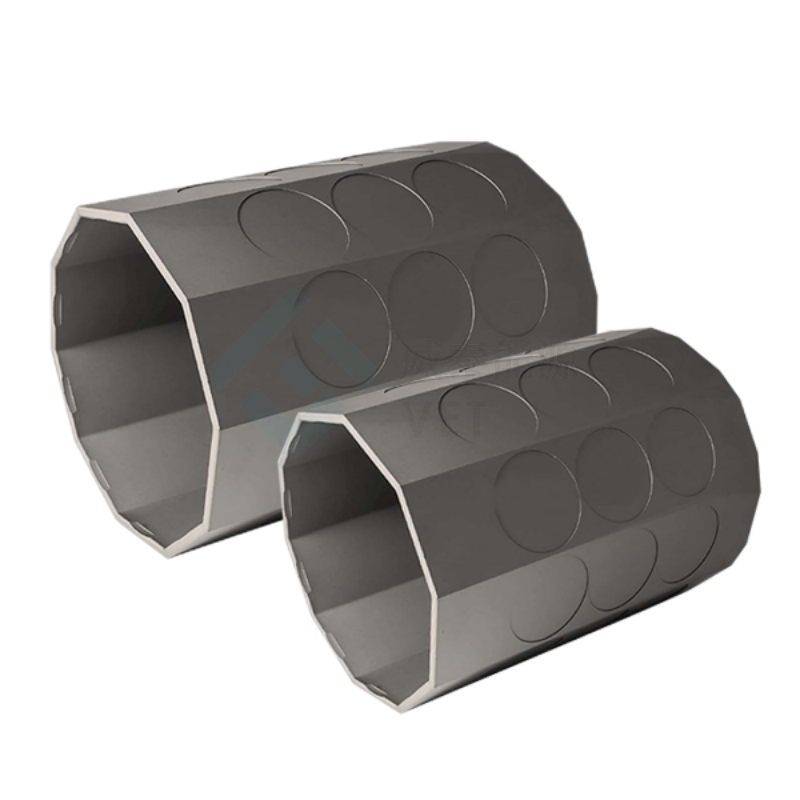
Choosing the right CVD SiC coating barrel type susceptor for CVD SiC coating applications significantly impacts performance and cost-efficiency. CVD SiC coating barrel susceptors excel in high-volume production due to their cylindrical design, enhancing throughput. Pancake-type susceptors, however, ensure uniform heating, making them ideal for semiconductor manufacturing. CVD SiC coating wafer EPL susceptors offer unmatched thermal stability, chemical resistance, and durability, ensuring consistent results in demanding environments.
特徴 | Barrel-Type Susceptors | Pancake-Type Susceptors |
---|---|---|
熱性能 | Enhanced throughput and efficiency in large-scale production due to cylindrical design. | Provides uniform heating essential for precise thermal management in various applications. |
適用 適性 | Ideal for high-volume manufacturing processes. | Widely used in semiconductor manufacturing and advanced coatings. |
コストへの影響 | Not explicitly compared, but generally associated with large-scale production efficiency. | Durability and advanced materials may imply higher initial costs but improved longevity. |
SiC-coated susceptors outperform alternatives in thermal conductivity and structural integrity, making them indispensable for critical applications.
要点
- Barrel-type susceptors speed up production, perfect for LED industries.
- Pancake-type susceptors heat evenly, important for making semiconductors.
- Picking the right susceptor boosts efficiency and lowers costs, fitting specific needs.
Overview of Susceptors in CVD SiC Coating
What Are Susceptors?
Susceptors play a critical role in chemical vapor deposition (CVD) processes, particularly in SiC coating applications. These components serve as the foundation for wafers during epitaxy, providing a stable platform to ensure precise material deposition. Their primary function involves absorbing heat and distributing it uniformly across the wafer surface. This even heat distribution is essential for maintaining consistent temperature conditions, which directly impacts the quality of semiconductor fabrication.
