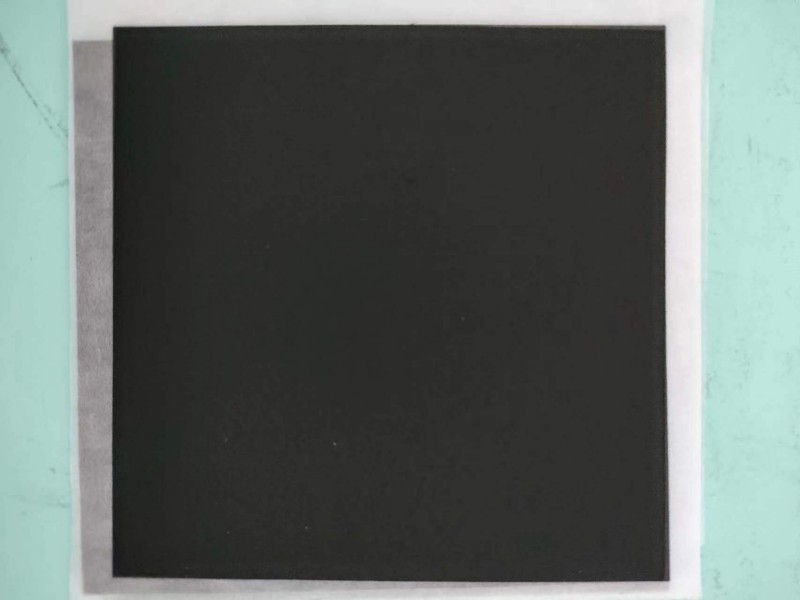
What makes a gas diffusion electrode system so essential in electrochemical reactions? At its core, this system creates a unique interface where gases, liquids, and solids meet to enable efficient energy conversion. By incorporating a porous structure and a catalyst, it facilitates reactions like CO2 reduction or oxygen reduction with remarkable precision. Its role extends beyond just energy; industries rely on it for processes like hydrogen production and chlorine synthesis. The integration of components like the membrane electrode assembly ensures seamless operation, making it a cornerstone of modern energy and industrial advancements.
Key Takeaways
- Gas diffusion electrode systems are crucial for efficient energy conversion, enabling processes like CO2 reduction and hydrogen production.
- The porous structure of gas diffusion electrodes allows for optimal gas flow and interaction with catalysts, enhancing reaction efficiency.
- These systems are integral to clean energy technologies, such as fuel cells, which convert hydrogen and oxygen into electricity with minimal emissions.
- Choosing the right electrolyte—liquid or solid—can significantly impact the efficiency and durability of the gas diffusion electrode system.
- Despite initial setup costs, gas diffusion electrode systems offer long-term cost-effectiveness due to their high efficiency and durability.
- Ongoing research is focused on improving materials and designs to enhance the performance and reduce costs of gas diffusion electrode systems.
- Gas diffusion electrodes play a vital role in advancing sustainable technologies, contributing to a greener future by reducing greenhouse gas emissions.
How Does a Gas Diffusion Electrode System Work?
Understanding how a gas diffusion electrode system operates can feel complex, but breaking it down makes it much clearer. At its heart, this system creates a space where gases, liquids, and solids interact to drive electrochemical reactions. Let’s explore its working principle and process flow.
The Working Principle
Role of gas diffusion electrodes in enabling gas flow and reactions.
Gas diffusion electrodes play a pivotal role in ensuring smooth gas flow and efficient reactions. These electrodes feature a porous structure that allows gases like oxygen or carbon dioxide to pass through while maintaining contact with the liquid electrolyte. This design ensures that the gas reaches the catalyst layer, where the magic happens. The porous nature also helps maintain a high concentration of gas near the catalyst, which boosts reaction efficiency.
For example, in CO2 reduction, the gas diffusion electrode ensures that carbon dioxide molecules interact with the catalyst and the electrolyte simultaneously. This interaction creates a “triple-phase boundary,” where the gas, liquid, and solid meet. This boundary is essential for facilitating reactions that convert CO2 into valuable products like fuels or chemicals.
