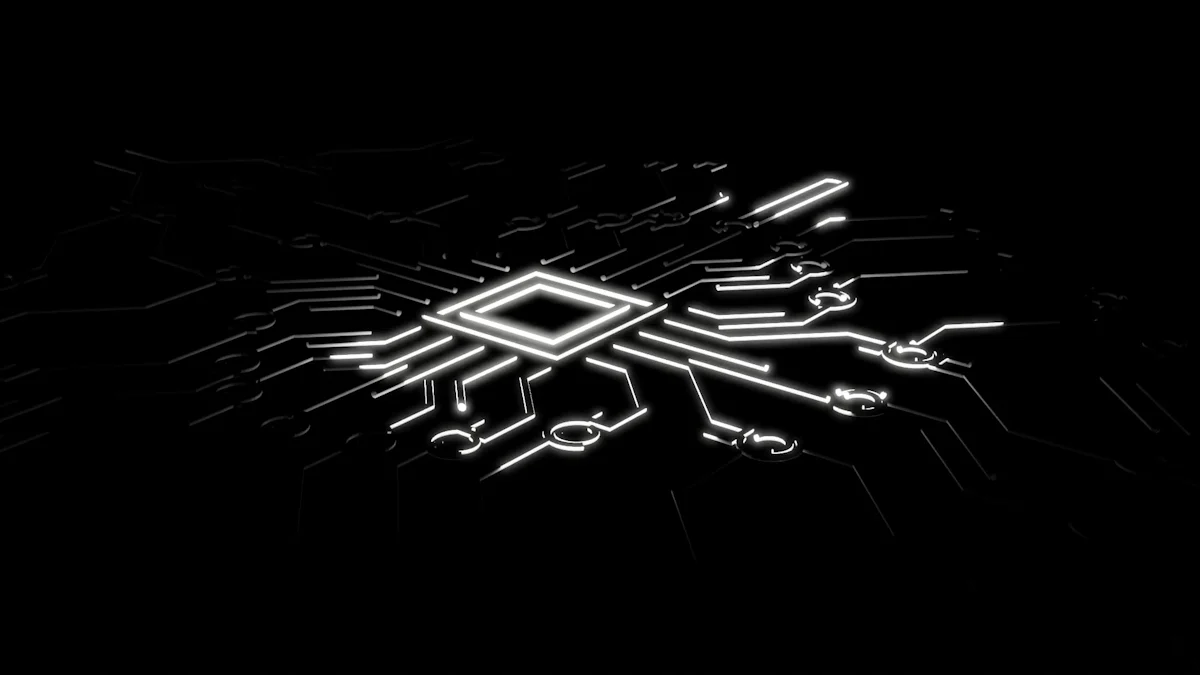
Wafer Cassette serve as essential tools in semiconductor manufacturing, ensuring wafers remain free from contamination and physical damage. These cassettes securely hold wafers during critical processes like etching, cleaning, and testing. By facilitating batch processing, they enhance efficiency and maintain precise wafer alignment. Advanced materials, such as PFA and stainless steel, allow wafer cassettes to withstand harsh chemical environments and high temperatures. Their role extends across multiple stages of production, from initial slicing to final packaging, making them indispensable for achieving precision and operational success in semiconductor fabrication.
要点
- Wafer Cassette are crucial for protecting semiconductor wafers from contamination and damage during manufacturing processes.
- Choosing the right material—such as stainless steel for high temperatures or PFA for chemical resistance—can significantly enhance operational efficiency.
- High-quality wafer cassettes reduce the need for frequent replacements, ultimately saving costs and improving production reliability.
- Understanding specific process requirements is essential for selecting the appropriate wafer cassette, ensuring compatibility and performance.
- Consulting with suppliers and industry experts can provide valuable insights into the best cassette options for unique manufacturing needs.
- Investing in advanced wafer cassettes can lead to long-term benefits, including improved yield and consistent product quality.
