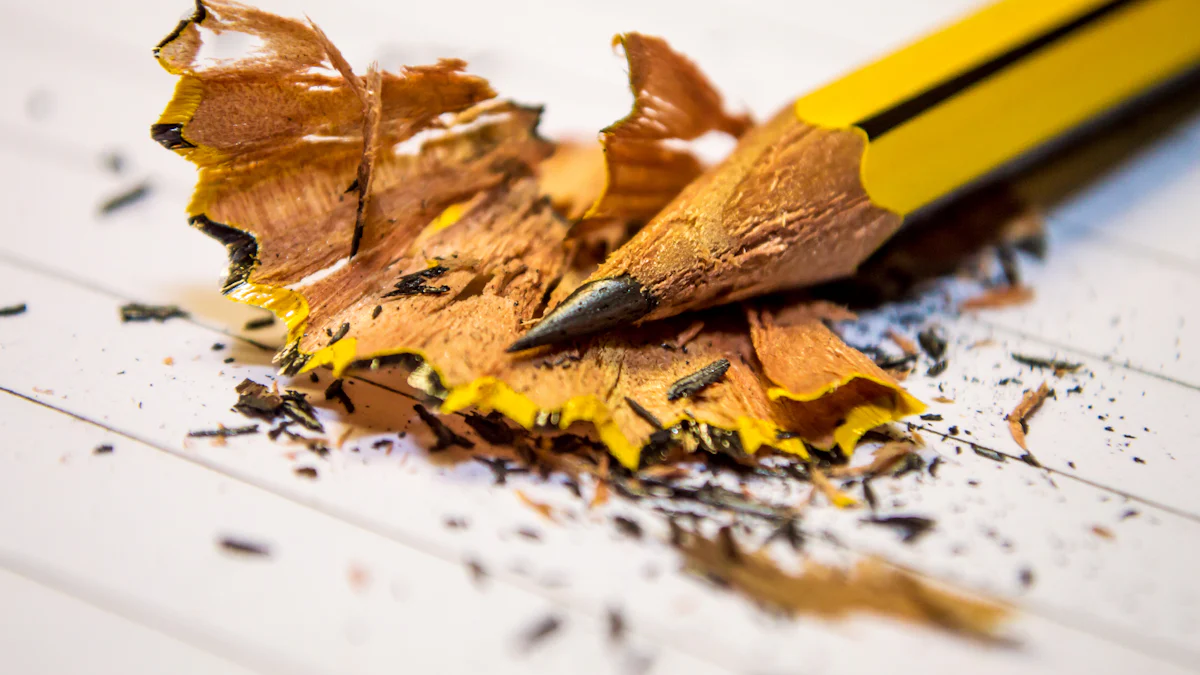
Graphite stands out as a vital material in semiconductor manufacturing due to its exceptional properties. You benefit from its high precision, which ensures accuracy in critical processes. Its ability to resist extreme temperatures and maintain stability under harsh conditions makes it indispensable. Graphite also offers high strength and chemical resistance, reducing material loss and enhancing efficiency. In demanding environments, its durability ensures reliable performance. Applications like crystal growth, epitaxy, ion implantation, and thermal insulation rely on graphite’s unique qualities. For instance, the Graphite Bipolar Plate plays a key role in supporting advanced semiconductor production.
Key Takeaways
- Graphite’s high precision and temperature resistance make it crucial for maintaining accuracy in semiconductor manufacturing processes.
- Customizable graphite components with low ash content (less than 5ppm) minimize contamination risks, ensuring the integrity of semiconductor materials.
- Graphite disks are essential in the epitaxial process, providing stability and uniformity that directly impact the performance of semiconductor devices.
- High-purity graphite components enhance ion implantation accuracy, allowing for precise ion placement critical for high-performance semiconductor devices.
- Graphite insulation materials help maintain thermal control, reducing energy loss and improving overall production efficiency.
- Durable graphite components, such as carbon-carbon trays and bipolar plates, support high-temperature processes, ensuring reliability and quality in semiconductor production.
- Incorporating alternative materials like ceramic and tungsten alongside graphite can enhance the efficiency and precision of semiconductor manufacturing.
