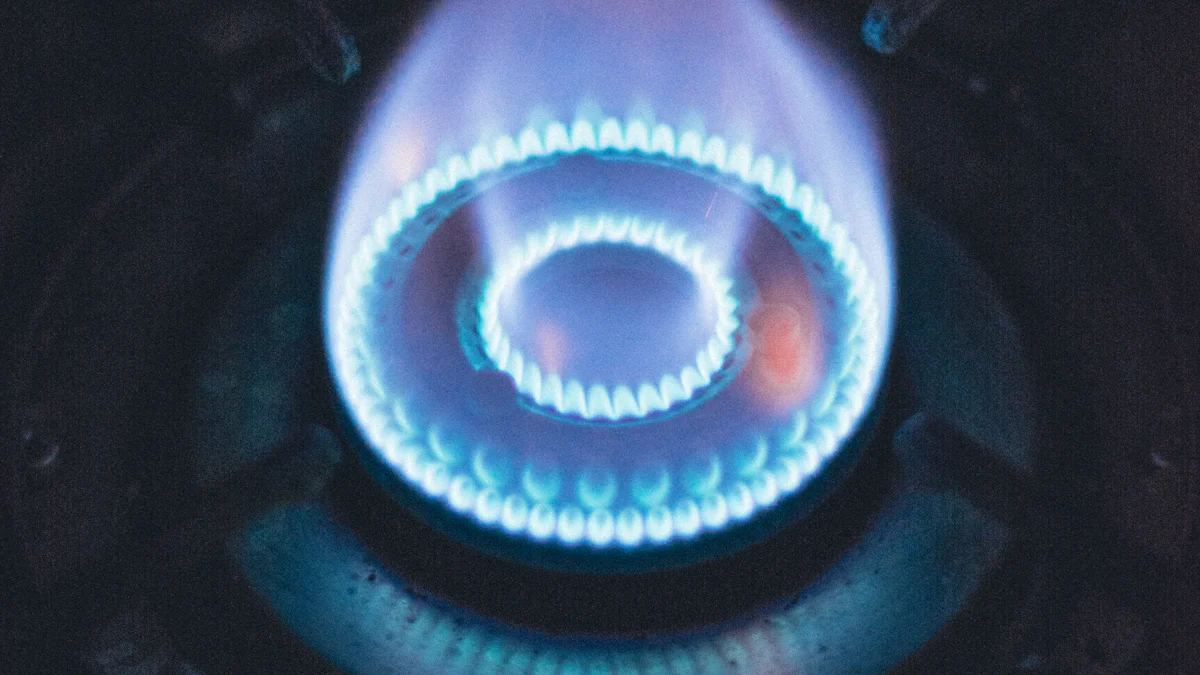
ウェーハヒーターは、特に半導体製造において、産業用途において重要な役割を果たしており、精密な温度制御により、集積回路の品質が保証されます。 これらの装置は生産の効率およびエネルギー消費に影響を与えます、それらを現代企業で必要としました。 ウェーハヒーターのグローバル市場を予測し、 2030年までにUS$ 2117.8百万成長する需要を反映している。 メーカーは熱伝導性および温度の均等性を高めるために高度材料と革新しています。 これは重要な質問を上げます:抵抗と赤外線ウエファーヒーターが比較する方法、およびどの技術が特定の産業ニーズに最も適したか?
要点
- 抵抗ウエハヒーターは、半導体製造における高精度な用途に理想的な温度安定性と均一性を提供します.
- 赤外線ウエファーのヒーターは速度およびエネルギー効率で、急速な熱調節を可能にし、結合および治癒のようなプロセスのために重要である集中された熱を、熱しました.
- 抵抗および赤外線ヒーター間の選択は特定の産業必要性によって決まります:抵抗のヒーターは安定性および均等性のために最もよく、赤外線ヒーターは速い熱周期のために適しています.