Key Features of High-Quality Wafer Cassettes
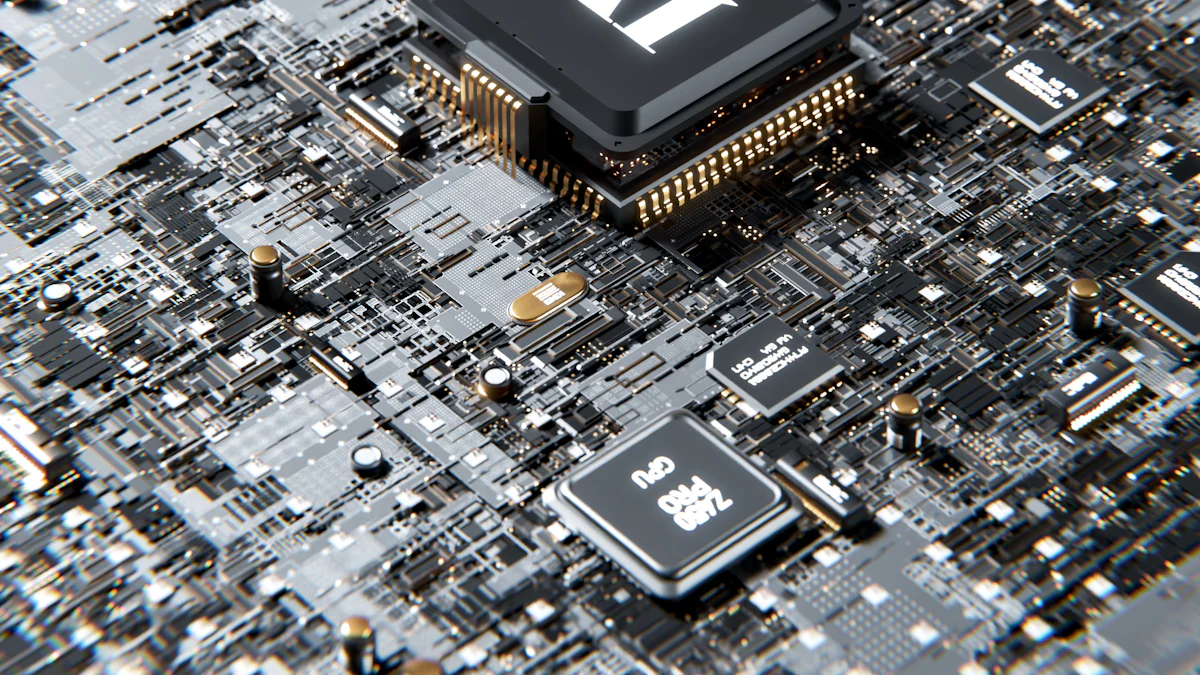
Durability and Longevity
High-quality wafer cassettes excel in durability, ensuring they withstand the demanding conditions of semiconductor manufacturing. Materials like stainless steel and aluminum provide exceptional resistance to wear, corrosion, and high temperatures. For instance, **** offer models such as WHS-M3, which endure temperatures up to 550°C, making them ideal for high-temperature processes. This durability reduces the need for frequent replacements, saving costs and maintaining operational efficiency. Advanced manufacturing techniques further enhance the structural integrity of these cassettes, ensuring long-term reliability in rigorous environments.
Precision in Wafer Handling
Precision plays a critical role in wafer handling, as even minor misalignments can disrupt semiconductor fabrication. Wafer cassettes are designed to securely hold wafers in place, maintaining their alignment during processes like wet chemical cleaning and physical vapor deposition (PVD). Products like Semiconductor Wafer Cassettes accommodate larger wafer sizes, up to 300mm in diameter, ensuring stability and accuracy throughout the production cycle. Their compatibility with automated systems, such as wafer handling robots, streamlines operations and minimizes human error. This precision safeguards delicate wafers from physical damage, enhancing overall yield.
Contamination Control and Cleanroom Compatibility
Contamination control is paramount in semiconductor manufacturing, where even microscopic particles can compromise product quality. Wafer cassettes, constructed from materials resistant to chemicals and contaminants, create a stable and protective environment for wafers. For example, Wafer Cassettes integrate seamlessly into cleanroom environments, supporting processes like thermal oxidation and etching. Their cleanroom compatibility ensures wafers remain free from impurities, preserving their integrity during critical stages. Additionally, advanced material properties, such as high resistance to heat and wear, further enhance their performance in maintaining contamination-free conditions.
