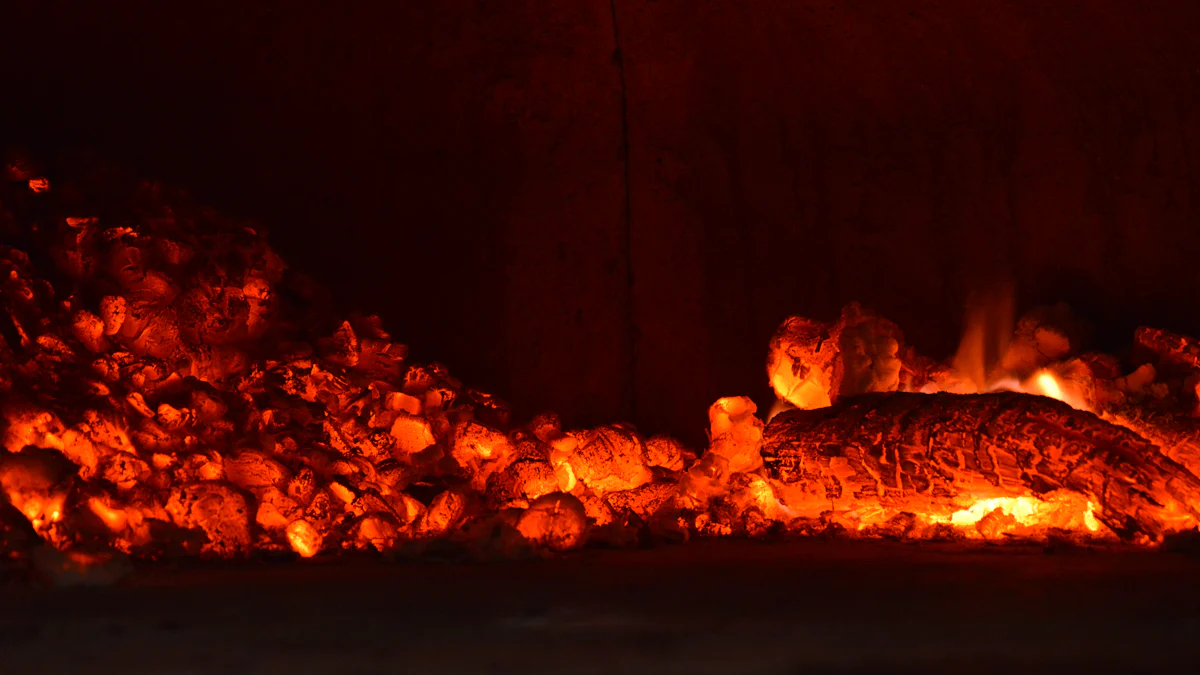
In high-temperature processes, achieving reliability and efficiency demands materials that can endure extreme conditions. A Barrel Susceptor coated with silicon carbide (SiC) offers unmatched performance in such environments. SiC’s exceptional thermal stability ensures consistent operation even under intense heat. Its chemical resistance protects against corrosion, extending the lifespan of the equipment. These qualities make SiC-coated barrel susceptors indispensable for industries like semiconductor manufacturing, where precision and durability are critical. By maintaining uniform heating and reducing defects, they optimize production and enhance overall process efficiency.
Key Takeaways
- Barrel susceptors are crucial for high-temperature processes, ensuring uniform heat distribution and minimizing defects in products like semiconductors.
- Silicon carbide (SiC) coating enhances the durability and thermal efficiency of barrel susceptors, allowing them to withstand extreme temperatures up to 1700°C.
- Using SiC-coated barrel susceptors can significantly reduce energy consumption and operational costs by optimizing heat transfer and minimizing maintenance needs.
- These components are essential in industries such as semiconductor manufacturing and chemical processing, where precision and reliability are paramount.
- Investing in SiC-coated barrel susceptors leads to improved product quality and yield, making them a smart choice for businesses aiming for innovation and efficiency.
- The versatility of barrel susceptors extends beyond semiconductors to applications in power electronics, automotive manufacturing, and renewable energy, highlighting their broad industrial relevance.
What Are Barrel Susceptors?
