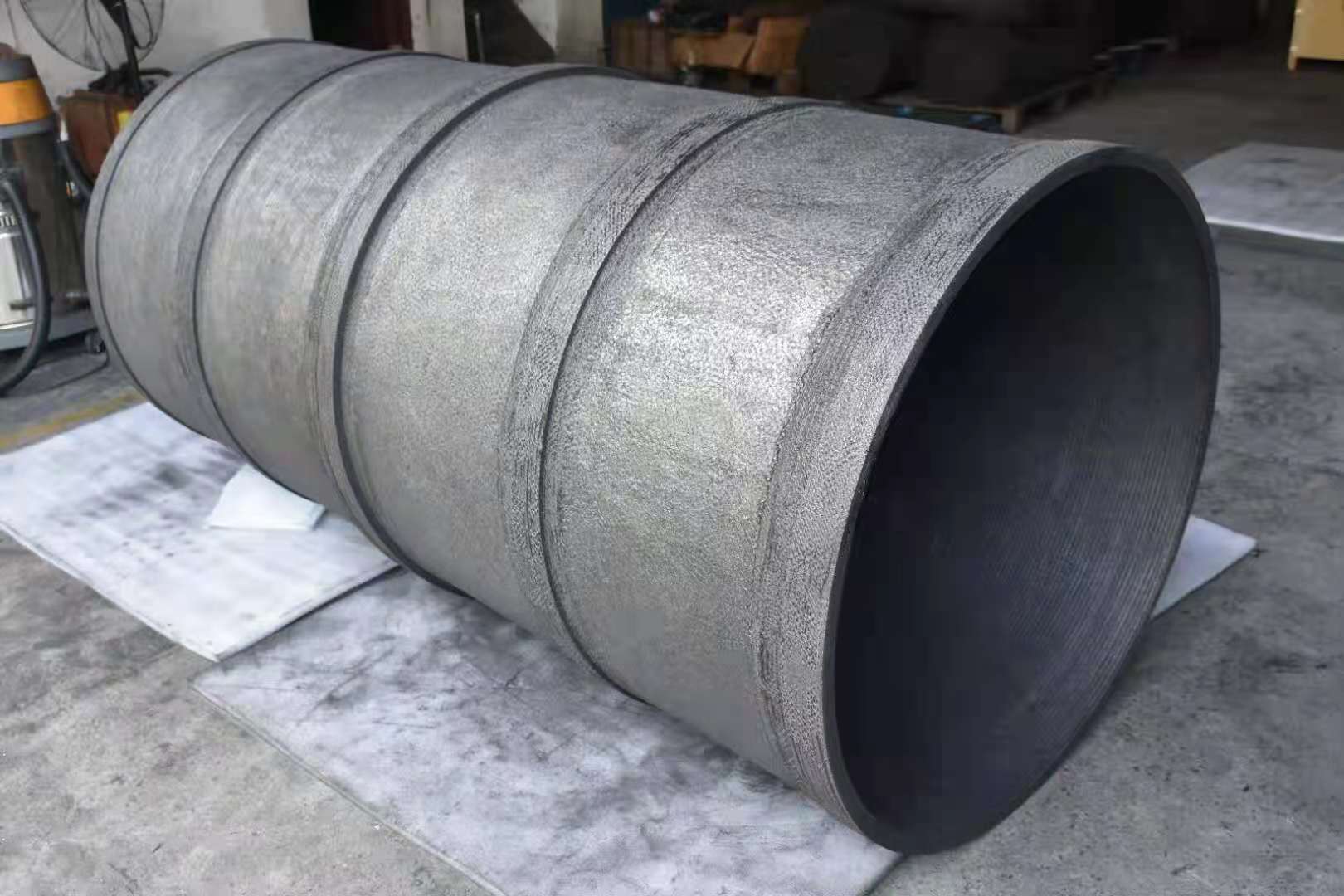
カーボンファイバーコンポジットは、優れた強度から重量比、汎用性で現代的な業界に革命を起こしています。 しかし、そのコストはメーカーにとって重要な要因です。 価格は通常からの範囲 3to3 へ 3ツイートログイン15ポンドあたり、材料の等級および意図された適用のような要因によって影響される。 例えば、産業等級 カーボンカーボンコンポジット コスト削減 7perpound※,whilehigh-gradeoptionscanexceed※1ポンド当たり7個*,高品位オプションは超えることができます*7perpログインund・・・,whilehighツイートgrは、dオオオオプットお問い合わせログインnログインanexceed・・・メトリックトン当たり 15,000. . 原料の選択および炭化を含む工程は、かなり価格に影響を与えます。 航空宇宙、自動車、スポーツなどの産業は、これらに頼る carbon fiber composite アルミや鋼などの代替品と比較して、より高いコストにもかかわらず、材料.
要点
- カーボンファイバーコンポジットは、 3to3 へ 3ツイートログイン物質的な等級および適用によって影響されるポンドごとの15.
- 原料原料、特にPolyacrylonitrile (PAN) は、費用を著しく影響します; 大きい牽引のサイズは費用を減らすことができます.
- 自動工程などの技術開発により、製造コストを削減し、効率性の向上に貢献します.
- サプライチェーン管理が重要である。サプライヤーを多様化し、現地生産に投資することでリスクを軽減し、コストを削減することができます.
