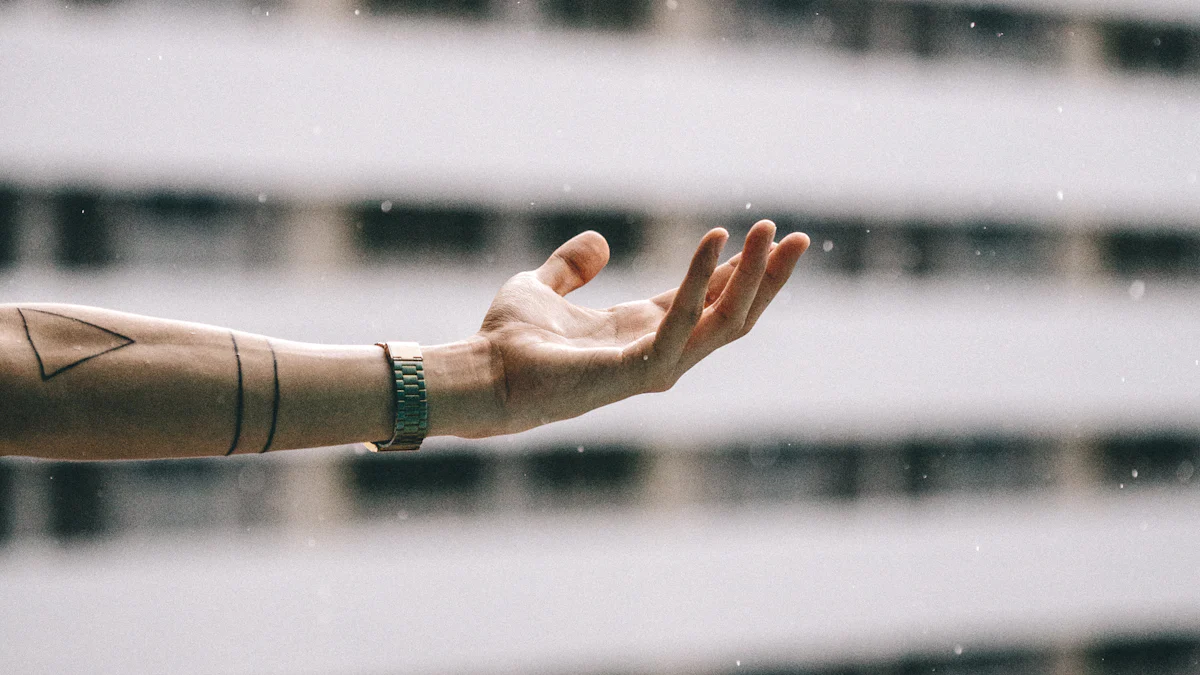
エンド・フェクター、ロボットアームの最後にツールは、自動化のアンソンヒーローです。 ロボットを握り、溶接し、組み立て、そして周囲を感知することを可能にします。 ロボットが世界とやりとりする能力が不足している。 製造業やヘルスケアの自動化などの業界として、先進的なエンド・フェクターの需要は急速に成長します。 彼らの設計は、ロボットがタスクを効果的に実行する方法を決定し、それらをロボットシステムに不可欠です。 現代のロボティクスの複雑性を高めるために、これらのデバイスが進化したのはなぜだろうか?
要点
- ロボットが環境とやりとりし、グリッピング、溶接、センシングなどの作業を行うことを可能にするためには、エンド・フェクターが不可欠です.
- シンプルな機械工具から高度な設計へと進化し、製造、ヘルスケア、農業などの業界のエンド・フェクターのアプリケーションを拡大しました.
- 素材の革新、特に柔らかいロボティクスでは、より柔軟性と感度を高め、ロボットが損傷なしで繊細なタスクを処理することを可能にします.
- AIとセンサー技術の統合により、エンドフェクターの適応性が向上し、ロボットが周囲の周囲をリアルタイムで学習し、対応することができます.
- 現代のエンドのフェクターは、グリッパー、吸引カップ、および特殊なツールなど、特定の産業用途に適したさまざまな形態で来ています.
- 未来のトレンドは、適応型および生体を刺激するエンドフェクターへのシフトを示し、ダイナミックな環境における効率と精度を向上させることを約束します.
