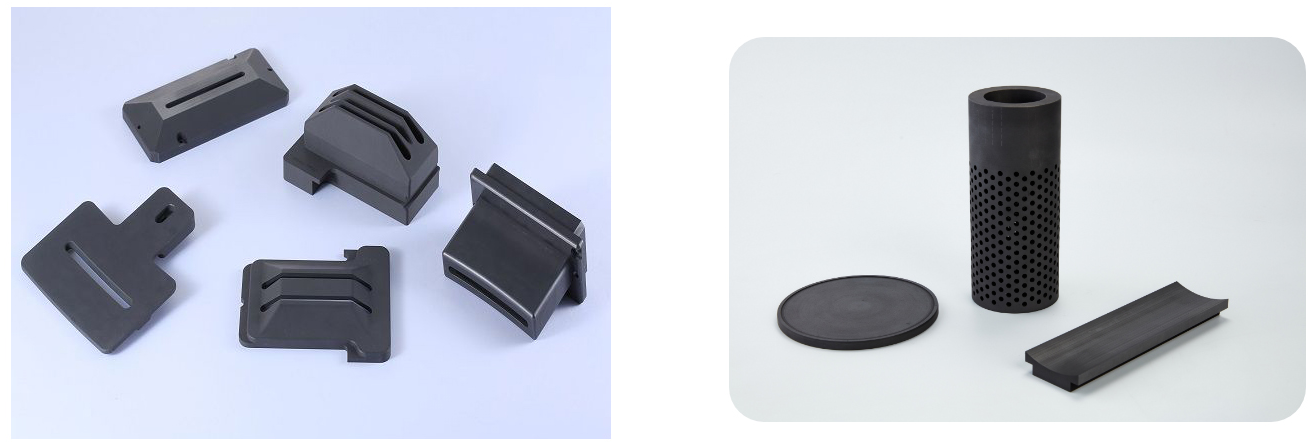
Graphite plays a pivotal role in ion implantation graphite, a critical process in semiconductor manufacturing. Its unique combination of properties makes it an essential material for this advanced technology. With exceptional thermal conductivity, graphite efficiently dissipates heat generated during high-energy ion acceleration. Its resilience at extreme temperatures ensures stability in demanding environments. Additionally, its electrical conductivity supports precise energy control, vital for implanting ions into semiconductor wafers. 多孔質グラファイト, a specialized form, enhances performance by offering superior durability and adaptability. As semiconductor graphite continues to evolve, it remains indispensable in driving innovation and efficiency across the industry.
要点
- Graphite is essential in ion implantation due to its exceptional thermal conductivity, which helps dissipate heat and maintain equipment stability during high-energy processes.
- The chemical stability of graphite prevents contamination during semiconductor manufacturing, ensuring the integrity and performance of devices.
- Graphite’s electrical conductivity allows for precise control of ion beams, which is crucial for achieving accurate implantation depths and uniform dopant distribution.
- Using high-purity graphite components reduces maintenance needs and operational costs, making it a cost-effective choice for semiconductor manufacturers.
- Graphite’s adaptability enables customization for specific applications, enhancing performance across various stages of semiconductor production.
- The ongoing advancements in graphite material science, including the exploration of graphene, promise to further improve the efficiency and capabilities of semiconductor technologies.
- Companies like Ningbo VET Energy Technology Co. are leading innovations in graphite solutions, supporting the evolving demands of the semiconductor industry.
What is Ion Implantation in Semiconductor Manufacturing?
Overview of the Ion Implantation Process
Ion implantation serves as a cornerstone in semiconductor manufacturing. This advanced technique introduces ions into a substrate, typically a silicon wafer, to modify its physical, chemical, or electrical properties. The process begins with the generation of ions in an ion source. These ions are then accelerated through an electric field, gaining high energy before being directed toward the target material. Upon impact, the ions penetrate the surface, embedding themselves into the lattice structure of the substrate.
This method offers unparalleled precision. Manufacturers can control the depth and concentration of the implanted ions by adjusting parameters such as energy levels and ion dosage. Unlike traditional diffusion processes, ion implantation operates at relatively low temperatures, reducing the risk of thermal damage to the wafer. This precision and control make it indispensable for creating the intricate features required in modern semiconductor devices.
Importance of Ion Implantation in Semiconductor Devices
Ion implantation plays a pivotal role in shaping the functionality of semiconductor devices. By altering the elemental composition of the substrate, this process enables the creation of regions with specific electrical properties. For instance, it facilitates the formation of p-type and n-type regions in transistors, which are essential for their operation.
