchers are developing non-platinum catalysts to reduce costs while maintaining high performance.
Can PEM fuel cells be used in transportation?
Yes, PEM fuel cells are widely used in transportation. They power electric vehicles, buses, and even trains. Their ability to provide clean energy with zero emissions makes them an attractive option for the automotive industry.
What makes PEM fuel cells a sustainable energy solution?
PEM fuel cells produce electricity with water as the only byproduct. They rely on hydrogen, a renewable resource, as fuel. This makes them an environmentally friendly and sustainable energy solution for reducing carbon emissions and combating climate change.