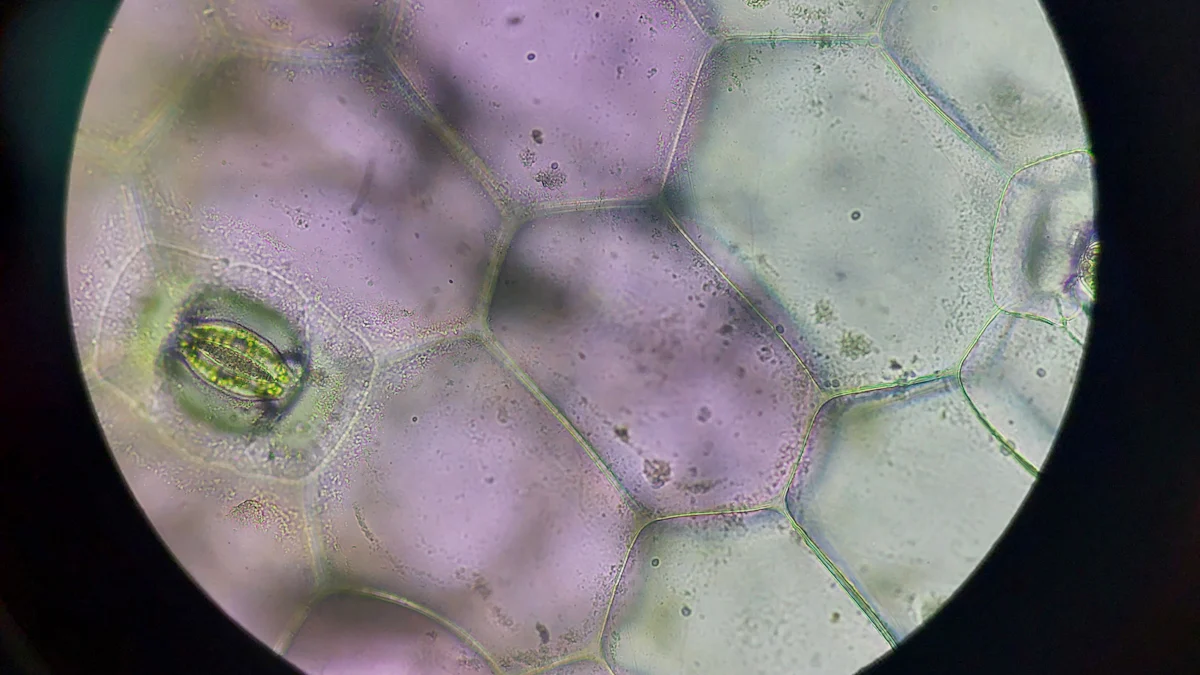
Catalyst coated membranes play a pivotal role in modern energy conversion systems. These membranes, often used in fuel cells and electrolyzers, enable efficient energy transformation by facilitating chemical reactions. Why does efficiency matter so much? It directly impacts energy output, cost savings, and sustainability. For instance, PEM membranes, known for their high performance, are widely adopted in automotive fuel cells. With the global CCM market projected to grow to $2.1 billion by 2025, advancements in these technologies continue to shape the future of clean energy solutions.
要点
- Catalyst coated membranes (CCMs) are essential for efficient energy conversion in fuel cells and electrolyzers, directly impacting energy output and sustainability.
- Proton Exchange Membranes (PEM) offer high efficiency and reliability, making them ideal for automotive fuel cells, but their reliance on expensive precious metals increases costs.
- Anion Exchange Membranes (AEM) provide a cost-effective alternative using non-precious metal catalysts, suitable for renewable energy storage, though they may have lower performance in some applications.
- Hybrid membranes combine the strengths of PEM and AEM technologies, aiming for a balance of efficiency and cost-effectiveness, but face challenges in complex fabrication.
- Advancements in fabrication techniques, such as Layer-by-Layer (LbL) and inkjet printing, are crucial for improving the performance and scalability of CCMs.
- The growing demand for cost-effective and sustainable energy solutions is driving innovation in CCM technology, with a focus on reducing reliance on precious metals.
- Ningbo VET Energy Technology Co. is leading the way in CCM advancements, focusing on innovative fabrication methods and cost reduction to enhance the commercial viability of clean energy technologies.
