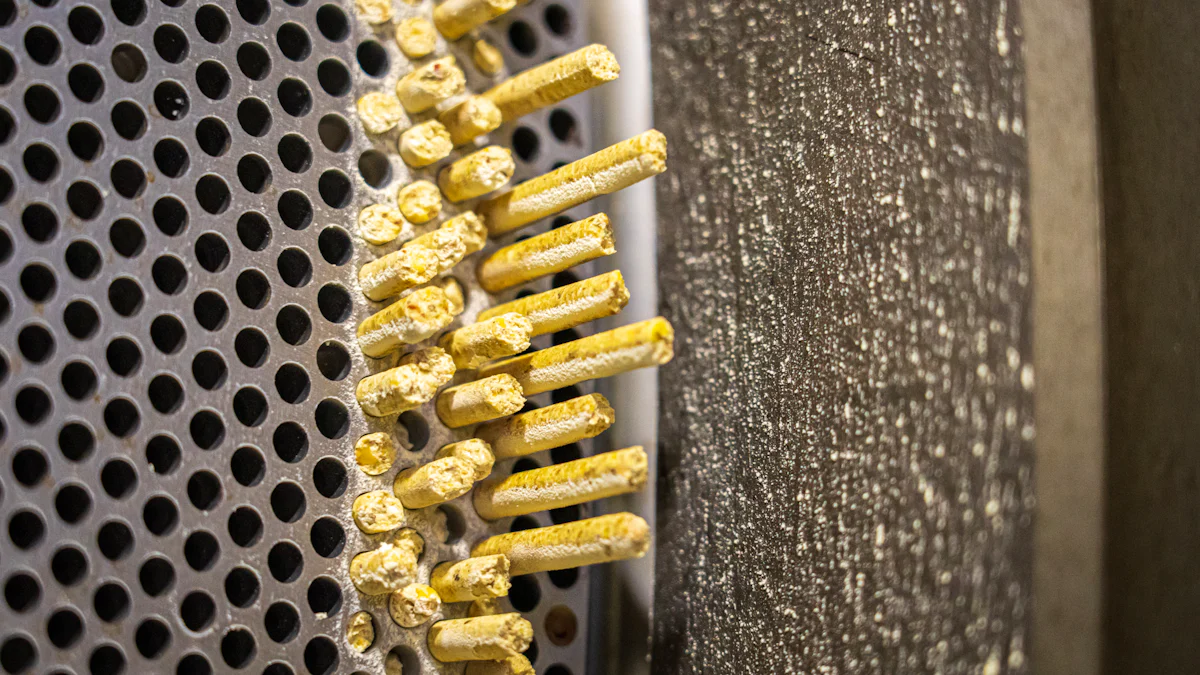
Selecting the right material for a Preheat Ring plays a critical role in industrial applications. The material directly impacts the durability, cost-efficiency, and overall performance of the equipment. Industries rely on materials that withstand extreme conditions, ensuring consistent heat distribution and minimal wear. For instance, advanced materials like graphite coated with silicon carbide offer exceptional resistance to chemical breakdown, making them ideal for high-stress environments. By choosing the appropriate material, manufacturers can enhance operational efficiency, reduce maintenance costs, and improve product quality, ultimately driving innovation in industrial processes.
Key Takeaways
- Choosing the right preheat ring material is crucial for enhancing operational efficiency and reducing maintenance costs in industrial applications.
- Steel and cast iron are cost-effective options that offer durability and excellent thermal conductivity, making them suitable for heavy-duty environments.
- Ceramic materials excel in extreme temperatures and provide high corrosion resistance, ideal for precision-driven applications despite their fragility.
- Graphite coated with silicon carbide combines exceptional thermal conductivity with chemical stability, making it a high-performance choice for demanding conditions.
- Composite materials offer a customizable solution with a high strength-to-weight ratio, perfect for weight-sensitive applications in industries like aerospace.
- Evaluating both initial costs and long-term value is essential; advanced materials may have higher upfront costs but can lead to significant savings over time.
- Sustainability is increasingly important; recyclable materials like steel and cast iron align with eco-friendly practices, while manufacturers seek to minimize environmental impact.