The ability to introduce dopants with high accuracy ensures consistent performance across devices. This consistency is critical in applications like microprocessors and memory chips, where even minor variations can lead to significant performance issues. Additionally, ion implantation supports the development of advanced technologies, such as high-performance power devices and optoelectronic components.
“Ion implantation is a low-temperature process used in semiconductor device fabrication to alter the physical, chemical, or electrical properties of the target.” This capability underscores its importance in the industry, as it allows manufacturers to meet the ever-increasing demands for smaller, faster, and more efficient electronic components.
The Role of Ion Implantation Graphite in Semiconductor Manufacturing
Graphite as a Core Material in Ion Implantation Systems
Graphite serves as a fundamental material in ion implantation systems due to its exceptional physical and chemical properties. Its ability to withstand extreme temperatures and resist chemical degradation makes it ideal for the high-energy environments of ion implanters. In these systems, graphite components, such as beamline parts and electrodes, play a critical role in ensuring operational stability and efficiency.
The unique structure of graphite contributes to its high thermal conductivity, which helps dissipate heat generated during the ion acceleration process. This property prevents overheating and extends the lifespan of the equipment. Additionally, graphite’s electrical conductivity supports the precise control of ion beams, a key requirement for achieving accurate implantation depths and concentrations.
Materials like graphite and refractory metals are often utilized in ion implanter beamlines to enhance the durability of the system. By incorporating graphite into these components, manufacturers can reduce wear and tear, minimizing maintenance needs and downtime. This reliability is crucial in semiconductor manufacturing, where consistent performance directly impacts production quality and throughput.
How Graphite Enhances the Ion Implantation Process
Graphite enhances the ion implantation process by improving both efficiency and precision. Its high purity ensures that no contaminants are introduced during implantation, which is essential for maintaining the integrity of semiconductor wafers. High-purity graphite components, such as susceptors and shields, protect wafers from contamination while withstanding the harsh conditions of the implantation chamber.
The adaptability of graphite allows it to be customized for specific applications within ion implantation systems. For example, porous graphite can be engineered to provide superior durability and adaptability, further optimizing the implantation process. This customization ensures that graphite components meet the exacting standards of semiconductor manufacturing.
Graphite’s role extends beyond its physical properties. Its chemical stability ensures that it remains inert even in reactive environments, preventing unwanted interactions with implanted ions. This stability contributes to the precision of the process, enabling manufacturers to achieve the desired electrical and structural modifications in the substrate.
Key Applications of Ion Implantation Graphite
Graphite Components in Ion Implantation Equipment
Graphite components form the backbone of ion implantation equipment, ensuring precision and durability in semiconductor manufacturing. These components, including beamline parts, electrodes, and shields, are engineered to withstand the extreme conditions of ion implantation systems. Their high thermal stability allows them to endure the intense heat generated during ion acceleration, while their chemical resistance ensures longevity in reactive environments.
Manufacturers rely on graphite for its ability to maintain structural integrity under high stress. For instance, POCO® graphite is widely used in ion implantation applications due to its cost-effectiveness and superior performance compared to refractory metals. Its electrical conductivity also plays a critical role in controlling the energy of accelerated ions, enabling precise implantation depths and uniform dopant distribution. By integrating graphite into these systems, manufacturers achieve enhanced reliability and reduced maintenance requirements, which are essential for maintaining high production throughput.
Graphite’s Role in Wafer Handling and Protection
Graphite’s versatility extends beyond its use in ion implantation equipment to wafer handling and protection. Semiconductor wafers, which are highly sensitive to contamination and mechanical damage, require robust materials to ensure their integrity throughout the manufacturing process. Graphite components, such as susceptors and wafer carriers, provide the necessary support and protection.
The high purity of graphite prevents contamination during wafer processing, a critical factor in maintaining the quality of semiconductor devices. Additionally, its thermal conductivity ensures uniform heat distribution, which is vital during processes like ion implantation and chemical vapor deposition. Graphite’s ability to withstand repeated heating and cooling cycles further enhances its suitability for wafer handling applications. This durability minimizes the risk of wafer damage, ensuring consistent performance and yield in semiconductor production.
