리튬 이온 배터리는 주로 고에너지 밀도의 방향에서 개발. 실내 온도에서, 리튬을 가진 실리콘 근거한 부정적인 전극 물자 합금은 흑연 부정적인 전극 372 mAh/g의 이론적인 특정한 수용량 보다는 매우 더 높은 3572 mAh/g의 특정한 수용량과 더불어 리튬 부유한 제품 Li3.75Si 단계를, 일으키기 위하여 합금합니다. 그러나, 실리콘 근거한 부정적인 전극 물자의 반복한 위탁 그리고 출력 과정 도중, Si와 Li3.75Si의 단계 변환은 전극 물자의 구조상 powdering 및 SEI 영화의 지속적인 대형에 지도할 거대한 양 팽창 (대략 300%에 관하여)를 일으킬 수 있고, 마지막으로 급속하게 떨어지는 수용량을 일으키는 원인이 됩니다. 산업은 주로 nano-sizing, carbon coating, pore 대형 및 기타 기술을 통해 실리콘 기반 배터리의 실리콘 기반 음극 물질 및 안정성의 성능을 향상시킵니다.
탄소 물자는 좋은 전도도, 저가 및 넓은 근원이 있습니다. 그들은 실리콘 근거한 물자의 전도도 그리고 표면 안정성을 개량할 수 있습니다. 그들은 실리콘 근거한 부정적인 전극을 위한 성과 개선 첨가물로 선호됩니다. 실리콘 탄화수소 물자는 실리콘 근거한 부정적인 전극의 주류 발달 방향입니다. 탄소 코팅은 실리콘 근거한 물자의 표면 안정성을 개량할 수 있습니다, 그러나 실리콘 양 확장을 금하는 그것의 능력은 일반 이고 실리콘 양 확장의 문제를 해결할 수 없습니다. 따라서, 실리콘 근거한 물자의 안정성을 개량하기 위하여, 다공성 구조는 건설될 필요가 있습니다. Ball Milling은 nanomaterials를 준비하는 산업용 방법입니다. 다른 첨가물 또는 물자 성분은 합성 물자의 디자인 필요조건에 따라 공 맷돌로 가는에 의해 얻어지는 슬러리에 추가될 수 있습니다. 슬러리는 다양한 슬러리와 스프레이 건조를 통해 균등하게 분산됩니다. 즉시 건조 과정 도중, 슬러리에 있는 nanoparticles 그리고 다른 성분은 다공성 구조상 특성을 형성할 것입니다. 이 종이는 산업화하고 환경에 친절한 공 맷돌로 갈고 살포 건조 기술을 사용하여 다공성 실리콘 근거한 물자를 준비합니다.
실리콘 근거한 물자의 성과는 또한 실리콘 nanomaterials의 형태학 그리고 배급 특성을 통제해서 개량될 수 있습니다. 현재 다양한 morphologies 및 유통 특성을 가진 실리콘 기반 재료는 실리콘 나노로드, 다공성 흑연에 내장 된 nanosilicon, nanosilicon 탄소 영역, 실리콘 / graphene 배열 다공성 구조 등 준비되었습니다. nanoparticles와 비교된 동일한 가늠자에, nanosheets는 볼륨 확장에 기인한 분쇄 문제를 더 잘 억압할 수 있고, 물자는 더 높은 압축 조밀도가 있습니다. nanosheets의 무질서 겹쳐 쌓이는 것은 또한 porous 구조를 형성할 수 있습니다. 실리콘 부정적인 전극 교환 그룹에 가입하십시오. 실리콘 재료의 볼륨 확장을위한 버퍼 공간을 제공합니다. 탄소 나노 튜브 (CNT)의 도입은 재료의 전도성을 향상시킬뿐만 아니라 하나의 차원 형태 특성 때문에 재료의 다공성 구조의 형성을 촉진 할 수 없습니다. 실리콘 나노 시트 및 CNT에 의해 건설 된 다공성 구조에 대한 보고서가 없습니다. 이 종이는 산업적으로 적용 가능한 볼 밀링, 연삭 및 분산, 스프레이 건조, 탄소 사전 코팅 및 calcination 방법을 채택하고, 실리콘 나노 시트 및 CNT의 자체 조립에 의해 형성 된 다공성 실리콘 기반 음극 물질을 준비하는 준비 과정에서 다공성 추진기를 소개합니다. 준비 과정은 간단하고 환경 친화적이며 폐기물 액체 또는 폐기물 잔류물이 생성되지 않습니다. 실리콘 근거한 물자의 탄소 코팅에 많은 문학 보고가 있습니다, 그러나 코팅의 효력에 약간 심상 토론이 있습니다. 이 종이는 코팅 효력에 2개의 탄소 코팅 방법, 액체 단계 코팅 및 단단한 단계 코팅의 효력을 조사하기 위하여 탄소 근원으로 아스팔트를 이용하고 실리콘 근거한 부정적인 전극 물자의 성과.
