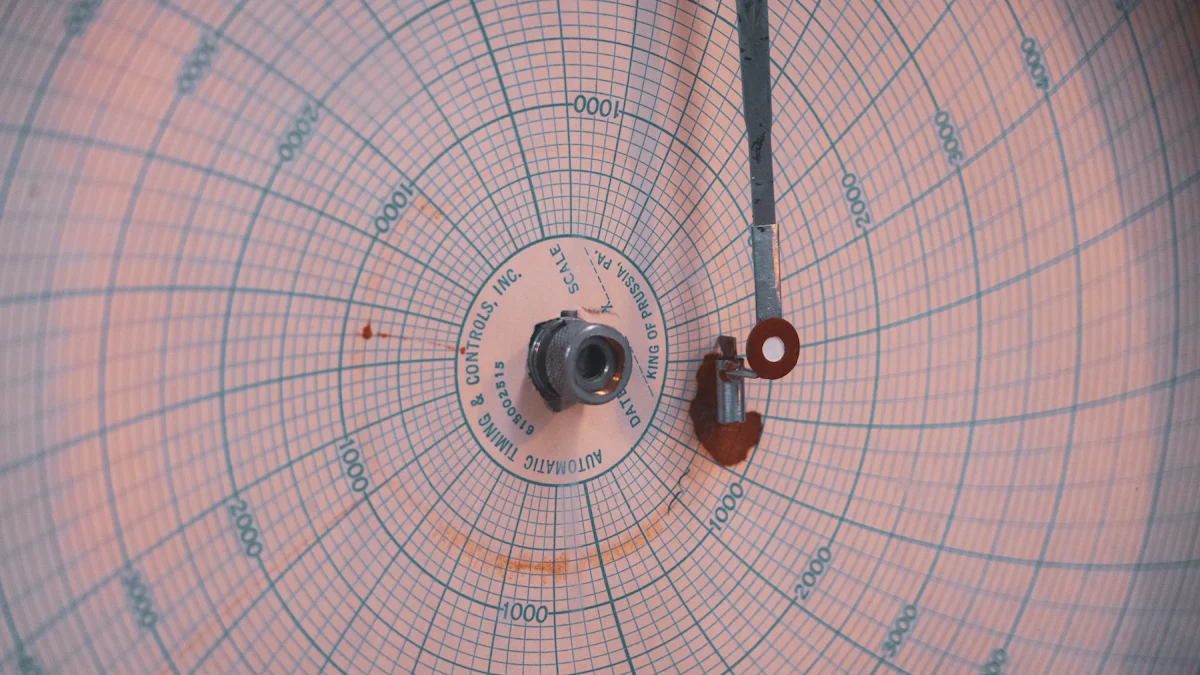
Pyrocarbon coating plays a crucial role in nuclear fuel technology. It provides a protective layer that enhances the performance and safety of nuclear fuel particles. Its unique properties, such as high thermal stability and chemical inertness, make it indispensable in extreme environments. These coatings not only withstand intense radiation but also prevent the release of harmful fission products. Interestingly, the same material has found applications in biomedical fields, where its durability and biocompatibility have proven valuable. This dual utility highlights the versatility and importance of pyrocarbon in advanced technologies.
Key Takeaways
- Pyrocarbon coatings enhance the safety and performance of nuclear fuel by providing a protective layer against radiation damage and preventing the release of harmful fission products.
- The unique turbostratic structure of pyrocarbon offers a balance of mechanical strength and flexibility, making it ideal for extreme environments in both nuclear and biomedical applications.
- Recent advancements in coating techniques, such as plasma-enhanced chemical vapor deposition, improve the precision and efficiency of pyrocarbon coatings, benefiting both industries.
- Pyrocarbon’s chemical inertness and biocompatibility make it a valuable material in medical devices, reducing wear and improving patient safety.
- The longevity and durability of pyrocarbon coatings lead to cost savings in nuclear operations by minimizing maintenance and replacement needs.