- 初期費用とメンテナンスコストを考慮する: 抵抗ヒーターは、一般的により手頃な価格ですが、赤外線ヒーターはより高い先行投資を必要とするかもしれませんが、長期的な運用コストを節約できます.
- 両方のヒーターのタイプに独特な利点があります:抵抗のヒーターは赤外線ヒーターがさまざまな熱条件のための柔軟性そして適応性を提供するように、大量生産のために耐久そして信頼できるです.
- 異なるウェーハ材料でヒーター技術の互換性を理解することは、処理中に性能を最適化し、熱的ストレスを最小限に抑えることが不可欠です.
- 運用目標でヒーターの選択を合わせることで、産業用途における最適な性能、エネルギー効率、コスト効率性を保証します.
ウェーハヒーター技術の概要
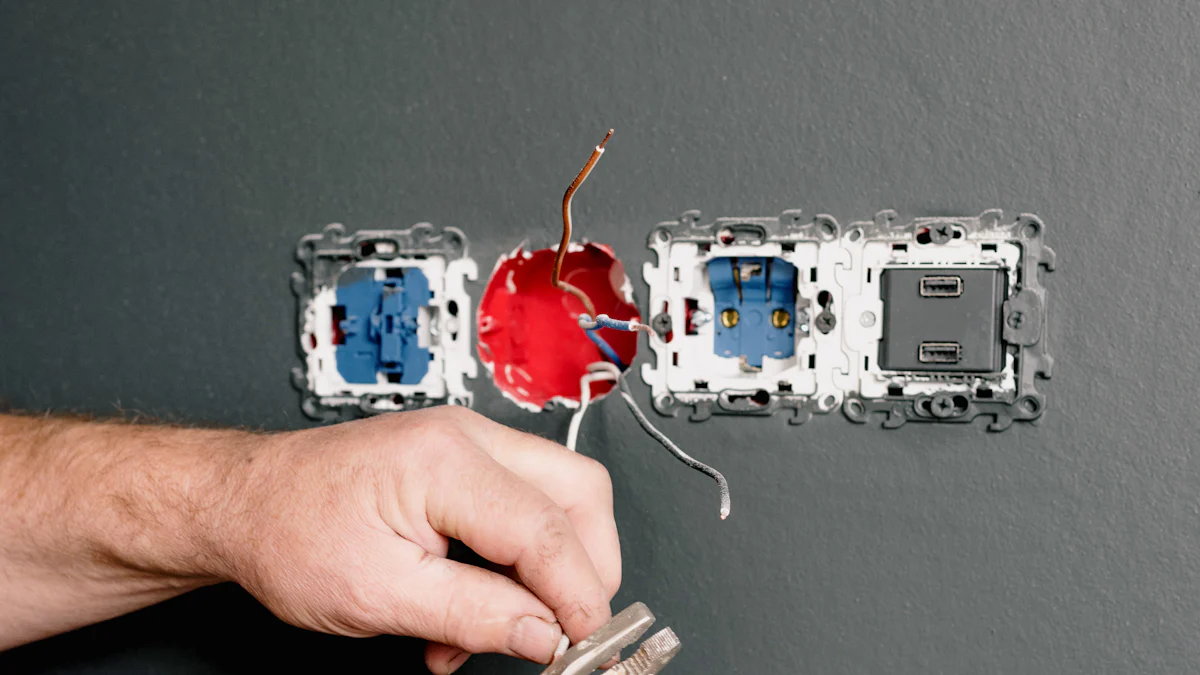
半導体製造、その他の工業プロセスにおいて、ウェーハヒーターが不可欠です。 一貫した品質と効率性を実現するために重要な正確な温度制御を保証します。 様々な技術が利用できる中、, 抵抗のウエファーのヒーター そして 赤外線ウエファーのヒーター 独自の作業原理とアプリケーションにより、スタンドアウトします.
