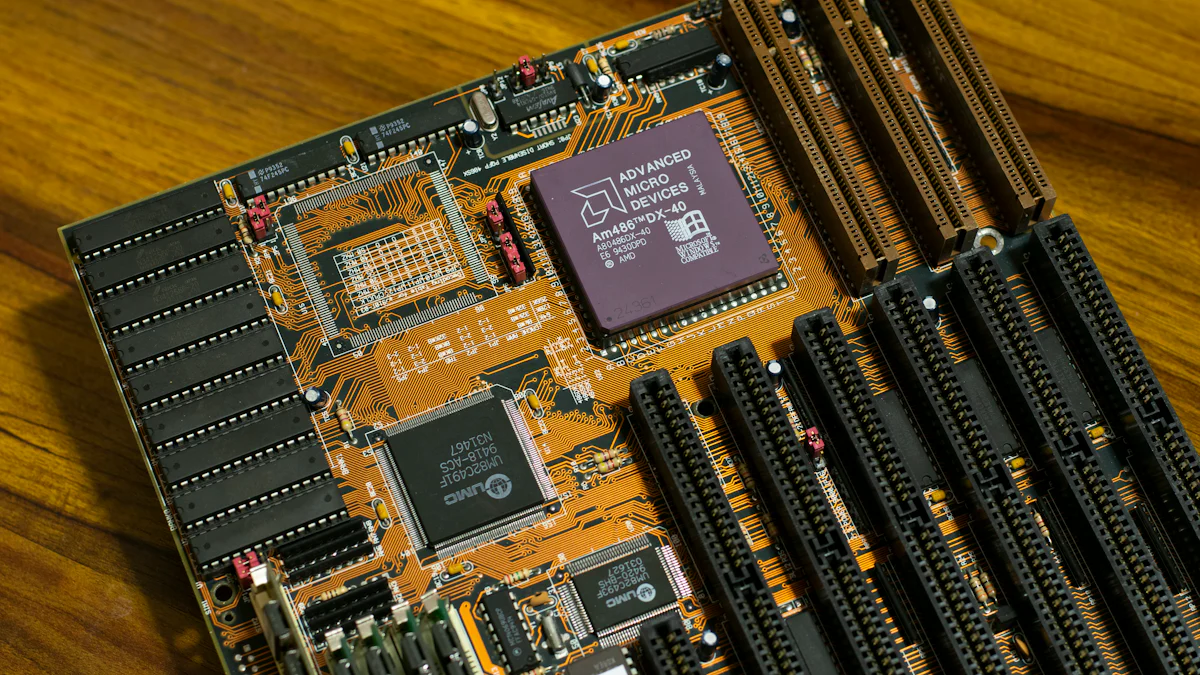
半導体製造は、革新的なソリューションを要求する課題に直面しています。 材料の劣化、熱安定性、汚染リスクは、生産を破壊し、効率性を低下させることが多い。 これらの障害を克服するための信頼できる方法が必要です。 SiCコーティングは、高度な特性に画期的なアプローチを提供します。 耐久性を高め、極端な温度に抵抗し、化学的安定性を保証します。 これらの資質は、お客様のプロセスにおいて一貫した性能と高い信頼性を実現するのに役立ちます。 この技術の統合によって、製造業の精密を高め、企業の競争の端を維持できます.
要点
- シスコ コーティングは、耐久性と耐摩耗性を高め、半導体製造装置の寿命を大幅に延ばします.
- コーティングの高い熱伝導性および安定性は高温プロセスの間に一貫した性能を保障しま、装置の失敗の危険を減らします.
- SiCコーティングの化学的不活性は、汚染リスクを最小限に抑え、ウェーハやデバイスの純度を向上し、高い収量と信頼性を実現します.
- プロセスにコーティングされたSiCを組み込むことで、メンテナンスコストを削減し、運用効率を向上させることができ、生産に集中することができます.
- 99.9995%までの純度のレベルを使って、SiC コーティングは、高度な半導体アプリケーションの厳しい要求を満たし、欠陥のない結果を保証します.
- この多彩なコーティングは、半導体だけでなく、航空宇宙、自動車、再生可能エネルギー分野でも適用可能で、業界全体のイノベーションを推進しています.
- SiCコーティング技術を採用することにより、半導体市場での競争力を維持し、製品が最高品質の基準を満たしていることを確認します.
