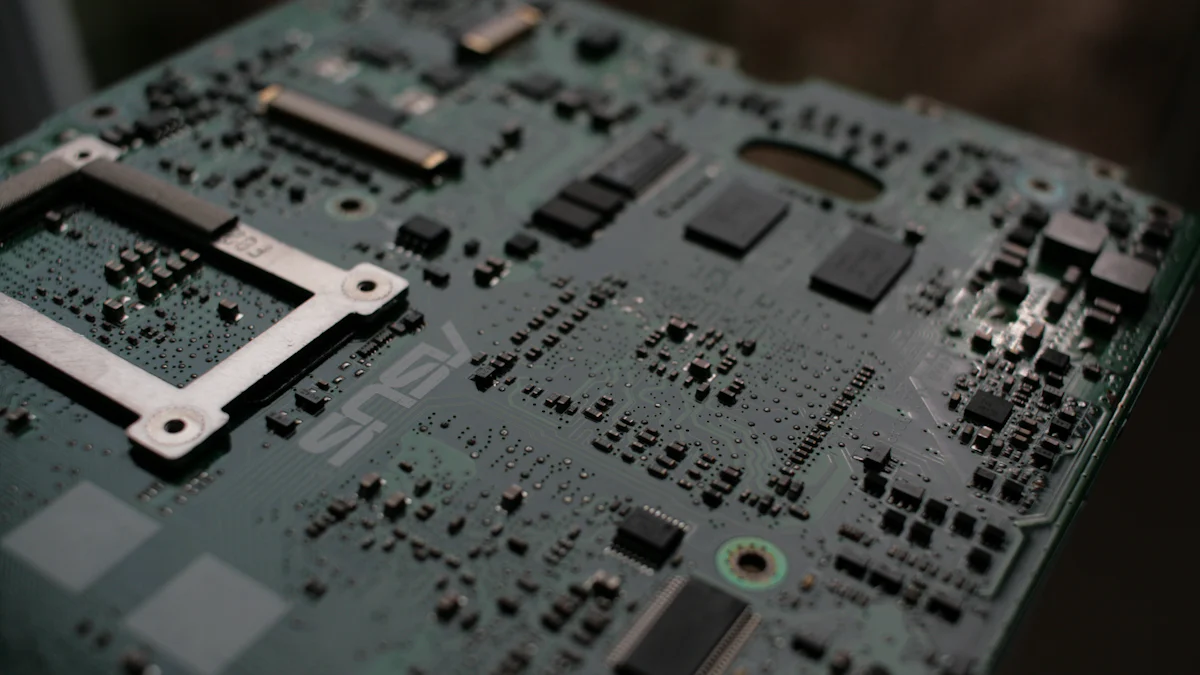
Plasma etching disk technology revolutionizes disk production by enabling the creation of intricate structures with unmatched precision. This process uses plasma to remove material from substrates, allowing manufacturers to achieve the fine details required for modern disk technology. Its ability to produce tiny features with high accuracy makes it indispensable for high-volume manufacturing. Plasma etching also accelerates production cycles, saving time and reducing costs. By combining speed, versatility, and precision, it empowers industries to meet the growing demand for advanced and efficient disk products.
Key Takeaways
- Plasma etching is essential for creating intricate disk structures with high precision, making it a cornerstone of modern disk production.
- The process utilizes ionized gas to remove material, allowing for the production of microscopic features that meet the demands of advanced technology.
- Techniques like the Bosch process, RIE, and ICP-RIE each offer unique advantages, enabling manufacturers to tailor their approach based on specific production needs.
- ICP-RIE stands out for its ability to achieve faster etching rates and superior precision, making it ideal for complex designs and high-volume manufacturing.
- Choosing the right plasma etching technique involves balancing factors such as design complexity, material composition, production volume, and cost.
- Mastering plasma etching techniques empowers manufacturers to innovate and enhance the performance of disk products in a rapidly evolving technological landscape.
