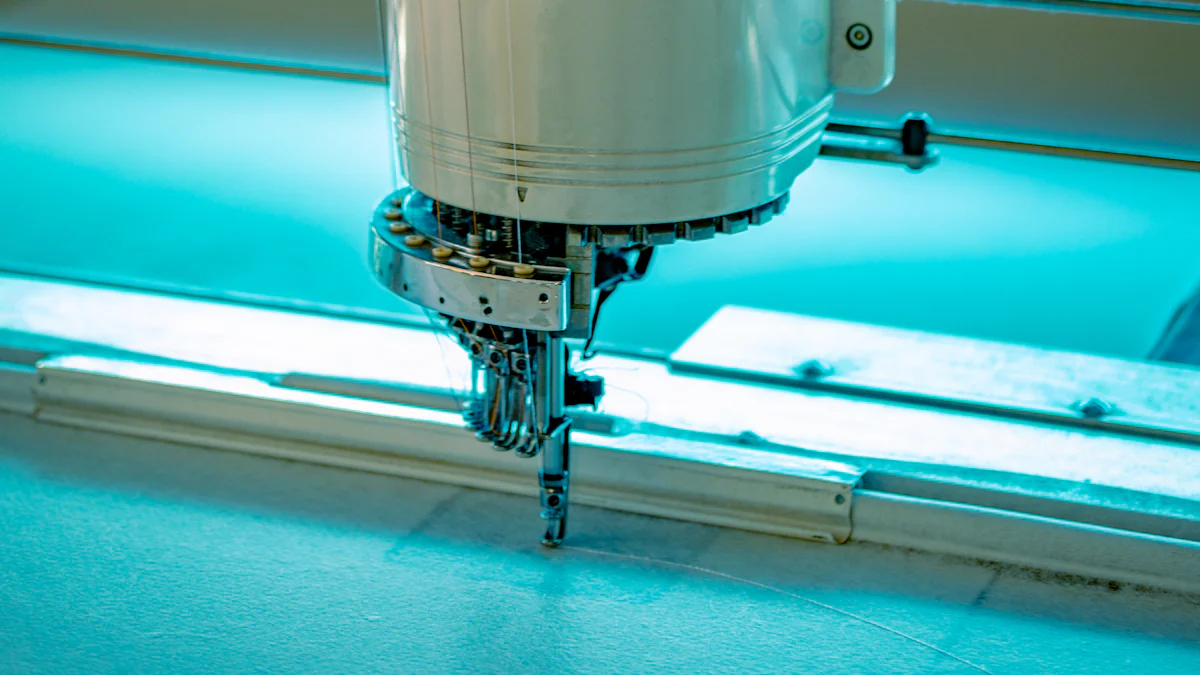
PSS/ICP Etch Carriers dienen als wesentliche Werkzeuge in der Halbleiterfertigung. Diese Träger bieten robuste Träger für Wafer beim Plasmaätzen, ein Verfahren, das Präzision und Konsistenz erfordert. Durch die Gewährleistung der Stabilität tragen sie dazu bei, die Gleichmäßigkeit der Materialentfernung zu wahren, was für hochwertige Halbleiterbauelemente entscheidend ist. Ihr Design priorisiert die Hitze- und Korrosionsbeständigkeit und macht sie ideal für die rauen Bedingungen des Plasmaätzens. Mit ihrer Fähigkeit, Genauigkeit und Effizienz zu verbessern, spielen PSS/ICP Etch Carrier eine zentrale Rolle bei der Skalierung der Produktion, während die Anforderungen der fortschrittlichen Halbleitertechnologien erfüllt.
Wichtigste Erkenntnisse
- PSS/ICP Etch Carriers sind unerlässlich, um die Waferstabilität beim Plasmaätzen zu erhalten, wodurch Präzision und Gleichmäßigkeit bei der Materialentfernung gewährleistet werden.
- Durch die Verwendung dieser Träger werden Defekte im Ätzprozess deutlich reduziert, was zu höheren Ausbeuten und besseren Halbleiterbauelementen führt.
- Eine ordnungsgemäße Vorbereitung und Ausrichtung von Trägern und Wafern sind entscheidend, um optimale Ergebnisse bei Ätzprozessen zu erzielen.
- Die regelmäßige Wartung sowohl von Trägern als auch von Ätzgeräten ist unerlässlich, um ihre Lebensdauer zu verlängern und die Produktionseffizienz zu steigern.
