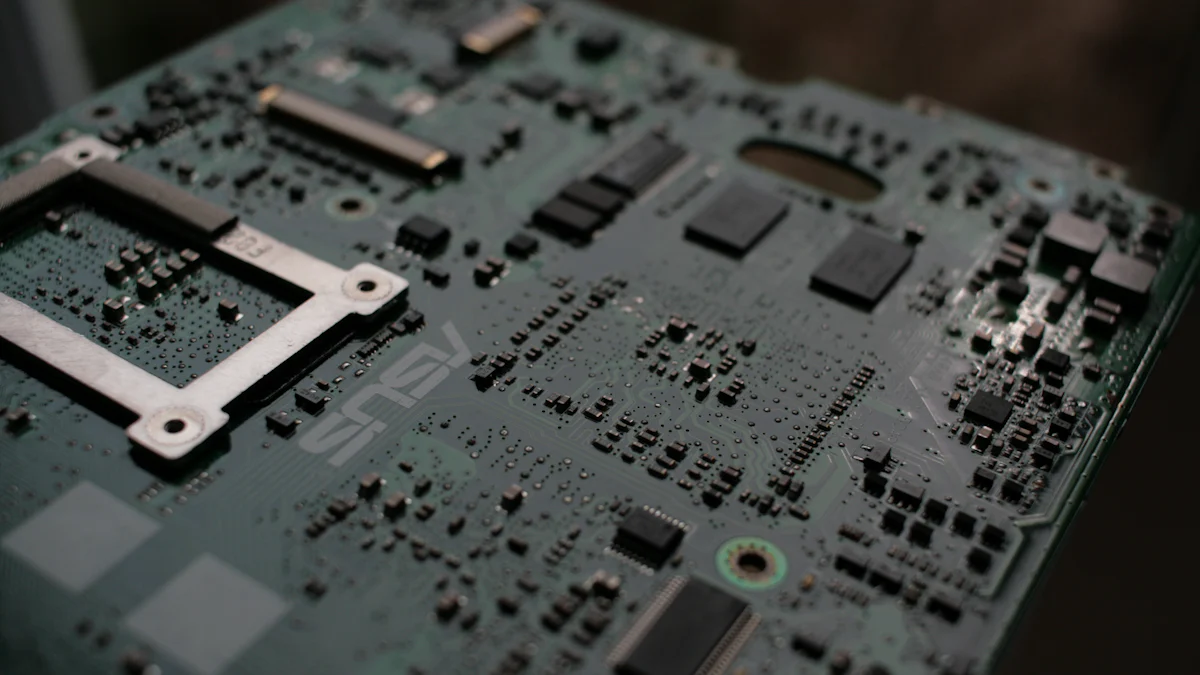
Epitaxial susceptors play a vital role in semiconductor manufacturing. These components provide essential support to wafers during epitaxial growth processes, ensuring stability and precision. Their thermal stability allows them to withstand extreme temperatures without compromising performance. By maintaining uniformity, they enable consistent deposition, which is critical for producing high-quality semiconductor devices. Manufacturers rely on these susceptors to meet the rigorous demands of modern technology, where even minor inconsistencies can lead to significant defects. Their unique properties make them indispensable for achieving efficiency and accuracy in semiconductor production.
Key Takeaways
- Epitaxial susceptors provide crucial mechanical support to wafers, ensuring stability and precision during the epitaxial growth process.
- Their exceptional thermal stability allows them to withstand extreme temperatures, maintaining performance and preventing defects in semiconductor devices.
- Uniform deposition facilitated by susceptors is essential for producing high-quality semiconductor wafers, directly impacting the reliability of end products.
- Enhanced process control through the use of epitaxial susceptors reduces variability, improves product quality, and lowers operational costs.
- Innovations in material coatings and structural designs are advancing the performance and durability of epitaxial susceptors, addressing current manufacturing challenges.
