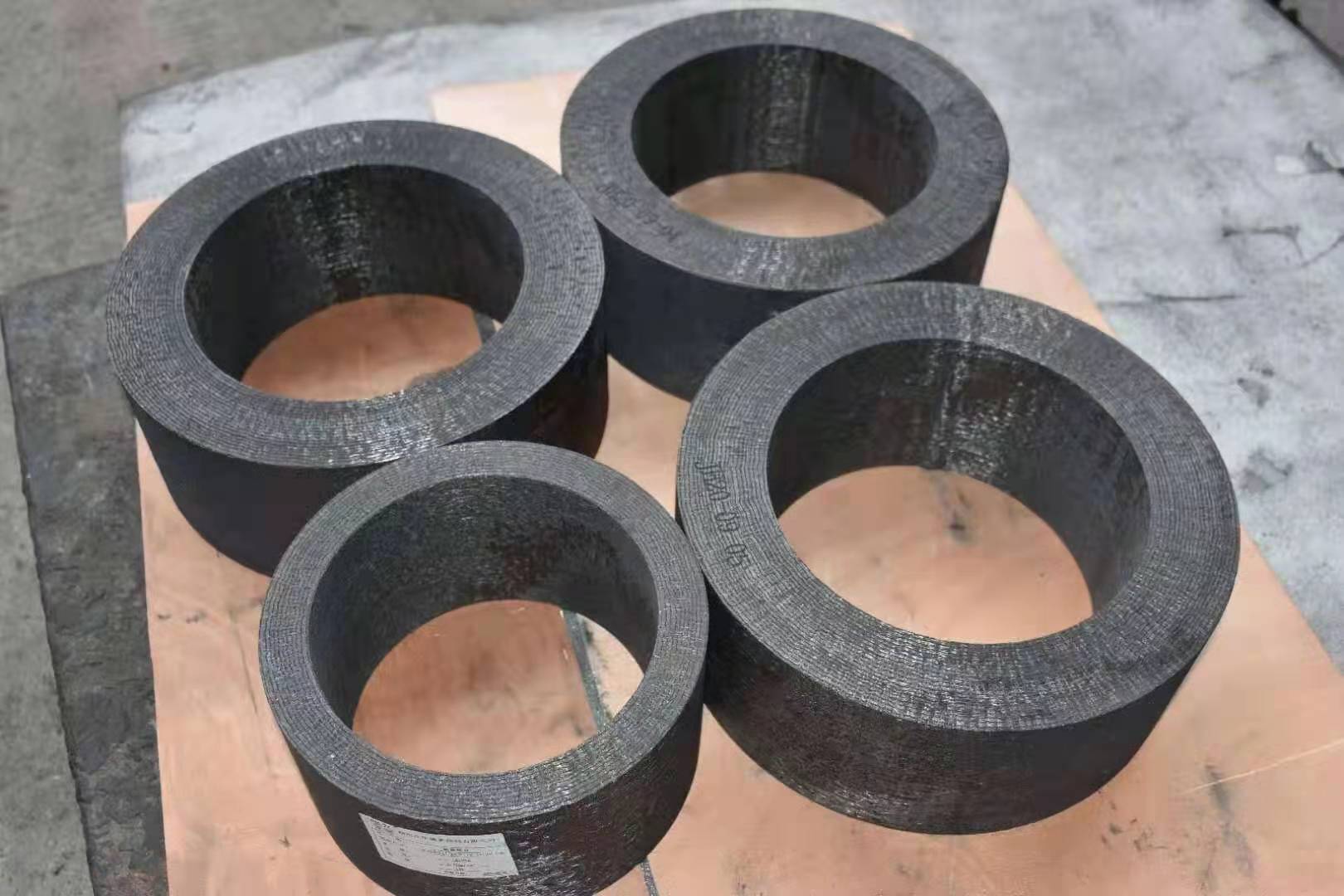
Carbon fiber composite stands out as a revolutionary material in modern engineering. It combines carbon fibers, known for their exceptional strength and stiffness, with a resin matrix that binds and shapes the structure. This synergy creates a material that is not only lightweight but also highly durable. Industries like aerospace, automotive, and renewable energy rely on its unique properties to enhance performance and efficiency. The high strength-to-weight ratio of carbon carbon composite makes it indispensable for applications where weight reduction and durability are critical.