抵抗ウエファーヒーター
働き原則
抵抗ウエハヒーターは、電気エネルギーを熱に変換し、抵抗の要素を通すことで作動します。 これらの要素は、アルミニウムやセラミックなどの材料から作られ、電流が通過したときに熱を発生させます。 ウェーハ表面全体に均一に熱伝達し、一貫した温度分布を保証します。 からなされるそれらのような高度の抵抗のヒーター、 アルミニウム6061-T6450°Cまでの実用温度を達成できます +/-1%の温度の均等性が付いているC。 この精密は安定した熱条件を要求するプロセスのためにそれらに非常に信頼できるようにします.
共通の産業適用
抵抗ウエハヒータは、半導体加工における広範囲な用途で使用されています。 薄膜蒸着、エッチング、レジストフィルムベーキングなどの用途に最適です。 高温均一性を維持する能力は、繰り返し、効率的なウェーハ処理を保証します。 産業はまた長期安定性および最低の熱変動を要求する仕事のためのこれらのヒーターに頼ります。 抵抗ヒーターの耐久性と精度は、大量生産環境に適した選択肢です.
赤外線ウエファーのヒーター
働き原則
赤外線ウエファーのヒーターは直接ウエファーの表面を熱する赤外線放射を出すことによって機能します。 抵抗ヒーターとは異なり、熱を移すための導電に依存しません。 代わりに、赤外線放射は材料を貫通し、内部に熱を発生させます。 この方法は急速な暖房および精密な温度制御を可能にします。 赤外線ヒーターは、他の技術と比較して時間の一部分の温度を達成できるため、迅速な熱サイクルを必要とするプロセスで優れています.
共通の産業適用
赤外線ウエファーのヒーターは結合、治癒およびアニーリングのようなプロセスで広く利用されています。 迅速でローカライズされた加熱を実現する能力は、スピードと精度が重要なアプリケーションに適しています。 これらのヒーターは、より少ないエネルギーを消費し、全体的な処理時間を削減するので、環境に優しいです。 業界の有利な赤外線ヒーターは、柔軟性と適応性を要求し、熱要件を変更します.
抵抗および赤外線ウエファーのヒーターの比較
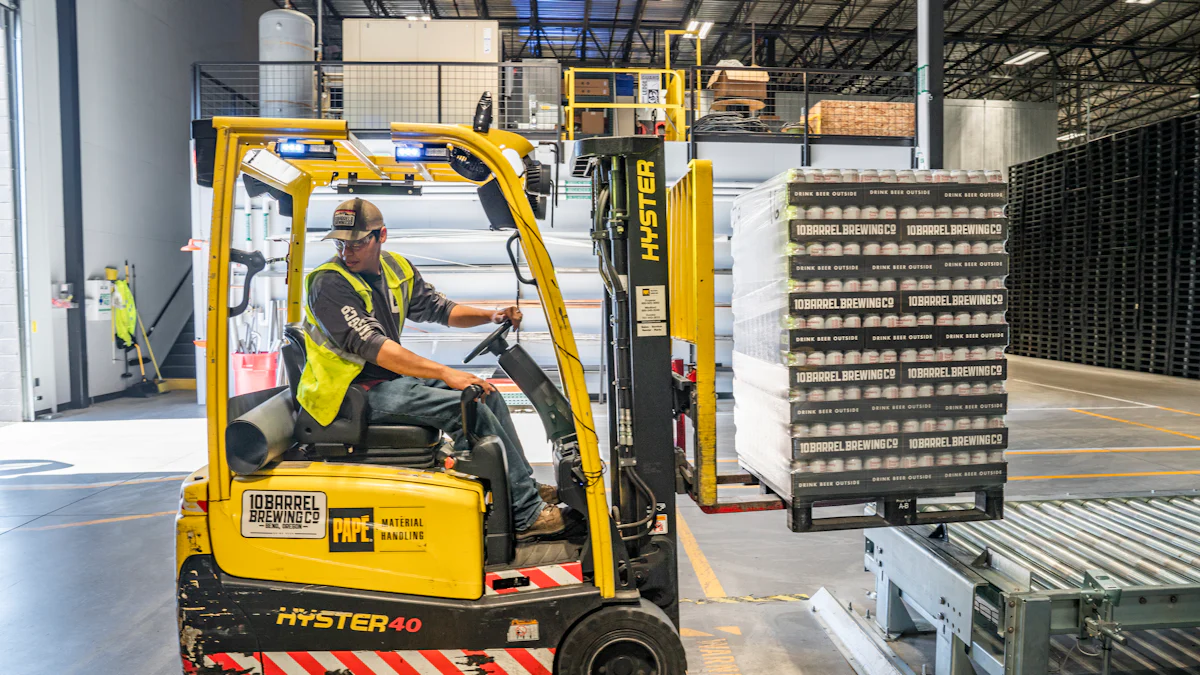
ソリューション
エネルギー消費量および熱伝達
エネルギー効率は、産業用途向けのウェーハヒーターの適合性を決定する際に重要な役割を果たします。 抵抗ウエハヒーターは、ウェーハ表面全体に一貫した熱伝達を提供する。 それらの設計は長期操作の間にエネルギー無駄を最小にする高温均等性を保障します。 これにより、長期にわたって安定した熱条件を必要とするプロセスに優れた選択肢が得られます.