- Both nuclear and biomedical applications rely on the precision of pyrocarbon coatings to ensure safety and effectiveness, highlighting the importance of quality control in manufacturing.
- Ongoing research aims to enhance the properties of pyrocarbon coatings, paving the way for innovative applications in advanced nuclear reactors and medical technologies.
Understanding Pyrocarbon Coatings
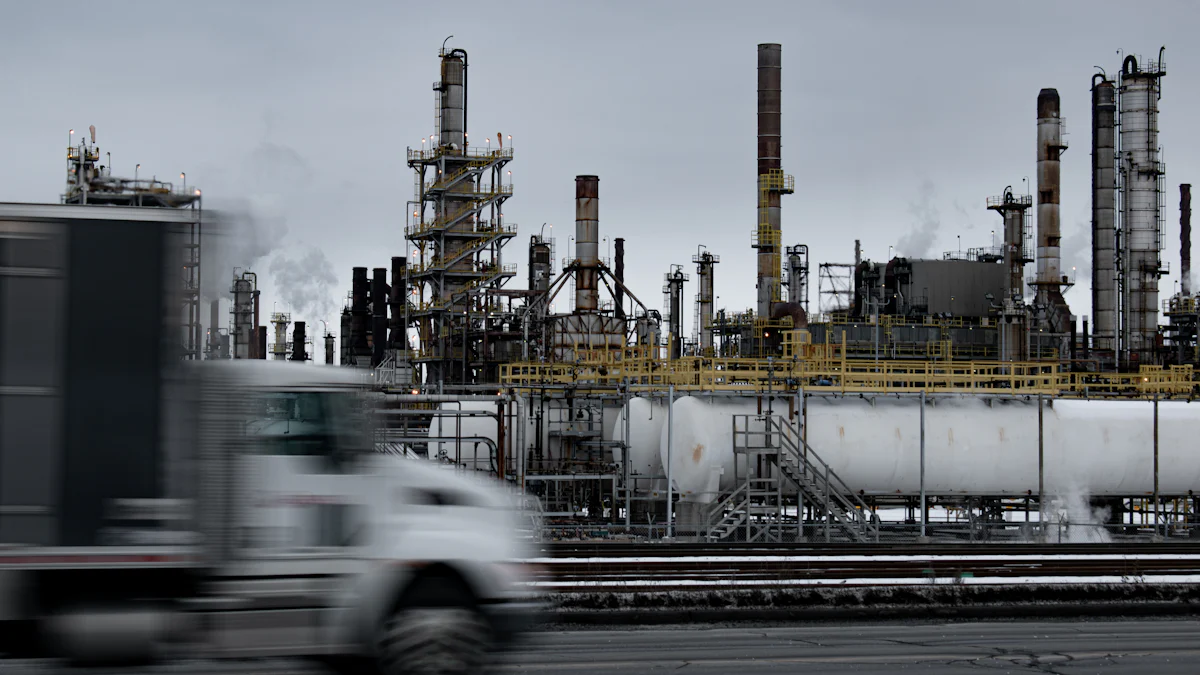
Defining Pyrocarbon Coatings
Composition and structure of pyrocarbon
Pyrocarbon consists of carbon atoms arranged in a unique, turbostratic structure. Unlike graphite, which has a highly ordered crystalline arrangement, pyrocarbon exhibits a more disordered yet layered configuration. This structure provides a balance between rigidity and flexibility, making it suitable for demanding applications. The material forms through a chemical vapor deposition process, where hydrocarbon gases decompose at high temperatures to deposit carbon layers. This method ensures a dense and uniform coating, critical for its performance in extreme environments.
How pyrocarbon differs from other carbon-based materials
Pyrocarbon stands apart from other carbon-based materials due to its distinct properties. While graphite offers excellent thermal conductivity, pyrocarbon provides superior mechanical strength and resistance to cracking under stress. Unlike diamond, which is extremely hard but brittle, pyrocarbon combines durability with a degree of elasticity. These characteristics make it ideal for applications requiring both toughness and adaptability. Additionally, its chemical inertness surpasses that of many other carbon materials, allowing it to perform reliably in corrosive or high-radiation environments.
