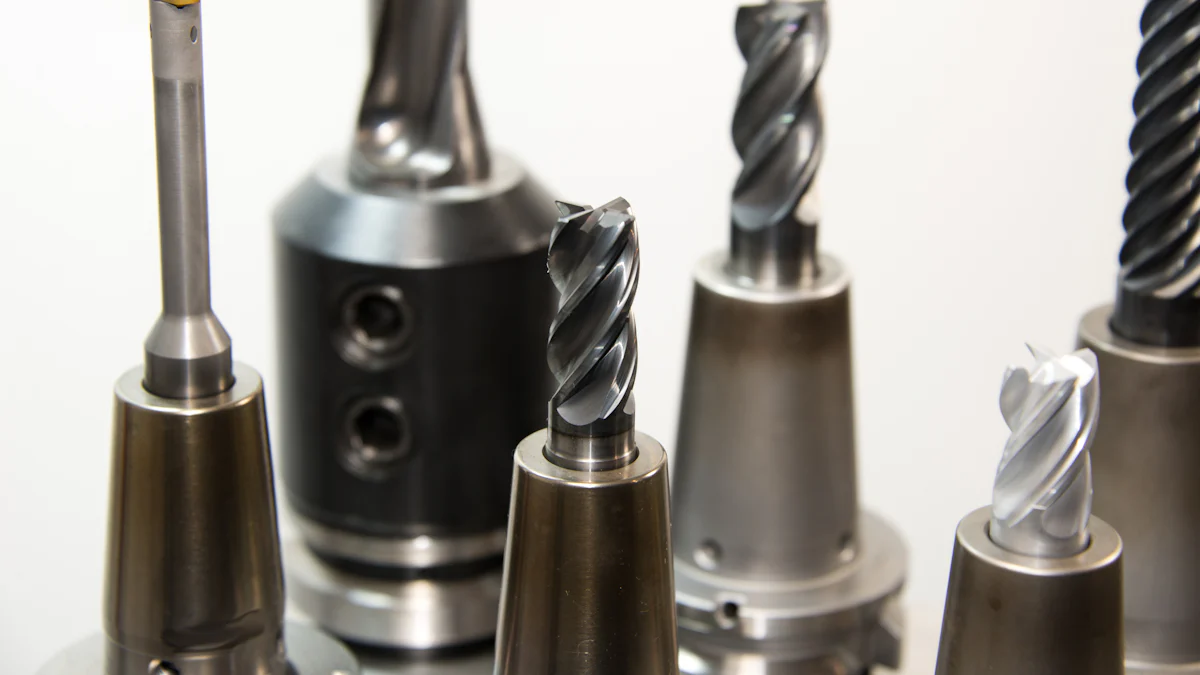
半導体製造、精密、安定性は、非交渉可能です。 ウェーハチャックは、リソグラフィやエッチングなどの重要なプロセス中にウェーハを安全に保持することにより、これらの基準を達成する際の重要な役割を果たしています。 ウェーハは、半導体デバイスの品質に直接影響を及ぼす、安定的かつ正確に位置付けられていることを保証します。 技術の進歩によって、ウェーハのチャックは高められた精密、よりよい熱管理を提供し、耐久性を改善しました。 これらのイノベーションは、製造業の効率性を高めるだけでなく、欠陥を削減し、電子機器、自動車、通信などの業界を横断する高性能半導体ソリューションの需要を増加させます.
要点
- ウェーハチャックは、半導体製造における精度と安定性を維持し、デバイスの品質に直接影響を及ぼすために不可欠です.
- 真空のウエファーのチャックは均一接触および安定性を提供し、それらをphotolithographyおよびエッチングのような複雑なプロセスにとって理想的にします.
- 静電ウエハチャックは、非接触保持を実現し、デリケートウエハへのダメージのリスクを軽減し、高温用途での剥離を実現します.
- メカニカルウエハチャックは、重量や不規則な形状のウエハに対して費用対効果が高く信頼性がありますが、極めて薄い素材には適していません.
- タンデムシリーズや高度なコーティングのようなイノベーションにより、ウェーハチャック性能を高め、効率性を高め、汚染リスクを削減します.
- 真空チャックの定期的なメンテナンスは、一貫した性能を確保し、真空の完全性に関する問題を防ぐため、非常に重要です.
- 適切なウェーハチャックタイプを選択すると、特定の製造ニーズ、ウェーハサイズ、および材料の互換性によって異なります.
