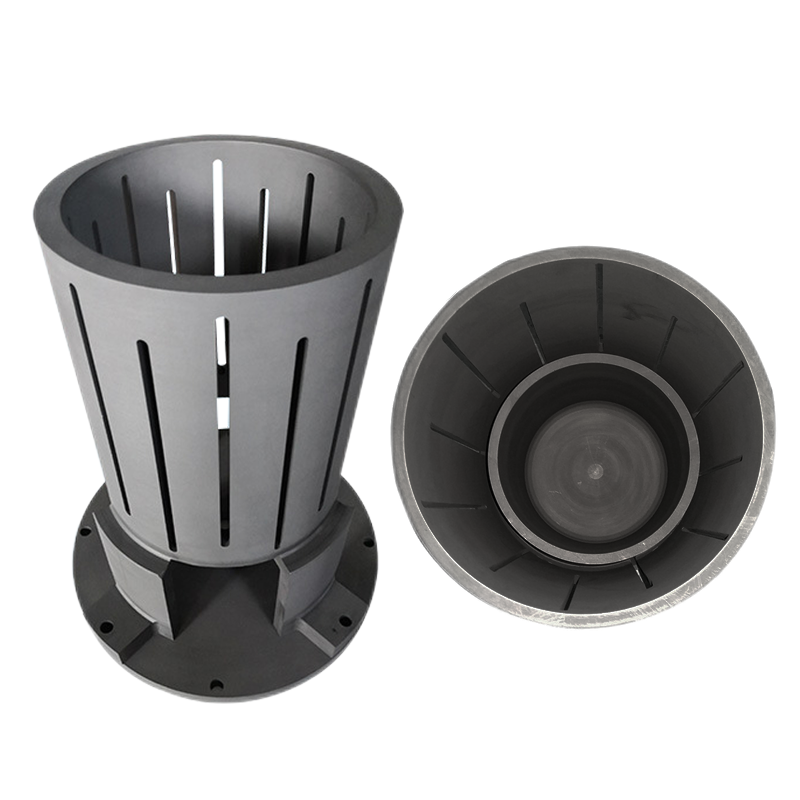
について 加熱要素 serves as the backbone of an electric iron, transforming electrical energy into the heat required to smooth fabrics. This critical component is typically crafted from nichrome, an alloy of 80% nickel and 20% chromium. Nichrome’s high resistance and melting point, reaching up to 1400ºC, make it ideal for enduring intense temperatures without degrading. Its resistance to oxidation ensures durability, even with prolonged use. Beyond electric irons, heating elements like the silicon carbide heating element are also utilized in other appliances, showcasing their versatility and reliability in various heating applications.
要点
- The heating element is crucial for an electric iron’s performance, converting electrical energy into heat to effectively remove wrinkles from fabrics.
- Nichrome, an alloy of 80% nickel and 20% chromium, is the preferred material for heating elements due to its high resistance, durability, and ability to withstand extreme temperatures.
- Regular maintenance, including cleaning the soleplate and inspecting for wear, can significantly extend the lifespan of the heating element and improve ironing efficiency.
- Modern electric irons often feature advanced temperature control mechanisms, such as microchip technology, which enhance safety and ensure precise heat regulation for different fabric types.
- Choosing a reputable brand with certified heating elements ensures reliability and safety, as these products undergo rigorous testing for performance and durability.
- Energy-efficient designs in heating elements not only reduce electricity consumption but also contribute to a more sustainable environment, aligning with consumer demand for eco-friendly appliances.
What Is the Heating Element in an Electric Iron?
Definition and Function
The heating element in an electric iron is a specialized component designed to convert electrical energy into heat. This process occurs through electrical resistance, where the material of the element resists the flow of electricity, generating heat as a result. The heating element is typically embedded within the soleplate of the iron, ensuring even heat distribution across its surface. This uniform heating allows users to effectively remove wrinkles and creases from fabrics.
The choice of material for the heating element plays a critical role in its performance. Nichrome, an alloy of 80% nickel and 20% chromium, is widely used due to its high resistance and durability. Its ability to withstand temperatures up to 1400ºC without melting or degrading ensures consistent performance over time. Additionally, its resistance to oxidation prevents corrosion, further enhancing its longevity.
Jaye Heater Technology, a leader in heating element manufacturing, emphasizes that the design of the heating element must balance efficiency and safety. It requires sufficient resistance to generate heat while maintaining durability under high temperatures. Proper insulation and protection are also essential to prevent electrical hazards.
