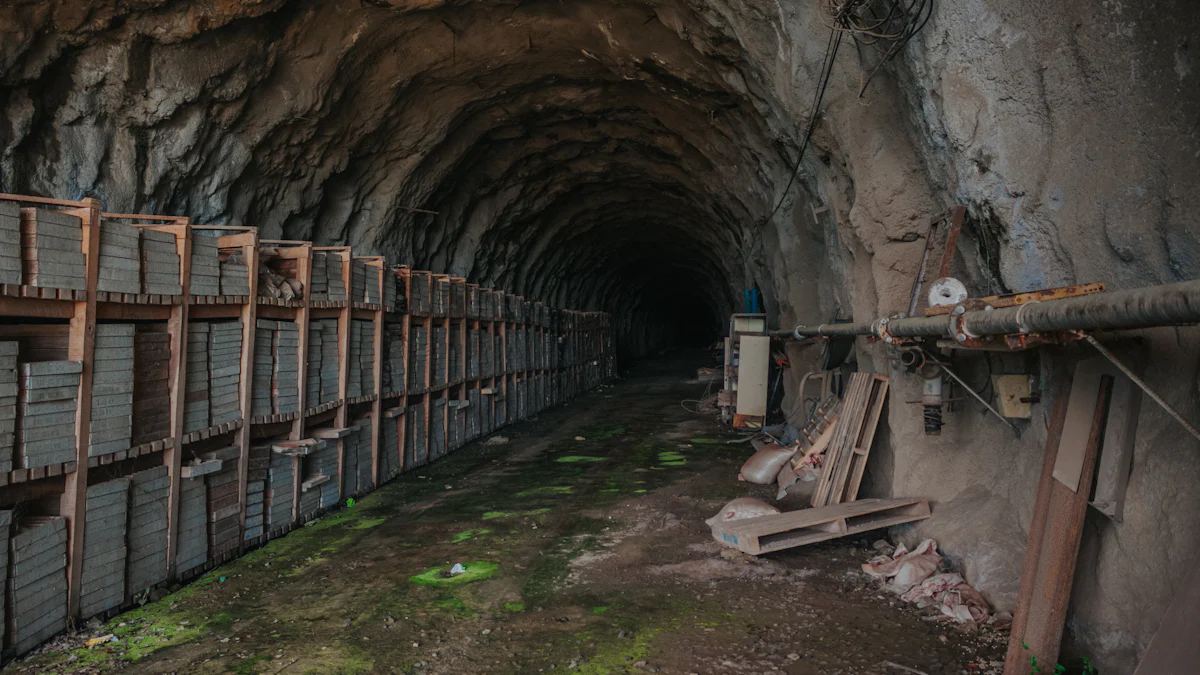
Process tubes play a vital role in industrial systems, ensuring smooth operations and optimal performance. Neglecting their maintenance can lead to severe consequences, including reduced efficiency, costly repairs, and unexpected system failures. Regular care prevents these issues and safeguards the longevity of equipment. Proactive measures, such as cleaning and inspections, help identify potential problems before they escalate. Systematic troubleshooting ensures that minor faults do not disrupt operations. By prioritizing maintenance, industries can enhance productivity, reduce downtime, and avoid unnecessary expenses.
要点
- Regular cleaning of process tubes is crucial to prevent buildup and corrosion, which can lead to leaks and reduced efficiency.
- Establish a consistent inspection schedule to identify wear and tear early, allowing for timely repairs and avoiding costly disruptions.
- Monitor and adjust flow rates using flow meters to ensure optimal performance and prevent damage from turbulence or blockages.
- Utilize specialized tools designed for process tube maintenance, such as tube brushes and inspection cameras, to enhance cleaning and inspection effectiveness.
- Address leaks promptly by identifying their causes and deciding whether to repair or replace damaged sections based on severity.
- Implement routine maintenance practices to prevent blockages, including regular cleanings and monitoring flow rates for early detection of issues.
- Maintain stable operating conditions by insulating tubes and monitoring temperature to minimize risks associated with thermal stress.
