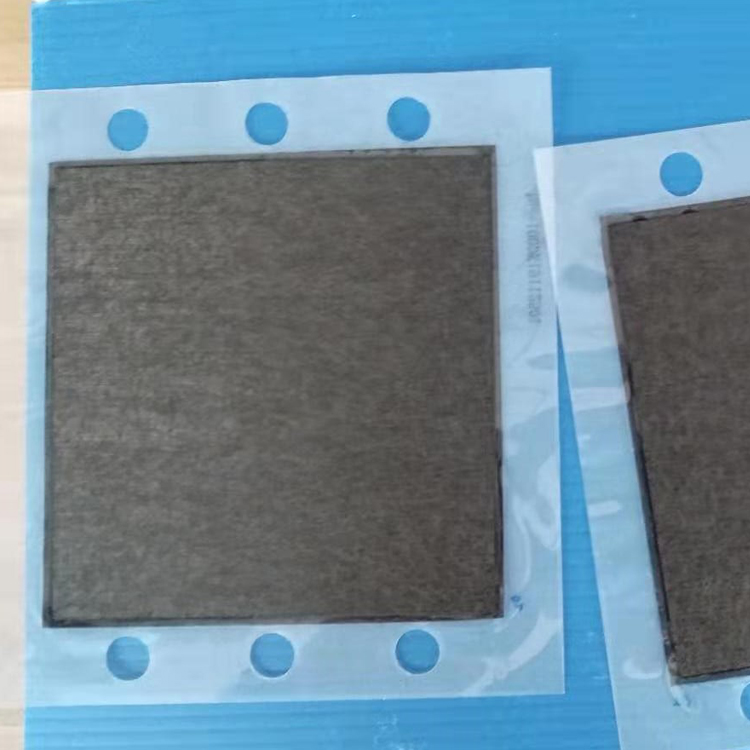
A membrane electrode assembly serves as the heart of electrochemical devices like fuel cells and electrolyzers. It combines multiple layers, including a proton exchange membrane, catalyst layers, and a gas diffusion electrode, to drive efficient energy conversion. This assembly enables electrochemical reactions that transform chemical energy into electrical energy or vice versa. Its design directly impacts the performance and efficiency of these devices, making it a critical component in advancing clean energy technologies. As industries shift toward renewable energy, the role of the membrane electrode assembly becomes even more significant.
Key Takeaways
- Membrane electrode assemblies (MEAs) are crucial for the efficiency of electrochemical devices like fuel cells and electrolyzers, enabling effective energy conversion.
- The key components of an MEA include the proton exchange membrane (PEM), catalyst layers, gas diffusion layers (GDL), and electrodes, each playing a vital role in performance.
- Optimizing the design of MEAs, such as reducing membrane thickness and enhancing catalyst layers, can significantly improve energy efficiency and output.
- Material innovations, including advanced polymers and non-noble metal catalysts, are essential for increasing the durability and reducing the costs of MEAs.
- MEAs are integral to various applications, from hydrogen production in electrolyzers to powering zero-emission vehicles, supporting the transition to sustainable energy.
- Emerging technologies, such as electrocatalytic CO2 reduction, showcase the versatility of MEAs in addressing environmental challenges and advancing clean energy solutions.
- Continuous research and development in MEA technology are vital for enhancing performance and making clean energy systems more accessible and cost-effective.
Components of a Membrane Electrode Assembly
Understanding the components of a membrane electrode assembly is essential to grasp how it functions as the core of electrochemical devices. Each layer plays a unique role in ensuring efficient energy conversion. Let’s explore these components in detail.
Proton Exchange Membrane (PEM)
The proton exchange membrane (PEM) serves as the backbone of the membrane electrode assembly. This thin, polymer-based layer allows protons to pass through while blocking electrons and gases. Its primary function is to facilitate proton transfer between the anode and cathode during electrochemical reactions.
You’ll find that the PEM is crucial for maintaining the separation of reactants, which ensures the efficiency and safety of the system. For example, in a fuel cell, the PEM prevents hydrogen and oxygen from mixing while enabling the flow of protons. Advanced PEMs, such as those used in 7-layer MEAs, often incorporate additional materials to enhance durability and performance under demanding conditions.
Catalyst Layers
The catalyst layers are where the magic of electrochemical reactions happens. These layers, positioned on either side of the PEM, contain finely dispersed catalyst particles, typically platinum or other noble metals. The catalyst facilitates the reactions that split hydrogen molecules into protons and electrons at the anode and combine protons, electrons, and oxygen to form water at the cathode.