Key Takeaways
- Carbon fiber composites are made of carbon fibers and a resin matrix, combining strength and lightweight properties for superior performance.
- The manufacturing process includes critical steps like precursor preparation, stabilization, carbonization, and resin infusion, each contributing to the composite’s durability.
- Carbon fiber composites excel in demanding applications, offering a high strength-to-weight ratio that is essential in industries like aerospace and automotive.
- Their resistance to corrosion and fatigue makes them ideal for use in harsh environments, extending the lifespan of components and reducing maintenance costs.
- The versatility of carbon fiber composites allows for complex designs, making them suitable for a wide range of applications, from sports equipment to renewable energy technologies.
- Sustainability is a key benefit, as carbon fiber composites can be recycled, reducing waste and supporting eco-friendly practices in manufacturing.
- Ningbo VET Energy Technology Co. leads in developing advanced carbon fiber composites, focusing on innovation and sustainability to meet industry demands.
What are the main components of Carbon Fiber Composite?
Carbon Fiber Composite consists of two primary components: carbon fibers and a resin matrix. These elements work together to create a material that is both strong and lightweight. Each component plays a distinct role in determining the composite’s overall performance and properties.
Carbon fibers
Composition and structure of carbon fibers
Carbon fibers are made of graphite sheets, where carbon atoms bond together in a hexagonal pattern. This unique structure provides exceptional strength and stiffness. The fibers are composed of small crystallites of graphite, which align along the fiber’s axis. This alignment enhances the material’s mechanical properties, making it ideal for demanding applications.
The composition of carbon fibers depends on the precursor material used during production. Common precursors include polyacrylonitrile (PAN), rayon, and pitch. Research has shown that the structure and composition of these precursors significantly influence the final properties of the carbon fibers. For example, PAN-based fibers are known for their high tensile strength, while pitch-based fibers offer superior thermal conductivity.
How carbon fibers are produced
The production of carbon fibers involves several steps, starting with the preparation of the precursor material. The precursor undergoes stabilization, a process that alters its chemical structure to make it thermally stable. Next, the material is subjected to carbonization, where it is heated to high temperatures in an inert atmosphere. This step removes non-carbon elements, leaving behind pure carbon fibers.
Surface treatment follows carbonization to improve the bonding between the fibers and the resin matrix. This step enhances the composite’s overall strength and durability. Finally, the fibers are sized with a protective coating to prevent damage during handling and processing.
Resin matrix
Types of resin used in Carbon Fiber Composite
The resin matrix binds the carbon fibers together and provides the composite with its shape. Common types of resin used in Carbon Fiber Composite include epoxy, vinyl ester, and polyester. Epoxy resins are widely preferred due to their excellent mechanical properties and resistance to environmental factors. Vinyl ester resins offer good chemical resistance, making them suitable for applications in harsh environments. Polyester resins are cost-effective and provide adequate performance for less demanding uses.
Role of the resin matrix in enhancing composite properties
The resin matrix plays a crucial role in distributing stress across the carbon fibers, ensuring the composite can withstand high loads. It also protects the fibers from environmental damage, such as moisture and UV exposure. By combining the flexibility of the resin with the strength of the carbon fibers, the composite achieves a balance of durability and lightweight performance.
In addition, the resin matrix contributes to the composite’s versatility. It allows manufacturers to mold the material into complex shapes, enabling its use in a wide range of industries. For instance, aerospace engineers rely on this adaptability to design lightweight yet robust aircraft components.
How is Carbon Fiber Composite manufactured?
The manufacturing process of Carbon Fiber Composite involves a series of precise steps. Each stage contributes to the creation of a material with exceptional strength, lightweight properties, and durability. Below is an overview of the key stages in the production process.
Precursor preparation
The journey begins with the selection and preparation of the precursor material. Polyacrylonitrile (PAN) is the most commonly used precursor due to its excellent carbonization properties. Other precursors, such as pitch and rayon, are also utilized but less frequently. The choice of precursor significantly influences the final properties of the carbon fibers.