- Innovationen im Trägerdesign, wie der Einsatz fortschrittlicher Materialien und die Anpassung für spezifische Anwendungen, transformieren die Halbleiterfertigung.
- Die Integration von intelligenten Trägern mit Sensoren und AI-getriebener Optimierung revolutioniert Ätzprozesse, verbessert die Genauigkeit und Reduzierung von Abfällen.
- Über Fortschritte in der PSS/ICP-Ätztechnik informiert zu bleiben, ist der Schlüssel für Hersteller, in der sich schnell entwickelnden Halbleiterindustrie wettbewerbsfähig zu bleiben.
PSS/ICP verstehen Ätzen und die Rolle von PSS/ICP Etch Carriers
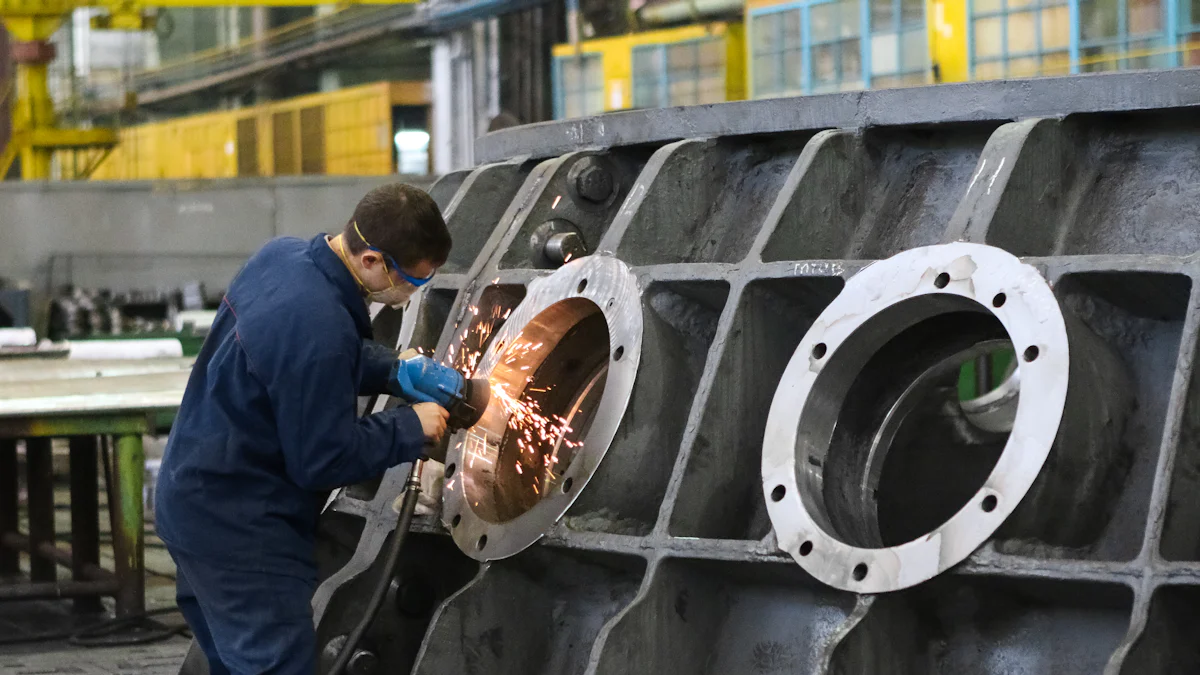
Was ist PSS/ICP Ätzen?
Übersicht Plasmaquelle Silikon (PSS) Ätzen
Plasma Source Silicon (PSS) Ätzen ist ein spezialisiertes Verfahren zur Halbleiterherstellung. Es beinhaltet die Verwendung von Plasma, um Material aus Siliziumscheiben mit hoher Präzision zu entfernen. Plasma, oft als vierter Materiezustand bezeichnet, besteht aus ionisierten Gasen, die mit der Oberfläche des Wafers reagieren können. Diese Reaktion ermöglicht eine kontrollierte Materialabtragung, die für die Erstellung komplizierter Muster auf dem Wafer unerlässlich ist. PSS-Ätzung ist besonders wertvoll für seine Fähigkeit, komplexe Designs zu handhaben und gleichzeitig Genauigkeit zu erhalten.