真空ウェーハチャック
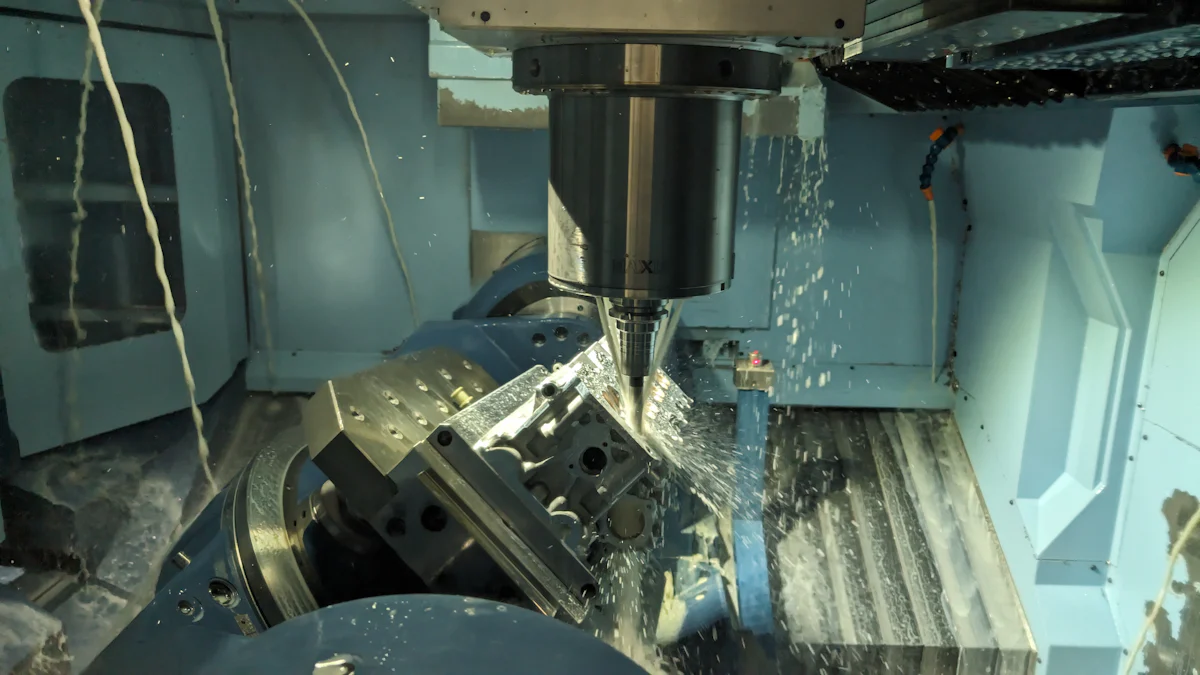
真空ウェーハチャックは、重要なプロセス中にウェーハを安全に保持することにより、半導体製造において重要な役割を果たしています。 これらのチャックは、真空圧力を使用して精密なアライメントと安定性を確保し、高度な加工技術で高品質の結果を達成するのに不可欠です.
真空ウェーハチャックの主な特長
真空ベースのウエファー保持機構
真空のウエファーのチャックは簡単でけれども有効なメカニズムに頼ります。 真空ポンプは、チャックの表面に対してウェーハをしっかりと保持する負圧を作成します。 ウェーハ全体に均一な接触を保ち、加工時の誤差や動きのリスクを最小限に抑えます。 ザ・オブ・ザ・ マイクロパックチャック技術 ウェーハ表面に均一な真空分布を提供することで、この機構を強化します。 超薄型ウェーハでも漏れを減らし、一貫した性能を発揮します.
セラミック真空チャックとその高精度表面プロファイル
セラミック真空チャックは、高精度な表面プロファイルに際立っています。 これらのチャックは多孔質セラミック材料から作られています。これにより、真空の均一な分布を可能にし、平坦で安定した表面を維持できます。 この設計は、精度がパラマウントされるリソグラフィやエッチングなどの繊細なプロセスに特に有益です。 多孔質セラミック構造は、汚染リスクを最小限に抑え、清潔で信頼性の高いウェーハ処理を保証します.
真空ウェーハチャックの利点
加工時の高精度・安定性
真空のウエファーのチャックは精密および安定性を渡します。 ウェハを所定の位置に固定することで、複雑なパターンや構造の精度を妥協できる不要な動きを防ぐことができます。 この安定性は、フォトリソグラフィなどのプロセスにとって重要であり、マイナーな誤差でも半導体デバイスに欠陥をもたらす可能性がある.