The Role of Graphite in Semiconductor Crystal Growth
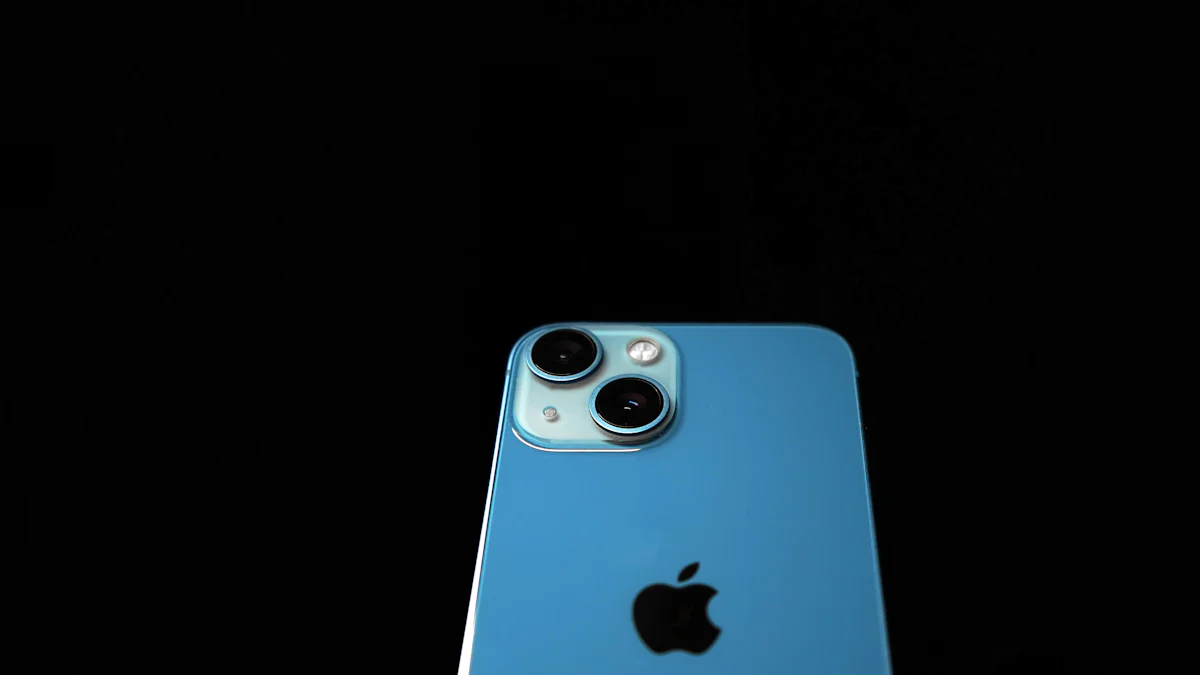
Graphite Components for Crystal Growth
Heaters, crucibles, and insulation cylinders for high-temperature environments.
You rely on graphite heaters, crucibles, and insulation cylinders to handle extreme temperatures during crystal growth. These components maintain structural integrity even in the most demanding thermal conditions. Their ability to withstand high heat ensures consistent performance, which is critical for producing high-quality semiconductor crystals. Graphite’s thermal conductivity also helps distribute heat evenly, reducing the risk of defects in the crystal structure.
Guide cylinders, electrodes, and crucible holders for corrosive conditions.
In corrosive environments, graphite guide cylinders, electrodes, and crucible holders provide unmatched durability. These components resist chemical reactions that could compromise their functionality. You benefit from their long service life, which minimizes the need for frequent replacements. This reliability ensures uninterrupted operations, saving both time and resources in semiconductor manufacturing.
Customization and Purity Standards
Customizable graphite parts with ash content less than 5ppm.
Graphite parts can be tailored to meet your specific production needs. Manufacturers offer customization options to ensure compatibility with your equipment and processes. High-purity graphite, with ash content below 5ppm, guarantees minimal contamination during crystal growth. This level of purity is essential for maintaining the integrity of semiconductor materials.
Ensuring durability and performance in extreme conditions.
Graphite’s exceptional durability allows it to perform reliably under extreme conditions. Whether exposed to high temperatures or corrosive chemicals, it retains its structural and functional properties. You can trust graphite components to deliver consistent results, ensuring the efficiency and quality of your semiconductor production processes.
Graphite Disks in the Epitaxial Process
Importance of Graphite Disks
Ensuring the quality of the wafer’s epitaxial layer.