Key Properties of Pyrocarbon Coatings
High-temperature resistance and thermal stability
Pyrocarbon coatings excel in high-temperature environments. They maintain structural integrity and resist degradation even under extreme heat. This property proves essential in nuclear reactors, where fuel particles face intense thermal conditions. The material’s ability to withstand such temperatures ensures the safety and efficiency of nuclear operations.
Mechanical strength and durability
The mechanical strength of pyrocarbon coatings enables them to endure significant stress without failure. Their durability prevents cracking or peeling, even when exposed to harsh conditions. This robustness is vital for protecting nuclear fuel particles, as it minimizes the risk of damage during reactor operation. The long-lasting nature of these coatings also reduces maintenance requirements.
Chemical inertness and biocompatibility
Pyrocarbon coatings exhibit remarkable chemical inertness, resisting reactions with most substances. This trait ensures their stability in chemically aggressive environments, such as those found in nuclear reactors. Furthermore, their biocompatibility has opened doors to biomedical applications. In medical devices, the material interacts safely with biological tissues, demonstrating its versatility across industries.
Pyrocarbon Coatings in Nuclear Fuel Applications
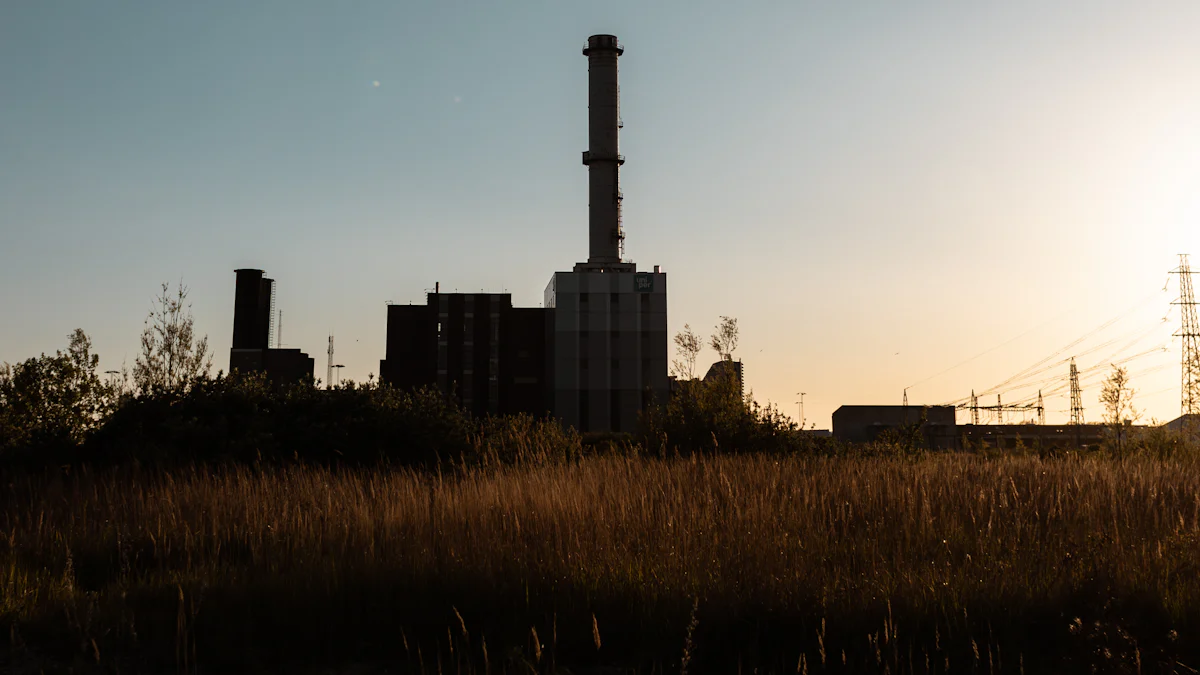
Enhancing Nuclear Fuel Performance
Protection of nuclear fuel particles from radiation damage
Pyrocarbon coating serves as a critical barrier for nuclear fuel particles. It shields the fuel kernels from intense radiation, which can degrade their structural integrity over time. This protective layer absorbs and disperses radiation energy, reducing the risk of material failure. By maintaining the stability of the fuel particles, it ensures consistent performance during reactor operations. This capability makes pyrocarbon coating an essential component in advanced nuclear technologies.