Understanding Plasma Etching Disk Processes
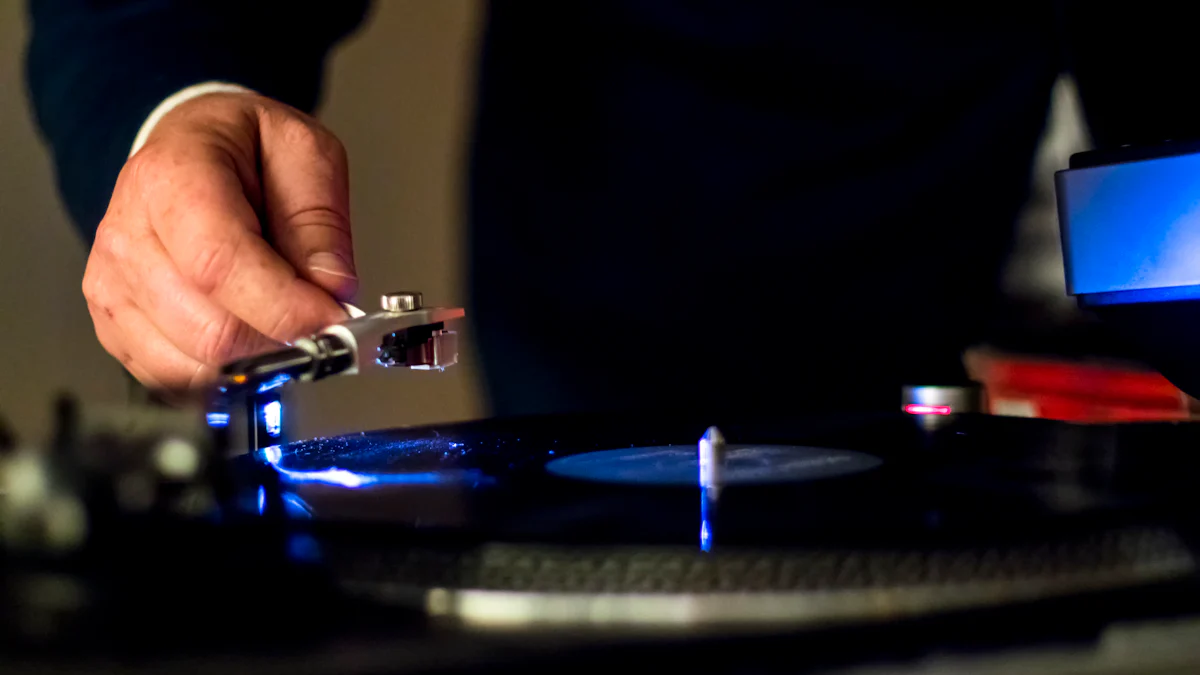
Plasma etching has become a cornerstone in the production of modern disks. By leveraging advanced techniques, manufacturers can achieve the precision and intricacy required for today’s high-performance disk technologies. This section delves into the fundamentals of plasma etching and its operational principles, offering a clear understanding of its transformative role in disk production.
What is Plasma Etching?
Definition and principles of plasma etching in disk production.
Plasma etching refers to a dry etching process that uses ionized gas, or plasma, to remove material from a substrate. In disk production, this method enables the creation of intricate patterns and structures with exceptional accuracy. The process relies on the interaction between the plasma and the material surface, where high-energy ions and reactive species break down and remove unwanted layers. This precision makes plasma etching indispensable for producing the microscopic features required in modern disks.
The principles of plasma etching revolve around controlled chemical and physical reactions. By adjusting parameters such as gas composition, pressure, and power, manufacturers can tailor the etching process to meet specific requirements. This adaptability ensures that plasma etching remains a versatile tool for creating complex designs on disk substrates.
Key components and their roles in the plasma etching process.
Several critical components drive the plasma etching process. The plasma chamber serves as the environment where the etching occurs, maintaining the necessary conditions for plasma generation. Inside the chamber, gases like fluorine or chlorine are introduced and ionized to form plasma. The radio frequency (RF) power source energizes the gas molecules, creating the high-energy ions needed for etching.
The substrate holder, or chuck, secures the disk material during the process. It often includes temperature control features to prevent overheating, which could damage the substrate. Additionally, the vacuum system ensures a controlled atmosphere by removing impurities and maintaining low pressure. Each component plays a vital role in achieving the precision and efficiency that plasma etching demands.
How Plasma Etching Works
The role of plasma discharges in material removal.
Plasma discharges lie at the heart of the etching process. When gases are ionized within the plasma chamber, they form a mixture of ions, electrons, and neutral particles. These charged particles bombard the substrate surface, breaking molecular bonds and removing material layer by layer. This mechanism allows plasma etching to achieve unparalleled precision, making it ideal for crafting the intricate features found in disk technology.
The energy of the plasma discharge determines the etching rate and depth. High-energy ions enable deeper etching, while lower energy levels allow for more delicate material removal. This flexibility ensures that plasma etching can meet the diverse needs of disk production, from creating shallow patterns to forming deep, complex structures.
Chemical and physical interactions during the etching process.
