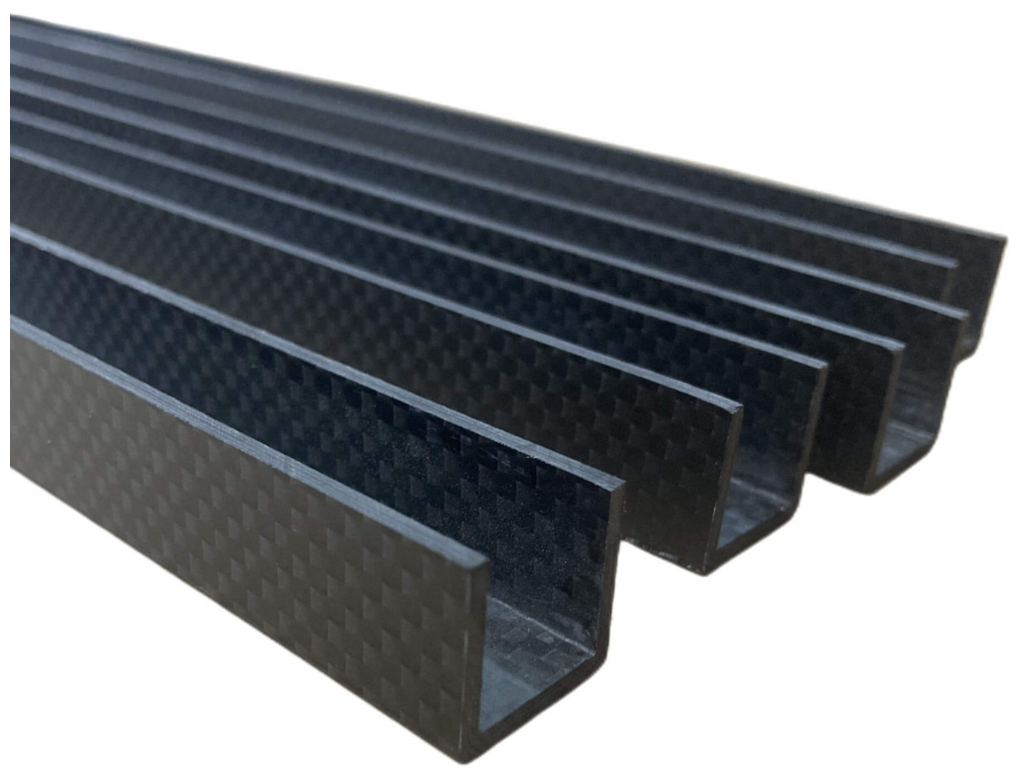
The 2.5D 3D Carbon Carbon Fiber Composite beams redefine performance in high-stress industries. These beams excel in aerospace, where they form vertical tails and missile nose cones, and in automotive brake systems. The C Beam CFC Bar by VET Energy offers unmatched thermal conductivity, tensile strength, and durability, making it indispensable for high-temperature manufacturing and C/C Composite (CFC) applications.
Key Takeaways
- 2.5D and 3D carbon-carbon fiber composite C beams offer a high strength-to-weight ratio, making them ideal for aerospace and automotive applications where reducing weight enhances performance and fuel efficiency.
- These composites excel in thermal management, maintaining exceptional thermal conductivity and resistance, which is crucial for high-temperature environments like vacuum furnaces and semiconductor manufacturing.
- VET Energy provides extensive customization options for these beams, allowing manufacturers to tailor them for specific applications, ensuring optimal performance in diverse and demanding industrial settings.
What Are 2.5D 3D Carbon Carbon Fiber Composite C Beams?
Overview of Carbon-Carbon Composites
Carbon-carbon composites are advanced materials known for their exceptional mechanical and thermal properties. These composites combine carbon fibers with a carbon matrix, resulting in a material that offers high strength, excellent wear resistance, and remarkable thermal stability. Unlike traditional composites, carbon-carbon materials maintain their strength even at temperatures exceeding 2500°C, making them ideal for extreme environments. Their low density, which is significantly lighter than metals, and tensile strength, which is 7-9 times greater than steel, further enhance their performance in demanding applications. Industries such as aerospace, automotive, and electronics rely on these composites for components like brake pads, high-pressure pumps, and conductive motor parts.
