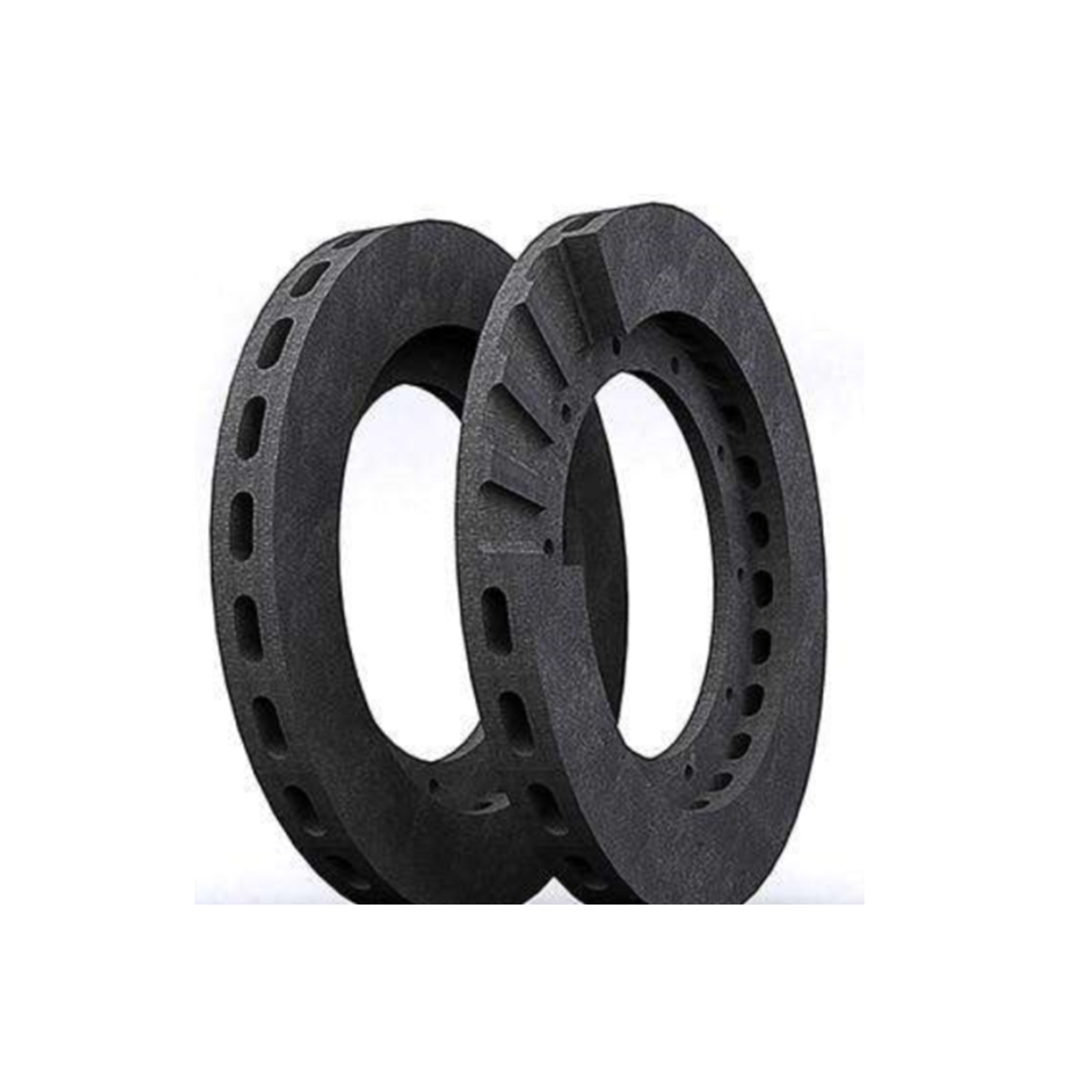
炭素繊維複合材料 parts have revolutionized modern manufacturing due to their exceptional properties. These materials combine lightweight construction with remarkable strength, making them indispensable in industries such as aerospace, automotive, and sports equipment. Their high strength-to-weight ratio enhances fuel efficiency in vehicles and aircraft, aligning with global sustainability goals. Additionally, カーボンカーボンコンポジット materials exhibit superior durability and resistance to corrosion, ensuring long-lasting performance in demanding environments. As the market for these advanced materials grows, their applications continue to expand, solidifying their role as a cornerstone of innovation in engineering and design.
要点
- Carbon fiber composites are lightweight yet incredibly strong, making them essential in industries like aerospace and automotive for improved fuel efficiency and performance.