To ensure optimal performance, the catalyst layers also include ionomers. These ionomers create a proton transfer network within the layer, improving proton conductivity and mechanical strength. For instance, hydrophobic properties in the catalyst layer help manage water produced during reactions, preventing flooding and maintaining efficiency.
Gas Diffusion Layers (GDL)
The gas diffusion layers (GDL) sit adjacent to the catalyst layers and perform several critical functions. They distribute reactant gases evenly across the catalyst surface, ensuring uniform reactions. Additionally, GDLs manage water by allowing excess water to escape while retaining enough moisture to keep the PEM hydrated.
You’ll notice that GDLs are designed with a porous structure, which balances gas flow and water management. In advanced MEA designs, such as those used in heavy-duty transport, GDLs are engineered to withstand high current densities and harsh operating conditions. This ensures consistent performance over extended periods.
By combining these components—PEM, catalyst layers, and GDLs—the membrane electrode assembly achieves its role as the heart of electrochemical devices. Each layer contributes to the overall efficiency, durability, and functionality of the system, making it indispensable in clean energy technologies.
Electrodes
The electrodes in a membrane electrode assembly (MEA) play a pivotal role in facilitating electrochemical reactions. These components act as the interface where reactants meet the catalyst layers, enabling the conversion of chemical energy into electrical energy or vice versa. Understanding their structure and function helps you appreciate their importance in the overall performance of electrochemical devices.
What Are Electrodes Made Of?
Electrodes typically consist of a conductive material, such as carbon-based substrates, which ensures efficient electron transfer. Manufacturers often enhance these substrates with advanced materials like platinum-based catalysts or novel carbon supports. These enhancements improve reaction rates and reduce energy losses. For instance, innovations in electrode materials have led to significant advancements in fuel cell efficiency and cost reduction.
Scientific Research Findings: Studies highlight that integrating advanced materials into electrodes can extend the lifespan of MEAs and boost their performance. Platinum-based catalysts, combined with optimized carbon supports, have proven to be highly effective in achieving these goals.
How Do Electrodes Function?
Electrodes serve as the site where reactants, such as hydrogen and oxygen, interact with the catalyst layers. At the anode, hydrogen molecules split into protons and electrons. The protons pass through the proton exchange membrane, while the electrons travel through an external circuit, generating electricity. At the cathode, oxygen combines with protons and electrons to form water, completing the reaction.
This process relies on the electrodes’ ability to maintain strong contact with the catalyst layers and ensure uniform distribution of reactants. Any defects in the electrode structure can disrupt this balance, leading to reduced efficiency or stack degradation.
Why Are Electrodes Crucial for MEA Performance?
Electrodes directly influence the efficiency, durability, and cost of MEAs. Optimizing their design parameters, such as thickness and conductivity, can significantly enhance current density in fuel cells. For example, the catalyst-coated membrane (CCM) method improves the contact between the membrane and catalyst layer, resulting in higher peak power density compared to other fabrication methods.
Key Insight: Advanced electrode designs not only improve performance but also address challenges like water management and gas distribution. This ensures consistent operation under varying conditions, making them indispensable in high-performance applications.
Real-World Applications of Electrodes
Electrodes are integral to various clean energy technologies, including fuel cells and electrolyzers. In heavy-duty transport, robust electrode designs withstand high current densities and harsh environments. Emerging technologies, such as electrocatalytic CO2 reduction, also rely on innovative electrode materials to achieve carbon neutrality.
By focusing on material innovations and design optimization, researchers and manufacturers continue to push the boundaries of what electrodes can achieve. This progress underscores their critical role in advancing sustainable energy solutions.
How a Membrane Electrode Assembly Works
Understanding how a membrane electrode assembly (MEA) operates helps you appreciate its role in electrochemical devices. Each layer within the MEA works together to enable efficient energy conversion. Let’s break down the process.
Electrochemical Reactions
Electrochemical reactions form the foundation of how an MEA functions. These reactions occur at the interface of the catalyst layers and electrodes. In a proton exchange membrane fuel cell (PEMFC), the process begins at the anode. Hydrogen molecules split into protons and electrons. The protons pass through the proton exchange membrane, while the electrons travel through an external circuit, generating electricity.
At the cathode, oxygen reacts with the incoming protons and electrons to form water. This reaction completes the circuit and produces the byproduct of water. The efficiency of these reactions depends on the precise design of the MEA. For instance, the thickness of the membrane and the properties of the catalyst layers significantly influence reaction rates and overall performance.