- 先進的なエンド・フェクターを搭載したコラボレーションロボット(コボット)は、人間ロボットの相互作用と生産性を高めることで、職場を変革しています.
ロボティクスにおけるエンドエフェクトの起源
初期設計とアプリケーション
ロボティクスの初期には、エンド・フェクターは、繰り返しのタスクを実行するように設計された簡単な機械的ツールでした。 これらのデバイスは、しばしば人手を模倣したが、近代的なデザインで見ているフィネスと適応性が欠けていました。 工場は、主にグリップオブジェクト、溶接、または部品を組み立てるような作業のために使用しました。 組み立てラインなどの構造化された環境で、精度と一貫性がパラマウントされたアセンブリラインなど、構造化された環境で信頼性のあるデザインです.
エンドフェクターの最も早いアプリケーションの一つが製造に登場しました。 これらのツールを搭載したロボットは、労力集中プロセスを自動化することにより、業界に革命をもたらしました。 たとえば、基本的なグリッパーを持つロボットアームは、重い材料を処理することができ、労働者の物理的な負担を軽減します。 このイノベーションは、効率性の向上だけでなく、より高度なロボットシステムのためのステージを設定します.
しかし、これらの初期設計は制限されていました。 農業分野やヘルスケアの設定など、未構造の環境に適応するのに苦労しました。 たとえば、デリケートな果実を収穫する際には、初期のエンドフェクターが提供できないレベルのケアが必要です。 シンプルさにもかかわらず、これらのツールは、ロボティックエンドのフェクターと関連した多様な機能の基礎を築きました.
早期終了効果の課題と限界
初期のエンド・フェクターが大きな進歩を遂げながら、多くの課題に直面しました。 繊細で不規則な形状の物体を処理する能力を制限した硬質設計。 壊れないガラスを拾うために、基本的なグリッパーでロボットアームにとっていかに難しいかを想像できます。 この多様性の欠如は、特定の業界やタスクへの使用を制限しました.
もう一つの大きな制限は、動的または予測不可能な環境で動作することができないものでした。 たとえば、農業では、ロボットは不均一な地形をナビゲートし、果物のようなソフトで永続的な製品と相互作用する必要があります。 このようなタスクに必要な感度と適応性が欠けている早期のエンドのフェクター。 このギャップは、より洗練されたデザインの必要性を強調しました.
また、これらのツールは、基本的なタスクを実行するための広範なプログラミングが必要であることが多いです。 高度なセンサーや人工知能がなければ、周囲の変化に調整できません。 この剛性率は、柔軟性と迅速な意思決定が不可欠だったシナリオでは、効率が低下しました.
これらの課題にもかかわらず、エンドフェクターの早期開発はロボティクスの重要なステップをマークしました。 人によって伝統的に行われるタスクを実行する機械の可能性を実証しました。 これらの限界に対処し、ロボティック・アプリケーションの範囲を拡大するイノベーションの考え方を明らかにした.
