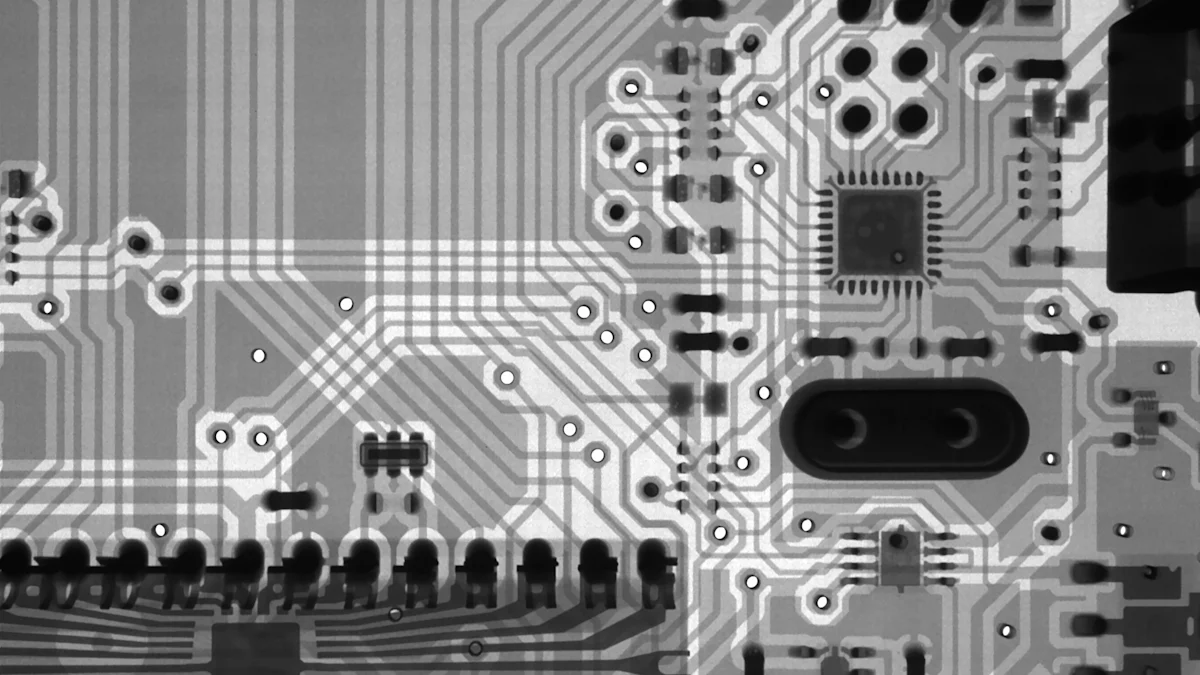
Wafer susceptor technology plays a pivotal role in semiconductor manufacturing, ensuring precision and reliability during critical processes. Recent breakthroughs have transformed this technology, introducing advanced materials and innovative designs that enhance performance. These advancements improve thermal conductivity, durability, and process stability, driving significant progress in the industry. By integrating cutting-edge techniques, manufacturers achieve higher efficiency and superior product quality. This evolution not only meets the growing demand for scalability but also sets new benchmarks for modern semiconductor production.
Key Takeaways
- Wafer susceptors are essential for maintaining the integrity of semiconductor wafers during high-temperature processes, ensuring precision and quality.
- Recent innovations, such as silicon carbide-coated susceptors, enhance thermal conductivity and durability, leading to improved production efficiency and reduced operational costs.
- Optimized designs and geometries of wafer susceptors promote uniform heat distribution, minimizing defects and enhancing overall yield in semiconductor manufacturing.
- The integration of automation and AI in wafer susceptor technology streamlines processes, reduces human error, and increases throughput, meeting the growing demand for high-quality semiconductors.
- Real-time monitoring systems in wafer susceptor technology help maintain critical process parameters, ensuring high precision and reducing waste during production.
- Adopting advanced materials and designs not only supports larger wafer sizes but also aligns with sustainability goals by lowering energy consumption and environmental impact.
- Investing in research and development is crucial for manufacturers to stay competitive and leverage the latest advancements in wafer susceptor technology.
Understanding Wafer Susceptor Technology
What is Wafer Susceptor Technology?
Definition and purpose in semiconductor manufacturing.