Overview of Catalyst Coated Membranes
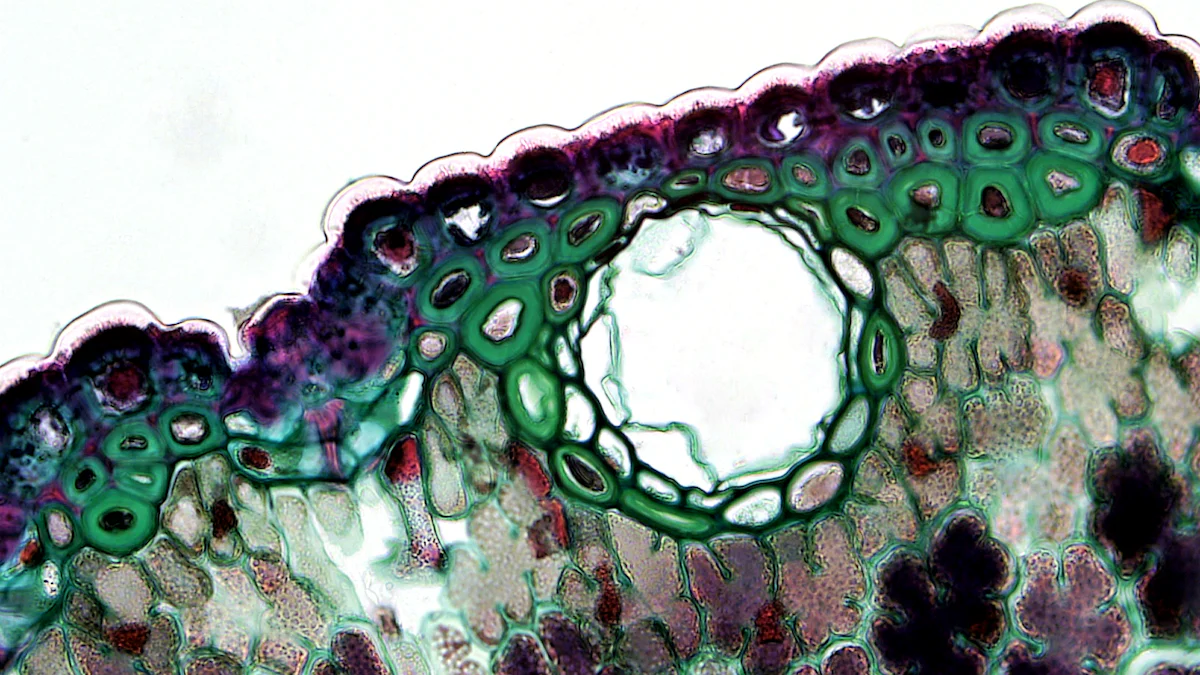
What Are Catalyst Coated Membranes?
Catalyst coated membranes, often referred to as CCMs, are a critical component in energy conversion technologies. These membranes consist of a solid polymer electrolyte with a thin layer of catalyst applied to their surface. The catalyst, typically made from precious metals like platinum or iridium, facilitates chemical reactions essential for energy production.
Where are CCMs used? They play a vital role in applications such as fuel cells, electrolyzers, and hydrogen production systems. For instance, in a PEM electrolyzer, CCMs enable the splitting of water into hydrogen and oxygen with high efficiency. Similarly, in fuel cells, they help convert hydrogen into electricity, making them indispensable for clean energy solutions.
“Catalyst coated membranes are the backbone of modern hydrogen energy systems, driving efficiency and sustainability in energy conversion.”
Types of Catalyst Coated Membranes
CCMs come in various types, each designed for specific applications. Let’s explore the most common ones:
Proton Exchange Membranes (PEM)
PEM membranes are widely recognized for their high performance and reliability. They exhibit excellent energy conversion efficiency and produce high-purity hydrogen. These membranes are commonly used in automotive fuel cells and PEM electrolyzers. However, their reliance on expensive materials like platinum increases their cost.
Anion Exchange Membranes (AEM)
AEM membranes offer a more cost-effective alternative. They use non-precious metal catalysts, which reduces material costs. These membranes are gaining popularity in renewable energy storage systems due to their environmental benefits. However, their performance may not match that of PEM membranes in certain applications.