エンド・フェクター・デザインにおける技術開発
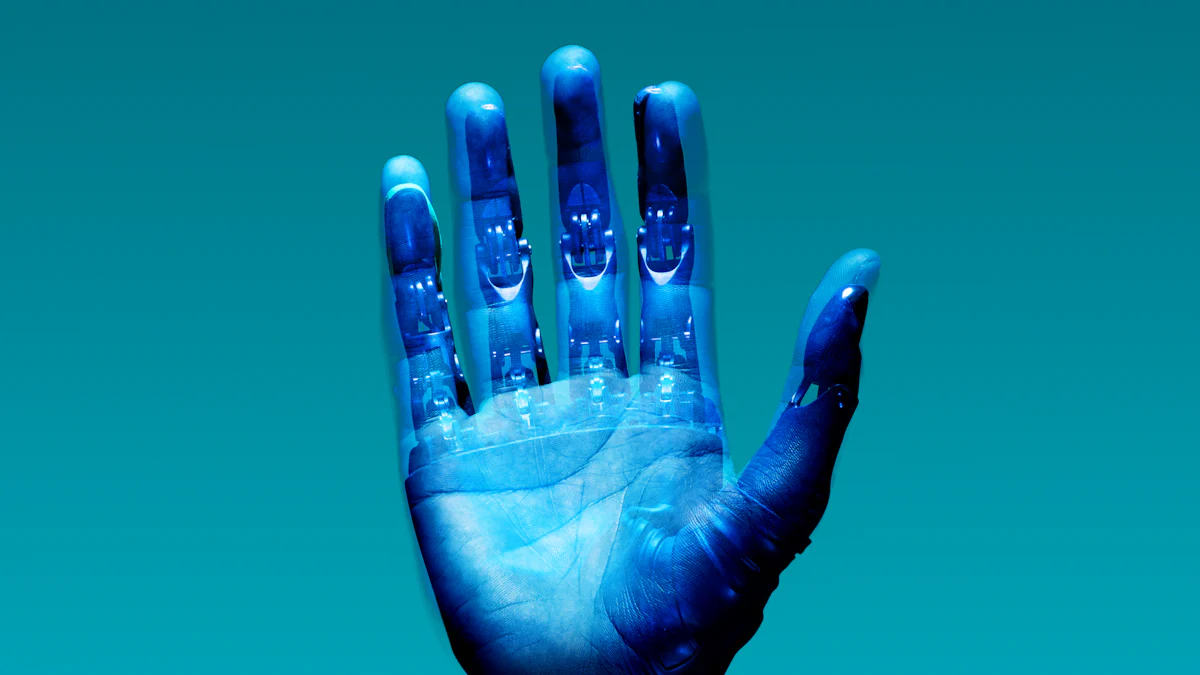
テクノロジーの進化は、エンド・フェクターの機能を変え、より多様で複雑なタスクを処理する能力を発揮しました。 これらの進歩は、アプリケーションを拡張するだけでなく、ヘルスケア、農業、製造などの産業で実現できるロボットを再定義しています.
素材イノベーションとソフトロボティクス
マテリアルサイエンスは、エンドフェクター設計の進歩に重要な役割を果たしています。 繊細な形状や不規則な形状のオブジェクトを処理する能力を制限する硬質材料に頼る従来のエンドのフェクター。 今日は、エンジニアは高度な材料を好みます エラストマー そして 形状記憶合金 ソフトなロボットエンドのフェクターを作る。 これらの材料は、ロボットが人間の手の柔軟性と感性を模倣することを可能にします.
ソフトロボティクスは、精度とケアが必要な業界に革命を起こしています。 たとえば、農業では、柔らかいグリッパーは、ダメージを起こさないで壊れやすい果実を収穫できるようになりました。 同様に、医療では、ソフトエンドのフェクターを搭載したロボットアームは、比類のない繊細さで組織を処理することによって手術を支援します。 これらのイノベーションは、従来のロボットシステムでは不可能だったアプリケーションにドアを開けました.
ロボティックな収穫操作に関する研究によると、軟端効果器の実装は、果実摘みや選別などの作業の効率性と精度を大幅に向上させました。 素材のイノベーションがロボット能力の限界を押し続けることを示しています.
精密・高機能化
ロボットが複雑なタスクを実行するためには、精度とデキステリティーが不可欠です。 初期のエンドのフェクターは、そのような操作に必要なフィネスを欠かしました。 しかし、現代のデザインは、その制御と動きを高める高度なメカニズムを組み込んでいます。 人間の手で触発されたマルチフィンガーのグリッパーは、ロボットが例外的な精度でオブジェクトを操作できるようにします.
エレクトロニクス製造のような産業は、これらの進歩から非常に利益をもたらします。 精密エンドフェクターを搭載したロボットは、小さなコンポーネントを組み立て、一貫性を確保し、エラーを減らすことができます。 医療分野では、強化されたデキステリティーを備えたロボットアームは、最小限の侵襲手術を実行し、患者は回復時間を短縮し、リスクを削減します.
これらの改善は、精度が非交渉可能である環境でロボットを不可欠にする方法を見ることができます。 ロボットが微細なモータースキルを要求するタスクを処理できるようにすることで、強化されたエンド・フェクターは近代的な自動化の礎となりました.