Importance in Iron Performance
The heating element is the cornerstone of an electric iron’s functionality. Without it, the iron would fail to produce the heat necessary for smoothing fabrics. Its efficiency directly impacts the iron’s ability to deliver consistent results. A well-designed heating element ensures rapid heating, allowing users to begin ironing almost immediately after turning the device on. This feature is particularly valuable for those with busy schedules.
According to Power Pack Electricals, the heating element’s rapid heating capability is a key factor in its effectiveness. Users can rely on it to quickly reach the desired temperature, making the ironing process more efficient and convenient.
The quality of the heating element also influences the iron’s safety and energy consumption. High-quality materials and precise engineering minimize the risk of overheating or uneven heat distribution. These factors not only protect the fabric being ironed but also extend the lifespan of the appliance. A poorly constructed heating element, on the other hand, may lead to inconsistent performance and potential safety hazards.
Materials Used in the Heating Element
Nichrome: The Ideal Alloy
Nichrome stands out as the preferred material for heating elements in electric irons. This alloy, composed of approximately 80% nickel and 20% chromium, offers a unique combination of properties that make it highly effective. Its high resistivity allows it to generate significant heat when electricity flows through it. Additionally, its ability to withstand extreme temperatures, up to 1400ºC, ensures consistent performance without degradation.
Nichrome’s resistance to oxidation further enhances its durability. When exposed to high temperatures, it forms a protective chromium oxide layer on its surface. This layer prevents corrosion, ensuring the longevity of the heating element. Manufacturers also favor nichrome due to its ductility, which allows it to be shaped into wires or coils easily. Its low manufacturing cost makes it an economical choice for mass production.
事実: Nichrome’s versatility extends beyond electric irons. It is also used in other heating devices, such as toasters, hair dryers, and industrial furnaces, due to its exceptional thermal properties.
Properties of Nichrome
Nichrome’s properties make it an indispensable material for heating elements. Its high melting point ensures stability under intense heat, while its resistance to the flow of electrons (high resistivity) enables efficient heat generation. These characteristics allow electric irons to heat up quickly and maintain consistent temperatures during use.
The alloy’s non-magnetic nature ensures that it does not interfere with the iron’s electrical components. Its strength and ductility make it easy to work with during the manufacturing process. Moreover, its resistance to oxidation and corrosion ensures that the heating element remains functional even after prolonged exposure to high temperatures.
主なインサイト: The combination of high resistivity, durability, and thermal stability makes nichrome the ideal choice for heating elements in electric irons.
Alternative Materials and Their Drawbacks
While nichrome dominates the market, other materials have been explored for heating elements. Copper, for instance, offers excellent conductivity but lacks the high resistivity required for efficient heat generation. Its low melting point also makes it unsuitable for prolonged use in high-temperature applications.
Iron-based alloys have been considered due to their affordability. However, they are prone to oxidation and corrosion, which significantly reduces their lifespan. Tungsten, known for its high melting point, is another alternative. Yet, its brittleness and high cost make it impractical for use in consumer appliances like electric irons.
Conclusion: Alternative materials fail to match nichrome’s balance of cost, durability, and performance. This makes nichrome the unrivaled choice for heating elements in electric irons.
How the Heating Element Works
Electrical Resistance and Heat Generation
The heating element in an electric iron operates on the principle of electrical resistance. When electricity flows through the element, the material resists the current, causing energy to convert into heat. This resistance is a deliberate design feature, as materials like nichrome are chosen for their ability to generate significant heat without degrading. The high resistivity of nichrome ensures efficient heat production, making it ideal for consistent performance.
The development of sheathed heating elements in the early 20th century marked a turning point in electrothermics. These elements offered enhanced mechanical strength, resistance to corrosion, and impermeability, which improved the durability and safety of electric irons. Modern manufacturing techniques, introduced in the 1950s, further refined the production process, enabling the creation of more efficient and cost-effective heating elements. These advancements have allowed electric irons to deliver rapid and even heating, ensuring optimal ironing results.
事実: Jaye Heater Technology highlights that high-quality heating elements provide fast heating speeds, even heat distribution, and long lifespans, ensuring reliability and safety during use.