- Emerging technologies, including automation and AI, are revolutionizing the design and production of susceptors, ensuring they meet the evolving demands of the semiconductor industry.
- Sustainability initiatives in susceptor production are being explored to minimize environmental impact and promote a circular economy in semiconductor manufacturing.
What Are Epitaxial Susceptors?
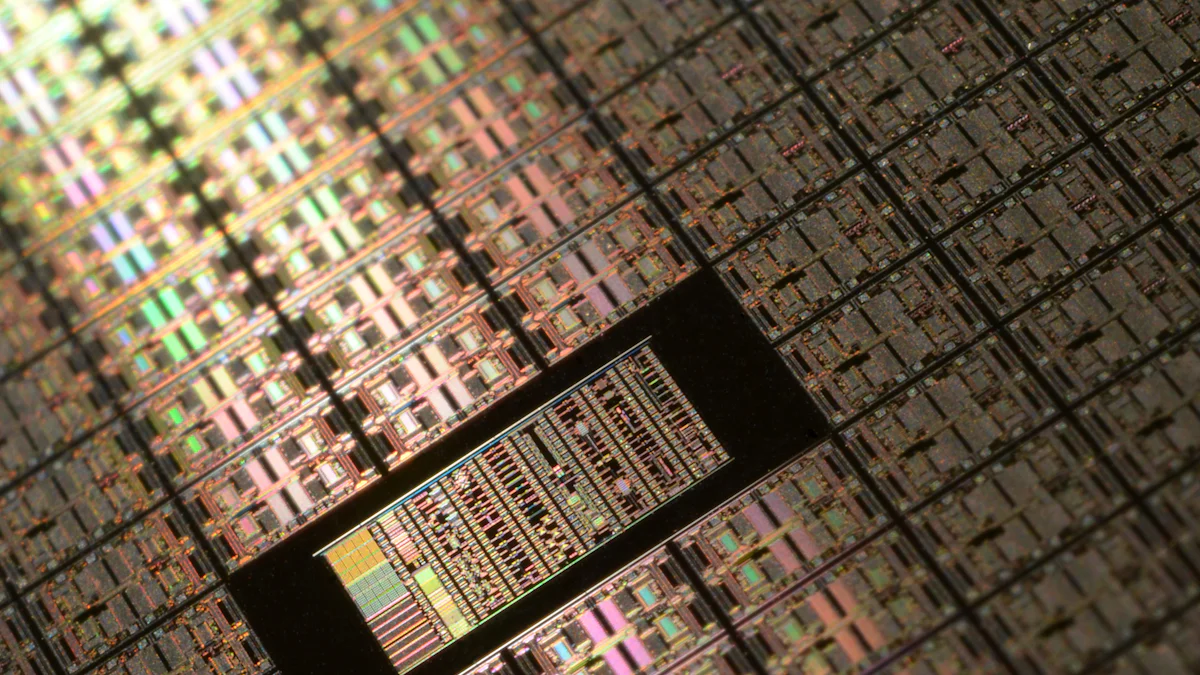
Definition and Function
Epitaxial susceptors serve as critical components in semiconductor manufacturing. They provide mechanical support to wafers during epitaxial growth processes, ensuring stability and precision throughout the operation. These susceptors act as platforms that facilitate uniform heating and deposition, which are essential for producing high-quality semiconductor devices. By maintaining consistent temperature distribution, they help achieve optimal conditions for epitaxial layer formation. Their role extends beyond support, as they also contribute to minimizing heat loss and enhancing process efficiency. This combination of functionality makes epitaxial susceptors indispensable in modern semiconductor fabrication.