Differences Between 2.5D and 3D Structures
The structural differences between 2.5D and 3D carbon-carbon fiber composites significantly impact their applications. The 2.5D woven composite features a shallow-crossing linkage of carbon fibers, which minimizes delamination issues and allows for diverse design possibilities. This structure is particularly beneficial for applications requiring lightweight yet strong materials. On the other hand, 3D composites exhibit enhanced toughness and a smaller Young’s modulus, making them suitable for critical applications like chest wall reconstruction. Their increased resistance to impact and breakage ensures reliability in high-stress environments. Both structures excel in different scenarios, offering tailored solutions for specific industrial needs.
Advanced Manufacturing Processes by VET Energy
VET Energy employs cutting-edge manufacturing techniques to produce 2.5D and 3D carbon-carbon fiber composite beams. The process begins with carbon fiber preform preparation, ensuring a precise and uniform fiber arrangement. Chemical vapor deposition follows, which enhances the material’s thermal and mechanical properties by depositing carbon atoms into the matrix. Finally, precision machining ensures that each beam meets exact specifications, delivering superior quality and performance. These advanced methods enable VET Energy to create products like the 2.5D 3D Carbon Carbon Fiber Composite C beams, which excel in high-temperature and high-stress applications.
Key Advantages of 2.5D 3D Carbon Carbon Fiber Composite C Beams
High Strength-to-Weight Ratio
The high strength-to-weight ratio of 2.5D 3D Carbon Carbon Fiber Composite C beams offers significant benefits across industries. This property allows engineers to design lightweight yet robust components, which is critical in sectors like aerospace and automotive.
- In aerospace, lighter materials reduce overall aircraft weight, improving fuel efficiency and enabling higher payload capacities.
- In automotive applications, the reduced weight enhances vehicle performance, leading to better acceleration, speed, and energy efficiency.
By incorporating these beams, manufacturers achieve superior structural integrity without compromising on weight limitations, making them indispensable for high-performance applications.
Exceptional Thermal Conductivity and Resistance
2.5D and 3D carbon-carbon fiber composites excel in thermal management, a crucial factor in high-temperature environments. These beams maintain thermal conductivity ranging from 10 to 30 W/m.k at 1150℃, ensuring efficient heat dissipation.
Composite Type | Thermal Conductivity (at 1150℃) | W/m.k |
---|---|---|
2.5D | 10~30 | |
3D | 10~30 |
This exceptional thermal resistance makes them ideal for applications in vacuum furnaces, crystal growth systems, and semiconductor manufacturing, where consistent performance under extreme heat is essential.
Durability in Extreme Environments
The durability of 2.5D 3D Carbon Carbon Fiber Composite C beams ensures reliable performance in harsh conditions. These beams resist wear, impact, and thermal degradation, making them suitable for environments with high mechanical stress or fluctuating temperatures. Their ability to maintain structural integrity under such conditions extends their lifespan, reducing maintenance costs and downtime for industries relying on continuous operations.
Customization and Versatility for Complex Applications
VET Energy offers extensive customization options for 2.5D and 3D carbon-carbon fiber composite beams, enabling their use in diverse applications.
Customization Options | Applications |
---|---|
High-performance carbon-carbon composite | Load-bearing structural parts for vacuum furnace |
Material formulation | Semiconductor industry |
Chemical vapor deposition | Photovoltaic applications |
Precision machining | High-temperature industrial furnace applications |
Excellent high-temperature strength | New energy equipment manufacturing |
Dimensional stability | Crystal growth furnace applications |
Thermal conductivity | Heat treatment processes |
These options allow manufacturers to tailor the beams to specific requirements, ensuring optimal performance in complex and demanding environments.
Applications of 2.5D 3D Carbon Carbon Fiber Composite C Beams
Aerospace: Lightweight and Heat-Resistant Components
2.5D 3D Carbon Carbon Fiber Composite C beams play a pivotal role in aerospace engineering. Their lightweight nature and exceptional heat resistance make them indispensable for critical components. These beams are used in secondary structures of aircraft, such as vertical tails and rudders, where reducing weight without compromising strength is essential. They also serve as integral parts of missile nose cones, brake pads, and nozzles, ensuring reliability under extreme conditions.
In advanced aerospace systems, these composites contribute to the leading edges of turbine engines and rocket nozzles for hypersonic re-entry vehicles. NASA utilized similar materials in the Apollo spacecraft heat shield system, demonstrating their ability to withstand intense thermal and mechanical stress. The versatility and performance of these beams make them a cornerstone of modern aerospace innovation.