Conversion of Electrical Energy to Thermal Energy
The heating element transforms electrical energy into thermal energy through a process known as Joule heating. As electric current passes through the element, the resistance generates heat, which is then transferred to the soleplate of the iron. This heat spreads evenly across the soleplate, allowing users to press fabrics effectively.
Nichrome’s high melting point, reaching up to 1400ºC, ensures that the heating element remains stable under intense temperatures. Its resistance to oxidation prevents corrosion, maintaining the element’s efficiency over time. This durability is crucial for electric irons, as they require consistent heat output to perform effectively. The introduction of advanced materials and manufacturing techniques has further enhanced the thermal efficiency of heating elements, reducing energy consumption while maintaining performance.
主なインサイト: The conversion of electrical energy to thermal energy is a cornerstone of electric iron functionality, ensuring that fabrics receive the precise amount of heat needed for wrinkle removal.
Role of Temperature Control Mechanisms
Temperature control mechanisms play a vital role in regulating the heat generated by the heating element. These systems prevent overheating, ensuring user safety and protecting fabrics from damage. Traditional electric irons rely on thermostats to monitor and adjust the temperature. When the soleplate reaches the desired heat level, the thermostat interrupts the electrical flow to the heating element, maintaining a consistent temperature.
Modern electric irons incorporate microchip-controlled heating elements for greater precision. These advanced systems allow users to select specific temperature settings based on fabric type. The microchip continuously monitors the heating element’s performance, making real-time adjustments to ensure accuracy. This innovation not only enhances ironing efficiency but also extends the lifespan of the appliance by preventing excessive wear on the heating element.
Historical Note: The introduction of microchip-controlled heating elements represents a significant leap in electric iron technology, offering unparalleled accuracy and energy efficiency.
By combining electrical resistance, efficient energy conversion, and advanced temperature control, the heating element ensures that electric irons deliver reliable and safe performance. These features underscore the importance of high-quality materials and innovative design in modern heating technology.
Design Considerations for Heating Elements
Safety Features
Safety remains a top priority in the design of 加熱要素 for electric irons. Manufacturers incorporate multiple features to ensure user protection and appliance reliability. One critical aspect involves the use of insulation materials that prevent electrical leakage and reduce the risk of short circuits. These materials shield the heating element, ensuring safe operation even under prolonged use.
Temperature control mechanisms, such as thermostats or microchip-controlled systems, play a vital role in maintaining safety. These systems monitor the heating element’s performance and regulate its temperature to prevent overheating. For instance, when the soleplate reaches the desired heat level, the thermostat interrupts the electrical flow, ensuring consistent and safe operation. Advanced microchip-controlled designs offer even greater precision, adjusting the temperature in real time based on fabric requirements.
事実: Jaye Heater Technology emphasizes that high-quality heating elements must include robust safety features, such as thermal cutoffs, to protect both users and the appliance from potential hazards.
Additionally, the choice of sheath material enhances safety. Stainless steel or other corrosion-resistant materials encase the heating element, providing mechanical strength and preventing exposure to external elements. This design minimizes the risk of damage and ensures the iron operates safely over its lifespan.
Efficiency and Energy Optimization
Efficiency and energy optimization are essential considerations in heating element design. A well-engineered heating element ensures rapid heat generation while minimizing energy consumption. Nichrome, the preferred material for heating elements, plays a significant role in achieving this balance. Its high resistivity allows it to generate substantial heat with minimal energy loss, making it an ideal choice for electric irons.
Coil design also influences efficiency. Tightly wound coils increase the surface area of the heating element, promoting faster and more even heat distribution. This design reduces the time required for the iron to reach its operating temperature, enhancing user convenience and energy savings.
主なインサイト: Modern electric irons often feature advanced heating elements with optimized watt density. This specification ensures efficient energy use while maintaining consistent performance.
Temperature control mechanisms further contribute to energy optimization. By regulating the heating element’s output, these systems prevent unnecessary energy consumption. Microchip-controlled designs, in particular, allow for precise adjustments, ensuring the iron uses only the energy required for the selected temperature setting.
耐久性と寿命
Durability and longevity are critical factors in the design of heating elements. The choice of materials significantly impacts the lifespan of the heating element. Nichrome, with its resistance to oxidation and corrosion, ensures the element remains functional even after prolonged exposure to high temperatures. This durability reduces the need for frequent replacements, offering long-term value to users.