一方の赤外線ウエファーのヒーターは、急速なエネルギー配達に焦点を合わせます。 ウェーハに直接赤外線放射を出すことで、インターメディアの熱伝達機構の必要性を減らします。 エネルギー損失を最小限にし、加熱サイクルの短縮を実現します。 速度およびエネルギー保存を優先する企業は、多くの場合、最小限のエネルギー入力で高温を達成するために能力の赤外線ヒーターを好む.
応答時間および暖房の均等性
応答時間は、ウェーハヒータの効率を著しく影響します。 抵抗ヒーターは、通常、導電の信頼性のために、希望する温度に達するために長くかかります。 しかし、一度安定して、熱の均一性を維持します。 この特徴は、一貫した温度分布が重要であるアプリケーションに最適です.
赤外線ヒーターは応答時間の面の抵抗のヒーターをoutperform。 ほぼ瞬時に熱を届ける能力は急速な熱調節を保障します。 暖房の均等性は抵抗加熱器と一致しないかもしれませんが、ローカライズされた加熱の精度は、この制限を補います。 これは、迅速な熱サイクルとターゲティング加熱を必要とするプロセスに適しています.
コスト
初期およびメンテナンスコスト
抵抗ウエハヒーターの初期投資は、赤外線ヒーターと比較して低下する傾向があります。 シンプルなデザインとワイドな可用性は、その手頃な価格に貢献します。 抵抗ヒーターのメンテナンスコストも比較的低く、コンポーネントは耐久性があり、交換が容易です.
高度の技術の赤外線ウエファーのヒーターは、頻繁により高い先端費と来ます。 赤外線エミッタなどの専門コンポーネントは、慎重な取り扱いと定期的な交換が必要です。 メンテナンス費を随時増加させます。 しかし、最先端の技術に投資する産業は、追加の費用価値のある赤外線ヒーターの利点を見つけるかもしれません.
長期運用コスト
運用コストはエネルギー消費と耐久性に依存します。 抵抗ヒーターは、均一温度を保ちながらエネルギー効率が良いため、頻繁な温度変化を必要とする用途で高い運用コストを削減できます。 応答時間が遅くなると、調整中にエネルギー使用量が増加します.
急速な暖房機能の赤外線ヒーターは、頻繁により低い長期運用費で起因します。 迅速な熱サイクル中にエネルギー廃棄物を最小限に抑える能力は、業界がスピードと効率を優先する費用対効果の高いソリューションです。 しかし、メンテナンスの要件は、全体的なコスト分析に考慮する必要があります.
