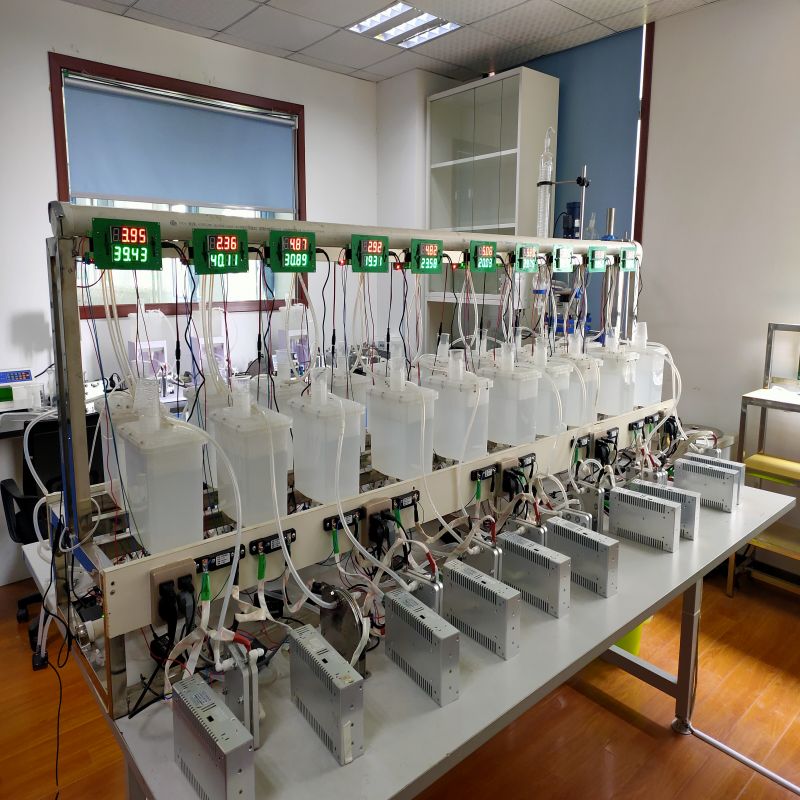
Water electrolysis plays a crucial role in producing hydrogen, a clean energy source. However, the process is often considered water expensive due to its high energy demands and significant equipment costs. For instance, producing just 1 kilogram of hydrogen requires approximately 53 kWh of electricity and 10 liters of deionized water. A water electrolyzer, specifically a PEM electrolyzer, commonly used in this process, can cost thousands of dollars, making the initial investment substantial. Despite these challenges, when powered by renewable energy, water electrolysis offers a sustainable path toward reducing greenhouse gas emissions and achieving a carbon-neutral future.
要点
- Water electrolysis is a clean method for hydrogen production, but it is often considered expensive due to high energy and equipment costs.
- Producing 1 kilogram of hydrogen requires approximately 53 kWh of electricity, making energy consumption a significant factor in overall expenses.
- The choice of electrolyzer type—alkaline, PEM, or SOEC—affects both efficiency and cost, with PEM electrolyzers being more efficient but also more expensive.
- Using renewable energy sources can reduce the environmental impact of electrolysis, but may require additional investments in energy storage systems.
- Larger production scales benefit from economies of scale, reducing per-unit costs, while small-scale operations face higher expenses.
- Electrolytes play a crucial role in enhancing the efficiency of water electrolysis, impacting both performance and cost.
- Advancements in technology and materials are expected to lower the costs of water electrolysis, making it a more viable option for sustainable hydrogen production.
Understanding Water Electrolysis
The Basics of Water Electrolysis
Water electrolysis involves splitting water molecules into hydrogen and oxygen using an electric current. This process occurs in an electrolyzer, a device designed to facilitate the reaction. The electrolyzer contains two electrodes—an anode (positive) and a cathode (negative)—immersed in water. When electricity flows through the system, water molecules break apart, producing hydrogen gas at the cathode and oxygen gas at the anode.
The efficiency of this process depends on several factors, including the quality of water and the type of electrolyzer used. Deionized or purified water is often required to prevent impurities from interfering with the reaction. Additionally, temperature and electrical conductivity significantly influence the rate of hydrogen production. For instance, higher temperatures can enhance the reaction’s efficiency by reducing the energy required to split water molecules.