In addition to thermal management, susceptors contribute to reducing defects and improving substrate quality. By ensuring uniform growth of epitaxial layers, they help minimize inconsistencies and enhance the overall yield in semiconductor manufacturing. Furthermore, their resistance to oxidation and corrosion allows them to maintain structural integrity under the harsh conditions typical of CVD processes. This durability makes them indispensable for high-performance applications.
Importance of Susceptor Design in CVD SiC Coating
The design of a susceptor significantly influences the efficiency and quality of CVD SiC coatings. Pancake-type susceptors, for instance, excel in providing uniform heating, which is crucial for producing high-quality thin films. Their design minimizes thermal gradients, ensuring even temperature distribution across the substrate. This uniformity reduces defects and inconsistencies in the deposited films, making them ideal for applications requiring precise thermal management.
On the other hand, the cylindrical structure of a cvd sic coating barrel type susceptor enhances throughput in high-volume production. This design supports efficient heat absorption and distribution, optimizing performance in large-scale manufacturing. Additionally, the SiC coating on these susceptors offers exceptional chemical resistance and thermal stability. This ensures that the susceptor retains its structural integrity even under extreme temperatures and corrosive environments, such as those encountered in metal-organic chemical vapor deposition (MOCVD) processes.
By carefully selecting the appropriate susceptor design, manufacturers can achieve superior thermal performance, reduced defects, and improved cost-efficiency, tailored to their specific application needs.
CVD SiC Coating Barrel Type Susceptor
Design and Structure
The cvd sic coating barrel type susceptor features a cylindrical design optimized for high-volume production. It is typically constructed using silicon carbide-coated graphite, which offers exceptional heat resistance and thermal uniformity. The SiC coating ensures chemical inertness, preventing contamination during epitaxial growth. This material also resists high-temperature oxidation, maintaining stability up to 1600°C. The fine SiC crystal coating creates a smooth surface, enhancing the evenness of thermal profiles and ensuring consistent wafer processing. Additionally, the dense surface and low porosity prevent impurities from diffusing into the substrate, safeguarding the purity of epitaxial layers.
Advantages of Barrel-Type Susceptors
Barrel-type susceptors excel in applications requiring high throughput. Their cylindrical structure supports efficient heat absorption and distribution, reducing energy consumption while maintaining uniform epitaxial growth. The use of silicon carbide-coated graphite enhances thermal conductivity, ensuring consistent heating across all wafers. This design also achieves an optimal laminar gas flow pattern, further improving process efficiency. Durability is another key advantage. These susceptors withstand corrosive environments and repeated chemical cleaning, making them ideal for demanding processes like MOCVD.
Limitations of Barrel-Type Susceptors
Despite their benefits, barrel-type susceptors may not suit every application. Their design prioritizes throughput over precise thermal control, making them less effective for processes requiring extreme uniformity. The initial cost of manufacturing these susceptors can also be higher due to the advanced materials used. Additionally, their cylindrical shape may limit compatibility with certain reactor designs, reducing flexibility in some production setups.
Pancake-Type Susceptors for CVD SiC Coating
Design and Structure
Pancake-type susceptors feature a flat, circular geometry designed to ensure even heat distribution across the substrate. This design minimizes temperature gradients, which is critical for achieving uniform thin-film deposition. Typically constructed from high-purity graphite, these susceptors exhibit excellent thermal conductivity and stability under high-temperature conditions. To enhance their performance, manufacturers coat the graphite with silicon carbide (SiC). This coating improves resistance to chemical reactions and wear, making pancake susceptors suitable for demanding environments.