Materials Used in Susceptor Design
The materials used in the design of epitaxial susceptors determine their performance and reliability. Manufacturers commonly use high-purity silicon, graphite, and silicon carbide (SiC) due to their excellent thermal and structural properties. Silicon carbide, in particular, stands out for its superior thermal conductivity and resistance to high temperatures. These materials ensure that susceptors can withstand the extreme conditions of epitaxial growth processes without deforming or degrading. Additionally, advanced coatings, such as SiC or other specialized materials, are often applied to enhance durability and reduce contamination risks. The careful selection of materials ensures that epitaxial susceptors meet the stringent demands of semiconductor manufacturing.
Key Benefits of Epitaxial Susceptors
Thermal Stability
Epitaxial susceptors exhibit exceptional thermal stability, a critical factor in semiconductor manufacturing. These components endure extreme temperatures during epitaxial growth processes without losing structural integrity. Their ability to maintain consistent performance under such conditions ensures reliable and precise wafer processing. Materials like silicon carbide enhance this stability by offering superior thermal conductivity and resistance to thermal stress. This property minimizes the risk of deformation or failure, which could compromise the quality of semiconductor devices. Thermal stability not only supports high-temperature operations but also contributes to the overall efficiency of manufacturing systems.
Uniformity in Deposition
Uniform deposition is essential for producing high-quality semiconductor wafers, and epitaxial susceptors play a pivotal role in achieving this goal. By providing a stable platform, they ensure even temperature distribution across the wafer surface. This uniformity prevents irregularities in the epitaxial layer, which could lead to defects in the final product. Advanced designs and coatings further enhance their ability to maintain consistent deposition conditions. Manufacturers rely on this precision to meet the stringent requirements of modern semiconductor devices. The uniformity achieved through these susceptors directly impacts the performance and reliability of the end products.
Enhanced Process Control
Epitaxial susceptors significantly improve process control in semiconductor fabrication. Their design allows for precise regulation of temperature and deposition parameters, ensuring optimal conditions throughout the manufacturing process. This level of control reduces variability and enhances repeatability, which are crucial for large-scale production. By minimizing heat loss and maintaining consistent thermal profiles, these susceptors enable manufacturers to achieve tighter tolerances. Enhanced process control not only improves product quality but also reduces waste and operational costs. The integration of advanced materials and coatings further strengthens their role in delivering consistent and efficient manufacturing outcomes.
Applications in Semiconductor Manufacturing
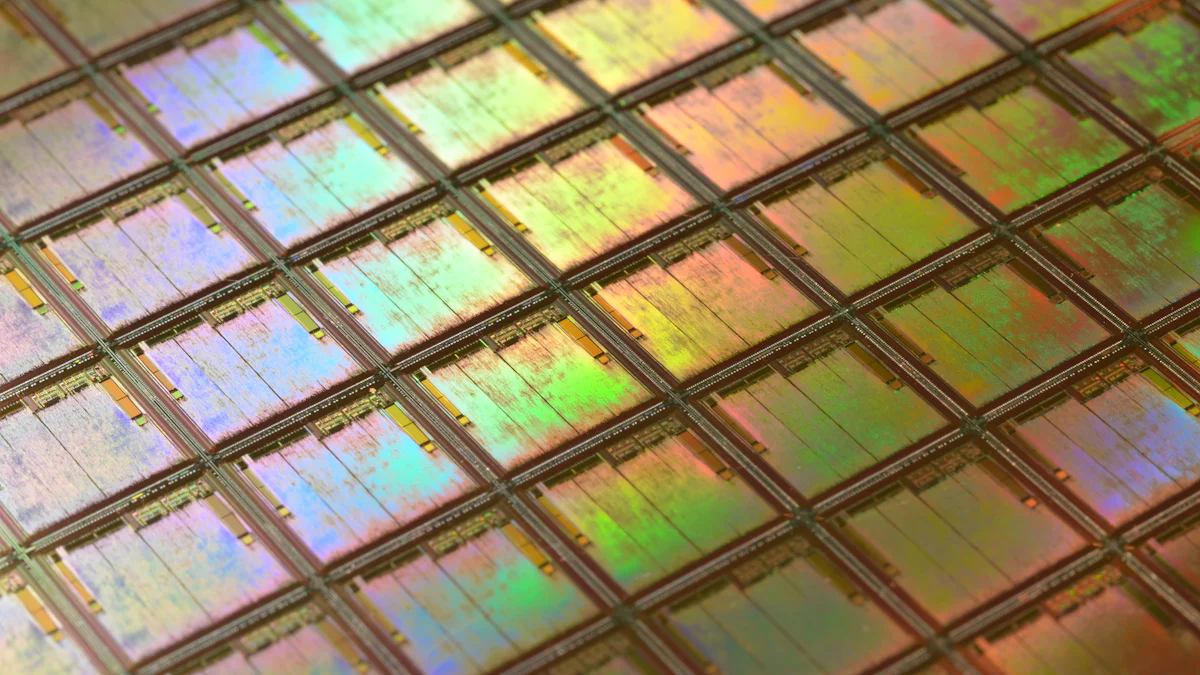
Epitaxial Growth Processes