Importance of the precursor in carbon fiber production
The precursor serves as the foundation for carbon fiber production. It determines the fiber’s mechanical properties, thermal stability, and overall performance. For instance, PAN-based precursors yield fibers with high tensile strength, while pitch-based precursors produce fibers with superior thermal conductivity. The preparation process involves spinning the precursor into long, thin fibers through a method called fiber spinning. This step ensures uniformity and consistency, which are critical for the subsequent stages.
Stabilization
Once the precursor fibers are prepared, they undergo stabilization. This step chemically alters the fibers to make them thermally stable and resistant to melting during high-temperature treatments.
The stabilization process and its role in production
Stabilization involves heating the fibers in an oxygen-rich environment at temperatures ranging from 200°C to 300°C. During this process, the atomic structure of the fibers transforms from linear bonding to a more thermally stable ladder-like bonding. Oxygen molecules from the air interact with the fibers, causing a rearrangement of their atomic structure. This step is crucial as it prepares the fibers for the intense heat of carbonization. Without stabilization, the fibers would lose their structural integrity during the next phase.
Carbonization
After stabilization, the fibers move on to carbonization. This stage involves exposing the fibers to extremely high temperatures in an inert atmosphere, typically above 1,000°C. The goal is to remove non-carbon elements and create a material predominantly composed of carbon atoms.
High-temperature treatment to form carbon fibers
During carbonization, the fibers are heated in an
Surface treatment
Surface treatment plays a vital role in enhancing the performance of Carbon Fiber Composite. This process focuses on improving the bonding between carbon fibers and the resin matrix, ensuring the composite achieves its maximum strength and durability.
Improving bonding between fibers and resin
The surface of carbon fibers is relatively inert, which can hinder effective adhesion to the resin matrix. To address this, manufacturers apply surface treatments that modify the fiber’s surface properties. These treatments often involve chemical or physical processes designed to increase surface roughness or introduce functional groups that enhance compatibility with the resin.
One common method involves oxidizing the fiber surface using gases like ozone or liquids such as nitric acid. This oxidation process introduces polar functional groups, such as carboxyl or hydroxyl groups, onto the fiber surface. These groups improve the chemical interaction between the fibers and the resin, resulting in a stronger bond.
Another approach includes plasma treatment, where the fibers are exposed to a plasma environment. This technique not only cleans the fiber surface but also activates it, further enhancing adhesion. By improving the bond between the fibers and the resin, surface treatment ensures the composite can withstand mechanical stresses and environmental challenges.
Resin infusion and curing
The final steps in the manufacturing process of Carbon Fiber Composite involve resin infusion and curing. These stages are critical for shaping the composite and solidifying its structure.
Application of resin to fibers
Resin infusion involves saturating the carbon fibers with a resin matrix. This step ensures that the resin thoroughly coats and penetrates the fiber layers, creating a uniform composite material. Manufacturers often use techniques like vacuum-assisted resin transfer molding (VARTM) or hand lay-up methods to achieve this.
In VARTM, the carbon fibers are placed in a mold, and a vacuum is applied to draw the resin into the fiber layers. This method minimizes air pockets and ensures even distribution of the resin. Proper resin application is essential for achieving the desired mechanical properties and structural integrity of the composite.
The curing process and its significance
After resin infusion, the composite undergoes curing, a process that solidifies the resin and bonds it to the fibers. Curing typically involves exposing the composite to heat or ultraviolet (UV) light, depending on the type of resin used. For example, epoxy resins often require elevated temperatures to initiate the curing reaction.
During curing, the resin undergoes a chemical transformation, changing from a liquid to a solid state. This transformation locks the carbon fibers in place, creating a rigid and durable structure. The curing process also enhances the composite’s resistance to environmental factors, such as moisture and temperature fluctuations.
By carefully controlling resin infusion and curing, manufacturers ensure that Carbon Fiber Composite achieves its optimal performance, making it suitable for demanding applications in industries like aerospace and automotive.
What are the key properties of Carbon Fiber Composite?
Strength and stiffness
Superior performance compared to traditional materials
Carbon Fiber Composite exhibits remarkable strength and stiffness, making it a superior choice over traditional materials like steel or aluminum. The carbon fibers within the composite align in a specific direction, allowing them to bear significant loads without deformation. This alignment enhances the material’s tensile strength, enabling it to withstand forces that would typically cause other materials to fail.