半導体における課題 製造業
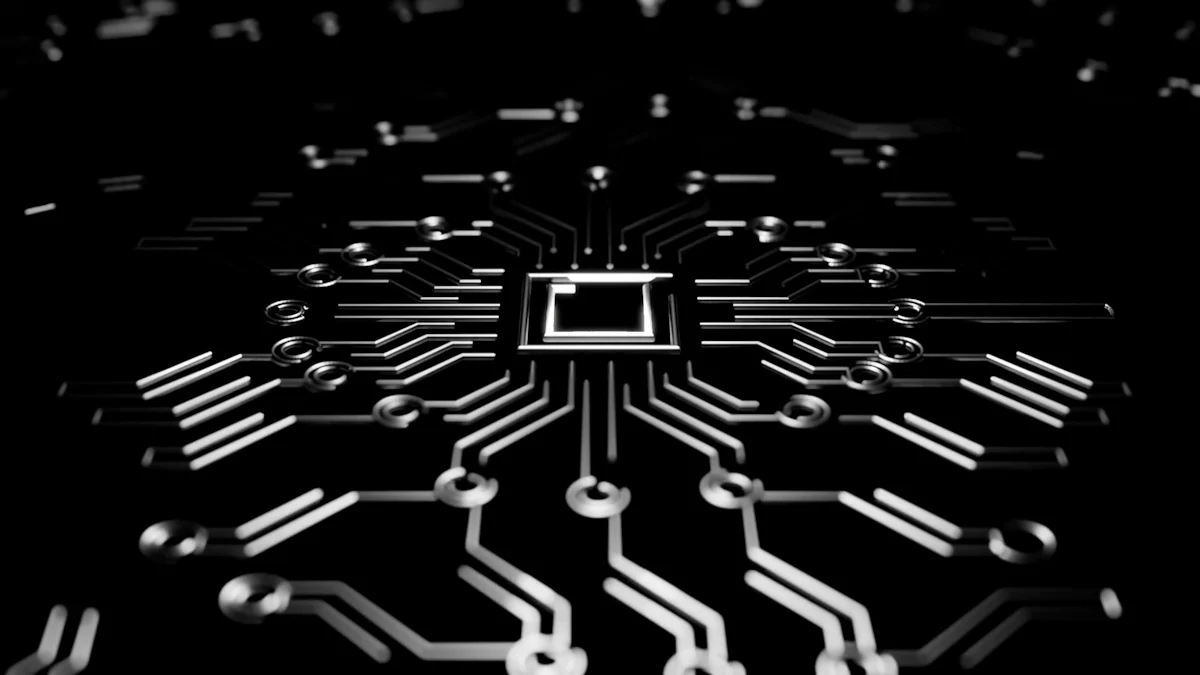
ハーシュ環境における材料分解
半導体製造における材料を扱う際の一定の課題に直面しています。 腐食性の化学薬品および研摩プロセスへの露出を含む堅実な環境は、頻繁に材料の低下をもたらします。 この摩耗および引き裂きはあなたの装置の寿命を減らし、生産の効率を妥協します。 時間が経つにつれて、劣化した材料は頻繁に交換し、運用コストとダウンタイムを増加させることができます。 この問題に対処するには、構造の完全性を失うことなく、これらの極端な条件に耐えることができる材料が必要です.
高温度プロセスにおける熱安定性
半導体製造では高温プロセスが不可欠ですが、重要なリスクを発揮します。 機器の故障や異常な結果を引き起こす可能性がある熱的不安定性に遭遇することがあります。 急速な温度変動は頻繁に材料の拡張か収縮に導きま、部品を弱める圧力を作成します。 この不安定性は精密を破壊し、最終製品の品質に影響を与えます。 安定した性能を維持するためには、安定性と機能性を維持しながら極端な熱に耐えることができる材料が必要です.
精密製造における汚染リスク
半導体製造において、精密は重要だが、汚染は深刻な脅威をもたらします。 最小粒子や化学不純物であっても、ウェーハやデバイスの品質を妥協することができます。 汚染は、多くの場合、機器の表面、環境要因、またはプロセス残余から発生します。 これらの不純物は欠陥に導き、収穫および信頼性を減らすことができます。 高品質の結果を得るためには、清潔で管理された環境のために設計された材料とコーティングを使用して、汚染リスクを最小限に抑える必要があります.
