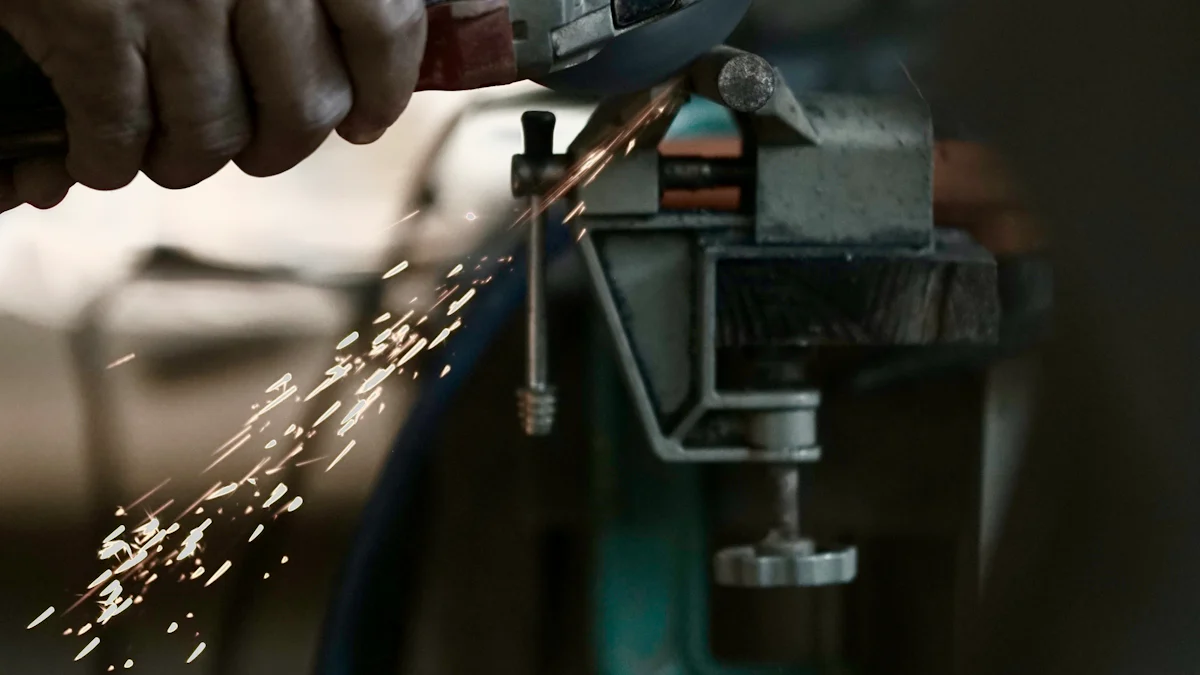
The semiconductor industry continues to demand innovative solutions to meet the growing need for ultra-thin wafers. Wafer grinding disk technology plays a critical role in achieving this goal. Recent advancements in materials and precision engineering have enhanced the performance of these disks, enabling manufacturers to produce thinner wafers with exceptional accuracy. Automation and sustainability have also emerged as key trends, driving efficiency and reducing environmental impact. These developments highlight the importance of wafer grinding disks in shaping the future of semiconductor manufacturing.
Key Takeaways
- Embrace advanced materials like diamond-embedded and ceramic composites to enhance durability and performance in wafer grinding.
- Utilize innovative coating technologies, such as diamond-like carbon and multi-layered coatings, to improve grinding efficiency and extend disk lifespan.
- Implement precision engineering tools and automation to achieve ultra-thin wafers with minimal defects and consistent quality.
- Leverage AI and IoT for real-time monitoring and optimization of grinding processes, ensuring high efficiency and predictive maintenance.
- Adopt sustainable practices by reducing waste and energy consumption in grinding operations, contributing to eco-friendly manufacturing.
- Recognize the critical role of wafer grinding disks in supporting emerging technologies like 5G and quantum computing, ensuring high-performance semiconductor devices.