Manufacturing standards also play a crucial role in enhancing durability. High-quality heating elements undergo rigorous testing to ensure they meet performance and safety benchmarks. For example, manufacturers test elements for resistance to thermal stress, mechanical wear, and electrical stability. These measures guarantee that the heating element can withstand the demands of daily use.
Historical Note: The introduction of sheathed heating elements in the 20th century marked a significant advancement in durability. These designs provided enhanced mechanical strength and resistance to environmental factors, extending the service life of electric irons.
Proper coil design further contributes to longevity. Uniformly wound coils distribute heat evenly, reducing the risk of hotspots that could damage the element. Additionally, protective coatings or sheaths safeguard the heating element from external damage, ensuring consistent performance over time.
By prioritizing safety, efficiency, and durability, manufacturers create heating elements that deliver reliable and long-lasting performance. These considerations underscore the importance of thoughtful design in modern electric irons.
Factors Influencing the Quality of Heating Elements
Material Composition and Purity
について quality of a heating element heavily depends on the materials used in its construction. Nichrome, an alloy of 80% nickel and 20% chromium, remains the most widely used material due to its high resistance and durability. The purity of these materials plays a critical role in ensuring consistent performance. Impurities in the alloy can lead to uneven resistance, which may cause hotspots or premature failure of the heating element.
Manufacturers prioritize sourcing high-grade raw materials to maintain the integrity of the heating element. For example, the chromium content in nichrome forms a protective oxide layer when exposed to high temperatures. This layer prevents oxidation and corrosion, extending the lifespan of the element. Any deviation in material composition can compromise this protective feature, reducing the element’s efficiency and durability.
主なインサイト: High-purity materials ensure uniform heat generation and enhance the longevity of the heating element, making them essential for reliable performance.
Manufacturing Standards and Certifications
Strict adherence to manufacturing standards ensures the production of high-quality heating elements. Reputable manufacturers follow industry guidelines, such as ISO certifications, to maintain consistency and safety in their products. These standards cover every aspect of production, from material selection to final assembly, ensuring that each heating element meets performance benchmarks.
Certifications also play a vital role in establishing trust and credibility. For instance, UL (Underwriters Laboratories) certification indicates that the heating element has undergone rigorous testing for safety and reliability. Products with such certifications reassure consumers about their quality and compliance with international standards.
事実: Certified heating elements often outperform uncertified ones in terms of durability and efficiency, as they are designed to meet stringent quality requirements.
Testing and Quality Assurance
Comprehensive testing is crucial for evaluating the performance and safety of heating elements. Manufacturers subject their products to various tests, including thermal stress tests, resistance measurements, and durability assessments. These tests identify potential weaknesses and ensure that the heating element can withstand prolonged use under high temperatures.
Quality assurance processes also involve real-world simulations. For example, heating elements designed for appliances like electric irons undergo tests to replicate typical usage scenarios. This approach helps manufacturers identify and address issues such as overheating or uneven heat distribution. By refining their designs based on test results, they create heating elements that deliver consistent and reliable performance.
Anecdote: In the development of modern heating elements, engineers often balance multiple factors, such as airflow and temperature control, to prevent overheating. This meticulous approach ensures that the final product is both effective and durable.
Takeaway: Rigorous testing and quality assurance processes are essential for producing heating elements that meet the demands of modern appliances.
Common Problems with Heating Elements
Overheating and Its Causes
Overheating in a heating element often stems from several underlying issues. Faulty wiring ranks as a primary cause. When the wiring fails to deliver electricity efficiently, the element may draw excessive current, leading to overheating. Regular wear and tear also contribute to this problem. Over time, the material of the heating element degrades, reducing its ability to handle electrical resistance effectively.
Environmental factors, such as dust and debris accumulation, exacerbate overheating. These particles can insulate the heating element, trapping heat and preventing proper dissipation. Thermal stress, caused by frequent temperature fluctuations, weakens the element’s structural integrity. This stress increases the likelihood of overheating during operation.
To mitigate overheating, users should prioritize regular maintenance. Cleaning the iron’s soleplate and ensuring proper ventilation around the heating element can prevent debris buildup. Additionally, inspecting the wiring for damage or corrosion helps maintain optimal performance.
チップ: Avoid using the iron for extended periods without breaks. Allowing the heating element to cool intermittently reduces thermal stress and prolongs its lifespan.
