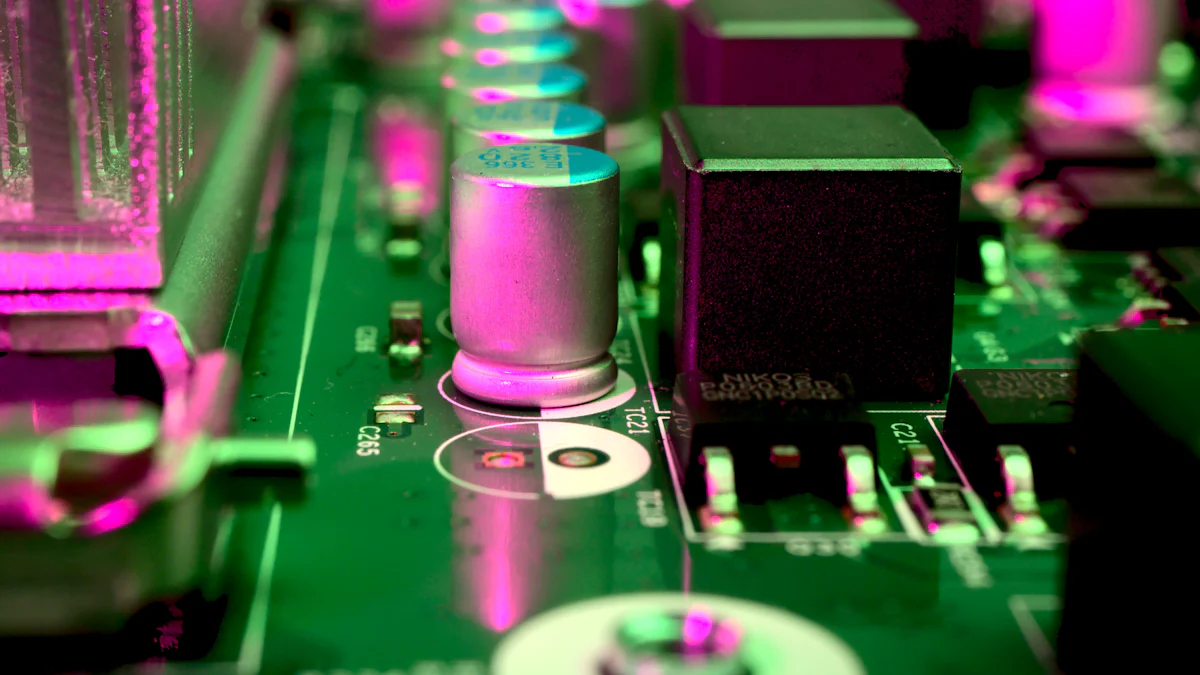
ICP Etching Carriers revolutionize the performance of ICP etching by addressing critical challenges in precision manufacturing. They enhance etching uniformity by ensuring consistent plasma exposure across the wafer surface. Their ability to stabilize thermal conditions prevents overheating and mitigates thermal gradients, which can otherwise lead to defects or uneven etch rates. Additionally, ICP etching carriers provide essential mechanical support for thin and fragile wafers, reducing the risk of damage during handling or processing. By integrating these carriers into the etching process, manufacturers achieve higher reliability and improved results in advanced applications.
Key Takeaways
- ICP Etching Carrier Wafers enhance etching uniformity by ensuring consistent plasma exposure across the wafer surface.
- These carriers provide essential mechanical support for thin and fragile wafers, reducing the risk of damage during handling.
- By stabilizing thermal conditions, carrier wafers prevent overheating and mitigate thermal gradients, leading to more reliable etching results.
- Carrier wafers help maintain a flat and stable wafer surface, which is crucial for achieving precise and uniform etching.
- They protect active wafers from debris and contamination, ensuring a clean surface for high-quality etching outcomes.
- Using carrier wafers improves yield and reliability in high-volume manufacturing by minimizing defect rates.
- The integration of carrier wafers supports process reproducibility, enabling consistent results across multiple production cycles.
The Role of ICP Etching Carrier Wafers
Supporting Thin and Fragile Wafers
Preventing mechanical damage during handling and processing
Thin and fragile wafers often face risks during handling and processing. ICP Etching Carrier wafers act as a protective layer, reducing the likelihood of mechanical damage. These carriers provide robust mechanical support, ensuring that delicate wafers remain intact throughout the etching process. By stabilizing the wafer, they prevent cracks, chips, or other physical defects that could compromise the final product. Manufacturers rely on carrier wafers to maintain the structural integrity of these sensitive materials, especially in high-precision applications.