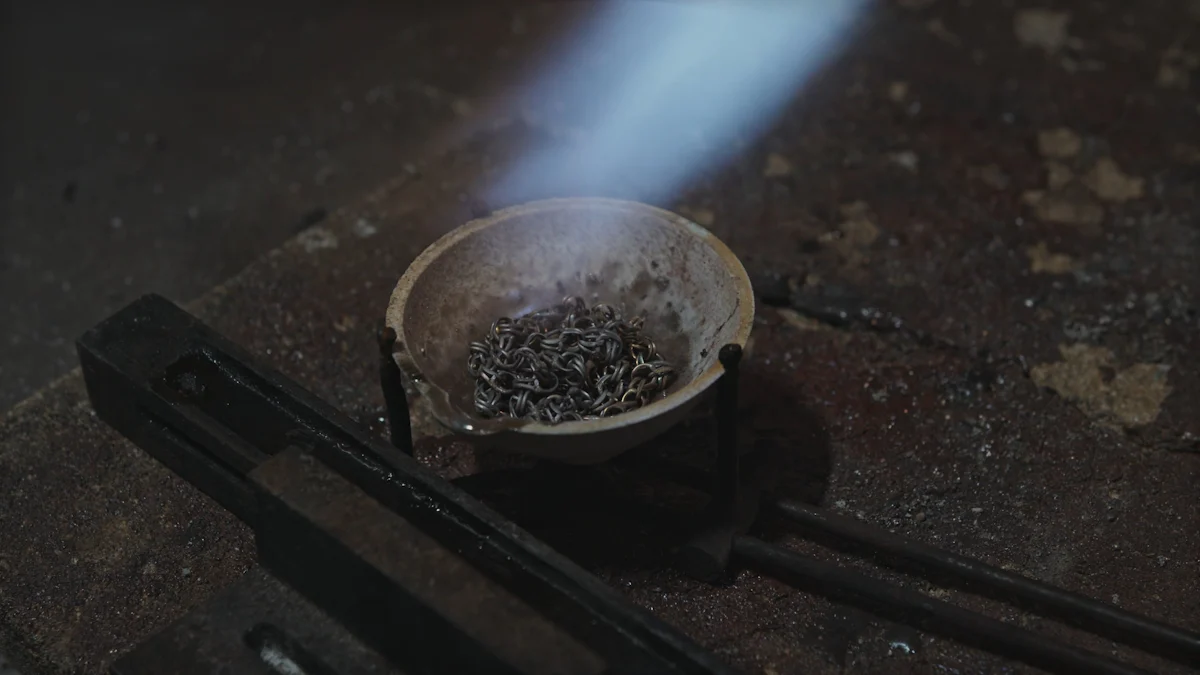
Definition and Function
A Barrel Susceptor is a specialized component designed for high-temperature industrial processes. It serves as a critical intermediary in systems where precise thermal management is essential. Typically, it is a cylindrical structure that holds or supports materials during processing. Its primary function is to absorb, distribute, and transfer heat uniformly to the materials it surrounds. This ensures consistent thermal conditions, which are vital for achieving high-quality results in demanding applications.
The design of a barrel susceptor often incorporates advanced materials like silicon carbide (SiC). This enhances its ability to withstand extreme temperatures and resist chemical degradation. By maintaining structural integrity under harsh conditions, it ensures reliable performance over extended periods. Industries such as semiconductor manufacturing rely heavily on these components to maintain precision and efficiency in their operations.
Role in High-Temperature Applications
In high-temperature environments, the role of a barrel susceptor becomes indispensable. It acts as a thermal conductor, ensuring even heat distribution across the materials being processed. This uniformity minimizes temperature fluctuations, which can lead to defects or inconsistencies in the final product. For example, in semiconductor manufacturing, even minor temperature variations can compromise the quality of wafers, leading to significant losses.
Barrel susceptors also provide a protective barrier between the heating elements and the materials being processed. This prevents contamination and ensures that the materials retain their purity. The use of SiC-coated barrel susceptors further enhances this protection. SiC’s exceptional thermal stability and oxidation resistance allow these components to operate effectively at temperatures as high as 1700°C. This makes them ideal for applications in industries where precision and durability are non-negotiable.
Moreover, barrel susceptors contribute to process optimization by improving energy efficiency. Their ability to retain and distribute heat reduces energy consumption, lowering operational costs. This combination of durability, efficiency, and precision makes barrel susceptors a cornerstone of innovation in high-temperature industrial processes.
Why SiC Coating Matters
Exceptional Properties of SiC Coating
Silicon carbide (SiC) coating elevates the performance of a Barrel Susceptor in high-temperature environments. Its exceptional thermal conductivity ensures efficient heat transfer, which is critical for maintaining uniform temperatures during industrial processes. This uniformity directly impacts the quality of the final product, especially in applications like semiconductor manufacturing.
SiC’s resistance to oxidation and corrosion sets it apart from other materials. It withstands extreme temperatures, up to 1700°C, without degrading. This durability ensures that your equipment remains reliable even in the harshest conditions. Additionally, SiC’s chemical inertness prevents contamination, preserving the purity of the materials being processed. This property is particularly valuable in industries where precision and cleanliness are non-negotiable.
