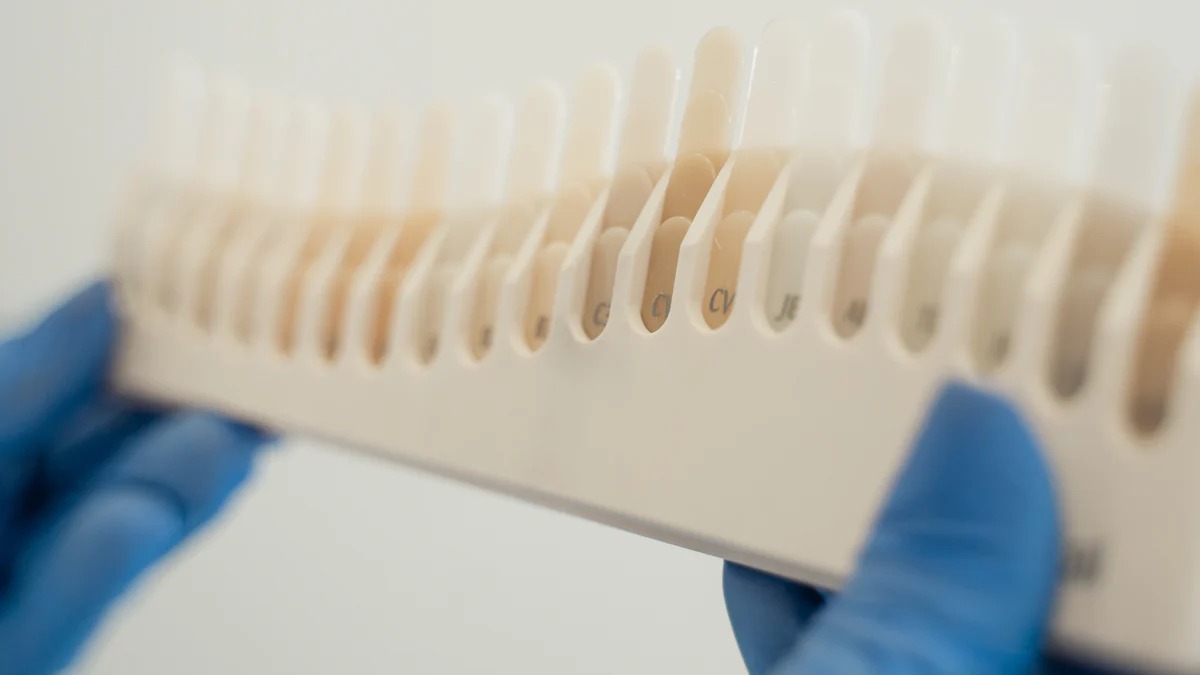
パンケーキの受容器は化学蒸気の沈殿物(CVD)システムで重要な役割を担います。 平らで円形の設計は広い区域を渡る均一暖房を保障しま、それらを精密な温度制御を要求するプロセスのために必要不可欠なようにします。 効率的な熱伝達を可能にすることで、基板上の高品質の薄膜の蒸着をサポートします。 これらのコンポーネントは、半導体製造において特に重要であり、小型の矛盾でも製品性能に影響を及ぼす可能性がある。 彼らの汎用性と有効性は、それらを現代の熱プロセスでコーナーストーンを作りました, SiC-コーティンググラファイト感受性のための市場を支配します.
要点
- パンケーキスセプターは、半導体製造に不可欠な高品質の薄膜を作成するために重要なCVDシステムで均一な加熱を保証します.
- 平らで円形の設計は温度の勾配を最小にしま、一貫した沈殿物率および改善されたフィルムの質に導きます.
- 炭化ケイ素でコーティングされた高純度のグラファイトから構成され、パンケーキの受容器は極端な条件下で優秀な熱伝導性および耐久性を提供します.
- パンケーキのスセプターをCVDプロセスに統合することで、熱管理が向上し、エネルギー消費を削減し、全体的な製造効率を向上します.
- これらのコンポーネントは、半導体アプリケーションだけでなく、太陽電池製造や高度なコーティングにも不可欠です。さまざまな業界における高品質の材料の需要をサポートします.
- パンケーキの受容器は精密な熱制御および物質的な安定性を保障することによってマイクロエレクトロニクスおよび再生可能エネルギーの革新に著しく貢献します.