Hybrid Membranes
Hybrid membranes combine the strengths of PEM and AEM technologies. They aim to balance high efficiency with cost-effectiveness. These membranes are still in the experimental stage but show promise for emerging applications like advanced hydrogen production systems.
Fabrication Techniques
The performance of a catalyst coated membrane heavily depends on its fabrication process. Several techniques are used to create these membranes, each with unique advantages:
Spray Coating and Hot Pressing
Spray coating involves applying a thin layer of catalyst onto the membrane surface, followed by hot pressing to ensure adhesion. This method is widely used due to its simplicity and effectiveness.
Layer-by-Layer (LbL) Techniques
The Layer-by-Layer (LbL) method allows precise control over the thickness and composition of the catalyst layer. This technique enhances the membrane’s performance and scalability, making it suitable for industrial applications.
Advanced Methods Like Inkjet Printing
Inkjet printing represents a cutting-edge approach to CCM fabrication. It enables the precise deposition of catalyst materials, reducing waste and improving efficiency. This method is particularly useful for creating complex designs in hybrid membranes.
Performance Metrics of Catalyst Coated Membranes
Understanding the performance metrics of a catalyst coated membrane is essential for evaluating its efficiency and reliability. These metrics provide insights into how well the membrane performs under various conditions and help identify areas for improvement.
Key Metrics for Efficiency
Energy Conversion Efficiency and Catalyst Utilization
Energy conversion efficiency measures how effectively a catalyst coated membrane transforms input energy into usable output. For instance, in a fuel cell, this metric evaluates how much hydrogen is converted into electricity. High efficiency often depends on optimal catalyst utilization. Precious metals like platinum and iridium, commonly used as catalysts, must be evenly distributed to maximize their activity. Uneven distribution can lead to wasted material and reduced performance.
“Maximizing catalyst utilization not only improves efficiency but also reduces costs by minimizing the use of expensive materials.”
Durability and Operational Lifespan
Durability plays a critical role in determining the operational lifespan of CCMs. Over time, factors like chemical degradation, mechanical stress, and catalyst loss can reduce membrane performance. For example, PEM membranes often face challenges with catalyst degradation due to prolonged exposure to high temperatures and humidity. A durable membrane ensures consistent performance, reducing the need for frequent replacements and lowering long-term costs.
Membrane Resistance and Mass Transport Properties
Membrane resistance refers to the opposition a membrane presents to ion flow. Lower resistance translates to better conductivity and higher efficiency. Mass transport properties, on the other hand, measure how effectively reactants like hydrogen and oxygen move through the membrane. Poor mass transport can create bottlenecks, limiting the overall reaction rate. Advanced fabrication techniques, such as Layer-by-Layer (LbL) methods, have shown promise in reducing resistance and enhancing mass transport, leading to improved performance.
Factors Influencing Performance
Catalyst Composition (e.g., Platinum, Iridium)
The choice of catalyst significantly impacts the performance of a CCM. Platinum, known for its high catalytic activity, is widely used in PEM membranes. Iridium, often employed in electrolyzers, excels in oxygen evolution reactions. However, the high cost of these materials drives research into alternatives like non-precious metal catalysts. Innovations in catalyst composition aim to strike a balance between performance and affordability.
Membrane Thickness and Porosity
Membrane thickness and porosity directly affect efficiency. Thinner membranes reduce resistance, allowing ions to flow more freely. However, excessively thin membranes may compromise durability. Porosity, which refers to the presence of tiny pores in the membrane, influences mass transport. A well-designed porous structure ensures efficient reactant flow while maintaining structural integrity.
Operating Conditions Like Temperature and Pressure
Operating conditions, such as temperature and pressure, play a pivotal role in CCM performance. Higher temperatures often enhance reaction rates but may accelerate membrane degradation. Similarly, increased pressure can improve mass transport but might strain the membrane’s mechanical properties. Optimizing these conditions ensures the membrane operates at peak efficiency without compromising its lifespan.
“Balancing operating conditions is like tuning an instrument—precision is key to achieving harmony between performance and durability.”