Overview of Common Preheat Ring Materials
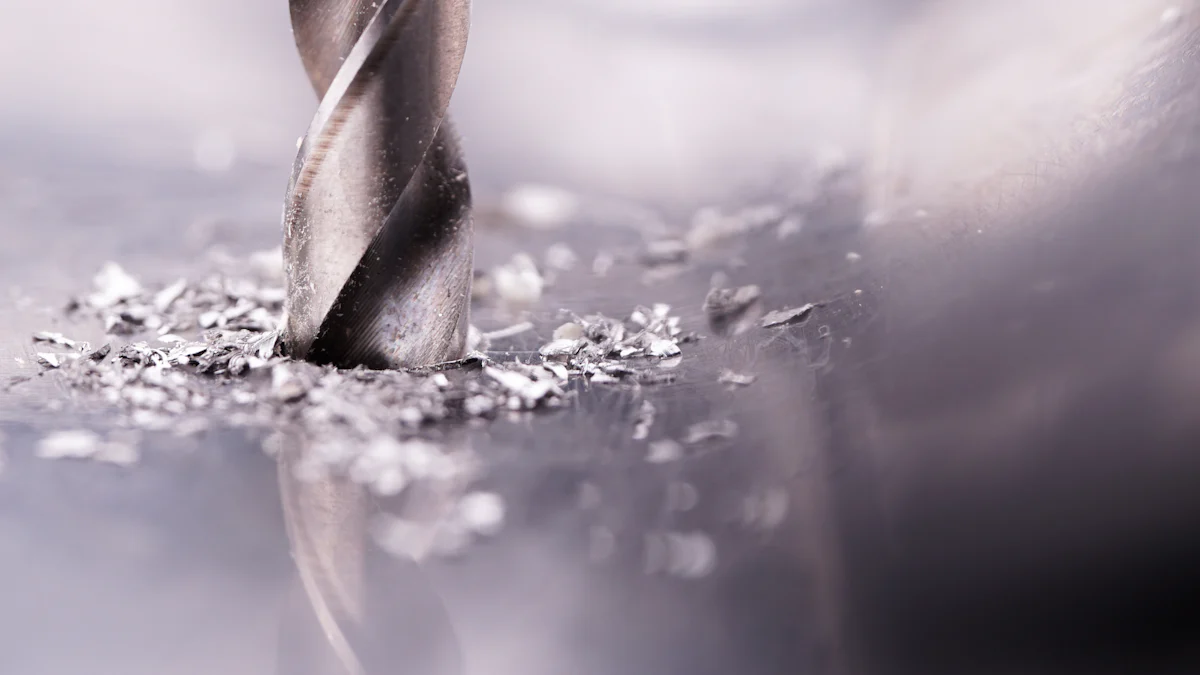
Steel
Description and properties
Steel is a widely used material in industrial applications due to its exceptional mechanical properties. It is an alloy primarily composed of iron and carbon, with additional elements like chromium enhancing its performance. For instance, 12% chrome steel exhibits excellent heat resistance, cavitation resistance, and durability. These attributes make it suitable for environments requiring consistent thermal performance.
Advantages
- High strength and durability ensure long-lasting performance.
- Excellent heat resistance allows it to withstand high-temperature conditions.
- Versatile and adaptable to various industrial processes.
- Readily available and cost-effective compared to some advanced materials.
Disadvantages
- Susceptible to corrosion without proper treatment or coatings.
- Heavier than alternative materials, which may limit its use in weight-sensitive applications.
Industrial use cases
Steel preheat rings are commonly used in industries such as manufacturing, metallurgy, and energy production. Their ability to endure high temperatures and mechanical stress makes them ideal for applications like water pumps, where components like impellers and wear rings demand robust materials.
Cast Iron
Description and properties
Cast iron is an iron-carbon alloy containing more than 2.06% carbon. Its structure includes graphite deposits within a ferritic-pearlitic matrix, which can be modified by adding elements like manganese. This composition provides cast iron with unique mechanical and technological properties, including excellent wear resistance and thermal conductivity.
Advantages
- High thermal conductivity ensures efficient heat transfer.
- Superior wear resistance extends the lifespan of components.
- Cost-effective for large-scale industrial applications.
- Easily cast into complex shapes, offering design flexibility.
Disadvantages
- Brittle nature limits its ability to withstand impact or sudden stress.
- Heavier than other materials, which may pose challenges in specific applications.
Industrial use cases
Cast iron preheat rings are frequently utilized in heavy-duty industrial settings, including foundries and automotive manufacturing. Their ability to handle high temperatures and resist wear makes them suitable for prolonged use in demanding environments.