1 실험
1.1 물자 준비
다공성 실리콘 탄소 복합 재료의 준비는 주로 5 단계가 포함되어 있습니다 : 볼 밀링, 연삭 및 분산, 스프레이 건조, 탄소 사전 코팅 및 탄소화. 첫 번째, 무게 500 g의 초기 실리콘 분말 (국내, 99.99% 순도), isopropanol의 2000 g를 추가하고 나노 스케일 실리콘 슬러리를 얻기 위해 24 시간 동안 2000 r / 분의 공 밀링 속도로 젖은 볼 밀링을 수행합니다. 얻어진 실리콘 슬러리는 분산 이동 탱크로 옮겨지고, 물자는 실리콘의 질량 비율에 따라 추가됩니다: 흑연 (상해에서 생성해, 건전지 급료): 탄소 nanotubes (톈진, 건전지 급료에서 생성해): polyvinyl pyrrolidone (톈진, 분석 급료에서 생성해) = 40:60:1.5:2. Isopropanol는 단단한 내용을 조정하기 위하여 이용되고, 단단한 내용은 15%이기 위하여 디자인됩니다. 가는과 분산은 4 h를 위한 3500 r/min의 분산 속도로 실행됩니다. CNT를 추가하지 않고 슬러리의 또 다른 그룹은 비교되고 다른 재료는 동일합니다. 얻은 분산 슬러리는 살포 건조 먹이는 탱크로 옮겨지고, 살포 건조는 인레트와 출구 온도가 180와 90 °C인 질소 보호한 대기에서, 각각 실행됩니다. 그 후에 탄소 코팅의 2가지의 유형은, 단단한 단계 코팅 및 액체 단계 코팅 비교되었습니다. 단상 코팅 방법은: 살포 건조한 분말은 20% 아스팔트 분말 (한국에서 만드는, D50는 5 μm입니다), 10 분을 위한 기계적인 믹서에서 섞이고, 섞는 속도는 2000 r/min에 전 입히는 분말을 얻기 위하여 섞입니다. 액상 코팅 방법은: 살포 건조된 분말은 55%의 단단한 내용에 분말에서 녹이는 20% 아스팔트를 포함하는 xylene 해결책 (톈진, 분석 급료에서 만드는)에 추가되고, 진공 균등하게 균등하게 동등합니다. 4h를 위한 85°C에 진공 오븐에서 Bake는, 섞기를 위한 기계적인 믹서로 끼워넣고, 섞는 속도는 2000 r/min이고, 섞는 시간은 전 입히는 분말을 얻기 위하여 10 분입니다. 마지막으로, 사전 코팅된 분말은 5°C/min의 난방 비율에 질소 대기권의 밑에 회전하는 킬른에서 calcined. 그것은 550°의 일정한 온도에 첫째로 지켜졌습니다 2h를 위한 C, 그 후에 800°까지 가열하는 것을 계속하십시오 C는 2h를 위한 일정한 온도에 지키고, 그 후에 100°의 밑에 자연적으로 냉각해 C 및 실리콘 탄소 복합 재료를 얻기 위해 배출.
1.2 특성화 방법
재료의 입자 크기 분포는 입자 크기 테스터 (Mastersizer 2000 버전, 영국에서 만든)를 사용하여 분석되었습니다. 각 단계에서 얻은 분말은 전자 현미경 검사 (Regulus8220, 일본에서 만든)를 검사하여 분말의 형태 및 크기를 검사합니다. 재료의 단계 구조는 X-ray 분말 확산 분석기를 사용하여 분석되었습니다 (독일에서 만든 D8 ADVANCE), 재료의 원소 구성은 에너지 스펙트럼 분석기를 사용하여 분석되었습니다. 얻어진 실리콘 탄소 합성 물자는 모형 CR2032의 단추 반 세포를 만들고, 실리콘 탄소의 질량 비율을 만들기 위하여 이용됩니다: SP: CNT: CMC: SBR는 92:2:2:1.5:2.5이었습니다. 카운터 전극은 금속 리튬 장, 전해질입니다 상업적인 전해질 (한국에서 만든 모형 1901년), Celgard 2320 격막 사용됩니다, 책임 및 출력 전압 범위는 0.005-1.5 V, 책임이고 방전 현재는 0.1 C (1C = 1A)이고, 출력 커트오프 현재는 0.05 C입니다.