Comparison of Different Catalyst Coated Membrane Types
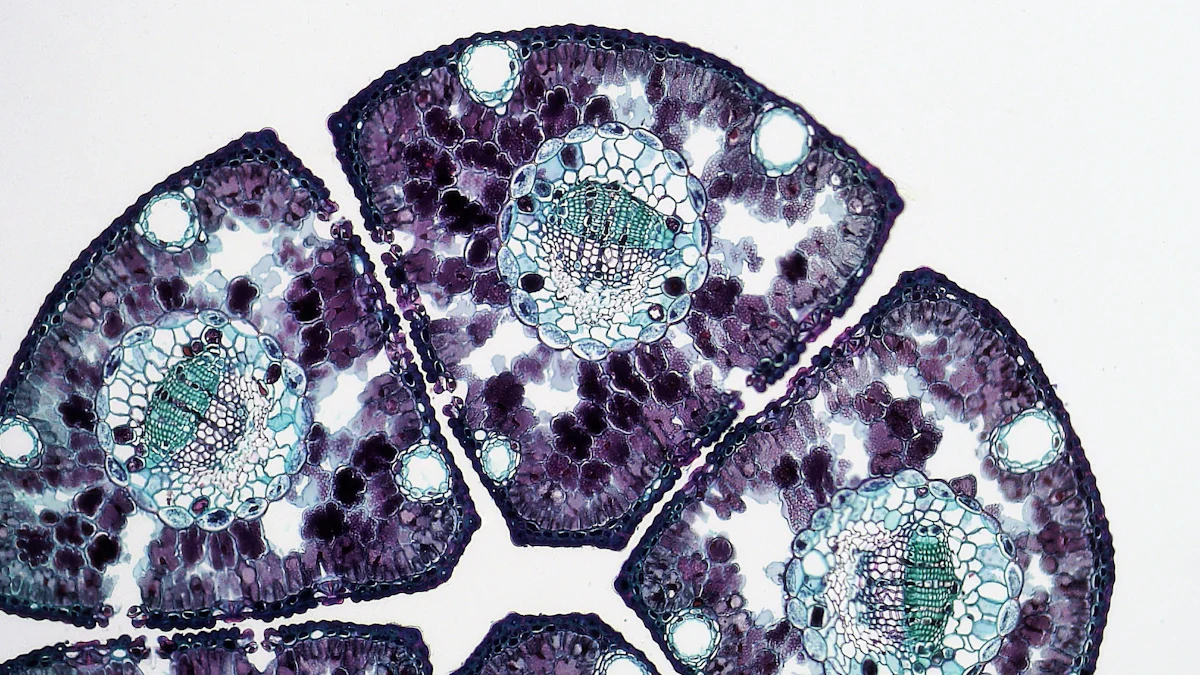
Catalyst coated membranes come in various forms, each with unique strengths and limitations. Choosing the right type depends on the specific application, budget, and performance requirements. Let’s break down the three main types: Proton Exchange Membranes (PEM), Anion Exchange Membranes (AEM), and Hybrid Membranes.
Proton Exchange Membranes (PEM)
Proton Exchange Membranes, or PEMs, are often considered the gold standard in energy conversion systems. Why? Their high efficiency and reliability make them a top choice for demanding applications like automotive fuel cells and PEM electrolyzers.
Advantages: High Efficiency and Proven Reliability
PEMs excel in energy conversion efficiency. They produce more hydrogen per unit of electricity compared to other membrane types. This makes them ideal for applications requiring maximum output, such as hydrogen production and grid-balancing systems. PEMs also adapt quickly to fluctuating power inputs, which is crucial when integrating renewable energy sources like wind or solar. Their proven track record in commercial and industrial settings further solidifies their reputation.
“PEM membranes deliver unmatched efficiency, making them a cornerstone of clean energy technologies.”
Disadvantages: High Cost Due to Precious Metal Catalysts
The primary drawback of PEMs lies in their cost. These membranes rely on precious metal catalysts like platinum and iridium, which significantly increase production expenses. Additionally, the solid polymer electrolyte in PEMs can degrade over time, impacting long-term durability. While advancements aim to reduce material usage, the high initial investment remains a barrier for widespread adoption.
Anion Exchange Membranes (AEM)
Anion Exchange Membranes offer a more budget-friendly alternative to PEMs. They are gaining traction in renewable energy storage and other cost-sensitive applications.
Advantages: Cost-Effectiveness and Environmental Benefits
AEMs use non-precious metal catalysts, which drastically lower material costs. Their simpler cell designs also contribute to reduced manufacturing expenses. Unlike PEMs, AEMs are less sensitive to water impurities, minimizing the need for extensive purification systems. This makes them an environmentally friendly option for regions with limited access to clean water.