- Stay informed about ongoing advancements in wafer grinding technology to maintain a competitive edge in the semiconductor industry.
Advancements in Materials and Coatings for Wafer Grinding Disks
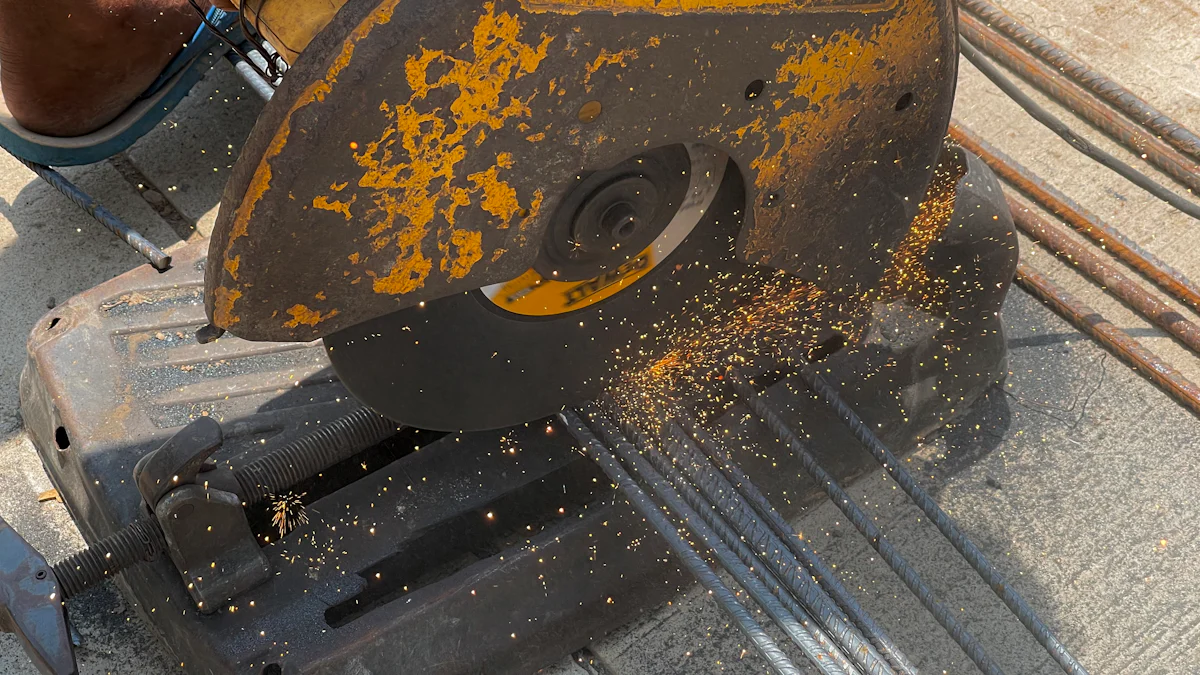
Development of High-Performance Materials
The evolution of wafer grinding disk technology relies heavily on the development of advanced materials. Manufacturers now prioritize materials that offer superior durability and performance under high-stress conditions. For instance, diamond-embedded grinding disks have gained significant traction due to their exceptional hardness and wear resistance. These materials enable the disks to maintain their cutting efficiency over extended periods, reducing the need for frequent replacements.
Ceramic composites also play a pivotal role in enhancing the structural integrity of wafer grinding disks. These composites provide a balance between strength and flexibility, ensuring consistent performance during grinding processes. By incorporating such high-performance materials, manufacturers address the growing demand for ultra-thin wafers while maintaining precision and efficiency.
Innovations in Coating Technologies
Coating technologies have revolutionized the functionality of wafer grinding disks. Advanced coatings, such as diamond-like carbon (DLC) and nano-coatings, improve the surface properties of grinding disks. These coatings minimize friction during the grinding process, which reduces heat generation and prevents damage to the wafer. As a result, manufacturers achieve higher precision and smoother finishes on ultra-thin wafers.
