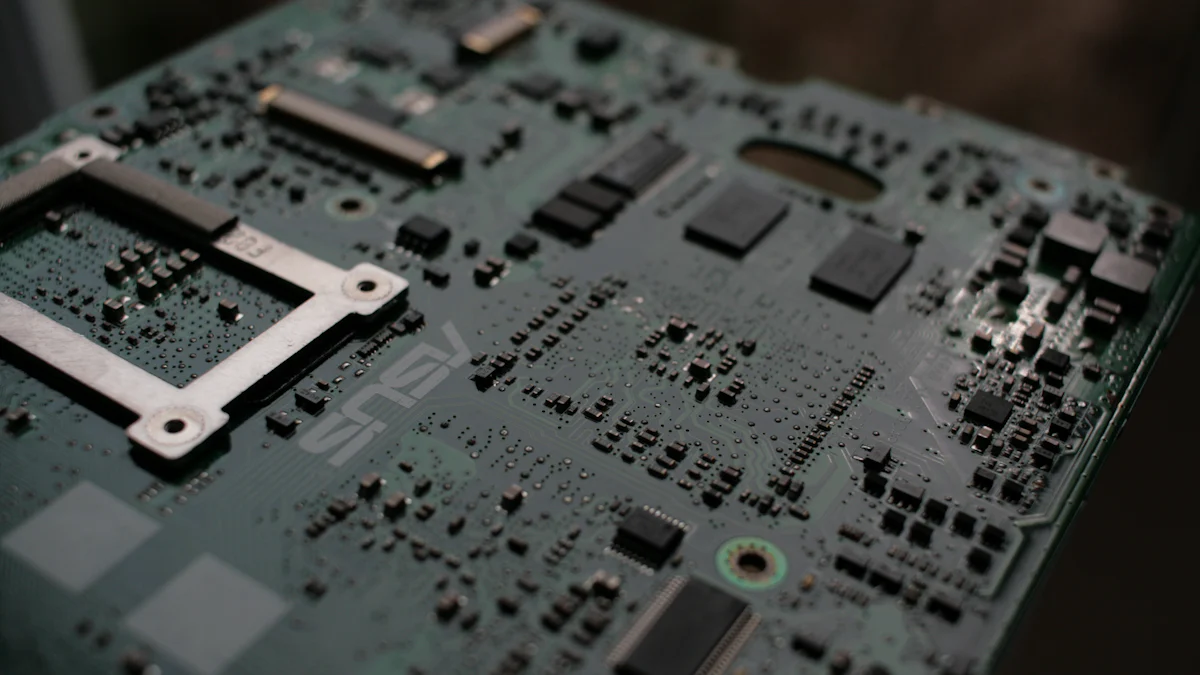
In the world of semiconductor manufacturing, the MOCVD Susceptor plays a pivotal role. This component supports substrates during the deposition process, ensuring precise thin-film growth. Its design and material directly influence the quality of semiconductors, making it indispensable for achieving high-performance devices. Adhering to strict standards guarantees consistent results, reduces defects, and enhances production efficiency. Standards also ensure compatibility across systems, allowing manufacturers to streamline operations and maintain reliability. As industries demand advanced electronics, the importance of these standards continues to grow, shaping the future of semiconductor technology.
要点
- Understanding and adhering to the SEMI HB13 standard is crucial for ensuring uniform performance and reliability in MOCVD processes.
- High thermal conductivity and resistance to high temperatures are essential properties for MOCVD susceptors, directly impacting semiconductor quality.
- Maintaining strict dimensional tolerances in susceptor design is vital for optimal functionality and consistent thin-film deposition.
- Regular inspections and preventive maintenance can significantly extend the lifespan and performance of MOCVD susceptors.
- Partnering with trusted suppliers ensures access to high-quality susceptors that meet industry standards, enhancing production efficiency.
- Compliance with industry standards not only builds trust but also simplifies collaboration between manufacturers and suppliers.