“AEM membranes combine affordability with sustainability, paving the way for accessible clean energy solutions.”
Disadvantages: Lower Performance in Some Applications
Despite their advantages, AEMs often fall short in energy conversion efficiency. They produce less hydrogen per unit of electricity compared to PEMs, which can limit their use in high-demand scenarios. Additionally, AEMs may generate hydrogen with lower purity levels, posing challenges for industries requiring ultra-pure hydrogen, such as electronics manufacturing or medical applications.
Hybrid Membranes
Hybrid membranes aim to bridge the gap between PEM and AEM technologies. By combining the best features of both, they offer a promising solution for emerging energy systems.
Advantages: Combining Strengths of PEM and AEM
Hybrid membranes leverage the high efficiency of PEMs and the cost-effectiveness of AEMs. This unique combination allows them to deliver balanced performance at a potentially lower cost. Researchers are exploring their use in advanced hydrogen production systems and next-generation fuel cells, where versatility is key.
Disadvantages: Complex Fabrication and Higher Costs
The complexity of hybrid membrane fabrication presents a significant challenge. Advanced techniques like inkjet printing or Layer-by-Layer (LbL) methods are often required, increasing production costs. While hybrids show great promise, their commercial viability depends on overcoming these manufacturing hurdles.
Each type of catalyst coated membrane offers distinct advantages and trade-offs. PEMs shine in efficiency and reliability but come with a hefty price tag. AEMs provide a cost-effective and sustainable option, though they may not match PEMs in performance. Hybrid membranes hold the potential to revolutionize the field but require further development to become commercially viable. Selecting the right membrane involves weighing these factors against the specific needs of the application.
Use Cases for Each Type
PEM in Automotive Fuel Cells and Hydrogen Production
Proton Exchange Membranes (PEM) have become a cornerstone in automotive fuel cells. Why? Their high efficiency and reliability make them ideal for vehicles requiring consistent energy output. PEM fuel cells power electric vehicles by converting hydrogen into electricity, offering a clean alternative to traditional combustion engines. For instance, companies like Toyota and Hyundai have integrated PEM technology into their hydrogen-powered cars, showcasing its potential in reducing carbon emissions.
In hydrogen production, PEM electrolyzers excel at splitting water into hydrogen and oxygen. Their ability to produce high-purity hydrogen makes them a preferred choice for industries like aerospace and energy storage. PEM electrolyzers also adapt well to fluctuating renewable energy inputs, such as solar or wind power, ensuring efficient hydrogen generation even under variable conditions.
“PEM membranes drive innovation in clean transportation and hydrogen production, paving the way for a sustainable future.”
AEM in Renewable Energy Storage Systems
Anion Exchange Membranes (AEM) are gaining traction in renewable energy storage systems. Their cost-effectiveness and environmental benefits make them a practical choice for large-scale applications. AEM electrolyzers, for example, convert excess renewable energy into hydrogen, which can be stored and used later. This process helps balance energy supply and demand, especially in regions relying heavily on solar or wind power.
AEM technology also offers improved durability compared to PEM in certain scenarios. This durability enhances long-term performance, making AEM electrolyzers a reliable option for energy storage projects. Additionally, their ability to operate with less purified water reduces operational costs and environmental impact, further solidifying their role in sustainable energy solutions.
“AEM membranes provide a cost-effective path to storing renewable energy, ensuring a steady energy supply when the sun isn’t shining or the wind isn’t blowing.”
Hybrid Membranes in Emerging Applications
Hybrid membranes represent the next frontier in energy conversion technologies. By combining the strengths of PEM and AEM, these membranes offer a balanced solution for emerging applications. Researchers are exploring their use in advanced hydrogen production systems, where efficiency and cost-effectiveness are equally critical. Hybrid membranes show promise in applications like grid-scale energy storage and next-generation fuel cells.
One exciting area of development involves hybrid membranes in portable power systems. These systems could revolutionize how we power remote locations or disaster-stricken areas. Although still in the experimental phase, hybrid membranes demonstrate the potential to deliver high performance while reducing reliance on expensive materials.
“Hybrid membranes hold the key to unlocking versatile and innovative energy solutions for the future.”