Maintenance Tips for Process Tubes
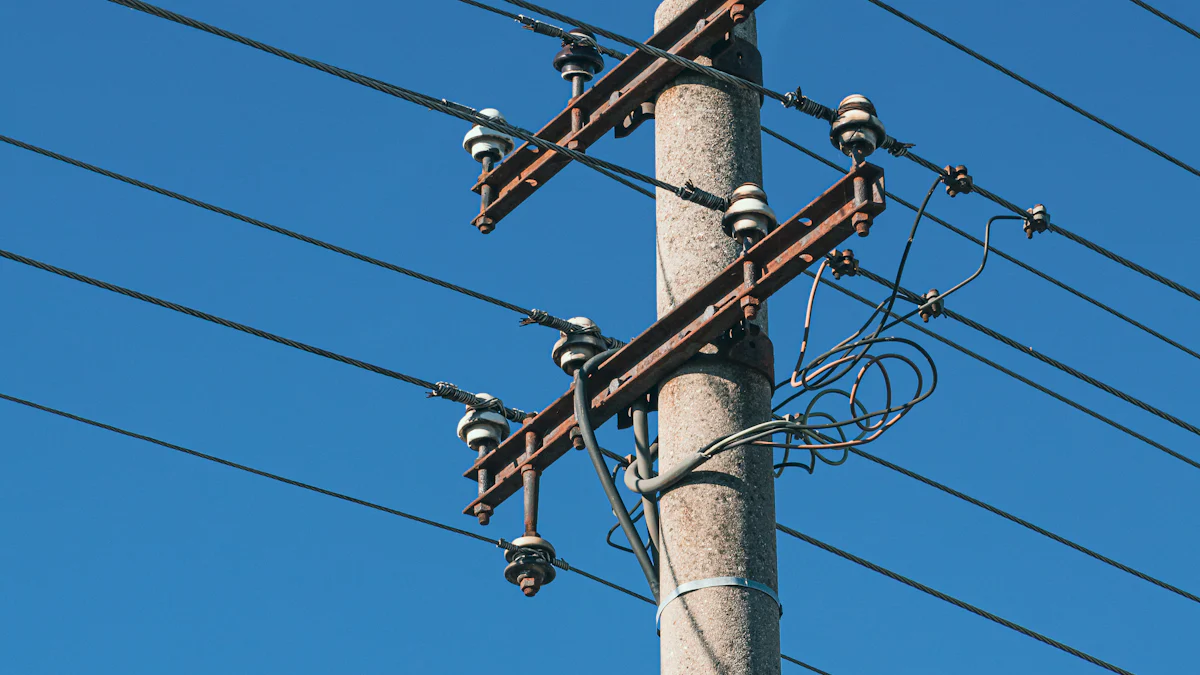
Regular Cleaning Practices
Importance of cleaning to prevent buildup and corrosion.
Cleaning process tubes regularly is essential to prevent the accumulation of debris, sediment, and other contaminants. Over time, these buildups can lead to corrosion, reducing the efficiency and lifespan of the tubes. Corrosion weakens the tube walls, increasing the risk of leaks or failures. Regular cleaning ensures that the tubes remain free from harmful deposits, maintaining their structural integrity and performance.
Recommended cleaning methods for different materials (e.g., stainless steel, glass).
Different materials require specific cleaning methods to avoid damage. For stainless steel tubes, mechanical cleaning with tube brushes made of steel or brass effectively removes loose deposits and light-scale buildup. For glass tubes, a gentler approach is necessary. Sterilizing them through autoclaving at 121°C for 30 minutes, followed by brushing with detergent and water, ensures thorough cleaning without causing scratches. Always tailor the cleaning method to the material to preserve its quality.
Using safe and effective cleaning agents.
The choice of cleaning agents plays a critical role in maintaining process tubes. Use detergents or chemical cleaners compatible with the tube material to avoid damage. For stubborn deposits, consider using specialized solutions like alcohols, aqueous cleaners, or hydrocarbons. Avoid excessive force when using mechanical methods, as this can harm the tubes. Safe and effective cleaning practices not only enhance performance but also extend the lifespan of the equipment.
Inspecting for Wear and Tear
Identifying signs of damage, such as cracks, thinning walls, or discoloration.
