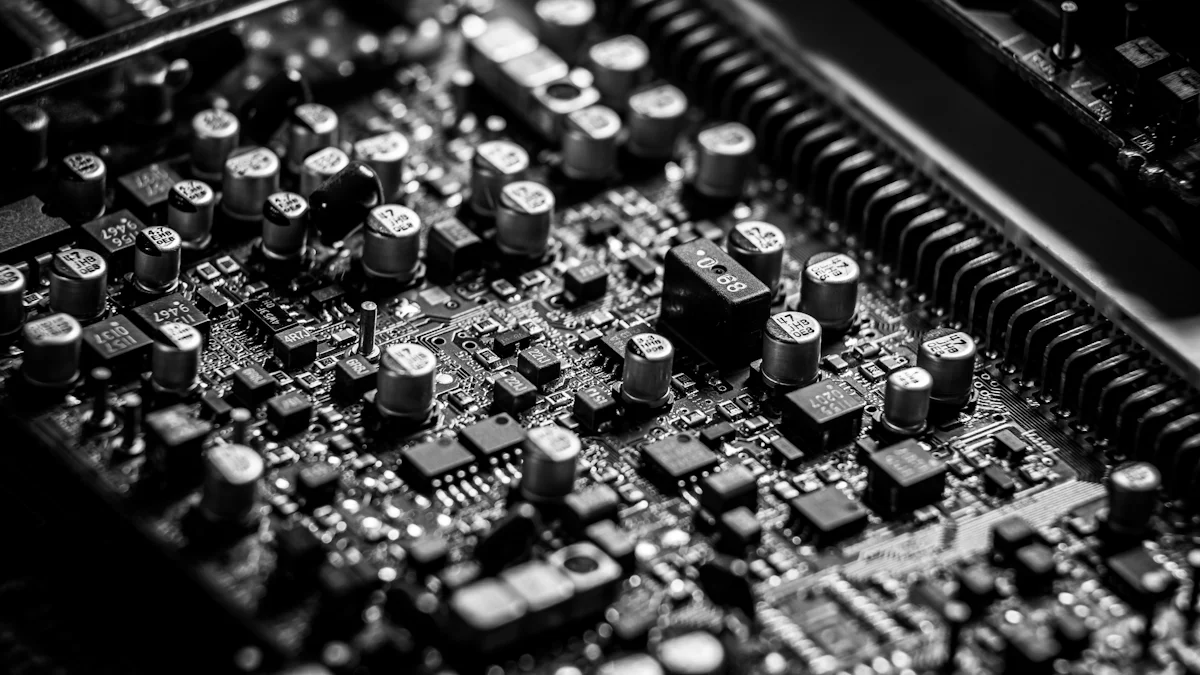
Epitaxial barrel susceptors play a critical role in semiconductor manufacturing by providing a stable and efficient platform for epitaxial growth. These components ensure precise deposition of materials, which is essential for creating high-quality semiconductor wafers. Recent advancements in this technology have introduced innovative materials and designs that enhance performance and reliability. These improvements address the increasing demand for high-performance semiconductors, driven by the rapid growth of advanced electronics and computing applications. By optimizing wafer quality and production efficiency, these technologies continue to shape the future of semiconductor fabrication.
Key Takeaways
- Epitaxial barrel susceptors are crucial for achieving high-quality semiconductor wafers through precise material deposition.
- Recent innovations in materials, such as SiC-coated graphite, enhance durability and thermal stability, leading to improved wafer quality.
- Design advancements, including vertical barrel reactors, optimize heat distribution and gas flow, ensuring uniform deposition across wafers.
- Integration with next-generation reactor systems increases production efficiency and accommodates larger wafer sizes, meeting industry demands.
- Automation in loading and unloading processes reduces human error and streamlines production, enhancing overall efficiency.
- Ongoing research in material science and reactor design is essential to overcome current limitations and drive future advancements in semiconductor manufacturing.
- Collaboration between academia and industry will accelerate innovation, ensuring the continued evolution of epitaxial barrel susceptor technologies.