Graphite disks play a critical role in the epitaxial process. You rely on these disks to ensure the wafer’s epitaxial layer meets the highest quality standards. The epitaxial layer directly impacts the performance of semiconductor devices. Any inconsistency or defect in this layer can compromise the functionality of the final product. Graphite disks provide the precision and stability needed to maintain uniformity during this process. Their ability to support consistent deposition ensures that you achieve optimal results in wafer production.
High-purity graphite with uniform coatings for optimal performance.
High-purity graphite is essential for epitaxial processes. You benefit from its minimal impurity levels, which reduce the risk of contamination. Manufacturers often apply uniform coatings to graphite disks, enhancing their performance. These coatings improve thermal conductivity and chemical resistance, ensuring reliable operation under demanding conditions. With high-purity graphite disks, you can achieve superior results while maintaining the integrity of your semiconductor materials.
Key Features of Graphite Disks
Chemical resistance and thermal stability.
Graphite disks offer exceptional chemical resistance. They withstand exposure to reactive gases and chemicals used in the epitaxial process. This resistance prevents degradation, ensuring the disks maintain their functionality over time. Thermal stability is another key feature. Graphite disks perform reliably under extreme temperatures, which are common in semiconductor manufacturing. Their ability to endure these conditions ensures consistent and efficient operations.
Long service life and consistent performance.
Durability is a hallmark of graphite disks. You can depend on them for a long service life, reducing the need for frequent replacements. This longevity translates to cost savings and uninterrupted production. Graphite disks also deliver consistent performance, which is crucial for maintaining the quality of semiconductor wafers. Their reliability ensures that your manufacturing processes run smoothly, helping you meet production goals with confidence.
High-Purity Graphite in Ion Implantation
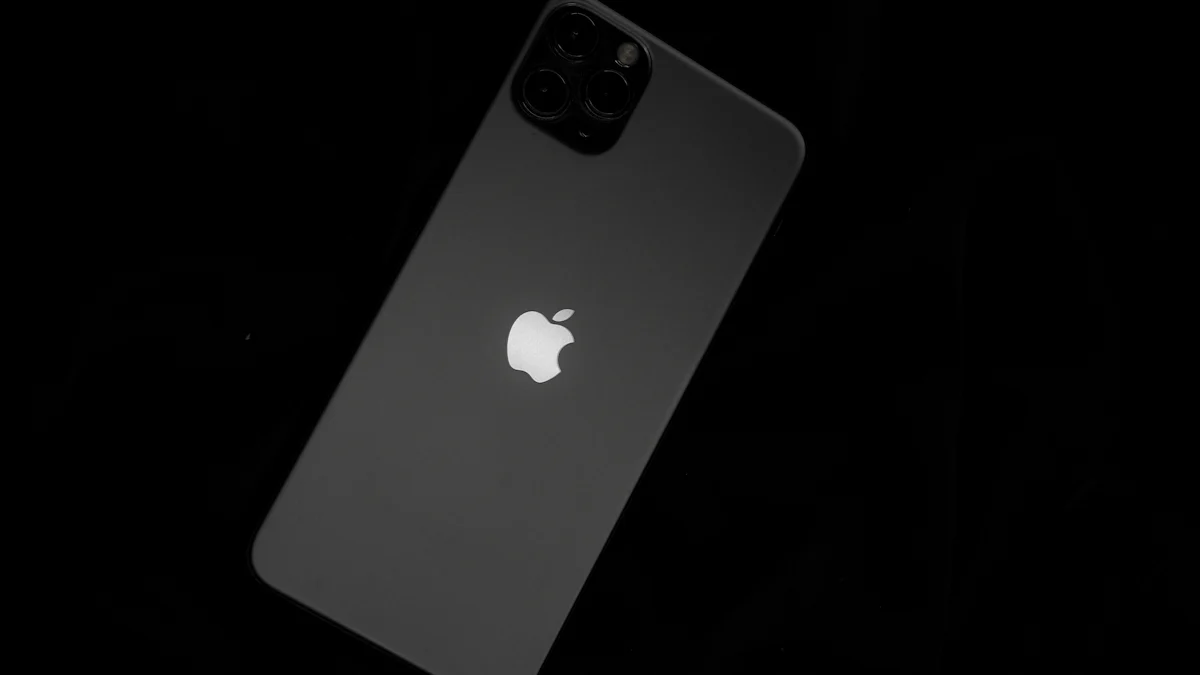
Graphite Components for Ion Implantation
Flight tubes, slits, electrodes, and beam terminators.