For example, in aerospace applications, engineers use Carbon Fiber Composite to construct aircraft wings and fuselages. These components endure immense stress during flight, yet the composite maintains its structural integrity. Its stiffness also ensures minimal flexing, which is crucial for maintaining aerodynamic efficiency. This combination of strength and stiffness makes the material indispensable for industries requiring high-performance solutions.
Lightweight nature
Benefits for weight-sensitive applications
One of the most notable properties of Carbon Fiber Composite is its lightweight nature. Despite its exceptional strength, the material weighs significantly less than metals like steel or titanium. This characteristic proves invaluable in industries where reducing weight is critical.
In the automotive sector, manufacturers use Carbon Fiber Composite to produce lightweight car frames and panels. By reducing the vehicle’s weight, they improve fuel efficiency and enhance overall performance. Similarly, in sports equipment, such as bicycles and tennis rackets, the lightweight nature of the composite allows athletes to achieve better speed and control.
The resin infusion process used in manufacturing further optimizes the material’s weight. Techniques like vacuum-assisted resin transfer molding (VARTM) minimize excess resin usage, ensuring the final product remains as light as possible. This careful balance between fiber and resin contributes to the composite’s unparalleled performance in weight-sensitive applications.
Resistance to corrosion and fatigue
Durability in challenging environments
Carbon Fiber Composite demonstrates excellent resistance to corrosion and fatigue, making it highly durable in harsh conditions. Unlike metals, which can corrode when exposed to moisture or chemicals, the composite remains unaffected due to its non-metallic nature. This property extends the lifespan of components made from the material, reducing maintenance costs and downtime.
In marine environments, for instance, Carbon Fiber Composite is used to construct boat hulls and underwater structures. These applications demand materials that can withstand constant exposure to saltwater without degrading. The composite’s resistance to corrosion ensures reliable performance over time.
Additionally, the material resists fatigue caused by repeated stress cycles. Traditional materials often weaken and fail under such conditions, but Carbon Fiber Composite retains its strength and functionality. This durability makes it a preferred choice for applications like wind turbine blades, which endure continuous mechanical stress in varying weather conditions.
Thermal and electrical conductivity
Unique characteristics of Carbon Fiber Composite
Carbon Fiber Composite exhibits unique thermal and electrical conductivity properties, setting it apart from many traditional materials. These characteristics stem from the inherent structure of carbon fibers, which consist of graphite sheets where carbon atoms align in a hexagonal pattern. This alignment facilitates the movement of electrons, contributing to the material’s conductivity.
In terms of thermal conductivity, Carbon Fiber Composite demonstrates varying performance depending on the type of precursor used during production. For instance, pitch-based carbon fibers excel in transferring heat due to their high degree of graphitization. This property makes the composite suitable for applications requiring efficient heat dissipation, such as electronic components or heat exchangers. Engineers often utilize this capability to prevent overheating in devices, ensuring optimal performance and longevity.
The electrical conductivity of Carbon Fiber Composite also offers significant advantages. The material can conduct electricity, albeit at a lower level compared to metals like copper or aluminum. This feature proves beneficial in industries like aerospace and automotive, where lightweight conductive materials are essential. For example, Carbon Fiber Composite is used in electromagnetic shielding to protect sensitive equipment from interference. Its conductivity also enables its use in applications like lightning strike protection for aircraft, where it safely dissipates electrical charges.
Despite these benefits, the conductivity of Carbon Fiber Composite can be tailored to meet specific requirements. Manufacturers achieve this by adjusting the resin matrix or incorporating additional materials. For instance, adding insulating resins can reduce conductivity, making the composite suitable for non-conductive applications. Conversely, enhancing the graphitization process during carbonization can increase conductivity for specialized uses.
These thermal and electrical properties, combined with the material’s lightweight and durable nature, make Carbon Fiber Composite a versatile choice for modern engineering challenges. Its adaptability ensures its continued relevance across industries seeking innovative solutions.
What are the advantages of Carbon Fiber Composite?
