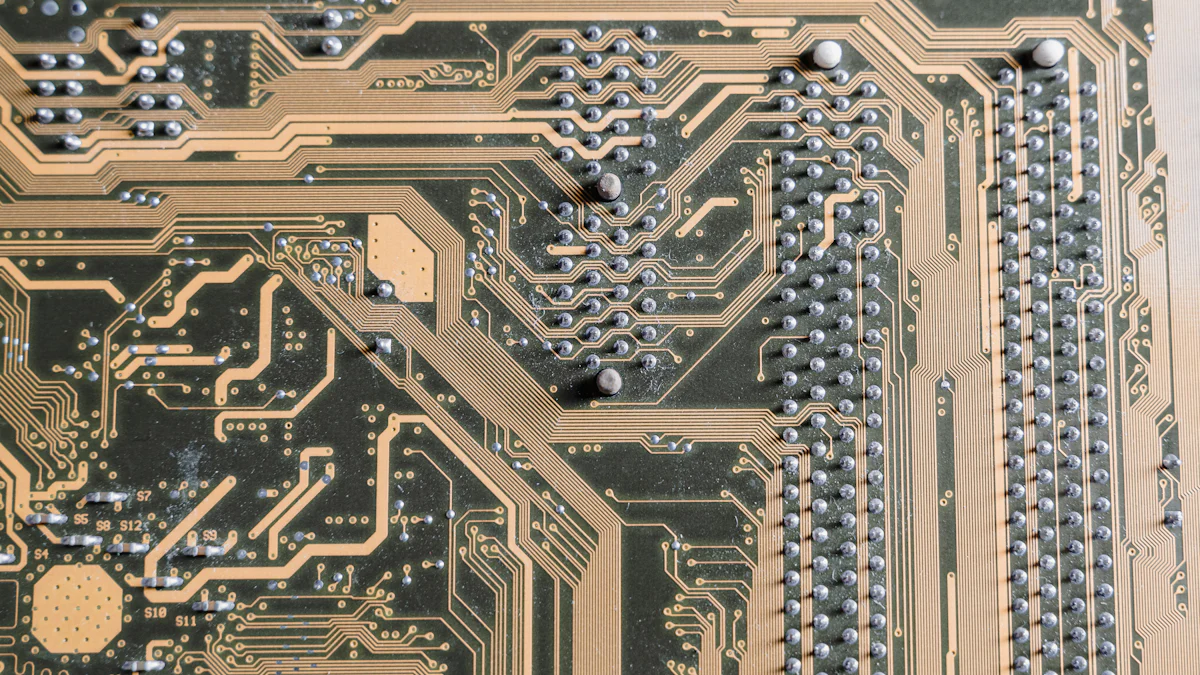
Gas inlet rings play a critical role in semiconductor manufacturing by ensuring precise gas delivery within the equipment. Their design directly impacts the efficiency of gas flow, which influences the quality of the final product. Properly selected inlet rings prevent leaks and contamination, maintaining the integrity of the manufacturing process. For instance, studies highlight how the positioning of gas inlets can enhance cluster flux under consistent pressure and power conditions. Additionally, high-purity inlet rings minimize risks of chemical reactions, ensuring compatibility with specific gases. These factors make the choice of inlet rings essential for achieving optimal performance and reliability.
Key Takeaways
- Choose gas inlet rings based on material compatibility to prevent chemical reactions and ensure system integrity.
- Evaluate performance specifications, including temperature and pressure ratings, to ensure reliability under operational conditions.
- Prioritize durability and longevity in gas inlet rings to reduce maintenance costs and minimize production downtime.
- Consider the total cost of ownership, including installation and maintenance, to achieve cost-effectiveness in your selection.
- Consult with experts or manufacturers for tailored recommendations that meet specific operational needs.
- Thoroughly review product specifications and certifications to ensure quality and compliance with industry standards.
- Test and validate gas inlet rings in controlled environments before full implementation to ensure optimal performance.