Overview of Epitaxial Barrel Susceptor Technologies
Basics of Epitaxial Growth
Epitaxial growth serves as a cornerstone in semiconductor manufacturing. This process involves depositing a crystalline layer on a substrate, ensuring the new layer aligns with the substrate’s atomic structure. Manufacturers rely on epitaxial growth to produce high-quality wafers with precise electrical properties. These wafers form the foundation for advanced electronic devices, including microprocessors and memory chips.
The process typically occurs in controlled environments within epitaxial reactors. These reactors maintain specific temperatures and gas compositions to achieve uniform deposition. By carefully managing these conditions, engineers can create layers with exceptional purity and structural integrity. This precision is essential for meeting the stringent requirements of modern semiconductor applications.
Role and Importance of Barrel Susceptors in Epitaxial Reactors
Barrel susceptors play a pivotal role in epitaxial reactors. These components hold the wafers during the deposition process, ensuring stability and uniformity. Their design allows for even heat distribution, which is critical for achieving consistent epitaxial growth across all wafers. Without this uniformity, the resulting semiconductor devices may suffer from performance inconsistencies.
Modern barrel susceptors often feature advanced materials like SiC-coated graphite. These materials withstand high temperatures and resist chemical degradation, making them ideal for demanding manufacturing environments. Additionally, barrel susceptors contribute to optimizing wafer throughput. By accommodating multiple wafers simultaneously, they enhance production efficiency while maintaining quality standards.
Recent innovations have further improved the functionality of barrel susceptors. For instance, vertical barrel reactors now offer better deposition uniformity, addressing challenges related to wafer thickness and surface quality. These advancements highlight the importance of barrel susceptors in pushing the boundaries of semiconductor technology.
Recent Advancements in Epitaxial Barrel Susceptor Technologies
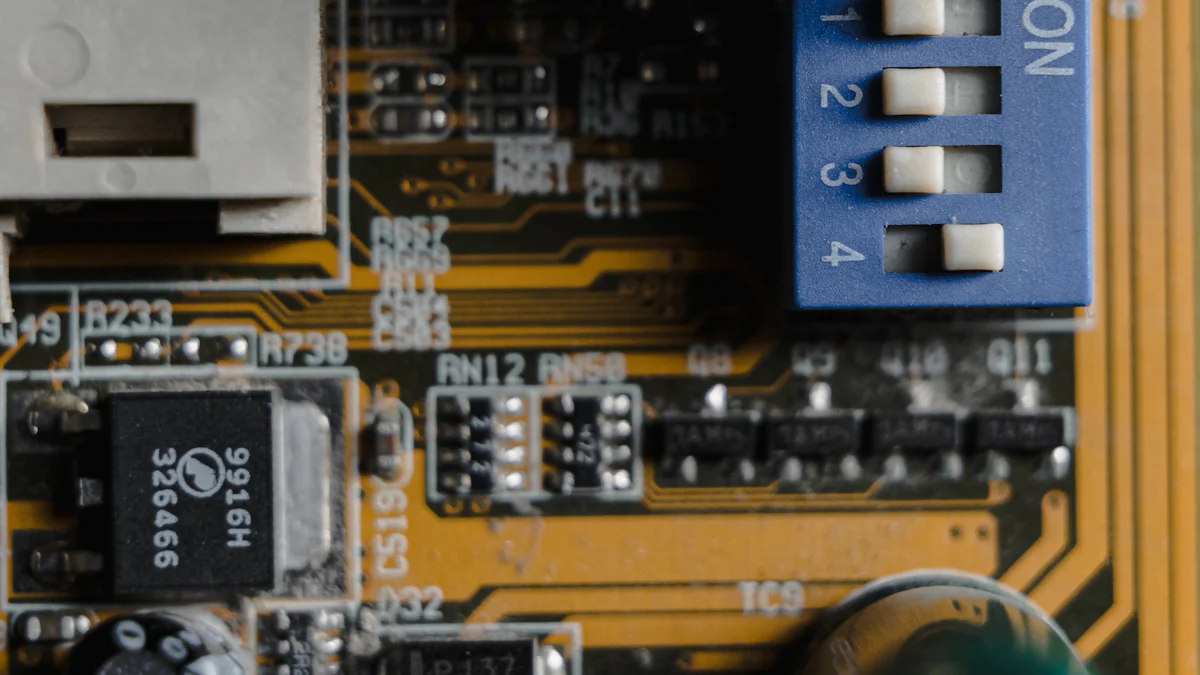
Material Innovations in Barrel Susceptors
Recent advancements in materials have significantly enhanced the performance of the epitaxial barrel susceptor. Manufacturers now use SiC-coated graphite as a standard material due to its ability to endure extreme temperatures and resist chemical wear. This material ensures durability during high-temperature processes, which are essential for semiconductor fabrication. The improved thermal stability of SiC-coated graphite also contributes to consistent wafer quality.