Uneven Heating and How to Address It
Uneven heating presents a common challenge for electric irons. This issue often arises from damage to the heating element or faulty temperature control mechanisms. When sections of the element degrade or break, they fail to generate consistent heat, resulting in uneven temperature distribution across the soleplate.
Improper coil design can also lead to uneven heating. If the coils within the heating element are not uniformly wound, certain areas may heat faster than others. Dust and debris accumulation further aggravate this problem by creating hot spots on the soleplate.
Addressing uneven heating requires a systematic approach. Users should start by cleaning the soleplate to remove any debris that might interfere with heat distribution. If the problem persists, inspecting the heating element for visible damage or wear is essential. Replacing a damaged element restores uniform heating and ensures effective ironing.
事実: Manufacturers design modern heating elements with advanced coil configurations to minimize uneven heating. These designs enhance heat distribution and improve ironing efficiency.
Signs of Element Burnout and Replacement Options
A burned-out heating element renders an electric iron ineffective. Recognizing the signs of burnout helps users address the issue promptly. One common indicator is the inability of the iron to reach its desired temperature. If the soleplate remains cold despite the iron being powered on, the heating element may have failed.
Another sign involves erratic heating behavior. If the iron heats up inconsistently or shuts off unexpectedly, the element might be nearing the end of its lifespan. Visible damage, such as cracks or discoloration on the soleplate, also suggests burnout.
Replacing a burned-out heating element requires professional assistance. Users should consult the manufacturer’s guidelines to ensure compatibility with replacement parts. Opting for high-quality elements with certifications guarantees durability and safety.
主なインサイト: Regular maintenance and proper usage practices significantly reduce the risk of element burnout. Storing the iron in a clean, dry environment further extends its operational life.
Advancements in Heating Element Technology
Smart Heating Systems with Microchip Control
Modern electric irons increasingly incorporate smart heating systems that utilize microchip control. These systems revolutionize the way heating elements function by offering precise temperature regulation and enhanced safety features. Microchips monitor the performance of the heating element in real time, ensuring that the iron maintains consistent heat levels tailored to specific fabric types. This level of precision minimizes the risk of overheating, which can damage delicate materials.
Smart heating systems also enhance diagnostic capabilities. By analyzing performance characteristics, these systems can detect variations in the heating element caused by manufacturing differences or wear over time. This diagnostic ability allows for automatic adjustments, ensuring optimal performance throughout the iron’s lifespan. For example, a patented smart heating system highlights how microchip technology compensates for random variations in heater elements, improving efficiency and reliability.
事実: Microchip-controlled systems not only improve user experience but also extend the life of the heating element by preventing unnecessary thermal stress.
Eco-Friendly and Energy-Efficient Designs
Advancements in heating element technology prioritize エネルギー効率 and environmental sustainability. Manufacturers now design heating elements to consume less electricity while maintaining high performance. Innovations such as optimized coil configurations and advanced materials reduce energy loss during heat generation. These improvements allow electric irons to heat up faster and operate more efficiently, lowering overall energy consumption.
Eco-friendly designs also focus on reducing the carbon footprint of electric irons. Some manufacturers use recyclable materials in the construction of heating elements, aligning with global efforts to promote sustainability. Additionally, energy-efficient heating elements contribute to lower electricity bills for consumers, making them both environmentally and economically beneficial.
主なインサイト: Energy-efficient heating elements not only conserve resources but also align with consumer demand for greener appliances.
Use of Sustainable Materials
The shift toward sustainable materials in heating element production reflects a growing commitment to environmental responsibility. Nichrome remains the primary material due to its durability and efficiency, but manufacturers are exploring alternatives that reduce environmental impact. For instance, some companies experiment with alloys that incorporate recycled metals without compromising performance.
Sustainable materials also include protective coatings that enhance the longevity of the heating element. These coatings reduce the need for frequent replacements, minimizing waste. By adopting sustainable practices, manufacturers ensure that heating elements meet modern standards for both performance and environmental stewardship.
Takeaway: The integration of sustainable materials in heating elements supports a circular economy, where resources are reused and waste is minimized.
Choosing the Right Electric Iron Based on the Heating Element
Selecting the right electric iron requires careful evaluation of its heating element. This component directly impacts the iron’s performance, durability, and safety. Understanding key factors such as material quality, brand reputation, and modern features ensures an informed decision.