Understanding Gas Inlet Rings
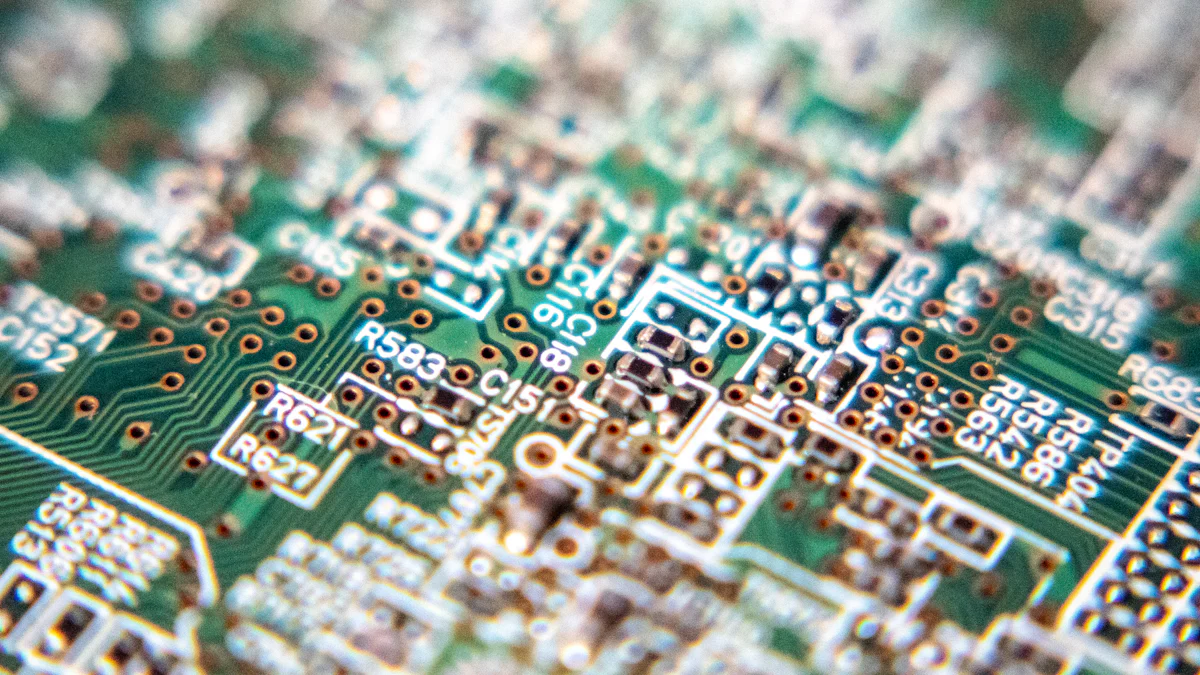
What Are Gas Inlet Rings?
Gas inlet rings are essential components in various industrial applications, particularly in semiconductor manufacturing. These rings regulate the flow of gases into equipment, ensuring precision and consistency. By maintaining a controlled environment, they help optimize processes that rely on specific gas compositions.
In semiconductor equipment, gas inlet rings often serve as seals or connectors within gas delivery systems. For example, Agilent Liner O-Rings provide a gas-tight seal between the inlet liner and weldment, preventing leaks and isolating gas flow paths. This functionality is critical for maintaining the purity of gases used in sensitive manufacturing processes. Similarly, Buna or Nitrile O-Rings are widely used due to their ability to withstand extreme temperatures and their compatibility with oil and gas applications.
The design and material of gas inlet rings vary depending on their intended use. High-purity applications, such as those in semiconductor manufacturing, often require specialized coatings or materials to prevent contamination. For instance, Agilent’s patented plasma-coating process enhances the durability of its O-rings, ensuring better performance under demanding conditions. These features highlight the importance of selecting the right gas inlet rings for specific applications.
The Role of Gas Inlet Rings in Semiconductor Equipment
Gas inlet rings play a pivotal role in semiconductor equipment by ensuring the precise delivery of gases required for manufacturing processes. Semiconductor production involves intricate steps, such as etching and deposition, which demand exact gas flow rates and compositions. Gas inlet rings help achieve this precision by creating airtight seals and regulating gas distribution.
