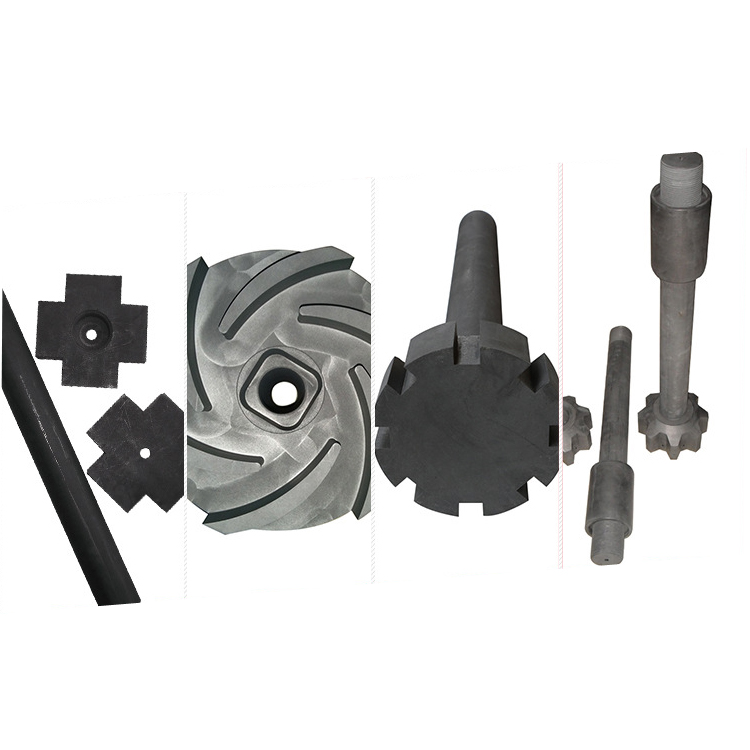
Graphite impellers have revolutionized aluminum degassing by combining exceptional thermal resistance, chemical inertness, and durability. These properties enable them to withstand extreme temperatures while maintaining structural integrity, ensuring efficient removal of hydrogen and impurities from molten aluminum. Unlike traditional materials, graphite impellers minimize friction and scouring forces, reducing contamination risks and enhancing product quality. Their lightweight design also optimizes energy consumption, making them a cost-effective solution for industries like aerospace and automotive. Additionally, graphite crystallizers complement this process by offering superior heat management, further improving the efficiency of aluminum processing systems.
Key Takeaways
- Graphite impellers provide exceptional thermal resistance, allowing them to maintain structural integrity in extreme temperatures, crucial for efficient aluminum degassing.
- Their chemical inertness prevents reactions with molten aluminum, ensuring the purity of the metal and enhancing the quality of aluminum alloys.
- The lightweight design of graphite impellers reduces energy consumption and mechanical stress on equipment, making them a cost-effective choice for industries.
- Graphite impellers excel in efficiently removing hydrogen and impurities from molten aluminum, resulting in higher-quality products with improved mechanical properties.
- Their durability and resistance to wear extend service life, minimizing the need for frequent replacements and supporting sustainability efforts.
- Graphite impellers outperform traditional materials like metal and ceramic by reducing contamination risks and ensuring consistent performance over time.
- Choosing high-quality graphite impellers, such as those from Ningbo VET Energy Technology Co., can lead to significant operational efficiencies and long-term cost savings.
Key Properties of Graphite Impellers
Thermal Resistance
Graphite impellers excel in high-temperature environments, making them indispensable for aluminum degassing. Their ability to withstand extreme heat ensures they maintain structural integrity even when exposed to molten aluminum, which often exceeds 1,200°F. Unlike other materials that may warp or degrade under such conditions, graphite remains stable. This property is why graphite is also used in aerospace applications, such as rocket nozzles and jet engine components, where thermal resistance is critical. By maintaining consistent performance in these demanding conditions, graphite impellers contribute to efficient and reliable degassing processes.