Automotive: High-Performance Structural Parts
The automotive industry benefits significantly from the high strength-to-weight ratio of 2.5D 3D Carbon Carbon Fiber Composite C beams. These beams enhance vehicle performance by reducing overall weight while maintaining structural integrity. They are commonly employed in brake systems, where their thermal stability and wear resistance ensure consistent performance under high-stress conditions.
High-performance vehicles, including electric and hybrid models, rely on these composites for lightweight structural components. By integrating these beams, manufacturers achieve improved acceleration, energy efficiency, and durability, meeting the demands of modern automotive engineering.
Industrial Use: Reliable Solutions for High-Temperature Systems
Industries requiring high-temperature solutions rely on 2.5D 3D Carbon Carbon Fiber Composite C beams for their exceptional thermal conductivity and durability. These beams are essential in vacuum furnaces, crystal growth systems, and semiconductor manufacturing, where consistent performance under extreme heat is critical.
Their ability to maintain dimensional stability and resist thermal degradation makes them ideal for photovoltaic applications and high-temperature industrial furnaces. The customization options offered by VET Energy allow these beams to meet specific industrial requirements, ensuring optimal performance in diverse and demanding environments.
Why Choose 2.5D 3D Carbon Carbon Fiber Composite C Beams Over Alternatives?
Advantages Over Metals: Weight, Strength, and Heat Resistance
2.5D and 3D carbon-carbon fiber composite beams outperform metals in several critical areas. Their lightweight nature, combined with high strength and heat resistance, makes them an ideal choice for demanding applications. These beams exhibit a bulk density of 1.40–1.50 g/cm³, significantly lighter than metals like steel or aluminum. Despite their low weight, they maintain impressive mechanical properties, including tensile strength of 90–130 MPa and compressive strength of 130–170 MPa.
Property | Value |
---|---|
Bulk density | 1.40~1.50 g/cm³ |
Tensile strength | 90~130 MPa |
Flexural Strength | 100~150 MPa |
Compressive strength | 130~170 MPa |
Thermal conductivity (1150℃) | 10~30 W/m.k |
Processing Temperature | ≥2400℃ |
These beams also excel in thermal conductivity, ranging from 10 to 30 W/m.k at 1150℃, and can withstand processing temperatures above 2400℃. Such properties make them indispensable for high-temperature environments where metals may fail due to thermal expansion or degradation.
Benefits Compared to Other Composites: Longevity and Performance
Compared to other composite materials, 2.5D and 3D carbon-carbon fiber composites offer superior longevity and performance. Their ability to maintain structural integrity under extreme conditions ensures a longer lifespan, reducing the need for frequent replacements. This durability translates to cost savings and operational efficiency for industries relying on continuous performance.
These beams also provide environmental benefits. Their strength allows for thinner, lighter structures, reducing material usage. Advances in manufacturing processes, including renewable energy integration, enhance sustainability. Ongoing research into carbon fiber recycling further minimizes their environmental footprint, making them a forward-thinking choice for eco-conscious industries.
VET Energy’s Expertise in Carbon-Carbon Solutions
VET Energy brings unparalleled expertise to the development of carbon-carbon solutions. The company specializes in high-performance, customized components, offering end-to-end solutions from material formulation to finished product manufacturing. Their advanced processes include carbon fiber preform preparation, chemical vapor deposition, and precision machining. These techniques ensure the production of 2.5D 3D carbon-carbon fiber composite beams that meet the highest standards of quality and performance.
By leveraging their technical knowledge and innovative manufacturing methods, VET Energy delivers products tailored to the unique requirements of industries such as aerospace, automotive, and high-temperature manufacturing. Their commitment to excellence positions them as a trusted partner for advanced material solutions.
2.5D and 3D carbon-carbon fiber composite C/C beams deliver unmatched performance in high-stress industries. Their strength, thermal resistance, and adaptability make them essential for demanding applications. VET Energy’s advanced manufacturing processes and dedication to quality ensure these beams meet rigorous standards, positioning the company as a trusted leader in carbon-carbon composite solutions.
FAQ
What makes 2.5D and 3D carbon-carbon fiber composites unique?
Their combination of lightweight design, high strength, and thermal resistance ensures superior performance in extreme environments. These properties make them ideal for aerospace, automotive, and industrial applications.
Can these beams be customized for specific applications?
Yes, VET Energy offers extensive customization options. Clients can specify dimensions, material formulations, and thermal properties to meet unique requirements for high-performance applications.
How do these composites compare to traditional materials like steel?
They outperform steel in weight, strength, and heat resistance. For example, their tensile strength is 7-9 times greater, while their density is significantly lower.