Another key advantage of SiC coating is its ability to enhance the lifespan of the Barrel Susceptor. The coating protects the underlying structure from wear and tear caused by repeated exposure to high heat and corrosive environments. This longevity reduces the need for frequent replacements, saving both time and operational costs.
Comparison to Alternative Materials
When compared to alternative materials, SiC-coated Barrel Susceptors demonstrate clear superiority. Traditional materials like graphite or uncoated metals often fall short in high-temperature applications. Graphite, while offering decent thermal conductivity, lacks the corrosion resistance needed for long-term use. Uncoated metals, on the other hand, are prone to oxidation and thermal degradation, leading to inconsistent performance over time.
SiC-coated components excel in areas where alternatives struggle. For instance:
- Thermal Conductivity: SiC-coated susceptors provide superior heat distribution, ensuring consistent processing conditions. This advantage is crucial for processes like epitaxy, where temperature uniformity directly affects wafer quality.
- Corrosion Resistance: Unlike uncoated materials, SiC resists chemical attacks, making it ideal for environments involving reactive gases or harsh chemicals.
- High-Temperature Stability: SiC maintains its structural integrity at extreme temperatures, outperforming materials that degrade or warp under similar conditions.
"SiC-coated barrel susceptors have excellent thermal conductivity, corrosion resistance, and high-temperature resistance, making them ideal for epitaxial processes in semiconductor manufacturing."
By choosing SiC-coated Barrel Susceptors, you gain a competitive edge in efficiency, reliability, and product quality. These benefits make them the preferred choice for industries that demand precision and durability.
Key Benefits of SiC-Coated Barrel Susceptors
Enhanced Thermal Efficiency and Uniformity
SiC-coated barrel susceptors deliver exceptional thermal efficiency, ensuring that heat is transferred and distributed evenly across the materials being processed. This uniformity eliminates temperature fluctuations, which can lead to defects or inconsistencies in high-precision applications. For example, in semiconductor manufacturing, maintaining consistent temperatures is critical for producing high-quality wafers. Uneven heating can compromise the structural integrity of the final product, resulting in costly rework or material waste.
The superior thermal conductivity of silicon carbide plays a pivotal role in achieving this efficiency. By optimizing heat transfer, you can reduce energy consumption and improve overall process performance. This makes SiC-coated barrel susceptors an invaluable asset for industries that demand precision and reliability in high-temperature environments.
Durability and Cost-Effectiveness
Durability is a defining characteristic of SiC-coated barrel susceptors. The silicon carbide coating protects the underlying structure from wear and tear caused by extreme heat and corrosive environments. Unlike traditional materials, SiC resists oxidation and chemical degradation, ensuring that your equipment remains functional over extended periods. This longevity reduces the frequency of replacements, saving you both time and operational costs.
In addition to durability, SiC-coated barrel susceptors offer cost-effectiveness. Their ability to withstand harsh conditions minimizes downtime and maintenance expenses. By investing in these advanced components, you can achieve long-term savings while maintaining high levels of productivity. This combination of durability and cost-efficiency makes them a preferred choice for industries like power electronics and automotive manufacturing, where high-performance solutions are essential.
Process Optimization and Improved Yield
SiC-coated barrel susceptors contribute significantly to process optimization. Their ability to maintain thermal stability and uniformity enhances the efficiency of high-temperature operations. This leads to fewer defects and higher yields, especially in applications like epitaxy, where precision directly impacts product quality. By reducing variability in the production process, you can achieve consistent results and meet stringent industry standards.
Moreover, the use of SiC-coated barrel susceptors aligns with the growing demand for high-performance solutions in sectors like renewable energy and telecommunications. As industries evolve, the need for reliable and efficient components becomes increasingly important. SiC-coated barrel susceptors not only meet these demands but also provide a competitive edge by improving operational efficiency and product quality.
"The ability of SiC-coated barrel susceptors to enhance yield and optimize processes makes them indispensable for industries that prioritize innovation and reliability."
By integrating these advanced components into your operations, you can streamline workflows, reduce costs, and achieve superior outcomes. Their role in improving yield and optimizing processes underscores their value in high-temperature industrial applications.
