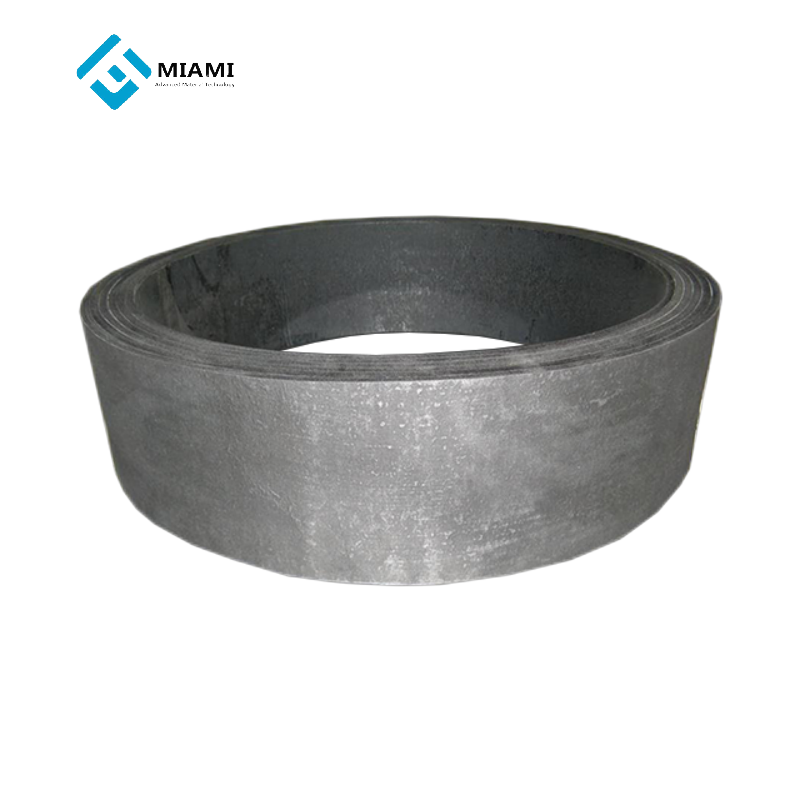
産業プロセスは、極端な条件に耐えることができる材料を要求します。. 絶縁材を、絶縁材および構造サポートのために広く使用されて堅く感じましたり、粗い環境の限界に直面します。 申請する cvd sic コーティングの堅い感じ 耐久性、耐熱性などの特性を強化します。 コーティングされていない材料とどのように比較しますか? 同様に、, cvd sic コーティング ダミー ウエファー アプリケーションは重要な性能の改善を明らかにします.
堅いフェルト材料の理解
堅いフェルト材料の特徴
高性能な用途向けに、硬質フェルト材を設計。 極端な条件下でも、優れた構造的完全性を発揮します。 それらの剛性率は、コンポーネントがその形状を保持することを保証し、精度と信頼性のために重要である。 これらの材料はまた、変動または高温の環境のために適したようにする例外的な熱安定性を提供します。 また、軽量で重量削減が不可欠である産業の使いやすさを高めています.
素材の多孔構造は、その絶縁特性に貢献します。 この機能は熱保護システムにとって重要な熱伝達の最小化で有効にします。 また、厚さや密度が変化するなど、特定の産業要件を満たすため、硬質フェルトをカスタマイズできます.
産業設定の適用
リジッドフェルト材料は、独自の特性により、いくつかの業界で重要な役割を果たしています。 共通の適用は下記のものを含んでいます:
- エアロスペース: 宇宙船および他の高温部品のための熱保護システムで使用される.
- 半導体:高温プロセス中に原子炉を絶縁します.
- 金属冶金学: 溶融金属を処理するための炉ライニングとしてサーブ.
- エネルギー貯蔵:燃料電池および高度電池システムを支えて下さい.
- Vacuum Furnaces: 焼結や焼鈍炉などの耐火炉や誘導加熱炉で利用.
- エレクトロニクス: フィルター、ヒートシンク、電子エンクロージャの断熱材を提供します.
これらのアプリケーションは、現代の産業の要求に対処し、硬質フェルトの汎用性を強調しています.