- Investing in superior materials and rigorous testing processes is key to reducing defects and lowering production costs in semiconductor manufacturing.
Overview of MOCVD Susceptor Standards
Industry Standards for MOCVD Susceptors
SEMI HB13 Standard and Its Relevance
について SEMI HB13 standard stands as a cornerstone in defining the requirements for MOCVD susceptors. This standard focuses on ensuring uniformity in communication interfaces and data collection protocols for susceptors used in HB-LED MOCVD equipment. By adhering to this specification, manufacturers can achieve consistent performance across different systems. The SEMI HB13 standard also promotes reliability by addressing critical aspects like material properties and design tolerances.
For instance, the SEMI HB13 standard emphasizes the importance of thermal stability and chemical resistance in susceptors. These qualities directly impact the efficiency of the MOCVD process, especially when dealing with high-temperature environments.
This standard not only enhances the quality of semiconductor manufacturing but also simplifies collaboration between suppliers and manufacturers. It ensures that all parties involved speak the same technical language, reducing errors and improving compatibility.
Other International Standards for MOCVD Susceptors
Beyond SEMI HB13, other international standards play a vital role in shaping the design and functionality of MOCVD susceptors. These standards often focus on specific aspects like purity, cleanliness, and dimensional accuracy. For example, some guidelines emphasize the need for high-temperature oxidation resistance, a key feature of SiC-coated graphite susceptors.
Patents such as US20060269390A1 そして US7122844B2 highlight innovations in susceptor design, showcasing how international standards influence advancements in this field. These patents underline the importance of meeting stringent specifications to ensure optimal performance in MOCVD reactors.
By following these global standards, manufacturers can produce susceptors that meet the diverse needs of semiconductor applications. This approach fosters innovation while maintaining a high level of quality.
Importance of Standards in Semiconductor Manufacturing
Ensuring Process Consistency and Quality
Standards serve as a blueprint for achieving consistency in semiconductor manufacturing. They define the material properties, dimensions, and surface finishes required for MOCVD susceptors. This level of precision minimizes variations during production, leading to higher-quality semiconductors.
For example, a susceptor with poor thermal conductivity can cause uneven heating, resulting in defects during thin-film deposition. Standards address such issues by specifying acceptable ranges for thermal and mechanical properties. This ensures that every susceptor performs reliably, regardless of the manufacturing batch.
Enhancing Compatibility Across MOCVD Systems
Compatibility is another critical benefit of adhering to MOCVD susceptor standards. These guidelines ensure that susceptors can function seamlessly across various MOCVD systems. This is particularly important as manufacturers often use equipment from different suppliers.
A well-designed susceptor, built to standard specifications, eliminates the need for frequent adjustments or replacements. This reduces downtime and enhances overall productivity.
By prioritizing compatibility, standards make it easier for manufacturers to scale their operations. They can integrate new technologies without worrying about compatibility issues, paving the way for more efficient and cost-effective production processes.