In addition to SiC coatings, researchers have explored alternative materials to further optimize performance. For example, advanced composites with higher thermal conductivity have been introduced. These materials improve heat distribution across the susceptor, ensuring uniform deposition during epitaxial growth. Such innovations address challenges related to wafer thickness variations and surface irregularities.
Material innovations also focus on reducing contamination risks. Impurities can compromise wafer quality, leading to defects in semiconductor devices. By using materials with lower outgassing properties, manufacturers minimize contamination, resulting in higher yields and better device reliability. These advancements demonstrate how material science continues to drive improvements in epitaxial barrel susceptor technologies.
Design Improvements for Enhanced Performance
The design of the epitaxial barrel susceptor has undergone significant refinement to meet the demands of modern semiconductor manufacturing. Engineers have optimized the geometry of susceptors to enhance heat distribution and improve wafer alignment. These changes ensure that each wafer receives uniform thermal exposure, which is critical for achieving consistent epitaxial growth.
Vertical barrel reactor designs represent a major breakthrough in this area. These reactors incorporate susceptors with improved vertical configurations, allowing for better gas flow and deposition uniformity. This innovation addresses previous limitations in horizontal designs, where uneven gas distribution often led to inconsistent results.
Another notable improvement involves the integration of advanced cooling mechanisms. Enhanced cooling systems prevent overheating, which can degrade the susceptor material and affect wafer quality. By maintaining optimal operating temperatures, these designs extend the lifespan of the susceptor and reduce maintenance costs.
Automation has also played a role in design advancements. Modern susceptors now feature automated loading and unloading systems, which improve efficiency and reduce the risk of human error. These systems streamline production processes, enabling manufacturers to meet the growing demand for high-performance semiconductors.
Integration with Next-Generation Reactor Systems
The epitaxial barrel susceptor has evolved to align with next-generation reactor systems, which prioritize efficiency and scalability. Double barrel reactors, for instance, utilize two parallel systems to increase throughput without compromising quality. This design innovation allows manufacturers to produce more wafers in less time, addressing the industry’s need for higher production capacity.
Next-generation reactors also incorporate advanced monitoring technologies. Sensors embedded within the susceptor provide real-time data on temperature, gas flow, and deposition rates. This information enables precise control over the epitaxial growth process, ensuring optimal conditions for wafer production.
Larger wafer sizes have become a focus in recent years, and barrel susceptors have adapted accordingly. Modern susceptors can accommodate larger diameters, which increases the output per batch. This capability supports the industry’s shift toward larger wafers, which offer greater efficiency in semiconductor manufacturing.
The integration of molecular beam epitaxy (MBE) and metalorganic chemical vapor deposition (MOCVD) techniques has further expanded the capabilities of barrel reactors. These advanced growth methods enable the production of complex semiconductor structures, paving the way for innovations in microelectronics and optoelectronics. By aligning with these cutting-edge technologies, the epitaxial barrel susceptor remains a cornerstone of semiconductor fabrication.