- Selecting the right materials, such as carbon fiber fabric and resin systems, is crucial for ensuring the strength and durability of the final product.
- Proper mold preparation, including cleaning and applying release agents, is vital to prevent defects and ensure a smooth finish on composite parts.
- Utilizing advanced manufacturing methods like prepreg lamination and resin transfer molding (RTM) enhances precision and quality in carbon fiber production.
Materials and Tools Required for Carbon Fiber Composite Manufacturing
Creating high-quality carbon fiber composite parts requires a combination of specialized materials and tools. Each component plays a critical role in ensuring the strength, durability, and precision of the final product. Below is a detailed breakdown of the essential materials and necessary tools for this process.
Essential Materials
Carbon fiber fabric (woven or unidirectional)
Carbon fiber fabric serves as the foundation of composite manufacturing. Woven fabrics provide balanced strength in multiple directions, making them suitable for general applications. Unidirectional fabrics, on the other hand, offer enhanced strength along a single axis, ideal for specific load-bearing components. Selecting the right type of fabric depends on the intended application and performance requirements.
Resin systems (epoxy, polyester, or vinyl ester)
Resin systems act as the binding agent that holds the carbon fibers together. Epoxy resin is widely preferred due to its superior strength, chemical resistance, and durability. Polyester and vinyl ester resins are also used for cost-effective solutions in less demanding applications. Proper resin selection ensures optimal bonding and structural integrity.
Mold release agents
Mold release agents prevent the composite part from sticking to the mold during the curing process. These agents simplify demolding and reduce the risk of surface defects. High-quality release agents, such as waxes or sprays, ensure a smooth finish and protect the mold for repeated use.
Core materials (e.g., foam or honeycomb) for structural reinforcement
Core materials like foam or honeycomb structures enhance the stiffness and strength of composite parts without adding significant weight. These materials are commonly used in aerospace and automotive industries to achieve lightweight yet robust components.
Necessary Tools
Molds (custom or pre-made)
Molds define the shape and dimensions of the composite part. Custom molds are tailored for specific designs, while pre-made molds offer convenience for standard shapes. High-quality molds ensure precision and consistency in the manufacturing process.
Brushes, rollers, and squeegees
These tools are essential for applying resin evenly across the carbon fiber layers. Brushes allow for detailed application, rollers help distribute resin smoothly, and squeegees remove excess resin to prevent pooling. Proper use of these tools ensures uniform resin distribution, which is crucial for the strength of the composite.
Vacuum bagging equipment
Vacuum bagging equipment removes air pockets and compresses the carbon fiber layers during the curing process. This technique enhances the structural integrity of the composite by eliminating voids and ensuring even resin impregnation. It is particularly important for achieving professional-grade results.
Heat sources (e.g., ovens or autoclaves)
Heat sources like ovens or autoclaves are used to cure the composite part. Controlled heat and pressure accelerate the curing process, resulting in a stronger and more durable product. Autoclaves are often preferred for high-performance applications due to their ability to maintain precise temperature and pressure conditions.
Safety gear (gloves, goggles, respirators)
Safety gear protects workers from potential hazards associated with resin handling and carbon fiber dust. Gloves prevent skin contact with chemicals, goggles shield the eyes, and respirators ensure safe breathing in environments with airborne particles. Prioritizing safety minimizes health risks and ensures a secure workspace.
“High-quality tools and materials are the backbone of successful carbon fiber composite manufacturing. Investing in the right equipment not only improves efficiency but also guarantees superior results.”
By combining these materials and tools, manufacturers can produce carbon fiber composite parts that meet the highest standards of performance and reliability. Proper preparation and attention to detail at this stage lay the foundation for a successful manufacturing process.
Preparation Steps for Carbon Fiber Composite Manufacturing
Proper preparation is essential to ensure the success of carbon fiber composite manufacturing. This stage lays the groundwork for achieving high-quality results by focusing on mold readiness and safety measures. Below are the key steps to follow.
Mold Preparation
Cleaning and polishing the mold surface
A clean mold surface ensures a flawless finish for the composite part. Dust, grease, or residue can cause imperfections, so thorough cleaning is critical. Use a lint-free cloth and a suitable cleaning agent to remove contaminants. Polishing the mold enhances its smoothness, which directly impacts the surface quality of the final product. For simple parts like car components or theatrical props, this step can be completed quickly and cost-effectively.
Applying mold release agents to prevent sticking
Mold release agents act as a barrier between the mold and the composite material. Apply a thin, even layer of the release agent using a brush or spray. This prevents the composite part from adhering to the mold during curing. High-quality release agents reduce the risk of defects and simplify the demolding process. Consistent application ensures the mold remains reusable for multiple production cycles.