SiCコーティングのプロパティは、これらの課題に対処します
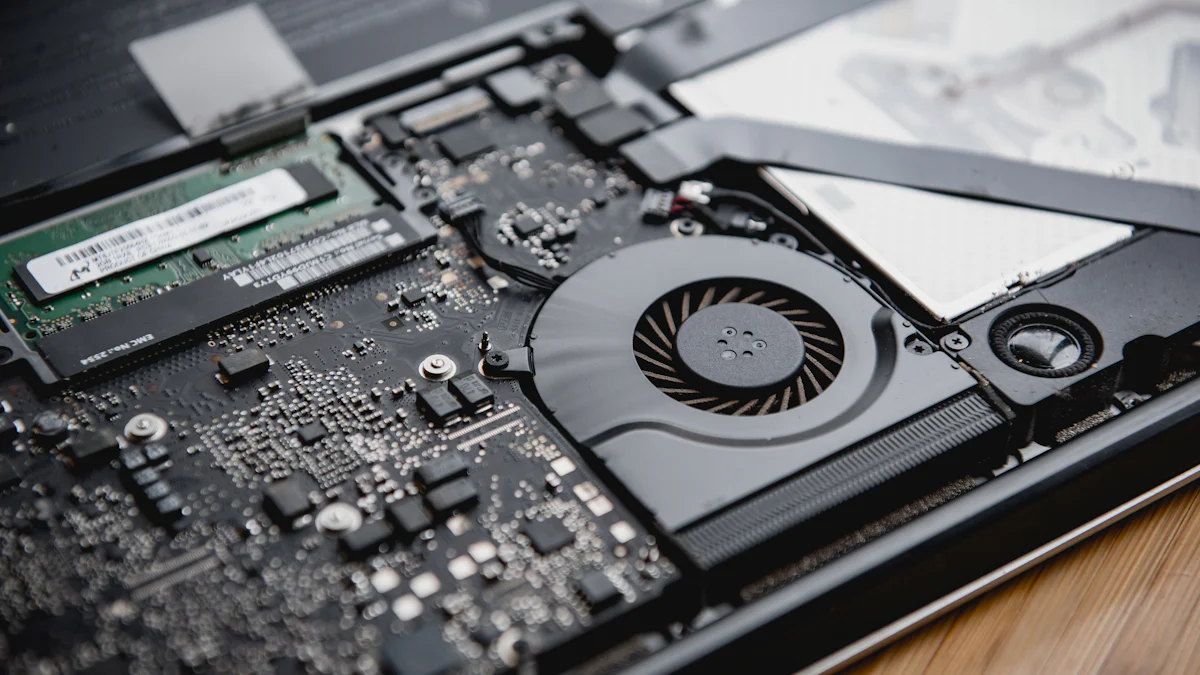
優れた耐久性と耐摩耗性
半導体製造の要求条件に耐えることができる材料が必要です。 SiCコーティングは、耐摩耗性、耐腐食性、耐摩耗性、耐腐食性、耐摩耗性、耐摩耗性、耐摩耗性、耐摩耗性、耐摩耗性、耐摩耗性、耐摩耗性、耐摩耗性、耐摩耗性、耐摩耗性、耐摩耗性、耐摩耗性、耐摩耗性、耐摩耗性、耐摩耗性、耐摩耗性、耐摩耗性、耐摩耗性、耐摩耗性、耐摩耗性、耐摩耗性、耐摩耗性、耐腐食性、耐摩耗性、耐摩耗性、耐摩耗性、耐摩耗性、耐摩耗性、耐摩耗性、耐摩耗性、耐摩耗性、耐摩耗性、耐摩耗性、耐摩耗性、耐摩耗性、耐摩耗性、耐摩耗性、耐摩耗性、耐摩耗性、耐摩耗性、耐摩耗性、耐摩耗性、耐摩耗性、耐摩耗性、耐摩耗性、耐摩耗性、耐摩耗性、耐摩耗性、耐摩耗性、耐摩耗性、耐摩耗性、耐摩耗性、耐摩耗性、耐摩耗性、耐摩耗性、耐摩耗性、耐摩耗性、耐摩耗性、耐摩耗性 耐摩耗性は表面劣化を最小限に抑え、工具や部品が長期にわたって構造的完全性を維持できるようにします。 この耐久性は、交換の頻度を減らし、時間を節約し、運用コストを削減します。 コーティングされたSiCを使用することで、過酷な条件でも、一貫して実行する装置に頼ることができます.
高い熱伝導性および安定性
熱安定性は高温プロセスの間に精密を維持するために重要です。 シスコ 温度の変動への顕著な熱伝導性および抵抗のこの区域の上塗を施してあるexcels。 装置のパフォーマンスを損なうことができるホットスポットを防止し、熱を効率的に散らす。 コーティングは、極端な熱の下で安定したままであり、製造プロセスの一貫した結果を保証します。 SiCによって塗られる、あなたの操作の質そして効率を高める信頼できる熱管理を達成できます.