Hersteller verlassen sich auf diese Technik, um konsequente Ergebnisse in der hochvolumigen Produktion zu erzielen. Das Verfahren stellt sicher, dass jeder Wafer die für fortgeschrittene Halbleiterbauelemente erforderlichen genauen Spezifikationen erfüllt. Mit PSS-Ätzung können Unternehmen Komponenten produzieren, die moderne Technologien wie Smartphones, Computer und andere elektronische Geräte unterstützen.
Grundlagen der induktiv gekoppelten Plasmaätzung (ICP)
Induktiv gekoppeltes Plasma (ICP) Ätzen nimmt Präzision auf die nächste Ebene. Dieses Verfahren verwendet eine hochdichte Plasmaquelle, um eine überlegene Ätzleistung zu erzielen. Das Plasma wird durch eine induktive Kopplungseinrichtung erzeugt, wobei ein Hochfrequenz-Generator eine Spule zur Erzeugung des Plasmas beaufschlagt. Diese Einrichtung ermöglicht eine bessere Kontrolle über den Ätzprozess, einschließlich der Geschwindigkeit der Materialentnahme und der Gleichmäßigkeit über den Wafer.
Ein herausragendes Merkmal der ICP-Ätzung ist seine Fähigkeit, empfindliche Strukturen zu handhaben. Zum Beispiel die Corial 210IL ICP-RIE Etch System verwendet eine spiralförmige Antenne und einen 2 MHz ICP RF-Generator, um hochdichtes Plasma zu erzeugen. Dies sorgt für ausgezeichnete Gleichmäßigkeit und hohe Ätzraten, so dass es ideal für fortgeschrittene Halbleiteranwendungen. Solche Systeme zeigen, wie das ICP-Ätzen die Nachfrage der Industrie nach Präzision und Skalierbarkeit unterstützt.
Die Rolle von PSS/ICP Etch Trägern im Prozess
Stützwafer beim Ätzen
PSS/ICP Etch Carriers spielen eine entscheidende Rolle im Ätzprozess, indem sie stabilen Träger für Wafer bieten. Diese Träger sollen den harten Bedingungen des Plasmaätzens standhalten, darunter hohe Temperaturen und korrosive Umgebungen. Durch die sichere Halterung der Wafer verhindern sie eine Bewegung oder Fehlausrichtung während des Prozesses. Diese Stabilität ist entscheidend, um konsequente Ergebnisse zu erzielen, insbesondere bei der Arbeit mit komplizierten Mustern oder kleinen Geometrien.
Stapelverarbeitungssysteme, die üblicherweise in der Halbleiterfertigung eingesetzt werden, verlassen sich häufig auf diese Träger. So sorgen PSS Etch Carriers beispielsweise bei der HB-LED-Fertigung für kontrolliertes GaN-Ätzen, was für die Herstellung hochwertiger Geräte entscheidend ist. Ihr robustes Design minimiert das Risiko von Beschädigungen der Wafer und erhöht die Gesamteffizienz des Produktionsprozesses.
Gewährleistung der Gleichmäßigkeit und Präzision bei der Materialentfernung
Gleichmäßigkeit und Präzision sind in der Halbleiterfertigung nicht verhandelbar. PSS/ICP Etch Carriers tragen maßgeblich zu diesen Aspekten bei, indem sie eine gleichmäßige Belichtung der Oberfläche des Wafers zum Plasma sicherstellen. Diese gleichmäßige Belichtung verhindert eine ungleichmäßige Materialentfernung, die zu Defekten oder Unstimmigkeiten im Endprodukt führen könnte.
Fortgeschrittene Ätzsysteme, wie die Corial 360IL ICP-RIE Etch System, diese Präzision weiter verbessern. Diese Systeme können mit Funktionen angepasst werden, die die Wechselwirkung zwischen Plasma und Wafer optimieren. Wenn sie mit hochwertigen Ätzträgern kombiniert sind, liefern sie außergewöhnliche Ergebnisse, die den hohen Anforderungen an moderne Halbleiter-Designs entsprechen.
Durch die Kombination der Fähigkeiten von PSS/ICP Etch Carriers mit fortschrittlichen Ätztechnologien können Hersteller die für Geräte der nächsten Generation benötigten Präzision und Zuverlässigkeit erreichen. Diese Träger unterstützen nicht nur die Wafer, sondern spielen auch eine entscheidende Rolle bei der Aufrechterhaltung der Integrität des Ätzprozesses.