In addition to controlling gas flow, these rings prevent contamination and leaks. For example, Fuel Inlet Box Rings, commonly used in fuel systems, demonstrate how effective sealing can maintain an airtight environment. In semiconductor equipment, similar principles apply. High-quality inlet rings, such as those designed for high-purity applications, minimize the risk of chemical reactions between gases and system components. This ensures the integrity of the manufacturing process and the quality of the final product.
Durability and compatibility are also crucial factors. Rings like the Agilent Inlet Liner O-Ring are engineered to withstand high temperatures and pressures, making them suitable for demanding semiconductor applications. Their ability to maintain performance under such conditions underscores their importance in achieving reliable and efficient operations.
By understanding the function and significance of gas inlet rings, manufacturers can make informed decisions when selecting components for their equipment. This knowledge ensures optimal performance, reduced downtime, and improved product quality.
Key Factors to Consider When Selecting Gas Inlet Rings
Material Compatibility
Material compatibility plays a vital role in the selection of gas inlet rings. Manufacturers must ensure that the materials used in the rings can withstand the specific gases involved in semiconductor processes. Certain gases may react chemically with incompatible materials, leading to contamination or system failure. For example, corrosive gases like chlorine require rings made from corrosion-resistant materials such as fluoropolymers or stainless steel.
High-purity applications demand materials that minimize the risk of chemical reactions. Rings designed for these applications often feature specialized coatings or are constructed from inert materials. By selecting compatible materials, manufacturers can maintain the integrity of their systems and ensure consistent performance.
Performance Under Specific Conditions
Gas inlet rings must perform reliably under the specific conditions of semiconductor manufacturing. These conditions often include high temperatures, varying pressures, and exposure to reactive gases. Rings that fail to meet these demands can compromise the efficiency of the equipment and lead to costly downtime.
Temperature and pressure ratings are critical factors to evaluate. Rings designed for high-temperature environments must resist thermal degradation. Similarly, those used in high-pressure systems should maintain their structural integrity to prevent leaks. Manufacturers should review product specifications to confirm that the rings meet the operational requirements of their equipment.
Durability and Longevity
Durability and longevity are essential for reducing maintenance costs and ensuring uninterrupted operations. Gas inlet rings must endure prolonged exposure to harsh conditions without losing their effectiveness. Frequent replacements not only increase expenses but also disrupt production schedules.
High-quality rings often feature enhanced durability through advanced manufacturing techniques. For instance, some rings undergo plasma coating to improve wear resistance. Selecting durable rings reduces the likelihood of failures and extends the lifespan of the equipment. Manufacturers should prioritize products with proven reliability to achieve long-term benefits.
Cost-Effectiveness
Cost-effectiveness remains a crucial factor when selecting gas inlet rings for semiconductor equipment. Manufacturers must balance quality and affordability to ensure optimal performance without exceeding budget constraints. High-quality inlet rings may have a higher upfront cost, but their durability and reliability often result in long-term savings by reducing maintenance expenses and minimizing downtime.
Evaluating the total cost of ownership provides a clearer picture of cost-effectiveness. This approach considers not only the purchase price but also factors such as installation, maintenance, and replacement costs. For example, durable inlet rings with extended lifespans reduce the frequency of replacements, leading to lower operational costs over time.
Bulk purchasing can also enhance cost-effectiveness. Many suppliers offer discounts for larger orders, which can significantly reduce the per-unit cost. However, manufacturers should ensure that the quality of the rings remains consistent across all units in the order.
Another strategy involves consulting with suppliers to explore cost-effective options tailored to specific applications. Suppliers often recommend products that meet performance requirements while staying within budget. This collaboration ensures that manufacturers achieve the best value for their investment.
By prioritizing cost-effectiveness, manufacturers can optimize their operations without compromising on quality or performance. Selecting the right inlet rings not only enhances efficiency but also contributes to the overall profitability of semiconductor manufacturing processes.