Chemical Inertness
Chemical inertness is another defining characteristic of graphite impellers. When immersed in molten aluminum, they resist chemical reactions that could compromise their functionality or contaminate the metal. This inertness ensures the purity of the aluminum, which is essential for industries like automotive and aerospace that demand high-quality alloys. Graphite’s chemical stability also makes it a preferred material in refractory applications, such as crucibles and molds, where it interacts with various molten metals. In aluminum degassing, this property minimizes the risk of introducing impurities, enhancing the overall quality of the final product.
Durability and Strength
Graphite impellers combine lightweight construction with exceptional durability, enabling them to endure the mechanical stresses of high-speed rotation during degassing. Their strength ensures long service life, reducing the need for frequent replacements and lowering operational costs. Additionally, graphite’s resistance to wear and abrasion further enhances its durability, even in harsh industrial environments. This robust performance makes graphite impellers a cost-effective choice for facilities aiming to optimize efficiency and minimize downtime. Their durability also aligns with sustainability goals by reducing material waste over time.
How Graphite Impellers Enhance Aluminum Degassing
Efficient Hydrogen Removal
Hydrogen removal is a critical step in aluminum degassing, as excessive hydrogen can lead to porosity and weaken the final product. Graphite impellers excel in this process by efficiently dispersing inert gases, such as argon or nitrogen, into the molten aluminum. These gases form fine bubbles that rise through the liquid, capturing dissolved hydrogen and other impurities along the way. The unique structure of graphite impellers ensures optimal bubble distribution, maximizing contact between the gas and the molten metal. This efficient gas dispersion accelerates the degassing process, reducing smelting time and enhancing the quality of the aluminum alloy.
The thermal conductivity of graphite also plays a vital role in maintaining the temperature of the molten aluminum during degassing. Unlike metallic or ceramic alternatives, graphite impellers minimize heat loss, ensuring consistent processing conditions. This property not only improves hydrogen removal but also contributes to energy efficiency, making graphite impellers a preferred choice for industries requiring high-performance materials.
Prevention of Contamination
Contamination during aluminum processing can compromise the integrity of the final product. Graphite impellers address this challenge by offering exceptional chemical inertness. When exposed to molten aluminum, they resist reactions that could introduce impurities into the metal. This stability ensures that the aluminum remains pure, meeting the stringent quality standards demanded by industries such as aerospace and automotive.
Additionally, the smooth surface of graphite impellers reduces the likelihood of particle detachment during operation. Unlike metal impellers, which may corrode or degrade over time, graphite maintains its structural integrity even under harsh conditions. This durability minimizes the risk of contamination, ensuring a cleaner and more reliable degassing process. By preventing impurities, graphite impellers help manufacturers produce high-quality aluminum alloys that meet industry specifications.
Consistent Performance Over Time
Graphite impellers deliver consistent performance, even in demanding industrial environments. Their resistance to wear and abrasion allows them to withstand the mechanical stresses of high-speed rotation without compromising efficiency. This durability translates to a longer service life, reducing the frequency of replacements and lowering operational costs.
Moreover, graphite impellers maintain their effectiveness across multiple cycles of use. Their ability to resist thermochemical stresses ensures that they perform reliably, regardless of the intensity or duration of the degassing process. This consistency is particularly valuable in large-scale operations, where downtime can result in significant financial losses. By providing stable and predictable performance, graphite impellers support uninterrupted production and contribute to overall operational efficiency.
Comparison of Graphite Impellers with Alternative Materials
Graphite vs. Ceramic Impellers
Graphite impellers and ceramic impellers both excel in high-temperature environments, but their performance characteristics differ significantly. Graphite impellers offer superior thermal conductivity, which helps maintain the temperature of molten aluminum during degassing. This property ensures consistent processing conditions, reducing energy consumption and improving efficiency. Ceramic impellers, while also resistant to high temperatures, lack the same level of thermal conductivity. This limitation can lead to uneven heat distribution, potentially affecting the quality of the aluminum.
In terms of durability, graphite impellers resist thermochemical stresses better than ceramic alternatives. Their lightweight structure minimizes wear during high-speed rotation, extending their service life. Ceramic impellers, though robust, are more prone to cracking under mechanical stress. This makes graphite a more reliable choice for operations requiring long-term performance and minimal downtime.