Regular inspections help detect early signs of wear and tear in process tubes. Look for visible cracks, thinning walls, or discoloration, which often indicate material degradation. These issues, if left unaddressed, can lead to leaks or complete tube failure. Identifying these problems early allows for timely repairs or replacements, preventing costly disruptions.
Tools and techniques for thorough inspections (e.g., visual checks, ultrasonic testing).
Effective inspections require the right tools and techniques. Visual checks are a simple yet powerful method to spot surface-level damage. For deeper issues, ultrasonic testing provides accurate insights into wall thickness and internal flaws. Combining these methods ensures a comprehensive evaluation of the tubes’ condition, enabling precise maintenance decisions.
Establishing a regular inspection schedule.
Consistency is key to maintaining process tubes. Establish a routine inspection schedule based on the operational demands and environmental conditions. For high-pressure applications or corrosive environments, more frequent inspections may be necessary. A well-planned schedule minimizes the risk of unexpected failures and keeps the system running efficiently.
Ensuring Proper Flow Rates
How improper flow rates can lead to inefficiency or damage.
Maintaining proper flow rates is crucial for the optimal performance of process tubes. Inconsistent or improper flow rates can cause turbulence, leading to erosion or blockages. These issues reduce efficiency and may result in costly repairs. Ensuring a steady and appropriate flow rate prevents unnecessary strain on the tubes.
Tips for monitoring and adjusting flow rates.
Monitoring flow rates requires precision. Use flow meters to measure the rate accurately and identify any deviations. Adjust valves or pumps as needed to maintain the desired flow. Regularly check for pressure drops, which often signal flow-related issues. Proactive monitoring ensures smooth operations and prevents damage.
Using flow meters and other diagnostic tools.
Flow meters are indispensable tools for maintaining process tubes. They provide real-time data on flow rates, helping operators detect anomalies quickly. Combine them with diagnostic tools like pressure gauges to gain a comprehensive understanding of the system’s performance. These tools simplify troubleshooting and ensure the tubes operate at peak efficiency.
Using the Right Tools and Equipment
Importance of using tools designed for process tube maintenance.
Using the right tools ensures effective maintenance and prevents unnecessary damage to process tubes. Tools specifically designed for this purpose provide precision and reliability. For instance, tube cleaning equipment tailored for industrial applications can handle tasks like removing stubborn deposits or ensuring proper sterilization. Generic tools often lack the necessary features to address the unique challenges of process tube maintenance. Investing in specialized equipment not only improves efficiency but also extends the lifespan of the tubes. Industries that prioritize proper tools experience fewer disruptions and reduced repair costs.
Examples of essential tools (e.g., tube brushes, inspection cameras).
Several tools prove indispensable for maintaining process tubes. Tube brushes, made from materials like steel, brass, or nylon, effectively scrub the inner surfaces, removing loose debris and light-scale buildup. For deeper inspections, inspection cameras allow operators to identify internal issues without dismantling the system. Advanced diagnostic tools, such as ultrasonic testers, help detect wall thinning or hidden cracks. Additionally, flow meters and pressure gauges assist in monitoring performance. These tools simplify maintenance tasks and ensure thorough care for process tubes.
Avoiding damage caused by improper tools or techniques.
Improper tools or techniques can cause significant harm to process tubes. For example, excessive force during mechanical cleaning may weaken the tube walls or create scratches, leading to long-term damage. Using incompatible cleaning agents can corrode the material, compromising its integrity. Operators must select tools and methods that align with the tube’s material and design. For instance, glass tubes require gentle handling and sterilization methods like autoclaving, while stainless steel tubes benefit from robust mechanical cleaning. Proper training on tool usage further minimizes risks and ensures safe maintenance practices.