各種ウェーハサイズ・材料との互換性
真空ウェーハチャックの最も重要な利点の1つは、その汎用性です。 さまざまなサイズと厚さのウエハに対応し、幅広い用途に適したウェハに対応できます。 標準的なシリコンウェーハやより繊細な素材を扱う場合でも、真空チャックはダメージを起こさない信頼性の高いサポートを提供します.
真空のウエファーのチャックのための箱を使用して下さい
Photolithographyおよびエッチングの適用
真空ウェーハチャックは、フォトリソグラフィやエッチングプロセスに不可欠です。 フォトリソグラフィでは、ウェーハが完全に整列され、回路パターンの正確な転送を可能にします。 エッチングでは、真空チャックによる安定性は、正確な材料除去を可能にします。これは、複雑な半導体構造を作成するために不可欠です.
複雑なウエファーの処理を必要とする企業の使用
電子機器、自動車、通信などの産業は、真空ウェーハチャックから大幅に利益をもたらします。 これらのチャックは、繊細なウェーハをケアで処理し、汚染や損傷の危険性を減らします。 それらの信頼性と精度は、現代の半導体製造の高い基準を満たすことを目指し、メーカーにとって好ましい選択肢になります.
真空ウェーハチャックの制限
真空の整合性を維持するチャレンジ
真空のウエファーのチャックは一貫した真空圧力にウエハを安全に握るために頼ります。 しかし、この真空整合性を維持することは重要な課題です。 システム内のマイナーな漏れでも、均一な圧力分布を混乱させ、処理中に誤差や不安定性を引き起こします。 シールやポンプなどのコンポーネントの摩耗や破損は、この問題を悪化させることができます。 たとえば、技術のような マイクロパックチャック技術 漏出を最小にし、真空の一貫性を高めて下さい、規則的な維持は最適性能を保障するために必要です残ります。 適切なアップキープがなければ、特に超薄型または繊細なウェーハで作業するとき、矛盾する結果に遭遇する可能性があります.
特定環境条件の適合性
真空ウェーハチャックの性能も環境条件に影響します。 ウェーハのしっかりしたグリップを維持する真空の能力を、例えば高い湿気レベルは、干渉できます。 同様に、極端な温度は、チャックで使用される材料に影響を及ぼす可能性があります。 高度なリソグラフィやエッチングなどの高温プロセスを必要とするアプリケーションでは、真空チャックは、常に必要な信頼性を提供することはできません。 代替品のような Pyrolytic Boronの窒化物の静電気のチャック(pBN ESCs)高温環境のために設計されている、そのようなシナリオでより適しているかもしれません。 これらの制限を理解することは、特定の製造ニーズに適したチャックを選択するための重要なことです.
静電ウエファーチャック
静電ウエハチャックは、ウェーハを保護する機械式以外の方法を提供することで、半導体製造に革命を起こしています。 これらのチャックは、静電力を使用してウェーハを所定の位置に保持し、ハイテクプロセスの安定性と精度を保証します。 高度な設計により、デリケートな取扱いや高温レジリエンスが必要な用途に欠かせない設計になっています.
静電ウエファーチャックの主な特長
静電力がウェーハを保護する方法
静電ウエハチャックは電動フィールドを利用し、チャックとウエハ間の魅力的な力を生み出します。 物理的なクランプや真空圧の必要性を排除し、脆弱なウェーハへの損傷の危険性を減らします。 チャック内で埋め込まれた電極に電圧を加えることで、電場が生成されます。 ウェーハの表面を覆い、平坦度とアライメントを保ちながら均一に保持します。 超薄型または脆弱なウエハを扱う場合でも、一貫した結果を得るために、この機能を利用することができます.
高い温度の適用のためのPyrolytic Boron Nitrideの静的なチャック(pBN ESCs)
Pyrolytic Boronの窒化物の静電気のチャック(pBN ESCs)は1000°を超過する極端な温度に耐える能力のために際立っています ツイート これらのチャックは優秀な熱安定性および電気絶縁材を提供する材料と設計されています。 設計は高度エッチングまたは沈殿プロセスのために要求されるそれらのような高温環境の信頼できる性能を保障します。 製造が要求する熱条件を伴う場合、pBN ESCは、ウェーハの完全性を維持するための信頼できるソリューションを提供します.