Additionally, graphite impellers exhibit chemical inertness, preventing reactions with molten aluminum. Ceramic impellers, while chemically stable, may introduce micro-particles into the metal due to surface degradation over time. This difference highlights graphite’s advantage in maintaining the purity of aluminum alloys.
Graphite vs. Metal Impellers
Metal impellers, traditionally used in aluminum degassing, fall short when compared to graphite impellers. Graphite impellers outperform metals in several key areas, starting with corrosion resistance. Unlike metals, which often require protective coatings to prevent corrosion, graphite naturally resists chemical reactions with molten aluminum. This eliminates the need for additional treatments, reducing maintenance costs.
Graphite impellers also excel in thermal resistance. Metals, despite their strength, can warp or degrade under extreme heat. Graphite maintains its structural integrity even at temperatures exceeding 1,200°F, ensuring consistent performance. Furthermore, graphite’s lightweight design reduces the mechanical load on degassing systems, enhancing operational efficiency. Metal impellers, being heavier, increase energy consumption and wear on equipment.
Another critical distinction lies in contamination prevention. Metal impellers, especially those with coatings, risk introducing impurities into the aluminum as the coatings degrade. Graphite impellers, with their smooth and stable surfaces, minimize this risk, ensuring higher-quality aluminum products.
Why Graphite Impellers Outperform Alternatives
Graphite impellers combine the best attributes of ceramic and metal impellers while addressing their shortcomings. Their unique properties—thermal conductivity, chemical inertness, and durability—make them indispensable in aluminum degassing. Unlike ceramic impellers, graphite ensures even heat distribution, optimizing the degassing process. Compared to metal impellers, graphite offers superior corrosion resistance and a longer service life without requiring additional coatings.
The ability of graphite impellers to create fine gas bubbles during degassing further sets them apart. These bubbles efficiently capture hydrogen and impurities, enhancing the quality of the aluminum alloy. This feature, coupled with their lightweight design, reduces smelting time and energy consumption, making graphite impellers a cost-effective solution.
Industries like aerospace and automotive increasingly rely on graphite impellers for their demanding applications. Their consistent performance, even under harsh conditions, ensures uninterrupted production and high-quality outputs. By outperforming ceramic and metal alternatives, graphite impellers have become the preferred choice for modern aluminum processing systems.
Real-World Applications of Graphite Impellers
Foundries and Casting Facilities
Foundries and casting facilities rely heavily on graphite impellers to optimize aluminum degassing processes. These facilities often operate under demanding conditions, where maintaining the purity of molten aluminum is critical. Graphite impellers play a pivotal role by efficiently dispersing inert gases like argon or nitrogen into the molten metal. This process removes hydrogen and other impurities, ensuring the production of high-quality aluminum alloys.
The lightweight design of graphite impellers reduces mechanical stress on degassing systems, enhancing operational efficiency. Their durability minimizes wear during high-speed rotation, which is essential for continuous operations in foundries. Additionally, the chemical inertness of graphite prevents contamination, a common challenge in aluminum processing. By addressing these needs, graphite impellers have become indispensable tools for foundries aiming to improve product quality and reduce production costs.
Aerospace and Automotive Industries
The aerospace and automotive industries demand materials that meet stringent quality and performance standards. Graphite impellers fulfill these requirements by ensuring the purity and structural integrity of aluminum alloys used in critical components. In aerospace applications, impurities in aluminum can compromise the safety and reliability of parts like fuselage panels and engine components. Similarly, in the automotive sector, high-quality aluminum is essential for manufacturing lightweight yet durable parts such as engine blocks and chassis components.
Graphite impellers enhance the degassing process by creating fine gas bubbles that effectively capture hydrogen and impurities. This results in aluminum alloys with superior mechanical properties, meeting the rigorous demands of these industries. Furthermore, the thermal conductivity of graphite helps maintain consistent processing temperatures, reducing energy consumption and ensuring uniform quality. These advantages make graphite impellers a preferred choice for manufacturers in aerospace and automotive sectors.