Plasma etching relies on a combination of chemical and physical interactions to remove material. Chemically, reactive species in the plasma, such as radicals, react with the substrate material to form volatile byproducts. These byproducts are then evacuated from the chamber, leaving behind the desired pattern. Physically, ion bombardment enhances the etching process by breaking molecular bonds and increasing the reaction rate.
This dual-action approach ensures that plasma etching delivers both precision and efficiency. The chemical reactions provide selectivity, allowing manufacturers to target specific materials, while the physical interactions enhance the overall effectiveness of the process. Together, these mechanisms make plasma etching a powerful tool for shaping the future of disk production.
Techniques of Plasma Etching in Disk Production

Plasma etching disk technology relies on advanced techniques to achieve the precision and complexity required for modern disk manufacturing. Each method offers unique advantages, enabling manufacturers to meet specific production demands. This section explores three prominent techniques: the Bosch process, Reactive Ion Etching (RIE), and Inductively Coupled Plasma Reactive Ion Etching (ICP-RIE).
The Bosch Process
Overview and applications of the Bosch process in disk manufacturing.
The Bosch process stands out as a specialized plasma etching technique designed for creating high-aspect-ratio structures. This method alternates between etching and passivation steps, ensuring precise control over depth and sidewall profiles. In disk manufacturing, the Bosch process proves invaluable for producing intricate patterns and deep microstructures essential for advanced disk technologies.
Manufacturers often use the Bosch process to fabricate components requiring exceptional detail and uniformity. Its ability to create vertical sidewalls with minimal undercutting makes it ideal for applications demanding high precision. This technique has become a cornerstone in the production of microelectromechanical systems (MEMS) and semiconductor devices, which share similarities with disk production processes.
Advantages of the Bosch process for achieving deep and precise etching.
The Bosch process offers several advantages that make it indispensable in disk production. Its alternating etch-and-passivate approach ensures unparalleled control over etching depth and sidewall angles. This precision allows manufacturers to achieve consistent results, even for complex designs.
Another key benefit lies in its ability to produce high-aspect-ratio structures. By maintaining vertical sidewalls and minimizing material loss, the Bosch process enables the creation of intricate features without compromising structural integrity. This capability enhances the performance and reliability of disks, meeting the rigorous demands of modern technology.
Reactive Ion Etching (RIE)
How RIE combines chemical and physical etching for disk production.
Reactive Ion Etching (RIE) combines chemical reactions and physical ion bombardment to remove material from substrates. This dual-action approach allows RIE to deliver both selectivity and precision, making it a versatile tool in plasma etching disk production. By adjusting parameters such as gas composition and power levels, manufacturers can tailor the process to meet specific design requirements.
RIE excels at creating fine details and intricate patterns on disk surfaces. Its ability to target specific materials ensures that only the desired areas are etched, leaving other regions untouched. This selectivity reduces material waste and enhances production efficiency, making RIE a preferred choice for many disk manufacturing applications.
Applications of RIE in creating intricate disk structures.
RIE plays a crucial role in crafting the intricate structures found in modern disks. Its precision enables the formation of microscopic features essential for high-performance disk technologies. Manufacturers rely on RIE to produce components with tight tolerances and complex geometries, ensuring optimal functionality and durability.
This technique also supports the development of advanced disk designs, such as those used in optical and electronic applications. By combining chemical and physical etching, RIE provides the flexibility needed to meet the evolving demands of the disk industry. Its adaptability and effectiveness make it a cornerstone of plasma etching disk production.
Inductively Coupled Plasma Reactive Ion Etching (ICP-RIE)
Features and benefits of ICP-RIE in disk production.
Inductively Coupled Plasma Reactive Ion Etching (ICP-RIE) represents a cutting-edge advancement in plasma etching technology. This method generates high-density plasma, enabling faster etching rates and improved uniformity. In disk production, ICP-RIE offers superior selectivity and precision, making it ideal for complex tasks involving multiple materials or intricate patterns.
One of the standout features of ICP-RIE is its ability to achieve deep etching with minimal damage to surrounding areas. This capability ensures that manufacturers can create detailed designs without compromising the integrity of the substrate. Additionally, ICP-RIE supports high-aspect-ratio etching, allowing for the production of advanced disk structures with exceptional accuracy.
Comparison of ICP-RIE with other plasma etching techniques.
When compared to other techniques, ICP-RIE demonstrates clear advantages in terms of precision and efficiency. Unlike RIE, which operates at lower plasma densities, ICP-RIE generates a more concentrated plasma, resulting in faster etching and better control over material removal. This makes ICP-RIE particularly suited for demanding applications requiring deep silicon etching and precise pattern transfer.