化学物質の不活性および汚染防止
高品質な半導体製造に欠かせないコンタミネーション制御。 コーティングされたSiCは不純物を導入できるプロセス化学薬品との反作用を防ぐ化学不活性を提供します。 その非反応表面は汚染の危険を最小限にし、精密製造のためのきれいな環境を保障します。 このプロパティは、ウェーハとデバイスの純度を維持し、歩留まりと信頼性を向上させることができます。 SiCをプロセスに組み込むことで、汚染による欠陥から製品を守ることができます.
厳格なアプリケーションのための高い純度レベル
半導体製造の厳しい要求に応じ、高純度の材料が必要です。 わずかな不純物であっても、デバイスの性能と信頼性を損なうことができます。 SiC コーティングは 99.9995% までの印象的な純度レベルを提供し、高度なアプリケーションの厳格な基準を満たします。 この例外的な純度は、汚染のリスクを最小限に抑え、プロセスの一貫した結果を達成することができます.
高純度材料は、エピタキシャル成長などの用途に不可欠であり、精度と清潔性が重要である。 SiCコーティングは、高品質のウェーハとデバイスの生産をサポートし、安定した、汚染されていない表面を提供します。 その純度は、あなたの製造環境が制御され、欠陥を減らし、収穫を改善することを保障します。 コーティングされたSiCを組み込むことにより、製品の完全性を維持し、現代の技術の厳しい要件を満たすことができます.
「Purityは単なる要件ではありません。半導体イノベーションの礎です。」 SiCコーティングは、製造の卓越性を達成するための信頼性の高いソリューションを提供します.
SiCコーティングにより、業界最要求の厳しい仕様に合わせる材料を得ることができます。 その高純度は、最先端の半導体を製造する能力を高め、お客様のプロセスが効率的であり、お客様の製品が市場の期待を満たしていることを確認します.
半導体製造におけるSiCコーティング用途
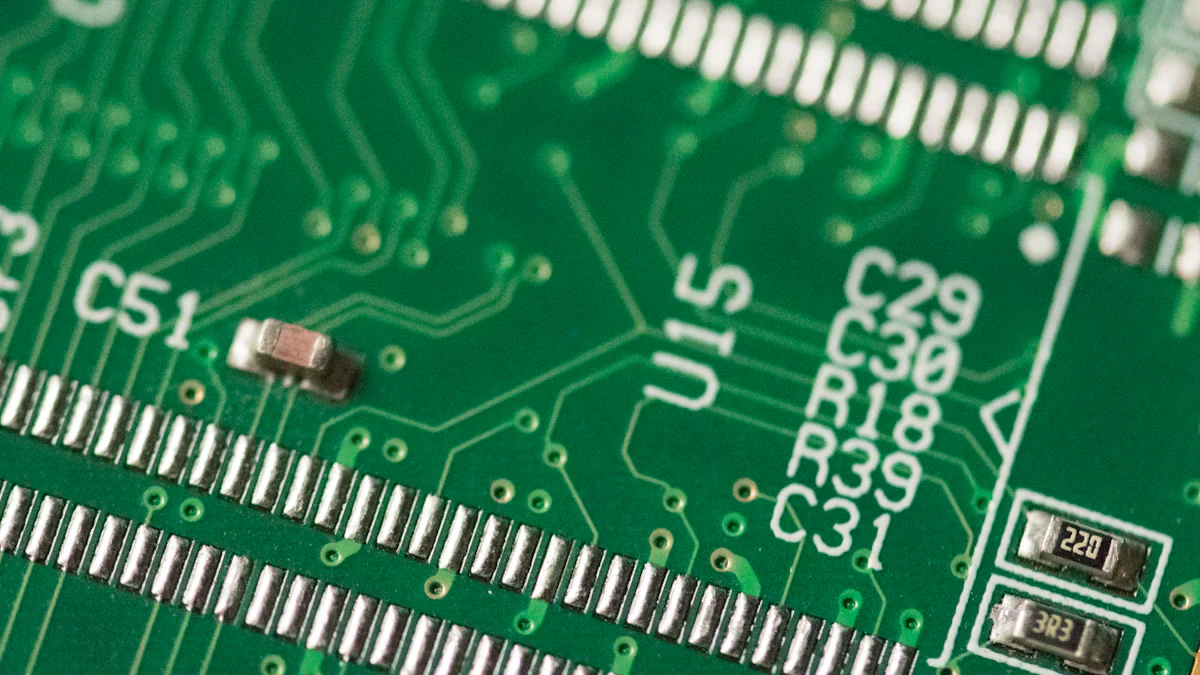
ウェーハ処理装置のための保護コーティング
半導体製造において、ウェーハ処理装置が重要な役割を果たしています。 これらのツールを使用して、ウェーハを精密に輸送および処理することができます。 しかし、研磨面への一定の暴露と過酷な化学物質は、装置を時間をかけて劣化させる可能性があります。 コーティングされたSiCは摩耗および腐食に抵抗する保護層を提供することによって強い解決を提供します。 このコーティングにより、ウェーハ処理ツールは、要求の厳しい条件下であっても、構造の完全性を維持します。 SiCコーティングを使用することで、機器のダウンタイムを削減し、運用効率を向上させることができます.
