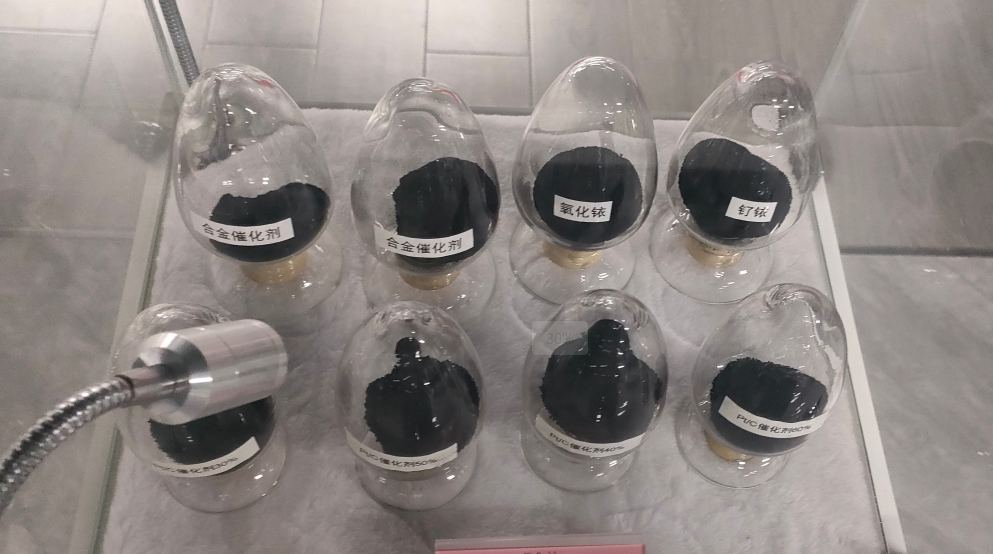
Catalyst deactivation poses a significant challenge in water electrolysis, directly impacting hydrogen production efficiency. Electrolyzer catalysts drive the reactions that split water into hydrogen and oxygen. However, these materials often degrade due to harsh operating conditions, reducing their activity over time. Understanding this vulnerability is essential for improving the durability and performance of electrolyzers.
Key Takeaways
- Catalyst deactivation in water electrolysis is primarily caused by fouling, poisoning, and thermal degradation, which can significantly reduce hydrogen production efficiency.
- Regular monitoring of electrolyte purity and maintaining stable operating conditions are crucial strategies to minimize catalyst degradation and extend its lifespan.
- Implementing advanced diagnostic techniques, such as spectroscopic and electrochemical testing, allows for early detection of catalyst degradation, enabling timely maintenance and optimization.
Mechanisms of Electrolyzer Catalyst Deactivation
Fouling and Surface Blocking
Fouling occurs when unwanted materials accumulate on the catalyst surface. These materials, often reaction byproducts or impurities, block active sites and reduce the efficiency of the electrolyzer catalyst. Surface blocking limits the interaction between the catalyst and reactants, hindering the electrochemical reactions. Over time, this buildup can become irreversible, requiring cleaning or replacement of the catalyst.
Catalyst Poisoning
Catalyst poisoning happens when specific chemical species bind strongly to active sites. These species, such as sulfur or chlorine compounds, originate from impurities in the electrolyte or feedstock. Poisoning reduces the number of available active sites, leading to a decline in catalytic activity. The severity of poisoning depends on the type of poison and the operating conditions.
Thermal Degradation
High operating temperatures can degrade the structure of the electrolyzer catalyst. Prolonged exposure to heat causes sintering, where catalyst particles agglomerate, reducing the surface area. This process diminishes the catalyst’s ability to facilitate reactions. Thermal degradation is particularly problematic in systems with poor thermal management.
Structural and Morphological Changes
Catalysts undergo structural changes during operation due to mechanical stress or chemical reactions. These changes alter the morphology of the catalyst, affecting its performance. For example, cracks or voids may form, reducing the active surface area. Such changes often result from repeated cycling or harsh operating conditions.
Site Dissolution and Metal Leaching
Site dissolution occurs when active metal components dissolve into the electrolyte. This phenomenon, often caused by corrosive environments, leads to the loss of catalytic material. Metal leaching reduces the overall activity of the electrolyzer catalyst and contaminates the electrolyte, further complicating the process.
Factors Contributing to Catalyst Deactivation
Chemical Influences (e.g., impurities, reaction byproducts)
Chemical impurities in the electrolyte or feedstock significantly impact the performance of an electrolyzer catalyst. These impurities, such as chloride ions or sulfur compounds, interact with the catalyst surface, leading to fouling or poisoning. Reaction byproducts, including oxygen radicals or metal oxides, also accumulate on the catalyst, reducing its active surface area.
Note: Even trace amounts of contaminants can accelerate catalyst degradation. Regular monitoring of electrolyte purity is essential to minimize these effects.
In addition, the chemical environment within the electrolyzer can promote unwanted side reactions. These reactions generate species that either block active sites or alter the catalyst’s chemical composition, further diminishing its efficiency.
Structural Properties of Electrolyzer Catalysts
The structural characteristics of a catalyst determine its durability and resistance to deactivation. Catalysts with high porosity and large surface areas often exhibit better initial performance. However, these features can make them more susceptible to fouling, sintering, or structural collapse under harsh conditions.