실리콘 탄화수소 복합 재료의 성능을 조사하기 위해 작은 소프트 팩 배터리 408595을 만들었습니다. 긍정 전극은 NCM811 (후난, 건전지 급료에서 만들어)를 사용하고, 부정적인 전극 흑연은 8% 실리콘 탄소 물자로 도핑됩니다. 긍정적인 전극 슬러리 공식은 96% NCM811, 1.2% polyvinylidene 불화물 (PVDF), 2% 전도성 대리인 SP, 0.8% CNT이고, NMP는 분산제로 사용됩니다; 부정적인 전극 슬러리 공식은 96% 합성 부정적인 전극 물자, 1.3% CMC, 1.5% SBR 1.2% CNT이고, 물은 분산제로 사용됩니다. 교반 후에, 코팅, 회전, 절단, 박판, 탭 용접, 포장, 굽기, 액체 주입, 대형 및 수용량 부, 408595는 3 Ah의 정격 수용량을 가진 작은 연약한 팩 건전지를 준비했습니다. 0.2C, 0.5C, 1C, 2C 및 3C의 비율 성과 및 0.5C 책임의 주기 성과는 시험되었습니다. 책임과 출력 전압 범위는 2.8-4.2 V, 일정한 현재 및 일정한 전압 위탁이고, 커트오프 현재는 0.5C였습니다.
2 결과 및 토론
초기 실리콘 분말은 전자 현미경 검사 (SEM)에 의해 관찰되었습니다. 실리콘 분말은 2μm 미만의 입자 크기로 불규칙하게 과립되었습니다. 그림 1 (a)에 보이는 것과 같이. 볼 밀링 후 실리콘 분말의 크기는 100 nm [Figure 1 (b)]에 크게 감소되었습니다. 입자 크기 시험은 공 맷돌로 가는 후에 실리콘 분말의 D50가 110 nm이고 D90는 175 nm이었습니다. 볼 밀링 후 실리콘 분말의 morphology의 신중한 시험은 flaky 구조를 보여줍니다 (flaky 구조의 형성은 단면 SEM에서 나중에 더 확인 될 것입니다). 따라서, 입자 크기 시험에서 얻은 D90 자료는 nanosheet의 길이 차원이어야 합니다. SEM 결과와 결합 된, 그것은 얻은 나노 시트의 크기가 적어도 하나의 치수를 충전하고 출력하는 동안 실리콘 분말의 파손의 150 nm보다 작다는 것을 판단 할 수 있습니다. flaky morphology의 형성은 주로 크리스탈 실리콘의 결정면의 다른 연관 에너지로 인해, 실리콘의 {111} 비행기가 {100} 및 {110} 크리스탈 비행기보다 낮은 연관 에너지를 가지고있다. 따라서,이 크리스탈 비행기는 볼 밀링에 의해 더 쉽게 얇은, 마지막으로 flaky 구조를 형성. flaky 구조는 느슨한 구조의 축적에 공헌하고, 실리콘의 양 확장을 위한 공간을 예비하고, 물자의 안정성을 개량합니다.
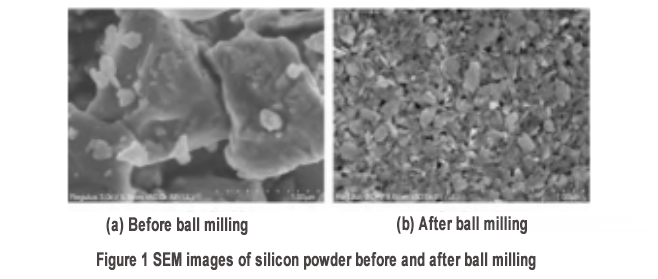
Nano-silicon, CNT 및 흑연을 함유 한 슬러리가 스프레이 된 후 분말은 SEM에 의해 검사되었습니다. 결과는 그림 2에서 표시됩니다. 살포하기 전에 추가되는 흑연 모체는 5 20 μm [Figure 2 (a)]의 크기로 전형적인 조각 구조입니다. 흑연의 입자 크기 배급 시험은 D50가 15μm임을 보여줍니다. 살포 후에 얻어지는 분말에는 둥근 morphology [Figure 2 (b)]가 있고, 살포 후에 코팅 층에 의해 흑연이 입혀 보일 수 있습니다. 살포 후에 분말의 D50는 26.2 μm입니다. 이차 입자의 형태적 특성은 SEM에 의해 관찰되었으며, 나노 물질에 의해 축적 된 느슨한 구조의 특성을 보여줍니다 [Figure 2 (c)]. 다공성 구조는 실리콘 나노 시트와 CNTs로 구성되어 각각 다른 [Figure 2 (d)], 테스트 특정 표면 영역 (BET)는 53.3 m2/g로 높다. 따라서, 살포 후에, 실리콘 nanosheets 및 숨구멍 구조를 형성하는 CNTs 각자 소집.