Other Semiconductor Manufacturing Applications of Graphite
Graphite’s unique properties make it indispensable in various other semiconductor manufacturing processes. In plasma etching, graphite components are used in etching chambers to selectively remove material from wafers, creating intricate patterns required for advanced semiconductor devices. The demand for graphite in this application continues to grow as device complexity increases and precision becomes more critical.
Graphite also plays a significant role in chemical vapor deposition (CVD) and epitaxy processes. Its resistance to high temperatures and corrosive environments makes it ideal for use as heaters, crucibles, and susceptors in these applications. Furthermore, graphite’s adaptability allows it to be customized for specific manufacturing needs, ensuring optimal performance across different stages of semiconductor production.
“Graphite materials used in the semiconductor industry require high precision, temperature resistance, strength, and durability.” This statement underscores the material’s versatility and importance in supporting the industry’s evolving demands.
By leveraging graphite’s exceptional properties, manufacturers can enhance efficiency, reduce costs, and achieve the high standards required for modern semiconductor devices.
Benefits of Using Ion Implantation Graphite
High Thermal Conductivity and Heat Resistance
Graphite exhibits exceptional thermal conductivity, making it a cornerstone material in ion implantation systems. This property allows it to dissipate the intense heat generated during the acceleration of ions, ensuring that equipment operates within safe temperature ranges. Unlike alternative materials, graphite maintains its structural integrity even under extreme thermal stress. For instance, in high-energy ion implantation chambers, graphite components such as beamline parts and shields prevent overheating, which could otherwise compromise the precision of the implantation process.
The heat resistance of graphite further enhances its suitability for semiconductor manufacturing. It withstands temperatures exceeding 3,000°F without degrading, a critical requirement for processes involving prolonged exposure to high-energy environments. This resilience ensures consistent performance, reducing the likelihood of equipment failure. Manufacturers rely on graphite’s ability to endure these conditions to maintain the efficiency and reliability of their production lines.
“Graphite’s unique structure enables it to handle extreme temperatures while maintaining high thermal conductivity,” a feature that sets it apart from other materials used in semiconductor manufacturing.
Durability and Longevity in High-Stress Environments
Ion implantation systems operate in high-stress environments where materials face constant exposure to mechanical wear, thermal cycling, and chemical interactions. Graphite’s durability makes it an ideal choice for such demanding conditions. Its robust structure resists cracking and deformation, even under repeated thermal and mechanical stress. This durability translates into longer lifespans for components, reducing the frequency of replacements and minimizing downtime.
Graphite also excels in environments where chemical stability is crucial. In ion implantation chambers, reactive gases and ions can corrode less resilient materials. Graphite’s inert nature prevents such degradation, ensuring that components remain functional over extended periods. For example, graphite electrodes and susceptors retain their performance characteristics despite continuous exposure to reactive elements, making them indispensable in maintaining the precision of the implantation process.
The longevity of graphite components offers significant cost advantages. By reducing wear and tear, manufacturers can lower maintenance costs and improve overall operational efficiency. This reliability underscores graphite’s value in high-stress applications within the semiconductor industry.
Cost-Effectiveness and Reusability
Graphite provides a cost-effective solution for semiconductor manufacturing due to its combination of durability, reusability, and performance. While the initial investment in high-purity graphite components may be higher than some alternatives, their extended lifespan and reduced maintenance requirements offset these costs. Over time, manufacturers benefit from lower operational expenses and fewer disruptions to production schedules.
Reusability further enhances the economic appeal of graphite. Components such as wafer carriers and shields can undergo multiple cycles of use without losing their effectiveness. This reusability reduces waste and aligns with the industry’s growing emphasis on sustainable manufacturing practices. Additionally, the adaptability of graphite allows for customization, enabling manufacturers to optimize components for specific applications, further improving cost efficiency.
Compared to alternative materials, graphite offers a superior balance of performance and affordability. Its ability to deliver consistent results while minimizing long-term costs makes it a preferred choice for ion implantation systems and other semiconductor manufacturing processes.
Technical Properties of Graphite for Semiconductor Use
Chemical Stability and Resistance to Corrosion
Graphite demonstrates remarkable chemical stability, making it a preferred material in semiconductor manufacturing. Its inert nature ensures that it does not react with most chemicals, even under extreme conditions. This property becomes crucial in ion implantation systems, where reactive gases and high-energy ions are present. Graphite components maintain their integrity, preventing contamination or degradation during the process.