Ceramic
Description and properties
Ceramic materials are inorganic, non-metallic compounds known for their exceptional thermal and chemical stability. They exhibit high resistance to heat and corrosion, making them ideal for extreme industrial conditions. Ceramics also possess low thermal expansion, ensuring dimensional stability under varying temperatures.
Advantages
- Outstanding heat resistance allows operation in extreme temperatures.
- Lightweight nature reduces the overall weight of equipment.
- High corrosion resistance ensures longevity in harsh environments.
- Minimal thermal expansion maintains structural integrity.
Disadvantages
- Fragility increases the risk of breakage under mechanical stress.
- Higher initial cost compared to traditional materials like steel or cast iron.
Industrial use cases
Ceramic preheat rings are widely used in industries such as semiconductors, photovoltaics, and aerospace. Their ability to maintain performance under high-stress and high-temperature conditions makes them indispensable in precision-driven applications.
Graphite
Description and properties
Graphite stands out as a high-performance material due to its unique crystalline structure. Composed of carbon atoms arranged in a hexagonal lattice, it exhibits excellent thermal conductivity and chemical stability. Its low density and self-lubricating properties further enhance its suitability for industrial applications. When coated with materials like silicon carbide, graphite achieves superior resistance to oxidation and wear, making it ideal for demanding environments.
Advantages
- Exceptional thermal conductivity ensures efficient heat transfer.
- High resistance to chemical corrosion extends its operational lifespan.
- Lightweight nature reduces the overall weight of industrial components.
- Self-lubricating properties minimize friction and wear during operation.
Disadvantages
- Susceptibility to oxidation at high temperatures without protective coatings.
- Brittle nature limits its ability to withstand mechanical shocks or impacts.
Industrial use cases
Graphite preheat rings find extensive use in industries such as semiconductors, photovoltaics, and metallurgy. Their ability to maintain structural integrity under extreme heat and stress makes them indispensable in high-temperature furnaces and reactors. Additionally, their lightweight and self-lubricating properties make them suitable for precision-driven applications like planetary disk systems.
Composite Materials
Description and properties
Composite materials combine two or more distinct substances to create a material with enhanced properties. These materials often include a matrix, such as resin or metal, reinforced with fibers like carbon or glass. This combination results in a material that offers superior strength, thermal stability, and resistance to wear. Composite preheat rings are engineered to meet specific industrial requirements, ensuring optimal performance in challenging conditions.
Advantages
- High strength-to-weight ratio improves efficiency in weight-sensitive applications.
- Excellent thermal stability ensures consistent performance under varying temperatures.
- Resistance to wear and corrosion extends the lifespan of industrial components.
- Customizable properties allow manufacturers to tailor materials for specific needs.
Disadvantages
- Higher production costs compared to traditional materials like steel or cast iron.
- Complex manufacturing processes may limit availability for certain applications.
Industrial use cases
Composite materials are widely used in industries such as aerospace, automotive, and energy production. Preheat rings made from composites excel in applications requiring lightweight yet durable components. Their adaptability and high-performance characteristics make them suitable for advanced systems, including those involving planetary disks and high-temperature operations.
Comparative Analysis of Preheat Ring Materials
Durability
Lifespan and resistance to wear in industrial environments
Durability remains a critical factor when evaluating preheat ring materials. Steel and cast iron exhibit exceptional resistance to mechanical wear, making them suitable for prolonged use in heavy-duty industrial environments. Steel, with its high tensile strength, can endure significant stress without deformation. Cast iron, known for its wear resistance, performs well in applications requiring consistent thermal conductivity.
Ceramic materials, while lightweight and heat-resistant, may face challenges in environments with high mechanical stress due to their brittle nature. However, their ability to maintain structural integrity under extreme temperatures makes them ideal for precision-driven applications. Graphite, especially when coated with silicon carbide, offers superior chemical stability and resistance to oxidation, ensuring a longer operational lifespan in high-temperature settings. Composite materials, engineered for specific industrial needs, combine strength and thermal stability, providing excellent durability in weight-sensitive applications.
Cost
Initial investment vs. long-term value
The cost of preheat ring materials varies significantly based on their composition and performance characteristics. Steel and cast iron are cost-effective options, offering a balance between affordability and durability. Their widespread availability and ease of manufacturing contribute to their lower initial investment. However, frequent maintenance or replacement may increase long-term costs in high-stress environments.
