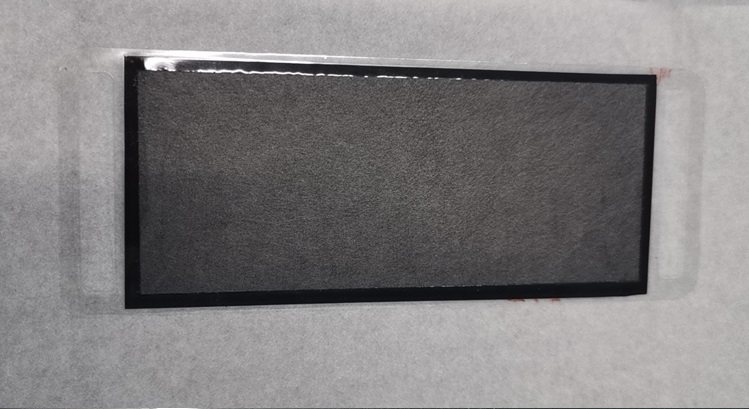
燃料電池 MEA、または膜電極アセンブリは、aのコアコンポーネントとして機能します 燃料電池エンジン. . 陽子交換膜、触媒層、電極を単体に統合し、電気を発生させる化学反応を可能にします。 このアセンブリは燃料電池の性能、耐久性および費用効果が大きいことに直接影響を与えます。 クリーンエネルギーのグローバル需要が高まるにつれて、MEA技術の進歩は、水素発電ソリューションの採用を推進する重要な役割を果たしています。 燃料電池市場が大きく成長するにつれて、持続可能なエネルギーシステムの未来を形づける上で、MEAsは不可欠です.
要点
- 燃料電池 MEAs は、水素発電ソリューションの性能と効率性のために重要であり、メーカーにとって重要な焦点を挙げています.
- バラード・パワー・システムズやプラグ・パワーなどのリーディング・カンパニーは、成長するグローバル・デマンドに対応する耐久性と効率性を強化し、MEA技術のイノベーションを推進しています.
- サステナビリティは、環境目標に合わせ、高性能なMEAsを開発する、ジョンソン・マテシーやBASFなどのメーカーにとって優先的です.
- トヨタやヒュンダイモビスなどの燃料電池技術に急速に普及しているアジア太平洋地域は、自動車用MEAの量産を担当しています.
- 次世代のトレンドは、水素搭載車両の需要が高まっています。クリーンな輸送の将来にMEAsの重要性を強調しています.
- MEAの生産におけるコストダウンとスケーラビリティは、さまざまな分野にわたってよりアクセス可能な水素ソリューションを作るために不可欠です.
- 燃料電池技術の高度化と持続可能性目標の達成のために、メーカー、政府、研究機関とのコラボレーションが不可欠です.
2024年の燃料電池MEAsのリーディングメーカー
バラードパワーシステムズ(カナダ)
バラード・パワー・システムズは、革新的な燃料電池ソリューションの開発におけるグローバル・リーダーです。 会社は専門にします プロトン交換膜(PEM)燃料電池技術効率および信頼性のために広く認められている、。 Ballardの専門知識は、燃料電池システムにおける重要なコンポーネントである膜電極アセンブリ(MEAs)の配合と統合に拡張します.
バラードは、カナダ・バーナビーの3つの先進施設を運営し、年間1万台のMEAsと燃料スタックの生産能力を組み合わせています.
会社は革新へのコミットメントを一貫して示しました。 たとえば、2020年、バラードは、バンクーバー本社で製造能力を拡張し、6倍にMEA生産量を増加させました。 この戦略的な動きは、Barardの献身を強調し、燃料電池MEAsの世界的な要求に応えます。 自動車、船舶、鉄道、材料の取扱分野を横断する強力な市場の存在により、Barardはクリーンエネルギー技術の未来を形作り続けています.
プラグパワー(米国)
水素燃料電池のMEAsの生産に焦点を合わせる水素経済のキー プレイヤーとして、プラグ力は出ました。 同社のMEAsは、生産、貯蔵、エネルギー生成システムを含むターンキー水素ソリューションに不可欠です。 MEAの設計のPlug Powerの革新は燃料電池の効率そして耐久性をかなり高めましたり、それらにさまざまな適用のための好まれる選択をします.
プラグパワーは、全世界で6万の燃料電池システムを展開し、約1億時間以上稼働しています.