Material Options for Wafer Cassettes
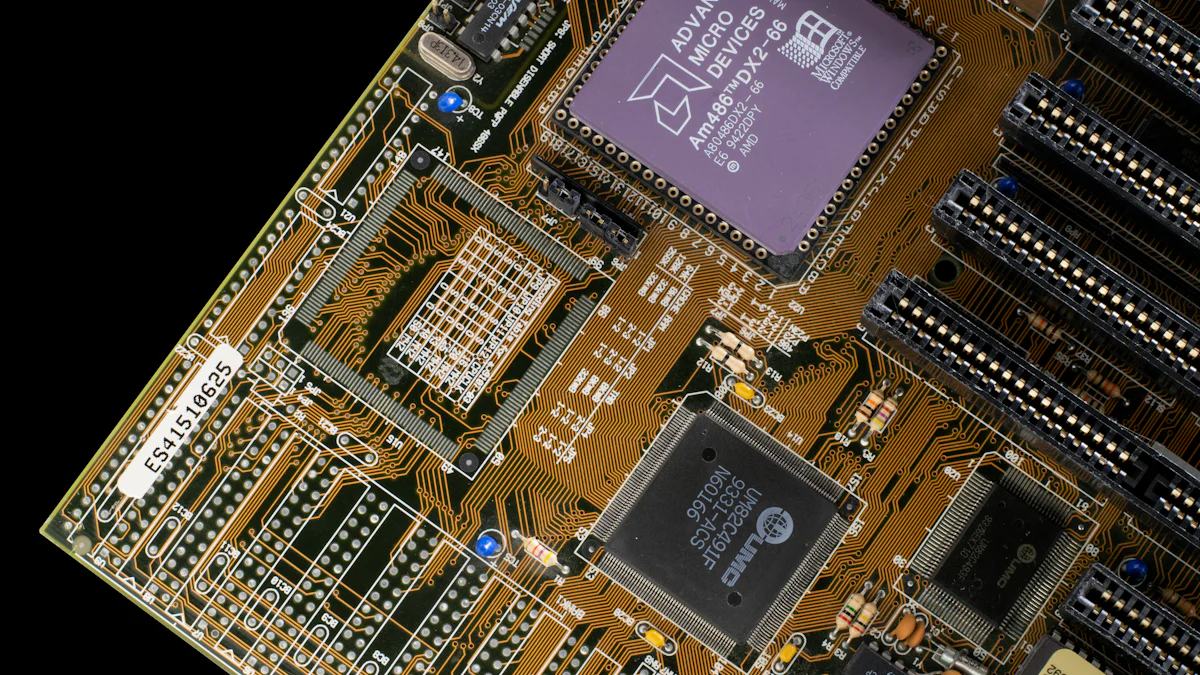
PFA (Perfluoroalkoxy Alkane)
Advantages of PFA
PFA offers exceptional chemical resistance, making it suitable for semiconductor processes involving strong acids and bases. Its high purity ensures minimal contamination, which is critical for maintaining wafer integrity. The material withstands extreme temperatures, enabling its use in high-temperature applications like thermal oxidation. PFA’s elasticity and toughness provide durability, reducing the risk of cracking under stress. Additionally, its translucent nature allows operators to visually inspect wafers without disassembling the cassette, enhancing operational efficiency.
Limitations of PFA
Despite its advantages, PFA has certain limitations. It may not match the rigidity of materials like stainless steel, which can be a drawback in processes requiring robust structural support. The cost of PFA cassettes tends to be higher due to the advanced properties of the material. Furthermore, while it resists many chemicals, it may not perform as well in environments with abrasive particles or mechanical stress.
Polypropylene
Advantages of Polypropylene
Polypropylene stands out for its lightweight nature and cost-effectiveness. It provides adequate chemical resistance for less aggressive environments, making it a practical choice for standard wafer handling processes. The material’s flexibility reduces the likelihood of breakage during routine operations. Its compatibility with various wafer sizes and automated systems enhances its versatility in semiconductor manufacturing.