Ceramic and composite materials often require a higher initial investment due to their advanced manufacturing processes. Despite this, their extended lifespan and reduced maintenance needs can offset the upfront costs, delivering better long-term value. Graphite coated with silicon carbide, while more expensive initially, provides exceptional performance in demanding conditions, reducing the frequency of replacements and minimizing downtime. Industries prioritizing efficiency and reliability often find these materials a worthwhile investment.
Performance
Heat resistance and thermal conductivity
Performance in terms of heat resistance and thermal conductivity plays a pivotal role in material selection. Steel and cast iron demonstrate excellent thermal conductivity, ensuring efficient heat transfer in industrial processes. However, their heat resistance may vary depending on the specific alloy composition. Ceramic materials excel in extreme temperatures, maintaining stability and performance where metals might fail. Their low thermal expansion ensures dimensional accuracy, even under fluctuating temperatures.
Graphite, with its unique crystalline structure, offers outstanding thermal conductivity, making it ideal for applications requiring rapid heat transfer. When coated with silicon carbide, it achieves enhanced resistance to oxidation and chemical breakdown, further improving its performance in high-temperature environments. Composite materials, designed for specific applications, provide a tailored balance of heat resistance and conductivity, meeting the demands of advanced industrial systems.
Suitability for high-stress and high-temperature applications
In high-stress and high-temperature environments, material performance becomes a decisive factor. Steel and cast iron, with their robust mechanical properties, handle significant loads and stresses effectively. However, their performance may diminish in extreme heat without proper treatment. Ceramic materials, resistant to both heat and corrosion, excel in applications requiring precision and stability under intense conditions.
Graphite coated with silicon carbide stands out for its ability to withstand both high temperatures and chemical exposure. Its lightweight nature and self-lubricating properties enhance its suitability for precision-driven systems, such as planetary disk applications. Composite materials, with their customizable properties, adapt to the specific requirements of high-stress environments, offering a reliable solution for industries seeking advanced performance.
Maintenance and Replacement
Ease of maintenance for each material
The ease of maintaining preheat ring materials varies significantly based on their composition and application. Steel and cast iron, being traditional materials, require regular inspections to prevent issues like corrosion or surface wear. Steel, when treated with protective coatings, resists rust and reduces maintenance efforts. Cast iron, known for its durability, demands less frequent upkeep but may need attention in environments with high mechanical stress.
Ceramic materials, due to their chemical stability and resistance to corrosion, require minimal maintenance. Their non-reactive nature ensures longevity, even in harsh industrial conditions. However, their brittle structure necessitates careful handling during installation and operation to avoid damage.
Graphite coated with silicon carbide offers a unique advantage in maintenance. The silicon carbide layer enhances resistance to oxidation and chemical breakdown, reducing the need for frequent interventions. Its self-lubricating properties further minimize wear, making it an efficient choice for high-performance systems like planetary disks.
Composite materials, engineered for specific industrial needs, often feature enhanced durability and resistance to wear. These properties translate into reduced maintenance requirements. However, their complex structure may necessitate specialized tools or expertise for repairs, depending on the application.
Frequency and cost of replacement
Replacement frequency depends on the material’s durability and the operating environment. Steel and cast iron, while cost-effective initially, may require more frequent replacements in high-stress or corrosive conditions. Their affordability offsets this drawback, making them suitable for industries prioritizing budget constraints.
Ceramic materials, with their exceptional heat and corrosion resistance, exhibit extended lifespans. Their higher initial cost is balanced by reduced replacement frequency, especially in applications involving extreme temperatures. However, accidental breakage due to their fragility can lead to unexpected expenses.
Graphite coated with silicon carbide stands out for its longevity in demanding environments. The protective coating significantly reduces wear and oxidation, extending the material’s operational life. Although the initial investment is higher, the reduced replacement frequency and downtime make it a cost-effective solution for industries requiring consistent performance.
Composite materials, designed for durability and thermal stability, offer long-term value. Their resistance to wear and corrosion minimizes replacement needs. While the upfront cost may be higher, the extended lifespan and reduced maintenance expenses justify the investment for advanced industrial applications.