Another significant innovation involves the use of multi-layered coatings. These coatings enhance the lifespan of wafer grinding disks by providing additional protection against wear and corrosion. Multi-layered coatings also improve the adhesion of abrasive particles, ensuring consistent grinding performance. Such advancements in coating technologies contribute to the overall efficiency and reliability of wafer grinding disk operations.
"The integration of high-performance materials and innovative coatings has transformed wafer grinding disk technology, enabling manufacturers to meet the stringent demands of the semiconductor industry."
Precision and Accuracy Improvements in Wafer Grinding Disks
Achieving Ultra-Thin Wafers
The demand for ultra-thin wafers has driven significant advancements in wafer grinding disk technology. Manufacturers now focus on achieving unparalleled precision during the grinding process. Ultra-thin wafers, often required for advanced semiconductor applications, demand a high level of accuracy to prevent structural damage. Wafer grinding disks equipped with enhanced abrasive materials ensure consistent material removal, enabling the production of wafers with minimal thickness variations.
Modern grinding techniques prioritize uniformity across the wafer surface. This uniformity reduces the risk of defects, which can compromise the performance of semiconductor devices. By optimizing grinding parameters, such as speed and pressure, manufacturers achieve smoother finishes and tighter tolerances. These improvements directly address the industry’s need for thinner, more reliable wafers.
Integration of Precision Engineering Tools
Precision engineering tools have become essential in enhancing the performance of wafer grinding disks. Advanced metrology systems now monitor grinding processes in real-time, ensuring that every wafer meets strict dimensional requirements. These systems detect deviations early, allowing manufacturers to make immediate adjustments and maintain consistent quality.
Automation plays a critical role in integrating precision tools with wafer grinding disk operations. Robotic systems handle wafers with extreme care, minimizing the risk of contamination or damage. Additionally, computer-aided design (CAD) software aids in the development of grinding disks tailored to specific wafer requirements. This customization ensures optimal performance and efficiency during grinding.
Laser-based measurement tools further enhance precision by providing accurate feedback on wafer thickness and surface quality. These tools enable manufacturers to refine their processes continuously, meeting the growing demands of the semiconductor industry. The integration of such technologies underscores the importance of precision in wafer grinding disk applications.
Automation and Smart Technology Integration in Wafer Grinding Disks
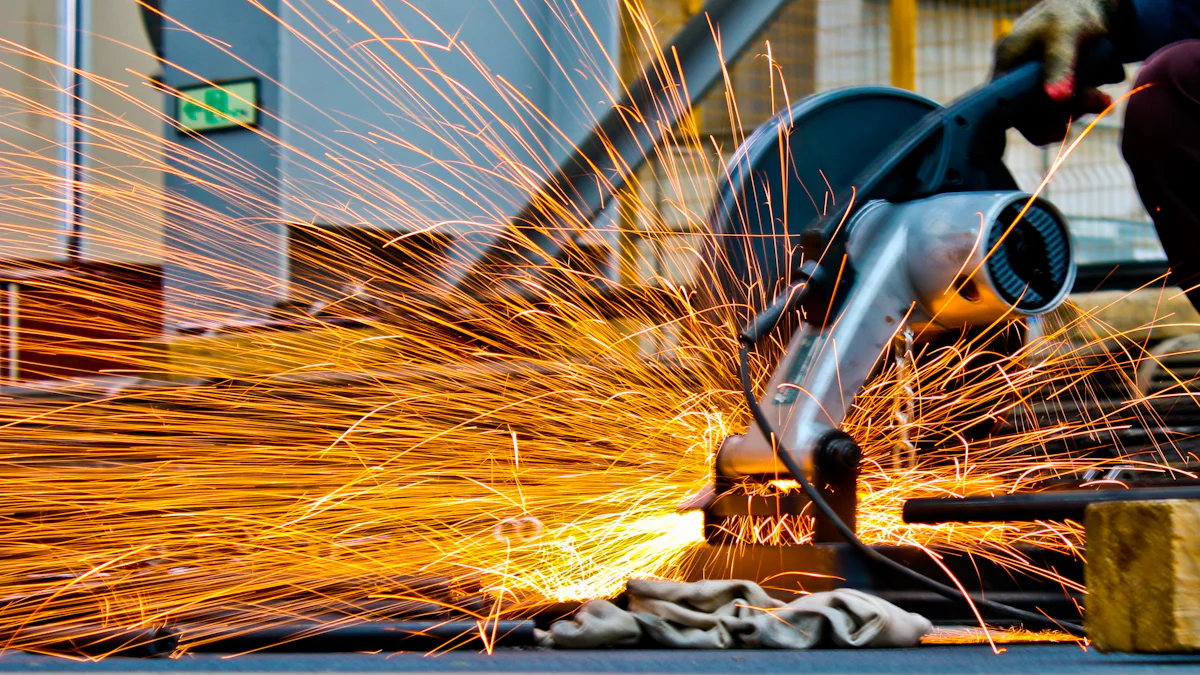
Role of Artificial Intelligence (AI) in Grinding Processes