CVDシステムの概要
化学蒸気蒸着装置(CVD)システムは材料の製作の礎石として役立つ。 これらのシステムは、化学反応を介して材料を基質に堆積することにより、薄膜の生成を可能にします。 半導体、光学、高度なコーティングなどの業界で広く使用されているCVDシステムがあります。 均一で高品質のフィルムを製造する能力は、現代の製造プロセスに不可欠です.
CVDシステムの目的と機能
原子炉ガスをエネルギー源と相互作用するチャンバーに導入することにより、CVDシステムは動作します。 このエネルギー源は、多くの場合、熱またはプラズマベースの、固体材料を基質に堆積させる化学反応をトリガーします。 プロセスはフィルムの厚さ、構成および均等性上の精密な制御を保障します。 CVDシステムは、マイクロエレクトロニクスや光起電細胞などのアプリケーションにとって重要な、卓越した純度と構造の完全性を備えたフィルムを作成するためにCVDシステムに依存することができます.
これらのシステムの機能は、蒸着を超えて拡張します。 また、プロセス中に汚染や欠陥を最小限に抑えます。 ガスの流れや温度を慎重に管理することにより、CVDシステムは、自動化や断層汚染などの問題を軽減します。 この細心のコントロールは、最終製品が厳格な品質基準を満たしていることを確認します.
CVDシステムにおけるパンケーキサスセプターの役割
パンケーキのスセプターは、CVDシステムの効率性を高めるために重要な役割を果たしています。 これらのコンポーネントは、通常、シリコンカーバイドでコーティングされた高純度のグラファイトから作られ、堆積プロセス中に基質のためのプラットフォームとして機能します。 その設計は均一薄膜の沈着を達成するために必要である基質を渡る熱配分を保障します.
パンケーキCVDの原子炉では、ガスの流れはsusceptorに平行移動します。 この構成は一貫した沈殿物率およびフィルムの質を促進します。 これらのシステム内のRFコイルの幾何学は、感受性の設計を補完し、温度の均等性をさらに改善することが多いことに気づくでしょう。 パンケーキのスセプターは精密な温度制御が沈殿物材料の質に直接影響を与えるウエハのエピタキシーのような適用で包んでいます.
パンケーキの受容器をCVDシステムに統合することにより、メーカーはより良い熱管理とプロセス効率を実現します。 これらのコンポーネントは、システムの性能を高めるだけでなく、高度な技術のための高品質の材料の生産に貢献します.
パンケーキスセプターのデザインと機能性
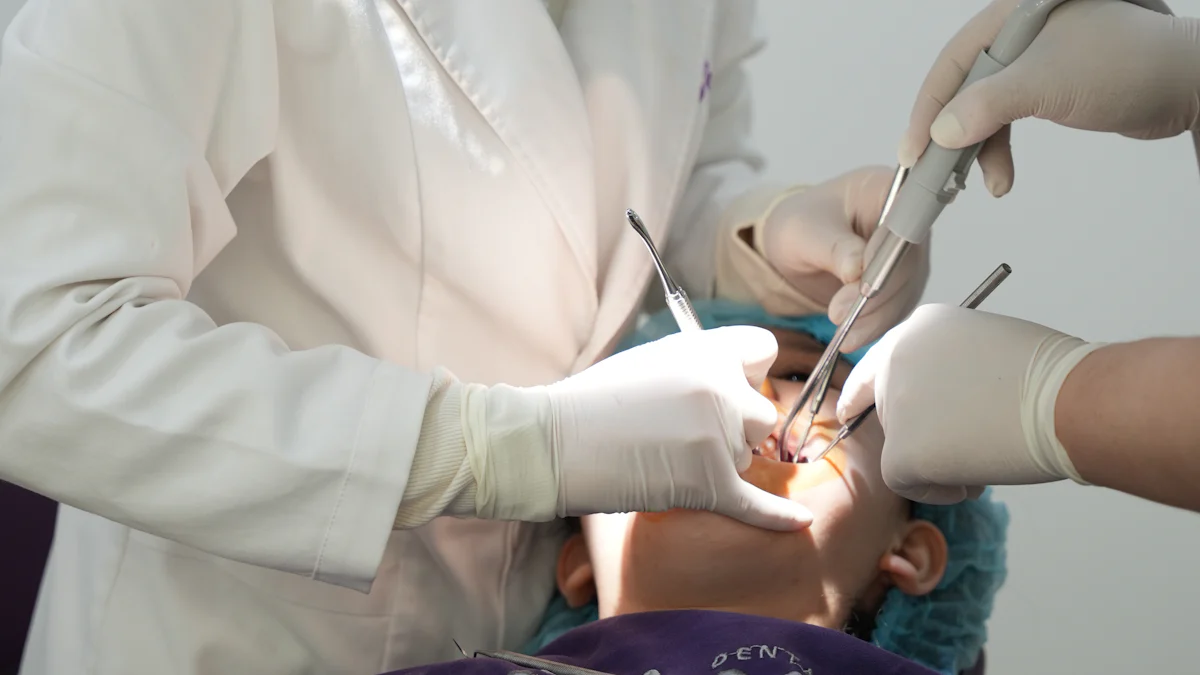
パンケーキサセプターの材料と構造
パンケーキの容器で使用される材料は耐久性および効率を保障するために注意深く選ばれます。 ほとんどのパンケーキの容器は極度な温度の下で優秀な熱伝導性および安定性を提供する高純度のグラファイトからなされます。 性能を高めるために、メーカーは、これらのグラファイト構造をシリコンカーバイド(SiC)でコーティングすることが多い。 このコーティングは、耐薬品反応や摩耗に対する感受性の抵抗を改善し、厳しい環境での長期使用に適しています.