AIとセンサー技術の融合
人工知能(AI)とセンサー技術は、エンドフェクターを新しいレベルの社会化に取組んでいます。 エンドフェクターに埋め込まれたセンサーは、ロボットが周囲に適応できるように、リアルタイムのフィードバックを提供します。 たとえば、フォースセンサーは、ロボットがグリップ強度を調整し、脆弱なアイテムをクラッシュさせないようにします.
AIは、ロボットが時間をかけて学習し改善できるようにすることで、これらの機能をさらに増幅させます。 機械学習アルゴリズムは、センサーからデータを分析し、ロボットが環境の変化を予測し、対応できるようにします。 AIとセンサーの融合により、エンドフェクターがよりスマートで自律的に実現しました.
世界的なロボットエンドフェクター市場に関するレポートでは、AI統合ソリューションの需要が高まっています。 自動車やヘルスケアなどの産業は、複雑なプロセスを自動化し、効率性を向上させるために、これらの技術に依存しています.
サイズや重量の異なるパッケージをソートする倉庫でロボットを想像してみてください。 AIとセンサーで、各パッケージを識別し、適切なグリップを決定し、人間の介入なしに、正しい位置に配置することができます。 適応性のこのレベルは、スマートエンドエフェクトの変革の可能性を示しています.
エンドエフェクトの現在の状態
ロボティクスの世界は、エンド・フェクターが単なるツールではなく、自動化のバックボーンであるという点に辿り着きました。 これらのデバイスは、よりスマートで、より汎用性があり、想像できないようなタスクを実行することができます。 現代のエンド・フェクター、業界におけるアプリケーション、そしてそれらを設計するチャレンジの種類を見てみましょう.
現代のエンドエフェクトの種類
現代のエンドのフェクターは、特定のタスクに合わせて、さまざまな形態で来ます。 最も一般的なタイプは次のとおりです
- グリッパー: : : これらは、オブジェクトの選択と配置のために広く使用されています。 シンプルな2フィンガーデザインから、人間の手を動かす先進的なマルチフィンガーモデルまで幅広く展開しています.
- 吸引カップ: 平らなか滑らかな表面を扱うための理想、吸引のコップは包装および兵站学の企業で一般に使用されます.
- 磁気エンド エフェクト: : : これらは、特に高速組立ラインで金属物を扱うのに最適です。 工具の複雑さを軽減し、精度を向上させます.
- 加工ツール: : : これらは、製造工程で不可欠である溶接トーチ、切削工具、塗装ノズルを含みます.
- 専門化されたエンド エフェクト: 医療や農業の道具を収穫するなど、ユニークな作業のために設計されています.
各タイプのエンドフェクターは、ロボットシステムの効率性と精度を向上させる上で重要な役割を果たしています。 たとえば、磁気エンドフェクターは、エラーを減らし、アセンブリプロセスをスピードアップすることにより、白物の製造における動作を合理化します.
各種産業用途
エンド・フェクターは、ロボットが比類のない精度とスピードでタスクを実行できるようにすることで、業界に革命をもたらしました。 ここにある主要な適用です:
- 自動車産業: エンド・フェクターが溶接、アセンブリおよび材料の処理の仕事を処理する装備されているロボット。 これは、自動車メーカーのためのゲームチェンジャーであり、彼らはより速く、より大きな一貫性で車を生産することができます.
- ヘルスケア: : : 外科では、専門にされた端のEffectorsが付いているロボティック腕は安定した、精密な動きを提供することによって医者を助けます。 これにより、リスクを削減し、患者の結果を改善します.
- 農業農業: : : ダメージを起こさずに、繊細な果実を収穫し、労力不足の課題に対処し、生産性を高めます.
- エレクトロニクス製造: 多フィンガーのグリッパーが付いているロボットは小さい部品を組み立て、高精度および欠陥を減らすことを保障します.
- 物流と倉庫: 吸引カップとグリッパーは、パッケージを効率的にソートして移動し、サプライチェーン業務をスピードアップします.
これらのアプリケーションは、エンド・フェクターが多様な環境に適応し、現代の産業に欠かせないものであることを強調しています.
現代のエンドエフェクトにおけるデザイン課題
彼らの進歩にもかかわらず、現代のエンド・フェクターの設計は、独自の課題のセットが付属しています。 1つの大きな問題は、専門性で汎用性のバランスをとることです。 一部の業界には、高度に専門性の高いツールが必要ですが、複数のタスクを処理することができる他の要求の適応可能な設計.