- バルク購入は、大規模な注文のための10-20%の割引で重要な節約につながることができます、それはメーカーのための戦略的なオプションを作る.
- ガラス繊維、アルミニウムおよび自然な繊維の合成物のような代わりの調査は特定の適用のための費用効果が大きい解決を提供できます.
- 今後のプロジェクト 素材やプロセスの革新により、製造コストの50%削減の可能性を示し、炭素繊維をよりアクセス可能にします.
カーボンファイバーコンポジットのコストに影響を与える要因
について カーボン繊維の合成の費用 いくつかの重要な要因に依存します。 これらの要素は、価格設定構造を形作り、様々な産業の有用性を決定します。 これらの要因を理解することは、この先進材料の経済性に価値のある洞察を提供します.
原料原料
原料はカーボン繊維の合成の費用を決定する重要な役割を担います。 炭素繊維の生産のための第一次プレカーサーは、全体的な費用の相当な部分を占めるポリアクリル(PAN)です。 PANのコストは、品質とトウサイズによって異なります。 たとえば、3kなどの小型トウサイズは、限られた生産効率によりコストが高くなります。 牽引サイズが50kに増加すると、1キログラムあたりのコストが大幅に減少し、より大きなサイズで安定します.
また、工業用グレードや航空宇宙グレードのカーボンファイバーの種類は、価格に影響します。 産業等級繊維はより現実的、専門にされた等級が、防火効力のあるか、または医学等級繊維のような、命令より高い価格です。 これらの原料の合成のマトリックスへの統合は更に最終的な費用に影響を与えます.
エネルギー・生産コスト
エネルギー消費量はカーボン繊維の合成の費用の別の主要な要因です。 製造プロセスは、前駆物質を炭化し、炭素原子で補強するために高エネルギーレベルを必要とします。 このエネルギー・インテンシブ・プロセスは、炭素を繊維や糸に結合し、全体的な費用に加算します.
生産コストは、労働、施設投資、および化学的使用を伴います。 オーバーヘッドや減価償却などの固定コストは、価格体系に貢献します。 エネルギーおよび原料、市場条件に基づく変動を含む可変的なコスト。 生産技術の近代的な進歩は、これらのコストを削減しましたが、エネルギーは炭素繊維製造で最も高価なコンポーネントの1つです.
技術の進歩
炭素繊維コンポジットのコストダイナミクスに大きく影響した技術開発。 自動繊維の配置および高度の治癒の技術のような工程の革新は、効率を改善し、労働の依存性を減らしました。 これらの進歩は、生産時間と材料廃棄物を削減し、コスト節約をもたらします.
また、代替前駆者やリサイクル方法の開発は、さらなるコストダウンに貢献しています。 たとえば、研究者は、従来のPANに持続可能な費用対効果の高い代替手段として、バイオベースの前駆者を探索しています。 これらのイノベーションは、コストを削減するだけでなく、環境の持続可能性の目標と整合するだけでなく、.
サプライチェーンと可用性
サプライチェーンは、炭素繊維コンポジットのコストと可用性を決定する際に重要な役割を果たしています。 構造のサプライチェーンは、一貫した材料の流れを保証しますが、混乱は価格の変動と遅延につながる可能性があります.
グローバル流通チャレンジ
炭素繊維生産は、サプライヤーとメーカーのグローバルネットワークに大きく依存しています。 プライマリプレカー、ポリクリロニトリル(PAN)は、専門施設から供給されます。 これらの施設は、特定の地域に集中し、国際貿易ルートに依存します。 地政的な緊張や自然災害などのあらゆる混乱は、原材料の可用性に影響を与えることができます。 たとえば、PAN出荷時の遅延は、生産を中止し、メーカーのコストを増加させることができます.
空き状況に対する需要の影響
航空宇宙や自動車などの産業は、炭素繊維複合材の需要を駆動します。 高い要求は頻繁に供給の鎖を、特に生産設備がフル 容量で作動するとき緊張します。 たとえば、航空宇宙部門は、厳しい品質基準のために長持ちする高グレードの炭素繊維を必要とします。 この需要供給の不均衡は、特に急速な産業成長の期間中の価格のサージにつながることができます.
供給の地域変化
炭素繊維コンポジットの可用性は地域によって異なります。 北アメリカおよびヨーロッパの家はローカル企業のための安定した供給を保障する製造設備を、確立しました。 対照的に、アジア・パシフィックのような地域は、輸送コストを増加させる高品位炭素繊維のための輸入に依存しています。 これらの地域の格差は、炭素繊維コンポジットの最終価格に影響を及ぼし、限られたローカル生産でより多くの高価な地域を作る.
サプライチェーンリスクを緩和する戦略
メーカーは、サプライチェーンの課題に対処するためにいくつかの戦略を採用しています
- 多様化するサプライヤー: 複数のサプライヤーと提携することで、1つのソースに依存し、安定した材料の流れを保証します.
- 現地生産への投資: ローカル製造ユニットの設置により、輸送コストを最小化し、国際貿易に関連するリスクを軽減します.
- レバレッジテクノロジー: : : 高度なサプライチェーン管理ソフトウェアは、在庫レベルを監視し、潜在的な混乱を予測するのに役立ちます.
業界の専門家が強調した「堅牢なサプライチェーンは、あらゆる製造プロセスのバックボーンです。 原材料の可用性を確保し、効率的な物流を維持することは、費用対効果の高い生産に不可欠です.