非コーティングされた堅いフェルトの使用の挑戦
未塗装の硬質フェルトは、厳しい産業環境でいくつかの課題に直面しています。 絶縁材のために有益である間、その多孔質な構造は、それを身に着け、引き裂くことを敏感にします。 反応性ガスや研磨条件への長期暴露は、材料を劣化させ、寿命を延ばすことができます。 また、極端な温度や腐食性の環境に従ったときに、その機械的強度を維持するために、コーティングされていない剛性感が苦しむかもしれません.
長期耐久性を必要とする産業は、しばしば非コーティングされた剛性感の不十分な見つける。 例えば、高温炉では、材料は時間とともに経ち、高められた維持費につながるかもしれません。 cvd の sic のコーティングの堅い感じは摩耗、腐食および熱圧力への抵抗を高めることによってこれらの限界に対処します.
堅いフェルトのCVD SiCのコーティングの役割
CVD SiCコーティングプロセスの概要
化学蒸気蒸着(CVD)プロセスは、シリコンカーバイド(SiC)コーティングを硬質フェルト材料に適用します。 シリコンとカーボンプレカーサを含むガス混合液を反応室に導入する方式です。 高温はこれらのガスを分解し、堅い感じの表面に薄く、均一SiCの層を堆積させます。 プロセスは一貫した性能を達成するために必要であるコーティングの厚さおよび均等性上の精密な制御を保障します。 メーカーは、多くの場合、この技術を使用して、その構造的完全性を損なうことなく、材料の特性を強化します.
堅いフェルトのためのCVD SiCのコーティングの利点
インフォメーション SiCコーティングは、硬質フェルト材料の性能を大幅に向上させます。 高温環境下でも安定性・機能性を極端に保ち、高温環境下でのコーティングが可能です。 それらの耐薬品性は、それらの関与反応ガスや過酷な化学物質などの腐食性条件に最適です。 SiCのコーティングの優秀な硬度は材料の寿命を拡張する摩耗を減らし、機械的に要求する適用に耐えることを可能にします。 例えば、cvdのsicのコーティングの堅い感じは真空の炉で非常によく、uncoated材料が時間の上の劣化するかもしれないです。 これらの増強物は産業使用のためにより信頼できる、費用効果が大きい上塗を施してある材料を作ります.
CVD SiCコーティングの制限と検討
その利点にもかかわらず、CVD SiCコーティングプロセスには制限があります。 蒸着に必要な高温は、そのような条件に耐えることができる材料への適用を制限することができます。 また、すべての予算やプロジェクトのタイムラインに適さないことができる、時間集中的で費用がかかるプロセスをすることができます。 産業はまた加えられたコーティングが材料の重量か次元を変えるかもしれないので、適用の特定の条件を考慮する必要があります。 cvd sic コーティングの堅い感じは多数の利点を提供しますが、これらの要因の慎重な評価は各使用例のための最適の結果を保障します.
比較の性能:CVD SiCのコーティングの堅いフェルト対Uncoated
機械的特性および強さ
CVD SiCコーティングの添加は、硬質フェルト材料の機械的特性を大幅に向上させます。 このコーティングは、約31.0 GPaの硬度と、約275 GPaのヤング率を展示しています。 この改善は材料の剛性率および耐久性を高め、要求する適用のために適したようにします。 36.4 ± 1.6で測定されるコーティングの付着力強さ Nは基質に強い結合を保障します。 対照的に、光沢が無い剛性は、このレベルの構造的整合性を欠いており、多くの場合、機械的ストレスの下で変形または故障につながる。 航空宇宙や冶金などの高耐久性を必要とする産業は、cvd sic コーティングの硬質フェルトによって提供される強化された強さから大幅に利益をもたらします.
Thermal Resistance and Stability
インフォメーション SiCのコーティングは極度な温度で確実に実行するために堅い感じを可能にする例外的な熱抵抗を提供します。 コーティングは障壁として機能し、熱伝達を減らし、熱分解からの基質を保護する。 真空炉や高温炉などの用途に最適です。 熱的に安定して、コーティングされたカウンターパートの高められた性能に一致しないで、光沢が無い堅い感じ。 高温への延長された露出は頻繁に物質的な故障に、効率を減らし、維持の必要性を高めます.