Enabling the use of thinner wafers for advanced applications
The demand for thinner wafers continues to grow in advanced semiconductor manufacturing. Carrier wafers enable the use of these ultra-thin wafers by offering essential support during processing. Without this support, thinner wafers would be too fragile to withstand the rigorous conditions of ICP etching. Materials like glass, quartz, or silicon are commonly used for carrier wafers due to their mechanical robustness and thermal stability. These properties allow manufacturers to push the boundaries of wafer thickness, unlocking new possibilities for innovation in microelectronics and other cutting-edge fields.
Enhancing Thermal and Mechanical Stability
Distributing heat evenly during the etching process
Thermal stability plays a critical role in achieving consistent etching results. Carrier wafers help distribute heat evenly across the wafer surface during the ICP etching process. This uniform heat distribution prevents localized overheating, which could otherwise lead to defects or uneven etch rates. High-end carrier wafers, made from materials like quartz or silicon, excel in thermal conductivity, ensuring that heat is managed effectively. This capability enhances the overall quality of the etched features and supports the production of reliable, high-performance devices.
Mitigating thermal gradients to prevent variations in etch rates
Thermal gradients can cause significant variations in etch rates, leading to inconsistencies in the final product. Carrier wafers mitigate these gradients by maintaining a stable thermal environment throughout the etching process. Their ability to resist high temperatures and maintain low tolerances ensures that the wafer remains uniformly exposed to the plasma. This stability minimizes variations in etch depth and quality, making carrier wafers indispensable for achieving precision in advanced manufacturing.
Improving Etching Uniformity with ICP Etching Carrier Wafers
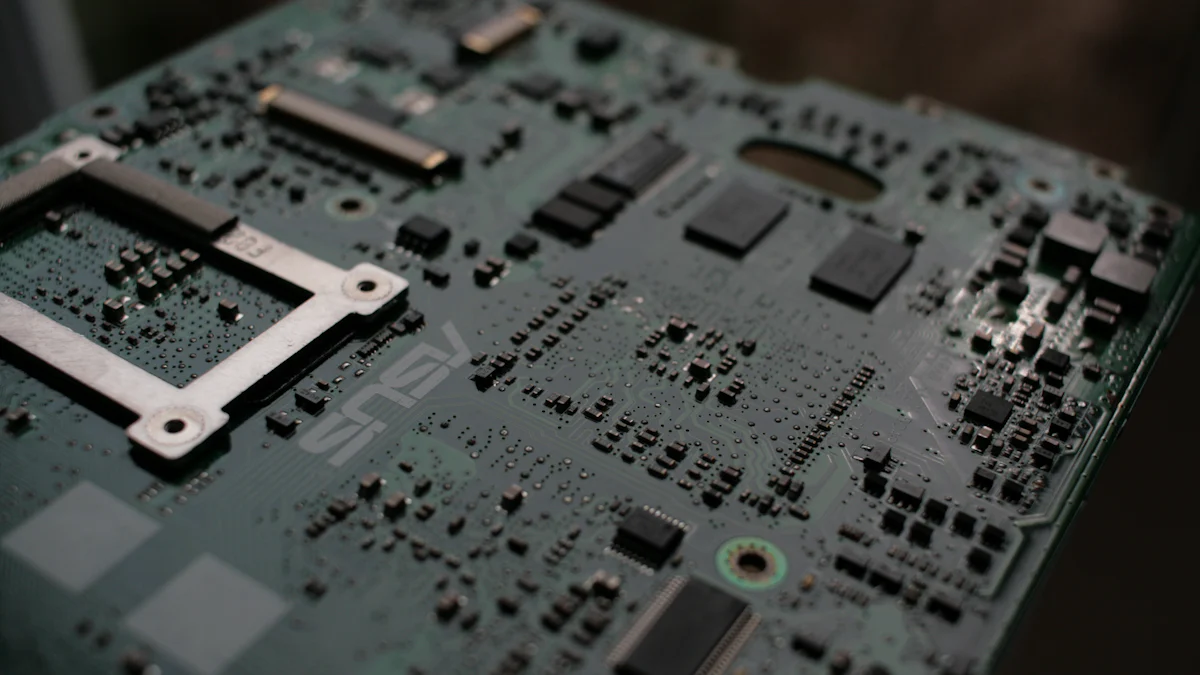
Ensuring Consistent Plasma Exposure
Maintaining a flat and stable wafer surface
A flat and stable wafer surface is essential for achieving uniform etching results. ICP Etching Carrier wafers provide the necessary support to maintain this stability throughout the etching process. Without this support, wafers may warp or shift, leading to uneven plasma exposure. The carrier wafers act as a foundation, ensuring that the wafer remains securely positioned within the etching chamber. This stability minimizes distortions and enhances the precision of the etched features, which is critical for high-performance applications.