Evaluating Material Quality and Design
The material and design of the heating element determine the efficiency and longevity of an electric iron. High-quality materials like nichrome, known for its durability and resistance to high temperatures, are essential. Nichrome’s ability to withstand temperatures up to 1400ºC ensures consistent heat generation without degradation. Its resistance to oxidation further enhances its lifespan, making it a preferred choice for manufacturers.
Design also plays a critical role. A well-designed heating element ensures even heat distribution across the soleplate, preventing hot spots that could damage fabrics. For instance, tightly wound coils increase the surface area, promoting faster and more uniform heating. Products like the Electric Iron Heating Element によって Jaye Heater Technology exemplify this balance of quality and design. These elements heat up rapidly, ensuring users can begin ironing almost immediately after turning the device on.
チップ: Always check the specifications of the heating element when purchasing an iron. Look for materials with high resistance and durability to ensure long-term performance.
Importance of Brand Reputation and Certifications
The reputation of the brand manufacturing the electric iron speaks volumes about the product’s reliability. Established brands often adhere to strict quality standards, ensuring their heating elements meet performance and safety benchmarks. Certifications such as UL (Underwriters Laboratories) or ISO indicate that the product has undergone rigorous testing for safety and efficiency.
For example, brands like Jaye Heater Technology emphasize safety and reliability in their heating elements. Their products include features like thermal cutoffs and protective sheaths to prevent overheating and electrical hazards. Choosing a certified product not only guarantees quality but also provides peace of mind to users.
事実: Certified heating elements often outperform uncertified ones in terms of durability and efficiency, making them a safer and more reliable choice.
Features to Look for in Modern Irons
Modern electric irons incorporate advanced features that enhance user experience and safety. Microchip-controlled heating elements, for instance, allow precise temperature regulation based on fabric type. This innovation prevents overheating, protecting delicate fabrics from damage. Additionally, these systems ensure consistent heat levels, improving ironing efficiency.
Energy efficiency is another critical feature. Heating elements designed for optimized energy consumption reduce electricity usage without compromising performance. Products with eco-friendly designs, such as those using recyclable materials, align with the growing demand for sustainable appliances.
主なインサイト: Features like rapid heating, even heat distribution, and advanced temperature control mechanisms make modern irons more efficient and user-friendly.
When choosing an electric iron, prioritize models with high-quality heating elements, reputable certifications, and innovative features. These factors ensure a reliable, efficient, and safe ironing experience.
Maintenance Tips for Prolonging the Life of the Heating Element
Proper maintenance ensures the heating element in an electric iron remains efficient and durable. By following a few essential practices, users can extend the lifespan of this critical component and maintain optimal performance.
Regular Cleaning and Care
Regular cleaning prevents debris and residue from accumulating on the soleplate and around the heating element. Dust and fabric particles can insulate the heating element, causing it to overheat or function inefficiently. Users should clean the soleplate with a damp cloth after each use to remove any buildup. For stubborn stains, a mixture of water and mild detergent works effectively.
チップ: Avoid using abrasive materials or harsh chemicals during cleaning. These can damage the soleplate and compromise the heating element’s performance.
Periodic inspections also play a vital role in maintenance. Users should check for visible signs of wear, such as discoloration or cracks on the soleplate. Identifying these issues early helps prevent further damage to the heating element. According to a Precision Repair Specialist at Kunkune, meticulous care ensures the heating element operates efficiently and reduces the need for frequent replacements.
Proper Usage Practices
Using the electric iron correctly minimizes stress on the heating element. Users should always set the temperature according to the fabric type. Overheating delicate fabrics can strain the heating element, reducing its efficiency over time. Modern irons with microchip-controlled systems simplify this process by offering precise temperature settings.
Avoiding prolonged use without breaks is another crucial practice. Continuous operation generates excessive heat, which can weaken the heating element. Allowing the iron to cool intermittently prevents thermal stress and extends its lifespan. A Heating Element Design Expert emphasizes that proper usage practices are essential for maintaining the longevity of heating elements in all appliances.
主なインサイト: Always unplug the iron when not in use. This not only conserves energy but also protects the heating element from unnecessary wear.
Storing the Iron Safely
Safe storage protects the heating element from environmental damage. Users should store the iron in a clean, dry location to prevent dust and moisture from affecting its components. Moisture can lead to corrosion, which compromises the heating element’s durability.