同社の広範なフットプリントは、世界最大の液体水素燃料ステーションネットワークが含まれています。 エンドツーエンドのグリーン水素エコシステムを構築することにより、Plug Powerは、Amazon、Walmart、BMWなどの主要なクライアントをサポートし、持続可能性の目標を達成します。 北米市場でのリーダーシップは、燃料電池MEA技術の進歩におけるその重要な役割を果たしています.
ジョンソン・マテージ(イギリス)
ジョンソンマテージ(JM)は、燃料電池MEAsのコアコンポーネントである触媒コーティング膜の専門知識で有名です。 同社は、高品質のMEAコンポーネントを製造するために、高度なリサイクル機能と貴金属の安全な供給を活用しています。 JMのサステナビリティに重点を置き、クリーンエネルギーソリューションのグローバル・プッシュと一体化したイノベーションを推進しています.
ジョンソン・マテシーは、Plug Powerと長期的な戦略的パートナーシップを確立し、触媒、膜、触媒コーティング膜(CCM)の主要サプライヤーとなりました.
このコラボレーションは、水素経済を支えるJMのコミットメントをベースとしています。 ジョンソン・マテシーは、欧州に強い存在感を持ち、持続可能で効率的な燃料電池MEA技術の開発を続けてきました.
ゴア燃料電池技術(米国)
ゴア燃料電池技術は、開発の先駆者として確立しました 高性能 MEA材料. . 同社は、1994年に最初の市販の膜電極アセンブリ(MEA)を導入し、燃料電池産業の革新のためのベンチマークを設定しました。 Goreの専門知識は、プロトン・エクスチェンジ・メンブレン(PEM)、触媒コーティング膜、および燃料電池の効率と信頼性を高めるために重要なMEA技術にあります.
ゴアのMEAsは、優れた耐久性と導電性を広く認識し、自動車および静止電力用途に適した選択肢となっています.
ヒュンダイモーターとキアとの長年にわたる協業により、燃料電池技術の進歩に取り組みます。 15年以上にわたるパートナーシップは、Goreの最先端PEM技術を次世代燃料電池システムに統合することに重点を置いています。 このコラボレーションは、特に商用車における燃料電池の性能と寿命を大幅に向上させました。 Goreは、クリーンエネルギー市場の進化する要求を満たす革新的なソリューションを提供することで、業界をリードし続けています.
ヒュンダイ・モビス(韓国)
ヒュンダイ・モビスは生産のpivotal役割を担います 燃料電池用電気自動車(FCEV). . アジア市場での主要選手として、水素動力を与えられた車両の需要の高まりを支えるため、量産化の大きな課題を抱えています。 ヒュンダイモビスは、効率性、耐久性、コスト効率性を兼ね備えた燃料電池システムの開発に注力しています.
ヒュンダイモビスは、韓国最大級の水素燃料電池製造施設で、年間4万台を収容しています.
ヒュンダイのNEXO FCEVや水素搭載車両向けに、量産の進展が実現しました。 ユンダイ・モビスは、自動車工学のノウハウを活かし、グローバル燃料電池市場におけるリーダーとして位置付けています。 その貢献は、自動車業界を超えて、静止した電力と産業機器のアプリケーションを拡張します.
トヨタ(日本)
トヨタは世界的なリーダーとして誕生しました 自動車用途向け独自のMEA設計. . 同社は、効率と長寿に焦点を合わせ、トヨタ・ミライのようなパワーカーの燃料電池システムの開発を推進しています。 トヨタのMEAsは要求の厳しい条件の下で耐久性を維持している間高性能を渡すように設計されます.
トヨタの燃料電池技術は、世界2万台以上のミライ単位でマイルストーンを達成し、MEAの設計の信頼性を示しています.
自動車業界を超えてのインパクトが高まっています。 トヨタは、政府や組織と連携し、水素インフラやクリーンエネルギーの採用を推進しています。 燃料電池業界における持続可能性とリーダーシップへのコミットメントをベースとしたMEA技術への革新的なアプローチ。 トヨタの進展は、今後も水素動力の未来をグローバル規模で形作り続けています.
寧波VETエネルギー技術有限公司(中国)
ニンポー VET エネルギーテクノロジー株式会社は、高品質の燃料電池MEAsの著名なメーカーとして設立しました。 同社は、水素エネルギー市場の成長要求を満たす信頼性の高い効率的なMEAを提供することに焦点を当てています。 Ningbo VET Energyは、先進的な製造技術を活用することで、燃料電池用途に欠かせない優れた性能と耐久性を発揮します.