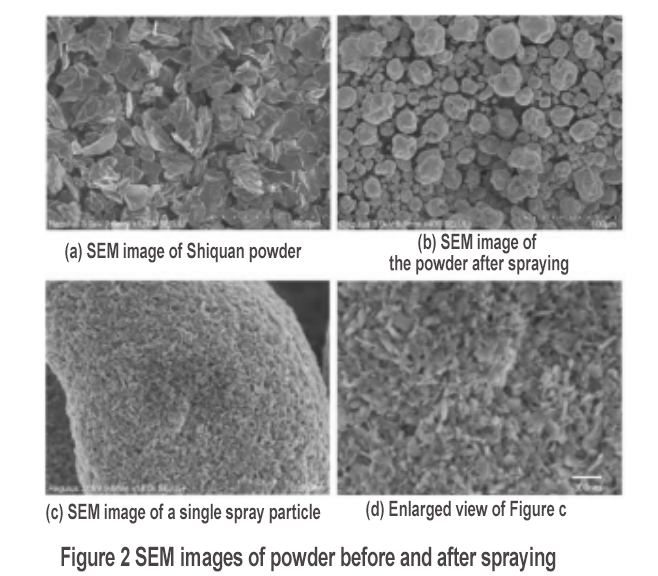
다공성 층은 액체 탄소 코팅으로 대우되고, 탄소 코팅 precursor 피치 및 carbonization를 추가한 후에, SEM 관측은 실행되었습니다. 결과는 그림 3에서 표시됩니다. 탄소 전 코팅 후에, 이차 입자의 표면은 명백한 코팅 층과 더불어 매끄럽게 되고, 코팅은 그림 3 (a) 및 (b)에서 보이는 것과 같이 완료됩니다. 탄소화 후에, 표면 코팅 층은 좋은 코팅 국가 [Figure 3 (c)]를 유지합니다. 또한, 단면 SEM 이미지는 스트립 모양의 nanoparticles [Figure 3 (d)]를 보여줍니다. 나노 시트의 변형 특성에 대응하는 것은 볼 밀링 후 실리콘 나노 시트의 형성을 더욱 검증합니다. 또한 그림 3 (d)는 일부 나노 시트 사이의 필러가 있음을 보여줍니다. 이것은 액체 단계 코팅 방법의 사용 때문에 주로 입니다. 아스팔트 해결책은 물자로 관통할 것입니다, 그래서 내부 실리콘 nanosheets의 표면은 탄소 코팅 방어적인 층을 얻습니다. 따라서, 액체 단계 코팅을 사용해서, 이차 입자 코팅 효력을 얻기 이외에, 1 차적인 입자 코팅의 두 배 탄소 코팅 효력은 또한 얻어질 수 있습니다. 탄화된 분말은 BET에 의해 시험되고, 시험 결과는 22.3 m2/g이었습니다.