You rely on high-purity graphite components like flight tubes, slits, electrodes, and beam terminators to ensure precision in ion implantation. These parts handle the intense demands of this process, maintaining their structural integrity under high-energy ion beams. Graphite’s exceptional thermal conductivity and resistance to wear make it ideal for these applications. By using these components, you achieve accurate ion placement, which is critical for producing high-performance semiconductor devices.
Compatibility with equipment models like Eaton, Azcelis, and Varian.
Graphite components are designed to be compatible with leading ion implantation equipment, including models from Eaton, Azcelis, and Varian. This compatibility ensures seamless integration into your existing systems. You benefit from reduced downtime and enhanced operational efficiency. Manufacturers tailor graphite parts to meet the specifications of these machines, providing you with reliable performance and consistent results during ion implantation.
Additional Materials and Applications
Use of ceramic, tungsten, molybdenum, and aluminum products.
In addition to graphite, you can incorporate materials like ceramic, tungsten, molybdenum, and aluminum into ion implantation processes. Each material offers unique properties that complement graphite’s capabilities. For example:
- Ceramic provides excellent electrical insulation.
- Tungsten and molybdenum deliver superior strength and heat resistance.
- Aluminum contributes lightweight durability.
By combining these materials with graphite, you enhance the overall efficiency and precision of your ion implantation systems.
Coated parts for enhanced performance in ion implantation.
Coated graphite parts elevate the performance of your ion implantation equipment. Manufacturers apply specialized coatings to improve chemical resistance, reduce wear, and extend the lifespan of these components. These coatings also minimize contamination risks, ensuring the purity of your semiconductor materials. With coated graphite parts, you achieve greater reliability and maintain the high standards required for advanced semiconductor production.
Graphite Insulation Materials and Related Applications
Thermal Insulation in Semiconductor Production
Graphite hard felt, soft felt, foil, paper, and rope for insulation.
You rely on graphite insulation materials to maintain precise thermal control during semiconductor production. These materials, including hard felt, soft felt, foil, paper, and rope, provide excellent thermal insulation. Each type serves a specific purpose, ensuring that your processes remain efficient and consistent. Hard felt and soft felt offer superior heat resistance, making them ideal for high-temperature environments. Graphite foil and paper deliver flexibility and adaptability, allowing you to use them in various applications. Rope insulation adds durability and strength, ensuring reliable performance in demanding conditions.
Graphite insulation materials also help reduce energy loss. Their ability to withstand extreme temperatures ensures that heat remains contained within the production system. This efficiency not only improves the quality of your semiconductor products but also reduces operational costs. By incorporating these materials, you enhance the overall performance of your manufacturing processes.
Customizable sizes to meet specific production needs.
Manufacturers offer graphite insulation materials in customizable sizes to suit your unique requirements. Whether you need large sheets for extensive coverage or smaller pieces for precision applications, you can find the right fit. Customization ensures that the insulation materials integrate seamlessly into your existing systems. This adaptability allows you to optimize your production setup, improving both efficiency and output quality.
Custom sizes also minimize material waste. By tailoring the insulation to your exact specifications, you avoid unnecessary cuts and adjustments. This precision saves time and resources, enabling you to focus on achieving your production goals. With customizable graphite insulation materials, you gain the flexibility to meet the demands of modern semiconductor manufacturing.
Carbon-Carbon Trays and Graphite Bipolar Plate Applications
Applications in solar silicon cell production.
Carbon-carbon trays and graphite bipolar plates play a vital role in solar silicon cell production. You depend on these components to handle the high temperatures and chemical reactions involved in the process. Carbon-carbon trays provide structural support, ensuring that silicon cells remain stable during production. Their lightweight yet durable design makes them an excellent choice for demanding applications.
Graphite bipolar plates contribute to the efficiency of solar cell manufacturing. Their high thermal conductivity and chemical resistance ensure consistent performance. These plates also help maintain the purity of the silicon cells, reducing the risk of contamination. By using carbon-carbon trays and graphite bipolar plates, you achieve superior results in solar silicon cell production.
Working principles in furnace tube processing.