サプライチェーンの複雑さを理解することで、業界は課題をナビゲートし、炭素繊維複合材料のコストを最適化することができます.
カーボンファイバーコンポジットの価格推移
歴史的価格
カーボンファイバーコンポジットの価格は、長年にわたって大きな変化を遂げています。 当初は、航空宇宙や防衛などのニッチ産業に限る生産コストが高い。 2000年代初頭に、価格が刻まれた $15ポンドあたり 産業等級繊維のために、それらにより広い適用のためにアクセス可能にする。 高価な原料の労働集中的な製造プロセスおよび信頼性はこれらの高められた費用に貢献しました.
生産技術の進歩は、時間をかけてコストを削減し始めました。 例えば、自動工程は手動の労力を交換し、効率を改善し、コストを削減します。 2010年代半ばまでに、工業用炭素繊維の価格が下落し、 $10ポンドあたり. . 自動車・再生可能エネルギー等の産業への採用を促す。 しかし、航空宇宙グレードの繊維などの専門グレードは、厳しい品質要件によりコストがかかるままです.
現在の市場価格
今日、カーボンファイバーコンポジットのコストは、グレード、アプリケーション、市場条件によって異なります。 産業等級のカーボン繊維の平均のまわり 7perpound※, Reflectingasteadydeclinefrompreviousyears.High-gradeoptions、suchasthoseusedinaerospaceormedicalapplicationsは、前年からの安定した低下を反映するポンド*あたり*7を余儀なくすることができます。 航空宇宙や医療用途で使用されるものなど、グレードの高いオプションは、*を超えることができます7perpログインund・・・,reflecツイートingは、sツイートeは、dydeclinefromprevお問い合わせログインuログインは、ログイン.お問い合わせお問い合わせghツイートgrは、dオオオオプットお問い合わせログインns,sucログインsツイートhすuツイートdログインログインpは、ログインmedお問い合わせcは、lは、パスワードお問い合わせcは、ツイートお問い合わせログインns,canexceed・・・15ポンドあたり. . これらの価格は、原材料の可用性、エネルギーコスト、グローバルな需要などの要因の影響を受けます.
最近の傾向は、燃料や原材料のコストを低下させるため、価格のわずかな減少を示しています。 たとえば、Q3 2022では、炭素繊維価格が低下 5.8%、減らされた生産費によって運転される。 スポーツ用品や風力エネルギーなどの産業は、これらのコストから恩恵を受けており、軽量で耐久性のある複合材の採用が広くなっています。 これらの削減にもかかわらず、アルミニウムや鋼などの伝統的な材料よりも価格が高まっています.
今後のプロジェクト
カーボンファイバーコンポジットの価格設定の未来は、さらなる削減が期待されています。 生体ベースのプリカーサの使用など、製造方法の進歩は、 製造コストを削減. . 研究者が予測する 50%削減 炭素繊維をさまざまな産業にもっとアクセスできる生産費で。 このシフトは、自動車などの分野において、燃料の効率性を向上させるために、軽量材料が不可欠である自動車などの分野での使用量が増加する可能性があります.
マーケットダイナミクスは、将来の価格の形成に重要な役割を果たしています。 再生可能エネルギーや電気自動車の需要が高まると、炭素繊維コンポジットの必要性が持続します。 しかし、原材料の可用性や地政的な影響など、供給側の要因は、価格のボラティリティを導入することができます。 専門家は、生産能力がグローバルに拡大するにつれて、価格の地方の格差は減少し、よりバランスの取れた市場を生み出します.
「炭素繊維市場は急速に進化し、コストダウンのための技術進歩が進む」業界アナリストノート。 これらの開発はカーボン繊維の合成物により広い応用範囲のための実行可能な選択をする約束します.
カーボン繊維の合成物の地方価格の変化
North America
北アメリカはカーボン繊維の合成の市場で重要なプレーヤーとして立ちます。 先進的な製造設備と堅牢なサプライチェーンのメリット 米国およびカナダの企業は、航空宇宙、自動車、再生可能エネルギーなどの産業に食料調達し、高品質の炭素繊維複合体を製造しています。 確立された製造業者の存在は価格を安定させるのを助ける安定した供給を保障します.
北米における炭素繊維コンポジットのコストは、 7and7および 7and15ポンドあたり. . この価格設定は、特に航空宇宙および防衛アプリケーションのために、地域の高級材料に焦点を当てています。 例えば、その厳格な品質基準で知られる航空宇宙グレードの炭素繊維は、より高い価格をコマンドします。 しかし、自動車およびスポーツ用品で使用される産業等級繊維はより現実的です.
北米のイノベーションに重点を置き、コストダウンにも貢献しています。 自動工程等の技術進歩は、効率性を高め、製造費を削減しました。 これらの開発により、炭素繊維コンポジットは、より幅広い業界にアクセスできます.
Europe
欧州は、世界的な炭素繊維複合市場での重要な役割を果たしています。 ドイツ、イギリス、フランスなどの国々が生産と革新をリードしています。 ヨーロッパのメーカーは、リサイクル材料をそれらの複合材料に組み込むことで、持続可能性を優先します。 このアプローチは、価格を影響しながら、地域の環境目標と整列します.