Epitaxial susceptors play a central role in epitaxial growth processes, which are fundamental to semiconductor manufacturing. These processes involve the deposition of a crystalline layer on a substrate to create high-quality semiconductor wafers. The susceptor provides a stable platform that ensures precise temperature control and uniform heating during these operations. This stability is critical for achieving consistent epitaxial layer formation, as even minor temperature fluctuations can lead to defects in the material.
Manufacturers rely on epitaxial susceptors to optimize the deposition environment. By minimizing heat loss and maintaining thermal uniformity, these components enhance the efficiency of epitaxial growth systems. Their ability to support wafers under extreme conditions ensures that the resulting layers meet the stringent quality standards required for advanced semiconductor devices. The integration of advanced materials, such as silicon carbide, further improves their performance, making them indispensable in this application.
Use in Advanced Semiconductor Devices
Epitaxial susceptors contribute significantly to the production of advanced semiconductor devices. These devices, including microprocessors, memory chips, and power electronics, demand exceptional material quality and precision. The susceptor’s role in ensuring uniform deposition directly impacts the performance and reliability of these components.
In the fabrication of advanced devices, epitaxial susceptors enable the creation of thin, defect-free layers essential for miniaturization and enhanced functionality. Their thermal stability and structural integrity allow manufacturers to achieve tighter tolerances and higher yields. Additionally, the use of specialized coatings on susceptors reduces contamination risks, further improving the quality of the final products. As semiconductor technology continues to evolve, the importance of these components in supporting innovation and meeting industry demands remains unparalleled.
Technological Advancements in Susceptor Design
Innovations in Material Coatings
Recent advancements in material coatings have significantly improved the performance of epitaxial susceptors. Manufacturers now apply specialized coatings, such as silicon carbide (SiC), to enhance durability and thermal efficiency. These coatings provide a protective layer that resists wear and contamination during high-temperature processes. By reducing the risk of particle generation, they ensure a cleaner environment for wafer processing, which is critical for maintaining the quality of semiconductor devices.
Innovative coating techniques also improve the thermal conductivity of susceptors. Enhanced heat transfer capabilities allow for more uniform temperature distribution across the wafer surface. This uniformity minimizes defects in the epitaxial layers, ensuring higher yields and better device performance. Additionally, advanced coatings extend the lifespan of susceptors by preventing oxidation and chemical degradation, even under extreme conditions. These developments highlight the importance of material science in driving the evolution of epitaxial susceptor technology.
Improved Thermal and Structural Designs
Thermal and structural designs of epitaxial susceptors have undergone significant improvements to meet the demands of modern semiconductor manufacturing. Engineers now focus on optimizing the geometry and material composition of susceptors to achieve precise temperature control. Enhanced designs reduce thermal gradients, ensuring consistent heating across the wafer. This precision is essential for producing defect-free epitaxial layers.