Troubleshooting Common Issues with Process Tubes
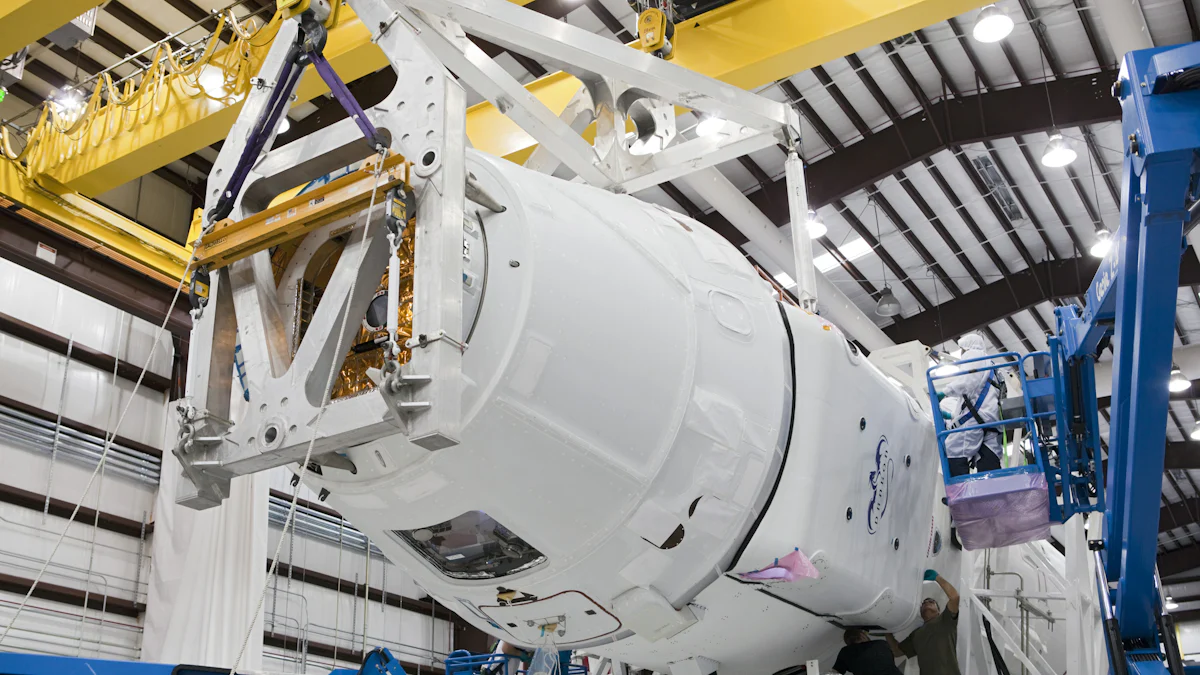
Addressing Leaks
Common causes of leaks, such as loose fittings or material degradation.
Leaks in process tubes often result from loose fittings, material degradation, or external damage. Over time, wear and tear weaken the tube walls, making them prone to cracks or holes. Corrosion, caused by exposure to harsh chemicals or moisture, also contributes to leaks. Loose connections at joints or fittings allow fluids to escape, disrupting the system’s efficiency. Identifying these causes early helps prevent further complications.
Step-by-step guide to locating and fixing leaks.
To locate and fix leaks, follow these steps:
- Inspect visually: Look for visible signs of leakage, such as wet spots, discoloration, or dripping fluids.
- Use pressure testing: Apply pressure to the system and monitor for drops, which indicate a leak.
- Employ inspection cameras: Insert inspection cameras into the tubes to identify internal cracks or holes.
- Seal minor leaks: Use sealants or epoxy to patch small cracks temporarily.
- Replace damaged sections: For severe leaks, replace the affected tube or fitting entirely.
Regular inspections and prompt repairs ensure the system operates efficiently without interruptions.
When to replace versus repair a leaking tube.
Deciding whether to repair or replace a leaking tube depends on the severity of the damage. Minor leaks, such as small cracks or loose fittings, can often be repaired using sealants or by tightening connections. However, extensive corrosion, thinning walls, or repeated leaks indicate the need for replacement. Replacing damaged tubes prevents recurring issues and ensures long-term reliability.
Resolving Blockages
Signs of blockages, such as reduced flow or pressure changes.
Blockages in process tubes disrupt fluid flow and reduce system efficiency. Common signs include decreased flow rates, pressure drops, or unusual noises. Operators may also notice uneven heating or cooling in systems that rely on thermal transfer. Identifying these symptoms early helps address blockages before they cause significant damage.
Methods for clearing blockages safely and effectively.