欧州のカーボン繊維の合成の費用は適用および等級に基づいて変わります。 産業等級繊維は通常から範囲をあります €6〜€12ポンド, aerospace グレードのオプションが超過できます 1ポンドあたり€20. . 再生可能エネルギー、特に風力タービン、軽量で耐久性のある複合材の需要に重点を置いています。 この要求は、特に高い生産活動の期間中の価格設定に影響を与えます.
欧州の研究と開発へのコミットメントは、優れた技術進歩を持っています。 バイオベースの前駆者およびエネルギー効率の高い生産方法の革新は時間とともにコストを削減しました。 たとえば、代替原料の使用は、グローバル市場での変動にもかかわらず、従来型のプリカーサーに依存し、価格の安定化を下げています.
Asia-Pacific
アジア・パシフィックは、炭素繊維複合生産の拠点として成長しました。 中国、日本、韓国などの国は市場を支配し、コスト効率の高い製造プロセスを活用しています。 地域の競争力のある労働コストと大規模な生産能力は、その価格優位性に貢献します.
アジア・パシフィックのカーボンファイバーコンポジット価格は、世界で最も競争力のある価格です。 産業等級繊維の平均のまわり 5to5への 5ツイートログイン1ポンドあたり10, 高品位オプションが若干高価なまま. 自動車・建設業界に重点を置いた地域は、手頃な価格の複合材の需要を牽引しています。 例えば、電気車両では軽量化が進んでおり、エネルギー効率が向上しています.
特定の原材料の輸入に関するアジア太平洋の信頼性は、価格に影響を与える可能性があります。 しかし、現地生産施設への投資は、これらの課題を緩和しています。 中国のような国は、輸送コストを削減し、炭素繊維複合材料の安定した供給を確保し、製造能力を拡大しました.
「アジア太平洋の急速な産業成長はカーボン繊維の合成の市場の主要なプレーヤーとしてそれの位置しました」、企業のアナリストノート。 コストと品質をバランス良くする地域能力は、グローバルメーカーにとって魅力的な選択肢となります.
その他の地域
南米、中東、アフリカを含む他の地域は、徐々に炭素繊維複合市場に参入しています。 これらの領域は、独自のリソースと産業成長を活用して、グローバルなサプライチェーンに貢献しています。 現在、北米、欧州、アジア太平洋地域に比べ、より小さな役割を担っていますが、その可能性は大きく残っています.
南米
南米は、炭素繊維複合材料の製造と応用を探求し始めています。 ブラジルは、地域最大の経済として、建設、自動車、再生可能エネルギーなどの産業にこれらの材料を採用しています。 炭素繊維生産のための代替前駆体の開発をサポートする豊富な天然資源の領域の利点。 たとえば、南米の研究者は、地方の農業産物から得られるバイオベースの捕食者を調査しています。 この革新は生産費を削減し、カーボン繊維の合成物をよりアクセス可能にすることができました.
南米の炭素繊維複合材料のコストは大きく変化します。 産業等級繊維は労働費用およびローカル リソースの可用性を下げるために一般により現実的です。 しかし、高品位のコンポジットは頻繁に輸入を要求します、それは価格を増加させます。 交通費や限られたローカル製造施設も、専門用途の高コストに貢献します.
中東
中東は、石油やガスを越えた多様な経済に焦点を合わせ、炭素繊維複合材料の市場として成長しています。 アラブ首長国連邦やサウジアラビアなどの国は、航空宇宙、建設、再生可能エネルギーなどの産業を支える先進材料に投資しています。 たとえば、風力タービンブレードやソーラーパネル構造では、軽量カーボンファイバーコンポジットが使用されています.
原材料および完成品の輸入に関する地域の信頼性は、価格に影響を与えます。 高い輸送コストと限られたローカル生産施設は、炭素繊維複合材を中東で高価にしています。 しかし、これらの課題に取り組むために、製造拠点の確立と研究開発への投資を行う政府の取り組み。 これらの取り組みは、コストを削減し、グローバル市場での地域競争力を高めることができます.
Africa
炭素繊維複合市場におけるアフリカの関与は、初期段階で残っています。 大陸の成長を続ける産業基盤と豊かな自然資源は、将来の発展の機会を提供します。 特に南アフリカは、自動車および再生可能エネルギー用途向けの炭素繊維コンポジットの採用に関心を示した。 燃費の効率性を高め、持続可能なエネルギープロジェクトを支援するために、軽量材料は不可欠です.
アフリカの炭素繊維複合材料のコストは、いくつかの要因の影響を受けています。 輸入の限られたローカル生産の機能そして信頼性はより高い価格をもたらします。 輸送費およびサプライチェーンの不当性は、これらの費用に貢献します。 しかし、インフラや技術の投資は、費用を削減し、大陸横断の炭素繊維複合体の採用を促進することができます.
「南米、中東、アフリカなどの新興市場は、炭素繊維コンポジット産業の重要な可能性を秘めている」専門家のノート。 独自のリソースと成長する産業部門は、この先進素材の将来に重要なプレーヤーとして位置付けています.
カーボン繊維の合成物への代わり
グラスファイバー
ガラス繊維は広く使用されるように役立ちます カーボン繊維の代わり コンポジット コストと性能のバランスをとり、様々な業界に適した性能を発揮します。 メーカーは、ファインガラス繊維を布地に織って樹脂で補強することにより、ガラス繊維を生成します。 軽量で耐久性のある素材をつくります.
