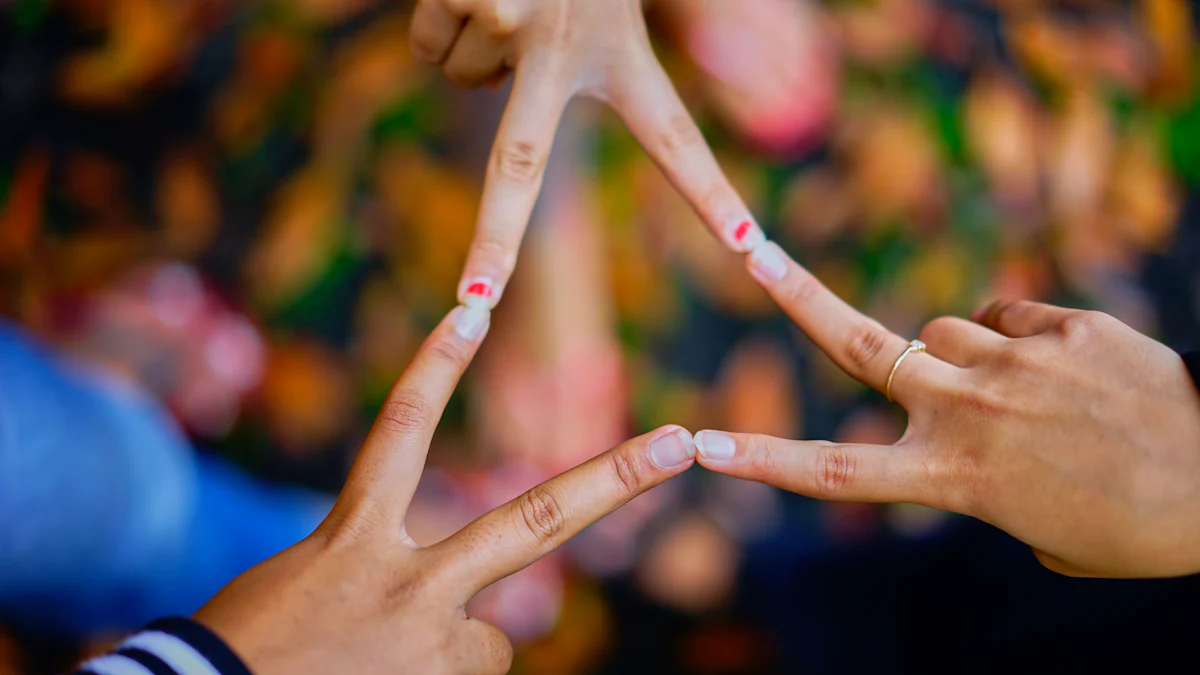
Tantalum carbide (TaC) coatings stand out due to their remarkable scientific attributes. Their unique composition combines tantalum and carbon, forming a material with extraordinary hardness and thermal stability. These coatings excel in extreme environments, enduring temperatures exceeding 2000°C while resisting chemical degradation. Industries rely on TaC coatings to enhance the durability and performance of components exposed to wear, heat, and corrosive conditions. Their ability to maintain structural integrity under such challenges makes them indispensable for modern technological advancements.
Key Takeaways
- TaC coatings are formed from tantalum and carbon, resulting in exceptional hardness and thermal stability, making them ideal for extreme environments.
- The crystalline structure of TaC enhances its durability and resistance to wear, ensuring long-lasting performance in demanding applications.
- Manufacturers utilize chemical vapor deposition (CVD) and physical vapor deposition (PVD) methods to create uniform and defect-free TaC coatings, crucial for their effectiveness.
- TaC coatings excel in high-temperature applications, maintaining structural integrity beyond 2000°C, which is vital for aerospace and energy sectors.
- The chemical inertness of TaC coatings protects components from corrosive environments, significantly reducing maintenance costs and extending operational lifespans.
- In the automotive industry, TaC coatings improve wear resistance in engine components, leading to enhanced performance and lower maintenance expenses.
- Emerging applications in additive manufacturing and next-generation electronics highlight the versatility of TaC coatings, paving the way for innovative technological advancements.