Scientific Research Findings: Studies highlight that parameters such as membrane thickness, catalyst porosity, and ionomer resistance directly impact the efficiency of electrochemical reactions. Optimizing these factors enhances the MEA’s ability to sustain high current densities.
Role of Each Component
Each component of the membrane electrode assembly plays a specific role in ensuring smooth operation. Here’s how they contribute:
-
Proton Exchange Membrane (PEM): The PEM acts as a selective barrier. It allows protons to pass through while blocking electrons and gases. This separation ensures that the electrochemical reactions proceed efficiently without reactant mixing.
-
Catalyst Layers: These layers facilitate the chemical reactions. At the anode, the catalyst splits hydrogen into protons and electrons. At the cathode, it enables the combination of protons, electrons, and oxygen to form water. The catalyst’s composition, such as platinum-based materials, determines the reaction speed and energy efficiency.
-
Gas Diffusion Layers (GDL): The GDLs distribute reactant gases evenly across the catalyst surface. They also manage water by removing excess moisture while maintaining hydration for the PEM. This balance is critical for consistent performance.
-
Electrodes: The electrodes serve as the interface where reactants meet the catalyst layers. They ensure efficient electron transfer and uniform distribution of reactants. Advanced electrode designs improve durability and reduce energy losses.
Key Insight: The integration of these components within the MEA creates a system capable of converting chemical energy into electrical energy with minimal losses. For example, innovations in catalyst-coated membranes (CCMs) enhance the contact between layers, boosting efficiency.
By understanding the roles of each component and the electrochemical reactions they enable, you can see why the membrane electrode assembly is considered the heart of electrochemical devices. Its design and functionality directly influence the performance of technologies like fuel cells and electrolyzers.
Applications of Membrane Electrode Assemblies
Membrane electrode assemblies (MEAs) play a pivotal role in advancing clean energy solutions. Their versatility enables their use in various applications, each contributing to a more sustainable future. Let’s explore how MEAs drive innovation in fuel cells, electrolyzers, and emerging technologies.
Fuel Cells
Fuel cells rely on membrane electrode assemblies to generate electricity through electrochemical reactions. These devices convert hydrogen and oxygen into water, producing electrical power in the process. MEAs serve as the core of this system, ensuring efficient energy conversion and minimal energy loss.
You’ll find MEAs in different types of fuel cells, such as proton exchange membrane fuel cells (PEMFCs). These fuel cells are widely used in transportation, portable power systems, and stationary energy storage. For example, hydrogen-powered vehicles use PEMFCs to achieve zero-emission performance. The MEA’s design directly impacts the fuel cell’s efficiency, durability, and cost-effectiveness. Recent advancements, such as the catalyst-coated membrane (CCM) method, have improved catalyst utilization and reduced contact resistance, resulting in higher power output.
Did You Know? Fuel cells equipped with advanced MEAs are becoming competitive alternatives to conventional combustion engines, offering cleaner and more efficient energy solutions.
Electrolyzers
Electrolyzers use membrane electrode assemblies to split water into hydrogen and oxygen through electrolysis. This process produces green hydrogen, a clean energy carrier with vast potential in decarbonizing industries. MEAs enable the efficient transfer of ions and electrons, ensuring high performance during hydrogen production.
You’ll see electrolyzers with MEAs in applications like renewable energy storage and industrial hydrogen production. For instance, wind and solar farms often pair with electrolyzers to store excess energy as hydrogen. This stored hydrogen can later be converted back into electricity or used as a fuel. The durability and efficiency of the MEA are critical for the long-term operation of electrolyzers. Innovations in MEA materials, such as enhanced membranes and catalysts, have significantly improved their performance under high current densities.
Key Insight: The integration of advanced MEAs in electrolyzers supports the global push toward carbon neutrality by enabling scalable and cost-effective hydrogen production.
Emerging Technologies
The versatility of membrane electrode assemblies extends beyond traditional applications. Emerging technologies are leveraging MEAs to address new challenges in energy and environmental sustainability. One promising area is electrocatalytic CO2 reduction, where MEAs facilitate the conversion of carbon dioxide into valuable chemicals and fuels. This technology holds potential for reducing greenhouse gas emissions while creating useful byproducts.
You’ll also find MEAs in next-generation energy systems, such as solid oxide fuel cells and hybrid energy devices. Researchers are exploring innovative designs and materials to expand the capabilities of MEAs. For example, scalable architectures are being developed to enhance the efficiency of electrochemical synthesis processes. These advancements position MEAs as key enablers of cutting-edge technologies that aim to reshape the energy landscape.