Vorteile der Verwendung von PSS/ICP Etch Carriers
Verbesserte Präzision und Genauigkeit
Wie Träger die Mustertreue verbessern
PSS/ICP Etch Carriers verbessern die Mustertreue während des Ätzprozesses deutlich. Durch das sichere Festhalten von Wafern verhindern diese Träger eine unerwünschte Bewegung, die komplizierte Muster verfälschen könnte. Diese Stabilität sorgt dafür, dass das Plasma genau wie beabsichtigt mit der Waferoberfläche interagiert, wodurch die Integrität des Designs erhalten bleibt.
Bei Prozessen ohne diese Träger entstehen häufig Unstimmigkeiten durch ungleichmäßige Plasmabelichtung. Studien haben gezeigt, dass die Anwendung von PSS/ICP Etch Carriers zu einer besseren Kontrolle über Ätzraten und Selektivität führt, insbesondere in komplexen Materialien wie SiC/Cr. Diese Präzision ist entscheidend für die Erstellung der detaillierten Strukturen, die in fortschrittlichen Halbleiterbauelementen benötigt werden.
Fehler im Ätzprozess reduzieren
Defekte im Ätzprozess können die Leistung von Halbleiterbauelementen beeinträchtigen. PSS/ICP Etch Carriers minimieren diese Risiken durch eine gleichmäßige Materialentfernung über den Wafer. Unebenes Ätzen, das oft ohne ordnungsgemäße Unterstützung auftritt, kann zu Defekten wie Überätzen oder Unterätzen in bestimmten Bereichen führen.
Das robuste Design der Träger schützt auch Wafer vor Schäden durch hohe Temperaturen und korrosive Umgebungen. Dieser Schutz verringert die Wahrscheinlichkeit von Mängeln, was zu höheren Ausbeuten und qualitativ besseren Produkten führt. Hersteller können sich auf diese Träger verlassen, um Konsistenz zu erhalten und Abfall während der Produktion zu reduzieren.
Verbesserung der Effizienz und Skalierbarkeit
Schnellere Bearbeitungszeiten mit Trägern
Zeit ist ein kritischer Faktor bei der Halbleiterherstellung. PSS/ICP Etch Carriers tragen zu schnelleren Bearbeitungszeiten bei, indem der Ätzprozess gestrafft wird. Ihre Fähigkeit, mehrere Wafer sicher in Batch-Verarbeitungssystemen zu halten, ermöglicht Herstellern, mehrere Wafer gleichzeitig zu ätzen. Dieser Ansatz spart nicht nur Zeit, sondern erhöht auch die Gesamtproduktivität.
Darüber hinaus sorgt die Kompatibilität der Träger mit hochdichten Plasmasystemen, wie sie bei der ICP-Ätzung verwendet werden, für eine effiziente Materialabtragung. Die Kombination von fortschrittlichen Ätztechniken und zuverlässigen Trägern beschleunigt die Produktion, ohne die Qualität zu beeinträchtigen.
Unterstützung der hochvolumigen Fertigung
Die Steigerung der Produktion, um die Anforderungen der Industrie zu erfüllen, erfordert Werkzeuge, die hohe Volumina handhaben können, ohne Präzision zu opfern. PSS/ICP Etch Carriers zeichnen sich in diesem Bereich durch Unterstützung von Batch-Verarbeitungssystemen aus, die üblicherweise in der Halbleiterfertigung eingesetzt werden. Diese Systeme ermöglichen es den Herstellern, große Mengen von Wafern in einem einzigen Zyklus zu verarbeiten, was sie ideal für die hochvolumige Produktion macht.
Die Haltbarkeit und Verschleißfestigkeit der Träger gewährleisten eine gleichbleibende Leistung über längere Zeiträume. Diese Zuverlässigkeit ist entscheidend für die Aufrechterhaltung der Effizienz im Großbetrieb. Durch die Integration dieser Träger in ihre Prozesse können die Hersteller die wachsende Nachfrage nach Halbleiterbauelementen unter Beibehaltung hoher Qualitätsstandards erfüllen.
Kompatibilität mit Advanced Semiconductor Designs
Anpassung an kleinere Knoten und komplexe Geometrien
Als sich Halbleiterkonstruktionen entwickeln, wird der Bedarf an Werkzeugen, die kleinere Knoten und komplizierte Geometrien handhaben können, mehr Pressung. PSS/ICP Etch Carriers sind darauf ausgelegt, diese Herausforderungen zu bewältigen. Ihre Präzision und Stabilität machen sie gut geeignet, um die winzigen Eigenschaften in modernen Halbleiter-Geräten zu ätzen.