The Science Behind TaC Coatings
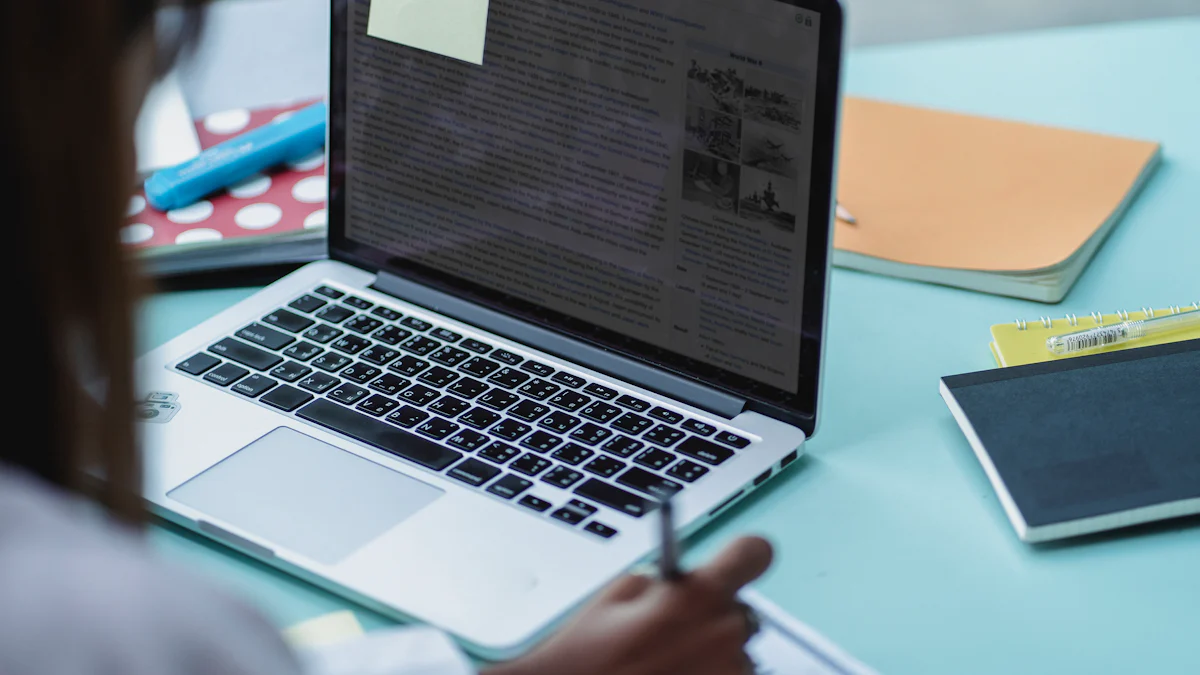
Composition and Microstructure
The role of tantalum and carbon in forming TaC
Tantalum carbide (TaC) forms through the combination of tantalum and carbon atoms. Tantalum, a transition metal, contributes to the material’s exceptional strength and resistance to high temperatures. Carbon, a non-metal, enhances the hardness and chemical stability of the compound. Together, these elements create a robust material capable of withstanding extreme conditions. The precise ratio of tantalum to carbon determines the final properties of the TaC coating, making it essential to maintain strict control during synthesis.
Crystalline structure and its impact on material properties
The crystalline structure of TaC plays a crucial role in defining its unique characteristics. TaC adopts a face-centered cubic (FCC) lattice, which ensures uniform atomic bonding throughout the material. This structure contributes to its high melting point and exceptional hardness. The arrangement of atoms within the lattice minimizes defects, enhancing the coating’s durability and resistance to wear. A well-ordered crystalline structure also improves the coating’s ability to maintain its properties under mechanical stress and thermal fluctuations.
Formation Processes
Chemical vapor deposition (CVD) and physical vapor deposition (PVD) methods
Manufacturers commonly use chemical vapor deposition (CVD) and physical vapor deposition (PVD) to produce TaC coatings. CVD involves the reaction of gaseous precursors, such as tantalum chloride and methane, at elevated temperatures. This process allows for precise control over the coating’s thickness and composition. PVD, on the other hand, relies on physical processes like sputtering or evaporation to deposit TaC onto a substrate. Both methods ensure strong adhesion between the coating and the underlying material, which is critical for performance in demanding applications.
Challenges in achieving uniform and defect-free TaC coatings
Producing uniform and defect-free TaC coatings presents significant challenges. Variations in temperature, pressure, or precursor concentration during deposition can lead to inconsistencies in the coating’s thickness or composition. Defects such as voids or cracks may form, compromising the coating’s performance. Advanced techniques, including real-time monitoring and process optimization, help address these issues. Achieving a defect-free TaC coating requires meticulous attention to detail and precise control over every step of the formation process.