Benefits of Advanced Epitaxial Barrel Susceptor Technologies
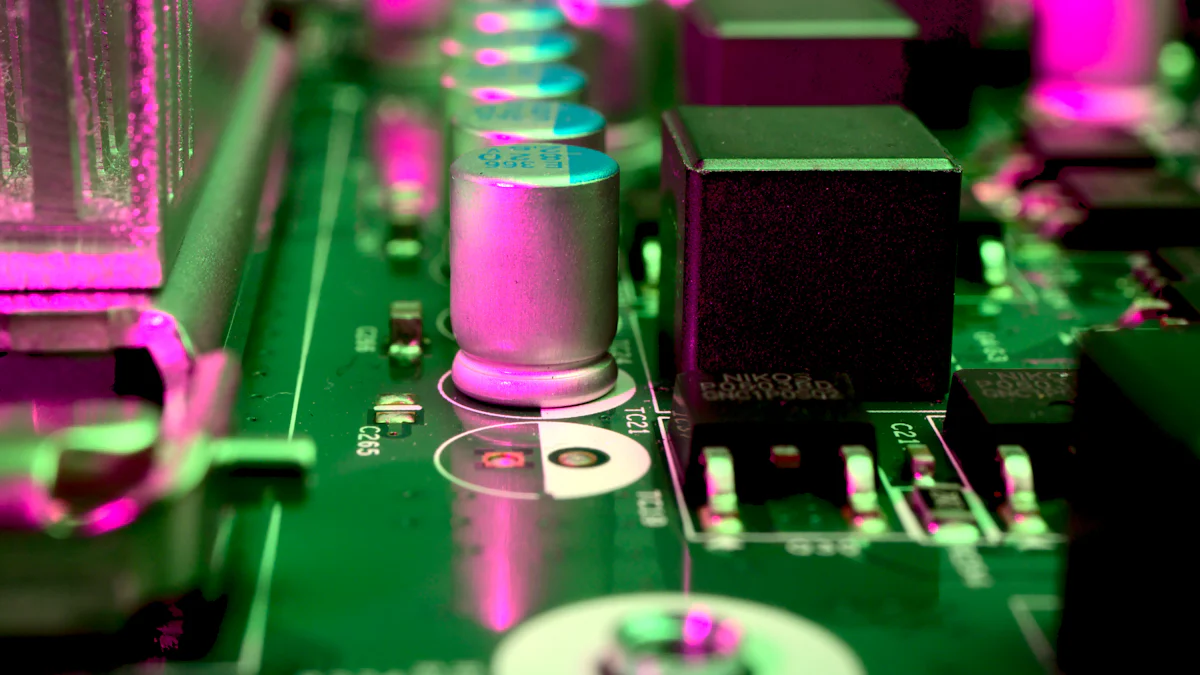
Improved Wafer Quality and Uniformity
Advanced epitaxial barrel susceptor technologies have significantly improved wafer quality. These innovations ensure precise control over temperature and gas flow during the epitaxial growth process. Consistent thermal distribution across the susceptor minimizes defects in the crystalline layers. This precision results in wafers with superior structural integrity and electrical properties.
Uniformity in wafer thickness has also seen remarkable advancements. Modern susceptors, particularly those used in vertical barrel reactors, enhance deposition uniformity. This improvement addresses challenges related to surface irregularities, which can affect the performance of semiconductor devices. By achieving consistent wafer quality, manufacturers meet the stringent requirements of advanced electronics.
Enhanced Energy Efficiency and Cost-Effectiveness
Energy efficiency has become a critical focus in semiconductor manufacturing. Advanced epitaxial barrel susceptor designs optimize heat retention and reduce energy consumption. Materials like SiC-coated graphite improve thermal stability, allowing reactors to operate efficiently at high temperatures. This efficiency lowers operational costs while maintaining production quality.
Cost-effectiveness extends beyond energy savings. The durability of modern susceptors reduces the frequency of replacements, cutting maintenance expenses. Automated systems integrated into these technologies streamline production processes. By minimizing downtime and human error, manufacturers achieve higher throughput at reduced costs.