Catalyst composition also plays a critical role. Materials prone to oxidation or dissolution degrade faster, especially in corrosive environments. For example, catalysts containing non-noble metals may leach into the electrolyte, reducing their long-term stability.
Operational Conditions (e.g., temperature, current density, corrosive environments)
Operating conditions directly influence the lifespan of an electrolyzer catalyst. High temperatures accelerate thermal degradation and sintering, while excessive current densities increase mechanical stress on the catalyst. Corrosive environments, such as those with acidic or alkaline electrolytes, exacerbate metal leaching and site dissolution.
Tip: Maintaining stable operating conditions can significantly extend catalyst life. Avoiding extreme temperature fluctuations and optimizing current density are effective strategies.
Frequent cycling between operational states also contributes to structural fatigue. This cycling causes cracks or voids to form, reducing the catalyst’s active surface area and overall efficiency.
Diagnostic and Characterization Techniques
Understanding the causes of catalyst deactivation requires precise diagnostic and characterization methods. These techniques help researchers identify degradation mechanisms and evaluate the performance of electrolyzer catalysts.
Spectroscopic Methods
Spectroscopic techniques provide valuable insights into the chemical composition and surface properties of catalysts. Methods such as X-ray photoelectron spectroscopy (XPS) and Raman spectroscopy detect changes in oxidation states, chemical bonds, and surface contaminants. These tools allow researchers to monitor the interaction between the catalyst and its environment. For example, XPS can reveal the presence of impurities that contribute to fouling or poisoning.
Microscopic Analysis
Microscopic methods examine the structural and morphological changes in catalysts. Scanning electron microscopy (SEM) and transmission electron microscopy (TEM) offer high-resolution images of catalyst surfaces. These techniques identify cracks, voids, or particle agglomeration caused by thermal or mechanical stress. Atomic force microscopy (AFM) further provides three-dimensional surface profiles, enabling a detailed analysis of surface roughness and degradation patterns.
Electrochemical Testing
Electrochemical techniques evaluate the activity and stability of electrolyzer catalysts under operating conditions. Cyclic voltammetry (CV) and electrochemical impedance spectroscopy (EIS) measure key parameters such as reaction kinetics and charge transfer resistance. These methods help quantify the loss of active sites and assess the impact of fouling or poisoning on catalytic performance.
Advanced Analytical Tools for Metal Leaching Detection
Metal leaching detection requires advanced tools to measure dissolved metal ions in the electrolyte. Inductively coupled plasma mass spectrometry (ICP-MS) and atomic absorption spectroscopy (AAS) provide precise quantification of leached metals. These methods help identify the extent of site dissolution and its contribution to catalyst degradation. Combining these tools with other techniques offers a comprehensive understanding of catalyst performance.
Mitigation Strategies for Electrolyzer Catalyst Deactivation
Catalyst Material Design and Protective Coatings
Designing catalysts with enhanced durability can significantly reduce deactivation. Researchers focus on developing materials with high resistance to fouling, poisoning, and thermal degradation. For example, alloying noble metals with transition metals improves stability while maintaining catalytic activity. Protective coatings, such as thin oxide layers, shield the catalyst from corrosive environments. These coatings prevent direct contact between the catalyst and harmful species, extending its operational life.
Tip: Selecting materials with low dissolution rates ensures better performance in long-term applications.
Operational Optimization and Control
Optimizing operating conditions minimizes stress on the electrolyzer catalyst. Maintaining stable temperatures and current densities reduces the risk of thermal degradation and structural damage. Automated control systems monitor key parameters, ensuring consistent performance. These systems also detect early signs of deactivation, allowing operators to take corrective actions promptly.
Note: Avoiding extreme fluctuations in operating conditions can prevent irreversible damage to the catalyst.
Periodic Regeneration and Cleaning
Regular maintenance restores the activity of deactivated catalysts. Cleaning methods, such as chemical rinsing or ultrasonic treatment, remove fouling and surface contaminants. Regeneration techniques, including thermal or electrochemical treatments, recover lost active sites. Implementing a maintenance schedule ensures the catalyst remains efficient over extended periods.
Development of Corrosion-Resistant Catalysts
Corrosion-resistant catalysts withstand harsh environments better than conventional materials. Advances in material science have led to the creation of catalysts with improved chemical stability. For instance, incorporating non-metallic elements into the catalyst structure enhances resistance to oxidation and leaching. These innovations increase the lifespan of the electrolyzer catalyst, reducing the need for frequent replacements.
Callout: Investing in corrosion-resistant materials lowers operational costs and improves system reliability.
Electrolyzer catalyst deactivation arises from mechanisms like fouling, poisoning, and thermal degradation. Diagnostic techniques, such as spectroscopy and electrochemical testing, provide critical insights into these issues. Advancements in corrosion-resistant materials and protective coatings show promise. Future research should focus on scalable solutions to enhance catalyst durability for industrial hydrogen production.
FAQ
What is the most common cause of catalyst deactivation in water electrolysis?
Fouling and surface blocking are the most frequent causes. Impurities and reaction byproducts accumulate on the catalyst, reducing its active surface area and efficiency.
How can operators detect early signs of catalyst degradation?
Operators can use electrochemical testing, such as cyclic voltammetry, to monitor performance. These methods identify reduced activity or increased resistance, signaling potential degradation.
Are corrosion-resistant catalysts more expensive than conventional ones?
Corrosion-resistant catalysts often have higher initial costs. However, their extended lifespan and reduced maintenance requirements make them cost-effective for long-term applications.