静電ウエファーチャックの利点
デリケートウエファーのための非接触保持
物理的な接触なしで敏感なウエファーを処理する静電気チャック。 メカニカルクランプや真空圧力の欠如は、傷、亀裂、または汚染の危険性を最小限に抑えます。 この機能は、化合物半導体や超薄型ウェーハなどの壊れやすい材料を関与するプロセスに特に有益です。 静電チャックを使用することで、製造工程を通して、ウェーハの安全・品質を保証できます.
高められた熱管理および均一熱放散
半導体製造において熱管理が重要であり、静電チャックはこの課題を効果的に解決します。 ウエハ全体で均一な熱放散を促進し、ホットスポットを防ぎ、一貫した処理温度を保証します。 この機能は、化学蒸気蒸着(CVD)やプラズマエッチングなどのプロセスにおいて、高品質の結果を得るために不可欠です。 静電気チャックで熱条件をコントロールし、製造歩留まりを改善します.
静電ウエファーチャック用ユースケース
高温度および高度の半導体プロセスの適用
静電ウエハチャックは、高温用途(エピタキシャル成長やイオン注入など)に最適です。 極端な条件下で安定性を維持する能力は、それらが高度な半導体プロセスの優先的な選択をします。 最先端のテクノロジーを伴った場合、これらのチャックは厳格な業界標準を満たすために必要な信頼性と精度を提供します.
精密用フラットウェーハ表面が必要な工程での使用
フラットネスは、フォトリソグラフィやメトロロジーを含む多くの半導体プロセスに不可欠です。 静電気チャックは、加工中にウェーハが完全に平らに残るようにし、正確なパターニングと測定を可能にします。 現代の半導体デバイスで求められる精度を実現できる機能です。 静電チャックをワークフローに組み込むことで、製造業務の精度と効率性を高めることができます.
静電ウエファーチャックの制限
電力供給の運用状況
静電ウエハチャックは、ウェーハを所定の位置に保持する電場を生成するために、連続電源に完全に依存します。 力がなければ、チャックはグリップを維持できません。これにより、製造工程を破壊できます。 停電時や変動時における潜在的なリスクについてご紹介します。 ウェーハの不整合や損傷、特に高精度な用途でも、軽微な割込みが可能です。 これを軽減するには、安定した信頼性の高い電源を確保する必要があります。 無停電電源装置(UPS)などのバックアップシステムは、予期しない混乱に対して効果的な保護を提供できます.
特定のウェーハ材料との潜在的な課題
すべてのウェーハ材料が静電力に等しく反応するわけではありません。 たとえば、低誘電率または非導電性表面を有するウェーハは、静電チャックにしっかりと付着しない場合があります。 この制限は、化合物半導体や特定の高度な基質などの専門材料を扱うときに課題をポーズすることができます。 また、ウェーハの表面の不規則性やコーティングは、チャックの均一なホールドを作成する能力に干渉することができます。 これらの問題に対処するためには、それらをあなたのプロセスに統合する前に、静電気チャックでウェーハ材料の互換性を評価する必要があります。 互換性が懸念である場合, 代替チャックタイプ, 真空や機械式チャックなど, より信頼性の高いソリューションを提供することができます。.
メカニカルウエファーチャック
メカニカルウエハチャックは、半導体製造時にウェーハを安全に保持するための堅牢で信頼性の高いソリューションを提供します。 物理的な締め金で止める機構を組み入れ、重いか不規則に形づけられたウエファーを扱うためにそれら理想をさせます。 これらのチャックは、電力の可用性が制限されるか、費用効果が優先されるプロセスにおいて特に価値があります.
機械式ウェーハチャックの主な特長
メカニズムと変種のクランプ
メカニカルウエハチャックは、ウェーハをしっかりと保持するためのクランプ機構を使用します。 これらの機構は、スプリング式クランプからネジ式システムまで様々です。 各バリエーションは、アプリケーションに応じてユニークな利点を提供します。 ばねによって荷を積まれるクランプはねじベースのシステムが別の厚さの調節可能な圧力、調節のウエファーを可能にする間、速く、一貫した保持を提供します。 この汎用性は、特定の製造要件を満たすために機械的なチャックを適応させることができることを保証します.
耐久性と材料の考慮事項
メカニカルウエハチャックを最後まで製作。 製造業者は頻繁に摩耗への長寿および抵抗を保障するためにステンレス鋼か高力合金のような耐久材料を使用します。 これらの材料は繰り返された使用の厳しさに耐えます、機械式は大量生産のための費用効果が大きい選択をチャックさせます。 また、重質または不規則な形状のウェーハを扱う場合でも、堅牢な構造により、チャック自体への損傷のリスクを最小限に抑えます.