The Bosch process, while effective for high-aspect-ratio structures, lacks the versatility of ICP-RIE. The latter’s ability to handle multiple materials and complex designs gives it an edge in modern disk production. By combining speed, accuracy, and adaptability, ICP-RIE sets a new standard for plasma etching disk technology.
Comparing Plasma Etching Methods for Disk Manufacturing
RIE vs. ICP-RIE
Differences in precision, efficiency, and control for disk production.
Reactive Ion Etching (RIE) and Inductively Coupled Plasma Reactive Ion Etching (ICP-RIE) represent two distinct approaches to plasma etching. Each method offers unique advantages, making them suitable for different manufacturing needs. RIE provides excellent selectivity by optimizing parameters such as gas composition, pressure, and RF power. This capability allows manufacturers to target specific materials with precision. However, RIE operates with lower plasma densities and ion energies, resulting in slower etching rates. This limitation may extend process times when deeper etching is required.
ICP-RIE, on the other hand, generates high-density plasma with greater ion energies. This feature enables faster etching rates and improved selectivity, particularly for intricate patterns or tasks involving multiple materials. ICP-RIE also excels in profile control, producing perfectly vertical features and maintaining high anisotropy. These qualities make it ideal for complex designs that demand both precision and efficiency. While RIE remains effective for simpler applications, ICP-RIE sets a higher standard for advanced disk production.
Suitability of each method for specific disk manufacturing needs.
The choice between RIE and ICP-RIE depends on the specific requirements of the disk manufacturing process. RIE suits applications where selectivity and material targeting are critical. Its simplicity and effectiveness make it a reliable option for tasks that do not demand high etching rates or extreme precision. For example, manufacturers may use RIE for creating shallow patterns or working with less intricate designs.
ICP-RIE, however, proves indispensable for more demanding applications. Its ability to achieve deep etching with minimal damage ensures the integrity of complex structures. This method supports high-aspect-ratio designs and delivers exceptional uniformity, even for challenging tasks. Manufacturers often rely on ICP-RIE for producing advanced disk components that require tight tolerances and intricate geometries. By offering superior control and adaptability, ICP-RIE meets the rigorous demands of modern disk technology.
Choosing the Right Plasma Etching Technique
Factors influencing the choice of plasma etching methods in disk production.
Selecting the appropriate plasma etching technique involves evaluating several factors. The complexity of the design plays a significant role. Intricate patterns or high-aspect-ratio structures often require the precision and efficiency of ICP-RIE. Conversely, simpler designs may benefit from the straightforward approach of RIE. Material composition also influences the decision. RIE’s excellent selectivity makes it suitable for processes involving specific materials, while ICP-RIE handles multiple materials with ease.
Production volume and time constraints further impact the choice. ICP-RIE’s faster etching rates make it ideal for high-volume manufacturing, where efficiency is paramount. RIE, with its slower rates, may suit smaller-scale operations or projects with less stringent timelines. Cost considerations also come into play. While ICP-RIE offers advanced capabilities, its systems and processes may involve higher expenses. Manufacturers must weigh these factors to determine the most suitable method for their needs.
Balancing cost, precision, and production efficiency.
Achieving the right balance between cost, precision, and efficiency is crucial in disk production. RIE provides a cost-effective solution for applications that do not require high-end capabilities. Its simplicity reduces operational expenses, making it an attractive option for budget-conscious manufacturers. However, its slower etching rates may impact overall production efficiency.
ICP-RIE, though more expensive, delivers unmatched precision and speed. Its ability to handle complex designs and achieve deep etching justifies the investment for advanced applications. Manufacturers can optimize costs by reserving ICP-RIE for tasks that demand its unique strengths while using RIE for less demanding processes. This strategic approach ensures that resources are allocated effectively, enabling manufacturers to meet production goals without compromising quality.
"The right plasma etching technique transforms disk production, balancing innovation with practicality to achieve excellence."
By understanding the strengths and limitations of RIE and ICP-RIE, manufacturers can make informed decisions. This knowledge empowers them to harness the full potential of plasma etching, driving progress in disk technology and meeting the ever-growing demands of the industry.
Plasma etching has redefined disk production by delivering unmatched precision and efficiency. Techniques such as the Bosch process, RIE, and ICP-RIE empower manufacturers to meet the intricate demands of modern disk technology. These methods enable the creation of advanced designs while maintaining exceptional quality. As the industry evolves toward three-dimensional architectures and atomic-scale precision, plasma etching continues to adapt, ensuring its relevance in shaping the future of disk manufacturing. By mastering these techniques, manufacturers can achieve superior performance and drive innovation in a rapidly advancing technological landscape.