特徴 | 説明 |
---|---|
Geometry | Flat, circular design ensures even heat distribution and minimizes temperature gradients. |
素材 | High-purity graphite with SiC coating for superior thermal conductivity and chemical resistance. |
熱安定性 | SiC coating enhances durability, supporting high-temperature applications. |
Dimensional Stability | Maintains shape and functionality during intense thermal processes, ensuring precise thermal control. |
This combination of materials and design ensures uniform heat transfer, which is essential for processes like thin-film deposition. The high thermal conductivity of graphite, paired with the protective SiC coating, allows pancake susceptors to maintain consistent performance over extended periods.
Advantages of Pancake-Type Susceptors
Pancake susceptors offer several advantages that make them indispensable in precision applications. Their flat, circular design ensures uniform temperature distribution, reducing defects and inconsistencies in thin-film deposition. This thermal uniformity is particularly beneficial in semiconductor manufacturing, where even minor temperature variations can compromise product quality.
The use of high-purity graphite coated with SiC enhances durability and thermal stability. This robust construction reduces the need for frequent replacements, saving both time and resources. Additionally, the efficient heat transfer properties of pancake susceptors minimize energy consumption during high-temperature processes. By maintaining consistent thermal conditions, these susceptors improve productivity and reduce operational costs.
Limitations of Pancake-Type Susceptors
Despite their numerous benefits, pancake-type susceptors have limitations. Their flat design, while excellent for thermal uniformity, may not support high-throughput applications as effectively as barrel-type susceptors. The advanced materials used, such as high-purity graphite and SiC coatings, can increase initial manufacturing costs. Furthermore, their compatibility with certain reactor designs may be limited, restricting their use in some production setups.
Pancake susceptors excel in precision applications but may not be the best choice for high-volume manufacturing. Manufacturers must evaluate their specific needs to determine the most suitable susceptor type.
Comparative Analysis of Barrel-Type and Pancake-Type Susceptors
Performance and Thermal Efficiency
Barrel-type and pancake-type susceptors exhibit distinct performance characteristics tailored to specific needs. Barrel susceptors excel in high-volume manufacturing due to their ability to heat multiple wafers simultaneously. This design enhances throughput and efficiency, making them ideal for large-scale production. Pancake susceptors, on the other hand, prioritize uniform heating. Their flat geometry ensures even heat distribution, minimizing temperature gradients and improving thin-film deposition quality.
Both types utilize silicon carbide (SiC) coatings, which enhance thermal stability and chemical resistance. However, pancake susceptors are better suited for applications requiring precise thermal control, such as semiconductor manufacturing. Barrel susceptors, while less precise, deliver superior efficiency in processes involving multiple substrates.
Cost and Maintenance Considerations
The cost implications of these susceptors depend on their design and application. Barrel-type susceptors, optimized for high-volume production, often involve higher initial costs due to their advanced materials and larger size. However, their durability and ability to process multiple wafers simultaneously can reduce long-term operational expenses. Pancake susceptors, with their focus on precision, may require more frequent replacements in high-throughput environments. Their advanced SiC coatings and high-purity graphite construction also contribute to higher upfront costs.
Maintenance requirements differ as well. Barrel susceptors, designed for robust industrial use, withstand repeated chemical cleaning and corrosive environments. Pancake susceptors, while durable, demand careful handling to maintain their precise thermal properties.
Application Suitability for Specific Scenarios
Barrel-type susceptors are particularly suitable for high-volume manufacturing scenarios. Their cylindrical design supports and heats multiple wafers simultaneously, enhancing throughput in large-scale production processes. This makes them indispensable in industries like LED manufacturing and photovoltaic cell production. Pancake susceptors, by contrast, are optimized for precision applications. Their uniform heating capabilities make them ideal for semiconductor fabrication and other processes requiring exact thermal control.
Manufacturers must evaluate their specific needs when choosing between these susceptors. For high-throughput operations, barrel-type designs offer unmatched efficiency. For applications demanding precision and uniformity, pancake susceptors provide superior performance.
Barrel-type and pancake-type susceptors cater to distinct needs. Barrel designs maximize throughput, while pancake designs ensure precise thermal control.