耐久性および耐久性
Cvd sic コーティングの堅い感じの耐久性は光沢が無い材料のそれを越えます。 SiC層は摩耗、化学腐食および反応ガスの露出から保護します。 過酷な産業環境でも、長寿命を確保します。 一方、非コーティングされた堅い感じは摩耗し、引き裂くために、特に研摩か腐食性の条件で脆弱に残ります。 たとえば、半導体製造では、コーティングされた硬質フェルトは、熱サイクルを繰り返す際の完全性を維持し、未塗装材料はすぐに劣化する可能性があります.
コスト効果と長期的な価値
CVD SiCコーティングを適用する初期費用は高そうなかもしれませんが、長期的な利点は費用を上回ります。 コーティングされた堅い感じはより少ない頻繁な取り替えおよび維持を、時間上の操作費を減らす要求します。 その耐久性と性能の向上により、重要な産業プロセスのダウンタイムを最小限に抑えます。 より短い寿命および高められた維持の要求によるより低い上面、頻繁により高いコストを通る間、光沢が無い堅い感じ。 効率および信頼性を優先する企業のために、cvdのsicのコーティングの堅い感じはより費用効果が大きい解決を提供します.
産業のための実用的な影響
Applications in High-Temperature Environments
CVD SiC-coatedの堅い感じは高温環境で例外的な性能を発揮します。 その熱安定性は1,000°を越える条件の機能性を維持できます ツイート これは、劣化なしで極端な熱に耐える材料を必要とする業界のための信頼性の高い選択肢になります。 コーティングの優秀な硬度は摩耗に抵抗し、研摩の条件に露出した部品の寿命を拡張します。 また、耐薬品性は腐食性物質から保護し、耐摩耗性を確保します.
材料はまた優秀な構造の完全性を提供します、それを作る適用の要求する精密および信頼性のために適しています。 たとえば、極端な条件下で形を保持する炭素(C/C)複合体を作るための安定した基盤として機能します。 航空宇宙やエネルギーなどの産業は、重要なシステムのパフォーマンスを向上させるために、これらの特性に依存しています.
反応ガス設定の耐食性
インフォメーション SiCコーティングは反応ガスの環境の腐食に対して顕著な保護を提供します。 コーティングの密で均一な構造は、酸やアルカリを含む腐食剤からの損傷を防ぎます。 これは、根本的な剛性感が、化学的に積極的な条件であっても、そのまま残っていることを保証します。 炭化ケイ素の熱安定性および機械強さはより粗い環境に耐える能力を高めます.
コーティングの立方体、3Cの微細構造は化学攻撃および温度変動に抵抗する重要な役割を担います。 半導体や化学加工などの業界に理想的なソリューションで、材料は反応ガスへの一定の曝露に直面しています.
CVDから得られる産業 SiCコーティングの堅いフェルト
業界トップ | CVD SiCコーティングの利点 |
---|---|
エアロスペース | 過酷な環境でのパフォーマンスと信頼性を高めます. |
半導体 | 電子機器の化学的安定性と耐久性を提供します. |
自動車産業 | 極端な条件下でコンポーネントの寿命を増加させます. |
エネルギー | 発電所および化学処理の装置を保護して下さい. |
これらの業界は、CVD SiC コーティングされた剛性感のユニークな特性を活用して、効率性を高め、メンテナンスコストを削減し、長期的な信頼性を保証します。 汎用性は、幅広い用途で価値ある素材です.
耐久性、熱抵抗、コスト効率性に優れたCVD SiCコーティングされた硬質フェルトは、耐摩耗性に優れています。 極端な条件に耐える能力は、航空宇宙や半導体などの業界に不可欠です。 これらのコーティングは信頼性を高め、維持費を削減します。 寧波VETエネルギー技術 Co.は良質の堅い感じおよび高度CVD SiCのコーティングを提供しま、要求する産業適用のための優秀な性能を保障します.