Explanation of electrochemical reactions facilitated by the system.
Electrochemical reactions in a gas diffusion electrode system rely on the catalyst layer. This layer, often made of materials like platinum or carbon-based compounds, accelerates the reaction between the gas and the electrolyte. When a gas like oxygen interacts with the catalyst, it undergoes a reduction reaction, producing energy or other desired outputs.
Take fuel cells as an example. Here, the gas diffusion electrode enables the oxygen reduction reaction, which generates electricity. Similarly, in hydrogen production, the system supports reactions that split water molecules into hydrogen and oxygen. These processes highlight the versatility of gas diffusion electrodes in driving various electrochemical reactions.
The Process Flow
Interaction between gases, electrodes, and electrolytes.
The process begins when a gas, such as oxygen or carbon dioxide, enters the system. The gas diffusion electrode ensures that the gas flows through its porous structure and reaches the catalyst layer. At the same time, the liquid electrolyte surrounds the electrode, providing ions necessary for the reaction.
This interaction creates a seamless flow of reactants. The gas molecules react with the ions from the electrolyte at the catalyst layer, producing energy or chemical products. For instance, in CO2 electrolysis, the gas diffusion electrode facilitates the conversion of carbon dioxide into useful compounds like ethylene or methanol.
How the system achieves efficiency in energy conversion.
Efficiency is a hallmark of gas diffusion electrode systems. Their design minimizes energy losses and maximizes reaction rates. The porous structure ensures optimal gas transport, while the catalyst layer speeds up the reaction. Together, these features reduce resistance and enhance current density, leading to higher energy output.
In addition, the system’s ability to maintain a high gas concentration near the catalyst plays a crucial role. This feature ensures that the reaction continues without interruptions, improving overall efficiency. Whether it’s powering a fuel cell or producing hydrogen, the gas diffusion electrode system delivers reliable and efficient performance.
Key Components of a Gas Diffusion Electrode System
Every gas diffusion electrode system relies on a combination of well-designed components to function effectively. Let’s break down these key elements and explore their roles in ensuring optimal performance.
Gas Diffusion Electrodes
Structure and material composition.
Gas diffusion electrodes form the backbone of the system. Their structure includes a porous catalyst layer applied to a carrier material, such as woven metal nettings or carbon fleeces. This design allows gases and electrolytes to interact at the catalyst grains, where electrochemical reactions occur. The catalyst layer, often made from materials like platinum or carbon-based compounds, conducts electrons and accelerates reactions. Some advanced designs incorporate porous PTFE-foil or microporous separators to enhance durability and efficiency.
The gas diffusion electrode also features a gas diffusion layer (GDL), which reduces the diffusion length of gases like CO2 to the catalyst surface. This layer ensures that gases reach the active sites quickly, improving reaction rates and overall system performance.
Importance of porosity and conductivity.
Porosity plays a critical role in the effectiveness of gas diffusion electrodes. A porous structure ensures that gases, liquids, and solids meet at the “triple-phase boundary,” where reactions take place. This design enhances mass transport, allowing reactant gases to reach the catalyst efficiently. For example, in CO2 reduction, the porous nature of the electrode ensures a steady supply of CO2 to the catalyst, boosting conversion rates.
Conductivity is equally important. The electrode must conduct electrons effectively to support the electrochemical reactions. High conductivity materials, such as carbon-based compounds, ensure minimal resistance and maximize energy output. Together, porosity and conductivity make gas diffusion electrodes indispensable in achieving high current densities and efficient energy conversion.
Electrolyte
Types of electrolytes used (e.g., liquid, solid).
The electrolyte serves as the medium for ion transfer within the system. Depending on the application, the system may use liquid or solid electrolytes. Liquid electrolytes, such as aqueous solutions, are common in applications like CO2 reduction or hydrogen production. Solid electrolytes, often found in advanced fuel cells, provide durability and reduce leakage risks.