精密加工
温度制御および安定性
抵抗ウエファーのヒーターは比類のない温度安定性を提供します。 彼らの設計は精密な熱制御を要求するプロセスのために重要な一貫した熱配分を保障します。 半導体製造における欠陥のリスクを低減し、レジストヒーターを高精度な用途に確実な選択肢にします.
赤外線ヒーターは優秀な温度制御を提供しますが、より大きい表面上の安定性を維持するで挑戦に直面するかもしれません。 彼らの強さは顕著な正確さと局所暖房を渡す能力にあります。 これは、均一加熱ではなく、ターゲティング温度調整を必要とするタスクに適しています.
高精度用途の適性
高精度な適用は厳しい熱条件を満たすことができるウエファーのヒーターを要求します。 抵抗ヒーターは、優れた均一性と安定性で、そのようなシナリオで優れています。 半導体加工に広く使われ、微小な温度変動でも製品品質を損なうことができる.
赤外線ヒーターは、より少ない均一ながら、迅速かつ精密な熱変化を必要とするアプリケーションで輝きます。 周囲の材料に影響を与えずに特定の領域を加熱する能力は、接着や硬化などのプロセスで有意に値する。 柔軟性と適応性を求める産業は、多くの場合、その高精度のニーズのための赤外線ヒーターに変わります.
適用 適性
ウエハ素材との互換性
異なるウェーハ材料を備えたウェーハヒーターの互換性は、性能と応用範囲に著しく影響します. 抵抗ウエファーヒーター シリコン、クオーツ、セラミックスなど、幅広い材料に均一な熱分布を提供することができます。 一貫した温度プロファイルを維持する能力は、材料の変形や損傷の危険性を軽減し、繊細なウェーハに最小限の熱的ストレスを保証します。 これにより、さまざまな熱特性でウェーハを処理する業界に信頼できる選択肢が生まれます.
赤外線ウエファーのヒーター対照的に、選択的な暖房機能を提供します。 赤外線放射は吸収特性に基づいて材料と異なる相互作用します。 例えば、シリコンウェーハは赤外線エネルギーを効率的に吸収し、迅速かつローカライズされた加熱を実現します。 しかし、低赤外線吸収材は、最適な加熱性能を達成するために追加の調整が必要な場合があります。 この選択的な性質は、特定の材料特性が精密な熱制御のために活用する必要がある適用のために赤外線ヒーターを理想的にします.
主なインサイト: 抵抗ヒーターは、材料固有の加熱精度を必要とするアプリケーションで赤外線ヒーターがExcelを出力しながら、多様なウェーハ材料間で高温均一性を提供します.
産業環境の性能
産業環境は一貫した性能を渡す間厳密な作動状態に抗できるウエファーのヒーターを要求します。 抵抗ヒーターは、大量生産設定でも、優れた耐久性と安定性を発揮します。 長期にわたって均一な温度を維持するための堅牢な構造と能力は、長期にわたる信頼性を必要とするプロセスに適しています。 業界は、繰り返し熱サイクルと厳格な品質基準を関与するタスクの抵抗ヒーターを好むことが多い.
一方、赤外線ヒーターは速度および適応性が重要である動的産業環境で繁栄します。 急激な応答時間とローカライズされた加熱を提供する能力により、温度変化の頻繁なプロセスで効率的に実行できます。 しかし、周囲温度や材料の反射率などの環境要因により性能が変化する場合があります。 適切な校正とメンテナンスは、このような設定で一貫した結果を確実にするために不可欠です.
比較ノート: 抵抗ヒーターは安定した、大量の操作で、赤外線ヒーターは高速で、適応産業プロセスで輝きます.
ウェーハヒーター技術の活用と限界
抵抗ウエファーヒーター
メリット
抵抗のウエファーのヒーターは例外的な温度の安定性および均等性を提供します。 設計は、精密な熱制御を必要とするプロセスのために重要なウエハ表面を渡る一貫した熱配分を保障します。 業界は、長期にわたって安定した動作条件を維持し、信頼性のためにこれらのヒーターを評価します。 構造のシンプルさは、機械的故障の可能性を減らし、耐久性を高めます.