Ningbo VET Energy Technology Co.’s Role in the Industry
Ningbo VET Energy Technology Co. has established itself as a leader in the production of high-quality graphite impellers. The company leverages advanced materials and cutting-edge technology to deliver products that meet the diverse needs of industries like foundries, aerospace, and automotive. Its graphite impellers are designed to withstand extreme temperatures and mechanical stresses, ensuring reliable performance in demanding applications.
By focusing on innovation and quality, Ningbo VET Energy Technology Co. has developed graphite impellers that offer exceptional thermal resistance, chemical inertness, and durability. These features not only enhance the efficiency of aluminum degassing but also contribute to long-term cost savings for their clients. The company’s commitment to customer-centric solutions and sustainable practices further solidifies its reputation as a trusted partner in the aluminum processing industry.
“Graphite impellers are essential tools for degassing in the aluminum industry, creating channels for supplying inert gas and distributing gas bubbles.” – EuroGraphite
Ningbo VET Energy Technology Co. exemplifies this principle by providing state-of-the-art graphite impellers that set new benchmarks for performance and reliability. Their expertise in advanced materials ensures that their products remain at the forefront of innovation, catering to the evolving demands of modern industries.
Environmental and Sustainability Benefits of Graphite Impellers
Reduced Material Waste
How do graphite impellers contribute to waste reduction? Their durability and long service life play a significant role. Unlike metal or ceramic alternatives, graphite impellers resist wear and degradation over extended periods of use. This longevity minimizes the frequency of replacements, reducing the volume of discarded materials in industrial operations. For industries focused on sustainability, this characteristic aligns with efforts to lower environmental impact.
Graphite’s lightweight nature also reduces strain on equipment, which decreases the likelihood of mechanical failures. For example, in aluminum degassing systems, the reduced wear on machinery translates to fewer component replacements and less waste generated during maintenance. By extending the operational lifespan of both the impellers and the associated equipment, graphite solutions support a circular economy approach, where resources are utilized more efficiently.
Additionally, the manufacturing process for graphite impellers generates less waste compared to other materials. Advanced production techniques, such as precision machining, ensure minimal material loss during fabrication. Companies like Ningbo VET Energy Technology Co. optimize these processes to further enhance sustainability, demonstrating their commitment to environmentally responsible practices.
Energy Efficiency in Manufacturing
Why are graphite impellers considered energy-efficient? Their thermal conductivity and lightweight design significantly reduce energy consumption during both manufacturing and operation. In aluminum degassing, graphite impellers maintain consistent temperatures in molten aluminum, minimizing heat loss. This property reduces the energy required to sustain optimal processing conditions, making them a preferred choice for energy-conscious industries.
The lightweight structure of graphite impellers also lowers the energy demand of degassing systems. For instance, high-speed rotation requires less power when using graphite impellers compared to heavier metal alternatives. This efficiency not only cuts operational costs but also reduces the carbon footprint of manufacturing facilities.
Moreover, the production of graphite impellers involves fewer energy-intensive steps than the creation of ceramic or metal components. Advanced material science and streamlined manufacturing techniques, such as those employed by Ningbo VET Energy Technology Co., further enhance energy efficiency. These innovations reflect the industry’s shift toward sustainable practices, ensuring that graphite impellers remain an environmentally friendly solution for modern industrial applications.
“Sustainability in manufacturing is no longer optional; it is a necessity for industries aiming to thrive in a resource-conscious world.” – Industry Insights Journal
By reducing material waste and optimizing energy use, graphite impellers exemplify how advanced materials can drive sustainability in industrial processes. Their adoption supports global efforts to minimize environmental impact while maintaining high standards of performance and efficiency.
Maintenance and Best Practices for Graphite Impellers
Proper Handling and Installation
Proper handling and installation of graphite impellers ensure their longevity and optimal performance. Mishandling during transportation or installation can lead to structural damage, reducing their effectiveness in aluminum degassing systems. Operators should always handle graphite impellers with care, avoiding unnecessary impacts or drops that may cause cracks or fractures.