Common Types of Gas Inlet Rings and Their Applications
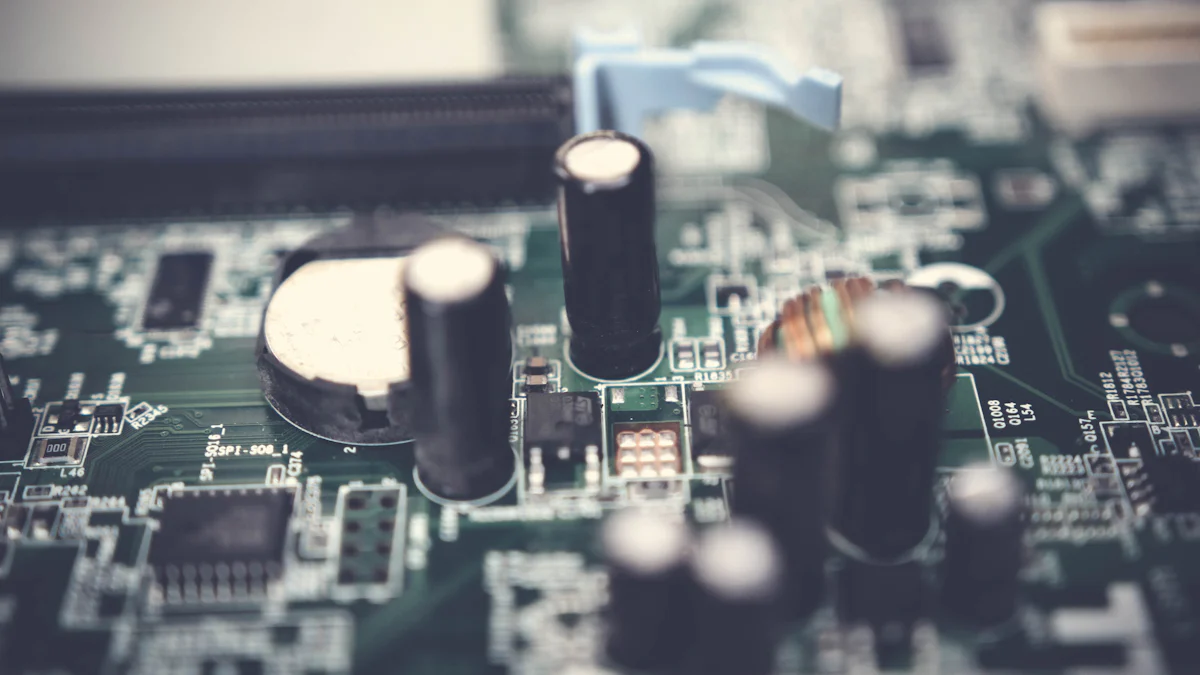
Standard and Specialized Gas Inlet Rings
Gas inlet rings come in two primary categories: standard and specialized. Standard gas inlet rings are designed for general applications and provide reliable performance under typical operating conditions. These rings often use durable materials like stainless steel or nitrile, which can withstand moderate temperatures and pressures. Their straightforward design makes them a cost-effective choice for many semiconductor manufacturing processes.
Specialized gas inlet rings, on the other hand, cater to unique or demanding requirements. These rings are engineered with advanced materials and coatings to handle extreme conditions, such as high-purity environments or exposure to corrosive gases. For instance, fluoropolymer-coated rings resist chemical reactions, ensuring compatibility with reactive gases like chlorine. Similarly, plasma-coated rings enhance durability, making them suitable for high-temperature and high-pressure applications.
The choice between standard and specialized rings depends on the specific needs of the equipment. While standard rings may suffice for less demanding tasks, specialized rings offer superior performance and longevity in challenging environments. Manufacturers must evaluate their operational requirements to determine the most appropriate option.
Applications in Semiconductor Manufacturing Processes
Gas inlet rings play a vital role in various semiconductor manufacturing processes. These processes often involve precise gas delivery to achieve desired outcomes, such as etching, deposition, or oxidation. In each case, the performance of the inlet rings directly impacts the quality and efficiency of the operation.
In etching processes, gas inlet rings ensure the controlled delivery of reactive gases that remove material from the wafer surface. High-purity rings prevent contamination, maintaining the integrity of the etched patterns. During deposition, inlet rings regulate the flow of precursor gases, enabling uniform layer formation on the wafer. Rings designed for high-temperature applications excel in this context, as deposition often occurs under elevated thermal conditions.