機械式ウェーハチャックの利点
重いか不規則に形づけられたウエファーのための信頼できる把握
機械式ウェーハチャックは、重いまたはユニークな形状のウェーハの安全な保持を必要とするアプリケーションで優れています。 物理的な締め金で止めるメカニズムは処理の間に安定性を保障するしっかりしたグリップを提供します。 この信頼性は、ウェーハのダイシングなどのバックエンドプロセスにおいて非常に重要であり、精密なアライメントと安定性は最終製品の品質に直接影響を与えます。 通常のウエハサイズや形状がない場合、機械式チャックは対応可能なソリューションを提供します.
コスト効果 他のタイプと比較される
機械ウエファーのチャックは真空か静電気のチャックより頻繁により現実的です。 シンプルな設計により、製造コストを削減し、さまざまな用途に経済的に選択できます。 また、耐久性とメンテナンス性が向上し、コスト効率性を高めます。 メカニカルチャックを選ぶことで、高い上面や継続的な経費を調達することなく、信頼性の高い性能を実現できます.
メカニカルウエハチャック用ケース
ウェーハダイシングとバックエンドプロセスのアプリケーション
ウエハダイシングやバックエンド処理に機械式ウエハチャックが不可欠です。 ダイシング中、チャックはウェーハを安全に保持し、誤ったカットや破損したウェーハにつながる動きを防ぐことができます。 高精度でクリーンなカットを実現し、高品質な半導体部品の製造に不可欠です。 あなたの製造業がバックエンドタスクを伴う場合、機械式チャックは、効率と精度を維持するために必要な信頼性を提供します.
限られた電力可用性で環境で使用する
メカニカルウエハチャックは、外部電源に依存せず、電力の可用性が制限されている環境や矛盾する環境に最適です。 停電や変動による混乱のリスクを電気から排除します。 操作が電力に制限されたアクセスと設定で行われる場合、機械式チャックは、真空または静電オプションの実用的で信頼性の高い代替手段を提供します.
機械式ウェーハチャックの制限
ウェーハへの物理的な損傷の危険性
メカニカルウエハチャックは、ウェーハを固定する機構をクランプすることで、不均等な圧力を発生させる場合があります。 この物理的な接触は敏感なウエファーを扱うとき傷、ひびおよび他の形態の損傷の危険を、特に高めます。 高値か壊れやすいウエファーと働けば、この限界は高価な欠陥か生産の遅れをもたらすことができます。 クランプ力は、ある設計で調節可能である間、敏感な材料のために要求される穏やかな処理を提供しないかもしれません。 このリスクを軽減するには、クランプ機構を慎重に評価し、クランプのソフトパディングやコーティングなどの追加の保護対策を検討する必要があります.
Ultra-ThinまたはFragileウエファーのための限られた可塑性
超薄型または脆弱ウェーハは、メカニカルウエハチャックのユニークな課題を提示します。 物理的な締め金で止めるメカニズムは変形か破損に導くウエファーの表面を渡る圧力を均等に分配しないかもしれません。 これらのウエハは、提供されたものなどの非接触保持方法を必要とすることが多いです 静電気チャック静電力を使用して、物理的な圧力なしでウェーハを保護します。 製造プロセスが高度な半導体技術や超薄型ウェーハを伴う場合、機械式チャックはお客様の精度と安全要件を満たしていない場合があります。 このような場合, などの代替品を探索 静電気チャック ダメージのリスクを最小限に抑えながら、より良い結果を達成することができます.