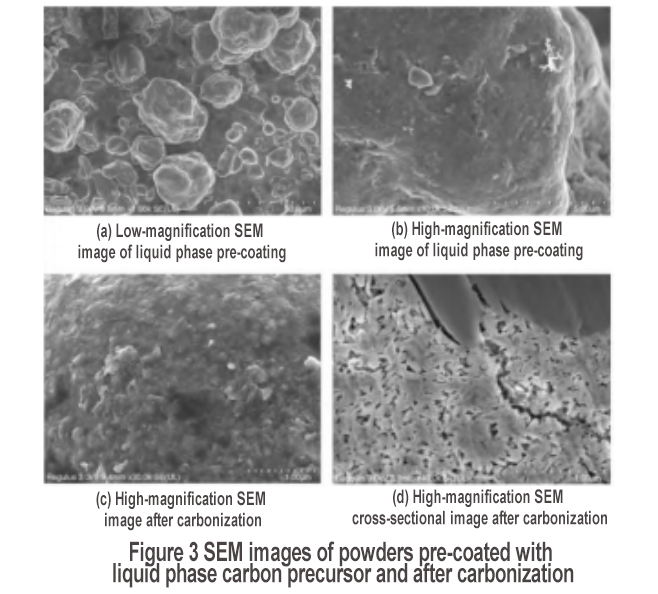
탄화된 분말은 단면 에너지 스펙트럼 분석 (EDS)에 적용되고, 결과는 그림 4 (a)에서 보입니다. 미크론 크기의 코어는 흑연 매트릭스에 대응하는 C 구성 요소이며 외부 코팅은 실리콘과 산소를 함유합니다. 실리콘의 구조를 더 조사하려면 X-ray diffraction (XRD) 테스트가 수행되었으며 결과는 그림 4 (b)에 표시됩니다. 물자는 흑연과 단결정 실리콘으로 주로, 명백한 실리콘 산화물 특성 없이, 에너지 스펙트럼 시험의 산소 성분이 실리콘 표면의 자연적인 산화에서 주로 옵니다 있다는 것을 나타냅니다. 실리콘 탄소 복합 재료는 S1로 기록됩니다.
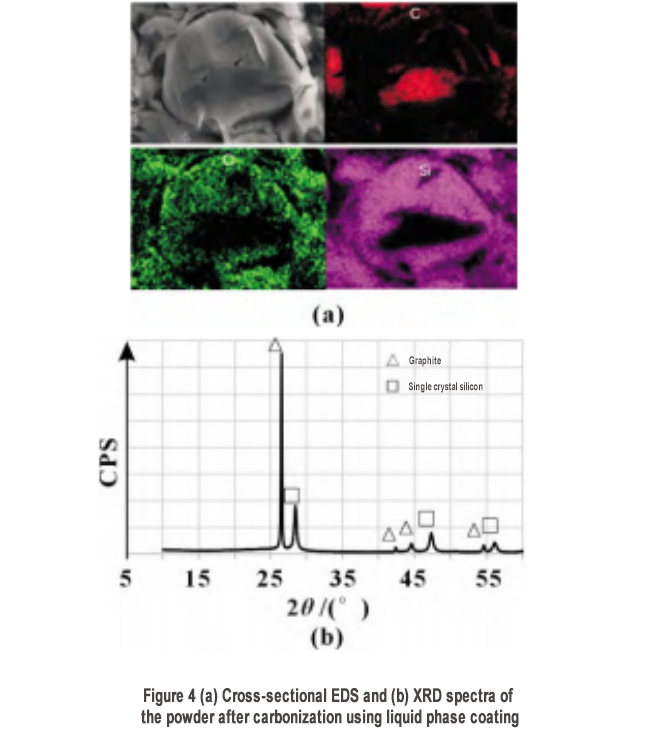
준비된 실리콘 탄소 재료 S1는 버튼 유형 반 셀 생산 및 충전 방전 시험에 적용되었습니다. 첫번째 책임 방전 곡선은 그림 5에서 보입니다. 뒤집을 수 있는 특정한 수용량은 1000.8 mAh/g이고, 첫번째 주기 효율성은 93.9%로, 문학에서 보고된 가장 실리콘 근거한 물자의 첫번째 효율성 보다는 더 높습니다. 높은 첫번째 효율성은 준비한 실리콘 탄소 복합 재료가 높은 안정성을 나타냅니다. 다공성 구조의 효력을 확인하기 위하여, 전도성 네트워크 및 탄소 코팅은 실리콘 탄소 물자의 안정성에, 실리콘 탄소 물자의 2가지의 유형 CNT를 추가하고 1 차적인 탄소 코팅 없이 준비되었습니다.