Wafer susceptor technology serves as a cornerstone in semiconductor manufacturing. A wafer susceptor acts as a platform that holds and supports semiconductor wafers during high-temperature processes. These processes are essential for creating the intricate structures found in modern electronic devices. By providing a stable and controlled environment, the susceptor ensures that wafers undergo precise transformations without compromising quality. This technology plays a critical role in maintaining the integrity of wafers, which directly impacts the performance of the final semiconductor products.
Overview of key processes like CVD and epitaxy.
Chemical Vapor Deposition (CVD) and epitaxy are two fundamental processes in semiconductor manufacturing where wafer susceptors prove indispensable. In CVD, thin films of material are deposited onto the wafer surface through chemical reactions at elevated temperatures. The susceptor ensures uniform heat distribution, which is vital for achieving consistent film thickness and quality. Epitaxy, on the other hand, involves growing a crystalline layer on the wafer to enhance its electrical properties. The susceptor provides the necessary thermal stability and precision required for this process. Both techniques rely heavily on the efficiency and reliability of wafer susceptor technology to meet the stringent demands of the semiconductor industry.
The Role of Wafer Susceptors in Semiconductor Processes
Supporting wafers during high-temperature processes.
Wafer susceptors are engineered to withstand extreme temperatures while securely holding wafers in place. During high-temperature processes, such as CVD or epitaxy, the susceptor prevents the wafer from warping or cracking under thermal stress. This support is crucial for maintaining the structural integrity of the wafer, especially as manufacturers push the boundaries with larger wafer sizes. By ensuring stability, the susceptor minimizes the risk of defects, which can lead to costly production errors.
Ensuring uniform heat distribution and process stability.
Uniform heat distribution is a key factor in achieving high-quality semiconductor wafers. Wafer susceptors excel in this area by evenly transferring heat across the wafer surface. This uniformity eliminates temperature gradients that could cause uneven material deposition or crystal growth. Additionally, the susceptor contributes to process stability by maintaining consistent thermal conditions throughout the manufacturing cycle. This stability enhances the overall efficiency of semiconductor production, resulting in higher yields and better-performing devices.
Key Innovations in Wafer Susceptor Technology

Material Improvements
Introduction of silicon carbide (SiC) coated graphite susceptors for enhanced thermal conductivity and durability.
The introduction of silicon carbide (SiC) coated graphite susceptors has revolutionized semiconductor manufacturing. These advanced materials offer exceptional thermal conductivity, ensuring even heat distribution during high-temperature processes. SiC coatings also enhance durability, allowing wafer susceptors to withstand prolonged exposure to extreme conditions without degradation. This innovation reduces the frequency of replacements, lowering operational costs and improving production efficiency. Manufacturers now rely on SiC-coated susceptors to achieve consistent results, even in demanding applications.
Development of advanced materials for extreme environments and high-performance applications.
The demand for high-performance semiconductor devices has driven the development of advanced materials for wafer susceptors. Researchers have engineered materials capable of withstanding extreme environments, such as ultra-high temperatures and corrosive atmospheres. These materials maintain structural integrity and thermal stability, ensuring reliable performance in cutting-edge applications. By adopting these innovations, manufacturers can produce semiconductors with superior quality and functionality, meeting the needs of industries like aerospace, telecommunications, and renewable energy.
Design Enhancements
Optimized geometries for better heat uniformity and reduced thermal stress.
Innovative design enhancements have transformed wafer susceptor technology. Optimized geometries now ensure better heat uniformity across the wafer surface, eliminating temperature variations that could compromise product quality. These designs also minimize thermal stress, reducing the risk of wafer cracking or warping during processing. By implementing these improvements, manufacturers achieve higher yields and fewer defects, enhancing overall production efficiency.
Use of removable wafer susceptors to improve batch processing and thermal management.
Removable wafer susceptors represent a significant leap forward in design innovation. These susceptors simplify batch processing by allowing quick and easy replacement between production cycles. This feature improves thermal management, as removable designs enable precise control over temperature conditions. Manufacturers benefit from reduced downtime and increased flexibility, making this advancement a valuable asset in modern semiconductor production.
Integration with Modern Manufacturing Techniques
Compatibility with automation and AI-driven process controls.
The integration of wafer susceptor technology with automation and AI-driven process controls has streamlined semiconductor manufacturing. Automated systems now handle wafer placement and retrieval with precision, reducing human error and increasing throughput. AI algorithms monitor and adjust process parameters in real time, ensuring optimal conditions for every production cycle. This compatibility enhances efficiency and consistency, enabling manufacturers to meet the growing demand for high-quality semiconductors.
Real-time monitoring systems for precision and defect reduction.