Artificial Intelligence (AI) has transformed wafer grinding processes by introducing advanced decision-making capabilities. AI algorithms analyze vast amounts of data generated during grinding operations. These algorithms identify patterns and optimize parameters such as grinding speed, pressure, and material removal rates. This optimization ensures consistent results and minimizes errors.
AI-powered systems predict potential issues before they occur. For example, they detect wear on grinding disks and recommend timely replacements. This predictive maintenance reduces downtime and enhances operational efficiency. Manufacturers also use AI to improve the quality of ultra-thin wafers by ensuring precise material removal. The integration of AI has elevated the performance of wafer grinding disk technology to meet the semiconductor industry’s stringent demands.
Internet of Things (IoT) in Wafer Grinding
The Internet of Things (IoT) has enabled seamless connectivity between wafer grinding equipment and monitoring systems. IoT sensors collect real-time data on temperature, vibration, and disk wear during grinding operations. This data provides valuable insights into the performance of wafer grinding disks.
IoT-enabled systems allow remote monitoring and control of grinding processes. Operators can adjust parameters or troubleshoot issues without being physically present. This capability enhances flexibility and reduces response times. Additionally, IoT facilitates data sharing across different stages of semiconductor manufacturing. This integration ensures that wafer grinding processes align with overall production goals.
IoT also supports sustainability efforts by tracking energy consumption and identifying areas for improvement. By leveraging IoT, manufacturers achieve greater efficiency and maintain high-quality standards in wafer grinding operations.
Robotics and Automation
Robotics has revolutionized wafer grinding by automating repetitive and delicate tasks. Robotic arms handle wafers with precision, reducing the risk of contamination or damage. These systems operate with high accuracy, ensuring consistent grinding results.
Automation streamlines wafer grinding processes by eliminating manual interventions. Automated systems load and unload wafers, monitor grinding parameters, and perform quality checks. This approach increases throughput and reduces human error. Manufacturers benefit from improved productivity and cost savings.
Advanced robotics also enables multi-tasking capabilities. For instance, a single robotic system can manage grinding, cleaning, and inspection processes. This versatility enhances the overall efficiency of wafer grinding operations. The integration of robotics and automation underscores the industry’s commitment to innovation and precision.
"The adoption of AI, IoT, and robotics has redefined wafer grinding disk technology, enabling manufacturers to achieve unmatched efficiency and precision."