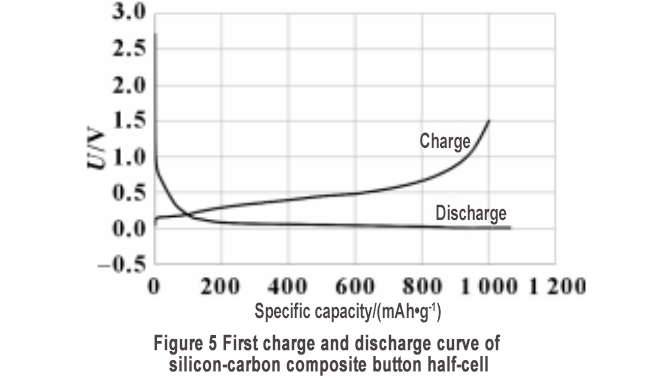
CNT를 첨가하지 않고 실리콘 탄화수소 복합 재료의 탄화 분말의 형태는 그림 6.에 표시됩니다. 액체 단계 코팅과 carbonization 후에, 코팅 층은 그림 6 (a)에 있는 이차 입자의 표면에 명확하게 보일 수 있습니다. 탄화된 물자의 단면 SEM는 숫자 6 (b)에서 보입니다. 실리콘 나노 시트의 겹쳐 쌓이는 다공성 특성을 가지고 있으며 BET 테스트는 16.6 m2/g입니다. 그러나, CNT와 비교 [그림 3 (d)에서 보이는 것처럼, 그것의 탄화한 분말의 BET 시험은 22.3 m2/g], 내부 nano-silicon 겹쳐 쌓이는 조밀도가 더 높다는 것을 나타내고, CNT의 추가가 다공성 구조의 대형을 승진시킬 수 있다는 것을 나타냅니다. 또한, 재료는 CNT에 의해 건설 된 3 차원 전도성 네트워크가 없습니다. 실리콘 탄소 복합 재료는 S2로 기록됩니다.
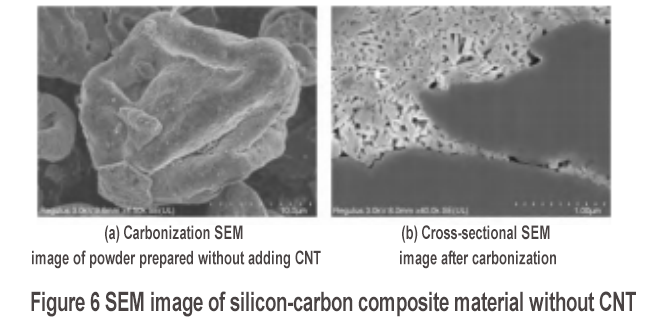
고체 탄소 코팅에 의해 준비된 실리콘 탄소 복합 재료의 형태 특성은 숫자 7.에서 표시됩니다. 탄소화 후에, 그림 7 (a)에서 보이는 것과 같이 표면에 명백한 코팅 층이 있습니다. Figure 7(b)는 nanosheets의 변형 특성에 대응하는 크로스 섹션의 스트립 모양의 나노 입자가 있음을 보여줍니다. nanosheets의 축적은 다공성 구조를 형성합니다. 내부 nanosheets의 표면에 명백한 충전물이 없습니다, 단단한 단계 탄소 코팅은 다공성 구조를 가진 탄소 코팅 층을 형성하고, 실리콘 nanosheets를 위한 내부 코팅 층이 없습니다. 이 실리콘 탄소 복합 재료는 S3로 기록됩니다.
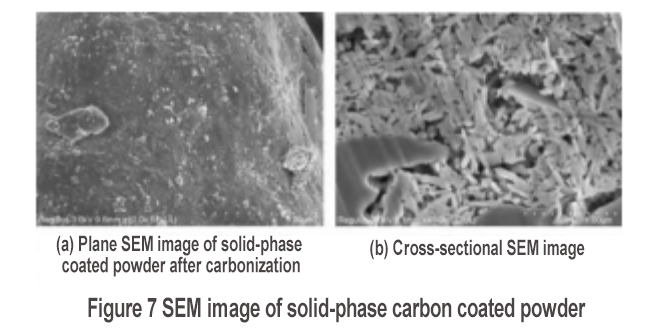
단추 유형 반 세포 책임과 출력 시험은 S2와 S3에 지휘되었습니다. S2의 특정한 수용량 그리고 첫번째 효율성은 각각 1120.2 mAh/g와 84.8%이고, S3의 특정한 수용량 그리고 첫번째 효율성은 각각 882.5 mAh/g 및 82.9%이었습니다. 고체 코팅 S3 샘플의 특정 용량과 첫 번째 효율은 가장 낮았으며, 다공성 구조의 탄소 코팅 만 수행되었으며 내부 실리콘 나노 시트의 탄소 코팅은 수행되지 않았습니다. 실리콘 기반 재료의 특정 용량에 전체 재생을 제공하지 않으며 실리콘 기반 재료의 표면을 보호 할 수 없습니다. CNT 없는 S2 표본의 첫번째 효율성은 또한 CNT를 포함하는 실리콘 탄소 합성 물자의 그것 보다는 더 낮습니다, 좋은 코팅 층의 기초에, 전도성 네트워크 및 다공성 구조의 더 높은 정도는 실리콘 탄소 물자의 책임 그리고 출력 효율성의 개선에 공헌합니다.