ウェーハチャック技術におけるイノベーション
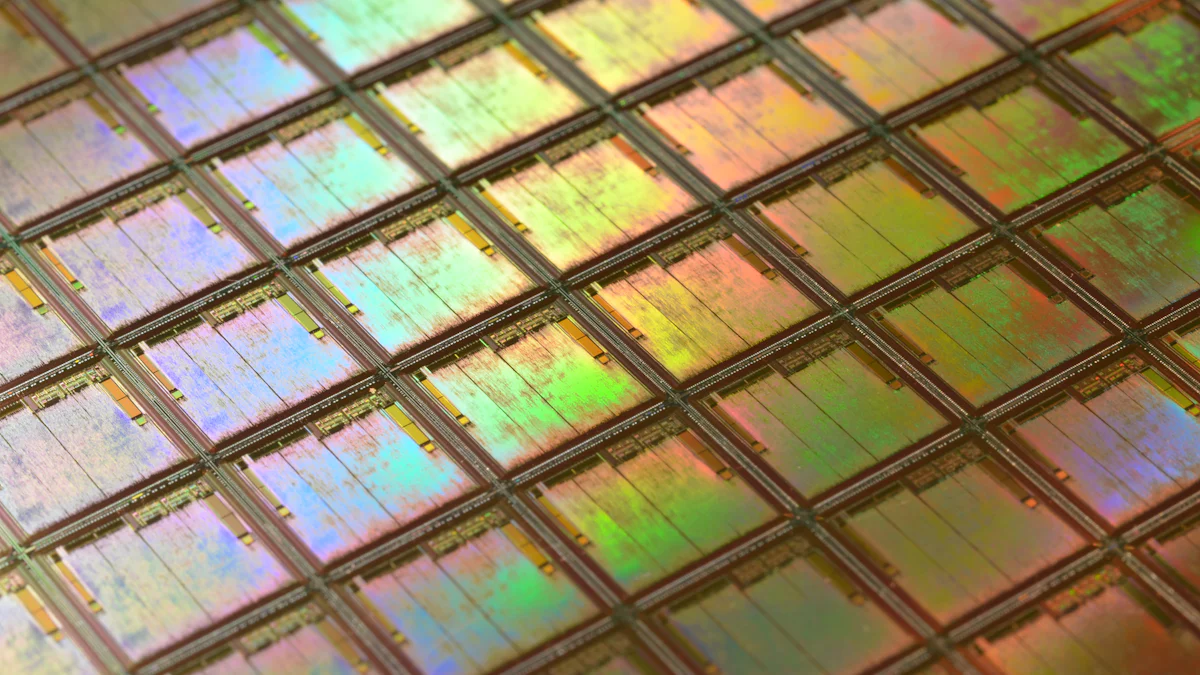
ウェーハチャック技術の進化により、半導体製造における効率・精度・耐久性を高める画期的なイノベーションを導入しました。 これらの進歩は、近代的な業界の成長する要求に対応し、より高い収量を達成し、運用コストを削減することができます.
タンデムシリーズウエファーチャック
二重ウエファーの土台のためのSymmetricの設計
タンデムシリーズのウエハチャックは、同時に2枚のウエハをマウントできる対称設計です。 このデュアルマウント機能は、機器の使用を最適化し、より多くのウェーハをより少ない時間で処理することができます。 2つのウェーハを1つの操作で安全に保持することにより、これらのチャックはワークフローを合理化し、全体的な生産性を向上させます。 対称設計は、両方のウェーハ間で均一な圧力分布を確保し、重要なプロセスの安定性とアライメントを維持します.
設備コストの削減と効率の向上
タンデムシリーズでは、設備コストを大幅に削減できます。 2つのウェーハを一度に処理する能力は、追加の機械の必要性を最小限に抑え、スペースと投資の両方を節約できます。 また、加工時間を削減し、作業効率を高めます。 大量生産環境では、タンデムシリーズは品質を損なうことなく生産目標を達成するための実用的なソリューションを提供しています.
高度なコーティング技術
金属の汚染の最小化
高度なコーティング技術は、金属汚染を最小限に抑えることで、ウェーハチャック表面に革命をもたらしました。 これらのコーティングは、超フラットで非反応的な表面を作成し、粒子の危険性やウエハへの転写残渣を減らす。 この機能は、フォトリソグラフィや化学蒸気蒸着などの高純度を必要とするプロセスに特に有益です。 コーティングされたウェーハチャックを使用することで、クリーンな製造環境を維持し、欠陥のない半導体デバイスを生成できます.
粒子発生の低減と耐久性の向上
革新的なコーティングは、ウェーハ処理中に粒子の発生を削減します。 この改善により、ウェーハがデブリから解放され、それ以外の場合、その完全性を損なう可能性があることを保証します。 また、これらのコーティングは、ウェーハチャックの耐久性を高め、寿命を延ばし、メンテナンス要件を削減します。 製造業者にとって、これはより少ない割込みと長期的なコストを下げることを意味し、一貫した結果を達成することに集中することができます.
熱ウエファーのチャック
電気プロービングおよびテストのための円形の熱チャック
熱ウェーハチャックは、電気のプロービングとテストを含むプロセスにおいて重要な役割を果たしています。 円形の熱チャックはウエファーの表面を渡る均一温度制御を提供するようにとりわけ設計されています。 この均等性は精密で欠陥か不整合性を識別することを可能にする正確なテスト条件を保障します。 丸型設計はさまざまなウエハサイズに対応し、これらのチャックはさまざまな用途に多彩です.