Real-time monitoring systems have become an essential component of wafer susceptor technology. These systems track critical variables, such as temperature and pressure, throughout the manufacturing process. By identifying deviations immediately, they help prevent defects and maintain product quality. Manufacturers leverage this technology to achieve greater precision, reduce waste, and optimize resource utilization. Real-time monitoring ensures that every wafer meets the stringent standards required in today’s competitive market.
Impact on Semiconductor Manufacturing
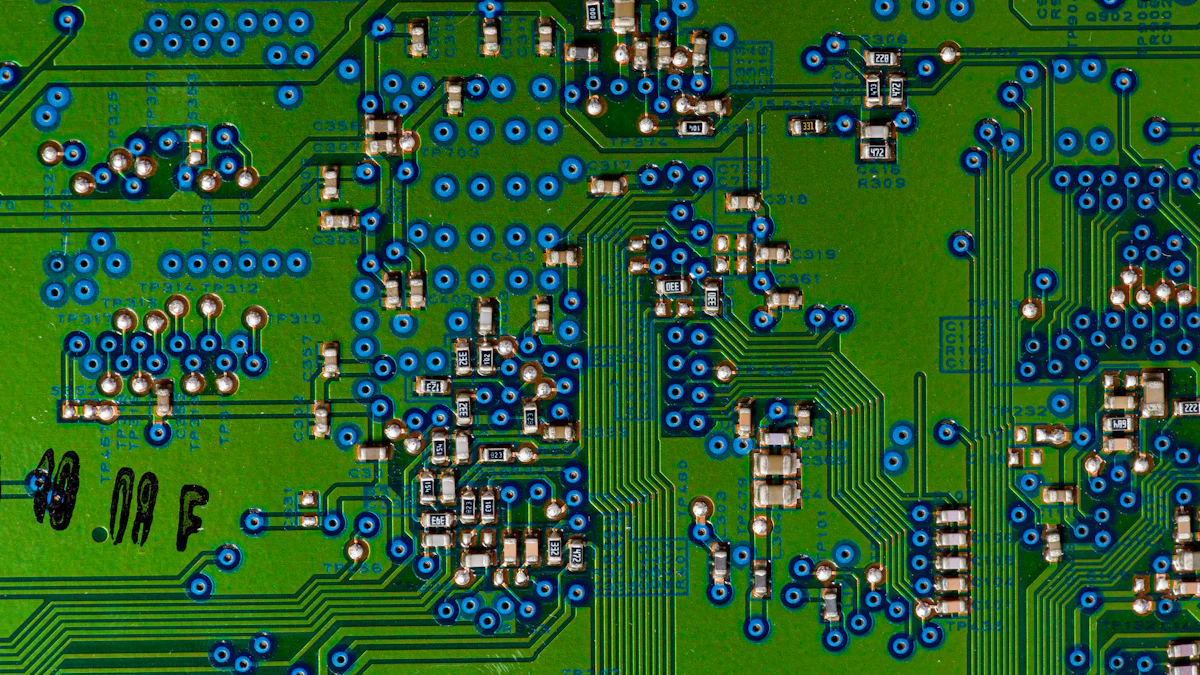
Improved Efficiency and Yield
Faster processing times and reduced defects through optimized rotational speeds in CVD processes.
Optimized rotational speeds in Chemical Vapor Deposition (CVD) processes have significantly improved manufacturing efficiency. By fine-tuning these speeds, manufacturers achieve faster processing times, which directly enhances production throughput. This optimization also minimizes defects by ensuring uniform material deposition across the wafer surface. The result is a higher yield of high-quality semiconductor wafers, meeting the rigorous standards of modern technology.
Enhanced crystal quality for larger wafer sizes, such as 150 mm Indium Phosphide wafers.
Advancements in wafer susceptor technology have enabled the production of larger wafer sizes, such as 150 mm Indium Phosphide wafers, with superior crystal quality. These innovations ensure precise thermal management and uniform heat distribution, which are critical for maintaining crystal integrity during growth processes. High-quality crystals improve the performance and reliability of semiconductors, making them ideal for advanced applications in telecommunications and optoelectronics.
Enhanced Scalability
Support for next-generation semiconductor technologies and larger wafer sizes.
Wafer susceptor advancements have paved the way for next-generation semiconductor technologies. These innovations support the transition to larger wafer sizes, which are essential for scaling up production to meet global demand. By accommodating these larger wafers, manufacturers can produce more chips per batch, increasing overall output without compromising quality. This scalability positions the industry to tackle future challenges and opportunities.