Each type of electrolyte has its advantages. Liquid electrolytes offer flexibility and ease of use, while solid electrolytes provide stability and long-term reliability. The choice depends on the specific requirements of the application.
Role in facilitating ion transfer.
The primary function of the electrolyte is to facilitate ion transfer between the electrodes. It ensures that ions generated during the reaction move seamlessly to the opposite electrode, completing the circuit. For instance, in a fuel cell, the electrolyte transports protons from the anode to the cathode, enabling the oxygen reduction reaction.
A well-chosen electrolyte minimizes resistance and enhances reaction efficiency. It also ensures compatibility with the gas diffusion electrode, maintaining a stable interface for consistent performance.
Supporting Framework
Design considerations for durability and efficiency.
The supporting framework provides structural integrity to the gas diffusion electrode system. It must withstand harsh operating conditions, including high temperatures and corrosive environments. Materials like stainless steel or advanced composites are often used to ensure durability.
Efficiency is another key consideration. The framework must support the seamless integration of components, such as the gas diffusion electrode and electrolyte, without introducing resistance or inefficiencies. A well-designed framework ensures that the system operates reliably over extended periods.
Integration with other system components.
Integration is crucial for the overall performance of the gas diffusion electrode system. The framework must align perfectly with other components, such as the membrane electrode assembly or external power sources. This alignment ensures that gases flow smoothly, reactions occur efficiently, and energy losses are minimized.
For example, in industrial CO2 electrolysis, the framework must support the precise positioning of the gas diffusion electrode and electrolyte to maximize CO2 conversion rates. Proper integration enhances the system’s scalability and adaptability for various applications.
Applications of Gas Diffusion Electrode Systems
Gas diffusion electrode systems have revolutionized several industries by enabling efficient energy conversion and chemical synthesis. Their versatility makes them indispensable in various applications, from clean energy production to cutting-edge research.
Energy Storage and Conversion
Use in fuel cells for clean energy production.
Fuel cells rely heavily on gas diffusion electrodes to produce clean energy. These systems enable the oxygen reduction reaction, a critical process in generating electricity. By facilitating the interaction between oxygen, the catalyst, and the electrolyte, gas diffusion electrodes ensure high efficiency and reliability. For instance, hydrogen fuel cells use these electrodes to convert hydrogen and oxygen into water while producing electricity. This technology powers vehicles, portable devices, and even large-scale energy grids, offering a sustainable alternative to fossil fuels.
Role in batteries and supercapacitors.
Gas diffusion electrodes also play a role in advanced batteries and supercapacitors. Zinc-air batteries, for example, use these electrodes to enable the oxygen reduction reaction, which enhances energy density and storage capacity. Similarly, nickel-metal hydride batteries benefit from the efficient gas transport provided by these systems. In supercapacitors, gas diffusion electrodes improve charge-discharge cycles by facilitating rapid ion movement. These advancements make energy storage systems more efficient, durable, and suitable for modern energy demands.
Industrial Processes
Application in chemical synthesis (e.g., hydrogen production).
Industries use gas diffusion electrode systems extensively for chemical synthesis. Hydrogen production through water electrolysis is a prime example. The system splits water molecules into hydrogen and oxygen, with the gas diffusion electrode ensuring efficient gas flow and reaction rates. This method provides a clean and sustainable way to produce hydrogen, which serves as a key component in fuel cells, ammonia synthesis, and other industrial processes.
Use in environmental technologies like CO2 reduction.
Gas diffusion electrodes have become essential in environmental technologies, particularly for carbon dioxide reduction. These systems enable the electrochemical conversion of CO2 into valuable products like ethylene, methanol, or carbon monoxide. By maintaining a high concentration of CO2 near the catalyst, the electrode enhances reaction efficiency and output. This technology not only helps reduce greenhouse gas emissions but also creates opportunities for sustainable chemical production. For instance, CO2 electrolysis using gas diffusion electrodes has shown significant progress in achieving high current densities and scalability.
Emerging Technologies
Potential in next-generation energy systems.