異なるウェーハサイズに対応する複数の真空ゾーン
現代の熱ウェーハチャックは複数の真空ゾーンを組み込んでおり、さまざまな寸法のウェーハを処理することができます。 これらのゾーンは、各ウェーハがサイズに関係なく確実に保持されることを保証します。 多様なウェーハ仕様に対応したメーカーにとって、この柔軟性は不可欠です。 高度な真空ゾーニングで熱チャックを使用することで、フロントエンドの加工からバックエンドテストまで、幅広いプロセスで最適な性能を実現できます.
ウェーハチャックの種類を比較する
パフォーマンスの比較
異なるチャックタイプを渡る精度と安定性
各ウェーハチャックタイプは、精度と安定性のユニークな利点を提供します. 真空チャック フォトリソグラフィのような複雑なプロセス中にウェーハアライメントを維持します。 真空圧力は均一な接触を保障し、不整列の危険を減らします. 静電気チャック一方、デリケートなウエファーにとって理想的な非接触保持を提供します。 高温下でも平坦性と安定性を維持し、先進的な半導体プロセスに適しています. 機械チャック 重いか不規則に形づけられたウエファーのための強い性能を提供します。 クランプ機構はしっかりしたグリップを確保しますが、真空や静電オプションの精度と極めて薄いウェーハを合わせることはできません.
各種ウェーハサイズ・材料の適性
ウェーハチャックは、多様なウエハサイズや素材に対応しなければなりません. 真空チャック さまざまな厚さおよび直径のウエファーを容易に扱う高度に多目的です。 この適応性は、複数のアプリケーション間で人気のある選択肢になります. 静電気チャック 非接触機構が損傷の危険を最小限にするように壊れやすいか、または極めて薄いウエファーと働いたら輝きます。 しかし、特定の非導電性材料で課題に直面することもあります. 機械チャック 標準的なか重いウエファーのために最も適しています、信頼できるサポートを提供しますが、敏感なか、または専門にされた材料との限られた両立性.
Cost and Maintenance Considerations
初期投資と長期メンテナンス コスト
コストは、適切なウェーハチャックを選択する際に重要な役割を果たします. 機械チャック 製造費用を削減するシンプルな設計で、最も費用効果が大きい選択です。 耐久性は、長期メンテナンスコストも削減します. 真空チャック 適度な初期投資を要求しますが、真空ポンプおよびシールの信頼性は維持の必要性を時間とともに増加します. 静電気チャック 高度な技術により、高コストを要求します。 また、電源の依存性や電極の潜在的な摩耗は、より高いメンテナンス費につながる可能性があります.
クリーニングとアップキープの消去
メンテナンスと清掃の要件は、チャックの種類によって異なります. 真空チャック 真空の完全性を維持するためにシールおよびポンプの規則的な点検を必要とします。 ほこりや破片は性能を損なうことができるので、頻繁な清掃は不可欠です. 静電気チャック 電極を傷つけることを避けるために慎重な処理を要求して下さい。 彼らの表面は、一貫した性能を確保するために、汚染物質から解放されなければなりません. 機械チャック、強い構造と、きれいになり、維持することは容易です。 シンプルな設計により、コンポーネントの故障のリスクを低減し、低メンテナンスオプションを実現します.
環境・プロセスの互換性
高温度・真空環境対応
環境条件はウエファーのチャックの性能に著しく影響を与えます. 静電気チャック 高温環境でのエクセル、オプションなど Pyrolytic Boronの窒化物の静電気のチャック(pBN ESCs) 極端な熱に耐えるように設計されています. 真空チャック 標準的な製造条件でよく実行しますが、高湿度や高温の設定に苦労するかもしれません. 機械チャック 環境要因を独立して作動させ、パワーリミットまたはより少ない制御された環境で信頼できるようにします.
特定の製造ワークフローへの適応性
各チャックタイプは、特定の製造ニーズに合わせます. 真空チャック フォトリソグラフィやエッチングなどの高精度な加工に最適です. 静電気チャック デリケートなウェーハや高温プロセスの高度なワークフローをサポート. 機械チャック ウェハダイシングなどのバックエンドタスクに適しており、耐久性とコスト効率性が優先されます。 ワークフローの要件を理解することで、作業を最適化し、生産性を向上させるチャックタイプを選択できます.