Cost and Commercial Viability of Catalyst Coated Membranes
Economic Considerations
Cost of Raw Materials Like Platinum and Iridium
The cost of raw materials plays a significant role in determining the commercial viability of catalyst coated membranes. Precious metals like platinum and iridium, often used as catalysts, are among the most expensive components. These materials ensure high performance but come with a hefty price tag. For instance, platinum’s market price fluctuates based on global demand, making cost management a challenge for manufacturers.
Reducing reliance on these materials has become a priority. Researchers are exploring alternatives, such as non-precious metal catalysts, to lower production costs without compromising efficiency. Innovations in material science aim to strike a balance between affordability and performance, paving the way for more accessible clean energy solutions.
Scalability and Manufacturing Challenges
Scaling up production of catalyst coated membranes introduces its own set of challenges. Manufacturing processes, such as spray coating or advanced techniques like inkjet printing, require precision and consistency. Achieving this on a large scale can be costly and time-consuming. Additionally, maintaining quality while increasing output often demands significant investment in equipment and skilled labor.
However, optimizing operations can lead to substantial cost reductions. Studies show that organizations can achieve a 15–20% decrease in costs by streamlining manufacturing processes. Automation, for example, reduces human labor and operational expenses, making large-scale production more feasible. Companies that invest in scalable and efficient fabrication techniques stand to gain a competitive edge in the growing CCM market.
Market Trends
Growing Demand for Cost-Effective CCMs
The demand for cost-effective catalyst coated membranes continues to rise as industries seek sustainable energy solutions. Applications in fuel cells, electrolyzers, and hydrogen production drive this growth. Governments worldwide are setting ambitious renewable energy targets, further fueling the need for affordable CCMs.
For instance, the global push toward hydrogen-powered vehicles has increased interest in PEM membranes. At the same time, AEM membranes are gaining traction in renewable energy storage systems due to their lower costs. This growing demand creates opportunities for manufacturers to innovate and meet market needs.
Role of Government Policies and Subsidies
Government policies and subsidies play a crucial role in shaping the CCM market. Many countries offer financial incentives to promote clean energy technologies, including tax credits and grants for research and development. These measures help offset the high initial costs of CCM production, making them more accessible to businesses and consumers.
For example, subsidies for hydrogen infrastructure development encourage the adoption of fuel cells and electrolyzers. Policies that support renewable energy projects also boost demand for CCMs, creating a favorable environment for manufacturers. By aligning with these initiatives, companies can capitalize on market opportunities and drive growth.
Role of Ningbo VET Energy Technology Co.
Innovations in CCM Fabrication Techniques
Ningbo VET Energy Technology Co. stands at the forefront of innovation in CCM fabrication. The company leverages advanced techniques, such as Layer-by-Layer (LbL) methods and inkjet printing, to enhance membrane performance and scalability. These methods allow precise control over catalyst distribution, improving efficiency and reducing material waste.
By adopting cutting-edge technologies, Ningbo VET Energy Technology Co. addresses key challenges in CCM production. Their commitment to innovation ensures that their products meet the evolving needs of the market while maintaining high standards of quality and reliability.
Contributions to Reducing Costs and Improving Performance
Cost reduction remains a top priority for Ningbo VET Energy Technology Co. The company focuses on optimizing operations to lower production expenses. For instance, automating repetitive processes minimizes human labor and operational costs, increasing overall efficiency. These efforts enable the company to offer high-quality CCMs at competitive prices.
In addition to cost savings, Ningbo VET Energy Technology Co. prioritizes performance improvements. Their research into alternative catalysts and advanced membrane designs demonstrates a commitment to sustainability and innovation. By balancing cost and performance, the company contributes to the widespread adoption of clean energy technologies.
Future Trends in Catalyst Coated Membranes
The future of catalyst coated membranes looks promising, with advancements in materials, fabrication techniques, and industry applications driving innovation. Let’s dive into what lies ahead for this transformative technology.
Innovations in Materials and Fabrication
Development of Nanomaterials and Novel Catalysts
What if membranes could achieve higher efficiency with less material? Researchers are exploring nanomaterials to make this a reality. Nanotechnology allows the creation of catalysts with larger surface areas, enhancing reaction rates while reducing the amount of precious metals like platinum. For example, nanoparticles of platinum or iridium can deliver the same performance as traditional catalysts but with significantly lower material usage. This not only cuts costs but also makes the technology more sustainable.