Oxidation processes also benefit from the use of high-quality gas inlet rings. These rings maintain airtight seals, ensuring consistent gas flow and preventing leaks. This precision is crucial for achieving uniform oxidation layers, which enhance the electrical properties of semiconductor devices.
By selecting the right gas inlet rings, manufacturers can optimize these processes and improve overall production efficiency. The durability and compatibility of the rings contribute to reduced downtime and lower maintenance costs, further enhancing the value they bring to semiconductor manufacturing.
Actionable Tips for Selecting the Best Gas Inlet Rings
Consult with Experts or Manufacturers
Consulting with experts or manufacturers ensures that the selected gas inlet rings meet the specific requirements of semiconductor equipment. Professionals in the field possess in-depth knowledge about material compatibility, performance under extreme conditions, and durability. Their insights help manufacturers avoid costly mistakes and select components that align with operational needs.
Manufacturers like Agilent provide detailed guidance on their products, such as the Agilent Liner O-Rings. These O-rings are available in fluorocarbon and graphite variants, catering to different temperature ranges and applications. By discussing these options with suppliers, manufacturers can identify the most suitable choice for their equipment. Additionally, experts often recommend solutions tailored to unique challenges, such as high-purity environments or exposure to reactive gases.
Engaging with professionals also facilitates access to technical support and product customization. For instance, suppliers may offer specialized coatings or materials to enhance the performance of inlet rings in demanding conditions. This collaboration ensures that the selected components deliver optimal results in semiconductor manufacturing processes.
Review Product Specifications and Certifications
Thoroughly reviewing product specifications and certifications guarantees the quality and reliability of gas inlet rings. Specifications provide critical information about material composition, temperature and pressure ratings, and compatibility with specific gases. Certifications, on the other hand, validate that the products meet industry standards and regulatory requirements.
For example, Agilent Gas Chromatography Inlet Liners and O-Rings include detailed specifications that highlight their ability to form proper seals and withstand high temperatures. These features ensure consistent performance in gas chromatography applications, which share similarities with semiconductor manufacturing processes. Similarly, Buna or Nitrile O-Rings are known for their versatility and durability, making them a reliable choice for various industrial applications.
Manufacturers should prioritize products with certifications that confirm their suitability for high-purity applications. These certifications minimize the risk of contamination and ensure compliance with stringent industry standards. By carefully evaluating product details, manufacturers can make informed decisions that enhance the efficiency and reliability of their equipment.
Test and Validate Before Full Implementation
Testing and validating gas inlet rings before full implementation reduces the risk of operational failures and ensures compatibility with existing systems. This step involves installing the rings in a controlled environment and monitoring their performance under actual operating conditions. Key metrics to evaluate include sealing effectiveness, resistance to wear, and stability under varying temperatures and pressures.
For instance, testing the Agilent Inlet Liner O-Ring in high-temperature environments confirms its ability to maintain a gas-tight seal without degradation. Similarly, validating the performance of Buna or Nitrile O-Rings in compressed natural gas applications ensures their reliability in demanding scenarios. These tests provide valuable insights into the durability and functionality of the rings, enabling manufacturers to address potential issues before large-scale deployment.
Validation also includes assessing the rings’ impact on overall system performance. For example, manufacturers can measure gas flow rates and contamination levels to determine whether the selected rings meet operational requirements. This proactive approach minimizes downtime and enhances the efficiency of semiconductor manufacturing processes.
By following these actionable tips, manufacturers can confidently select the best gas inlet rings for their equipment. Consulting with experts, reviewing product details, and conducting thorough testing ensure that the chosen components deliver optimal performance and long-term value.
Selecting the right gas inlet rings is crucial for maintaining the efficiency and reliability of semiconductor equipment. Key factors such as material compatibility, performance under specific conditions, durability, and cost-effectiveness play a significant role in ensuring optimal results. Manufacturers should prioritize informed decisions by consulting with experts and reviewing product specifications. For instance, Agilent’s patented plasma-coating process enhances the durability of inlet rings, ensuring long-term performance in demanding environments. To optimize manufacturing processes, readers are encouraged to reach out to trusted suppliers or conduct further research to identify the best solutions for their needs.