The potential of gas diffusion electrode systems in next-generation energy solutions is immense. Researchers are exploring their use in solid oxide fuel cells, which operate at higher temperatures and offer greater efficiency. These systems could also play a role in hybrid energy setups, combining renewable sources like solar or wind with electrochemical storage. By integrating gas diffusion electrodes, these technologies aim to achieve better performance and sustainability.
Research and development trends.
Ongoing research continues to push the boundaries of gas diffusion electrode applications. Scientists are investigating new materials for the catalyst layer to improve durability and reduce costs. Innovations in reactor designs, such as gas-fed electrolysers, aim to enhance mass transport and reaction rates. Studies on failure modes and long-term performance are helping refine these systems for industrial-scale use. The focus remains on making gas diffusion electrode systems more efficient, adaptable, and accessible for a wide range of applications.
Advantages and Challenges of Gas Diffusion Electrode Systems
Gas diffusion electrode systems have transformed the way industries approach energy conversion and chemical processes. They bring a host of benefits, but like any technology, they also face certain challenges. Let’s dive into both sides to understand their impact better.
Advantages
High efficiency in energy conversion.
Gas diffusion electrode systems excel in energy conversion. Their design ensures that gases like oxygen or carbon dioxide reach the catalyst layer efficiently. This feature enhances mass transport and boosts reaction rates. For instance, in fuel cells, these systems achieve higher current densities compared to traditional electrodes. By maintaining a high gas concentration near the catalyst, they minimize energy losses and maximize output. This efficiency makes them a preferred choice for applications requiring reliable and consistent energy production.
Sustainability and environmental benefits.
Sustainability stands out as a key advantage of gas diffusion electrode systems. They enable processes like CO2 reduction, which converts harmful greenhouse gases into valuable products such as fuels or chemicals. This capability not only reduces carbon emissions but also supports the development of a circular economy. Additionally, these systems rely on clean energy sources, making them an environmentally friendly alternative to fossil fuel-based technologies. Their role in hydrogen production further underscores their potential to drive a greener future.
Cost-effectiveness in long-term operations.
While the initial investment might seem significant, gas diffusion electrode systems prove cost-effective over time. Their high efficiency reduces energy consumption, leading to lower operational costs. Moreover, their durability and ability to maintain performance over extended periods make them a financially viable option for industries. For example, in large-scale CO2 electrolysis, these systems deliver consistent results, minimizing the need for frequent replacements or repairs. This long-term reliability translates into substantial savings for businesses.
Challenges and Limitations
Initial setup costs and material challenges.
The upfront costs of gas diffusion electrode systems can pose a barrier for some industries. High-quality materials like platinum or advanced carbon compounds used in the catalyst layer contribute to these expenses. Additionally, the manufacturing process for components like the gas diffusion layer requires precision, which adds to the cost. Despite these challenges, ongoing research aims to develop more affordable materials without compromising performance.
Maintenance and durability concerns.
Operating conditions can impact the durability of gas diffusion electrode systems. Factors like high temperatures, corrosive environments, or prolonged use may lead to wear and tear. Maintenance becomes crucial to ensure consistent performance. For instance, the porous structure of the electrode might degrade over time, affecting gas flow and reaction rates. Regular inspections and timely replacements of worn-out components can help address these concerns effectively.
Need for further research to optimize performance.
Although gas diffusion electrode systems have achieved remarkable progress, there’s still room for improvement. Researchers continue to explore new materials and designs to enhance efficiency and reduce costs. For example, innovations in catalyst composition aim to increase reaction rates while minimizing material usage. Studies on failure modes and long-term performance provide valuable insights for refining these systems. Advancing this technology requires sustained efforts in research and development.
“Gas diffusion electrode systems represent a leap forward in energy and industrial applications. Their advantages far outweigh the challenges, making them a cornerstone of sustainable innovation.”