Prevention of fission product release
Fission reactions within nuclear fuel produce byproducts that can pose significant safety risks if released. Pyrocarbon coating prevents these fission products from escaping into the reactor environment. Its dense and impermeable structure acts as a containment layer, trapping harmful isotopes within the fuel particles. This containment reduces contamination risks and enhances the overall safety of nuclear reactors. The reliability of this coating contributes to the secure handling and operation of nuclear fuel.
Benefits of Pyrocarbon Coatings in Nuclear Fuel
Improved safety and reliability of nuclear reactors
The application of pyrocarbon coating directly improves the safety of nuclear reactors. Its ability to withstand extreme conditions ensures that fuel particles remain intact, even under high temperatures and radiation exposure. This stability minimizes the likelihood of accidents caused by fuel degradation. Additionally, the coating enhances reactor reliability by maintaining consistent fuel performance over extended periods. These qualities make it a cornerstone of modern nuclear reactor design.
Longevity and cost-effectiveness
Pyrocarbon coating extends the lifespan of nuclear fuel particles. Its durability reduces wear and tear, allowing the fuel to function effectively for longer durations. This longevity translates to fewer replacements and lower operational costs for nuclear facilities. Furthermore, the coating’s resistance to chemical and physical damage minimizes maintenance requirements. These economic advantages make pyrocarbon coating a cost-effective solution for enhancing nuclear fuel efficiency.
Challenges and Limitations
Manufacturing complexities and costs
Producing pyrocarbon coating involves intricate processes that require precise control. The chemical vapor deposition method demands high temperatures and specialized equipment, which increases production costs. Achieving uniformity in the coating also adds to the complexity of manufacturing. These challenges make the production process resource-intensive, posing a barrier to widespread adoption in some applications.
Potential issues with coating uniformity
Uniformity in pyrocarbon coating is crucial for its effectiveness. Variations in thickness or density can compromise its protective properties. Inconsistent coatings may lead to weak points, increasing the risk of radiation damage or fission product leakage. Ensuring uniform application requires advanced techniques and rigorous quality control measures. Addressing these issues remains a key focus for researchers and manufacturers.
Recent Advancements in Pyrocarbon Coatings
Innovations in coating techniques
Recent years have seen significant progress in the methods used to apply pyrocarbon coatings. Researchers have refined chemical vapor deposition (CVD) processes to achieve greater precision and efficiency. Advanced control systems now monitor temperature, gas flow, and deposition rates with remarkable accuracy. These improvements ensure consistent coating thickness and density, which are critical for maintaining the protective properties of the material.
Innovative approaches, such as plasma-enhanced CVD, have also emerged. This technique uses plasma to enhance the reaction process, enabling faster deposition and improved material quality. Plasma-enhanced methods reduce energy consumption and production time, making the manufacturing process more sustainable. Additionally, researchers are exploring hybrid techniques that combine traditional CVD with other methods, such as atomic layer deposition, to further enhance coating performance.
Automation has played a pivotal role in advancing coating techniques. Automated systems reduce human error and increase production scalability. These systems allow manufacturers to produce high-quality pyrocarbon coatings at a larger scale, meeting the growing demand in nuclear and biomedical industries. The integration of robotics into the coating process has also improved uniformity and reduced production costs.