ニンポー VET エネルギーは費用効果が大きい製造業の革新のために、妥協する質なしで競争の価格で燃料電池MEAsの生産を可能にします.
堅牢性に対する当社のコミットメントは、クリーンエネルギー分野におけるスケーラブルなソリューションを求める企業にとって好まれる選択肢となっています。 Ningbo VET Energyは、世界的な市場プレゼンスを拡大する戦略的重点を置き、国際燃料電池業界における主要なプレーヤーとしての地位を強化し続けています.
SGLカーボン(ドイツ)
SGL カーボンは、燃料電池システムの効率性を高める軽量で耐久性のあるコンポーネントを提供する燃料電池 MEAs の炭素ベースの材料の開発を専門としています。 同社の専門知識は、現代の燃料電池アプリケーションに不可欠である重量削減と材料の長寿の課題に対処する革新的なソリューションを作成しています.
SGL Carbonの製品は、欧州全域で広く使用され、地域のクリーンエネルギーへの取り組みに著しく貢献しています.
同社は、EU(欧州連合)の厳格な環境規制に適合する持続可能性に焦点を当てています。 高性能材料を提供することで、SGLカーボンは自動車、産業、固定電力分野における燃料電池技術の進歩をサポートします。 欧州市場への貢献は、最先端の燃料電池部品の開発のリーダーとしての役割を果たしています.
アドベントテクノロジーズ(米国)
アドベント・テクノロジーズは、多様な用途向けに設計された高温燃料電池MEAの先駆的な作業を目指しています。 これらのMEAsは、堅牢で汎用性の高い燃料電池ソリューションを必要とする業界に適した、極端な条件下で卓越した性能を提供します。 燃料の柔軟性のアドベントの革新により、MEAsはさまざまな燃料源と効率的に作動させ、適応性を高めます.
同社は、燃料電池の体重、電力、寿命を決定する上でMEAの重要性を強調し、全体的なコスト効率性を強調しています.
アドベント・テクノロジーズは、クリーンエネルギー分野の進化するニーズに応える先進的なMEAソリューションを提供することで、北米での市場参入を着実に拡大しました。 イノベーションとパフォーマンスへのこだわりは、持続可能なエネルギーシステムの未来への重要な貢献として位置付けています.
BASF(ドイツ)
燃料電池MEAsのための触媒および膜の技術
BASFは、先進触媒・膜技術の開発のリーダーとして、 燃料電池 MEAs. . 会社案内 セルテック® MEAs、15年以上の生産にありました、例外的な長期安定性および高性能を示します。 これらのMEAsは、陽極、膜、陰極、内部シールを単一のユニットに統合し、厳しい動作条件下で堅牢な機能性を保証します。 BASFの革新的なプロトン導電膜は180°Cまでの温度で作動し、より効率的な水素分離を可能にし、燃料電池システムの耐久性を高めます.
BASF はまたテストしました Celtec®技術 過去5年間の電気化学式水素分離のために、水素関連ソリューションの推進に取り組みます.
最先端の材料を厳格な試験と組み合わせることで、BASFは、多様な用途における信頼性と効率性を確保し、MEA技術の限界を押し続けます.
産業および自動車適用に焦点を合わせて下さい
BASFのMEAソリューションは、それぞれ固有の要求に対応する、産業および自動車分野の両方に対応します。 産業用アプリケーションでは、高温膜は、ガス混合物から効率的な水素抽出を可能にし、一貫した信頼性の高いエネルギー出力を必要とするプロセスをサポートしています。 自動車用途では、BASFのMEAsは、さまざまな運用条件下で燃料電池車に電力を供給するために必要な耐久性と性能を提供します.
BASFのMEAsの汎用性は、持続可能でスケーラブルなエネルギーソリューションを求める業界に好まれる選択肢になります.
このデュアルフォーカスにより、BASFは複数の分野にわたる水素発電技術の採用に著しく貢献し、クリーンエネルギー市場でのキープレーヤーとしての地位を強化することができます.
欧州燃料電池市場への進出
BASFは、地域の持続可能性の目標と革新を合わせ、欧州の燃料電池市場の発展に重要な役割を果たしています。 同社は、高性能自動車MEAの開発に重点を置いた、欧州連合のGAIAプロジェクトなど、水素ベースの技術の普及を目指した取り組みを積極的に支援しています。 BASFの貢献は、広範な採用に欠かせないコスト、耐久性、および運用目標を達成するのに役立ちます.