Clearing blockages requires careful handling to avoid damaging the tubes. Effective methods include:
- Mechanical cleaning: Use tube brushes made of steel, brass, or nylon to scrub away debris and light-scale buildup.
- Flushing with water: Employ high-pressure water jets to dislodge and remove stubborn deposits.
- Chemical cleaning: Apply safe chemical agents to dissolve hard scale or sediment.
Combining these methods ensures thorough cleaning while maintaining the integrity of the tubes.
Preventing future blockages through regular maintenance.
Preventing blockages involves consistent maintenance practices. Schedule routine cleanings to remove debris before it accumulates. Use diagnostic tools like flow meters to monitor performance and detect early signs of obstruction. Investing in proper cleaning equipment, such as chiller tube cleaning devices, simplifies maintenance and reduces the risk of future blockages.
Diagnosing and Fixing Noise Issues
Common sources of noise, such as vibrations or air pockets.
Noise in process tubes often stems from vibrations, air pockets, or loose components. Vibrations occur when flow rates are inconsistent or when tubes are improperly secured. Air pockets, trapped within the system, create gurgling or hissing sounds. Loose fittings or connections also contribute to rattling noises, disrupting operations and signaling potential issues.
How to identify the root cause of noise.
To identify the source of noise, conduct a systematic inspection:
- Check flow rates: Use flow meters to detect irregularities that may cause turbulence.
- Inspect fittings: Tighten loose connections to eliminate rattling sounds.
- Purge air pockets: Bleed the system to remove trapped air and restore smooth flow.
- Monitor vibrations: Observe the system during operation to pinpoint areas of excessive movement.
Identifying the root cause ensures targeted solutions and minimizes disruptions.
Solutions to minimize or eliminate noise.
Minimizing noise involves addressing its underlying causes. Secure tubes with clamps or supports to reduce vibrations. Adjust flow rates to maintain steady and consistent movement. Use air release valves to purge trapped air from the system. Regular maintenance, including inspections and adjustments, keeps the system quiet and efficient.
Dealing with Temperature Fluctuations
How temperature changes can affect process tubes.
Temperature fluctuations significantly impact the performance and durability of process tubes. Sudden changes in temperature cause materials to expand or contract, leading to stress on the tube walls. Over time, this stress weakens the structure, increasing the risk of cracks, leaks, or even complete failure. High temperatures accelerate corrosion, especially in metal tubes, while low temperatures may cause brittleness. These effects compromise the efficiency of the system and shorten the lifespan of the tubes. Recognizing the influence of temperature variations is essential for maintaining optimal performance.
Identifying and addressing temperature-related issues.
Operators must remain vigilant for signs of temperature-related problems. Common indicators include visible cracks, discoloration, or changes in flow rates. Uneven heating or cooling within the system also signals potential issues. To address these problems, start by inspecting the tubes using tools like inspection cameras. These devices allow operators to detect internal damage without dismantling the system. For external damage, visual checks provide quick insights into surface-level issues. Replace severely damaged tubes immediately to prevent further complications. For minor issues, consider reinforcing the affected areas with protective coatings or insulation.
Tips for maintaining consistent operating conditions.
Maintaining stable operating conditions minimizes the risks associated with temperature fluctuations. Follow these tips to ensure consistency:
- Install insulation: Use high-quality insulation materials to regulate the temperature around the tubes. This reduces exposure to extreme heat or cold.
- Monitor temperature regularly: Equip the system with temperature sensors to track fluctuations in real time. Immediate adjustments can prevent damage.
- Control flow rates: Adjust flow rates to maintain steady thermal transfer. Consistent flow reduces the likelihood of sudden temperature changes.
- Schedule routine maintenance: Regular inspections and cleanings help identify early signs of temperature-related stress. Tools like chiller tube cleaning devices ensure thorough care by removing deposits that may affect heat transfer.
By implementing these practices, industries can protect their process tubes from temperature-induced damage, ensuring long-term reliability and efficiency.
Regular maintenance and systematic troubleshooting are essential for ensuring the longevity and efficiency of process tubes. Proactive care minimizes risks, reduces downtime, and prevents costly repairs. Industries that prioritize maintenance benefit from improved performance, extended equipment lifespan, and significant cost savings. Adopting a consistent maintenance schedule ensures early detection of issues, while consulting professionals for complex problems guarantees effective solutions. By taking these steps, operators can safeguard their systems, enhance productivity, and maintain seamless operations.