“Attention to mold preparation not only improves the quality of the composite part but also extends the lifespan of the mold.”
Safety Precautions
Ensuring proper ventilation in the workspace
Resin systems and other chemicals used in composite manufacturing can emit harmful fumes. A well-ventilated workspace minimizes exposure to these substances. Install exhaust fans or use fume extraction systems to maintain air quality. Proper ventilation protects workers and ensures compliance with safety regulations.
Wearing appropriate personal protective equipment (PPE)
Personal protective equipment shields workers from potential hazards. Gloves protect the skin from resin and chemicals, while goggles safeguard the eyes from splashes. Respirators prevent inhalation of harmful fumes or carbon fiber dust. Always select PPE that meets industry standards to ensure maximum protection.
Handling resins and chemicals safely to avoid health risks
Resins and chemicals require careful handling to prevent accidents. Store these materials in labeled containers and follow the manufacturer’s guidelines for use. Avoid direct contact with skin and eyes. Dispose of waste materials responsibly to minimize environmental impact. Training workers on safe handling practices reduces risks and promotes a secure working environment.
“Prioritizing safety not only protects workers but also enhances productivity by reducing downtime caused by accidents.”
By following these preparation steps, manufacturers can create a solid foundation for producing high-performance carbon fiber composite parts. Proper mold preparation and adherence to safety precautions ensure a smooth and efficient manufacturing process.
Manufacturing Methods for Carbon Fiber Composite Parts
Manufacturing carbon fiber composite parts involves various methods, each tailored to specific applications and performance requirements. These techniques determine the quality, precision, and efficiency of the final product. Below is an exploration of three widely used methods: wet lay-up, prepreg lamination, and resin transfer molding (RTM).
Wet Lay-Up
Overview of the wet lay-up process
The wet lay-up method is one of the most straightforward techniques for manufacturing carbon fiber composites. In this process, manufacturers cut carbon fiber fabric to the desired shape and place it into a mold. Resin is then applied directly onto the fabric using brushes, rollers, or spray guns. Workers ensure even distribution of the resin by manually working it into the fibers. Once the layers are saturated, the composite is left to cure under ambient conditions or with the aid of heat.
This method is particularly suitable for creating simple parts that do not require high structural loads. It is often used in applications such as prototypes, decorative components, and non-critical automotive parts.
Advantages and limitations of this method
The wet lay-up process offers several advantages:
- 費用対効果: It requires minimal equipment, making it accessible for small-scale production.
- Flexibility: It allows for the creation of custom shapes and sizes without extensive tooling.
However, this method also has limitations:
- Inconsistent quality: Manual application of resin can lead to uneven distribution, affecting the strength of the composite.
- Limited precision: It is less suitable for high-performance applications requiring tight tolerances.
“The wet lay-up method remains a popular choice for its simplicity and affordability, despite its limitations in precision and consistency.”
Prepreg Lamination
Using pre-impregnated carbon fiber sheets for precision
Prepreg lamination involves the use of pre-impregnated carbon fiber sheets, where the fibers are already infused with a precise amount of resin. These sheets are stored at low temperatures to prevent premature curing. During the manufacturing process, the prepreg material is cut and layered into a mold. Heat and pressure are then applied to cure the composite, ensuring a high-quality finish.
This method is widely used in industries such as aerospace and automotive, where precision and performance are critical. For example, aircraft components often rely on prepreg materials to meet stringent safety and durability standards.
Benefits of prepreg materials, such as enhanced quality
Prepreg lamination offers several key benefits:
- Superior quality: The pre-impregnated resin ensures consistent fiber-to-resin ratios, resulting in stronger and more reliable composites.
- Enhanced precision: The controlled curing process minimizes defects and ensures uniformity across the part.
- Reduced waste: Prepreg sheets eliminate the need for excess resin, making the process more efficient.
Despite its advantages, this method requires specialized equipment, such as autoclaves, and is generally more expensive than wet lay-up. However, the investment is justified for applications demanding high performance and durability.
“Prepreg lamination sets the standard for precision and quality in carbon fiber composite manufacturing, making it indispensable for advanced engineering applications.”
Resin Transfer Molding (RTM)
How RTM works, including resin injection into molds
Resin transfer molding (RTM) is a closed-mold process that combines precision with efficiency. In this method, dry carbon fiber fabric is placed into a mold, which is then sealed. Resin is injected under pressure into the mold, saturating the fibers. The composite is cured within the mold, often with the application of heat.
RTM is particularly effective for producing complex shapes and large parts. It is commonly used in the automotive industry for manufacturing lightweight yet robust components, such as car body panels and structural reinforcements.