パンケーキの受容器の構造は等しく重要です。 平らに、円の設計は基質を渡る熱配分を保障します。 この幾何学は温度の勾配を、そうでなければ不均等な薄膜の沈殿物に導くことができる最小にします。 これらの感受性器の寸法安定性は、それらが表軸蒸着プロセスで見つけられたような高温条件でも、その形状と機能性を維持することができます.
科学的研究ファインディング: パンケーキのスセプターが120W/m・Kまでの熱伝導性レベルを展示し、作業中に効率的な熱伝達を確保するという点を調査します。 このプロパティは、精密な熱管理を必要とするアプリケーションに不可欠です.
堅牢な材料とよく設計された構造を組み合わせることで、パンケーキのスセプターは、化学蒸気蒸着(CVD)システムで一貫した結果を達成するための信頼性の高いプラットフォームを提供します.
熱伝達および均一熱のメカニズム
パンケーキのスセプターは熱を均一に移す能力を発揮します。 SiCコーティングと組み合わせたグラファイトの高い熱伝導性により、これらのコンポーネントは表面全体に均等に熱を分配することができます。 この均一な加熱は、薄膜蒸着のようなプロセスにとって重要です。温度の一貫性は最終製品の品質を妥協することができます.
パンケーキCVDの原子炉では、ガスの流れはsusceptorの表面に平行移動します。 熱伝達の効率を高め、基質が一貫した熱エネルギーを受け取ることを保障します。 これらのシステム内のRFコイルジオメトリは、スセプターの設計を補完し、温度の均一性をさらに向上します。 スセプターとリアクターのコンポーネント間のこの相乗効果は、堆積率とフィルムの品質をコントロールします.
科学的研究ファインディング:パンケーキの受容器は高温環境の例外的な性能を、次元安定性を維持し、均一熱配分を支えます示します。 これらの特徴は、高度な製造プロセスに理想的です.
パンケーキの受容器の熱伝達のメカニズムはプロセス効率を改善するだけでなく、堆積フィルムの欠陥の可能性を減らすだけでなく。 一貫した熱条件を保ち、半導体製造などの業界に高品質の材料を生産する上で重要な役割を果たしています.
CVDシステムにおけるパンケーキサセプターの用途
半導体製造
パンケーキスセプターは、半導体製造に欠かせないものとなっています。 ウェーハエピタキシのようなプロセスに必要な精度を達成するために、これらのコンポーネントに依存しています。 平らで円形設計は、高品質の半導体ウェーハを作成するために重要な基板全体の均一な加熱を保証します。 マイナーな温度の不整合体でさえ、欠陥につながる可能性があり、パンケーキの受容体の役割は、製品の完全性を維持します.
半導体製造では、パンケーキのスセプターは、一貫した薄膜堆積をサポートする能力のために支配します。 炭化ケイ素のコーティングは熱安定性および化学抵抗を高めます、それらが高温プロセスの要求する条件に抗することを可能にします。 性能を損なうことなく繰り返し使用できる耐久性です。 また、垂直構成との互換性により、より高い基板の取り扱いや、高度な半導体アプリケーションでのユーティリティの拡大にも適しています.