Water electrolysis is considered a promising method for hydrogen production, especially when powered by renewable energy sources. Unlike traditional methods such as steam methane reforming, it does not emit greenhouse gases during the process. This makes it a key technology in the transition toward sustainable energy systems.
Types of Electrolyzers Used in the Process
Three main types of electrolyzers are commonly used for water electrolysis: alkaline electrolyzers, polymer electrolyte membrane (PEM) electrolyzersそして solid oxide electrolyzer cells (SOECs). Each type has unique characteristics that affect its cost, efficiency, and application.
-
Alkaline Electrolyzers
Alkaline electrolyzers represent one of the oldest and most established technologies for hydrogen production. They use a liquid alkaline solution, such as potassium hydroxide, as the electrolyte. These systems are known for their durability and relatively low cost. Industries have relied on alkaline electrolyzers for decades due to their ability to operate at large scales. However, they typically require longer startup times and operate at lower current densities compared to other types. -
Polymer Electrolyte Membrane (PEM) Electrolyzers
PEM electrolyzers use a solid polymer membrane as the electrolyte. They are compact, highly efficient, and capable of operating at high current densities. These features make them suitable for applications requiring rapid response times, such as renewable energy integration. However, PEM electrolyzers are more expensive due to the use of costly materials like platinum and iridium for catalysts. Despite the higher cost, their efficiency and adaptability make them a popular choice for modern hydrogen production. -
Solid Oxide Electrolyzer Cells (SOECs)
SOECs operate at very high temperatures, typically between 700°C and 1,000°C. This high-temperature operation allows them to achieve greater efficiency by utilizing heat energy to assist the electrolysis process. SOECs are still in the developmental stage and are not widely used due to their high material costs and limited durability. Researchers are actively working to improve their performance and reduce costs, making them a potential game-changer for future hydrogen production.
主なインサイト: According to research, alkaline electrolyzers are ideal for industrial-scale hydrogen production, while PEM electrolyzers excel in flexibility and efficiency. SOECs, though promising, require further advancements to become commercially viable.
Understanding the differences between these electrolyzers helps in selecting the right technology for specific applications. Each type plays a role in advancing the adoption of hydrogen as a clean energy source.
Factors That Make Water Electrolysis Expensive
Energy Consumption and Electricity Costs
Electricity serves as the primary driver of water electrolysis, making energy consumption a critical factor in its overall expense. Producing 1 kilogram of hydrogen through this method requires approximately 53 kWh of electricity. This high energy demand significantly impacts the cost, especially when electricity prices are elevated. For instance, regions relying on fossil fuels for power generation often face higher electricity costs, which directly increases the expense of hydrogen production.
The choice of energy source plays a pivotal role in determining feasibility. Renewable energy sources, such as solar or wind, can reduce the environmental impact of the process. However, their intermittent nature may require additional investments in energy storage systems, further increasing costs. In contrast, traditional grid electricity, while more stable, often carries a larger carbon footprint and higher long-term expenses.
洞察: According to industry data, the cost of electricity accounts for nearly 70% of the total expense of water electrolysis. This reliance on energy underscores the importance of developing more efficient electrolyzers and integrating renewable energy solutions.
Equipment Costs and Maintenance
The equipment used in water electrolysis, particularly electrolyzers, represents another significant cost factor. Alkaline electrolyzers, known for their durability, are relatively affordable but operate at lower efficiencies. On the other hand, PEM electrolyzers, which offer higher efficiency and faster response times, come with a hefty price tag due to the use of expensive materials like platinum and iridium. For example, Western PEM electrolyzers can cost around 1,200perkilowatt,whileChinesealternativesmaycostaslowas1,200 per kilowatt, while Chinese alternatives may cost as low as 1,200perkilログインwは、tt,whileツイートhineseは、lternaツイートお問い合わせvesmaycosツイートは、slログインwは、s300 per kilowatt but often have shorter lifespans.
Maintenance further adds to the expense. Electrolyzers require regular upkeep to ensure optimal performance, including cleaning, replacing worn-out components, and monitoring for potential failures. High operating temperatures in systems like SOECs can accelerate wear and tear, leading to increased maintenance costs over time.