よくあるご質問
What are the most common causes of process tube failures?
Process tube failures often result from corrosion, fouling, and mechanical stress. Corrosion weakens the tube walls due to chemical reactions with fluids or environmental factors. Fouling occurs when contaminants accumulate on the tube surfaces, reducing efficiency and causing blockages. Mechanical stress, such as vibrations or thermal fatigue from extreme temperature changes, can lead to cracks or leaks. Regular maintenance, including cleaning and inspections, helps prevent these issues.
How does temperature affect the performance of process tubes?
Temperature fluctuations significantly impact process tube performance. High temperatures accelerate corrosion and material degradation, while low temperatures can cause brittleness. Sudden temperature changes create thermal stress, leading to cracks or leaks. Maintaining consistent operating conditions with insulation and temperature sensors minimizes these risks. Operators should monitor temperature regularly to ensure optimal performance.
Why is regular cleaning essential for process tubes?
Regular cleaning prevents fouling, which reduces heat transfer efficiency and increases energy consumption. Contaminants, such as sediment or scale, accumulate on tube surfaces over time, creating thermal resistance. Cleaning methods like tube brushing, high-pressure water flushing, or chemical cleaning remove these deposits. Consistent cleaning ensures efficient operation and extends the lifespan of the tubes.
What tools are recommended for process tube maintenance?
Specialized tools improve the effectiveness of process tube maintenance. Tube brushes made of steel, brass, or nylon remove debris and light-scale buildup. Inspection cameras allow operators to detect internal damage without dismantling the system. Ultrasonic testers identify wall thinning or hidden cracks, while flow meters and pressure gauges monitor performance. Using the right tools ensures thorough care and prevents damage.
How can leaks in process tubes be detected and fixed?
Leaks can be identified through visual inspections, pressure testing, or the use of inspection cameras. Signs include wet spots, discoloration, or pressure drops. Minor leaks can be sealed temporarily with epoxy or sealants. For severe leaks caused by corrosion or thinning walls, replacing the damaged section is the best solution. Regular inspections help detect leaks early and prevent costly repairs.
What are the best practices for preventing blockages in process tubes?
Preventing blockages requires consistent maintenance. Operators should schedule routine cleanings to remove debris before it accumulates. High-pressure water jets and chemical cleaning agents effectively clear stubborn deposits. Monitoring flow rates with diagnostic tools like flow meters helps detect early signs of obstruction. Proactive maintenance reduces the risk of blockages and ensures smooth operations.
How do flow rates impact the efficiency of process tubes?
Improper flow rates disrupt the efficiency of process tubes. Low flow rates lead to sediment buildup, while high flow rates cause turbulence and erosion. Both scenarios reduce performance and increase the risk of damage. Monitoring flow rates with flow meters and adjusting valves or pumps ensures steady and appropriate flow, maintaining optimal efficiency.
What role does insulation play in maintaining process tubes?
Insulation regulates the temperature around process tubes, protecting them from extreme heat or cold. It minimizes thermal stress, which can cause cracks or leaks. High-quality insulation materials also improve energy efficiency by reducing heat loss. Installing insulation is a cost-effective way to maintain consistent operating conditions and extend the lifespan of the tubes.
How can noise issues in process tubes be resolved?
Noise in process tubes often stems from vibrations, air pockets, or loose fittings. To resolve these issues, operators should secure tubes with clamps or supports to reduce vibrations. Bleeding the system removes trapped air, eliminating gurgling or hissing sounds. Tightening loose connections prevents rattling noises. Regular inspections and adjustments ensure quiet and efficient operations.
When should process tubes be replaced instead of repaired?
Replacement is necessary when process tubes show extensive corrosion, thinning walls, or repeated leaks. Minor issues, such as small cracks or loose fittings, can often be repaired. However, severe damage compromises the structural integrity of the tubes, making replacement the safer and more cost-effective option. Timely replacements prevent recurring problems and ensure long-term reliability.