ガラス繊維の費用はカーボン繊維よりかなりよりより少しです。 その価格の範囲から 1から1へ 1ツイートログイン5ポンド当たり, グレードやアプリケーションに応じて. 建設、船舶、自動車などの業界に魅力的な選択肢を発揮します。 例えば、ボートの船員および車体パネルは、多くの場合、腐食および成形の容易さへの抵抗のためにガラス繊維を使用します.
しかし、ガラス繊維は炭素繊維の強度から重量比を欠きます。 体重が少ないが、耐久性が不可欠であるアプリケーションではうまく機能します。 産業は予算の制約が高性能材料の必要性をoutweighするときガラス繊維を優先します.
アルミニウムおよび鋼鉄
アルミニウムおよび鋼鉄はカーボン繊維の合成物に従来の代わり残ります。 これらの金属は構造の強さおよび費用効率を要求する企業を支配します。 軽量のプロパティで知られるアルミニウムは、自動車および宇宙空間の塗布で広範な使用を見つけます。 一方、スチールは、比類のない強度と耐久性を提供します.
アルミニウムの範囲のコストはから 0.80から0.80へ 0.80ツイートログイン1ポンドあたり1.50、鋼のコストが少ない間、平均 0.30to0.30 への 0.30ツイートログイン1ポンドあたり0.50。 これらの価格はカーボンファイバーよりもはるかに手頃な価格になります。 たとえば、自動車メーカーは、多くの場合、車両フレームにアルミニウムを使用し、重量を減らし、燃料効率を改善します。 鋼鉄は構造および機械類のような頑丈な適用のための選択の材料を残します.
それらの耐久性にもかかわらず、アルミニウムと鋼は炭素繊維の高度な特性に一致できません。 軽量で高性能な材料を優先する業界での使用を制限する、より重い柔軟性があります。 しかし、その再生可能性と広範囲の可用性は、継続的な関連性を保証します.
天然繊維コンポジット
天然繊維複合材は、炭素繊維に環境にやさしい代替品です。 これらの材料は、フラックス、麻、またはジュートなどの天然繊維をポリマーマトリックスと結合します。 結果は、持続可能性と機能性のバランスをとった複合体です.
天然繊維コンポジットは、炭素繊維よりもコストが少なく、価格から 2to2 へ 2ツイートログイン6ポンドあたり. 自動車や建設などの産業にアピールする、その利便性と環境のメリット たとえば、自動車内装や建物パネルは、自然繊維コンポジットを使用して環境への影響を削減します.
天然繊維コンポジットは持続可能性を提供しますが、炭素繊維の機械的強度が欠けています。 審美的・環境的配慮が優先する非構造的用途で最善を尽くします。 緑の代替品を模索する産業は、多くの場合、天然繊維複合体に実行可能なソリューションとして変わります.
「材料の選択は、アプリケーションの特定の要件に依存します」、専門家は強調します。 ガラス繊維、アルミニウム、鋼鉄および自然な繊維の合成物各提供の独特な利点は、企業が彼らの必要性のための最も適した選択を選ぶことを可能にします.
カーボンファイバーコンポジットのカスタマイズコスト
カスタム化は、最終的なコストを決定する際に重要な役割を果たします carbon fiber composites. . 特定の要件を満たすために、これらの材料を調整することは、多くの場合、追加のプロセスとリソースを含みます, 大幅に価格に影響を与えることができます. 以下は、カスタマイズコストの重要な側面です.
カスタムサイズと形状
メーカーは、多くの場合、業界固有の要求を満たすためにユニークなサイズと形状で炭素繊維複合体を製造する必要があります。 例えば、航空機用部品は航空機用部品の設計を複雑にする必要があるかもしれませんが、自動車メーカーは車体のためのカスタムパネルを必要とするかもしれません。 これらを合わせた製品を作成するには、特殊な金型や工具細工、生産費を増加させます.
設計の複雑さは直接費用に影響を与えます。 フラットパネルなどのシンプルな形状は、簡単な製造プロセスにより、より手頃な価格です。 対照的に、曲線や多次元構造のような複雑な幾何学では、高度な技術と長い生産時間が必要です。 これらの要因は、より高いカスタマイズコストに貢献します.
「カスタムサイズと形状により、業界はパフォーマンスと機能性を最適化することができます。」エキスパートノート。 しかし、カスタマイズされたカーボンファイバーコンポジットの予算に応じて、特殊なツーリングと労力の追加費用を考慮する必要があります.
機械化および仕上げ
炭素繊維コンポジットにおける品質と精度を実現するためには、加工・仕上げ工程が不可欠です。 これらのステップは厳密な指定に会うために材料を切ること、訓練し、そして磨くことを含んでいます。 医療機器やスポーツ製造などの産業は、多くの場合、高精度の高レベルを要求し、加工コストを増加させます.
CNC機械のような高度装置は、通常これらのプロセスのために使用されます。 これらの機械が精密を保障している間、それらはまた運用コストおよび維持の条件による全体的な費用に加えます。 また、コーティングや表面テクスチャーなどの仕上げ処理により、更に価格を上げます。 たとえば、屋外用途で使用されるカーボンファイバー部品にUV耐性コーティングを適用することでコストを増加させることができます 15%.
加工や仕上げの際に発生する追加費用に対して、性能と美学の向上のメリットを産む必要があります。 これらのプロセスは最終製品が機能的で視覚的な基準を満たしていることを確認します.