Real-World Impact: Emerging applications of MEAs, like CO2 reduction and hybrid systems, demonstrate their potential to drive innovation in clean energy and environmental solutions.
By supporting fuel cells, electrolyzers, and emerging technologies, membrane electrode assemblies play a central role in the transition to sustainable energy systems. Their adaptability and continuous improvement make them indispensable in addressing the world’s energy and environmental challenges.
Importance and Advancements in Membrane Electrode Assembly Technology
The evolution of membrane electrode assembly technology has been pivotal in advancing clean energy solutions. As industries strive for higher efficiency and sustainability, innovations in this field continue to shape the future of energy systems. Let’s explore how efficiency improvements, material innovations, and future trends are driving progress.
Efficiency Improvements
Efficiency remains a top priority in membrane electrode assembly development. You’ll notice that researchers and manufacturers focus on optimizing every layer of the assembly to enhance performance. For instance, reducing the thickness of the proton exchange membrane improves proton conductivity, which directly boosts current density. A numerical study revealed that thinner membranes significantly enhance fuel cell efficiency by minimizing resistance during electrochemical reactions.
Another approach involves refining catalyst layers. Advanced designs now incorporate ionomers that improve proton transfer within the catalyst, ensuring faster and more efficient reactions. This not only increases energy output but also reduces energy losses. Companies like Gore and Johnson Matthey have introduced high-performance MEAs that demonstrate remarkable efficiency under demanding conditions. These advancements make MEAs more reliable for applications like transportation and renewable energy storage.
Scientific Research Findings: Studies show that optimizing membrane thickness and catalyst porosity can lead to substantial gains in energy conversion efficiency. These improvements enable MEAs to sustain high current densities, even in challenging environments.
Material Innovations
Material innovations play a crucial role in enhancing the durability and functionality of membrane electrode assemblies. You’ll find that modern MEAs integrate advanced materials into their components to address challenges like degradation and cost. For example, platinum-based catalysts, combined with novel carbon supports, improve reaction rates while reducing material usage. This approach not only lowers costs but also extends the lifespan of the assembly.
Proton exchange membranes have also seen significant advancements. Manufacturers now use reinforced polymers to create membranes that withstand higher temperatures and pressures. These durable membranes maintain performance over extended periods, making them ideal for heavy-duty applications. Additionally, gas diffusion layers are being engineered with hydrophobic properties to manage water more effectively, ensuring consistent operation.
Key Insight: Material innovations, such as enhanced membranes and optimized catalysts, are transforming MEAs into more robust and cost-effective solutions. These advancements support their adoption in diverse industries, from automotive to industrial hydrogen production.
Future Trends
The future of membrane electrode assembly technology looks promising, with ongoing research paving the way for groundbreaking developments. One emerging trend involves the integration of scalable architectures. These designs aim to improve the efficiency of electrochemical synthesis processes, making MEAs more adaptable to large-scale applications.
You’ll also see a growing emphasis on sustainability. Researchers are exploring alternative materials, such as non-noble metal catalysts, to reduce reliance on expensive resources like platinum. This shift not only lowers production costs but also aligns with global efforts to minimize environmental impact. Furthermore, advancements in manufacturing techniques, such as 3D printing, are enabling precise and cost-efficient production of MEAs.
Real-World Impact: Emerging technologies, such as electrocatalytic CO2 reduction, highlight the potential of MEAs to address environmental challenges. By converting carbon dioxide into valuable products, these innovations contribute to carbon neutrality and sustainable development.
As you look ahead, it’s clear that membrane electrode assemblies will continue to play a central role in clean energy technologies. Efficiency improvements, material innovations, and future trends are driving their evolution, ensuring they remain at the forefront of sustainable energy solutions.
Membrane electrode assemblies stand at the forefront of clean energy technologies, driving advancements in fuel cells, electrolyzers, and emerging innovations. You’ve seen how their design and functionality enable efficient energy conversion, making them indispensable in sustainable energy systems. Continuous research and innovation remain vital for improving MEA performance and accessibility. Companies like Ningbo VET Energy Technology Co., Ltd. play a crucial role in this progress. By specializing in high-efficiency PEM hydrogen fuel cell stacks and renewable energy solutions, they contribute significantly to the global shift toward cleaner energy.
FAQ
What is the importance of MEA in fuel cells and electrolyzers?
The membrane electrode assembly (MEA) serves as the core of fuel cells and electrolyzers. It is the site where electrochemical reactions take place, enabling energy conversion. Without a well-designed MEA, the efficiency and performance of these devices would significantly decline. You’ll find that defects during the manufacturing process can lead to stack degradation, which impacts durability. Additionally, the high cost of MEAs remains a challenge for widespread adoption.