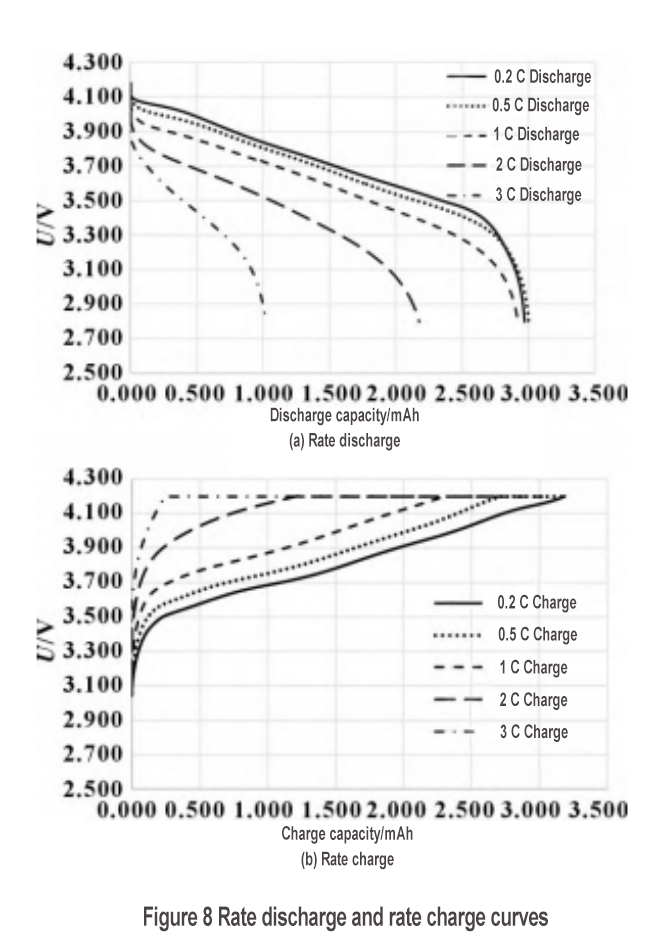
S1 실리콘 탄소 물자는 비율 성과와 주기 성과를 시험하기 위하여 작은 연약한 팩 가득 차있는 건전지를 만들기 위하여 이용되었습니다. 출력 비율 곡선은 그림 8 (a)에서 보입니다. 0.2C, 0.5C, 1C, 2C 및 3C의 출력 수용량은 2.970, 2.999, 2.920, 2.176 및 1.021입니다 아, 각각. 1C 방전 비율은 98.3%로 높지만, 2C 방전 비율은 73.3%로 떨어지고, 3C 방전 비율은 34.4%로 더 떨어졌습니다. 실리콘 부정적인 전극 교환 그룹에 가입하려면 WeChat : shimobang을 추가하십시오. 충전율 측면에서 0.2C, 0.5C, 1C, 2C 및 3C 충전 용량은 3.186, 3.182, 3.081, 2.686 및 2.289입니다. 아, 각각. 1C 충전율은 96.7%이며, 2C 충전율은 여전히 84.3%에 도달합니다. 그러나, 숫자 8 (b)에 있는 위탁 곡선을 관찰해서, 2C 위탁 플랫폼은 1C 위탁 플랫폼 보다는 현저하게 더 큽니다, 대부분의 (55%)를 위한 그것의 일정한 전압 위탁 수용량 계정, 2C 재충전 전지의 극화가 이미 아주 크다는 것을 나타내는. 실리콘 탄소 물자는 1C에 좋은 위탁 그리고 출력 성과가 있습니다, 그러나 물자의 구조상 특성은 더 높은 비율 성과를 달성하기 위하여 개량될 필요가 있습니다. 그림 9에서 보이는 것과 같이, 450 주기 후에, 수용량 보유 비율은 좋은 주기 성과를 보여주는 78%입니다.