ウェーハチャックは、精密で安全なウェーハ処理を実現し、半導体製造を簡素化する重要な役割を果たしています。 各タイプは独特な利点を提供します。 真空チャックは、比類のない精度を実現し、複雑なプロセスに最適です。 静電チャックは、デリケートなウエファーや高温用途の取り扱いに優れています。 機械チャックは、重量または不規則な形状のウェーハに費用対効果の高いソリューションを提供します。 タンデムシリーズや高度なコーティングなどのイノベーションにより、性能と効率性が向上します。 適切なウェーハチャックを選択するには、特定のニーズを評価し、高度な機能を探求し、業界の専門家に適切な推奨事項を合わせる必要があります.
よくあるご質問
半導体製造におけるウェーハチャックの主な目的は何ですか?
ウェーハチャックは、リソグラフィ、エッチング、蒸着などの重要な製造工程においてウェーハを固定します。 高品質の半導体デバイスを作成するために不可欠である精度と安定性を保証します。 ウェハをしっかりと保持することで、複雑なパターンの精度を損なう恐れや動きを防ぎます.
真空のウエファーのチャックは静電気および機械チャックと異なっていますか?
真空のウエファーのチャックはウエファーを安全に握るために否定的な圧力を使用し、均一接触を表面を渡ることを保障します。 静電チャックは、静電力に依存し、物理的な接触なしでウェーハを保護し、繊細なまたは超薄型ウェーハに最適です。 メカニカルチャックは、ウェーハをグリップする機構をクランプし、重量または不規則な形状のウェーハのための費用対効果の高いソリューションを提供します.
静電ウエハチャックを使用する利点は何ですか?
静電ウエハチャックは非接触式保持を実現し、脆弱ウエハへのダメージを最小限に抑えます。 また、熱管理を加速し、高温プロセス中に均一な熱放散を保証します。 これらの特徴は、エピタキシャル成長やプラズマエッチングなどの高度な半導体製造技術に適しています.
すべてのタイプのウエハに適した機械式ウェーハチャックですか?
メカニカルウエハチャックは、標準または重いウエハに適していますが、超薄型または壊れやすいウエハには最適ではありません。 物理的な締め金で止めるメカニズムは不均等な圧力を、傷かひびの危険を高めることができます。 デリケートなウエハ、静電、または真空チャックは、より良い代替品を提供します.
真空ウェーハチャックが性能を維持する際にどのような課題に直面していますか?
真空の完全性を維持することは共通の挑戦です。 シールやポンプなどのコンポーネントの漏れや摩耗は、均一な圧力分布を破壊し、不安定性につながる可能性があります。 高い湿気のような環境要因は、また性能に影響を与えることができます。 定期的なメンテナンスは、一貫した結果を確実にするために不可欠です.
高度なコーティング技術は、ウェーハチャック性能を向上させる方法は?
高度のコーティングは金属の汚染を最小にし、粒子の生成を減らす超平らな、非反応表面を作成します。 これらのコーティングはウエハのチャックの耐久性を高め、寿命を延ばし、維持の必要性を下げます。 また、高純度のプロセスに重要なクリーナー製造環境を確保します.
タンデムシリーズのウエハチャックをユニークにするものは?
タンデムシリーズは、デュアルウエハ実装を可能にする対称設計を採用しています。 2つのウェーハの同時処理を可能にし、機器のコストと処理時間を削減することにより、このイノベーションは効率性を高めます。 また、ウェーハ全体の均一な圧力分布を確保し、安定性とアライメントを維持します.
ウェーハチャックは異なるウェーハサイズや材料に適応できますか?
はい、さまざまなウエハサイズや素材に対応できるウエハチャックも多数あります。 真空チャックは、さまざまな厚さと直径のウェーハを扱う、非常に汎用性の高いものです。 静電気チャックは、デリケートまたは超薄型ウェーハで優れていますが、メカニカルチャックは標準または重いウエハに適しています.
半導体製造で熱ウェーハチャックが再生する役割は?
熱ウエファーのチャックは電気プロービングおよびテストのようなプロセスの間に精密な温度調整を提供します。 それらは正確なテストおよび欠陥の同一証明のために必要であるウエファーの表面を渡る均一熱配分を保障します。 モダンなデザインは、さまざまなサイズのウェーハを処理する複数の真空ゾーンを含みます.
ウェーハチャック市場は、技術の進歩にどのように関与していますか?
ウェーハチャック市場は、IoT、AI、5Gなどの先進的なパッケージング技術と新興トレンドの採用により成長しています。 チャックソリューションの継続的な革新は、近代的な半導体製造の複雑な要件に対処し、効率性の向上と高い歩留まりの機会を提供します.