BASFのイノベーションとコラボレーションへのコミットメントは、燃料電池技術のグローバルリーダーとしての欧州の地位を強化します.
MEAの設計と生産の進歩を駆動することにより、BASFは水素経済の成長だけでなく、クリーナーやより持続可能な未来の道を舗装するのに役立ちます.
燃料電池MEAsのグローバル市場風景
メーカーの地理的分布
北アメリカ: 主要なプレーヤーおよび市場の傾向
北米は、燃料電池技術の研究開発と商品化に大きな拠点として誕生しました。 クリーンエネルギーソリューションの領域の焦点は、研究開発プログラムに大きな投資を主導しています。 米国は、水素ベースの技術の早期採用者として、堅牢なインフラと政府主導の取り組みで市場をリードしています.
北米は、2032年までに20%の化合物年間成長率(CAGR)で成長し、燃料電池技術の商業導入に燃料を供給する.
プラグパワーやボラードパワーシステムズなどの大手メーカーが、この地域で強い存在感を確立しました。 燃料電池のMEAの生産の彼らの進歩は水素動力を与えられた車および静止した電力システムの採用を支えました。 持続可能なエネルギーソリューションの需要が高まっています。北米は、グローバル市場における主要なプレーヤーとして位置します.
ヨーロッパ:イノベーションと持続可能性の焦点
欧州は、燃料電池技術への取り組みにおいて、持続可能性と革新を優先しています。 地域の厳しい環境規制と炭素排出量削減へのコミットメントは、水素ベースの輸送の採用を加速しました。 ジョンソン・マテージやBASFなどのヨーロッパのメーカーは、これらの目標に合わせ、高性能なMEAsの開発に注力しています.
欧州は、高電力効率車両の生産を強調し、欧州連合のGAIAプロジェクトのような取り組みにより、水素ベースの輸送を推進しています.
政府、研究機関、民間企業との協業により、燃料電池のイノベーションのための繁栄したエコシステムを構築しました。 コストと耐久性に関する課題に取り組むことで、欧州は先進的なMEA技術の開発に着手し続けています.
アジアパシフィック: 急速な成長と技術の進歩
アジアパシフィックは、電気・水素搭載車両の需要が高まっています。 中国、日本、韓国などの国は、燃料電池技術のスケールアップと展開に大きな課題を抱えています.
地域は、インド、オーストラリア、シンガポールなどの国におけるクリーンエネルギーと水素インフラの整備を支援する政府の政策から急速に成長しています.
トヨタ、ヒュンダイ・モビス、ニンポーVETエネルギー技術Co.などのメーカーは、MEAの生産に革新的なアプローチで市場を支配します。 アジア・パシフィックは、技術の発展と費用対効果の高い製造に注力し、グローバル燃料電池業界におけるリーダーとして位置付けています.
燃料電池MEA市場における新興トレンド
水素搭載車両のリース需要
洗剤の交通機関の解決のための全体的な押しはのための要求のサージに導きました 水素駆動車. . トヨタやヒュンダイなどの自動車メーカーが、先進的なMEAに頼る燃料電池電気自動車(FCEV)を導入し、最適な性能を実現しました。 この傾向は、持続可能なモビリティオプションのための成長する消費者の好みを反映しています.
水素動力を与えられた車両は、ゼロエミッションソリューションを提供し、将来の輸送システムの重要なコンポーネントとなります.
MEAの耐久性および効率の進歩
メーカーは耐久性および効率性を高めるためにMEAの設計で革新し続けます。 Gore Fuel Cell TechnologiesやAdvent Technologiesなどの企業は、MEAsの寿命と伝導性を向上させる高性能材料を開発しました。 これらの進歩は、燃料電池技術の重要な課題に対処し、多様な条件下で信頼性の高い操作を保証します.
MEAの耐久性の向上により、メンテナンスコストを削減し、燃料電池システムの全体的な生存率を増加させます.
コストダウンとスケーラビリティの焦点
燃料電池業界は、水素ベースのソリューションをより使いやすくするためのコストダウンとスケーラビリティを優先しました。 寧波VETエネルギー技術有限公司のようなメーカーは、品質を妥協することなく、費用対効果の高い生産技術を導入しています。 様々な分野における燃料電池 MEAs の広範な採用をサポートする手頃な価格のこの焦点.