お問い合わせ? パンケーキの受容器はより小さい、より有効な電子装置のための成長した要求に会うために必要です。 精密な熱管理能力は、スマートフォン、コンピュータ、その他最先端技術で使用されるマイクロチップの生産に直接貢献します.
パンケーキのスセプターをCVDシステムに統合することで、進化する半導体業界において競争力を維持するために必要な精度と効率性のレベルを達成することができます.
その他の産業における薄肉堆積
半導体を超えて、パンケーキの受容体は薄膜蒸着に依存する他の業界で重要な役割を果たしています。 あなたは、エネルギー変換効率を最大化するために均一なフィルム品質が不可欠である太陽電池製造で広く使用されているそれらを見つけることができます。 一貫した加熱を提供する能力は、ソーラーパネルに堆積した薄膜が再生可能エネルギー用途に必要な厳格な基準を満たしていることを確認します.
光学系や高度なコーティングなどの業界では、パンケーキのスセプターは、高性能材料の生産を可能にします。 彼らの設計は温度の勾配を最小にし、沈殿物のフィルムが均一厚さおよび構成を示すことを保障します。 この精度は、反射防止コーティングや保護層などの用途に特に重要です。また、わずかな変化でも機能に影響を与える可能性があります.
主な洞察: パンケーキの受容体は、再生可能エネルギーや電子機器などの分野で高品質の材料の需要が高まっています。 彼らの汎用性は、さまざまな堆積プロセスに適応し、複数の業界に価値のある資産を作ることを可能にします.
パンケーキの受容器の機能を活用することで、薄膜蒸着プロセスの効率性と品質を向上させることができます。 太陽電池や光学コーティングを製造している場合でも、これらのコンポーネントは業界標準を満たすために必要な信頼性と性能を提供します.
パンケーキのスセプターの利点
Enhanced Process Efficiency
パンケーキの感受性器は化学蒸気の沈殿(CVD)システムの効率をかなり改善します。 設計は高温プロセスの間にエネルギー消費を減らす最適熱伝達を保障します。 一貫した熱条件を維持することで、薄膜蒸着に必要な時間を最小限に抑えます。 この効率性により、製造サイクルを高速化し、全体的な生産性を向上させることができます.
パンケーキスセプターの耐久性は、プロセス効率にも貢献します。 メーカーは、シリコンカーバイド(SiC)でコーティングされた高純度のグラファイトのような高度な材料を使用して、これらのコンポーネントを構築します。 この組み合わせは、極端な条件下であっても、摩耗する優れた熱安定性と抵抗を保証します。 たとえば、最新のCVD SiCパンケーキスセプターは、性能を維持しながら厳しい処理環境に耐えるように設計されています。 この信頼性は、頻繁な交換の必要性を減らし、時間とリソースの両方を節約します.
主な洞察: パンケーキの受容器は精密および質のための企業の厳しい条件を満たすことによって半導体の製造業のための固体基礎を提供します。 極端な温度への適応性は、さまざまなアプリケーション間で一貫した結果を保証します.
パンケーキのスセプターをCVDシステムに統合することにより、高品質の基準を維持しながら、より迅速で信頼性の高い操作を実現します.
薄膜の均一性と品質の向上
均一な加熱は、高品質の薄膜を作成するために不可欠であり、パンケーキの受容器はこの領域で優れています。 平らで円の設計は熱勾配を最小にし、基質を渡る温度の配分を保障します。 この均一性は、堆積フィルムの品質に直接影響を与え、欠陥や不整合性を減らす.
ウエハエスタキシーなどの用途では、精密な温度制御が不可欠です。 パンケーキのスセプターは、薄膜の構造的完全性を損なう可能性があるバリエーションを排除することによって、この必要性に対処します。 これらのコンポーネントの断面設計は、複雑な蒸着プロセスであっても、一貫した熱条件を維持する能力をさらに高めます。 高度な製造で求められる高精度を実現するために欠かせない機能です.
お問い合わせ? パンケーキのスセプターはエピタキシャル成長の間に熱勾配を除去する重要な役割を果たします。 この機能により、基質ウェーハが不均一な加熱によって影響を受けないまま、優れたフィルム品質が得られます.