Applications in High-Temperature Processes
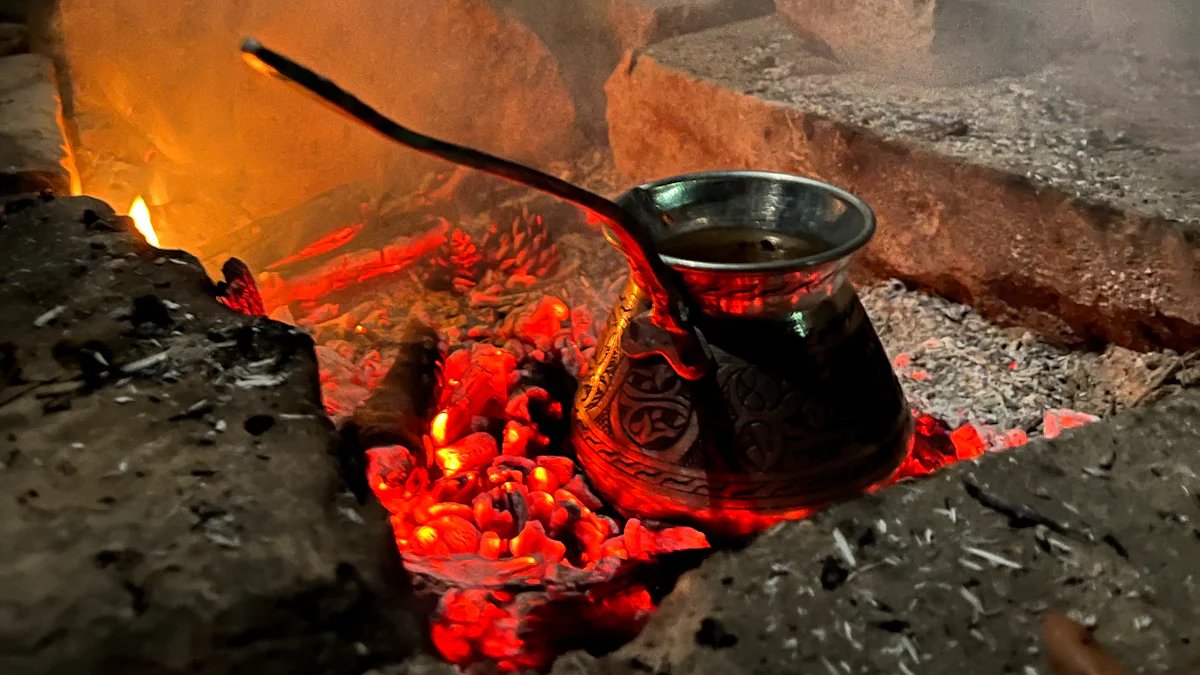
Semiconductor Manufacturing
In semiconductor manufacturing, precision and consistency define success. A barrel susceptor plays a pivotal role in processes like epitaxy, where maintaining uniform temperatures is critical. You rely on these components to ensure that wafers receive consistent heat distribution during deposition. This uniformity directly impacts the quality of the semiconductor layers, reducing defects and improving yield. The silicon carbide coating enhances the susceptor’s durability, allowing it to withstand the harsh conditions of high-temperature environments. By using SiC-coated barrel susceptors, you can achieve superior results while minimizing operational disruptions.
Chemical Processing
Chemical processing demands equipment that can endure extreme conditions without compromising performance. Barrel susceptors coated with silicon carbide excel in these environments. They resist corrosion caused by reactive gases and chemicals, ensuring the purity of the materials being processed. You benefit from their ability to maintain thermal stability, which is essential for reactions requiring precise temperature control. Whether you’re working with high-purity chemicals or conducting complex synthesis, these susceptors provide the reliability and efficiency needed to optimize your operations.
Other Industrial Applications
Beyond semiconductors and chemical processing, barrel susceptors find applications in various industries. In power electronics, they support the production of components that require exacting thermal conditions. In the automotive sector, they contribute to the manufacturing of advanced materials used in electric vehicles. Renewable energy industries also leverage these components for processes like photovoltaic cell production. By integrating SiC-coated barrel susceptors into your workflows, you can enhance efficiency, reduce costs, and meet the demands of cutting-edge technologies.
"The versatility of barrel susceptors makes them indispensable across industries that prioritize precision, durability, and efficiency."
SiC-coated barrel susceptors stand as essential components for high-temperature processes. Their superior thermal stability ensures reliable performance in extreme conditions, making them indispensable for industries like semiconductor manufacturing. You benefit from their exceptional thermal conductivity and corrosion resistance, which enhance product quality and yield. These susceptors optimize operations by reducing defects and improving efficiency, ultimately lowering costs.
"SiC-coated barrel susceptors are the cornerstone of innovation, offering unmatched durability and reliability."
As industries advance, integrating these advanced components into your processes will keep you at the forefront of precision and efficiency.