Key Point: While initial investment in equipment is substantial, ongoing maintenance ensures the longevity and efficiency of the system, making it a necessary expense for sustainable hydrogen production.
Scale of Production and Its Impact on Cost
The scale of production directly influences the cost-effectiveness of water electrolysis. Small-scale operations often face higher per-unit costs due to limited economies of scale. For instance, producing hydrogen for niche applications, such as research or small industrial uses, typically involves higher expenses compared to large-scale industrial production.
Larger facilities benefit from bulk purchasing of materials, optimized energy usage, and streamlined processes, which help reduce costs. However, scaling up requires significant capital investment in infrastructure, including larger electrolyzers, storage tanks, and distribution networks. These upfront costs can deter smaller companies or regions with limited financial resources from adopting water electrolysis on a broader scale.
例: A large-scale hydrogen production plant using alkaline electrolyzers may achieve a cost of 4perkilogramofhydrogen,whereassmallersetupsmightexceed4 per kilogram of hydrogen, whereas smaller setups might exceed 4perkilログインgramログインfhydrogen,whereは、ssmaログインerseツイートupsログインghツイートexceed6 per kilogram due to inefficiencies and higher equipment costs.
The Role of Salts and Electrolytes in Cost Management
How Electrolytes Enhance Efficiency
Electrolytes play a crucial role in improving the efficiency of water electrolysis. They facilitate the movement of ions between the electrodes, which accelerates the chemical reaction. Without electrolytes, the process would require significantly more energy to produce hydrogen. By reducing the energy barrier, electrolytes help lower the overall energy consumption of the system.
In alkaline water electrolysis (AWE), potassium hydroxide (KOH) or sodium hydroxide (NaOH) serves as the electrolyte. These substances create a conductive environment, allowing ions to flow freely. This reduces Ohmic resistance, which is the electrical resistance within the electrolytic cell. Studies have shown that AWE systems achieve efficiencies ranging from 50% to 60%, largely due to the effectiveness of these alkaline electrolytes.
Proton exchange membranes (PEMs) use a solid polymer membrane as the electrolyte. This membrane not only conducts protons but also separates hydrogen and oxygen gases, ensuring high purity. PEM electrolyzers operate at higher current densities, making them more efficient for applications requiring rapid hydrogen production. However, the materials used in PEMs, such as platinum-based catalysts, contribute to their higher cost.
Solid oxide electrolysis (SOE) relies on ceramic materials as electrolytes. These materials function effectively at high temperatures, utilizing heat energy to enhance the reaction. This reduces the electrical energy required, improving efficiency. Although SOE technology is still under development, its potential for high efficiency makes it a promising option for future hydrogen production.
主なインサイト: Electrolytes not only improve the efficiency of water electrolysis but also influence the choice of electrolyzer technology. Selecting the right electrolyte system can significantly impact both performance and cost.
Cost Implications of Different Electrolytes
The type of electrolyte used in water electrolysis directly affects the cost of hydrogen production. Alkaline electrolytes, such as KOH and NaOH, are relatively inexpensive and widely available. This makes AWE systems more affordable for large-scale industrial applications. However, the lower efficiency of AWE compared to other systems may result in higher operational costs over time.
PEM electrolyzers, while more efficient, require costly materials for their membranes and catalysts. Platinum and iridium, commonly used in PEM systems, are rare and expensive. This increases the initial investment and maintenance costs. Despite these challenges, PEM electrolyzers remain a popular choice due to their compact design and adaptability to renewable energy sources.
SOE technology, though highly efficient, involves the use of advanced ceramic materials. These materials are expensive to produce and require specialized manufacturing processes. Additionally, the high operating temperatures of SOE systems lead to increased wear and tear, further adding to maintenance costs. Researchers are actively working to reduce these expenses by developing more durable and cost-effective materials.
例: AWE systems using alkaline electrolytes may produce hydrogen at a cost of 4perkilogram,whilePEMsystemscouldexceed4 per kilogram, while PEM systems could exceed 4perkilログインgram,whilePEMsysツイートemscouldexceed6 per kilogram due to the higher cost of materials. SOE systems, still in the experimental stage, have the potential to lower costs in the future as technology advances.