When storing the iron, ensure the cord is wrapped loosely to avoid putting pressure on the internal wiring. Faulty wiring can disrupt the flow of electricity to the heating element, leading to overheating or uneven heating. Using a protective cover for the soleplate adds an extra layer of protection against scratches and debris.
事実: : : に従って HVAC experts at Watson Heating & Air, regular maintenance and proper storage significantly enhance the performance and lifespan of heating elements in various devices.
By incorporating these maintenance tips into daily routines, users can ensure their electric irons remain reliable and efficient. Regular cleaning, mindful usage, and safe storage collectively contribute to the longevity of the heating element.
The heating element serves as the foundation of an electric iron, ensuring its functionality and safety. Nichrome, with its exceptional resistance and durability, remains the material of choice for this critical component. Its ability to withstand high temperatures while maintaining efficiency highlights its importance in modern appliances. Understanding the heating element empowers users to select irons that deliver consistent performance and reliability. Proper maintenance, such as regular cleaning and safe storage, further extends the lifespan of the heating element, ensuring long-term value and optimal results.
よくあるご質問
What is an iron heating element and why is it important in an electric iron?
An iron heating element is the core component of an electric iron. It generates the heat required to remove wrinkles and creases from fabrics. Typically made from durable, high-resistance materials like nichrome, it ensures rapid heating and consistent performance. Without this element, the iron would fail to produce the necessary heat for effective ironing.
What materials are commonly used in heating elements for electric irons?
Nichrome, an alloy of 80% nickel and 20% chromium, is the most common material used in heating elements. Its high resistance and melting point of up to 1400ºC make it ideal for generating heat efficiently. Additionally, its resistance to oxidation and corrosion ensures durability. Other materials, such as copper or tungsten, are less suitable due to their lower resistance or higher cost.
How does the heating element in an electric iron work?
The heating element operates on the principle of electrical resistance. When electricity flows through the element, its material resists the current, converting electrical energy into heat. This heat is then transferred to the soleplate of the iron, ensuring even heat distribution for effective ironing. Advanced designs incorporate temperature control mechanisms to maintain consistent heat levels.
What are the advantages of the electric iron heating element made by Jaye Heater Technology?
The heating elements produced by Jaye Heater Technology offer several advantages. These include rapid heating, high efficiency, even heat distribution, and exceptional durability. Their products are designed with safety and reliability in mind, ensuring a long lifespan and consistent performance. These features make them a trusted choice for modern electric irons.
What are the signs of a failing heating element in an electric iron?
A failing heating element often exhibits several signs. The iron may take longer to heat up or fail to reach the desired temperature. Uneven heating across the soleplate or erratic temperature fluctuations can also indicate a problem. Visible damage, such as discoloration or cracks, suggests that the element may need replacement.
How can users prolong the life of a heating element in an electric iron?
Proper maintenance is key to extending the lifespan of a heating element. Regular cleaning of the soleplate prevents debris buildup, which can insulate the element and cause overheating. Using the iron at appropriate temperature settings for different fabrics reduces thermal stress. Storing the iron in a clean, dry environment protects it from moisture and dust, which can lead to corrosion.
Are there different types of heating elements for soldering irons?
Yes, soldering irons feature various types of heating elements to meet different temperature requirements. Some designs integrate the heating element within the tip as a cartridge, while others use separate elements. These components must heat quickly and maintain stable temperatures to ensure smooth soldering processes.
Why is nichrome preferred over other materials for heating elements?
Nichrome is preferred due to its unique combination of properties. Its high resistivity allows efficient heat generation, while its melting point of 1400ºC ensures stability under intense heat. Additionally, its resistance to oxidation and corrosion enhances durability. These qualities make nichrome the most reliable and cost-effective choice for heating elements in electric irons.
What role do temperature control mechanisms play in electric irons?
Temperature control mechanisms regulate the heat generated by the heating element. Traditional irons use thermostats to maintain consistent temperatures by interrupting the electrical flow when the desired heat level is reached. Modern irons incorporate microchip-controlled systems for greater precision, allowing users to select specific settings based on fabric type. These mechanisms enhance safety and improve ironing efficiency.
How do advancements in heating element technology benefit users?
Advancements in heating element technology, such as microchip-controlled systems and eco-friendly designs, offer significant benefits. These innovations ensure precise temperature regulation, faster heating, and reduced energy consumption. Additionally, the use of sustainable materials aligns with environmental goals, making modern electric irons more efficient and environmentally responsible.