大量注文と割引
一括でカーボンファイバーコンポジットを注文すると、カスタマイズコストを大幅に削減できます。 メーカーは、多くの場合、大規模な購入のための割引を提供しています, それは、実質の量を必要とする業界のための費用対効果の高いオプションを作る. たとえば、自動車メーカーは、軽量部品を1台あたりのコストを削減することにより、電気自動車の大量注文から利益を得ることができます.
生産の規模は、これらの割引の程度に影響を及ぼします。 より大きい順序は製造業者が生産ラインを最適化し、無駄を減らし、効率を改善することを可能にします。 コストを削減するだけでなく、すべてのユニット間で一貫した品質を確保するというアプローチです。 例えば、10,000単位の一括注文は、 10-20% より小さい量と比較される割引.
しかし、大量注文は、過剰生産や貯蔵の課題を避けるために慎重な計画が必要です。 業界は、長期的なニーズを評価し、信頼できるサプライヤーと協力してバルク購入の利点を最大限に高める必要があります.
「大量注文は、コストを効果的に管理するために探している産業のための戦略的な利点を提供します」アナリストは提案します。 経験豊富なメーカーと提携し、企業がカスタマイズされたカーボンファイバーコンポジットで手頃な価格と品質の両方を実現できるようにします.
カーボンファイバーコンポジットの費用に関するアプリケーションとその影響
航空宇宙・防衛
航空宇宙および防衛産業は大きく依存しています carbon fiber composite 軽量・高強度の特性により、 航空機メーカーは重量を減らすためにこの材料を使用し、燃料の効率を改善し、ペイロード容量を増加させます。 たとえば、ボーイング787ドリームライナーのような近代的な商用航空機は、自分の胴体と翼に重要な量の炭素繊維複合体を組み込んでいます。 従来のアルミニウム構造と比較して、最大20%までの重量を削減します.
について カーボン繊維の合成の費用 航空宇宙用途では高いままです。 大気および宇宙空間等級のカーボン繊維は厳密な安全および性能の標準を満たすために厳密な質の点検を経ます。 これらの要件は生産コストを増加させ、航空宇宙グレードのコンポジットは、産業グレードのオプションよりも高価です。 また、曲げられた翼パネルや複雑な構造部品などのコンポーネントのカスタマイズも、コストに追加します。 これらのコストにもかかわらず、燃料消費量を削減し、メンテナンスニーズを削減するなど、長期にわたる利点は、航空宇宙企業への投資を正当化します.
防衛アプリケーションは、炭素繊維コンポジットにもメリットがあります。 軍の航空機、無人機および高度の武器システムは極度な条件への耐久性そして抵抗のためにこの材料を使用します。 例えば、無人航空機車(UAV)は、多くの場合、操縦性と耐久性を高めるために、炭素繊維コンポーネントを備えています。 防衛プロジェクトのカーボン繊維の合成の費用は精密工学および専門にされた設計のための必要性を反映します.
自動車産業
自動車産業はますますます車の性能および効率を改善するカーボン繊維の合成を採用します。 軽量材料は、電池範囲を拡張し、エネルギー消費を削減することにより、電気自動車(EV)で重要な役割を果たします。 フェラーリやランボルギーニが制作したスポーツカーは、ボディパネル、シャシ、インテリアパーツのカーボンファイバーコンポジットを使用。 これらのアプリケーションは、速度、処理、および全体的な美学を高めます.
自動車分野における炭素繊維複合材のコストは、車種や部品の種類により異なります。 豪華で高性能な車は、航空宇宙グレードの炭素繊維を使用して、より高価です。 対照的に、大量市場EVは、コストとパフォーマンスのバランスを取るために、工業用グレードのコンポジットを選ぶことができます。 バルク生産は、メーカーがスケールの経済性から利益を得るため、コストを削減するのに役立ちます。 たとえば、同一の炭素繊維コンポーネントの何千もの部品を製造することで、一口の価格が下がり、中距離車両の材料がよりアクセス可能になります.
その利点にもかかわらず、炭素繊維複合材は、アルミニウムや鋼などの伝統的な材料よりも大幅に高価です。 アルミは1キログラムあたり約45倍のコストで、予算を重視するメーカーにとってより経済的に選択できます。 しかし、カーボンファイバーコンポジットの優れた強度から重量比は、性能が高価な考慮事項を上回る用途での継続的な使用を保証します.
スポーツ・レクリエーション
スポーツおよびレクリエーションの企業は性能および耐久性を高める機能のためのカーボン繊維の合成を包囲します。 ハイエンドの自転車、テニス ラケット、ゴルフクラブ、釣り竿は、多くの場合、この材料を備えています。 アスリートや愛好家は、その軽量性のために炭素繊維装置を好む、速度と精度を向上させる。 例えば、プロのサイクリストはカーボンファイバーフレームを使用して、レース中の加速とより良い制御を実現します.
スポーツ機器のカーボンファイバーコンポジットのコストは、カスタマイズと品質のレベルによって異なります。 顧客用自転車やプロ級のテニス ラケットなどのプレミアム製品、高品質の炭素繊維を使用して、価格を増加させます。 メーカーは、高度な加工と仕上げプロセスに投資して、選手の特定のニーズを満たしています。 これらの要因は、ガラス繊維やアルミニウムなどの代替品と比較して、炭素繊維ベースのスポーツギアの高コストに貢献します.