When installing graphite impellers, alignment plays a critical role. Misaligned impellers can create uneven rotation, leading to inefficient gas dispersion and increased wear. Technicians should verify that the impeller is securely mounted on the rotor shaft and aligned with the system’s specifications. Using calibrated tools during installation minimizes errors and ensures precision.
To prevent contamination, operators should wear clean gloves when handling graphite impellers. Direct contact with bare hands can transfer oils or debris onto the impeller’s surface, potentially affecting its chemical inertness. Additionally, inspecting the impeller for any visible defects before installation helps identify issues early, reducing the risk of operational failures.
Cleaning and Storage Guidelines
Regular cleaning of graphite impellers maintains their efficiency and extends their service life. Residue from molten aluminum or other impurities can accumulate on the impeller’s surface over time, hindering its performance. Cleaning should involve non-abrasive methods to preserve the smooth surface of the graphite. For instance, using a soft brush or compressed air effectively removes debris without causing damage.
Operators should avoid using harsh chemicals or abrasive tools during cleaning, as these can compromise the impeller’s structural integrity. If stubborn residues persist, soaking the impeller in a mild cleaning solution designed for graphite materials can help loosen deposits. After cleaning, thoroughly drying the impeller prevents moisture-related issues during storage or subsequent use.
Proper storage practices are equally important. Graphite impellers should be stored in a clean, dry environment away from direct sunlight and extreme temperatures. Exposure to moisture or fluctuating conditions can weaken the material over time. Placing the impellers in protective packaging or padded containers minimizes the risk of accidental damage during storage or transportation.
For long-term storage, labeling each impeller with its specifications ensures easy identification and reduces handling errors. Facilities should also implement regular inspections of stored impellers to check for signs of wear or environmental damage. By following these guidelines, industries can maximize the performance and lifespan of their graphite impellers, ensuring consistent results in aluminum degassing processes.
Innovations in Graphite Impeller Technology
Advances by Ningbo VET Energy Technology Co.
How has Ningbo VET Energy Technology Co. advanced graphite impeller technology? The company has consistently pushed the boundaries of material science to meet the evolving demands of aluminum degassing. By leveraging its expertise in advanced materials, Ningbo VET Energy Technology Co. has developed graphite impellers with enhanced thermal resistance, chemical stability, and mechanical strength. These innovations ensure superior performance in high-temperature and high-stress environments.
One notable advancement lies in the precision engineering of impeller designs. Ningbo VET Energy Technology Co. employs state-of-the-art manufacturing techniques, such as CNC machining, to create impellers with optimized geometries. These designs improve gas dispersion efficiency, enabling faster and more effective hydrogen removal. For example, their streamlined impeller blades reduce rotational resistance, which enhances energy efficiency and minimizes wear on equipment.
The company also integrates proprietary surface treatments into its graphite impellers. These treatments increase resistance to oxidation and abrasion, extending the service life of the impellers. In addition, Ningbo VET Energy Technology Co. has introduced customizable solutions tailored to specific industrial needs. Clients can select impellers with unique dimensions, coatings, or performance characteristics, ensuring compatibility with diverse aluminum processing systems.
“Innovation is the cornerstone of our success. By combining cutting-edge technology with customer-focused solutions, we deliver graphite impellers that redefine industry standards.” – Ningbo VET Energy Technology Co.
Through continuous research and development, Ningbo VET Energy Technology Co. remains a leader in graphite impeller technology. Its commitment to quality and innovation ensures that its products meet the highest standards of performance and reliability.
Future Trends in Aluminum Degassing
What trends will shape the future of aluminum degassing? The industry is moving toward greater efficiency, sustainability, and automation. Graphite impellers will play a pivotal role in these advancements, as their unique properties align with emerging demands.