パンケーキの受容器の使用はまた例外的な純度および構造の完全性が付いている材料の生産を支えます。 一貫した堆積率を維持する能力は最終製品が最高の業界標準を満たしていることを確認します。 半導体製造やその他業界に携わっている場合でも、これらのコンポーネントは、薄膜蒸着における比類のない品質を実現するのに役立ちます.
パンケーキの受容器は化学蒸気の沈殿物システム内の有効で、均一プロセスを保障する重要な役割を担います。 半導体製造や太陽電池製造などの産業に欠かせない高品質の材料の生産を可能にし、一貫した加熱と汚染の低減を実現。 極端な条件下での信頼性を維持する能力は、高度な熱用途に不可欠です。 現代のテクノロジーを探求する中、パンケーキのスセプターは、マイクロエレクトロニクス、再生可能エネルギー、そしてそれを超える技術革新に著しく貢献していることがわかります。 素材の安定性とプロセスの効率性を向上させるためのインパクトは、複数のセクターにわたって進歩を駆動し続けています.
よくあるご質問
パンケーキの受容体とCVDシステムの役割は何ですか?
パンケーキの受容器は広い区域を渡る均一暖房を提供するように設計されている平らな、円の部品です。 薄膜蒸着プロセス中に温度分布をさらに確保することにより、化学蒸気蒸着(CVD)システムにおいて重要な役割を果たしています。 その汎用性と効率性は、精密が不可欠である半導体製造などの業界で不可欠です.
CVD SiCパンケーキサスセプターの主な物理的性質は何ですか?
インフォメーション SiC パンケーキ スセプターは高度の化学蒸気の沈殿の技術を使用して製造されます。 優れた耐久性を発揮し、極端な温度に耐えることができます。 これらの特性は、要求の厳しい環境で高性能なアプリケーションに信頼性を発揮します.
CVDパンケーキスセプターの熱伝導性は何ですか?
CVDパンケーキのスセプターの熱伝導率はまで達します 120 W/m・K効率的な熱伝達を有効にします。 この高い熱伝導性は均一薄膜の沈着を達成するために重要な一貫した暖房を保障します.
SiCパンケーキサセプターの典型的な熱膨張係数は何ですか?
シスコ パンケーキのスセプターはおよその典型的な熱拡張係数を備えています 4.0×10^-6 /°C. . 高温プロセスにおける寸法安定性を確保し、ウェーハの厚さと品質の一貫性を維持します.
SiCコーティングされたグラファイトバレルの感受性の重要性は何ですか?
バレルのスセプター、パンケーキのスセプターとは違って、円筒形の設計を特色にします。 複数のウェーハや基質を同時にサポートし、同時に加熱し、スループットと効率性を高めます。 SiCコーティングは、熱安定性と耐薬品性を向上させ、大量生産に最適です.
パンケーキCVD反応器内の温度フィールドの理論的研究はどこにありますか?
パンケーキCVD原子炉内の温度フィールドの詳細な理論的研究を探索することができます 日本化学工学会 1992年1月6日(水)、692-697) この研究では、パンケーキCVDシステムの熱的動態に貴重な洞察を提供します.
パンケーキ型スセプターのデザインとは?
パンケーキタイプのスセプターは、クロスセクチュアルでトッププランのビューで、フラットで円形のデザインが特徴です。 この幾何学は基質を渡る熱配分を保障し、温度の勾配を最小にし、薄膜の沈殿物の質を改善します.
パンケーキの受容器の適用は何ですか?
パンケーキの容器は半導体の製造、太陽電池の生産および高度のコーティングで広く利用されています。 均一な加熱を提供する能力は、ウェーハエピタキシや薄膜蒸着などの精密な熱管理を必要とするプロセスに不可欠です.
SiC-coatedグラファイトスセプターの市場はどのように区分されますか?
SiC-coatedのグラファイトの感受性のための市場は2つの主要なタイプに分けられます: パンケーキ スセプター そして バレルのスセプター. . バレルスセプターは、複数の基質を同時に処理する能力のために重要な市場シェアを保持し、高スループットのアプリケーションに適しています.
アメリカ市場でパンケーキの受容体の重要性は何ですか?
アメリカでは、パンケーキスセプターは、半導体製造や再生可能エネルギーなどの業界において重要な役割を果たしています。 精密な熱管理能力は、先進材料の生産をサポートし、これらの分野における技術の進歩に貢献します.