Die Fähigkeit der Träger, eine gleichmäßige Exposition gegenüber Plasma zu gewährleisten, ist besonders vorteilhaft, wenn sie mit komplexen Designs arbeiten. Diese Gleichmäßigkeit verhindert Fehler, die durch ungleichmäßiges Ätzen entstehen könnten, so dass Hersteller Bauteile herstellen können, die die genauen Spezifikationen für fortschrittliche Technologien erfüllen.
Unterstützung von Halbleitertechnologien der nächsten Generation
Halbleitertechnologien der nächsten Generation, wie 3D-Strukturen und fortgeschrittene Knoten, erfordern innovative Fertigungslösungen. PSS/ICP Etch Carriers spielen eine entscheidende Rolle bei der Unterstützung dieser Fortschritte. Ihre Kompatibilität mit modernsten Ätzsystemen ermöglicht es den Herstellern, die komplizierten Strukturen für aufstrebende Anwendungen zu schaffen.
So hat sich die Rolle der Träger bei der Steuerung von GaN-Ätzungen für die Produktion von HB-LEDs und anderen fortschrittlichen Geräten als wesentlich erwiesen. Durch die Bereitstellung der für diese Prozesse erforderlichen Stabilität und Präzision unterstützen PSS/ICP Etch Carriers Innovationen in der Halbleiterindustrie.
Wie man PSS/ICP Etch Träger effektiv verwendet
Schritt für Schritt Anleitung zur Verwendung von PSS/ICP Etch Carriers
Herstellung von Träger und Wafer
Die richtige Vorbereitung sorgt für einen reibungslosen Betrieb während des Ätzprozesses. Beginnen Sie mit der Überprüfung der PSS/ICP Etch Carrier für jegliche Verschleißerscheinungen oder Beschädigungen. Selbst kleinere Unvollkommenheiten können die Stabilität des Wafers beeinflussen. Reinigen Sie den Träger gründlich, um Restpartikel oder Verunreinigungen zu entfernen. Dieser Schritt verhindert unerwünschte Reaktionen bei der Plasmabelichtung.
Anschließend den Wafer mit Sorgfalt zu behandeln, um Kratzer oder Trümmer zu vermeiden. Legen Sie es sicher auf den Träger, um sicherzustellen, dass es perfekt mit den vorgesehenen Schlitzen oder Nuten passt. Fehlausrichtung kann zu unebenem Ätzen oder Defekten im Endprodukt führen. Hersteller empfehlen oft, antistatische Handschuhe zu verwenden, um Verunreinigungsrisiken zu minimieren.
Einrichtung der Ätzanlage
Sobald der Träger und der Wafer bereit sind, konzentrieren Sie sich auf die Ätzausrüstung. Beginnen Sie, indem Sie das System nach den spezifischen Anforderungen des Ätzprozesses kalibrieren. Überprüfen Sie den Plasmagenerator, die Gasdurchflussraten und die Temperatureinstellungen, um sicherzustellen, dass sie den gewünschten Parametern entsprechen.
Den Träger vorsichtig in die Ätzkammer laden. Stellen Sie sicher, dass es fest an Ort und Stelle sitzt, um Bewegung während des Betriebs zu verhindern. Überprüfen Sie alle Verbindungen und Einstellungen, bevor Sie den Prozess starten. Ein gut vorbereitetes Setup minimiert Fehler und erhöht die Gesamteffizienz des Ätzvorgangs.
Best Practices für optimale Ergebnisse
Sicherstellung der richtigen Ausrichtung und Kalibrierung
Die Ausrichtung spielt eine entscheidende Rolle bei der Erreichung von Präzision. Prüfen Sie immer, dass der Wafer auf dem Träger zentriert ist und dass der Träger selbst in der Ätzkammer korrekt positioniert ist. Fehlausrichtung kann eine ungleichmäßige Plasmabelichtung verursachen, was zu einer inkonsistenten Materialentfernung führt.
Die Kalibrierung der Ausrüstung ist ebenso wichtig. Regelmäßig testen Sie das System, um sicherzustellen, dass es gleichmäßige Plasmadichte und gleichbleibende Ätzraten liefert. Zu den fortschrittlichen Systemen gehören oft automatisierte Kalibrierfunktionen, die diesen Prozess vereinfachen und die Genauigkeit verbessern.