What are the critical components of an MEA and their roles?
An MEA consists of several essential components, each with a specific function:
- Membranes: These act as the medium for ion conduction. Materials like PFSA (perfluorosulfonic acid) are commonly used for their high proton conductivity.
- Electrodes: These facilitate the transfer of electrons and ensure efficient reactions at the catalyst layers.
- Catalysts: Typically made of platinum or other noble metals, catalysts accelerate the chemical reactions.
- Gas Diffusion Layers (GDLs): These distribute reactant gases evenly and manage water produced during reactions.
Each component works together to ensure the MEA operates efficiently and reliably.
How does the MEA contribute to power production in fuel cells?
The MEA is the heart of power generation in fuel cells. At the anode, hydrogen molecules split into protons and electrons. The protons pass through the membrane, while the electrons travel through an external circuit, generating electricity. At the cathode, oxygen combines with protons and electrons to form water. This entire process occurs within the MEA, making it indispensable for power production. However, hardware components like bipolar plates and gaskets are also necessary to support MEA operation.
What advancements in MEA technology are driving market growth?
Recent advancements in MEA technology focus on improving durability, performance, and cost-effectiveness. Researchers are developing novel materials and designs to enhance the lifespan of MEAs. For example, thinner membranes improve proton conductivity, while optimized catalyst layers increase reaction efficiency. These innovations make fuel cells more reliable and competitive with traditional combustion engines. As a result, MEAs are becoming more viable for applications like transportation and renewable energy storage.
Key Insight: By reducing costs and increasing reliability, advancements in MEA technology are accelerating the adoption of clean energy solutions.
What challenges exist in optimizing MEA parameters?
Optimizing MEA parameters, such as membrane thickness and catalyst particle size, poses significant challenges. Once a fuel cell is operational, you cannot easily modify these parameters. This limitation makes experimental studies time-consuming and costly. For instance, adjusting the protonic conductivity coefficient of the membrane requires precise material engineering during the manufacturing phase. Overcoming these challenges is essential for improving MEA performance and efficiency.
Why is material innovation important for MEAs?
Material innovation plays a crucial role in addressing challenges like durability and cost. Advanced membranes made from reinforced polymers can withstand higher temperatures and pressures, making them suitable for demanding applications. Similarly, catalysts with novel carbon supports reduce material usage while maintaining high reaction rates. These innovations not only enhance performance but also lower production costs, making MEAs more accessible for various industries.
Did You Know? Platinum-based catalysts combined with optimized carbon supports have significantly improved the efficiency and lifespan of MEAs.
How do MEAs support hydrogen production in electrolyzers?
In electrolyzers, MEAs enable the splitting of water into hydrogen and oxygen through electrolysis. The membrane facilitates ion transfer, while the electrodes and catalysts ensure efficient reactions. This process produces green hydrogen, a clean energy carrier with vast potential for decarbonizing industries. MEAs in electrolyzers must be durable and efficient to handle high current densities over extended periods. Innovations in MEA design have made hydrogen production more scalable and cost-effective.
What role do MEAs play in emerging technologies?
MEAs are driving innovation in emerging technologies like electrocatalytic CO2 reduction. In this process, MEAs facilitate the conversion of carbon dioxide into valuable chemicals and fuels. This application holds promise for reducing greenhouse gas emissions while creating useful byproducts. Additionally, researchers are exploring MEAs for next-generation energy systems, such as hybrid devices and solid oxide fuel cells. These advancements highlight the versatility of MEAs in addressing energy and environmental challenges.
How do MEAs impact the cost of fuel cells?
The cost of MEAs significantly influences the overall expense of fuel cells. High-performance materials like platinum catalysts and advanced membranes contribute to the cost. However, recent advancements aim to reduce these expenses. For example, researchers are developing non-noble metal catalysts and scalable manufacturing techniques. These efforts make fuel cells more affordable and competitive with traditional energy systems.
What is the future of MEA technology?
The future of MEA technology looks promising, with ongoing research focusing on sustainability and scalability. Alternative materials, such as non-noble metal catalysts, are being developed to reduce reliance on expensive resources. Manufacturing innovations, like 3D printing, enable precise and cost-efficient production. Additionally, scalable architectures are improving the adaptability of MEAs for large-scale applications. These trends ensure that MEAs remain at the forefront of clean energy solutions.
Real-World Impact: Emerging technologies powered by MEAs, such as CO2 reduction systems, demonstrate their potential to reshape the energy landscape and contribute to a sustainable future.