Key Scientific Principles
High melting point and its correlation with atomic bonding
TaC exhibits one of the highest melting points among known materials, exceeding 3800°C. This remarkable property stems from the strong covalent bonds between tantalum and carbon atoms. These bonds require significant energy to break, allowing the material to retain its structural integrity at extreme temperatures. The high melting point makes TaC coatings ideal for applications in aerospace and energy sectors, where components face intense heat.
Resistance to chemical degradation in harsh environments
TaC coatings demonstrate exceptional resistance to chemical degradation, even in highly corrosive environments. The material’s inert nature prevents reactions with aggressive substances like acids, alkalis, or gases such as hydrogen and ammonia. This resistance ensures long-term protection for components exposed to harsh conditions. Industries rely on TaC coatings to safeguard tools and machinery, reducing maintenance costs and extending operational lifespans.
Unique Properties of TaC Coatings
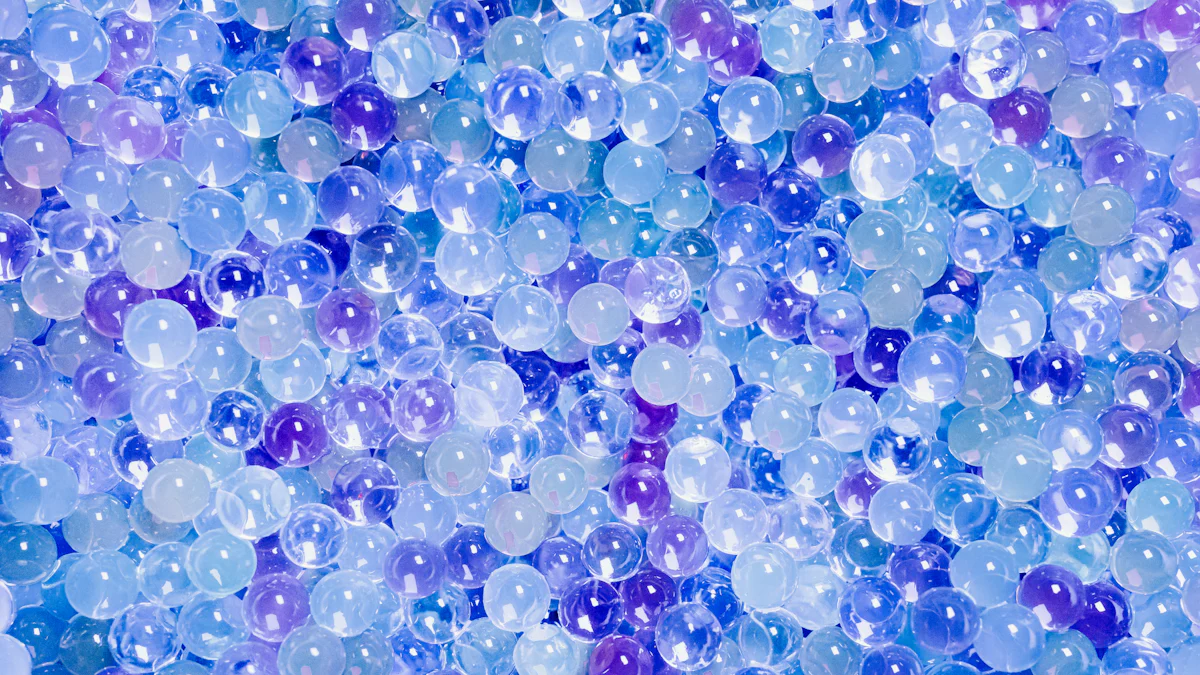
Exceptional Hardness
Comparison with other carbide coatings (e.g., TiC, WC)
TaC coatings exhibit superior hardness compared to other carbide coatings like titanium carbide (TiC) and tungsten carbide (WC). This exceptional hardness stems from the strong covalent bonds between tantalum and carbon atoms. While TiC and WC also offer high hardness, TaC surpasses them in its ability to resist deformation under extreme pressure. The unique atomic structure of TaC contributes to its unparalleled durability, making it a preferred choice for applications requiring maximum wear resistance.