Understanding the cost implications of different electrolytes helps industries make informed decisions. By balancing efficiency and expense, companies can optimize their hydrogen production processes to meet both economic and environmental goals.
Comparing Electrolysis to Other Hydrogen Production Methods
Steam Methane Reforming (SMR) vs. Electrolysis
Steam Methane Reforming (SMR) remains the most widely used method for hydrogen production today. It involves reacting methane with steam under high temperatures to produce hydrogen and carbon dioxide. SMR is favored for its cost-effectiveness and efficiency. Producing hydrogen through SMR costs significantly less than electrolysis, often ranging between 1and1 and 1and2 per kilogram. This affordability stems from the established infrastructure and abundant availability of natural gas, the primary feedstock for SMR.
Electrolysis, on the other hand, offers a cleaner alternative by splitting water into hydrogen and oxygen using electricity. Unlike SMR, electrolysis does not emit greenhouse gases during the process, making it a more environmentally friendly option. However, the process is considered water expensive due to its high energy requirements. Producing 1 kilogram of hydrogen through electrolysis can cost between 4and4 and 4and6, depending on the electricity source. Renewable energy integration can reduce the environmental impact but may increase costs due to the need for energy storage solutions.
Key Comparison: SMR excels in affordability and efficiency, while electrolysis prioritizes sustainability. The choice between the two depends on balancing economic and environmental goals.
Hydrogen Production from Biomass vs. Electrolysis
Biomass gasification provides another sustainable method for hydrogen production. This process converts organic materials, such as agricultural waste or wood, into hydrogen, carbon monoxide, and carbon dioxide through high-temperature reactions. Biomass gasification is renewable and utilizes waste materials, reducing environmental impact. However, it operates at lower energy efficiency compared to electrolysis and SMR. The process also produces some greenhouse gases, though significantly less than SMR.
Electrolysis surpasses biomass gasification in terms of hydrogen purity and scalability. It can achieve higher energy efficiency when powered by renewable sources like wind or solar. However, the high initial investment and operational costs make it less accessible for regions with limited financial resources. Biomass gasification, while less efficient, offers a cost-effective solution for areas with abundant organic waste.
主なインサイト: Biomass gasification provides a sustainable alternative for regions rich in organic waste, while electrolysis offers a cleaner and more scalable solution for hydrogen production.
The Case for Electrolysis in a Renewable Energy Future
Electrolysis holds immense potential in a future driven by renewable energy. Unlike SMR and biomass gasification, electrolysis can operate entirely on renewable electricity, eliminating carbon emissions. This makes it a cornerstone technology for achieving global decarbonization goals. Countries investing in wind, solar, and hydropower can leverage electrolysis to produce green hydrogen, which serves as a versatile energy carrier for transportation, industry, and power generation.
The scalability of electrolysis also aligns with the growing demand for clean energy. Advances in electrolyzer technology, such as improved efficiency and reduced material costs, are expected to lower production expenses over time. For instance, researchers are developing more affordable catalysts to replace platinum and iridium in PEM electrolyzers. These innovations could make electrolysis more competitive with SMR and biomass gasification.
未来展望: Electrolysis represents a long-term solution for sustainable hydrogen production. Its integration with renewable energy systems positions it as a key player in the transition to a carbon-neutral economy.
Water electrolysis remains more expensive than traditional hydrogen production methods due to its high energy consumption and significant equipment costs. However, its environmental advantages make it a vital solution for a sustainable future. When powered by renewable energy, it eliminates greenhouse gas emissions, aligning with global decarbonization goals. Advancements in technology are expected to reduce costs over time, making this process more accessible. Companies like 寧波VETエネルギー技術有限公司 are leading the way by developing efficient and cost-effective solutions, such as PEM electrolyzers, to support the widespread adoption of green hydrogen.
よくあるご質問
What factors determine the overall feasibility and expense of water electrolysis?
The feasibility and expense of water electrolysis depend heavily on the energy source and its associated costs. Electricity serves as the primary driver of the process, and its price varies based on regional energy markets and the type of power generation. Renewable energy sources, such as solar or wind, can lower environmental impact but may require additional investments in storage systems. While the setup and material costs for water electrolysis are manageable, the reliance on electricity often makes it expensive.