High performance in demanding applications
Carbon fiber composite excels in applications requiring exceptional strength and durability. Its high tensile strength surpasses that of traditional materials like steel and aluminum. For instance, carbon fiber can be up to five times stronger than steel and twice as stiff, while weighing significantly less. This strength-to-weight ratio makes it ideal for industries such as aerospace and automotive, where performance under stress is critical.
In aerospace, engineers use carbon fiber composite to construct aircraft wings and fuselages. These components endure extreme forces during flight, yet the material maintains its structural integrity. Similarly, in the automotive sector, manufacturers rely on carbon fiber to create lightweight yet robust car frames. This reduces vehicle weight, enhancing speed and fuel efficiency without compromising safety. The material’s ability to withstand high loads while remaining lightweight ensures its dominance in demanding environments.
Versatility in design and manufacturing
Carbon fiber composite offers unparalleled flexibility in design and manufacturing. Its adaptability allows engineers to mold it into complex shapes, enabling innovative solutions across various industries. Unlike metals, which often require extensive machining, carbon fiber can be tailored to specific dimensions with minimal waste.
For example, in the sports industry, manufacturers use carbon fiber to produce high-performance equipment like bicycles, tennis rackets, and golf clubs. These items benefit from the material’s lightweight nature and strength, improving user performance. In renewable energy, carbon fiber’s versatility supports the creation of large wind turbine blades, which demand both precision and durability.
The manufacturing process also enhances its versatility. Techniques like vacuum-assisted resin transfer molding (VARTM) ensure uniformity and precision, making it suitable for intricate designs. This adaptability extends to industries like robotics and medical devices, where custom shapes and sizes are essential. Carbon fiber composite’s ability to meet diverse design requirements underscores its value in modern engineering.
Sustainability and recyclability
Carbon fiber composite contributes to sustainability through its long lifespan and recyclability. Its resistance to corrosion and fatigue reduces the need for frequent replacements, minimizing waste over time. Unlike traditional materials, carbon fiber retains its properties even after prolonged use, making it a cost-effective and environmentally friendly choice.
Recycling processes for carbon fiber have advanced significantly. Manufacturers now recover fibers from used composites, repurposing them for new applications. This reduces the environmental impact of production and aligns with global efforts to promote sustainable practices. For instance, recycled carbon fiber finds use in automotive parts, consumer goods, and construction materials.
Additionally, the lightweight nature of carbon fiber composite supports energy efficiency. In transportation, lighter vehicles consume less fuel, reducing greenhouse gas emissions. Wind turbines made from carbon fiber generate renewable energy, further contributing to environmental conservation. By combining performance with sustainability, carbon fiber composite addresses the growing demand for eco-friendly materials in various industries.
What are the applications of Carbon Fiber Composite?
Carbon Fiber Composite has transformed modern industries with its unique combination of strength, lightweight properties, and versatility. Its applications span across sectors where performance, efficiency, and durability are paramount.
Aerospace industry
Use in aircraft structures and components
The aerospace industry relies heavily on Carbon Fiber Composite for constructing critical components like aircraft wings, fuselages, and tail sections. Engineers value its high strength-to-weight ratio, which allows aircraft to achieve superior performance while reducing overall weight. This reduction directly improves fuel efficiency and increases payload capacity.
For example, commercial aircraft manufacturers use Carbon Fiber Composite to design lighter yet robust wings that endure immense aerodynamic forces during flight. Fighter jets and spacecraft also benefit from this material, as it withstands extreme conditions, including high stress and temperature fluctuations. Its stiffness ensures that structural components maintain their shape, enhancing aerodynamic efficiency and safety.
Fact: Carbon Fiber Composite is up to five times stronger than steel while weighing significantly less, making it indispensable for aerospace applications.
Automotive industry
Lightweight materials for improved fuel efficiency
In the automotive sector, Carbon Fiber Composite plays a pivotal role in creating lightweight vehicles that consume less fuel. Manufacturers incorporate it into car frames, body panels, and interior components to reduce weight without compromising safety or durability. This material enables automakers to meet stringent environmental regulations by improving fuel efficiency and lowering carbon emissions.
High-performance sports cars often feature Carbon Fiber Composite in their chassis and exterior designs. Its strength allows these vehicles to handle high speeds and sharp turns while maintaining structural integrity. Electric vehicles (EVs) also benefit from this material, as the reduced weight extends battery range and enhances overall efficiency.