Regelmäßige Wartung von Trägern und Geräten
Die routinemäßige Wartung erweitert die Lebensdauer sowohl der Träger als auch der Ätzeinrichtung. Nach jeder Anwendung säubern Sie den Träger, um Reste aus dem Ätzprozess zu entfernen. Prüfen Sie es für Verschleißerscheinungen, wie Risse oder Verformungen, und ersetzen Sie es gegebenenfalls.
Für die Ausrüstung, regelmäßige Überprüfungen, um sicherzustellen, dass alle Komponenten funktionieren ordnungsgemäß. Achten Sie besonders auf das Plasmagenerator- und Gasliefersystem, da diese die Qualität des Ätzprozesses direkt beeinflussen. Das Halten alles in Top-Zustand reduziert Ausfallzeiten und erhöht die Produktivität.
Gemeinsame Herausforderungen und Überwindung von Them
Trägerverschleiß und Reiß
Im Laufe der Zeit können Träger Verschleiß durch Einwirkung von hohen Temperaturen und korrosiven Umgebungen erleben. Um dies zu erreichen, sollten die Hersteller Träger aus dauerhaften Materialien verwenden, die solche Bedingungen widerstehen. Regelmäßige Inspektionen helfen, Probleme frühzeitig zu identifizieren, so dass rechtzeitige Ersetzungen möglich sind.
Einige fortschrittliche Träger enthalten innovative Designs, die ihre Haltbarkeit verbessern. Zum Beispiel verfügen bestimmte Modelle über verstärkte Strukturen oder Beschichtungen, die Korrosion widerstehen. Die Investition in qualitativ hochwertige Träger reduziert die Häufigkeit von Ersatz und sorgt für eine gleichbleibende Leistung.
Fehlerbehebung Ätzunfälle
Unstimmigkeiten im Ätzprozess können aus verschiedenen Faktoren wie ungleichmäßiger Plasmaverteilung oder unsachgemäßer Trägerausrichtung entstehen. Um diese Probleme zu beheben, beginnen Sie mit der Prüfung der Träger und Wafer-Setup. Stellen Sie sicher, dass alles richtig ausgerichtet und frei von Verunreinigungen ist.
Wenn das Problem besteht, überprüfen Sie die Geräteeinstellungen. Schwankungen der Gasstromraten oder der Plasmadichte können zu einem unebenen Ätzen führen. Die Anpassung dieser Parameter löst oft das Problem. Bei komplexeren Problemen konsultieren Sie das Gerätehandbuch oder suchen Sie Hilfe vom Hersteller.
Durch die folgenden Schritte und Best Practices können die Hersteller die Wirksamkeit ihrer PSS/ICP Etch Carriers. Richtige Vorbereitung, Wartung und Fehlerbehebung sorgen auch bei anspruchsvollen Halbleiteranwendungen für zuverlässige Ergebnisse.
Fortschritte und Trends in der PSS/ICP-Ätztechnik
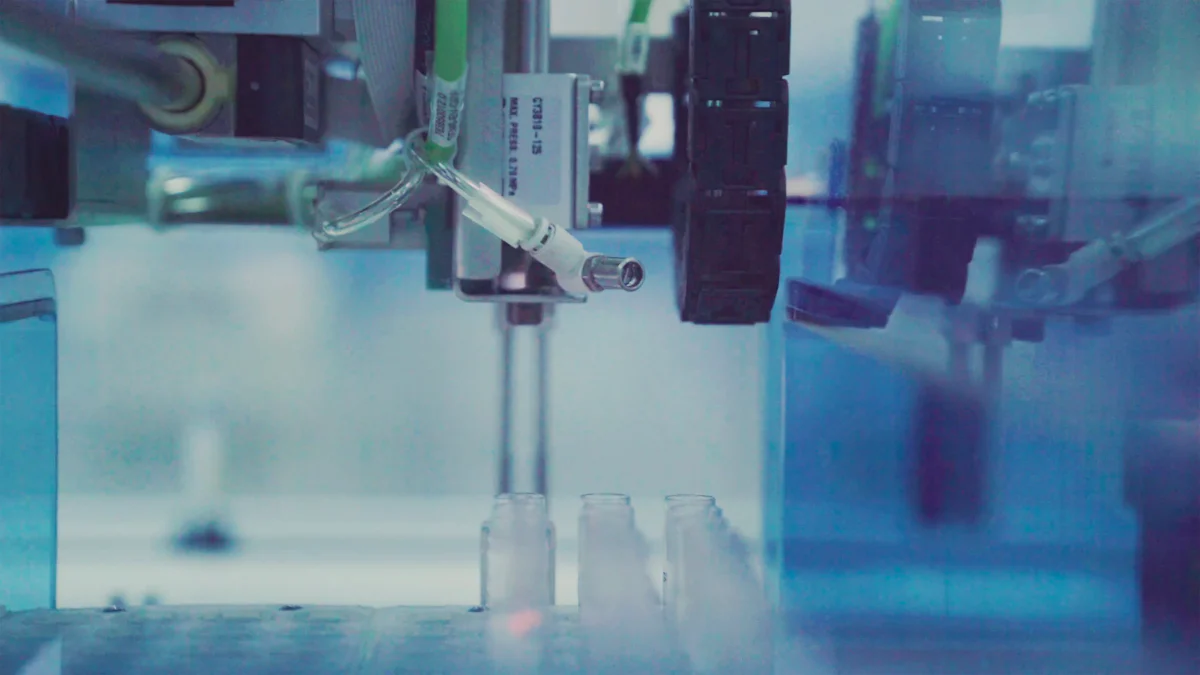