Applications and benefits of RTM for complex parts
RTM offers several advantages:
- High precision: The closed-mold system ensures accurate resin distribution, reducing the risk of voids and defects.
- 汎用性: It accommodates complex geometries and intricate designs, making it suitable for a wide range of applications.
- ソリューション: The process allows for faster cycle times compared to traditional methods, increasing production rates.
This method is ideal for industries requiring high-performance parts with intricate designs. For instance, RTM is frequently used in the production of wind turbine blades, where strength and aerodynamic efficiency are paramount.
“Resin transfer molding combines precision and efficiency, making it a preferred choice for manufacturing complex and high-performance carbon fiber composite parts.”
By understanding these manufacturing methods, businesses can select the most appropriate technique based on their specific needs and resources. Each method offers unique advantages, ensuring that carbon fiber composite parts meet the desired standards of quality and performance.
Other Techniques
Filament Winding for Cylindrical Parts
Filament winding stands out as a specialized technique for manufacturing cylindrical or tubular carbon fiber composite parts. This method involves winding continuous carbon fiber strands, pre-impregnated with resin, around a rotating mandrel. The fibers are strategically placed at specific angles to optimize strength and stiffness based on the part’s intended application. Once the winding process is complete, the composite undergoes curing, either at room temperature or with the application of heat, depending on the resin system used.
This technique is widely used in industries requiring high-performance cylindrical components. For example, aerospace engineers rely on filament winding to produce lightweight yet robust rocket motor casings. Similarly, the automotive sector uses this method to create drive shafts and pressure vessels, where durability and weight reduction are critical.
Advantages of Filament Winding:
- Precision in Fiber Placement: The automated nature of filament winding ensures consistent and accurate fiber alignment, enhancing the mechanical properties of the final product.
- Cost Efficiency for Cylindrical Shapes: This method minimizes material waste and reduces production time for tubular structures.
- 高い強度重量比: The ability to control fiber orientation allows manufacturers to achieve optimal strength with minimal weight.
However, filament winding is best suited for parts with simple geometries, such as cylinders or cones. Complex shapes may require alternative methods like resin transfer molding (RTM) or vacuum-assisted resin transfer molding (VARTM).
“Filament winding exemplifies precision and efficiency, making it indispensable for producing high-performance cylindrical carbon fiber components.”
Vacuum-Assisted Resin Transfer Molding (VARTM)
Vacuum-assisted resin transfer molding (VARTM) builds upon the principles of traditional resin transfer molding (RTM) but incorporates vacuum pressure to enhance resin flow and impregnation. In this process, dry carbon fiber fabric is laid into a mold, which is then sealed with a vacuum bag. The vacuum creates a pressure differential, drawing resin into the mold and saturating the fibers. This method ensures uniform resin distribution and eliminates air pockets, resulting in a high-quality composite part.
VARTM is particularly effective for manufacturing large, complex structures. For instance, the wind energy industry uses this technique to produce lightweight yet durable wind turbine blades. The automotive sector also benefits from VARTM for creating structural components that demand both strength and precision.
Key Benefits of VARTM:
- Enhanced Resin Flow: The vacuum-assisted process ensures thorough fiber impregnation, reducing voids and defects.
- Cost-Effective for Large Parts: VARTM eliminates the need for expensive autoclaves, making it a more economical choice for large-scale production.
- Environmental Advantages: This method generates less waste compared to traditional techniques, aligning with sustainable manufacturing practices.
Despite its advantages, VARTM requires meticulous preparation to ensure a proper vacuum seal and resin flow. Any errors during setup can compromise the quality of the final product.
“VARTM combines precision and cost-efficiency, offering a reliable solution for producing large and complex carbon fiber composite parts.”
By leveraging advanced techniques like filament winding and VARTM, manufacturers can expand the possibilities of carbon fiber composite production. These methods cater to specific applications, ensuring that each part meets the highest standards of performance and reliability.
Step-by-Step Process for Manufacturing Carbon Fiber Composite Parts
Manufacturing carbon fiber composite parts requires a systematic approach to ensure precision and durability. Each stage of the process plays a vital role in achieving a high-quality final product. Below is a detailed guide to the step-by-step process.
Layup Stage
Cutting and arranging carbon fiber layers in the mold
The process begins with cutting carbon fiber fabric into precise shapes and sizes. Manufacturers use templates or cutting tools to ensure accuracy. Proper alignment of the fibers is critical, as it directly impacts the strength and performance of the composite. Once cut, the layers are carefully arranged in the mold. This step requires attention to detail to avoid misalignment, which could compromise the structural integrity of the part.