Sustainability and Eco-Friendly Practices in Wafer Grinding Disk Technology
Reducing Waste in Grinding Processes
Manufacturers in the semiconductor industry have prioritized waste reduction during wafer grinding processes. This focus stems from the need to minimize material loss while maintaining high-quality standards. Advanced grinding techniques now ensure precise material removal, reducing excess waste generated during operations. By optimizing grinding parameters, such as speed and pressure, manufacturers achieve efficient material usage and limit unnecessary byproducts.
Recycling initiatives have also gained traction. Many manufacturers now collect and repurpose residual materials, such as slurry and grinding debris, for secondary applications. This approach not only reduces waste but also lowers production costs. Additionally, the development of reusable components in wafer grinding disk systems has further contributed to waste minimization. These practices align with the industry’s commitment to sustainability and resource conservation.
"Reducing waste in grinding processes reflects the industry’s dedication to sustainable manufacturing while addressing environmental concerns."
Energy-Efficient Grinding Technologies
Energy efficiency has become a cornerstone of eco-friendly wafer grinding disk technology. Modern grinding systems now incorporate energy-saving features that optimize power consumption without compromising performance. For instance, variable-speed drives adjust motor speeds based on operational requirements, ensuring minimal energy usage during low-demand periods.
Innovative cooling systems have also enhanced energy efficiency. Traditional cooling methods often consumed significant amounts of energy. However, advanced cooling technologies now regulate temperatures more effectively, reducing energy expenditure. These systems maintain optimal grinding conditions while lowering the overall carbon footprint of manufacturing processes.
The integration of automation has further improved energy efficiency. Automated systems streamline operations, eliminating unnecessary energy usage caused by manual interventions. Smart sensors monitor energy consumption in real-time, providing actionable insights to optimize processes. These advancements underscore the industry’s efforts to adopt sustainable practices while meeting the growing demand for wafer grinding disk technology.
"Energy-efficient grinding technologies demonstrate how innovation can drive sustainability in semiconductor manufacturing."
Applications of Wafer Grinding Disks in the Semiconductor Industry
Impact on Semiconductor Manufacturing
Wafer grinding disks play a pivotal role in semiconductor manufacturing by enabling precise wafer thinning. This process ensures that wafers meet the dimensional requirements for advanced electronic devices. Manufacturers rely on these disks to achieve uniform thickness across wafers, which directly impacts the performance and reliability of semiconductor components. The ability to produce ultra-thin wafers has become essential for creating compact and high-performance devices.
The use of wafer grinding disks enhances production efficiency. These disks allow manufacturers to streamline the backgrinding process, reducing cycle times and increasing throughput. By maintaining consistent grinding performance, they minimize defects and improve yield rates. This reliability supports the industry’s demand for high-quality wafers, which serve as the foundation for modern electronics.
Wafer grinding disks also contribute to cost optimization. Their durability and precision reduce material waste, lowering overall production expenses. Manufacturers benefit from fewer replacements and maintenance requirements, ensuring uninterrupted operations. These advantages make wafer grinding disks indispensable in the competitive semiconductor market.
"The integration of wafer grinding disks into semiconductor manufacturing processes has elevated production standards, ensuring the delivery of reliable and efficient electronic components."
Role in Emerging Technologies
Emerging technologies, such as 5G, artificial intelligence, and the Internet of Things, have increased the demand for advanced semiconductor devices. Wafer grinding disks support these technologies by enabling the production of ultra-thin wafers required for high-performance chips. These wafers enhance the functionality of devices by improving heat dissipation and power efficiency.
In advanced packaging technologies, wafer grinding disks play a critical role. Techniques like system-in-package (SiP) and fan-out wafer-level packaging (FOWLP) require precise wafer thinning to accommodate complex designs. These disks ensure that wafers meet the stringent specifications needed for these applications, driving innovation in semiconductor packaging.
The development of flexible electronics has further highlighted the importance of wafer grinding disks. Flexible displays, wearable devices, and other applications rely on ultra-thin wafers for their lightweight and adaptable designs. Wafer grinding disks enable manufacturers to meet these requirements, supporting the growth of next-generation technologies.