The resistance of graphite to corrosion further enhances its reliability. In environments involving corrosive substances, such as plasma etching or chemical vapor deposition (CVD), graphite remains unaffected. For example, susceptors and electrodes made from high-purity graphite withstand prolonged exposure to reactive chemicals without losing functionality. This durability ensures consistent performance, reducing the need for frequent replacements and minimizing operational disruptions.
“Graphite materials used in the semiconductor industry must exhibit high precision, temperature resistance, and chemical stability,” as highlighted in industry studies. These attributes make graphite indispensable for maintaining the stringent quality standards required in semiconductor production.
Electrical Conductivity and Its Relevance in Ion Implantation
Graphite’s excellent electrical conductivity plays a pivotal role in ion implantation systems. This property allows it to efficiently conduct electricity, which is essential for controlling the energy of accelerated ions. Components such as electrodes and beamline parts rely on graphite’s conductivity to ensure precise ion beam manipulation. This precision directly impacts the accuracy of implantation depths and dopant distribution in semiconductor wafers.
Unlike alternative materials, graphite combines electrical conductivity with 熱安定性, making it uniquely suited for high-energy environments. For instance, in ion implanters, graphite electrodes maintain consistent performance even under intense electrical and thermal stress. This reliability supports the production of advanced semiconductor devices, where precision and consistency are non-negotiable.
The global demand for high-performance materials like graphite continues to grow. According to market analyses, the semiconductor graphite market, valued at approximately USD 1.5 billion in 2022, reflects the increasing reliance on graphite’s unique properties. Its role in enabling efficient and accurate ion implantation underscores its importance in the industry.
Customizability for Specific Semiconductor Applications
Graphite offers unparalleled customizability, allowing manufacturers to tailor its properties for specific semiconductor applications. This adaptability stems from its unique structure, which can be engineered to meet diverse requirements. For example, porous graphite can be designed to enhance durability and thermal performance in ion implantation systems. Similarly, high-density graphite provides superior strength and wear resistance for components exposed to mechanical stress.
Manufacturers leverage this flexibility to optimize graphite for various processes, including wafer handling, plasma etching, and epitaxy. Custom graphite susceptors, for instance, ensure uniform heat distribution during CVD, improving the quality of deposited films. Wafer carriers made from graphite protect delicate wafers from contamination and damage, ensuring high yields in production.
“The success story of graphite in the semiconductor industry lies in its ability to adapt to evolving technological demands,” as noted in industry research. This adaptability positions graphite as a cornerstone material, capable of meeting the challenges of modern semiconductor manufacturing.
By combining chemical stability, electrical conductivity, and customizability, graphite continues to drive innovation and efficiency in the semiconductor industry. Its technical properties not only meet current demands but also pave the way for advancements in next-generation technologies.
Why Ion Implantation Graphite is Indispensable in Semiconductor Manufacturing
Comparison with Alternative Materials
Graphite stands out as a superior material in semiconductor manufacturing when compared to alternatives like refractory metals and ceramics. Its unique combination of properties makes it indispensable in ion implantation systems. Unlike refractory metals, graphite offers exceptional thermal conductivity, which ensures efficient heat dissipation during high-energy processes. This capability prevents overheating and maintains the stability of equipment, a critical factor in achieving precise ion implantation.
Ceramics, while known for their durability, lack the electrical conductivity required for controlling ion beams. Graphite, on the other hand, excels in this area. Its ability to conduct electricity supports the precise manipulation of ion energy, ensuring accurate implantation depths and uniform dopant distribution. This precision directly impacts the performance and reliability of semiconductor devices.
Graphite also surpasses alternative materials in terms of cost-efficiency. While the initial investment in high-purity graphite components may be higher, their durability and reusability significantly reduce long-term operational costs. For example, graphite components can withstand repeated thermal cycling and mechanical stress without degrading, minimizing the need for frequent replacements. This longevity not only lowers maintenance expenses but also enhances production efficiency by reducing downtime.
“Graphite’s ability to operate effectively at high temperatures, combined with its durability and cost-efficiency, makes it a cornerstone material in the semiconductor industry.”
In addition, graphite contributes to sustainability efforts. Its reusability aligns with the industry’s push toward eco-friendly manufacturing practices, offering a more sustainable alternative to disposable or less durable materials. This environmental advantage further solidifies its position as the material of choice in ion implantation systems.