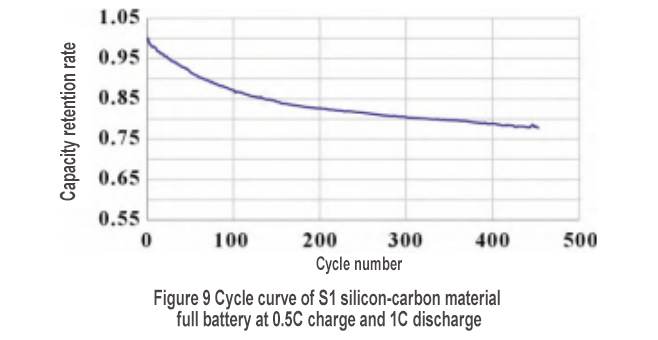
전 전극의 표면 상태와 사이클이 SEM에 의해 조사 된 후 결과는 그림 10에서 표시됩니다. 주기의 앞에, 흑연과 실리콘 탄소 물자의 표면은 명확합니다 [Figure 10 (a)]; 주기 후에, 코팅 층은 두꺼운 SEI 영화인 표면 [Figure 10 (b)]에 명백하게 생성합니다. SEI 필름 거칠기 활동적인 리튬 소비는 주기 성과에 conducive 하지 않는 높습니다. 따라서, 매끄러운 SEI 영화의 형성을 승진시킵니다 ( 인공적인 SEI 영화 건축과 같은, 적당한 electrolyte 첨가물 추가, 등) 주기 성과를 개량할 수 있습니다. 사이클 [Figure 10 (c)] 후 실리콘 탄소 입자의 단면 SEM 관측은 원래의 스트립 모양의 실리콘 나노 입자가 coarser되고 다공성 구조가 기본적으로 제거되었습니다. 이것은 주기 도중 실리콘 탄소 물자의 지속적인 양 확장 그리고 수축 때문에 주로 입니다. 따라서, 다공성 구조는 실리콘 근거한 물자의 양 확장을 위한 충분한 완충기 공간을 제공하기 위하여 더 강화되어야 합니다.
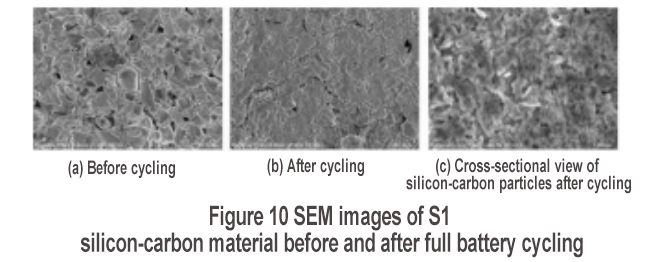
3 결론
실리콘 나노 시트, 다공성 구조 건설, 전도성 네트워크 건설 및 전체 이차 입자의 탄소 코팅을 완료하는 실리콘 나노 시트, 다공성 구조 건설, 전도성 네트워크 건설 및 전체 이차 입자의 탄소 코팅의 변종 개선을 바탕으로 실리콘 기반 부정적인 전극 재료의 안정성을 전체로 향상시킵니다. 실리콘 나노 시트의 축적은 다공성 구조를 형성 할 수 있습니다. CNT의 도입은 더 다공성 구조의 형성을 촉진합니다. 액체 단계 코팅에 의해 준비된 실리콘 탄소 복합 재료는 단단한 단계 코팅에 의해 준비된 두 배 탄소 코팅 효력을 비치하고, 더 높은 특정한 수용량 및 첫번째 효율성을 전시합니다. 또한, CNT를 함유 한 실리콘 탄소 복합 재료의 첫 번째 효율은 주로 실리콘 기반 재료의 볼륨 팽창을 완화하는 데 특이한 구조의 높은 정도로 인해 CNT없이 더 높다. CNT의 소개는 3차원 전도성 네트워크를 건설하고, 실리콘 근거한 물자의 전도도를 개량하고, 1C에 좋은 비율 성과를 보여줍니다; 그리고 물자는 좋은 주기 성과를 보여줍니다. 그러나 재료의 다공성 구조는 실리콘의 볼륨 확장을위한 충분한 버퍼 공간을 제공하기 위해 더 강화되어야하며, 실리콘 탄소 복합 재료의 사이클 성능을 향상시키기 위해 스플래드 밀도 SEI 필름의 형성을 촉진합니다.
우리는 또한 산화, 확산 및 어닐링과 같은 웨이퍼 가공에 널리 사용되는 고순도 흑연 및 실리콘 카바이드 제품을 공급합니다.
더 많은 토론을 위해 우리를 방문하기 위해 전 세계의 모든 고객을 환영합니다!