センサーやAIなどの先端技術を統合するチャレンジです。 機能性を高めながら、複雑さとコストも向上します。 たとえば、グリッパーに力センサーを埋め込むと、精度が向上しますが、細心のキャリブレーションとメンテナンスが必要です.
耐久性は別の懸念です。 エンド スペクターは性能を妥協することなく、極端な温度や腐食性環境などの過酷な条件に耐える必要があります。 エンジニアは、軽量で堅牢な材料を選ぶの困難な作業に直面しています.
最後に、異なるロボットシステムとの互換性を確保することで、複雑さの別のレイヤーを追加します。 メーカーは、さまざまなロボットとシームレスに統合できるエンド・フェクターを設計しなければなりません。これはしばしばユニークな仕様を持っています.
自動化の需要が高まるにつれて、これらの課題を克服することは、エンド・フェクターの継続的な進化にとって不可欠です。 これらの課題に取り組むことで、技術者は、業界を横断するロボティクスの可能性を広げることができます.
エンドフェクターの将来のトレンド
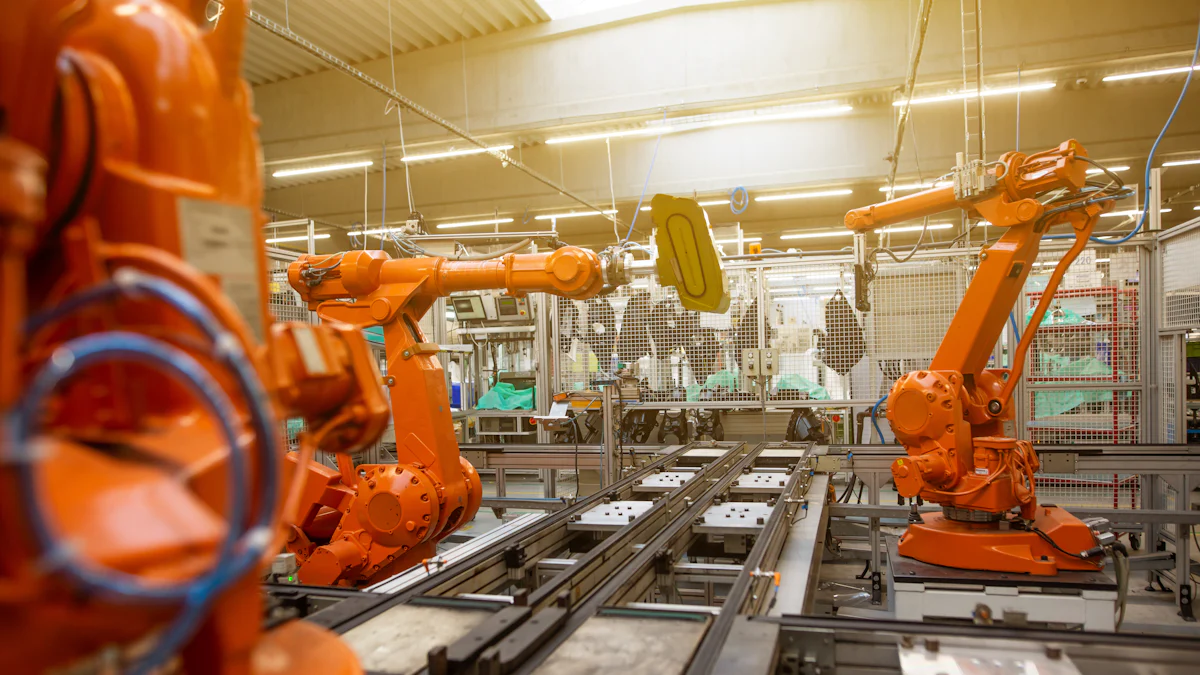
ロボットの未来は、エンド・フェクターの継続的な進化にあります。 これらのツールは、より賢く、より適応性があり、人間と一緒に作業することができるようになりました。 業界は、より効率的な精度が求められ、次世代のエンド・フェクターは、どのようなロボットが達成できるかを再定義することを約束します.