How Graphite Improves Manufacturing Efficiency and Product Quality
Graphite plays a pivotal role in enhancing both the efficiency of semiconductor manufacturing and the quality of the final products. Its high thermal conductivity ensures that equipment operates within optimal temperature ranges, preventing overheating and maintaining consistent performance. This stability allows manufacturers to achieve higher throughput without compromising the precision of the ion implantation process.
The chemical stability of graphite also contributes to improved product quality. High-purity graphite components, such as shields and susceptors, prevent contamination during wafer processing. This purity is essential for maintaining the integrity of semiconductor wafers, which are highly sensitive to impurities. By using graphite, manufacturers can ensure that the implanted ions achieve the desired electrical and structural modifications, resulting in devices with superior performance and reliability.
Graphite’s adaptability further enhances manufacturing efficiency. Its customizability allows manufacturers to design components tailored to specific applications, optimizing performance across various stages of semiconductor production. For instance, porous graphite can be engineered to provide enhanced durability and thermal performance in ion implantation systems. This flexibility ensures that graphite components meet the exacting standards of modern semiconductor manufacturing.
“Graphite enhances the efficiency and performance of semiconductor devices while supporting sustainability efforts through its reusability and adaptability.”
The use of graphite also reduces operational costs. Its durability minimizes wear and tear, lowering maintenance requirements and extending the lifespan of equipment. This reliability translates into fewer disruptions and higher production yields, enabling manufacturers to meet the growing demand for advanced semiconductor devices.
The Future of Ion Implantation Graphite in Semiconductor Manufacturing
Innovations in Graphite Material Science
Advancements in graphite material science are reshaping its role in semiconductor manufacturing. Researchers are focusing on developing high-purity and high-strength graphite to meet the increasing demands of modern semiconductor processes. These materials exhibit superior thermal and electrical properties, which are essential for maintaining precision and efficiency in ion implantation systems. For instance, high-purity graphite minimizes contamination risks, ensuring the integrity of semiconductor wafers during processing.
Emerging forms of graphite, such as graphene, are also gaining attention. Graphene, a single layer of carbon atoms arranged in a hexagonal lattice, offers exceptional electrical conductivity and thermal performance. Its strength surpasses that of traditional graphite, making it a promising candidate for next-generation semiconductor applications. Industry experts believe that graphene could revolutionize semiconductor design by enabling smaller, faster, and more energy-efficient devices.
“Graphene’s remarkable properties, including its strength and conductivity, have the potential to redefine semiconductor technology,” according to recent studies. This innovation highlights the ongoing evolution of graphite materials and their expanding capabilities in advanced manufacturing.
Potential for Expanded Applications in Advanced Technologies
The versatility of ion implantation graphite positions it for broader applications in emerging technologies. As industries like artificial intelligence, 5G communication, and quantum computing continue to grow, the demand for advanced semiconductor devices increases. Graphite’s unique properties make it an ideal material for supporting these advancements.
In quantum computing, for example, graphite’s thermal stability and electrical conductivity play a critical role in maintaining the delicate conditions required for qubit operation. Similarly, in 5G infrastructure, graphite components enhance the performance of high-frequency devices by ensuring efficient heat dissipation and electrical control. These applications demonstrate how graphite’s adaptability extends beyond traditional semiconductor manufacturing into cutting-edge technological domains.
The integration of graphite into advanced technologies also aligns with sustainability goals. Its reusability and long lifespan reduce waste, making it a more environmentally friendly option compared to disposable materials. This alignment with eco-conscious practices further solidifies graphite’s relevance in future innovations.
Contributions of Ningbo VET Energy Technology Co. to Graphite Advancements
Ningbo VET Energy Technology Co. has emerged as a leader in driving innovation within the graphite industry. The company invests heavily in research and development to create advanced graphite materials tailored for semiconductor applications. By leveraging its expertise in high-end materials, Ningbo VET Energy Technology Co. produces graphite components that meet the stringent requirements of modern manufacturing processes.
The company’s focus on high-purity graphite ensures that its products deliver consistent performance in ion implantation systems. Its R&D team continuously explores new ways to enhance graphite’s thermal, electrical, and mechanical properties. For example, the development of custom graphite solutions allows manufacturers to optimize their equipment for specific applications, improving both efficiency and product quality.
“Ningbo VET Energy Technology Co. combines innovation with practical expertise to deliver cutting-edge graphite solutions,” as highlighted in industry reports. This commitment to excellence has earned the company recognition as a trusted partner in the semiconductor sector.