Applications requiring extreme wear resistance
Industries utilize TaC coatings in environments where components face constant abrasion or mechanical stress. Cutting tools, for instance, benefit from the enhanced lifespan provided by TaC coatings. These coatings reduce wear and maintain sharpness over extended periods. Mining equipment and industrial machinery also rely on TaC coatings to withstand harsh operating conditions. By minimizing material loss due to wear, TaC coatings improve efficiency and reduce maintenance costs.
Thermal Stability
Performance at high temperatures in aerospace and energy sectors
TaC coatings maintain their structural integrity at temperatures exceeding 2000°C, making them indispensable in high-temperature environments. In the aerospace sector, these coatings protect rocket nozzles and heat shields from intense thermal loads. Energy industries use TaC coatings to safeguard turbines and reactors operating under extreme heat. The ability of TaC coatings to perform reliably in such conditions ensures the longevity and safety of critical components.
Resistance to thermal shock and oxidation
Thermal shock occurs when materials experience rapid temperature changes, leading to cracks or failure. TaC coatings resist thermal shock due to their robust atomic bonding and stable crystalline structure. This property makes them ideal for applications involving fluctuating temperatures. Additionally, TaC coatings exhibit excellent resistance to oxidation, even at elevated temperatures. This resistance prevents material degradation, ensuring consistent performance in demanding environments.
Chemical Inertness
Protection against corrosive environments
TaC coatings provide exceptional protection in chemically aggressive settings. Their inert nature prevents reactions with corrosive substances, including acids, alkalis, and industrial gases. Components coated with TaC remain unaffected by prolonged exposure to harsh chemicals, ensuring reliable operation. This property proves invaluable in industries such as chemical processing, where equipment must endure constant contact with reactive materials.
Use in chemically aggressive industrial processes
Industrial processes involving hydrogen, ammonia, or silane often require materials that can withstand corrosive conditions. TaC coatings excel in these scenarios, offering unmatched chemical stability. Semiconductor manufacturing, for example, benefits from TaC coatings that protect tools and surfaces during etching and deposition processes. By resisting chemical attack, TaC coatings enhance the efficiency and durability of equipment used in such environments.
Electrical and Thermal Conductivity
Applications in electronics and heat management
TaC coatings exhibit impressive electrical and thermal conductivity, making them valuable in advanced electronics and heat management systems. Their ability to conduct electricity efficiently allows their use in components such as electrodes, circuit boards, and microelectronic devices. These coatings ensure stable performance by minimizing energy loss during operation. In high-power electronics, TaC coatings help dissipate heat effectively, preventing overheating and enhancing the reliability of devices.
In heat management, TaC coatings play a critical role in thermal interface materials and heat exchangers. Their excellent thermal conductivity enables rapid heat transfer, which is essential for maintaining optimal temperatures in industrial machinery and electronic systems. For instance, in semiconductor manufacturing, TaC coatings improve heat dissipation in equipment, ensuring consistent performance under demanding conditions. Their dual role in conducting electricity and managing heat makes them indispensable in modern technology.
Balancing conductivity with other properties
Achieving a balance between conductivity and other properties is crucial for the effective use of TaC coatings. While high conductivity is desirable, it must not compromise the coating’s hardness, chemical resistance, or thermal stability. Manufacturers carefully control the composition and microstructure of TaC coatings to maintain this balance. By optimizing the ratio of tantalum to carbon, they ensure that the coating retains its durability and resistance to wear while delivering excellent conductivity.
Industries often tailor TaC coatings to meet specific application requirements. For example, in aerospace, coatings must withstand extreme temperatures while maintaining thermal conductivity. In electronics, coatings need to provide electrical conductivity without sacrificing chemical inertness. This adaptability highlights the versatility of TaC coatings and their ability to meet diverse industrial demands. The careful engineering of these coatings ensures their effectiveness across a wide range of applications.
Practical Applications of TaC Coatings
Aerospace Industry
Use in rocket nozzles and heat shields
Rocket nozzles and heat shields face extreme thermal and mechanical stress during operation. TaC coating provides a robust solution for these challenges. Its high melting point ensures that it remains stable even at temperatures exceeding 2000°C. This stability protects rocket nozzles from erosion caused by intense heat and high-velocity gases. Heat shields coated with TaC maintain their structural integrity, preventing damage during atmospheric re-entry. The aerospace industry values this coating for its ability to enhance the reliability and safety of critical components.