Key Considerations for Choosing a Preheat Ring Material
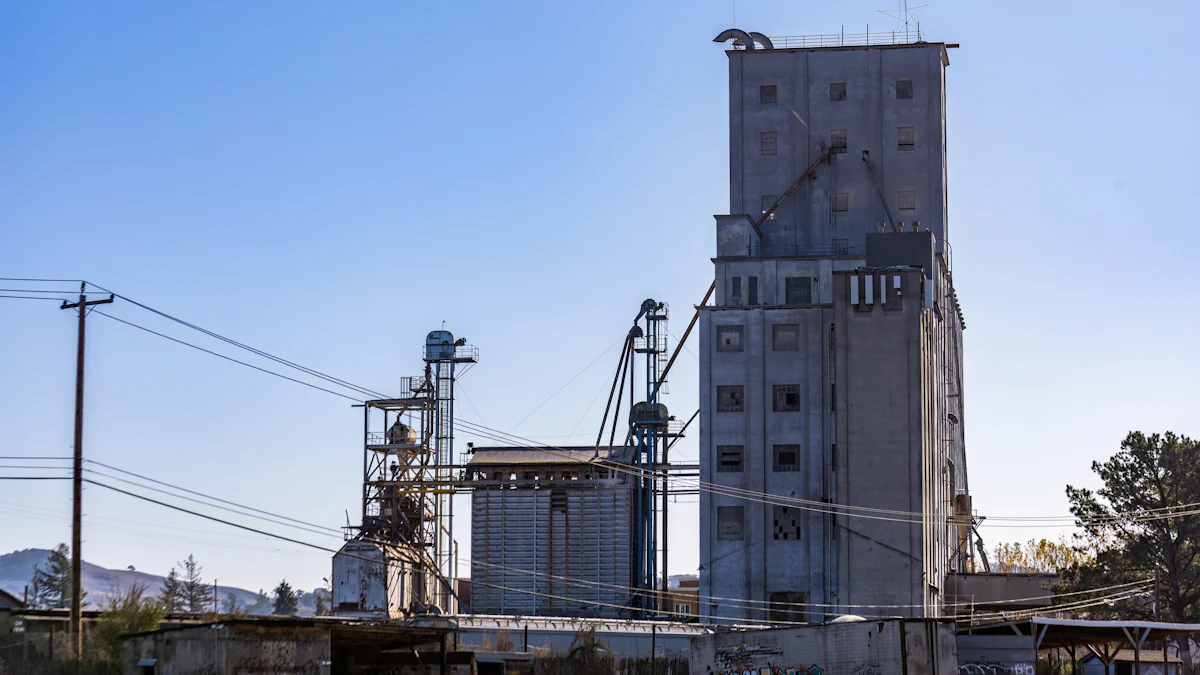
Application-Specific Requirements
Temperature ranges and thermal expansion
Industrial applications often expose preheat rings to extreme temperature fluctuations. Materials like graphite coated with silicon carbide excel in such conditions due to their high thermal conductivity and resistance to oxidation. Steel and cast iron, while durable, may experience thermal expansion that affects dimensional stability. Ceramic materials, with their low thermal expansion, maintain structural integrity even under intense heat. Composite materials offer tailored solutions, balancing thermal stability with strength for specific industrial needs.
Key Insight: Selecting a material with appropriate thermal properties ensures consistent performance and prevents equipment failure.
Load and stress conditions
Preheat rings must endure varying levels of mechanical stress. Steel and cast iron provide excellent strength, making them suitable for heavy-duty applications. Graphite, though lightweight, performs well under high-stress conditions when reinforced with protective coatings. Composite materials, engineered for specific stress tolerances, deliver a high strength-to-weight ratio, ideal for weight-sensitive systems. Ceramic materials, while heat-resistant, require careful handling to avoid damage under mechanical loads.
Budget Constraints
Balancing cost with performance and durability
Cost considerations play a pivotal role in material selection. Steel and cast iron offer affordability and durability, making them popular choices for budget-conscious industries. However, frequent maintenance or replacement may increase long-term expenses. Ceramic and composite materials demand higher initial investments but provide extended lifespans and reduced maintenance costs. Graphite coated with silicon carbide, though more expensive upfront, minimizes downtime and replacement frequency, offering long-term value for high-performance applications.
Pro Tip: Industries should evaluate both initial costs and long-term savings to make informed decisions.