Key Specifications for MOCVD Susceptors
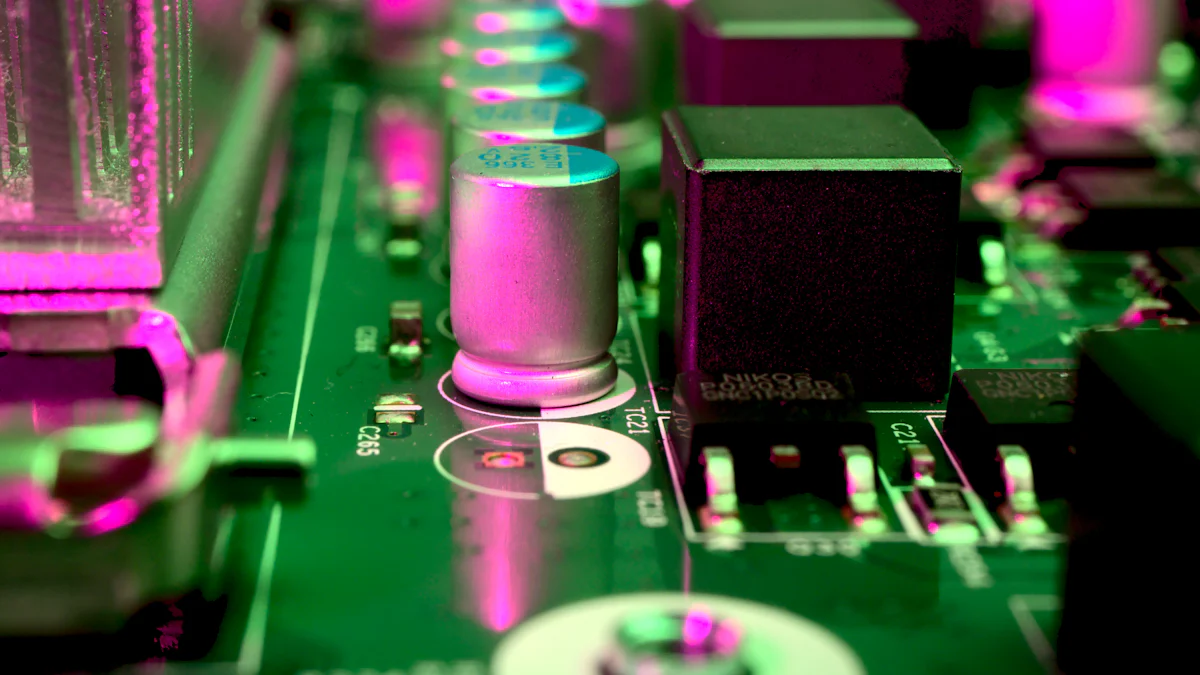
Material Properties of MOCVD Susceptors
Thermal Conductivity and Its Role in Performance
Thermal conductivity plays a vital role in the performance of an MOCVD susceptor. It ensures even heat distribution across the substrate during the deposition process. Uneven heating can lead to inconsistent thin-film growth, which directly impacts the quality of the final semiconductor product. Materials like silicon carbide (SiC) are often used for susceptors due to their excellent thermal conductivity. This property helps maintain uniform temperatures, which is critical for achieving consistent film thickness and composition.
For example, in power electronics, where high-performance components like transistors and diodes are manufactured, precise thermal control is essential. The susceptor’s ability to manage heat effectively ensures that these components meet the required performance standards.
高温抵抗と耐久性
High-temperature resistance is another key attribute of MOCVD susceptors. The deposition process involves extreme temperatures, often exceeding 1000°C. Materials like SiC-coated graphite are commonly chosen for their ability to withstand such conditions without degrading. This durability ensures the susceptor’s longevity, reducing the need for frequent replacements and minimizing downtime.
Durable susceptors also contribute to process efficiency. They maintain their structural integrity under repeated thermal cycles, ensuring consistent performance over time. This reliability is especially important in industries like renewable energy and electric vehicles, where high-quality semiconductors are essential for efficient power conversion and control.
Dimensional Tolerances in MOCVD Susceptor Design
Precision Requirements for Optimal Functionality
Precision in dimensional tolerances is crucial for the optimal functionality of MOCVD susceptors. Even minor deviations can disrupt the deposition process, leading to defects in the thin films. Manufacturers must adhere to strict specifications to ensure that susceptors fit perfectly within the MOCVD system. This precision allows for smooth operation and consistent results.
For instance, a susceptor with precise dimensions ensures proper alignment of the substrate, which is critical for achieving uniform deposition. This level of accuracy minimizes errors and enhances the overall quality of the semiconductor.
Common Tolerance Ranges in the Industry
In the industry, common tolerance ranges for MOCVD susceptors are typically within micrometer levels. These tight tolerances reflect the high standards required in semiconductor manufacturing. Advanced machining techniques and quality control processes are employed to achieve these specifications. By maintaining such exacting standards, manufacturers can produce susceptors that meet the demands of modern electronic systems.