Novel catalysts are also gaining attention. Scientists are investigating non-precious metal alternatives, such as nickel or cobalt-based compounds, to replace expensive materials. These innovations aim to maintain high performance while making catalyst coated membranes more accessible for widespread use.
Advances in Membrane Technology and Durability
Durability remains a key focus for improving membranes. Advanced polymer designs are being developed to withstand harsh operating conditions, such as high temperatures and humidity. For instance, reinforced membranes with cross-linked structures show better resistance to chemical degradation, ensuring longer lifespans.
Fabrication methods are evolving too. Techniques like 3D printing and inkjet printing allow precise control over membrane structure and catalyst distribution. These methods reduce waste and improve consistency, paving the way for scalable production. The University of Delaware’s Center for Composite Materials has been recognized for its contributions to material synthesis, showcasing how interdisciplinary research can drive technological breakthroughs.
Research Directions
Reducing Environmental Impact of CCM Production
Sustainability is becoming a priority in CCM production. Traditional manufacturing processes often rely on energy-intensive methods and rare materials, which can harm the environment. To address this, researchers are focusing on eco-friendly alternatives. For example, water-based solvents are replacing toxic chemicals in fabrication processes, reducing environmental risks.
Efforts to recycle and reuse materials are also gaining traction. Recovering precious metals from used membranes can lower production costs and minimize waste. These initiatives align with global goals for reducing carbon footprints and promoting green technologies.
Enhancing Efficiency and Scalability
Efficiency improvements remain at the forefront of research. Scientists are optimizing catalyst utilization to ensure every particle contributes to the reaction. Layer-by-layer (LbL) techniques, for instance, allow precise layering of catalysts, maximizing their activity and minimizing waste.
Scalability is another challenge being tackled. Automated production lines and modular designs are making it easier to produce membranes on a large scale without compromising quality. These advancements are crucial for meeting the growing demand for CCMs in industries like transportation and renewable energy.
Industry Outlook
Growth in Renewable Energy Applications
The renewable energy sector is driving the adoption of catalyst coated membranes. Applications in hydrogen production, fuel cells, and energy storage are expanding rapidly. Governments worldwide are investing in hydrogen infrastructure, creating opportunities for CCM manufacturers. For instance, the European Union’s Green Deal aims to install at least 40 gigawatts of electrolyzer capacity by 2030, highlighting the increasing reliance on CCM technology.
Fuel cell vehicles are another area of growth. Companies like Toyota and Hyundai are incorporating CCMs into their hydrogen-powered cars, offering a cleaner alternative to traditional engines. This shift toward sustainable transportation underscores the importance of advancing CCM technology.
Contributions of Ningbo VET Energy Technology Co. to Industry Advancements
Ningbo VET Energy Technology Co. is playing a pivotal role in shaping the future of CCMs. The company’s focus on innovation has led to breakthroughs in fabrication techniques, such as inkjet printing and LbL methods. These advancements enhance membrane performance while reducing production costs, making CCMs more competitive in the market.
By prioritizing sustainability, Ningbo VET Energy Technology Co. is also addressing environmental concerns. Their efforts to develop eco-friendly materials and processes demonstrate a commitment to responsible manufacturing. As a leader in the field, the company continues to drive progress, ensuring that catalyst coated membranes remain at the forefront of clean energy solutions.
“The future of CCMs lies in balancing innovation, efficiency, and sustainability—a vision that Ningbo VET Energy Technology Co. is bringing to life.”
Catalyst coated membranes (CCMs) offer diverse options, each tailored to specific needs. PEMs excel in efficiency and reliability, AEMs provide cost-effective solutions, and hybrid membranes combine the strengths of both. Selecting the right type requires balancing performance, cost, and sustainability. Ningbo VET Energy Technology Co. leads innovation by enhancing CCM fabrication techniques and reducing costs. When choosing CCMs, consider application-specific requirements and emerging trends. For example, industries focused on renewable energy storage might prioritize AEMs, while automotive applications often benefit from PEMs. Staying informed ensures optimal decisions for long-term success.
よくあるご質問
What are catalyst-coated membranes (CCMs)?
Catalyst-coated membranes, or CCMs, are advanced materials used in energy conversion systems like fuel cells and electrolyzers. They consist of a solid polymer electrolyte with a thin layer of catalyst applied to their surface. This catalyst, often made from precious metals such as platinum or iridium, facilitates chemical reactions that produce energy or hydrogen. CCMs play a vital role in clean energy technologies by improving efficiency and sustainability.