In furnace tube processing, carbon-carbon trays and graphite bipolar plates ensure reliable and efficient operations. You rely on these components to withstand the extreme conditions inside the furnace. Carbon-carbon trays provide stability, preventing deformation under high temperatures. Their robust construction ensures long service life, reducing the need for frequent replacements.
Graphite bipolar plates enhance the performance of furnace tube systems. Their ability to conduct heat evenly ensures uniform processing, which is critical for producing high-quality semiconductor materials. These plates also resist chemical reactions, maintaining their integrity over time. By incorporating carbon-carbon trays and graphite bipolar plates into your furnace tube processing, you improve both efficiency and product quality.
Graphite plays a vital role in semiconductor manufacturing due to its unmatched properties. You rely on its high precision, temperature resistance, and chemical stability to meet the rigorous demands of production. Its applications in crystal growth, epitaxy, ion implantation, and thermal insulation ensure efficient and durable processes. Components like the Graphite Bipolar Plate enhance performance and maintain quality standards. As semiconductor technology evolves, graphite continues to drive innovation, helping you achieve superior results and stay ahead in the industry.
FAQ
What makes graphite a preferred material in semiconductor manufacturing?
Graphite stands out due to its exceptional properties. You benefit from its high precision, which ensures accuracy in critical processes. Its ability to resist extreme temperatures and maintain stability under harsh conditions makes it indispensable. Additionally, graphite offers chemical resistance and durability, reducing material loss and ensuring reliable performance in demanding environments.
How does graphite contribute to crystal growth in semiconductors?
Graphite plays a key role in crystal growth by providing components like heaters, crucibles, and insulation cylinders. These parts withstand high temperatures and distribute heat evenly, ensuring defect-free crystal structures. You also rely on graphite’s chemical resistance to maintain durability in corrosive conditions, which is essential for uninterrupted production.
Why is high-purity graphite important in semiconductor applications?
High-purity graphite minimizes contamination risks during manufacturing. You benefit from its low ash content (less than 5ppm), which ensures the integrity of semiconductor materials. This purity level is critical for processes like crystal growth and epitaxy, where even minor impurities can compromise product quality.
What role do graphite disks play in the epitaxial process?
Graphite disks ensure the quality of the wafer’s epitaxial layer. You rely on their precision and stability to maintain uniformity during deposition. High-purity graphite disks with uniform coatings enhance thermal conductivity and chemical resistance, ensuring optimal performance in wafer production.
How does graphite improve ion implantation processes?
Graphite components like flight tubes, slits, electrodes, and beam terminators handle the intense demands of ion implantation. You achieve precise ion placement due to graphite’s thermal conductivity and wear resistance. These components are also compatible with leading equipment models, ensuring seamless integration into your systems.
Can graphite insulation materials be customized for specific needs?
Yes, manufacturers offer graphite insulation materials in customizable sizes. You can tailor these materials to fit your production requirements, ensuring seamless integration into your systems. Custom sizes reduce material waste and improve efficiency, helping you optimize your manufacturing processes.
What are the benefits of using carbon-carbon trays in semiconductor production?
Carbon-carbon trays provide structural support and stability during high-temperature processes. You depend on their lightweight yet durable design to handle demanding applications like solar silicon cell production. These trays ensure consistent performance, reducing the risk of deformation or failure.
How do graphite bipolar plates enhance furnace tube processing?
Graphite bipolar plates improve furnace tube processing by conducting heat evenly and resisting chemical reactions. You rely on their durability and thermal conductivity to ensure uniform processing. These plates maintain their integrity over time, enhancing the efficiency and quality of semiconductor materials.
Are there alternative materials that complement graphite in semiconductor manufacturing?
Yes, you can use materials like ceramic, tungsten, molybdenum, and aluminum alongside graphite. Each material offers unique benefits. Ceramic provides electrical insulation, tungsten and molybdenum offer strength and heat resistance, and aluminum adds lightweight durability. Combining these materials with graphite enhances overall efficiency and precision.
How does graphite support advancements in semiconductor technology?
Graphite drives innovation by meeting the rigorous demands of modern semiconductor manufacturing. You benefit from its unmatched properties, including high precision, temperature resistance, and chemical stability. Its versatility ensures that it remains a critical material as technology evolves, helping you achieve superior results in production.