Example: A luxury sports car manufacturer uses Carbon Fiber Composite for its monocoque chassis, achieving a lightweight yet rigid structure that enhances speed and handling.
Sports and recreation
High-performance equipment like bicycles and tennis rackets
Athletes and sports enthusiasts benefit from Carbon Fiber Composite in high-performance equipment. Its lightweight nature and stiffness improve speed, control, and precision, giving users a competitive edge. Bicycles made from this material are easier to maneuver and accelerate, making them ideal for professional racing and mountain biking.
Tennis rackets constructed with Carbon Fiber Composite offer enhanced power and reduced vibration, improving player performance and comfort. Golf clubs, fishing rods, and hockey sticks also utilize this material to achieve optimal balance and durability. Its adaptability allows manufacturers to create custom designs tailored to specific sports, ensuring maximum efficiency.
Insight: Carbon Fiber Composite’s ability to resist deformation under stress makes it a preferred choice for sports equipment that demands consistent performance.
Renewable energy
Role in wind turbine blades and green technologies
Carbon Fiber Composite plays a pivotal role in advancing renewable energy technologies. Its lightweight nature and exceptional strength make it an ideal material for constructing wind turbine blades. These blades must endure constant mechanical stress and harsh environmental conditions, such as strong winds and temperature fluctuations. Carbon Fiber Composite ensures durability while maintaining the structural integrity of the blades, even under extreme loads.
The high stiffness of Carbon Fiber Composite allows wind turbine blades to maintain their aerodynamic shape, which is crucial for efficient energy generation. Engineers design longer and more efficient blades using this material, increasing the energy output of wind turbines. For instance, modern wind turbines with blades made from Carbon Fiber Composite can generate significantly more electricity compared to those using traditional materials like fiberglass.
Beyond wind turbines, Carbon Fiber Composite contributes to other green technologies. It is used in the production of lightweight components for solar panels and energy storage systems. By reducing the weight of these systems, manufacturers improve their transportability and installation efficiency. Additionally, the material’s resistance to corrosion ensures long-term performance, making it a sustainable choice for renewable energy applications.
Fact: Wind turbine blades made from Carbon Fiber Composite can weigh up to 30% less than those made from traditional materials, enabling higher efficiency and reduced operational costs.
Medical and industrial uses
Applications in prosthetics and robotics
Carbon Fiber Composite has revolutionized the medical and industrial sectors with its unique properties. In prosthetics, the material provides lightweight yet strong solutions for artificial limbs. Patients benefit from improved mobility and comfort due to the reduced weight of prosthetic devices. The high stiffness of Carbon Fiber Composite ensures that these devices can withstand repeated stress without deforming, offering long-lasting performance.
Robotics also relies heavily on Carbon Fiber Composite for creating advanced components. Robotic arms and joints require materials that combine strength with precision. Carbon Fiber Composite meets these demands by offering high tensile strength and low thermal expansion. This ensures that robotic systems maintain accuracy and reliability, even in demanding environments.
In industrial applications, Carbon Fiber Composite enhances the performance of machinery and tools. Its resistance to fatigue and corrosion makes it suitable for use in harsh conditions, such as manufacturing plants and offshore facilities. For example, robotic systems used in underwater exploration often incorporate Carbon Fiber Composite to ensure durability and efficiency.
Insight: Prosthetic limbs made from Carbon Fiber Composite are not only lighter but also more durable, enabling users to perform daily activities with greater ease and confidence.
How does Ningbo VET Energy Technology Co. contribute to the Carbon Fiber Composite industry?
Expertise in advanced materials
Ningbo VET Energy Technology Co. has established itself as a leader in the field of advanced materials. The company specializes in developing and manufacturing high-performance carbon fiber composites tailored to meet the needs of various industries. By leveraging cutting-edge technology and extensive research, it ensures that its products deliver exceptional strength, stiffness, and lightweight properties.
The team at Ningbo VET Energy Technology Co. possesses deep knowledge of carbon fiber production and composite manufacturing processes. This expertise enables the company to create innovative solutions that outperform traditional materials like steel and aluminum. For instance, its carbon fiber composites are widely used in aerospace and automotive applications, where superior mechanical properties are essential.