“Accurate cutting and meticulous arrangement of carbon fiber layers form the foundation of a strong and reliable composite.”
Applying resin or using prepreg materials for bonding
After arranging the carbon fiber layers, resin application follows. For wet lay-up methods, workers apply resin using brushes, rollers, or spray guns, ensuring even distribution across the fibers. In contrast, prepreg materials already contain resin, simplifying this step. The resin acts as a binding agent, holding the fibers together and providing the composite with its characteristic strength. Proper resin application ensures uniform bonding and eliminates weak points.
Curing Stage
Vacuum bagging and sealing the part
Vacuum bagging enhances the quality of the composite by removing air pockets and compressing the layers. Workers place the mold inside a vacuum bag, seal it tightly, and connect it to a vacuum pump. The vacuum pressure consolidates the layers, ensuring even resin impregnation. This step is essential for achieving a defect-free composite with optimal mechanical properties.
Applying heat and pressure (e.g., in an autoclave) for curing
Curing solidifies the composite, transforming it into a durable and stable structure. Heat and pressure accelerate the curing process, often performed in an autoclave for high-performance applications. The controlled environment ensures consistent temperature and pressure, resulting in a composite with superior strength and durability. For simpler parts, ovens or ambient conditions may suffice, depending on the resin system used.
“Vacuum bagging and precise curing conditions are crucial for producing composites that meet industry standards.”
Finishing Stage
Trimming and sanding the part for precision
Once cured, the composite part undergoes trimming and sanding to achieve the desired shape and dimensions. Excess material is removed using cutting tools, while sanding smooths the edges and surfaces. This step ensures that the part meets the required specifications and fits seamlessly into its intended application.
Applying protective coatings or paint for durability
The final step involves applying protective coatings or paint to enhance the part’s durability and appearance. Coatings protect the composite from environmental factors such as UV radiation, moisture, and chemicals. Paint adds aesthetic value, making the part visually appealing. This finishing touch ensures the composite is ready for use in demanding environments.
“Finishing transforms a raw composite into a polished and functional component, ready to excel in its application.”
By following these steps, manufacturers can produce carbon fiber composite parts that meet the highest standards of quality and performance. Each stage, from layup to finishing, contributes to the creation of reliable and durable components.
Tips and Best Practices for High-Quality Carbon Fiber Composite Parts
Achieving excellence in manufacturing carbon fiber composite parts requires attention to detail and adherence to proven techniques. This section provides actionable tips and highlights common pitfalls to help manufacturers produce superior components.
Achieving High-Quality Results
Ensuring even resin distribution during layup
Uniform resin distribution is critical for the structural integrity of carbon fiber composites. Uneven application can lead to weak spots, compromising the part’s performance. Manufacturers should use tools like brushes, rollers, or squeegees to spread resin evenly across the carbon fiber layers. Vacuum bagging further enhances resin impregnation by eliminating air pockets and ensuring consistent bonding. For prepreg materials, maintaining proper storage conditions prevents premature curing, ensuring optimal resin flow during the layup process.
“Consistency in resin application directly impacts the strength and durability of the final product.”
Avoiding air bubbles to maintain structural integrity
Air bubbles trapped within the composite can weaken its structure and reduce its lifespan. To prevent this, manufacturers should employ vacuum-assisted techniques during the curing process. Properly sealing the vacuum bag and monitoring pressure levels ensures that air pockets are removed effectively. Additionally, careful handling of resin and fibers during layup minimizes the introduction of air into the material. These practices result in a defect-free composite with enhanced mechanical properties.
Common Mistakes to Avoid
Skipping mold preparation steps, leading to defects
Neglecting mold preparation often results in surface imperfections and adhesion issues. Dust, grease, or residue on the mold can transfer to the composite, affecting its appearance and performance. Manufacturers must clean and polish the mold thoroughly before applying a mold release agent. Consistent application of the release agent ensures easy demolding and protects the mold for repeated use. Skipping these steps can lead to costly rework and wasted materials.
“Proper mold preparation is a non-negotiable step for achieving flawless composite parts.”
Using incorrect resin-to-fiber ratios, affecting strength
The resin-to-fiber ratio plays a pivotal role in determining the composite’s strength and weight. Excess resin adds unnecessary weight without improving strength, while insufficient resin leads to weak bonding. Manufacturers should follow precise measurements and guidelines provided by resin suppliers. For example, using pre-impregnated carbon fiber sheets simplifies this process by ensuring an optimal resin-to-fiber ratio. Adhering to these standards guarantees a balanced and high-performance composite.