As quantum computing gains traction, wafer grinding disks will remain essential. Quantum chips demand extreme precision during manufacturing, and these disks provide the accuracy needed for such applications. Their role in shaping the future of technology underscores their significance in the semiconductor industry.
"Wafer grinding disks serve as a cornerstone for emerging technologies, enabling advancements in electronics, packaging, and quantum computing."
Wafer grinding disk technology has undergone significant advancements in materials, precision, automation, and sustainability. These trends have reshaped semiconductor manufacturing by enabling ultra-thin wafers, improving production efficiency, and reducing environmental impact. The integration of smart technologies and eco-friendly practices highlights the industry’s commitment to innovation. As emerging technologies like 5G and quantum computing evolve, wafer grinding disks will remain essential. Continued innovation will ensure that manufacturers meet the growing demands of next-generation devices while maintaining high-quality standards.
FAQ
What is a wafer grinding disk?
A wafer grinding disk is a specialized tool used in semiconductor manufacturing to thin wafers to precise dimensions. These disks are designed with abrasive materials that remove excess material from the wafer surface, ensuring uniform thickness and smooth finishes. They play a critical role in producing ultra-thin wafers for advanced electronic devices.
Why is wafer grinding important in semiconductor manufacturing?
Wafer grinding ensures that wafers meet the dimensional requirements for modern semiconductor applications. Thinner wafers improve heat dissipation, enhance device performance, and enable compact designs. Grinding also reduces defects, increases yield rates, and supports the production of high-quality semiconductor components.
What materials are commonly used in wafer grinding disks?
Manufacturers use high-performance materials such as diamond and ceramic composites in wafer grinding disks. Diamond provides exceptional hardness and wear resistance, while ceramic composites offer a balance of strength and flexibility. These materials ensure durability and consistent performance during grinding processes.
How do coatings improve wafer grinding disk performance?
Advanced coatings, such as diamond-like carbon (DLC) and nano-coatings, enhance the surface properties of grinding disks. These coatings reduce friction, minimize heat generation, and prevent wafer damage. Multi-layered coatings also extend the lifespan of grinding disks by protecting them from wear and corrosion.
What role does automation play in wafer grinding?
Automation streamlines wafer grinding processes by reducing manual interventions. Robotic systems handle wafers with precision, ensuring consistent results and minimizing contamination risks. Automated systems also monitor grinding parameters, perform quality checks, and increase overall productivity.
How does artificial intelligence (AI) enhance wafer grinding?
AI optimizes wafer grinding by analyzing data and adjusting parameters such as speed and pressure. It predicts potential issues, recommends maintenance, and ensures precise material removal. AI-powered systems improve efficiency, reduce errors, and maintain high-quality standards in wafer grinding operations.
What are the sustainability practices in wafer grinding disk technology?
Sustainability practices include waste reduction, energy-efficient technologies, and recycling initiatives. Advanced grinding techniques minimize material loss, while reusable components reduce waste. Energy-saving features, such as variable-speed drives and innovative cooling systems, lower energy consumption and carbon footprints.
What industries benefit from wafer grinding disk technology?
The semiconductor industry relies heavily on wafer grinding disk technology. It supports the production of chips for emerging technologies like 5G, artificial intelligence, and the Internet of Things. Wafer grinding disks also play a vital role in advanced packaging and flexible electronics manufacturing.
How do wafer grinding disks contribute to emerging technologies?
Wafer grinding disks enable the production of ultra-thin wafers required for high-performance chips. These wafers enhance device functionality by improving power efficiency and heat dissipation. Grinding disks also support advanced packaging techniques and the development of flexible electronics and quantum computing.
What advancements can be expected in wafer grinding disk technology?
Future advancements may include smarter automation systems, enhanced AI integration, and more sustainable manufacturing practices. Innovations in materials and coatings will likely improve durability and performance. These developments will address the growing demands of next-generation semiconductor devices.