-
Integration with Smart Systems
The adoption of Industry 4.0 technologies is transforming aluminum processing. Smart degassing systems equipped with sensors and real-time monitoring capabilities are becoming more common. Graphite impellers, with their consistent performance and durability, complement these systems by ensuring reliable operation. For instance, sensors can monitor impeller wear and optimize rotation speeds, reducing downtime and maintenance costs. -
Focus on Sustainability
Environmental concerns are driving the development of eco-friendly degassing solutions. Graphite impellers, known for their long service life and energy efficiency, align with sustainability goals. Future innovations may include impellers made from recycled graphite or those designed for even lower energy consumption. These advancements will help industries reduce their carbon footprint while maintaining high production standards. -
Enhanced Material Science
Advances in material science will further improve the performance of graphite impellers. Researchers are exploring composite materials that combine graphite with other elements to enhance strength and thermal conductivity. These next-generation impellers could withstand even harsher conditions, making them suitable for cutting-edge applications in aerospace and renewable energy sectors. -
Customization and Modular Designs
The demand for tailored solutions is growing. Manufacturers are seeking impellers that can adapt to specific operational requirements. Modular designs, where components can be easily replaced or upgraded, are gaining traction. Graphite impellers with interchangeable parts could offer greater flexibility and cost savings for industrial facilities.
“The future of aluminum degassing lies in smarter, greener, and more adaptable technologies. Graphite impellers will remain at the forefront of this evolution, driving efficiency and innovation.” – Industry Insights Journal
As these trends unfold, graphite impellers will continue to set benchmarks for performance and sustainability. Companies like Ningbo VET Energy Technology Co. are well-positioned to lead this transformation, ensuring that their products meet the demands of tomorrow’s aluminum processing challenges.
Why Choose Ningbo VET Energy Technology Co. for Graphite Impellers
Expertise in Advanced Materials
Ningbo VET Energy Technology Co. stands as a leader in the field of advanced materials. The company specializes in producing high-end materials such as graphite, silicon carbide, and ceramics, which are integral to industries like photovoltaic, semiconductor, and metallurgy. Their deep understanding of material science enables them to design graphite impellers that excel in thermal resistance, chemical inertness, and durability. This expertise ensures that their products meet the rigorous demands of aluminum degassing processes.
The company’s focus on innovation drives its ability to deliver cutting-edge solutions. By leveraging years of research and development, Ningbo VET Energy Technology Co. has refined its manufacturing techniques to produce graphite impellers with superior performance. For example, their precision-engineered impellers optimize gas dispersion, enhancing the efficiency of hydrogen removal in molten aluminum. This level of expertise makes them a trusted partner for industries requiring reliable and high-performing materials.
“VET Energy is a tailor-made graphite product expert,” a statement that reflects their commitment to delivering customized solutions for diverse industrial needs.
Commitment to Quality and Innovation
Ningbo VET Energy Technology Co. prioritizes quality at every stage of production. The company adheres to the ISO 9001:2015 international quality management system, ensuring that each graphite impeller meets stringent quality standards. This commitment to excellence guarantees consistent performance and reliability, even in demanding industrial environments.
Innovation remains at the core of their operations. The company invests heavily in research to stay ahead of industry trends. For instance, they have developed proprietary surface treatments that enhance the durability and oxidation resistance of their graphite impellers. These advancements not only extend the service life of the impellers but also reduce maintenance costs for their clients. By combining quality with innovation, Ningbo VET Energy Technology Co. delivers products that set new benchmarks in the aluminum processing industry.
Customer-Centric Solutions
Ningbo VET Energy Technology Co. places a strong emphasis on understanding and addressing the unique needs of its clients. The company offers tailored solutions, allowing customers to select graphite impellers with specific dimensions, coatings, or performance characteristics. This flexibility ensures compatibility with a wide range of aluminum processing systems.
Their customer-centric approach extends beyond product customization. The company provides comprehensive support, from initial consultations to after-sales services. For example, they assist clients in selecting the most suitable impeller designs for their operations, ensuring optimal performance and efficiency. This dedication to customer satisfaction has earned them recognition and trust across various industries, including aerospace, automotive, and foundries.
By combining technical expertise, a commitment to quality, and a focus on customer needs, Ningbo VET Energy Technology Co. has established itself as a leading provider of graphite impellers. Their solutions not only enhance the efficiency of aluminum degassing but also contribute to long-term cost savings and sustainability for their clients.