Die Halbleiterindustrie entwickelt sich ständig und die PSS/ICP-Ätztechnik ist keine Ausnahme. Innovationen im Trägerdesign, die Integration mit aufstrebenden Prozessen und die Einführung von Automatisierung und KI prägen die Zukunft dieses Bereichs. Lassen Sie uns diese Fortschritte erkunden und wie sie die Halbleiterfertigung transformieren.
Innovationen in PSS/ICP Etch Carrier Design
Werkstoffe in Trägern der nächsten Generation
PSS/ICP der nächsten Generation Etch Carriers werden mit fortschrittlichen Materialien gefertigt, um den strengen Anforderungen moderner Ätzprozesse gerecht zu werden. Hersteller verwenden jetzt Materialien wie Siliziumkarbid (SiC) und spezialisierte Keramik aufgrund ihrer außergewöhnlichen Hitzebeständigkeit und Haltbarkeit. Insbesondere SiC hat für seine Fähigkeit, hohe Temperaturen und korrosive Umgebungen zu widerstehen, die es ideal für Plasmaätzanwendungen macht.
„Siliconcarbid (SiC) ist ein vielversprechendes Material für elektronische und photonische Anwendungen“ wie in einer Studie über SiC-Anwendungen und Plasmaätztechniken hervorgehoben. Seine Eigenschaften machen es zu einer bevorzugten Wahl für Träger, die in hochpräzisen Ätzverfahren eingesetzt werden.
Diese Materialien verbessern nicht nur die Lebensdauer der Träger, sondern verbessern auch ihre Leistung bei der Aufrechterhaltung der Waferstabilität beim Ätzen. Durch die Reduzierung von Verschleiß sorgen sie für konsequente Ergebnisse über längere Produktionszyklen.
Anpassung an bestimmte Ätzanwendungen
Die Individualisierung ist zu einem entscheidenden Trend bei der Carrier-Design geworden. Hersteller maßen nun PSS/ICP Etch Carrier an, die für bestimmte Ätzanwendungen geeignet sind, wie z.B. tief reaktives Ionenätzen (DRIE) oder hochaspekt-ratio Ätzen. Diese Anpassung ermöglicht es Trägern, einzigartige Wafergeometrien und Ätzanforderungen zu erfüllen.
So verfügen beispielsweise für die HB-LED-Herstellung ausgelegte Träger oft über spezialisierte Nuten oder Schlitze, um Wafer während des kontrollierten GaN-Ätzens sicher zu halten. Solche maßgeschneiderten Designs verbessern die Präzision und verringern das Risiko von Defekten und gewährleisten optimale Ergebnisse für bestimmte Halbleiteranwendungen.
Integration mit Emerging Semiconductor Verfahren
Kompatibilität mit 3D-Strukturen und erweiterten Knoten
Da Halbleiter-Geräte komplexer werden, ist der Bedarf an Trägern, die 3D-Strukturen und fortgeschrittene Knoten bewältigen können, gewachsen. PSS/ICP Etch Carriers unterstützen nun komplizierte Designs wie FinFETs und 3D NAND, indem sie eine gleichmäßige Plasmabelichtung über alle Oberflächen des Wafers gewährleisten.