Fact: Carbon fiber composites are up to five times stronger than steel while being significantly lighter, making them ideal for industries requiring high performance.
Commitment to innovation and sustainability
Innovation drives the success of Ningbo VET Energy Technology Co. The company continuously invests in research and development to improve the performance and versatility of its carbon fiber composites. By staying ahead of industry trends, it introduces new products that address the evolving demands of modern engineering.
Sustainability remains a core focus for Ningbo VET Energy Technology Co. The company adopts eco-friendly practices throughout its production processes, minimizing waste and reducing environmental impact. It also supports recycling initiatives by developing methods to recover and repurpose carbon fibers from used composites. These efforts align with global goals to promote sustainable materials and reduce carbon emissions.
Insight: Recycled carbon fiber composites are increasingly used in automotive parts and consumer goods, contributing to a circular economy.
Products and solutions for various industries
Ningbo VET Energy Technology Co. offers a diverse range of carbon fiber composite products designed for multiple industries. Its solutions cater to sectors such as aerospace, automotive, renewable energy, sports equipment, and medical devices. Each product is engineered to meet specific performance requirements, ensuring reliability and efficiency.
In the aerospace industry, the company provides lightweight yet durable composites for aircraft structures and components. Automotive manufacturers rely on its materials to produce fuel-efficient vehicles with reduced emissions. In renewable energy, its carbon fiber composites enhance the performance of wind turbine blades, enabling higher energy output.
The versatility of Ningbo VET Energy Technology Co.’s products extends to sports and recreation. High-performance bicycles, tennis rackets, and golf clubs made from its composites offer athletes improved speed, control, and durability. Additionally, the medical sector benefits from its lightweight and strong materials, which are used in prosthetics and robotic systems.
Example: Wind turbine blades made from Ningbo VET Energy Technology Co.’s carbon fiber composites weigh less and last longer, improving efficiency and reducing operational costs.
By combining expertise, innovation, and a commitment to sustainability, Ningbo VET Energy Technology Co. plays a pivotal role in advancing the carbon fiber composite industry. Its products empower industries to achieve greater performance while addressing environmental challenges.
Contact information
Ningbo VET Energy Technology Co. provides comprehensive support and solutions for industries utilizing carbon fiber composites. The company welcomes inquiries and collaborations from businesses seeking advanced materials for their projects. Below are the details to reach out:
- Phone: 86-1891 1596 392
- Email: yeah@china-vet.com
- Address: No. 777, Zhongguan West Road, Zhenhai District, Ningbo, Zhejiang, 315201, China
- Contact Person: General Manager Ye
For more information about their products and services, visit their official website: https://www.cnvetenergy.com/. The website offers detailed insights into their expertise, innovative solutions, and commitment to sustainability.
Tip: Businesses in aerospace, automotive, renewable energy, and other sectors can explore tailored solutions by contacting Ningbo VET Energy Technology Co. directly. Their team of experts ensures high-quality materials and exceptional customer service.
Ningbo VET Energy Technology Co. remains dedicated to advancing the carbon fiber composite industry. Reach out today to discover how their products can elevate your projects.
Carbon Fiber Composite represents a breakthrough in material science, combining carbon fibers and a resin matrix to deliver unmatched strength, lightweight properties, and versatility. The meticulous manufacturing process, from precursor preparation to resin infusion, ensures its superior performance. Industries such as aerospace, automotive, and renewable energy rely on this material for its durability and efficiency. Ningbo VET Energy Technology Co. continues to drive innovation in the carbon fiber industry, offering advanced solutions while prioritizing sustainability. Their expertise supports industries in achieving high-performance goals with eco-friendly materials.
FAQ
What makes carbon fiber composites unique compared to traditional materials?
Carbon fiber composites stand out due to their exceptional strength, stiffness, and lightweight properties. Unlike traditional materials like steel or aluminum, carbon fiber composites offer a superior strength-to-weight ratio. This makes them ideal for industries such as aerospace, automotive, and renewable energy, where reducing weight without compromising durability is critical. Additionally, their resistance to corrosion and fatigue ensures long-term performance in challenging environments.