Environmental Considerations
Sustainability and recyclability of materials
Sustainability has become a critical factor in material selection. Steel and cast iron, being recyclable, align with eco-friendly practices. Composite materials, depending on their composition, may pose challenges in recycling. Graphite and ceramics, while durable, require careful disposal to minimize environmental impact. Manufacturers increasingly prioritize materials that reduce waste and support circular economy initiatives.
Environmental impact of material production and disposal
The production process significantly influences the environmental footprint of preheat ring materials. Steel and cast iron manufacturing involve energy-intensive processes, contributing to carbon emissions. Ceramic and composite materials, though advanced, may require specialized production techniques with varying environmental impacts. Graphite coated with silicon carbide offers a balance, combining high performance with relatively lower environmental costs when sourced responsibly.
Industry Trend: Companies are shifting toward materials with lower environmental footprints to meet sustainability goals.
Selecting the right material for a preheat ring is essential for optimizing industrial performance. Each material offers unique properties. Steel and cast iron provide durability and cost-efficiency, while ceramics excel in extreme temperatures. Graphite, especially with silicon carbide coatings, delivers exceptional thermal conductivity and chemical resistance. Composite materials stand out for their adaptability and strength-to-weight ratio. Industries should evaluate specific needs, such as temperature ranges, stress conditions, and budget constraints, to make informed decisions. Balancing cost, durability, and performance ensures long-term efficiency and reliability in industrial applications.
FAQ
What is the primary purpose of a preheat ring in industrial applications?
A preheat ring ensures uniform heat distribution during industrial processes. It plays a crucial role in maintaining consistent temperatures, which enhances equipment efficiency and product quality. Industries like metallurgy, semiconductors, and energy production rely on preheat rings to optimize thermal performance.
How does material selection impact the performance of a preheat ring?
Material selection directly influences the durability, thermal conductivity, and resistance to wear of a Preheat Ring. For instance, graphite coated with silicon carbide offers superior chemical stability and heat resistance, making it ideal for high-temperature environments. On the other hand, steel provides strength and affordability but may require protective coatings to prevent corrosion.
Why is graphite coated with silicon carbide considered a high-performance material?
Graphite coated with silicon carbide combines excellent thermal conductivity with resistance to oxidation and chemical breakdown. This combination makes it suitable for demanding applications, such as high-temperature furnaces and Planetary Disk systems. Its lightweight nature and self-lubricating properties further enhance its efficiency in precision-driven industries.
What are the advantages of using composite materials for preheat rings?
Composite materials offer a high strength-to-weight ratio, exceptional thermal stability, and resistance to wear. These properties make them ideal for weight-sensitive applications, such as aerospace and automotive industries. Additionally, their customizable nature allows manufacturers to tailor them for specific industrial requirements.
How does preheating affect the mechanical properties of materials?
Preheating can enhance the microhardness and elastic modulus of certain materials, improving their performance under stress. For example, preheating silorane composites increases their microhardness, while preheating brittle thermoplastic carbon-fiber-reinforced plastics (TP-CFRP) softens them, preventing fractures during processing.
What factors should industries consider when choosing a preheat ring material?
Industries should evaluate application-specific requirements, such as temperature ranges, load conditions, and thermal expansion. Budget constraints and environmental considerations, including sustainability and recyclability, also play a significant role. Selecting the right material ensures long-term efficiency and reliability.
Are ceramic preheat rings suitable for high-stress environments?
Ceramic Preheat Ring excel in extreme temperatures due to their heat resistance and low thermal expansion. However, their brittle nature limits their ability to withstand mechanical shocks. They are best suited for precision-driven applications where thermal stability is critical.
How does the cost of preheat ring materials affect long-term value?
While materials like steel and cast iron have lower initial costs, they may require frequent maintenance or replacement in high-stress environments. Advanced materials, such as ceramics and composites, demand higher upfront investments but offer extended lifespans and reduced maintenance expenses, providing better long-term value.
What role does sustainability play in the selection of preheat ring materials?
Sustainability has become a key consideration for many industries. Recyclable materials like steel and cast iron align with eco-friendly practices. Manufacturers increasingly prioritize materials with lower environmental impacts, such as responsibly sourced graphite, to support circular economy initiatives.
Can preheat rings be customized for specific industrial applications?
Yes, preheat rings can be tailored to meet specific industrial needs. Composite materials, for example, allow manufacturers to adjust properties like strength, thermal conductivity, and weight. This adaptability ensures optimal performance in advanced systems, including planetary disk applications and high-temperature operations.