Applications of Carbon Fiber Composite Parts
Carbon fiber composite parts have transformed various industries by offering lightweight, durable, and high-performance solutions. Their versatility and strength-to-weight ratio make them indispensable in sectors where efficiency and reliability are paramount. Below are some of the most prominent applications.
航空宇宙産業
Lightweight components for aircraft to improve fuel efficiency
The aerospace industry relies heavily on carbon fiber composite parts to enhance aircraft performance. These materials reduce the overall weight of aircraft, which directly improves fuel efficiency and reduces operational costs. For example, carbon fiber is used in constructing fuselages, wings, and tail sections. Its ability to withstand extreme conditions while maintaining structural integrity makes it ideal for aviation.
“Close control is required to ensure consistent quality,” as emphasized by experts in carbon fiber manufacturing. This precision ensures that aerospace components meet stringent safety and performance standards.
Lightweight materials also contribute to increased payload capacity, allowing airlines to transport more passengers or cargo without compromising efficiency. The durability of carbon fiber composites ensures long service life, reducing maintenance costs and downtime.
自動車産業
High-performance car parts for speed and durability
In the automotive sector, carbon fiber composite parts have revolutionized vehicle design and performance. Manufacturers use these materials to create lightweight yet robust components such as body panels, chassis, and drive shafts. The reduced weight enhances acceleration, braking, and fuel efficiency, making vehicles more agile and environmentally friendly.
High-performance sports cars, for instance, often feature carbon fiber-reinforced parts to achieve superior speed and handling. The material’s durability ensures that these components can withstand the stresses of high-speed driving and harsh conditions.
“Talk to the experts” when selecting carbon fiber composites for automotive applications. Expert guidance ensures the right materials and techniques are used to meet specific performance requirements.
Additionally, carbon fiber’s aesthetic appeal adds a premium look to vehicles, making it a popular choice for luxury and performance car manufacturers.
Sports Equipment
Durable and lightweight gear for athletes
Athletes benefit significantly from the use of carbon fiber composite parts in sports equipment. The material’s lightweight nature reduces fatigue, allowing athletes to perform at their best for longer periods. For example, tennis rackets, bicycles, and golf clubs made from carbon fiber offer enhanced precision and power due to their reduced weight and increased stiffness.
Durability is another key advantage. Carbon fiber composites resist wear and tear, ensuring that sports equipment maintains its performance over time. This reliability is crucial for professional athletes who demand consistency in their gear.
“Reduced surgical fatigue,” a benefit noted in medical applications of carbon fiber, parallels its impact in sports. Lightweight equipment minimizes physical strain, enabling athletes to focus on their performance.
From cycling to rowing, carbon fiber’s adaptability allows manufacturers to design equipment tailored to the specific needs of each sport. This customization enhances the athlete’s experience and competitive edge.
By integrating carbon fiber composite parts into these industries, manufacturers achieve unparalleled performance, efficiency, and durability. The material’s unique properties continue to drive innovation, setting new standards across aerospace, automotive, and sports sectors.
Environmental Considerations in Carbon Fiber Composite Manufacturing
The growing demand for carbon fiber composites in industries such as aerospace and automotive has brought attention to the environmental impact of their production. While these materials offer exceptional performance benefits, addressing sustainability challenges is essential for long-term growth and environmental responsibility.
Recycling Carbon Fiber Composites
Challenges in recycling and potential solutions
Recycling carbon fiber composites presents significant challenges due to the complexity of their structure. Unlike metals, which can be melted and reused, carbon fiber composites consist of fibers embedded in a resin matrix. Separating these components without degrading the fibers requires advanced techniques.
One major challenge lies in the energy-intensive recycling processes. Pyrolysis, a common method, involves heating the composite to high temperatures to burn off the resin and recover the fibers. This process consumes substantial energy and may release harmful emissions. Additionally, the recovered fibers often lose some mechanical properties, limiting their reuse in high-performance applications.
“The carbon fiber market is projected to grow from USD 3.31 billion in 2023 to USD 7.05 billion by 2032, highlighting the urgency of developing efficient recycling methods.”
To address these challenges, researchers are exploring innovative solutions. Chemical recycling, for instance, uses solvents to dissolve the resin without damaging the fibers. This method preserves the quality of the fibers, making them suitable for reuse in demanding applications. Another promising approach involves mechanical recycling, where composites are shredded into smaller pieces for use in non-structural applications, such as automotive interiors or construction materials.
Collaboration between manufacturers, researchers, and policymakers is crucial to advancing recycling technologies. By investing in sustainable practices, the industry can reduce waste and minimize its environmental footprint.