抵抗ヒーターの有用性は重要な利点として際立っています。 彼らの簡単な設計と広範囲の可用性は、初期投資とメンテナンスの両方に費用対効果が大きいようにします。 さらに、抵抗ヒーターは高温を効率的に達成でき、最大450°に達する高度なモデルもあります。 +/-1%の温度の均等性を維持している間C。 半導体製造における高精度な用途に適しています.
制限事項
強度にもかかわらず、抵抗ウエファーヒーターは応答時間の制限に直面しています。 熱伝達のための伝導に対する信頼性は、他の技術と比較して熱調節が遅くなります。 この特性は、迅速な温度変化を必要とするプロセスの非効率性につながることができます.
別の制限は、動的操作中にエネルギー消費量にあります。 抵抗ヒーターは、安定した温度を維持しながら、頻繁な調整はエネルギー使用量を増やすことができます。 さらに、その性能は、抵抗要素を磨耗し、定期的な交換を怠り、効率性を維持するために劣化する可能性があります.
赤外線ウエファーのヒーター
メリット
速度および精密の赤外線ウエファーのヒーターのExcel。 赤外線放射によるウェーハ表面に直接熱を届ける能力はエネルギー損失を最小限にし、急速な熱調節を可能にします。 この機能は、接着、硬化、アニールなどの迅速な温度変化を必要とするプロセスに最適です.
赤外線ヒーターの選択加熱機能は、別の利点を提供します。 赤外線放射は材料の特性に基づいてターゲットを絞られた暖房を可能にするさまざまな材料と異なって相互作用します。 例えば、シリコンウェーハは赤外線エネルギーを効率的に吸収し、正確でローカライズされた加熱を実現します。 この適応性は、柔軟性と材料固有の熱制御を要求するアプリケーションのための適合性を高めます.
赤外線ヒーターはまたエネルギー効率に貢献します。 中間熱伝達のメカニズムの必要性を減らすことによって、それらは全面的なエネルギー消費を下げます。 環境に配慮した自然は、持続可能な製造慣行に向けた業界のトレンドに合わせています.
制限事項
より大きい表面を渡る均一熱配分を達成する赤外線ウエファーのヒーターは挑戦に直面します。 局所加熱の強さは、一貫した熱条件を必要とするプロセスに影響を与えることができる不均等な温度プロファイルをもたらすかもしれません。 適切な校正とセットアップは、この制限を緩和するために不可欠です.
赤外線ヒーターのより高い初期費用は別の欠点を示します。 赤外線エミッタなどの高度な技術と専門コンポーネントは、前方費用を増加させます。 これらのコンポーネントの定期的な交換の必要性により、メンテナンスコストも高くなります。 インダストリーズは、赤外線ヒーターを検討する際に、速度と精度のメリットに対してこれらのコストを削減しなければなりません.
科学的洞察: SnO2:Sb、outperformの高温安定性の金属片、特に1300 K付近の動作温度で、半導体のヒーター材料が、強調する。 ヒーター性能を最適化する材料選定の重要性を強調しています.
抵抗および赤外線ウエファーのヒーターは特定の産業必要性に合わせる各提供の明瞭な利点を提供します。 抵抗ヒーターは温度の均等性で、一貫した質および有効なウエファーの処理を保障します。 耐久性と耐久性は、大量生産に最適です。 急速な応答および物質的な特定の暖房の精密の赤外線ヒーター、速い熱周期および適応性を要求するスーツの塗布.
適切な技術を選択すると、アプリケーション要件、予算、および精度のニーズによって異なります。 安定性と均一性を優先する産業は、速度とエネルギー効率を評価している間、抵抗ヒーターを考慮する必要があります。 運用目標に合わせてヒーターの選択を合わせることで、最適な性能と費用効果が向上します.