Evenly distributing plasma across the wafer to minimize etching depth variations
Plasma distribution plays a pivotal role in determining the uniformity of the etching process. Carrier wafers help evenly distribute plasma across the wafer surface, reducing the likelihood of etching depth variations. By creating a uniform carrier layer, these wafers ensure that every part of the wafer receives consistent plasma exposure. This consistency improves the overall quality of the etched patterns and reduces the risk of defects. Manufacturers benefit from this enhanced uniformity, as it leads to higher yields and more reliable device performance.
Reducing Edge Effects
Mitigating over-etching or under-etching at wafer edges
Edge effects, such as over-etching or under-etching, often compromise the quality of etched wafers. Carrier wafers address this issue by stabilizing the wafer edges during the etching process. This stabilization prevents excessive plasma concentration at the edges, which can lead to over-etching. At the same time, it ensures that the edges receive adequate plasma exposure to avoid under-etching. By mitigating these edge effects, carrier wafers enhance the precision of the etching process and improve the overall uniformity of the wafer.
Enhancing uniformity for high-precision applications
High-precision applications demand exceptional uniformity in etched features. Carrier wafers play a crucial role in meeting this requirement by minimizing variations across the wafer surface. Their ability to maintain a stable and uniform environment within the etching chamber ensures that the entire wafer is etched with consistent quality. This uniformity is particularly important for advanced manufacturing processes, where even minor deviations can impact the performance of the final product. By enhancing etching uniformity, carrier wafers enable manufacturers to achieve the precision needed for cutting-edge technologies.
Reducing Defects and Contamination
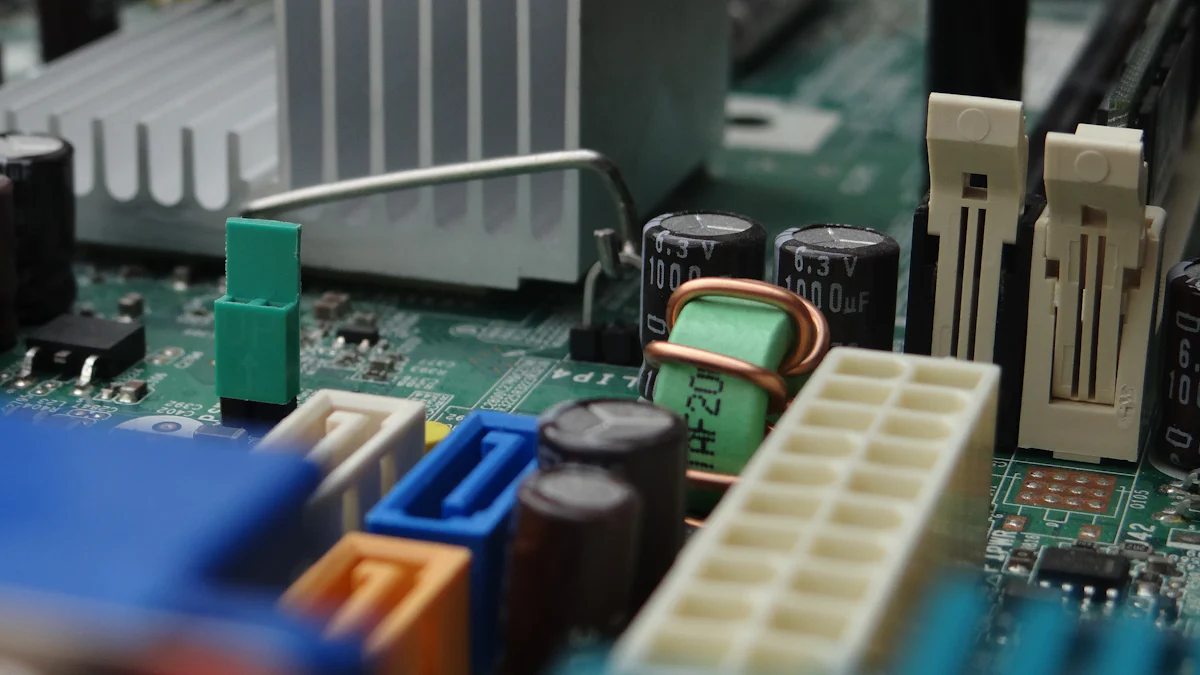
Protecting the Wafer Surface
Shielding the active wafer from debris and contamination
Carrier wafers play a critical role in shielding active wafers from debris and contamination during the ICP etching process. The etching environment often exposes wafers to particles and residues that can compromise their surface quality. Carrier wafers act as a barrier, preventing these contaminants from reaching the active wafer. This protective function ensures that the wafer remains clean, which is essential for achieving precise etching results. By maintaining a pristine surface, manufacturers can produce high-quality devices with fewer defects.
Preventing micro-scratches and other surface defects
Handling and processing wafers without adequate support can lead to micro-scratches and other surface defects. These imperfections can degrade the performance of the final product. Carrier wafers provide a stable and secure base, reducing the risk of physical damage during the etching process. Materials like quartz or silicon, commonly used for carrier wafers, offer excellent mechanical properties that protect the wafer surface. This protection is especially important for advanced applications, where even minor defects can impact functionality.