Sustainable Manufacturing Practices
Reducing waste and emissions during production
Sustainable manufacturing practices play a vital role in minimizing the environmental impact of carbon fiber composite production. The manufacturing process often generates significant waste, including excess resin, offcuts of carbon fiber fabric, and defective parts. Implementing waste reduction strategies can improve efficiency and sustainability.
One effective strategy involves optimizing material usage. Advanced software tools enable manufacturers to design components with minimal waste by precisely calculating the required amount of carbon fiber and resin. Automated cutting machines further reduce material waste by maximizing the use of each fabric sheet.
“Carbon fiber is approximately 1.5x lighter than aluminum, making it ideal for lightweight applications in aerospace and automotive sectors. However, reducing production waste ensures its environmental benefits outweigh its manufacturing impact.”
Energy consumption during production also contributes to emissions. Autoclaves, commonly used for curing composites, require high energy input. Manufacturers can adopt alternative curing methods, such as out-of-autoclave (OOA) techniques, which use lower temperatures and pressures. These methods not only reduce energy consumption but also lower production costs.
Recycling production waste offers another avenue for sustainability. For example, offcuts of carbon fiber fabric can be repurposed into non-structural components or blended with other materials to create hybrid composites. This approach reduces the need for virgin materials and diverts waste from landfills.
“The global carbon fiber composites market is expected to reach USD 39.39 billion by 2034, driven by demand for lightweight and high-strength materials. Sustainable practices will ensure this growth aligns with environmental goals.”
By adopting these practices, manufacturers can align their operations with sustainability objectives while maintaining the performance advantages of carbon fiber composites. The industry’s commitment to reducing waste and emissions will play a pivotal role in shaping a greener future.
Why Choose Ningbo VET Energy Technology Co. for Carbon Fiber Composite Manufacturing
Expertise and Innovation
Advanced materials and tools for superior results
Ningbo VET Energy Technology Co. stands at the forefront of carbon fiber composite manufacturing. The company employs cutting-edge materials and state-of-the-art tools to deliver exceptional results. By utilizing advanced resin systems and high-performance carbon fiber fabrics, they ensure that every product meets rigorous industry standards. Their commitment to innovation drives the development of lightweight, durable, and high-strength components tailored for demanding applications.
The company’s expertise extends to integrating modern manufacturing techniques such as vacuum-assisted resin transfer molding (VARTM) and prepreg lamination. These methods enhance precision and efficiency, ensuring consistent quality across all products. For example, their use of VARTM minimizes material waste while maintaining structural integrity, aligning with sustainable production practices. This approach not only reduces costs but also supports environmentally conscious manufacturing.
“Recycled carbon fibers offer an improved CO2 footprint compared to virgin fibers,” highlighting the importance of sustainable practices. Ningbo VET Energy Technology Co. incorporates such advancements to meet both performance and environmental goals.
Customized solutions for diverse applications
Ningbo VET Energy Technology Co. excels in providing tailored solutions to meet the unique needs of various industries. Whether it’s aerospace, automotive, or sports equipment, the company designs and manufactures components that align with specific performance requirements. For instance, their lightweight carbon fiber parts enhance fuel efficiency in vehicles and aircraft, addressing the growing demand for sustainable transportation solutions.
The company’s ability to customize extends to creating complex geometries and intricate designs. By leveraging advanced techniques like resin transfer molding (RTM), they produce components with precise dimensions and superior mechanical properties. This versatility makes them a trusted partner for clients seeking innovative solutions in high-performance applications.
“The automotive segment is expected to witness significant growth in the carbon fiber composites market.” Ningbo VET Energy Technology Co. positions itself as a leader in this expanding market by offering cost-effective and high-quality solutions.
Contact Information
Address: No. 777, Zhongguan West Road, Zhenhai District, Ningbo, Zhejiang, 315201, China
Phone: 86-1891 1596 392
Email: yeah@china-vet.com
Website: 寧波VETエネルギー技術有限公司
For inquiries or to learn more about their services, reach out to Ningbo VET Energy Technology Co. Their team of experts is ready to assist with your carbon fiber composite manufacturing needs.
Manufacturing carbon fiber composite parts demands meticulous preparation, high-quality materials, and a thorough understanding of the process. By adhering to the outlined steps and implementing best practices, manufacturers can achieve durable, high-performance components suitable for diverse applications.
Ningbo VET Energy Technology Co. provides advanced materials and innovative solutions tailored to meet industry-specific needs. Their expertise in high-end materials and cutting-edge manufacturing techniques ensures exceptional results. For reliable and efficient carbon fiber composite production, contact Ningbo VET Energy Technology Co. today to explore their comprehensive offerings.
よくあるご質問
What are carbon fiber composites, and why are they widely used?