By prioritizing quality and innovation, Ningbo VET Energy Technology Co. contributes significantly to the advancement of ion implantation graphite. Its efforts not only support current manufacturing needs but also pave the way for future breakthroughs in semiconductor technology.
Graphite remains a cornerstone material in ion implantation, driving advancements in semiconductor manufacturing. Its unmatched thermal conductivity, chemical stability, and electrical properties ensure precision and efficiency in critical processes. Beyond its technical advantages, graphite offers cost-effectiveness and reusability, making it indispensable for modern production demands. Companies like Ningbo VET Energy Technology Co. play a pivotal role in this field. By delivering high-purity graphite solutions and fostering innovation, they empower manufacturers to meet the evolving challenges of the semiconductor industry with confidence and reliability.
よくあるご質問
What is ion implantation, and why is it important in semiconductor manufacturing?
Ion implantation introduces ions into a substrate, such as a silicon wafer, to alter its physical, chemical, or electrical properties. This process enables precise control over dopant placement, which is essential for creating the intricate features found in modern semiconductor devices. It ensures consistent performance in components like transistors, microprocessors, and memory chips.
Why is graphite used in ion implantation systems?
Graphite is used due to its exceptional thermal conductivity, chemical stability, and electrical properties. These characteristics allow it to withstand extreme temperatures, resist chemical degradation, and support precise energy control during ion implantation. Its high purity also ensures that no contaminants interfere with the delicate semiconductor manufacturing process.
How does graphite improve the efficiency of ion implantation?
Graphite enhances efficiency by dissipating heat generated during ion acceleration, maintaining equipment stability, and preventing overheating. Its chemical stability ensures no unwanted reactions occur, while its electrical conductivity allows for precise ion beam manipulation. These factors collectively improve the accuracy and reliability of the implantation process.
What are the key applications of graphite in semiconductor manufacturing?
Graphite plays a critical role in various applications, including:
- Ion implantation equipment: Beamline parts, electrodes, and shields.
- Wafer handling: Susceptors and carriers that protect wafers from contamination and damage.
- Other processes: Plasma etching, chemical vapor deposition (CVD), and epitaxy.
Its versatility makes it indispensable across multiple stages of semiconductor production.
How does the growth of the semiconductor industry affect the demand for graphite components?
The rapid growth of the semiconductor industry and advancements in technology have significantly increased the demand for graphite components. These materials are essential for meeting the precision, durability, and efficiency requirements of modern semiconductor manufacturing processes.
“As semiconductor devices become smaller and more complex, the need for high-performance materials like graphite continues to rise.”
What makes graphite more cost-effective than alternative materials?
Graphite offers durability, reusability, and long lifespans, reducing the frequency of replacements and maintenance costs. While the initial investment may be higher, its ability to withstand extreme conditions and repeated use offsets long-term expenses. Additionally, its adaptability allows manufacturers to optimize components for specific applications, further enhancing cost efficiency.
Can graphite be customized for specific semiconductor applications?
Yes, graphite can be tailored to meet the unique demands of various semiconductor processes. For example, porous graphite enhances durability and thermal performance, while high-density graphite provides superior strength for mechanically stressed components. This customizability ensures optimal performance across different manufacturing stages.
How does graphite contribute to sustainability in semiconductor manufacturing?
Graphite’s reusability and long lifespan align with eco-friendly manufacturing practices. Its durability reduces waste, while its ability to maintain performance over multiple cycles minimizes resource consumption. These attributes make it a sustainable choice for the semiconductor industry.
What role does Ningbo VET Energy Technology Co. play in advancing graphite for semiconductor use?
Ningbo VET Energy Technology Co. specializes in producing high-purity graphite tailored for semiconductor applications. The company invests in research and development to enhance graphite’s thermal, electrical, and mechanical properties. By delivering innovative and reliable solutions, it supports manufacturers in meeting the evolving challenges of the semiconductor industry.
“Ningbo VET Energy Technology Co. combines expertise and innovation to provide cutting-edge graphite solutions, ensuring high-quality performance in advanced manufacturing processes.”
What does the future hold for ion implantation graphite in semiconductor manufacturing?
The future of ion implantation graphite looks promising, with ongoing advancements in material science. Innovations like graphene, a derivative of graphite, offer even greater electrical conductivity and thermal performance. These developments position graphite to play a pivotal role in next-generation technologies, including quantum computing, 5G communication, and artificial intelligence.