Enhancing durability of components exposed to extreme heat
Components in aerospace applications often operate under extreme heat conditions. TaC coating significantly improves their durability by resisting thermal degradation and oxidation. Turbine blades, for example, benefit from this coating as it prevents material loss due to high-temperature exposure. By extending the lifespan of these components, TaC coating reduces the need for frequent replacements. This durability contributes to cost savings and ensures uninterrupted performance in demanding environments.
Automotive Sector
Improving wear resistance in engine components
Engine components in automobiles experience constant friction and wear. TaC coating addresses this issue by providing exceptional hardness and wear resistance. Pistons, valves, and cylinder liners coated with TaC exhibit reduced surface degradation, ensuring smoother operation. This coating minimizes friction, which improves fuel efficiency and reduces energy loss. Automotive manufacturers rely on TaC coating to enhance the performance and longevity of critical engine parts.
Reducing maintenance costs through longer-lasting parts
Frequent maintenance and part replacements increase operational costs for vehicle owners. TaC coating offers a cost-effective solution by extending the lifespan of automotive components. Its resistance to wear and corrosion ensures that parts remain functional for longer periods. This durability reduces the frequency of repairs and replacements, leading to lower maintenance expenses. Vehicle manufacturers use TaC coating to deliver reliable and durable products to their customers.
Energy and Power Generation
Protecting turbines and reactors in high-temperature environments
Turbines and reactors in power generation facilities operate under extreme heat and pressure. TaC coating provides a protective barrier that prevents thermal damage and material degradation. Gas turbines, for instance, benefit from this coating as it resists oxidation and wear caused by high-temperature combustion. Nuclear reactors also use TaC coating to shield components from radiation and chemical exposure. This protection ensures the safe and efficient operation of energy systems.
Enhancing efficiency in renewable energy systems
Renewable energy systems, such as solar and wind power, require materials that can withstand harsh environmental conditions. TaC coating enhances the efficiency of these systems by improving the durability of critical components. In solar power plants, it protects mirrors and receivers from thermal and chemical damage. Wind turbines benefit from TaC coating on their blades, which reduces wear caused by constant exposure to wind and debris. By increasing the reliability of renewable energy systems, TaC coating supports the transition to sustainable energy sources.
Emerging Applications
Potential use in additive manufacturing and 3D printing
Additive manufacturing, commonly known as 3D printing, has revolutionized the production of complex components. TaC coatings show immense potential in this field due to their exceptional thermal stability and wear resistance. These properties make them ideal for enhancing the performance of 3D-printed parts used in high-stress environments. For instance, industries can apply TaC coatings to 3D-printed molds and dies to improve their durability during repeated use.
The aerospace and automotive sectors benefit significantly from this application. TaC-coated 3D-printed parts can withstand extreme temperatures and mechanical stress, ensuring reliability in critical operations. Additionally, the chemical inertness of TaC coatings protects 3D-printed components from corrosive environments, extending their lifespan. Researchers continue to explore ways to integrate TaC coatings into additive manufacturing processes, aiming to create parts with superior performance and longevity.
Role in next-generation electronics and nanotechnology
Next-generation electronics demand materials that combine electrical conductivity with durability. TaC coatings meet these requirements, making them a valuable asset in the development of advanced electronic devices. Their ability to conduct electricity efficiently supports their use in microchips, sensors, and other electronic components. Furthermore, the thermal conductivity of TaC coatings helps manage heat in high-power devices, preventing overheating and ensuring stable operation.
Nanotechnology also benefits from the unique properties of TaC coatings. Their exceptional hardness and chemical resistance make them suitable for protecting nanoscale structures from wear and corrosion. In semiconductor manufacturing, TaC coatings enhance the precision and durability of tools used in nanoscale fabrication processes. This application ensures consistent performance and reduces the risk of defects in delicate components.
"The integration of TaC coatings into nanotechnology and electronics represents a significant step forward in material science," according to experts in the field. By leveraging the unique properties of TaC, industries can develop innovative solutions for emerging technological challenges.
TaC coatings showcase a remarkable blend of scientific principles, unique properties, and practical applications. Their exceptional hardness, thermal stability, chemical inertness, and conductivity enable industries to enhance the performance and durability of critical components. These coatings play a pivotal role in advancing material science, addressing challenges in aerospace, automotive, energy, and emerging technologies.
"TaC coatings represent a breakthrough in material innovation," experts emphasize. Future advancements may unlock new possibilities, expanding their use in cutting-edge fields like nanotechnology and additive manufacturing. TaC coatings continue to pave the way for technological progress across diverse industries.