Surface Finish of MOCVD Susceptors
Impact of Surface Smoothness on Deposition Uniformity
The surface finish of an MOCVD susceptor significantly affects deposition uniformity. A smooth surface ensures that the substrate remains stable during the process, reducing the risk of irregularities in the thin film. Rough or uneven surfaces can cause variations in film thickness, leading to defects that compromise the performance of the semiconductor.
For example, in applications like power electronics, where devices operate at high voltages and currents, even minor imperfections in the thin film can result in performance issues. A high-quality surface finish helps prevent such problems, ensuring reliable operation.
Techniques for Achieving High-Quality Surface Finishes
Achieving a high-quality surface finish requires advanced manufacturing techniques. Polishing and coating processes are commonly used to create smooth, defect-free surfaces. SiC coatings, for instance, not only enhance thermal and chemical resistance but also improve the surface finish of the susceptor. These techniques ensure that the susceptor meets the stringent requirements of semiconductor manufacturing.
Manufacturers often invest in state-of-the-art equipment and rigorous quality control measures to achieve the desired surface finish. This attention to detail ensures that the susceptor performs reliably, contributing to the overall success of the MOCVD process.
Compliance and Testing for MOCVD Susceptors
Ensuring Compliance with Industry Standards
Certification Processes and Documentation
Certification ensures that every MOCVD susceptor meets the required industry standards. Manufacturers must follow strict protocols to certify their products. These certifications validate that the susceptor’s material properties, dimensions, and performance align with established guidelines. Certification processes often involve third-party audits, which add an extra layer of credibility.
Documentation plays a key role in this process. It provides detailed records of the susceptor’s specifications, manufacturing methods, and testing results. This transparency helps manufacturers and customers verify compliance. For example, a certified susceptor with proper documentation assures semiconductor producers that the component will perform reliably under demanding conditions.
Certification not only builds trust but also simplifies collaboration between suppliers and manufacturers. It ensures that everyone operates on the same page, reducing misunderstandings and errors.
Traceability Requirements for MOCVD Susceptors
Traceability is essential in maintaining quality and accountability. Each MOCVD susceptor must have a unique identifier, such as a serial number or batch code. This identifier allows manufacturers to track the susceptor’s journey from production to deployment. If issues arise, traceability makes it easier to pinpoint the source of the problem.
For instance, if a batch of susceptors shows defects, traceability helps identify whether the issue stems from raw materials, production methods, or handling during transport. This level of detail enables quick corrective actions, minimizing downtime and losses.
Traceability also supports compliance with international standards. It ensures that every susceptor can be traced back to its origin, providing confidence in its quality and reliability.
Testing Methods for MOCVD Susceptors
Thermal and Mechanical Testing Techniques
Thermal and mechanical testing ensures that MOCVD susceptors can withstand the harsh conditions of semiconductor manufacturing. Thermal tests evaluate how well the susceptor handles extreme temperatures. These tests measure properties like thermal conductivity and resistance to high-temperature oxidation. A susceptor with excellent thermal performance ensures even heat distribution, which is critical for thin-film deposition.
Mechanical testing assesses the susceptor’s strength and durability. These tests simulate the stresses the susceptor will face during operation. For example, repeated thermal cycling can weaken materials over time. Mechanical tests ensure that the susceptor maintains its structural integrity, even after prolonged use.
Advanced materials like SiC-coated graphite often excel in these tests. Their superior thermal stability and mechanical strength make them ideal for demanding applications.
Surface Analysis and Quality Assurance
Surface analysis focuses on the susceptor’s finish, which directly impacts deposition uniformity. Techniques like scanning electron microscopy (SEM) and atomic force microscopy (AFM) examine the surface at a microscopic level. These methods detect imperfections that could affect the thin-film growth process.
Quality assurance involves rigorous inspections to ensure that every susceptor meets the required standards. Manufacturers use tools like profilometers to measure surface roughness and verify that it falls within acceptable ranges. High-quality surface finishes reduce the risk of defects, improving the overall efficiency of the MOCVD process.