How do CCMs contribute to clean energy?
CCMs enable efficient energy conversion by facilitating chemical reactions in systems like fuel cells and electrolyzers. For example, in a fuel cell, CCMs help convert hydrogen into electricity with minimal emissions. In electrolyzers, they split water into hydrogen and oxygen, producing green hydrogen for various applications. Their ability to enhance energy output while reducing environmental impact makes them essential for advancing renewable energy solutions.
What are the main types of CCMs?
CCMs are typically categorized into three types:
- Proton Exchange Membranes (PEM): Known for high efficiency and reliability, often used in automotive fuel cells and hydrogen production.
- Anion Exchange Membranes (AEM): A cost-effective option that uses non-precious metal catalysts, ideal for renewable energy storage systems.
- Hybrid Membranes: Combine the strengths of PEM and AEM, offering a balance of performance and cost-effectiveness for emerging applications.
Each type serves specific needs, making it important to choose based on the intended application.
What factors influence the performance of CCMs?
Several factors affect CCM performance:
- Catalyst Composition: Precious metals like platinum and iridium enhance efficiency but increase costs. Alternatives like non-precious metals are being explored.
- Membrane Thickness and Porosity: Thinner membranes reduce resistance, while optimized porosity improves mass transport.
- Operating Conditions: Temperature and pressure significantly impact reaction rates and durability. Balancing these conditions ensures optimal performance.
Understanding these factors helps in selecting the right CCM for specific applications.
How are CCMs fabricated?
CCMs are created using various fabrication techniques, including:
- Spray Coating and Hot Pressing: A widely used method for applying catalyst layers.
- Layer-by-Layer (LbL) Techniques: Offers precise control over catalyst thickness and composition, enhancing performance.
- Inkjet Printing: A cutting-edge approach that reduces material waste and allows for complex designs.
Each method has unique advantages, influencing the efficiency and scalability of CCM production.
What industries benefit from CCM technology?
CCMs are crucial in industries focused on clean energy and sustainability:
- Automotive: Used in hydrogen-powered vehicles for efficient energy conversion.
- Renewable Energy Storage: AEM membranes store excess energy from solar and wind power as hydrogen.
- Industrial Hydrogen Production: PEM electrolyzers produce high-purity hydrogen for aerospace, electronics, and medical applications.
Their versatility makes CCMs indispensable across multiple sectors.
Are CCMs expensive to produce?
The cost of CCMs depends on factors like raw materials and fabrication methods. Precious metals such as platinum and iridium drive up costs, but innovations in non-precious metal catalysts aim to reduce expenses. Advanced manufacturing techniques, like automation and inkjet printing, also help lower production costs. Companies like Ningbo VET Energy Technology Co. focus on optimizing processes to make CCMs more affordable without compromising quality.
How does Ningbo VET Energy Technology Co. contribute to CCM advancements?
Ningbo VET Energy Technology Co. leads the way in CCM innovation. The company uses advanced fabrication techniques, such as Layer-by-Layer (LbL) methods and inkjet printing, to improve performance and scalability. By prioritizing cost reduction and sustainability, they make high-quality CCMs accessible to a broader market. Their commitment to research and development ensures they stay at the forefront of clean energy technology.
What are the future trends in CCM technology?
The future of CCMs looks promising, with several exciting trends:
- Nanomaterials and Novel Catalysts: Researchers are developing catalysts with larger surface areas to enhance efficiency while reducing material usage.
- Eco-Friendly Manufacturing: Efforts to minimize environmental impact include using water-based solvents and recycling precious metals.
- Scalable Production: Automation and modular designs make large-scale CCM production more feasible, meeting growing demand in renewable energy sectors.
These advancements will shape the next generation of clean energy solutions.
How can I choose the right CCM for my needs?
Selecting the right CCM depends on the application:
- For automotive fuel cells or high-purity hydrogen production: Choose PEM membranes for their efficiency and reliability.
- For renewable energy storage or cost-sensitive projects: AEM membranes offer a budget-friendly and sustainable option.
- For emerging technologies or versatile applications: Hybrid membranes provide a balanced solution.
Consider factors like performance requirements, budget, and long-term goals when making your decision.