適応性とインテリジェントなエンドエフェクト
握っているオブジェクトに基づいてグリップ強度を調整するロボットアームを想像してみてください。 アダプティブ・エンド・フェクターはこの現実を成し遂げています。 これらのツールは、統合センサーと人工知能を使用して、環境を分析し、リアルタイムで応答します。 たとえば、フォースセンサーは、ロボットが壊れずにガラス製品のような壊れやすい物を扱うことを可能にします。 AIアルゴリズムにより、これらのエンド・フェクターが過去のインタラクションから学習し、パフォーマンスを向上させることができます.
研究内容 エンド・フェクター開発における将来のトレンド 適応性の向上の重要性を強調します。 スマートテクノロジーとタッチ感度は、次のロボットツールの波を形作ります.
適応型エンドフェクターは、動的環境で優れています。 倉庫では、人間の介入を最小限に抑えて、さまざまなサイズと重量のパッケージをソートできます。 医療では、彼らは人間の組織の繊細な性質に自分の動きを調整することによって、手術を支援します。 これらの進歩は、効率性を高めるだけでなく、以前に考えられなかったアプリケーションへの扉を開くだけでなく、.
バイオインスパイアとソフトロボティクス
自然は革新のためのインスピレーションの源常にありました。 バイオインスパイアされたエンドフェクターは、生物学的リムスの柔軟性と機能性を模倣します。 エンジニアは、人手やオクトープの触手の吸引能力のデキステリティーを再現するツールを設計しています。 これらのデザインは、比類のない汎用性と精度を提供します.
ソフトロボティクスは、このトレンドにおいて重要な役割を果たしています。 従来の堅い用具とは違って、柔らかさのエンド フェルトは材料をのような使用します エラストマー 不規則な形に合わせるため。 農業や臓器の果物などのデリケートな物品を扱うのに理想的です.
研究によると、ソフトなロボティックグリッパーは、果実の収穫などの作業で大幅に改善しました。 ダメージなしで脆弱なアイテムを処理する能力は、バイオインスパイアされたデザインの可能性を示しています.
先端材料とバイオインスパイアされた原則を組み合わせることで、これらのエンド・フェクターは、ロボットができることの限界を押しています。 それらは単なるツールではなく、ロボットシステムの拡張であり、人間のような精度でタスクを実行することができます.
連携ロボティクスと人間ロボットの相互作用
コラボレーションロボットやコボットの立ち上がりは、職場を変革しています。 これらのロボットは、人と一緒に働き、生産性と安全性を高めます。 エンド・フェクターは、このコラボレーションで重要な役割を果たしています。 人間と機械のシームレスなやりとりを確保し、安全、直感的、そして応答性を実現するように設計されています.
たとえば、エンドフェクターの触覚センサーは人間のタッチを検出し、ロボットがアクションを一時停止または調整できるようにします。 労働者やロボットが同じ空間を共有するような環境では、この特徴が重要である。 専用グリッパーは、複雑なコンポーネントを組み立てるなど、高い精度を必要とするタスクを実行するために、コボットを有効にします.
適応型グリッパーとAI主導のエンドフェクターの統合は、市場ダイナミクスを積極的に影響しています。 これらのイノベーションは、業界全体でコラボレーションロボティクスをよりアクセス可能にしています.
人間ロボットの相互作用は、安全性だけでなく、相乗関係です。 先進技術を搭載したエンド・フェクターは、ロボットが人間のスキルを補完することを可能にします。 重い物体を持ち上げたり、反復タスクを実行している場合でも、これらのツールは、ロボットと人間の対向の両方の機能を強化します.
エンドフェクターの旅は、ロボットが簡単な機械的なツールから高度にインテリジェントなシステムに進化してきた方法を示しています。 これらの装置は、ロボットを多様な機械に変形させ、業界を横断する複雑なタスクや多様なタスクを実行できます。 技術の進歩として、エンド・フェクターはオートメーションを再定義し、ロボットがより精密で適応性のある課題に取り組むことを可能にします。 ロボットと環境のインターフェイスとしての役割は欠かせません。 未来のイノベーションを実践することで、世界中の産業を再構築しながら、新たな可能性を享受し、効率性と生産性を発揮するエンド・フェクターが期待できます.