コーティングされたSiCの保護特性はまたウエハの処理の間に粒子の生成を最小に助けます。 粒子の減少により、ウェーハの品質を維持するために不可欠であるクリーナー環境が確保されます。 この高度なコーティングにより、製造工程で高い収量と一貫した性能を得ることができます.
エッチングおよび蒸着ツールの長寿を高める
エッチングや蒸着ツールは、半導体ウェーハの複雑なパターンやレイヤーを作成するために不可欠です。 これらのツールは、プラズマ、高温、反応化学物質への曝露を含む極端な条件に直面します。 時間が経つにつれて、これらの要因は、摩耗と削減ツールのパフォーマンスにつながることができます。 シスコ コーティングは腐食および化学攻撃に例外的な抵抗を提供することによってこれらの用具の耐久性を高めます。 このコーティングはより信頼できる結果を達成することを可能にするあなたの装置の寿命を拡張します.
SiCをエッチングや蒸着ツールに組み込むことで、プロセスの精度と一貫性を維持できます。 コーティングの高熱安定性により、工具が長時間の使用中でも最適に実行されるようにします。 ツールの長寿のこの改善は、メンテナンスコストを削減し、生産スケジュールの中断を減らします.
高温度処理チャンバーの性能向上
高温処理室は、アニールやエピタキシャル成長などの様々な半導体製造工程に不可欠です。 これらの部屋は、安定した汚染のない環境を維持しながら極端な熱に耐える必要があります。 シスコ 優れた熱伝導性と安定性を提供することで、これらのアプリケーションでコーティングされた排泄物。 コーティングは効率的に熱を散らばり、ホットスポットを防ぎ、室内内の均一な温度分布を保証します.
化学反応や材料劣化から加工チャンバーの内部表面を保護するためにコーティングされたSiCに頼ることができます。 その化学的不活性は、汚染のリスクを最小限に抑え、少数の欠陥で高品質のウェーハを生成するのに役立ちます。 高温チャンバーの性能を向上させることで、お客様の製造業務において、より効率性・信頼性を向上します.
「半導体製造・精密・耐久性は、非交渉可能」 SiCコーティングは、プロセスのあらゆるステップで卓越性を達成することを可能にします
LEDおよび単一水晶ケイ素のための支持のエピタキシャル成長
エピタキシャル成長は半導体製造のコーナーストーンです。 あなたは、LEDと単結晶シリコン用の高品質のレイヤーを作成するために、このプロセスに依存しています。 デバイスの性能を損なう可能性があるため、この段階では、精度と純度が極めて重要です。 SiCコーティングは、これらの厳格な要件を満たす理想的なソリューションを提供します.
シスコ コーティングは、エピタキシャル成長のための安定した汚染のない表面を提供します。 その化学的不活性は、プロセス中に不要な反応が起こることを確実にします。 この安定性は、あなたの材料の完全性を維持するのに役立ちます, 欠陥のない層をもたらす. コーティングの高純度で、99.9995% まで到達し、この用途の適合性を高めます。 要求の厳しい環境でも、一貫した結果を届けるために信頼できます.
熱管理は表軸成長の重要な役割を担います。 シスコ 注目の熱伝導性で、このエリアでコーティングされたエクセル。 それは効率的に熱を散らす、あなたの層の均等性を破壊できるホットスポットを防ぐ。 ウェーハが希望する品質と厚さを達成することを保証します。 SiCコーティングを使用することで、熱プロセスを最適化し、作業の全体的な効率を向上させることができます.
「エピタキシャル成長の予測は、半導体イノベーションの未来を定義します。 シスコ コーティングは、比類のない信頼性で、この精度を達成することを可能にします
高温に耐えることができるLEDの生産の要求材料のような適用は安定性を維持します。 シスコ コーティングは、これらの課題を容易に解決します。 熱応力に対する耐久性と耐性は、ガリウム窒化物(GaN)および他の先進材料の成長をサポートする信頼性の高い選択肢になります。 この高度なコーティングをプロセスに組み込むことで、LEDのパフォーマンスと長寿を向上させることができます.