By combining surface analysis with thorough quality checks, manufacturers can deliver susceptors that consistently perform at a high level. This attention to detail ensures reliable results in semiconductor production.
Common Challenges and Best Practices for MOCVD Susceptors
Challenges in Maintaining MOCVD Susceptor Standards
Material Degradation and Longevity Issues
MOCVD susceptors face constant exposure to extreme temperatures and chemical reactions during the deposition process. Over time, this exposure can lead to material degradation, which reduces the susceptor’s performance and lifespan. For instance, high-temperature oxidation can weaken the structural integrity of the susceptor, especially if it lacks proper coatings like silicon carbide (SiC). This degradation not only impacts the quality of thin-film deposition but also increases the frequency of replacements, driving up operational costs.
Another common issue arises from the buildup of reaction deposits on the susceptor’s surface. These deposits, formed during repeated fabrication cycles, can interfere with subsequent processes. They may cause uneven heating or contamination, leading to defects in the semiconductor material. Regular cleaning is essential, but improper methods can further damage the susceptor, creating a cycle of inefficiency.
Variability in Manufacturing Processes
Manufacturing inconsistencies pose another significant challenge. Even minor variations in material composition, dimensional tolerances, or surface finishes can disrupt the performance of an MOCVD susceptor. For example, a slight deviation in thermal conductivity might result in uneven heat distribution, compromising the uniformity of thin films. Similarly, inconsistencies in surface smoothness can lead to irregular deposition, affecting the overall quality of the semiconductor.
These variations often stem from differences in supplier standards or production techniques. Without strict quality control measures, manufacturers may struggle to maintain uniformity across batches. This lack of consistency can hinder compatibility with MOCVD systems, causing delays and inefficiencies in production.
Best Practices for Maintaining MOCVD Susceptor Standards
Regular Inspection and Preventive Maintenance
Routine inspections play a crucial role in maintaining the performance of MOCVD susceptors. By identifying early signs of wear or damage, manufacturers can address issues before they escalate. For instance, visual checks for surface deposits or cracks can help prevent contamination and ensure consistent deposition quality. Advanced tools like profilometers or scanning electron microscopes (SEM) can provide detailed insights into surface conditions, enabling precise maintenance.
Preventive maintenance, such as scheduled cleaning and recoating, extends the susceptor’s lifespan. Using appropriate cleaning techniques minimizes the risk of surface damage while removing harmful deposits. Recoating with materials like SiC restores the susceptor’s thermal and chemical resistance, ensuring reliable performance over time. These proactive measures reduce downtime and improve overall efficiency.
Partnering with Trusted Suppliers for Quality Assurance
Collaborating with reliable suppliers ensures access to high-quality MOCVD susceptors that meet industry standards. Trusted suppliers adhere to stringent manufacturing protocols, delivering products with consistent material properties, dimensions, and surface finishes. This consistency eliminates the need for frequent adjustments, streamlining the integration of susceptors into MOCVD systems.
Suppliers often provide detailed documentation and certifications, which validate the susceptor’s compliance with established standards. This transparency builds trust and simplifies quality assurance processes. Additionally, working with experienced suppliers allows manufacturers to benefit from technical support and customized solutions tailored to their specific needs. By fostering strong partnerships, manufacturers can maintain high standards while optimizing their production processes.
Adhering to MOCVD Susceptor standards is essential for achieving consistent performance and producing high-quality semiconductors. These standards ensure extreme precision, uniformity, and purity, which are critical for optimizing manufacturing processes. Rigorous testing and compliance help manufacturers maintain reliability while meeting industry regulations. By prioritizing high-quality susceptors, companies can enhance productivity, reduce defects, and lower production costs. As demand for advanced electronic devices grows, investing in superior materials and smart system controls becomes even more vital. Choosing the right susceptor design not only improves device performance but also ensures long-term operational efficiency.