Structural advancements have also increased the mechanical stability of susceptors. Reinforced designs prevent warping or deformation during high-temperature operations, maintaining the integrity of the wafer support system. Lightweight materials with high thermal resistance, such as silicon carbide, are now widely used to improve both efficiency and reliability. These innovations enable manufacturers to achieve tighter tolerances and higher production rates, addressing the growing complexity of semiconductor devices.
The integration of computational modeling has further revolutionized susceptor design. Simulation tools allow engineers to predict thermal behavior and optimize designs before production. This approach reduces development time and ensures that new susceptors meet the stringent requirements of advanced semiconductor processes. As technology progresses, these advancements will continue to play a pivotal role in enhancing the capabilities of epitaxial susceptors.
Challenges and Future Trends
Current Limitations
Epitaxial susceptors face several challenges that impact their performance and efficiency in semiconductor manufacturing. One significant limitation lies in material degradation over time. Prolonged exposure to extreme temperatures and chemical environments can lead to wear, reducing the lifespan of susceptors. This degradation increases maintenance costs and disrupts production schedules.
Another challenge involves contamination risks. Despite advancements in coatings, susceptors can still generate particles during high-temperature processes. These particles may compromise wafer quality, leading to defects in semiconductor devices. Manufacturers must implement stringent cleaning protocols to mitigate this issue, which adds complexity to the production process.
Dimensional precision also presents a hurdle. Even minor deviations in the geometry of susceptors can affect temperature distribution and uniformity during deposition. Achieving the required level of precision demands advanced manufacturing techniques, which can be costly and time-consuming.
Thermal management remains a critical concern. While materials like silicon carbide offer excellent thermal conductivity, achieving perfect heat distribution across the wafer surface is still challenging. Inconsistent heating can result in defects, reducing yield rates and impacting overall efficiency.
Emerging Developments
Innovations in epitaxial susceptor technology aim to address these limitations and enhance their performance. Researchers are exploring new materials with superior thermal and structural properties. For instance, advanced composites and hybrid materials show promise in improving durability and reducing contamination risks. These materials can withstand harsher conditions, extending the operational life of susceptors.
Coating technologies continue to evolve. Manufacturers are developing next-generation coatings that offer enhanced resistance to wear and oxidation. These coatings not only improve thermal efficiency but also create cleaner processing environments by minimizing particle generation. Such advancements contribute to higher-quality semiconductor wafers.
Automation and precision engineering are transforming susceptor manufacturing. Advanced machining techniques, such as laser cutting and additive manufacturing, enable the production of highly precise susceptors. These methods reduce dimensional errors and ensure consistent performance during epitaxial growth processes.
Digital tools, including computational modeling and artificial intelligence, are revolutionizing susceptor design. Engineers use simulation software to predict thermal behavior and optimize designs before production. AI algorithms analyze data from manufacturing processes to identify patterns and suggest improvements. These technologies accelerate innovation and help manufacturers meet the stringent demands of modern semiconductor fabrication.
The future of epitaxial susceptors also includes sustainability. Researchers are investigating eco-friendly materials and processes to reduce the environmental impact of susceptor production. Recycling initiatives aim to recover valuable materials from used susceptors, promoting a circular economy within the semiconductor industry.
"The evolution of epitaxial susceptors reflects the industry’s commitment to overcoming challenges and driving innovation," as noted by experts in semiconductor manufacturing. These advancements will play a pivotal role in shaping the future of high-performance semiconductor devices.
Epitaxial susceptors form the backbone of semiconductor manufacturing. They deliver unmatched precision, efficiency, and reliability, ensuring the production of high-quality devices. Their thermal stability and ability to maintain uniform deposition make them essential for meeting the rigorous demands of modern technology. As advancements in materials and design continue, these components will drive innovation in the industry. By addressing current challenges, epitaxial susceptors will unlock new opportunities, shaping the future of semiconductor manufacturing and enabling the development of cutting-edge technologies.