Improving Yield and Reliability
Reducing defect rates in high-volume manufacturing
High-volume manufacturing demands consistency and reliability. Defects can significantly reduce yield, leading to increased costs and wasted resources. Carrier wafers help minimize defect rates by stabilizing the wafer and ensuring uniform processing conditions. Their ability to maintain a clean and controlled environment during etching reduces the likelihood of contamination and physical damage. This stability allows manufacturers to achieve higher yields, making carrier wafers indispensable for large-scale production.
Enhancing the quality of etched features for advanced devices
The quality of etched features directly affects the performance of advanced devices. Carrier wafers contribute to this quality by providing thermal and mechanical stability throughout the etching process. They ensure that the wafer remains flat and evenly exposed to plasma, resulting in precise and uniform etching. This precision is crucial for applications like microelectronics and 3D wafer-level packaging, where intricate patterns and structures are required. By enhancing the quality of etched features, carrier wafers enable the production of cutting-edge technologies.
Enhancing Process Stability with ICP Etching Carrier Wafers
Maintaining Consistent Etching Conditions
Stabilizing wafer positioning within the etching chamber
Precise wafer positioning is essential for maintaining consistent etching conditions. ICP Etching Carrier wafers provide the mechanical support needed to stabilize thin and fragile wafers during the etching process. Without this stabilization, wafers may shift or warp, leading to uneven plasma exposure and inconsistent results. Carrier wafers ensure that the wafer remains securely positioned within the etching chamber, minimizing movement and maintaining alignment throughout the process. This stability is particularly important for advanced manufacturing techniques, where even minor misalignments can compromise the quality of the final product.
Carrier wafers also simplify handling by acting as a temporary support structure. They bond to the wafer during processing and can be detached afterward using specialized de-bonding technologies. This temporary stabilization allows manufacturers to process thin wafers without risking damage or misalignment, ensuring consistent etching performance across multiple production cycles.
Reducing variability in plasma density and energy distribution
Variability in plasma density and energy distribution can significantly impact the quality of etched features. Carrier wafers help reduce this variability by creating a uniform environment within the etching chamber. Their ability to maintain a flat and stable wafer surface ensures that plasma interacts evenly with the wafer, minimizing fluctuations in etch rates and depths. This uniformity is critical for achieving high-precision results, especially in applications that require intricate patterns or structures.
The material properties of carrier wafers, such as thermal expansion adjustment and chemical resistance, further enhance their ability to stabilize etching conditions. These properties allow carrier wafers to withstand the rigorous demands of the etching process while maintaining consistent performance. By reducing variability in plasma conditions, carrier wafers enable manufacturers to produce reliable and high-quality devices.
Enabling Repeatable Results
Supporting process reproducibility across multiple wafers
Reproducibility is a key factor in high-volume manufacturing. ICP Etching Carrier wafers play a vital role in supporting process reproducibility by providing consistent mechanical and thermal stability across multiple wafers. Their robust design ensures that each wafer undergoes the same processing conditions, reducing variability between production runs. This consistency allows manufacturers to achieve uniform results, even when processing large batches of wafers.
The use of carrier wafers also simplifies the handling of thin and fragile wafers, which are more prone to stress and breakage. By providing a stable support structure, carrier wafers minimize the risk of damage during processing, ensuring that each wafer meets the same high-quality standards. This reliability is essential for maintaining efficiency and reducing waste in large-scale production environments.
Improving long-term reliability in production environments
Long-term reliability is crucial for sustaining high-performance manufacturing processes. Carrier wafers contribute to this reliability by enhancing the durability and stability of the etching process. Their ability to maintain consistent etching conditions over time reduces the likelihood of defects and ensures that production remains efficient and cost-effective.
In addition to stabilizing the wafer, carrier wafers protect it from environmental factors that could compromise its quality. Their chemical resistance and thermal stability prevent contamination and damage, preserving the integrity of the wafer throughout the etching process. This protection not only improves the quality of individual wafers but also enhances the overall reliability of the production environment. By enabling repeatable results and reducing variability, carrier wafers play a critical role in advancing semiconductor manufacturing.
ICP Etching Carrier wafers have become essential in semiconductor manufacturing due to their ability to enhance precision and reliability. They ensure uniform etching, reduce defects, and stabilize processes, making them indispensable for high-performance applications. By supporting fragile wafers and maintaining thermal stability, they enable advanced techniques that meet the growing demands of modern technology. Their role in protecting wafers and ensuring consistent results highlights their importance in achieving high-quality production. As the industry evolves, carrier wafers will continue to drive innovation and efficiency in etching processes.