単一水晶ケイ素のために、塗られるSiCは強い基礎を提供します。 その非反応表面は汚染リスクを最小限に抑え、不純物なしで結晶が成長することを確認します。 この純度は、大規模な集積回路やその他のハイテクアプリケーションを製造するために不可欠です。 コーティングされたSiCを利用することで、単結晶シリコン製造の優れた結果を得ることができます.
あなたのエピタキシャル成長プロセスに上塗を施してあるSiCを組み込むことは複数の利点を提供します:
- 層の質の改善: LEDやシリコンウェーハ用の欠陥のない均一なレイヤーを実現します.
- 高められた熱管理: 最適な成長条件のための一貫した温度を維持します.
- 汚染リスクの低減: 不純物や欠陥から材料を保護します.
- プロセス効率の向上: ダウンタイムを最小化し、歩留まりを最大化します.
シスコ コーティングは、より信頼性と効率的なプロセスにエピタキシャル成長を変換します。 業界最高水準の最先端半導体製造能力を発揮します。 この高度なコーティングにより、半導体製造の競争力のある風景に先立ちます.
半導体業界向けSiCのメリット
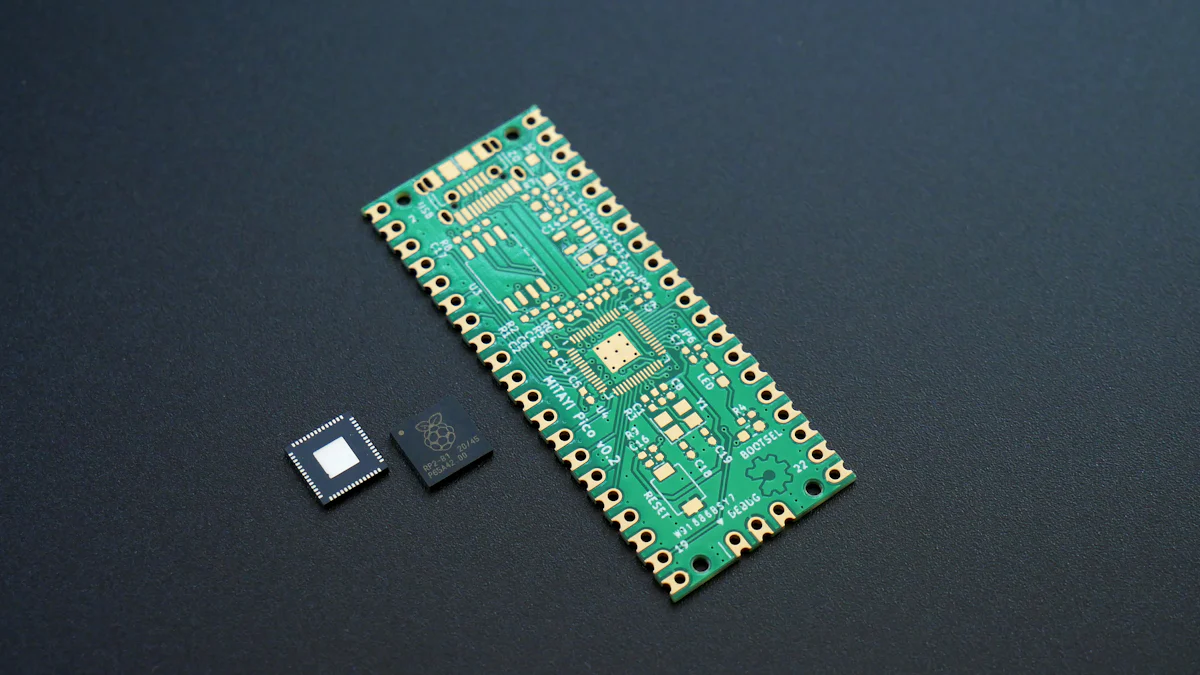
装置寿命の増加とメンテナンスコストの削減
長持ちする機器が必要で、確実に実行できます。 シスコ コーティングは摩耗、腐食および熱圧力に例外的な抵抗を提供することによってあなたの用具および機械類の寿命を高めます。 この耐久性は、お客様の機器が最も要求の厳しい環境でも機能し続けることを保証します。 交換頻度を削減することで、運用コストを削減し、生産ダウンタイムを最小限に抑えます.