Fact: Carbon fiber composites can be up to five times stronger than steel while weighing significantly less.
Are carbon fiber composites safe for medical applications?
Yes, carbon fiber composites are safe for medical use. These materials are non-toxic and biocompatible, making them suitable for prosthetics, implants, and surgical instruments. They also allow X-rays to pass through, which aids in medical imaging and diagnostics. This property ensures that carbon fiber-based devices do not interfere with medical procedures.
Example: Prosthetic limbs made from carbon fiber composites provide patients with lightweight and durable solutions, enhancing mobility and comfort.
How are carbon fiber composites used in the aerospace industry?
The aerospace industry relies on carbon fiber composites for constructing aircraft wings, fuselages, and other structural components. These materials reduce the overall weight of aircraft, improving fuel efficiency and payload capacity. Their high stiffness ensures that components maintain their shape under extreme aerodynamic forces, enhancing safety and performance.
Insight: Modern commercial aircraft incorporate carbon fiber composites to achieve lighter designs, resulting in significant cost savings on fuel.
Why are carbon fiber composites preferred in sports equipment?
Carbon fiber composites are widely used in sports equipment due to their lightweight and high-performance characteristics. They enhance speed, control, and durability in products like bicycles, tennis rackets, and golf clubs. Athletes benefit from the material’s ability to resist deformation under stress, ensuring consistent performance during use.
Example: Professional cyclists often choose carbon fiber bicycles for their superior maneuverability and acceleration.
Can carbon fiber composites be recycled?
Yes, carbon fiber composites can be recycled. Advanced recycling methods recover fibers from used composites, repurposing them for new applications. This process reduces waste and supports sustainability efforts. Recycled carbon fibers are often used in automotive parts, consumer goods, and construction materials.
Fact: Recycling carbon fiber composites contributes to a circular economy by minimizing environmental impact and promoting resource efficiency.
What role do carbon fiber composites play in renewable energy?
Carbon fiber composites play a crucial role in renewable energy, particularly in the construction of wind turbine blades. Their lightweight nature and high strength allow for longer and more efficient blades, increasing energy output. The material’s resistance to environmental factors ensures durability, even in harsh conditions.
Insight: Wind turbine blades made from carbon fiber composites weigh less and last longer, reducing operational costs and improving efficiency.
How do carbon fiber composites contribute to automotive innovation?
In the automotive industry, carbon fiber composites enable the production of lightweight vehicles that consume less fuel. Manufacturers use these materials in car frames, body panels, and interior components to improve fuel efficiency and reduce emissions. High-performance sports cars and electric vehicles benefit significantly from the reduced weight and enhanced structural integrity.
Example: A luxury sports car manufacturer uses carbon fiber composites in its chassis to achieve a lightweight yet rigid structure, enhancing speed and handling.
What are the thermal and electrical properties of carbon fiber composites?
Carbon fiber composites exhibit unique thermal and electrical conductivity properties. Pitch-based carbon fibers excel in heat transfer, making them suitable for applications like electronic components and heat exchangers. The material also conducts electricity, which proves beneficial in aerospace and automotive industries for electromagnetic shielding and lightning strike protection.
Fact: Engineers can tailor the conductivity of carbon fiber composites by adjusting the resin matrix or production process to meet specific application needs.
Are carbon fiber composites resistant to environmental damage?
Yes, carbon fiber composites resist environmental damage, including corrosion and fatigue. Unlike metals, they do not corrode when exposed to moisture or chemicals. This property makes them ideal for marine environments and other harsh conditions. Their resistance to fatigue ensures long-term reliability, even under repeated stress cycles.
Example: Marine vessels and underwater structures use carbon fiber composites to withstand constant exposure to saltwater without degrading.
How does Ningbo VET Energy Technology Co. support the carbon fiber composite industry?
Ningbo VET Energy Technology Co. specializes in developing high-performance carbon fiber composites for various industries. The company focuses on innovation and sustainability, offering advanced solutions tailored to meet specific needs. Its products enhance performance in sectors like aerospace, automotive, renewable energy, and medical devices.
Tip: Businesses seeking reliable and eco-friendly carbon fiber composite solutions can contact Ningbo VET Energy Technology Co. for expert guidance and support.