Limitations of Polypropylene
Polypropylene’s lower resistance to high temperatures limits its application in processes involving extreme heat. It may also degrade when exposed to certain aggressive chemicals over extended periods. The material’s relatively lower strength compared to metals or PFA makes it less suitable for heavy-duty or high-precision tasks.
Stainless Steel
Advantages of Stainless Steel
Stainless steel offers unmatched durability and rigidity, making it ideal for demanding semiconductor processes. It resists wear, corrosion, and mechanical stress, ensuring long-term reliability. The material performs exceptionally well in high-temperature environments, supporting processes like annealing and deposition. Its structural integrity allows it to securely hold wafers, maintaining precise alignment throughout production. Stainless steel cassettes, such as the Palbam Class models, provide a robust solution for manufacturers seeking maximum performance.
Limitations of Stainless Steel
While stainless steel excels in strength and durability, it lacks the chemical resistance of materials like PFA. In environments with strong acids or bases, it may require additional coatings or treatments to prevent corrosion. The weight of stainless steel cassettes can also pose challenges in automated systems, where lighter materials may be preferred.
Compatibility with Semiconductor Processes
Etching Processes
Etching processes in semiconductor manufacturing demand precision and contamination-free environments. Wafer cassettes play a vital role in maintaining wafer alignment during these intricate procedures. Materials like PFA ensure resistance to strong acids used in wet etching, safeguarding wafers from chemical damage. Their high-purity construction minimizes the risk of particle contamination, which is critical in cleanroom settings. Stainless steel cassettes, known for their rigidity, provide stability during plasma etching, where mechanical stress can occur. By securely holding wafers, these cassettes enhance process accuracy and reduce the likelihood of defects.
Deposition Processes
Deposition processes, such as chemical vapor deposition (CVD) and physical vapor deposition (PVD), require wafer cassettes that can withstand extreme temperatures. Stainless steel cassettes excel in these conditions, offering durability and structural integrity. Their ability to maintain precise wafer positioning ensures uniform material deposition, which is essential for creating high-quality semiconductor layers. PFA cassettes also perform well in deposition processes, particularly when handling wafers exposed to reactive gases. Their chemical resistance and flexibility make them suitable for applications requiring both purity and adaptability.
Cleaning and Rinsing Processes
Cleaning and rinsing processes are crucial for removing contaminants from wafers before and after key manufacturing stages. Wafer cassettes designed for these processes must resist aggressive cleaning agents and maintain a stable environment for wafers. PFA cassettes, with their exceptional chemical resistance, are ideal for handling wafers during acid-based cleaning cycles. Polypropylene cassettes, while less resistant to harsh chemicals, offer a cost-effective solution for standard cleaning tasks. Cleanroom-compatible designs ensure that wafers remain free from particles and impurities, preserving their integrity throughout the production cycle.
Top Brands and Models of Wafer Cassettes
Palbam Class Stainless Steel Wafer Cassette
Palbam Class Stainless Steel Wafer Cassettes stand out for their exceptional durability and precision. These cassettes are specifically engineered to replace traditional plastic models, offering superior strength and rigidity. Their stainless steel construction ensures resistance to wear, corrosion, and mechanical stress, making them ideal for high-temperature processes like annealing and deposition.
"Designed for thermal cleanroom applications, these cassettes comply with SEMI standards, ensuring compatibility with advanced semiconductor manufacturing systems."
The robust design of Palbam Class cassettes provides reliable wafer alignment, reducing the risk of damage during handling and processing. Their compatibility with automated systems enhances operational efficiency, making them a preferred choice for manufacturers seeking long-term reliability.
Entegris PFA Wafer Cassette
Entegris PFA Wafer Cassettes deliver unmatched chemical resistance and purity, making them indispensable in semiconductor processes involving strong acids and bases. These cassettes excel in maintaining wafer integrity during critical stages like wet etching, cleaning, and transportation. The high-performance PFA material resists extreme temperatures, ensuring suitability for thermal oxidation and other demanding applications.