コーティングされたSiCを使用する場合、メンテナンスは負担を軽減します。 堅牢なプロパティは、損傷の可能性を低下させ、機器が長期にわたってスムーズに動作できるようにします。 製造プロセスを最適化するために、より少ないリソースを修復し、より集中することができます。 装置の長寿のこの改善は重要なコスト節約および高められた生産性に翻訳します.
プロセス効率および収穫の強化
半導体製造における効率性が重要である。 シスコ さまざまな用途で一貫した性能を発揮し、プロセスの効率性を高めます。 高い熱伝導性および化学的不活性により、製造条件の精密な制御が可能になります。 この精度は、より高い収量につながる少数のエラーでより良い結果を達成するのに役立ちます.
汚染を防ぐコーティングの能力は、プロセスの完全性を維持する上で重要な役割を果たします。 不純物を最小限にすることで、ウェーハやデバイスを少ない欠陥で生成できます。 欠陥を直接低減することで、品質を損なうことなく、出力を最大化できます。 シスコ コーティングは、お客様の業務を合理化し、製造工程の各工程で効率性を高めます.
製品の品質・信頼性の向上
半導体業界におけるお客様の成功を確かなものにします。 シスコ コーティングは、汚染、熱安定性、材料劣化などの重要な課題に取り組むことで、製品が最も高い基準を満たしていることを確認します。 高い純度と化学的安定性は、欠陥のないウェーハやデバイスを製造するための理想的な環境を作り出します.
信頼性は、SiCをプロセスに組み込むと、製品の特徴になります。 コーティングの優れた特性は、極端な条件下でも、一貫した性能を保証します。 この信頼性はあなたのプロダクトの評判を高めます、それらを市場で競争させます。 SiCコーティングを使用することで、現代の技術の要求を満たす高品質の半導体を提供できます.
「品質と信頼性は、半導体イノベーションの礎石です。 シスコ コーティングは、あなたの製品が競争力のある業界で際立っていることを確実にするために、あなたが両方を達成するのに役立ちます
半導体・その他ハイテク産業における汎用性
シスコ 半導体製造だけでなく、様々なハイテク業界にも及ぶ価値ある資産を発揮する、驚くべき汎用性を発揮します。 独自の特性により、多様な用途での課題に対応し、最適な性能と信頼性を実現します.
半導体を超えて拡大する
半導体製造においてSiCコーティングされたエクセルは、その利点は他の先進分野に及ぶ。 高い熱伝導性、化学的不活性、および以下のような産業の卓越した耐久性を活用することができます
- エアロスペース: シック 上塗を施してあるは極度な温度および腐食性の環境に露出される部品の性能を高めます。 軽量で堅牢な性質により、航空宇宙用途にも最適で、精度と信頼性が重要になります.
- 原子力エネルギー: : : 放射線に抵抗し、高温下での安定性を維持するためのコーティングの能力は、原子力原子炉の安全性と効率を保証します。 このデマンドフィールドで重要なコンポーネントの長寿を改善するためにコーティングされたSiCに依存することができます.
- 自動車産業: SiCコーティングの熱管理機能により、電気自動車(EV)と高性能エンジンのメリット パワーエレクトロニクスなどの重要なシステムの信頼性を確保し、効率的な放熱をサポートしています.
- 高速レール:SiCコーティングは、高速レールシステム内のコンポーネントの耐久性と効率性に貢献します。 その耐久性および熱安定性は厳密な条件の下で性能を維持するための信頼できる選択をします.
新興技術のイノベーションを支える
テクノロジーが進化するにつれて、イノベーションを続けることができる材料の需要が増えています。 シスコ コーティングは最先端の分野のブレークスルーの基礎を提供します:
- ソーラー太陽光発電: シック ソーラーパネルの効率性と耐久性を高めます。 高い純度および熱安定性は粗い屋外の環境の一貫した性能、を保障します.
- LEDライト 製造業: : : コーティングは、エピタキシャル成長のための安定した汚染のない表面を提供することにより、高品質のLEDの生産をサポートしています。 これにより、エネルギー効率の高い照明やディスプレイの需要が高まっています.
- Quantumコンピューティング: SiCコーティングの優れた純度と安定性により、量子計算アプリケーションに適したため、精度と材料の完全性がパラマウントされます.
業界全体でのメリット
SiC をプロセスに組み込むことで、複数の部門に適用するいくつかの利点へのアクセスを得ることができます
- 高められた構成の寿命: : : コーティングの耐摩耗性と耐久性は、頻繁な交換の必要性を減らし、時間とリソースを節約します.
- 改善された効率: : : 熱伝導性および化学不活性は性能を最大限に活用し、要求する適用の一貫した結果を保障します.