Die Fähigkeit, Präzision in diesen anspruchsvollen Anwendungen zu erhalten, ist entscheidend. Fortgeschrittene Träger verhindern ein ungleichmäßiges Ätzen, was die Funktionalität dieser Geräte der nächsten Generation beeinträchtigen könnte. Diese Kompatibilität gewährleistet, dass Hersteller die Anforderungen moderner Technologien erfüllen können, ohne Qualitätseinbußen.
Rolle bei der Realisierung neuer Gerätearchitekturen
PSS/ICP Etch Carriers spielen eine zentrale Rolle, um neue Gerätearchitekturen zu ermöglichen. Durch die stabile Unterstützung beim Ätzen ermöglichen sie Herstellern innovative Designs zu schaffen, die die Grenzen der Halbleitertechnologie drängen. So ermöglichen beispielsweise bei der Herstellung von SiC-basierten Geräten verwendete Träger die Schaffung von Hochleistungskomponenten für Leistungselektronik und Photonik.
Die Integration dieser Träger mit fortschrittlichen Ätzsystemen sorgt dafür, dass auch die komplexesten Architekturen präzise gefertigt werden können. Diese Fähigkeit treibt Innovation an und unterstützt die Entwicklung bahnbrechender Technologien.
Automatisierung und KI in Ätzprozessen
Smart Carrier mit integrierten Sensoren
Automatisierung revolutioniert die Halbleiterindustrie und PSS/ICP Etch Carriers sind keine Ausnahme. Smart Carrier mit integrierten Sensoren kommen nun in den Markt. Diese Sensoren überwachen kritische Parameter wie Temperatur und Ausrichtung in Echtzeit. Durch sofortiges Feedback helfen sie, den Ätzprozess zu optimieren und das Fehlerrisiko zu reduzieren.
So kann beispielsweise ein intelligenter Träger eine Fehlausrichtung vor Beginn des Ätzprozesses erkennen, so dass der Bediener Anpassungen vornehmen und Fehler vermeiden kann. Dieses Maß an Automatisierung verbessert die Effizienz und sorgt für konsequente Ergebnisse, auch in hochvolumigen Produktionsumgebungen.
KI-getriebene Prozessoptimierung
Künstliche Intelligenz (KI) nimmt Ätzprozesse auf die nächste Ebene. AI-Algorithmen analysieren während des Ätzens gesammelte Daten, um Muster zu identifizieren und Prozessparameter zu optimieren. Dieser Ansatz minimiert die Variabilität und verbessert die Gesamteffizienz.
In Kombination mit intelligenten Trägern kann AI eine vorausschauende Wartung ermöglichen, indem potenzielle Probleme identifiziert werden, bevor sie die Produktion beeinflussen. Wenn beispielsweise ein Träger Verschleißerscheinungen zeigt, kann das System die Bediener auffordern, diese zu ersetzen, Ausfallzeiten zu verhindern und einen unterbrechungsfreien Betrieb zu gewährleisten.
Eine Überprüfung des reaktiven Ionenätzens unterstreicht die Bedeutung technologischer Fortschritte bei der Erzielung von hochachtungsfähigen Eigenschaften. KI-getriebene Optimierung passt perfekt zu diesem Ziel, da sie Präzision und Skalierbarkeit bei Ätzprozessen verbessert.
Durch die Integration von Automatisierung und KI können die Hersteller mehr Kontrolle über ihre Prozesse erzielen, Abfall reduzieren und die Anforderungen einer sich ständig weiterentwickelnden Industrie erfüllen.
PSS/ICP Etch Carriers spielen eine wichtige Rolle bei der Halbleiterfertigung, indem Präzision, Effizienz und Anpassungsfähigkeit an fortgeschrittene Designs gewährleistet werden. Diese Träger verbessern die Waferstabilität beim Plasmaätzen, was zu konsistenten Ergebnissen und reduzierten Defekten führt. Ihre Kompatibilität mit modernsten Technologien wie der SiC-Verarbeitung und der ICP-RIE-Ätzung unterstützt Innovationen in den Bereichen Energieelektronik, Automotive und erneuerbare Energien.
Für die Hersteller, die wettbewerbsfähig bleiben wollen, ist es unerlässlich, auf den Fortschritten in Trägermaterialien und Ätztechniken aufrechtzuerhalten. Durch die Einbindung dieser Innovationen kann die Industrie die wachsende Nachfrage nach Geräten der nächsten Generation erfüllen und gleichzeitig hochwertige Standards einhalten.