"Customizable to accommodate various wafer sizes and configurations, these cassettes play a pivotal role in ensuring contamination-free environments."
Entegris cassettes integrate seamlessly with automated wafer handling systems, streamlining operations and minimizing human error. Their translucent design allows for easy visual inspection of wafers, further enhancing process efficiency.
Shin-Etsu Polypropylene Wafer Cassette
Shin-Etsu Polypropylene Wafer Cassettes offer a cost-effective solution for standard wafer handling tasks. These lightweight cassettes provide adequate chemical resistance for less aggressive environments, making them suitable for routine cleaning and rinsing processes. Their flexibility reduces the likelihood of breakage, ensuring safe and efficient wafer transportation.
"Widely used in mainstream semiconductor manufacturing, these cassettes are designed to hold wafers with diameters up to 200mm."
Shin-Etsu cassettes support compatibility with automated systems, enhancing their versatility in semiconductor production. Their affordability and practicality make them an excellent choice for manufacturers balancing performance and budget considerations.
Tips for Choosing the Right Wafer Cassette
Assessing Process Requirements
Selecting the right wafer cassette begins with understanding the specific needs of the semiconductor manufacturing process. Each stage, such as etching, deposition, or cleaning, demands unique cassette properties. For instance, high-temperature processes require materials like stainless steel, which can endure extreme heat without compromising structural integrity. On the other hand, chemical-intensive processes benefit from PFA cassettes due to their exceptional resistance to acids and bases. Manufacturers must evaluate the wafer size, batch processing requirements, and environmental conditions to ensure the cassette aligns with operational goals. By matching the cassette’s features to the process requirements, manufacturers can enhance efficiency and reduce the risk of wafer damage.
Evaluating Material Compatibility
Material compatibility plays a pivotal role in determining the performance of a wafer cassette. The choice of material impacts durability, contamination control, and resistance to environmental factors. Stainless steel offers unmatched strength and rigidity, making it ideal for mechanical stress and high-temperature applications. PFA provides superior chemical resistance, ensuring wafers remain uncontaminated during exposure to harsh chemicals. Polypropylene, while cost-effective, suits less aggressive environments and standard handling tasks. Manufacturers should consider the chemical agents, temperature ranges, and mechanical demands of their processes when evaluating material options. Proper material selection ensures the wafer cassette performs optimally under specific manufacturing conditions.
Considering Budget and Longevity
Budget constraints often influence the decision-making process when choosing wafer cassettes. However, focusing solely on initial costs can lead to higher expenses in the long run. Durable materials like stainless steel and PFA may require a higher upfront investment but offer extended lifespans and reduced replacement frequency. Polypropylene cassettes, while more affordable, may incur additional costs due to their limited durability in demanding environments. Manufacturers should also consider the total cost of ownership, including maintenance, replacement, and customization expenses. Investing in high-quality wafer cassettes ensures long-term reliability and operational efficiency, ultimately reducing overall costs.
Consulting with Suppliers and Experts
Engaging with suppliers and industry experts provides valuable insights when selecting wafer cassettes for semiconductor manufacturing. Suppliers often possess in-depth knowledge about their products, including material properties, compatibility with specific processes, and customization options. By consulting them, manufacturers can identify cassettes tailored to their unique operational needs.
Experts in the semiconductor field offer guidance on emerging technologies and trends. For instance, advancements in diffusion processes have increased the demand for specialized components like TaC Coated Guide Rings, Planetary Disksそして Preheat Rings. These innovations highlight the importance of staying informed about the latest developments to ensure compatibility with cutting-edge manufacturing techniques.
When consulting suppliers, manufacturers should:
-
Request Detailed Specifications
Suppliers should provide comprehensive information about wafer cassette materials, temperature thresholds, and chemical resistance. This ensures the selected cassette aligns with the demands of processes like etching or deposition.
-
Inquire About Customization Options
Customization enhances the performance of wafer cassettes in specific applications. For example, some suppliers offer tailored designs to accommodate unique wafer sizes or batch processing requirements.
-
Evaluate Total Cost of Ownership
Beyond initial costs, manufacturers should assess long-term expenses, including maintenance and replacement. Suppliers can help calculate the total cost of ownership, ensuring an informed investment decision.