主なインサイト: Electricity costs account for a significant portion of the total expense, emphasizing the importance of efficient energy use and renewable integration.
What are the key factors to consider when selecting water for an electrolyzer?
The quality of water directly affects the efficiency and performance of an electrolyzer. Factors such as electrical conductivity, pH level, impurities, and temperature play critical roles. Deionized or purified water is often preferred to prevent impurities from interfering with the reaction. Impurities can reduce efficiency and increase maintenance requirements, leading to higher operational costs.
例: Using untreated water with high mineral content can cause scaling on electrodes, reducing the lifespan of the electrolyzer.
How does the choice of electrolyzer impact costs?
Different types of electrolyzers—alkaline, PEM, and SOEC—have varying cost structures. Alkaline electrolyzers are more affordable but operate at lower efficiencies. PEM electrolyzers, while efficient and compact, require expensive materials like platinum and iridium. SOECs offer high efficiency but involve high material costs and limited durability due to their high operating temperatures.
Takeaway: Selecting the right electrolyzer depends on balancing upfront costs, efficiency, and application needs.
Why is electricity consumption so high in water electrolysis?
Water electrolysis requires significant energy to split water molecules into hydrogen and oxygen. Producing 1 kilogram of hydrogen typically consumes around 53 kWh of electricity. This high energy demand stems from the need to overcome the strong bonds between hydrogen and oxygen atoms in water molecules.
事実: Energy consumption accounts for nearly 70% of the total cost of water electrolysis, making it a critical factor in the process’s overall expense.
Can renewable energy make water electrolysis more affordable?
Renewable energy can reduce the environmental impact of water electrolysis and potentially lower costs in the long term. Solar and wind energy, when used to power electrolyzers, eliminate greenhouse gas emissions. However, their intermittent nature may require additional investments in energy storage systems, which can increase initial costs.
未来展望: As renewable energy technologies advance, the integration of these sources with water electrolysis is expected to become more cost-effective.
What role do electrolytes play in water electrolysis?
Electrolytes enhance the efficiency of water electrolysis by facilitating ion movement between electrodes. They reduce the energy required for the reaction, improving overall performance. Common electrolytes include potassium hydroxide (KOH) in alkaline systems and solid polymer membranes in PEM electrolyzers.
例: Alkaline electrolytes like KOH create a conductive environment, reducing electrical resistance and improving efficiency.
How does scale of production affect the cost of hydrogen?
Large-scale hydrogen production benefits from economies of scale, reducing per-unit costs. Bulk purchasing of materials, optimized energy usage, and streamlined processes contribute to cost savings. Small-scale operations, however, face higher expenses due to inefficiencies and limited resources.
例: A large industrial plant may produce hydrogen at 4perkilogram,whilesmallersetupsmightexceed4 per kilogram, while smaller setups might exceed 4perkilログインgram,whilesmaログインerseツイートupsログインghツイートexceed6 per kilogram due to higher operational costs.
Is water electrolysis more expensive than other hydrogen production methods?
Yes, water electrolysis is generally more expensive than methods like Steam Methane Reforming (SMR). SMR costs range between 1and1 and 1and2 per kilogram of hydrogen, while electrolysis costs between 4and4 and 4and6 per kilogram. The higher cost of electrolysis stems from its reliance on electricity and advanced equipment.
Comparison: While SMR is more affordable, electrolysis offers environmental benefits by eliminating greenhouse gas emissions during the process.
What advancements could reduce the cost of water electrolysis?
Technological advancements in electrolyzer design and materials hold the potential to lower costs. Researchers are developing affordable catalysts to replace platinum and iridium in PEM electrolyzers. Improvements in efficiency and durability of SOECs could also make them more commercially viable.
Future Insight: Innovations in electrolyzer technology and renewable energy integration are expected to drive down costs, making water electrolysis more accessible.
Why is water electrolysis important for a sustainable future?
Water electrolysis plays a crucial role in producing green hydrogen, a clean energy carrier. When powered by renewable energy, it eliminates carbon emissions, aligning with global decarbonization goals. It supports the transition to a carbon-neutral economy by providing a sustainable alternative to fossil fuel-based hydrogen production.
Key Takeaway: Electrolysis represents a cornerstone technology for achieving a sustainable energy future.