Research on improving material properties for TRISO fuel particles
TRISO (tri-structural isotropic) fuel particles represent a breakthrough in nuclear fuel technology, and pyrocarbon coatings are essential to their design. Researchers are actively working to enhance the material properties of these coatings to meet the demanding requirements of advanced reactors. One area of focus involves increasing the thermal conductivity of pyrocarbon. Improved thermal conductivity helps manage heat more effectively, ensuring the stability and efficiency of TRISO fuel particles under extreme conditions.
Another key research direction involves enhancing the mechanical strength of pyrocarbon coatings. Scientists are investigating ways to optimize the turbostratic structure of the material to resist cracking and deformation. These advancements aim to extend the lifespan of TRISO fuel particles, reducing the frequency of replacements and improving reactor reliability.
Efforts to improve the chemical inertness of pyrocarbon coatings have also gained momentum. Enhanced chemical resistance ensures that the coating remains stable in aggressive environments, such as those with high radiation or corrosive substances. Researchers are experimenting with doping techniques, where small amounts of other elements are introduced to modify the material’s properties. These modifications aim to create coatings that are even more robust and versatile.
Collaboration between academic institutions and industry leaders has accelerated progress in this field. Joint research initiatives have led to the development of experimental coatings that show promise in laboratory tests. These advancements bring the industry closer to deploying next-generation TRISO fuel particles in commercial reactors, paving the way for safer and more efficient nuclear energy.
Pyrocarbon Coatings in Biomedical Applications
Applications in Medical Devices and Implants
Use in artificial heart valves and joint replacements
Pyrocarbon coatings have revolutionized the design of artificial heart valves and joint replacements. Engineers use this material to enhance the durability and functionality of these medical devices. In artificial heart valves, pyrocarbon ensures smooth blood flow by reducing friction and wear. Its hemocompatibility minimizes the risk of blood clot formation, which is critical for patient safety. Joint replacements, such as hip and knee implants, benefit from the material’s exceptional wear resistance. This property extends the lifespan of the implants, reducing the need for frequent replacements and improving the quality of life for patients.
Role in reducing wear and improving biocompatibility
The unique properties of pyrocarbon coatings significantly reduce wear in medical devices. The material’s smooth surface minimizes friction between moving parts, which prevents degradation over time. This feature is particularly important in joint replacements, where constant movement can lead to material breakdown. Pyrocarbon also exhibits excellent biocompatibility, allowing it to interact safely with human tissues. Its chemical inertness prevents adverse reactions, making it a preferred choice for implants. These qualities ensure that medical devices coated with pyrocarbon perform reliably and safely within the human body.
Similarities Between Nuclear and Biomedical Applications
Importance of durability and chemical inertness
Both nuclear and biomedical applications rely heavily on the durability and chemical inertness of pyrocarbon coatings. In nuclear reactors, the material withstands extreme radiation and thermal conditions without degrading. Similarly, in biomedical devices, it resists wear and chemical reactions within the human body. This shared reliance on durability ensures long-term performance in both fields. Chemical inertness plays a crucial role in maintaining stability, whether in a reactor’s harsh environment or within biological systems.
Need for precision in coating application
Precision in applying pyrocarbon coatings is essential for success in both industries. In nuclear fuel, uniform coatings prevent weak points that could compromise safety. In biomedical devices, precise application ensures compatibility with human tissues and reduces the risk of device failure. Advanced techniques, such as chemical vapor deposition, enable manufacturers to achieve the required accuracy. This focus on precision highlights the importance of quality control in both nuclear and biomedical applications.
Key Differences in Application Requirements
Operating environments and performance expectations
The operating environments for nuclear and biomedical applications differ significantly. Nuclear reactors expose pyrocarbon coatings to extreme heat, radiation, and corrosive substances. These conditions demand exceptional thermal stability and mechanical strength. In contrast, biomedical devices operate within the human body, where biocompatibility and resistance to biological wear are critical. Performance expectations also vary. Nuclear coatings must ensure reactor safety and efficiency, while biomedical coatings prioritize patient health and device longevity.