-
Seek Recommendations for Advanced Applications
Experts can recommend solutions for high-precision tasks or harsh environments. For instance, stainless steel cassettes excel in high-temperature processes, while PFA cassettes perform well in chemically aggressive settings.
"Collaborating with experienced suppliers and industry professionals ensures manufacturers select wafer cassettes that enhance efficiency and align with technological advancements."
By leveraging the expertise of suppliers and professionals, manufacturers can make informed decisions that optimize production processes and reduce operational risks.
High-quality wafer cassettes ensure precision and durability in semiconductor manufacturing. They protect wafers from contamination and damage during critical stages like slicing, testing, and packaging. Selecting the right material and model enhances compatibility with specific processes, improving operational efficiency. Manufacturers benefit from investing in advanced options, such as stainless steel or PFA cassettes, which offer long-term reliability. These tools play a pivotal role in achieving seamless semiconductor processing, contributing to consistent production quality and long-term success.
よくあるご質問
What is the primary purpose of wafer cassettes in semiconductor manufacturing?
Wafer cassettes ensure the safe handling, transportation, and storage of delicate semiconductor wafers. They maintain wafer stability, protect against physical damage, and prevent contamination during critical fabrication processes.
Why are PFA wafer cassettes widely used in semiconductor fabs?
PFA wafer cassettes excel in chemical resistance and contamination control. Their high purity ensures wafers remain clean during processes like photolithography and wet etching. These cassettes also withstand extreme temperatures, making them indispensable for achieving high yields in semiconductor manufacturing.
How do stainless steel wafer cassettes benefit high-temperature processes?
Stainless steel wafer cassettes provide unmatched durability and rigidity. They resist wear, corrosion, and mechanical stress, making them ideal for high-temperature applications such as annealing and deposition. Their structural integrity ensures precise wafer alignment throughout these demanding processes.
What factors should manufacturers consider when selecting a wafer cassette?
Manufacturers should evaluate process requirements, material compatibility, and budget constraints. For example, high-temperature processes may require stainless steel cassettes, while chemical-intensive tasks benefit from PFA options. Assessing wafer size, batch processing needs, and environmental conditions ensures optimal performance.
Are polypropylene wafer cassettes suitable for all semiconductor processes?
Polypropylene wafer cassettes work well for standard wafer handling and less aggressive environments. They offer lightweight and cost-effective solutions for routine cleaning and rinsing tasks. However, their lower resistance to high temperatures and harsh chemicals limits their application in demanding processes.
What role do wafer cassettes play in contamination control?
Wafer cassettes create a stable and protective environment for wafers, minimizing exposure to contaminants. Materials like PFA and stainless steel resist chemicals and particles, ensuring wafers remain clean during processes such as thermal oxidation and etching. Cleanroom-compatible designs further enhance contamination control.
How do advanced diffusion cassettes meet next-generation semiconductor demands?
Advanced diffusion cassettes accommodate larger wafer sizes, such as 300 mm, required by modern semiconductor fabs. Their precision engineering supports high-temperature and chemically intensive processes, ensuring compatibility with next-generation fabrication techniques.
What are TaC Coated Guide Rings, Planetary Disks, and Preheat Rings, and how do they relate to wafer cassettes?
These components enhance semiconductor manufacturing by improving process precision and efficiency. TaC Coated Guide Rings resist wear and contamination, while Planetary Disks ensure uniform wafer rotation during deposition. Preheat Rings optimize temperature distribution, complementing the performance of wafer cassettes in advanced processes.
Can wafer cassettes integrate with automated systems?
Yes, many wafer cassettes are designed for seamless integration with automated wafer handling systems. This compatibility reduces human error, enhances operational efficiency, and ensures precise wafer alignment during critical manufacturing stages.
Why is consulting suppliers and experts important when choosing wafer cassettes?
Suppliers and experts provide valuable insights into material properties, customization options, and emerging technologies. They help manufacturers select cassettes tailored to specific processes, ensuring long-term reliability and compatibility with advanced semiconductor systems.