カヤックやパドルボードなどのレクリエーションアプリケーション、カーボンファイバーコンポジットにもメリットがあります。 これらの製品は、パフォーマンスと長寿を改善し、屋外愛好家の間で人気を博しています。 初期費用が高くなりますが、炭素繊維装置の耐久性と軽量性は、ユーザーにとって長期的な価値を提供します.
「カーボンファイバーコンポジットは、耐久性と性能を兼ね備えたスポーツとレクリエーションに革命を起こしています」と業界の専門家が強調しています。 多様な活動を通じた採用は、その汎用性とプレミアムな魅力を強調しています.
カーボン繊維の合成の費用効果が大きい調達のための先端
信頼できるサプライヤーと提携
信頼できる製造者はカーボン繊維の合成物の費用効果が大きい調達を保障する重要な役割を担います。 製造業者は、高品質の材料を提供する実証済みの実績を持つサプライヤーを優先する必要があります。 企業様様 寧波VETエネルギー技術有限公司 信頼できるサービスおよび一貫したプロダクト質を提供し、それらに多くの企業のための好まれる選択をします.
信頼できる製造者は価格表で透明物を提供し、時機を得た配達を保障します。 生産遅延を最小限に抑え、予期しないコストを回避します。 例えば、高度な製造能力を持つサプライヤーからの調達は、欠陥のリスクを減らし、追加の費用につながることができます。 企業はまたカーボン繊維の習慣のサイズか等級のような特定の条件を満たすために製造者の能力を評価するべきです.
「信頼できるサプライヤーとの強いパートナーシップにより、コストを最適化しながら材料の安定した供給を保証します」と業界の専門家は強調しています。 経験豊富なサプライヤーとのコラボレーションにより、メーカーは品質と手頃な価格の両方を実現できます.
バルク購入オプションの探索
バルク購入は、大量の炭素繊維複合材を必要とする産業のための重要なコストメリットを提供します。 メーカーが生産プロセスを最適化し、廃棄物を最小限に抑えることができるため、バルクでの注文は、一口あたりのコストを削減します。 このアプローチは、自動車や航空宇宙などの分野に大きな影響を与えます.
たとえば、軽量車両部品を製造する自動車会社は、大量注文のための割引を交渉することができます。 典型的なバルク購入は、節約につながる可能性があります 10-20% より小さい量と比較される。 これらの節約により、企業は研究開発やマーケティングなどの他の分野にリソースを割り当てることができます.
しかし、大量購入は慎重な計画が必要です。 企業は、過剰な在庫や無駄を避けるために長期的なニーズを評価する必要があります。 柔軟な注文サイズとストレージソリューションを提供するサプライヤーと提携することで、バルク購入のメリットをさらに高めることができます.
代替を検討する
カーボンファイバーコンポジットの代替品を探索することで、性能を損なうことなく、企業がコストを管理するのに役立ちます。 材料 のような ファイバーグラス, アルミニウムそして 天然繊維複合材 特定の適用のための実行可能な選択を提供します。 各代替は、メーカーが要件に基づいて最も適した材料を選択できるように、ユニークな利点を提供します.
- グラスファイバー: : : この材料はカーボン繊維よりかなりよりよりよりよりよりより少し、及ぶから 1から1へ 1ツイートログイン5ポンドあたり. . それは重量がより重要であるが、耐久性が不可欠である適用でよく働きます、ボートの船員か構造のパネルのような.
- アルミニウムおよび鋼鉄: : : これらの金属は、構造用途の費用対効果の高い選択を維持します。 アルミ、価格 0.80and0.80および 0.80and1ポンドあたり1.50、鋼鉄がより低い費用で比類しない強さを提供する間、軽量の特性を提供します.
- 天然繊維コンポジット: ポリマーとフラックスや麻などの天然繊維を組み合わせることで、環境に優しい素材を生み出します。 これらのコンポジットはの間のコスト 2and2と2 2and6ポンドあたり 持続可能性を優先する産業に適して下さい.
「適切な材料の選択は、バランシングコスト、パフォーマンス、およびアプリケーションのニーズによって異なります」専門家は提案します。 代替品を検討することで、材料の選択肢を最適化し、費用を効果的に削減することができます.
炭素繊維コンポジットのコストは、その生産の複雑さと、産業に持ち込む価値を反映しています。 原材料、エネルギー集中製造、地域供給チェーンはすべて、価格変動に貢献します。 特定のアプリケーションのための費用効果が大きい解決を提供するガラス繊維かアルミニウムのような代わりを探検することによって企業は費用を削減できます。 ニンポーVETエネルギー技術Co.のような信頼できる製造者と、一貫した質および競争価格を保障します。 バルク購入戦略はコストをさらに最適化します。 技術革新の進歩とカスタマイズオプションは、炭素繊維コンポジットの未来を形作り続け、多様な分野にますますアクセス可能にします.
よくあるご質問
カーボンファイバーのコンポジットが高価になるのは?
カーボンファイバーコンポジットは、複雑な製造プロセスと高品質の原材料によります。 主の前駆体、ポリアクリルニトリル(PAN)は、炭素繊維に変換する広範な処理が必要です。 コストを増加させる高エネルギー消費量および専門装置を含みます。 また、炭化・製織などの労働集中的なステップは、コスト全体に貢献します。 業界は、厳しい品質基準により、航空宇宙グレードまたは医療グレードのコンポジットのプレミアムを頻繁に支払います.