- 汚染リスクの低減: : : コーティングされたSiCの高純度は不純物を最小限にし、製品の品質と信頼性を維持するのに役立ちます.
「汎用性はイノベーションの枠組みです。 シスコ コーティングにより、多様な産業の普及、進展、信頼性の向上に寄与します
シスコ コーティングされた各業界のユニークな要件に適応し、課題を克服するための信頼性の高いソリューションを提供します。 半導体、宇宙空間、再生可能エネルギーのいずれにも関わらず、この高度なコーティングにより、お客様のプロセスが効率的で、製品が最も高い基準を満たしていることを確認します.
シスコ 半導体製造における課題を克服するための変革ソリューションを提供します。 そのユニークな特性は耐久性、熱安定性、および汚染抵抗を改善し、より高い効率と優れた製品品質を達成することができます。 この高度なコーティングをプロセスに統合することにより、一貫した性能を確保し、競争力を維持することができます。 半導体業界が進化し続けています。SiCコーティングはイノベーションを推進し、信頼性と精度で近代的な技術の要求に応えます.
よくあるご質問
SiCコーティングと半導体製造のメリットとは?
シスコ シリコンカーバイドコーティングは、半導体製造における装置や工具の性能を高めるよう設計されています。 それは例外的な耐久性、熱安定性および化学薬品の不活性を提供します。 これらの特性は材料の劣化を減らし、プロセス効率を改善し、製品品質を維持するのに役立ちます.
SiCコーティングは機器の寿命を改善する方法は?
シスコ 上塗を施してあるは優秀な耐久性および腐食の保護を提供します。 それは研摩プロセスおよび粗い化学薬品からあなたの装置を保護します、より長い操作上の生命を保障します。 頻繁な交換の必要性を減らすことによって、それは維持費を節約し、ダウンタイムを最小にします.
半導体製造において高い純度が重要なのはなぜですか?
高い純度は、製造プロセスが汚染から解放されることを保障します。 ウェーハやデバイスの品質を損なう可能性も軽微な不純物。 シスコ 上塗を施してあるは99.9995%までの純度のレベルを達成しま、それに厳しい物質的な指定を必要とする適用のために理想的にします.
缶SiC 上塗を施してある抵抗の高温か?
はい、SiC 高温環境での耐摩耗性に優れています。 その驚くべき熱伝導性と安定性により、構造の完全性を失うことなく極端な熱に耐えることができます。 この機能は、アニールやエピタキシャル成長などのプロセス中に一貫した性能を保証します.
SiCコーティングは汚染を防ぎますか?
シスコ コーティングはプロセス化学薬品との反作用に抵抗する化学的に不活性の表面を備えています。 製造環境に不純物を導入するリスクを最小限に抑えます。 SiCコーティングを使用することで、ウエハやデバイスの純度を維持できます.
SiCコーティングによる半導体製造のメリットは何ですか?
シスコ 上塗を施してあるは多目的であり、さまざまな適用を、を含む支えます:
- ウェーハの処理装置のための保護コーティング.
- エッチングや蒸着工具の耐久性を高めます.
- 高温処理室での性能向上.
- LEDおよび単一水晶ケイ素のための支持のエピタキシャル成長.
SiCは半導体を越える企業に適していますか?
はい、SiCコーティングは複数のハイテク業界を横断する汎用性を示しています。 航空宇宙、原子力、自動車、高速鉄道、太陽光発電に使用されます。 そのユニークな特性は、これらの分野での要求の厳しいアプリケーションのための信頼できる選択になります.
SiCコーティングはプロセス効率を高めますか?
シスコ 一貫した熱管理および汚染の危険を減らすことによってコーティングされた改善の効率。 高い熱伝導性は精密な温度制御を可能にし、化学不活性は欠陥を防ぎます。 これらの要因は、より高い収量とより良い結果を達成するのに役立ちます.
SiCは費用効果が大きい解決に塗りましたか?
シスコ コーティングは、機器の寿命を延ばし、メンテナンスニーズを最小限に抑えることで、運用コストを削減します。 その耐久性はより少ない取り替えを保障します、そして汚染の防止機能は収穫を改善します。 これらの利点は、時間の経過とともに重要なコスト節約に翻訳します.
製造プロセスにSiCコーティングを組み込む方法は?
重要なツールや機器に適用することで、SiC コーティングをプロセスに組み込むことができます。 一般的な用途には、ウエハ処理システム、エッチングツール、高温チャンバーなどがあります。 VET ENERGYのエキスパートに相談して、特定のニーズに最適なソリューションを決定します.