Regulatory and safety considerations
Regulatory and safety requirements present another key difference between the two fields. Nuclear applications must comply with strict regulations to prevent environmental contamination and ensure reactor safety. These standards focus on material performance under extreme conditions. Biomedical applications face rigorous testing to meet medical safety standards. Regulatory bodies evaluate biocompatibility, toxicity, and long-term effects on human health. These distinct requirements shape the development and application of pyrocarbon coatings in each industry.
Comparing and Contrasting Applications
Overlapping Benefits of Pyrocarbon Coatings
Shared reliance on thermal and chemical stability
Pyrocarbon coatings demonstrate exceptional thermal and chemical stability, which benefits both nuclear and biomedical applications. In nuclear reactors, these coatings endure extreme heat and radiation without degrading. This stability ensures the safety and efficiency of fuel particles over extended periods. Similarly, in biomedical devices, pyrocarbon resists chemical reactions within the human body. Its inert nature prevents adverse interactions with biological tissues, ensuring long-term compatibility.
Both fields rely on this stability to maintain performance under demanding conditions. The ability of pyrocarbon to resist wear and corrosion makes it a reliable choice for applications requiring durability. This shared reliance highlights the material’s versatility and underscores its importance in advanced technologies.
Cross-disciplinary advancements benefiting both fields
Advancements in pyrocarbon research often benefit both nuclear and biomedical industries. Innovations in coating techniques, such as plasma-enhanced chemical vapor deposition, improve the precision and quality of coatings. These developments enhance the performance of nuclear fuel particles and medical implants alike. Researchers in one field frequently draw inspiration from the other, fostering cross-disciplinary collaboration.
For example, studies on improving the mechanical strength of pyrocarbon for TRISO fuel particles have informed the design of more durable biomedical implants. Similarly, biocompatibility research in the medical field has influenced the development of safer coatings for nuclear applications. This exchange of knowledge accelerates progress and expands the potential of pyrocarbon across diverse industries.
Diverging Challenges and Innovations
Field-specific challenges in manufacturing and application
Each field faces unique challenges in the manufacturing and application of pyrocarbon coatings. In nuclear technology, achieving uniform coatings on fuel particles remains a critical issue. Variations in thickness or density can compromise the protective properties of the material. Manufacturers must employ advanced techniques and rigorous quality control to address these concerns.
In the biomedical sector, ensuring biocompatibility poses a significant challenge. Coatings must meet strict medical standards to avoid adverse reactions within the human body. The production process requires precision to create smooth surfaces that reduce friction and wear. These field-specific challenges shape the development of pyrocarbon coatings and influence their application.
Unique research directions in nuclear and biomedical fields
Research efforts in nuclear and biomedical applications often diverge due to differing priorities. In the nuclear industry, scientists focus on enhancing thermal conductivity and radiation resistance. These improvements aim to optimize the performance of TRISO fuel particles and ensure reactor safety. Researchers also explore ways to reduce production costs, making advanced coatings more accessible.
In contrast, biomedical research prioritizes biocompatibility and wear resistance. Scientists investigate methods to improve the interaction between pyrocarbon and biological tissues. Efforts to extend the lifespan of medical implants drive innovation in surface engineering and material composition. These distinct research directions reflect the specific needs of each field while showcasing the adaptability of pyrocarbon coatings.
Pyrocarbon coatings play a vital role in both nuclear fuel and biomedical applications. Their unique properties, such as durability and chemical stability, make them indispensable in these fields. Both industries benefit from advancements in coating techniques, though each faces distinct challenges. Future research holds the potential to unlock new applications, enhancing efficiency and safety across various sectors. Pyrocarbon’s versatility underscores the importance of material science in solving complex problems. Exploring innovations in this area can inspire breakthroughs that shape the future of technology and healthcare.