炭素繊維複合材料のコストに影響する技術は?
炭素繊維複合材のコストを大幅に削減しました。 自動化された繊維の配置および高度の治癒の技術のような革新は合理化された生産を持っています。 これらは、材料廃棄物を最小限にし、労働依存性を減らし、製造コストを削減します。 研究者は、伝統的な素材に持続可能な費用対効果の高い代替手段を提供する、バイオベースの前駆者を探索しています。 技術の進化が進むにつれて、炭素繊維コンポジットの価格はさらに減少すると予想されます.
「製造技術の進歩は、業界全体でよりアクセス可能な炭素繊維複合体を作った」専門家ノート.
工業用グレードと航空宇宙グレードの炭素繊維の違いはなぜですか?
工業用グレードの炭素繊維は、航空宇宙グレードの繊維と比較して品質要件が少ないため、コストを削減します。 航空宇宙用途は、優れた強度、耐久性、および極端な条件に対する耐性を持つ材料を要求します。 これらの繊維は生産費を増加する厳密なテストおよび証明プロセスを、経ます。 対照的に、産業等級繊維は手頃な価格を優先し、自動車部品およびスポーツ用品のような適用で使用されます.
炭素繊維複合材料のコストに地域の違いはありますか?
はい、製造能力とサプライチェーンの違いにより地域の変化が起こります。 北アメリカおよびヨーロッパは安定した価格を保障するローカルで良質の合成物を、作り出します。 コスト効率の高い製造プロセスのアジア・パシフィック・メリット、コンポジットをより手頃な価格に。 しかし、中東やアフリカなどの地域は輸入に依存しており、輸送コストと最終価格が増加しています。 これらの地域における地方生産投資は、そのような分散を削減することを目的としています.
バルク購入は、炭素繊維複合材料のコストを削減できますか?
バルク購入は重要な費用節約を提供します。 メーカーは、多くの場合、大口注文のための割引を提供します, 単元価格を削減. たとえば、軽量車両部品を生産する自動車会社は、スケールの経済性から恩恵を受けています。 大量注文は、生産効率を最適化し、廃棄物と運用コストを最小限に抑えます。 企業は、在庫を回避し、最大の利益のために信頼できるサプライヤーと協業するために慎重に計画する必要があります.
炭素繊維複合材の代替品は何ですか?
いくつかの選択肢は、特定のアプリケーションに費用対効果の高いソリューションを提供します
- グラスファイバー: コスト 1から1へ 1ツイートログイン5ポンドあたりと重量が少ないアプリケーションに適しています.
- アルミ: 軽量・価格 0.80and0.80および 0.80and1ポンドあたり1.50、自動車や航空宇宙用途に最適です.
- 天然繊維コンポジット: 環境に優しい、現実的、費用がかかること 2to2 へ 2ツイートログイン6ポンドあたり、持続可能なプロジェクトに適しています.
各代替品は、業界が性能と予算要件に基づいて選ぶことを可能にするユニークな利点を提供します.
カスタマイズは炭素繊維複合材料のコストにどのように影響しますか?
追加のプロセスとリソースにより、カスタマイズコストが増加します。 ユニークなサイズと形状を作成するには、特殊な金型や工具が必要です。 曲線や多次元構造、要求の高度な技術、調達コストなどの複雑な設計。 切断および磨くことのような機械化し、仕上げプロセスはまた費用に加えます。 業界は、関連する費用と合わせたソリューションの利点のバランスを取る必要があります.
炭素繊維コンポジットから最も有利な業界は?
航空宇宙、自動車、スポーツ製造などの産業は、炭素繊維コンポジットから最も多く得ます。 航空機会社では、航空機重量を削減し、燃費効率を改善するために使用します。 自動車メーカーは、電動車両に蓄電池範囲を増強するために組み込まれています。 自転車やテニスのラケットなどのスポーツ用品、素材の軽量で耐久性のある特性からの利点。 これらの産業は性能を優先し、カーボン繊維の合成物に価値のある投資をします.
炭素繊維コンポジットの費用対効果の高い調達を企業が確保する方法は?
企業は費用効果が大きい調達を達成できます:
- 信頼できるサプライヤーと提携: 信頼できる製造者との共同作業は一貫した質および競争価格を保障します。 企業様様 寧波VETエネルギー技術有限公司 信頼できるサービスを提供します.
- バルク購入オプションの探索: ロット単位での注文は、1単位のコストを削減し、生産効率を最適化します.
- 代替を検討する: : : ガラス繊維やアルミニウムなどの材料の評価は、妥協することなくコストを管理するのに役立ちます.
「戦略的調達の決定は、企業が品質と手頃な価格のバランスをとり、アナリストは提案するのを助けます.
カーボン繊維の合成の価格のための未来の把握は何ですか?
未来は技術の進歩として有望な一見はコストを削減し続けます。 研究者は、バイオベースの前駆者やリサイクル方法などの革新による生産費の50%削減を予測しています。 再生可能エネルギーや電気自動車などの業界から需要を成長させ、市場成長を支えます。 グローバルな生産能力が拡大するにつれて、地域価格の格差は減少し、よりバランスの取れた市場を作ることができます.