Graphite impellers have proven to be the most effective solution for aluminum degassing, offering unmatched thermal resistance, chemical inertness, and durability. These qualities ensure efficient hydrogen removal, reduced contamination, and consistent performance, which are critical for producing high-quality aluminum alloys. By optimizing operational efficiency and minimizing material waste, graphite impellers help industries meet stringent quality standards while achieving cost savings. Ningbo VET Energy Technology Co. exemplifies excellence in this field, delivering innovative graphite impellers tailored to modern industrial needs. Their expertise ensures reliable solutions for aluminum processing challenges.
FAQ
What role do graphite impellers play in degassing systems?
Graphite impellers serve as essential components in aluminum degassing systems. They agitate molten aluminum, creating a controlled flow that facilitates the removal of hydrogen and other impurities. This process ensures the production of high-quality aluminum alloys with improved mechanical properties. By dispersing inert gases like argon or nitrogen into the molten metal, graphite impellers enhance the efficiency of degassing operations.
Why are graphite impellers preferred over other materials?
Graphite impellers outperform alternatives like ceramic or metal due to their unique combination of properties. They offer superior thermal conductivity, which helps maintain consistent temperatures in molten aluminum. Their chemical inertness prevents reactions with the metal, ensuring purity. Additionally, graphite impellers resist wear and abrasion, providing a longer service life and reducing operational costs.
How do graphite impellers contribute to the quality of aluminum alloys?
Graphite impellers ensure the removal of hydrogen and impurities from molten aluminum, which is critical for producing defect-free alloys. Their ability to create fine gas bubbles maximizes contact between the inert gas and the molten metal, enhancing impurity capture. This process results in aluminum alloys with improved strength, durability, and surface finish, meeting the stringent standards of industries like aerospace and automotive.
What makes graphite degassing rotors significant in the aluminum industry?
Graphite degassing rotors play a pivotal role in stirring, degassing, and purifying molten aluminum. They enhance the overall performance of the metal by efficiently removing dissolved gases and impurities. This purification process improves the quality of the final product, making it suitable for high-performance applications. Their reliability and efficiency make them indispensable in modern aluminum processing.
What properties do graphite rotors offer?
Graphite rotors, crafted from high-purity graphite material, provide excellent thermal conductivity, corrosion resistance, and mechanical strength. These properties enable them to withstand the harsh conditions of molten aluminum processing. Precise manufacturing and strict quality control ensure their reliable performance and long service life, making them a cost-effective choice for industrial applications.
How do graphite impellers reduce contamination risks?
Graphite impellers minimize contamination by resisting chemical reactions with molten aluminum. Their smooth surfaces prevent particle detachment during operation, unlike metal impellers that may corrode or degrade over time. This stability ensures the purity of the aluminum, reducing the risk of defects in the final product.
What characteristics set EuroGraphite’s graphite impellers apart?
EuroGraphite’s graphite impellers feature enhanced resistance to thermochemical stresses. This improvement is achieved through the use of specialized graphite types and vacuum impregnation with antioxidants. Their design and rotation parameters optimize gas bubble formation, ensuring efficient degassing and superior performance in aluminum processing systems.
How do graphite impellers support sustainability in industrial processes?
Graphite impellers contribute to sustainability by offering a long service life and reducing material waste. Their lightweight design lowers energy consumption during operation, enhancing the efficiency of degassing systems. Additionally, advanced manufacturing techniques minimize material loss, aligning with eco-friendly practices in industrial production.
Can graphite impellers handle high-temperature environments?
Yes, graphite impellers excel in high-temperature environments. They maintain structural integrity even when exposed to molten aluminum, which often exceeds 1,200°F. This thermal resistance ensures consistent performance and reliability, making them ideal for demanding applications in aluminum degassing.
Why should industries choose Ningbo VET Energy Technology Co. for graphite impellers?
Ningbo VET Energy Technology Co. offers graphite impellers designed with advanced materials and cutting-edge technology. Their products deliver exceptional thermal resistance, chemical inertness, and durability, ensuring reliable performance in aluminum degassing. The company’s commitment to innovation, quality, and customer-centric solutions makes it a trusted partner for industries seeking high-performance materials.