スケーラブルな生産方法により、メーカーは燃料電池技術の世界的な需要を増加させることができます.
2024年の燃料電池MEAsのトップメーカーは、クリーンエネルギー技術の進歩に著しい貢献を実証しました。 バラードパワーシステムズ、プラグパワー、トヨタなどの企業は、性能、耐久性、およびMEAsのスケーラビリティを強化し、イノベーションを推進しています。 業界を形づける主要トレンドには、水素搭載車両の需要が高まっています。MEAの効率性、コストダウンに重点を置いています。 燃料電池MEA市場の将来は、MEAの設計を最適化し、アプリケーションを拡大するための継続的な努力で有望です。 これらの課題は、持続可能なエネルギーソリューションをグローバルに育成する重要な役割を果たします.
よくあるご質問
燃料電池の重量、電力、寿命を決定するものは何ですか?
メンブレン電極アセンブリ(MEA)は、燃料電池の重量、電力、寿命を定義する重要な役割を果たしています。 また、所有およびインフラ投資の総コストにも影響します。 コアコンポーネントとして、MEAは効率的なエネルギー変換と耐久性を保証し、燃料電池の性能の重要な要因となります.
MEAsとは、燃料電池に重要なのはなぜですか?
膜電極アセンブリ(MEAs)は、燃料電池の心臓を形成します。 プロトン交換膜、触媒層、電極を単体に統合。 電力を発生させる化学反応を有効にします。 それらの重要性は、高温の下で動作し、メタノール、天然ガス、または液体風や液体の太陽などの再生可能エネルギー燃料から得られる不純物水素で働く能力にあります.
PEM燃料電池におけるMEAの役割は何ですか?
プロトン・エクスチェンジ・メンブレン(PEM)燃料電池では、MEAは化学反応が起こるためのプラットフォームを提供します。 燃料を運用電力に変換します。 燃料電池の性能そして安定性はMEAの質そして構造に大きく依存します。 このアセンブリは出力を管理し、燃料電池システムの信頼性を保障します.
MEAsがクリーンエネルギーソリューションに貢献する方法?
クリーンエネルギー技術の進歩に不可欠です。 効率的な水素利用を可能にすることで、温室効果ガス排出量を削減します。 燃料電池への統合は、水素駆動車、静止電力システム、産業用途の開発をサポートし、持続可能なエネルギーの未来に貢献します.
水素を不純物で働きますか?
はい、特定のMEAs、特に高温変形は、不純物の水素と作動できます。 この機能により、メタノールや天然ガスなどの再生可能エネルギー燃料から水素を改質させることができます。 多様化する産業・エネルギー・システムを通じた機能性を高めます.
なぜMEAの設計で耐久性が重要か?
耐久性は燃料電池の長期性能を保障します。 高品質のMEAsは、極端な条件下での劣化に抵抗し、メンテナンスコストを削減し、燃料電池の寿命を延ばします。 メーカーは、自動車、産業、および固定電力アプリケーションの要求を満たすために耐久性を優先順位付けします.
MEAsは燃料電池システムのコストにどのように影響しますか?
MEAsは燃料電池システムの全体的なコストを著しく影響します。 設計および材料は生産費、操作効率および維持の条件を決定します。 MEA技術のイノベーションは、高性能を維持しながらコストを削減し、燃料電池をよりアクセス可能にします.
MEA技術の進歩は?
膜伝導性、触媒効率、材料の耐久性の改善を含む最近の進歩。 メーカーは、MEA製造をスケールアップするコスト効果の高い生産技術を開発しています。 これらの革新は燃料電池の性能そして有用性を高めます.
水素駆動車にMEAsを使用しましたか?
はい、MeAsは燃料電池電気自動車(FCEV)などの水素駆動車に不可欠です。 水素を電気に変換し、車両のモーターに動力を与えます。 トヨタおよびヒュンダイのような自動車メーカーはFCEVモデルの効率そして信頼性を保障するために高度MEAsに頼ります.
MEAsが持続可能性の目標をサポートする方法?
水素系エネルギーシステムの採用を可能にし、炭素排出量削減に重要な役割を果たしています。 輸送、産業プロセス、発電の用途は、クリーンなエネルギー源への移行にグローバルな取り組みと整合します。 MEA技術の発展により、より持続可能な未来に貢献します.