Support for Advanced Semiconductor Applications
The evolution of epitaxial barrel susceptor technologies supports the development of advanced semiconductor applications. These technologies enable the production of wafers with exceptional purity and precision. Such wafers are essential for high-performance devices like microprocessors, memory chips, and optoelectronic components.
Larger wafer sizes, made possible by modern susceptors, cater to the growing demand for scalable semiconductor solutions. These larger wafers enhance production efficiency, meeting the needs of industries such as artificial intelligence and telecommunications. Additionally, the integration of advanced growth methods like molecular beam epitaxy expands the capabilities of barrel reactors. This progress drives innovation in next-generation semiconductor devices.
Challenges and Future Directions
Current Limitations in Barrel Susceptor Technologies
Despite significant advancements, epitaxial barrel susceptor technologies face several limitations that hinder their full potential. One major challenge lies in material degradation during prolonged high-temperature operations. Even with durable materials like SiC-coated graphite, repeated thermal cycling can lead to wear and tear, reducing the lifespan of the susceptor. This issue increases maintenance requirements and operational costs for manufacturers.
Another limitation involves achieving absolute uniformity in wafer deposition. While vertical barrel reactors have improved deposition consistency, minor variations in gas flow or temperature distribution can still result in defects. These inconsistencies affect wafer quality, especially for applications requiring ultra-precise semiconductor structures.
The scalability of barrel susceptors also presents challenges. As the industry shifts toward larger wafer sizes, adapting susceptor designs to accommodate these dimensions without compromising performance remains a complex task. Larger susceptors often require enhanced thermal management systems, which can complicate reactor designs and increase production costs.
Contamination risks further complicate the manufacturing process. Impurities introduced during epitaxial growth can compromise wafer quality, leading to defects in semiconductor devices. Although modern materials reduce outgassing, eliminating contamination entirely remains a persistent challenge.
Future Research and Development Opportunities
Future research offers promising opportunities to address these challenges and push the boundaries of epitaxial barrel susceptor technologies. Material science will likely play a pivotal role in overcoming current limitations. Researchers could develop new composite materials with superior thermal stability and resistance to chemical degradation. These materials would extend the lifespan of susceptors and improve their performance under extreme conditions.
Innovations in reactor design present another avenue for improvement. Engineers may explore advanced geometries and gas flow mechanisms to achieve near-perfect deposition uniformity. Enhanced simulation tools could aid in optimizing reactor configurations, ensuring consistent results across all wafers.
Automation and artificial intelligence (AI) hold significant potential for advancing susceptor technologies. AI-driven monitoring systems could provide real-time data on temperature, gas flow, and deposition rates. This data would enable precise adjustments during the epitaxial growth process, minimizing defects and maximizing efficiency.
The integration of next-generation growth techniques, such as atomic layer deposition (ALD) and hybrid epitaxy methods, could further expand the capabilities of barrel reactors. These techniques would allow for the production of more complex semiconductor structures, meeting the demands of emerging technologies like quantum computing and advanced optoelectronics.
Collaboration between academia and industry will be essential for driving innovation. Joint research initiatives could accelerate the development of cutting-edge solutions, ensuring that epitaxial barrel susceptor technologies continue to evolve. By addressing current challenges and exploring new possibilities, the semiconductor industry can unlock the full potential of these critical components.
Advancements in epitaxial barrel susceptor technologies have revolutionized semiconductor manufacturing. Innovations in materials, design, and reactor integration have enhanced wafer quality, improved energy efficiency, and supported cutting-edge applications. These developments address the growing demand for high-performance semiconductors in industries like artificial intelligence and telecommunications.
Continued innovation remains essential to meet emerging technological challenges. Researchers and engineers must explore new materials, refine reactor designs, and adopt advanced growth techniques. Collaboration between academia and industry will drive progress. Investments in research and development will unlock future potential, ensuring that epitaxial barrel susceptors remain vital to the semiconductor industry’s evolution.