Adaptability to evolving industry demands.
The adaptability of modern wafer susceptor designs ensures compatibility with evolving industry requirements. As semiconductor technologies advance, manufacturers face new challenges, such as higher processing temperatures and more complex wafer geometries. Innovative susceptor materials and designs address these needs, providing the flexibility required to stay ahead in a competitive market. This adaptability ensures that manufacturers can respond quickly to technological shifts and customer demands.
Cost and Sustainability Benefits
Lower operational costs through longer susceptor lifespans and energy-efficient designs.
Modern wafer susceptor technology reduces operational costs by extending the lifespan of susceptors. Advanced materials, such as silicon carbide coatings, resist wear and degradation, minimizing the need for frequent replacements. Energy-efficient designs further lower costs by optimizing thermal conductivity, which reduces energy consumption during high-temperature processes. These cost-saving measures enhance profitability while maintaining production efficiency.
Reduced environmental impact with advanced materials and coatings.
Sustainability has become a priority in semiconductor manufacturing, and wafer susceptor innovations contribute to this goal. Advanced materials and coatings reduce waste by improving durability and performance. Energy-efficient designs lower the carbon footprint of manufacturing processes. These eco-friendly advancements align with global efforts to create a more sustainable and environmentally responsible semiconductor industry.
Future Trends and Challenges
Emerging Trends in Wafer Susceptor Technology
Exploration of new materials for extreme environments and high-temperature applications.
The semiconductor industry continues to push boundaries, demanding materials that can endure extreme conditions. Researchers are exploring innovative materials capable of withstanding ultra-high temperatures and corrosive environments. These materials promise to enhance the durability and performance of wafer susceptors, especially in cutting-edge applications like aerospace and advanced telecommunications. Manufacturers adopting these materials can achieve greater reliability and efficiency, ensuring their products meet the rigorous demands of next-generation technologies.
"The future of wafer susceptor technology lies in materials that can thrive where traditional options fail," experts suggest. This shift will redefine the limits of semiconductor manufacturing.
Integration with Industry 4.0 technologies for smart manufacturing and process optimization.
Industry 4.0 technologies are revolutionizing wafer susceptor technology. Automation, artificial intelligence (AI), and the Internet of Things (IoT) are enabling smarter manufacturing processes. AI-driven systems now optimize production parameters in real time, ensuring precision and reducing defects. IoT-enabled sensors provide continuous monitoring, offering valuable insights into performance and maintenance needs. By integrating these technologies, manufacturers can streamline operations, reduce waste, and maximize productivity. Companies embracing this trend position themselves as leaders in the era of smart manufacturing.
Challenges in Adoption and Development
High costs of R&D and sourcing advanced materials.
Developing advanced wafer susceptor technology requires significant investment in research and development (R&D). The high costs associated with sourcing innovative materials, such as silicon carbide or other exotic compounds, present a major challenge. Smaller manufacturers may struggle to allocate resources for these advancements, potentially widening the gap between industry leaders and smaller players. However, companies that prioritize R&D can gain a competitive edge by delivering superior products that meet evolving market demands.
"Innovation comes at a price, but the rewards far outweigh the initial investment," industry leaders emphasize. Businesses must weigh short-term costs against long-term benefits.
Ensuring compatibility with existing systems while driving innovation.
Balancing innovation with compatibility remains a critical hurdle. New wafer susceptor designs and materials must integrate seamlessly with existing manufacturing systems. Retrofitting older equipment to accommodate advanced susceptors can be costly and time-consuming. Manufacturers must carefully evaluate the trade-offs between adopting cutting-edge technology and maintaining operational continuity. Those who successfully navigate this challenge can unlock new levels of efficiency and scalability without disrupting their production lines.
The path forward requires a strategic approach. Companies must invest in solutions that align with their long-term goals while addressing immediate operational needs. By doing so, they can overcome these challenges and remain competitive in an ever-evolving industry.
Wafer susceptor technology remains a cornerstone of semiconductor manufacturing, driving advancements in efficiency, scalability, and sustainability. Recent innovations, such as enhanced materials, optimized designs, and integration with modern techniques, have redefined industry standards. These breakthroughs enable manufacturers to produce high-quality semiconductors while reducing costs and environmental impact. Continued investment in research and development will address emerging challenges and unlock new opportunities for growth. Industry professionals must stay informed about these advancements to maintain a competitive edge and contribute to the future of semiconductor innovation.