Gas diffusion electrode systems have emerged as a game-changer in energy conversion and industrial processes. Their unique design enables efficient electrochemical reactions, making them indispensable for applications like fuel cells, CO2 reduction, and hydrogen production. By combining advanced components such as porous electrodes, electrolytes, and robust frameworks, these systems deliver unmatched performance and sustainability. Companies like Ningbo VET Energy Technology Co., Ltd. play a pivotal role in driving innovation. Their expertise in fuel cell parts and membrane electrode assemblies ensures the continuous evolution of this technology, paving the way for a greener and more efficient future.
FAQ
What are gas diffusion electrodes composed of?
Gas diffusion electrodes (GDEs) consist of two main components: a gas diffusion layer (GDL) and a catalyst layer. The GDL provides a porous structure that allows gases to flow efficiently, while the catalyst layer facilitates the electrochemical reactions. Together, these layers create the “triple-phase boundary,” where gases, liquids, and solids interact to drive reactions.
How do gas diffusion electrodes improve CO2 electrolysis?
Gas diffusion electrodes play a crucial role in CO2 electrolysis by maintaining a high concentration of carbon dioxide near the catalyst. This design enhances reaction efficiency and enables the production of valuable products like ethylene or methanol. Researchers emphasize the importance of using gas-fed electrolysers with GDEs to achieve high current densities and selectivities, which are essential for scaling up CO2 electrolysis.
What is the purpose of the gas diffusion layer in a GDE?
The gas diffusion layer (GDL) ensures smooth gas transport to the catalyst layer. It reduces the diffusion distance for gases like oxygen or carbon dioxide, allowing them to reach the active sites quickly. This feature improves reaction rates and overall system performance. The GDL also provides structural support, ensuring durability under various operating conditions.
Why are gas-fed electrolysers important for CO2 reduction?
Gas-fed electrolysers are vital for CO2 reduction because they enable higher current densities and better selectivity compared to traditional liquid-phase systems. By integrating gas diffusion electrodes, these electrolysers ensure efficient gas flow and reaction rates. This approach is critical for industrial-scale applications, where maximizing output and minimizing energy losses are priorities.
What was the focus of the study on gas diffusion electrode systems for CO2 conversion?
The study titled “Investigation of Gas Diffusion Electrode Systems for the Electrochemical CO2 Conversion” explored how GDEs facilitate the conversion of carbon dioxide into useful products. It examined the physical and chemical phenomena that occur during the process, providing insights into optimizing GDE performance for CO2 electrolysis.
Can gas diffusion electrodes be used in hydrogen production?
Yes, gas diffusion electrodes are widely used in hydrogen production through water electrolysis. They enable efficient gas flow and reaction rates, splitting water molecules into hydrogen and oxygen. This method offers a clean and sustainable way to produce hydrogen, which serves as a key component in fuel cells and other industrial processes.
What materials are commonly used in the catalyst layer of GDEs?
The catalyst layer in gas diffusion electrodes often includes materials like platinum, carbon-based compounds, or other advanced catalysts. These materials accelerate electrochemical reactions and ensure high conductivity. Researchers continue to explore new catalyst materials to improve efficiency and reduce costs.
How do gas diffusion electrodes contribute to environmental sustainability?
Gas diffusion electrodes support environmental sustainability by enabling technologies like CO2 reduction. They convert greenhouse gases into valuable products, such as fuels or chemicals, reducing carbon emissions. Additionally, their role in clean energy production, such as in fuel cells and hydrogen generation, helps transition industries away from fossil fuels.
Are gas diffusion electrodes suitable for next-generation energy systems?
Absolutely. Gas diffusion electrodes hold immense potential for next-generation energy systems. They are being explored for use in solid oxide fuel cells, hybrid energy setups, and advanced electrochemical reactors. Their ability to enhance efficiency and scalability makes them a cornerstone of future energy innovations.
What challenges do gas diffusion electrodes face in industrial applications?
Gas diffusion electrodes face challenges like material costs, durability under harsh conditions, and the need for precise manufacturing. High-quality materials, such as platinum, can increase initial costs. Over time, factors like corrosion or wear may impact performance. However, ongoing research aims to address these issues by developing more affordable and durable designs.