炭素繊維複合材料 combine carbon fibers with a polymer matrix to create materials that are lightweight yet exceptionally strong. These composites offer a high strength-to-weight ratio, making them ideal for industries like aerospace, automotive, and sports equipment. Their durability, corrosion resistance, and ability to withstand extreme conditions further enhance their appeal.
“Carbon fiber composites have revolutionized modern manufacturing by offering unmatched performance and versatility,” as highlighted by industry experts.
What industries benefit the most from carbon fiber composite parts?
Several industries rely heavily on carbon fiber composite parts:
- エアロスペース: Lightweight components improve fuel efficiency and reduce operational costs.
- 自動車産業: High-performance parts enhance speed, durability, and fuel economy.
- Sports Equipment: Durable and lightweight gear improves athletic performance.
- 再生可能エネルギー: Wind turbine blades benefit from the material’s strength and low weight.
These applications demonstrate the versatility and value of carbon fiber composites across diverse sectors.
What methods are commonly used to manufacture carbon fiber composites?
Manufacturers use several methods to produce carbon fiber composites, including:
- Wet Lay-Up: A cost-effective method for simple parts.
- Prepreg Lamination: Ensures precision and high-quality results.
- Resin Transfer Molding (RTM): Ideal for complex shapes and large parts.
- Filament Winding: Specialized for cylindrical components.
- Vacuum-Assisted Resin Transfer Molding (VARTM): Combines precision with cost-efficiency.
Each method caters to specific applications and performance requirements.
How does Ningbo VET Energy Technology Co. ensure high-quality carbon fiber composites?
Ningbo VET Energy Technology Co. employs 新素材 and cutting-edge manufacturing techniques to deliver superior results. The company uses high-performance resin systems and carbon fiber fabrics to meet rigorous industry standards. Techniques like vacuum-assisted resin transfer molding (VARTM) and prepreg lamination enhance precision and efficiency.
“By integrating innovation and expertise, Ningbo VET Energy Technology Co. consistently delivers high-quality solutions tailored to diverse applications.”
What safety precautions should be taken during carbon fiber composite manufacturing?
Safety is crucial in carbon fiber composite manufacturing. Key precautions include:
- Proper Ventilation: Ensures safe air quality when handling resins.
- Personal Protective Equipment (PPE): Gloves, goggles, and respirators protect workers from chemicals and dust.
- Safe Handling of Resins: Following manufacturer guidelines minimizes health risks.
Prioritizing safety not only protects workers but also ensures a smooth production process.
炭素繊維複合材料はリサイクル可能か?
Recycling carbon fiber composites poses challenges due to their structure. However, methods like pyrolysis and chemical recycling are being developed to recover fibers without degrading their quality. Recycled fibers often find use in non-structural applications, such as automotive interiors or construction materials.
“Innovative recycling techniques are essential for reducing waste and promoting sustainability in the carbon fiber industry.”
What makes Ningbo VET Energy Technology Co. a trusted partner for carbon fiber composite manufacturing?
Ningbo VET Energy Technology Co. stands out for its expertise, innovation, and commitment to quality. The company offers customized solutions for industries like aerospace, automotive, and sports equipment. Advanced techniques and sustainable practices ensure superior results while aligning with environmental goals.
For inquiries, contact Ningbo VET Energy Technology Co. via:
- 電話: 86-1891 1596 392
- 電子メール: yeah@china-vet.com
- Website: 寧波VETエネルギー技術有限公司
What are the environmental benefits of using carbon fiber composites?
Carbon fiber composites contribute to sustainability by reducing weight in vehicles and aircraft, which improves fuel efficiency. Additionally, manufacturers adopting sustainable practices, such as recycling production waste and using energy-efficient curing methods, further enhance the environmental benefits of these materials.
How can businesses choose the right manufacturing method for their carbon fiber composite parts?
Businesses should consider factors like part complexity, performance requirements, and budget. For example:
- Simple Parts: Wet lay-up offers a cost-effective solution.
- High-Performance Applications: Prepreg lamination ensures precision and quality.
- Complex Shapes: Resin transfer molding (RTM) accommodates intricate designs.
Consulting experts, such as those at Ningbo VET Energy Technology Co., helps businesses select the most suitable method.
Why is proper mold preparation important in carbon fiber composite manufacturing?
Mold preparation ensures a flawless finish and prevents defects. Cleaning and polishing the mold surface remove contaminants, while applying mold release agents simplifies demolding. Skipping these steps can lead to imperfections and reduce the lifespan of the mold.
“Attention to detail during mold preparation lays the foundation for high-quality composite parts.”