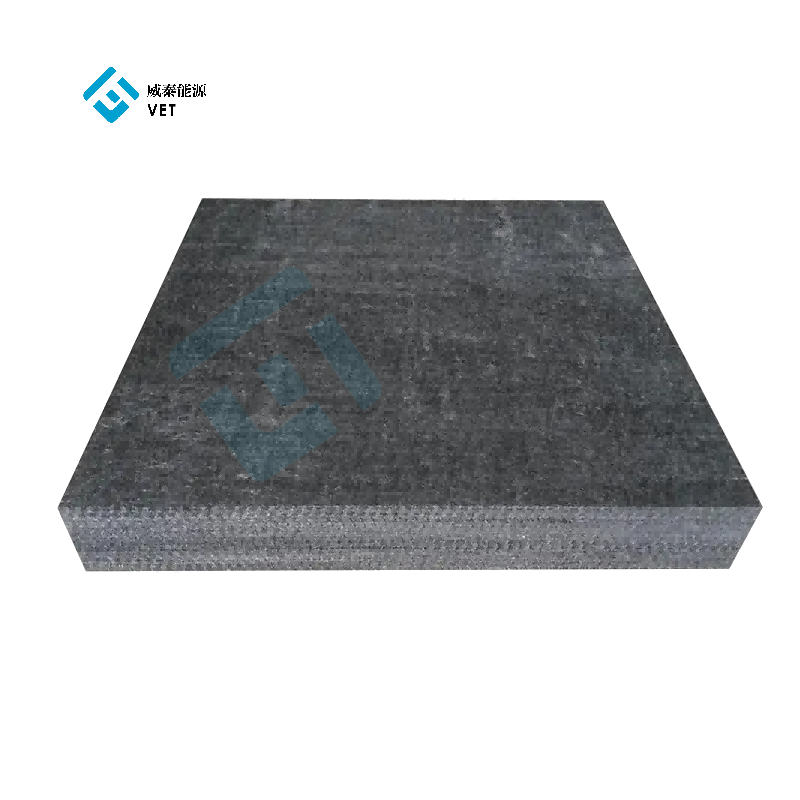
Rigid graphite felt stands out as a high-performance material, offering exceptional thermal insulation and durability. Its lightweight structure makes it indispensable in industries requiring efficient heat management, such as aerospace, chemical processing, and energy. Unlike soft graphite felt, which provides flexibility, rigid graphite felt excels in maintaining structural integrity under extreme conditions. The global market reflects its growing demand, with projections estimating a rise from 580millionin2022to580 million in 2022 to 580millionin2022to1.15 billion by 2030. This surge highlights its critical role in advanced industrial applications, where reliability and thermal stability are paramount.
Key Takeaways
- Rigid graphite felt offers exceptional thermal insulation, making it ideal for high-temperature applications in industries like aerospace and metallurgy.
- Its lightweight properties facilitate easy handling and installation, reducing overall system weight, which is crucial in sectors such as aerospace.
- The material’s chemical resistance ensures durability in harsh environments, minimizing maintenance costs in industries like chemical processing.
- Despite its advantages, rigid graphite felt comes with a high cost, which may limit its use in budget-sensitive applications.
- Careful handling is essential due to its brittleness; improper treatment can lead to cracking and performance issues.
- While rigid graphite felt excels in thermal insulation, it may require additional support in applications with high mechanical loads due to its limited mechanical strength.
- Understanding the specific requirements of your application is key to leveraging the benefits of rigid graphite felt while addressing its limitations.
Advantages of Rigid Graphite Felt
Exceptional Thermal Insulation
High-temperature resistance and low thermal conductivity make it ideal for furnaces, kilns, and high-heat environments.
Rigid graphite felt excels in thermal insulation due to its ability to withstand extreme temperatures while minimizing heat transfer. This material demonstrates low thermal conductivity, which ensures efficient energy conservation in industrial processes. Industries such as aerospace and metallurgy rely on this property to maintain stable operating conditions in high-temperature environments like furnaces and kilns.
According to the Global Graphite Rigid Felt Board Market Report (2023), the material’s high-temperature stability makes it indispensable for applications requiring precise thermal management.
For example, in the semiconductor industry, rigid graphite felt is used to insulate high-temperature reactors, ensuring consistent performance and reducing energy consumption. Its thermal shock resistance further enhances its reliability, even under rapid temperature fluctuations.
Chemical Resistance
Resistant to most acids, alkalis, and corrosive substances, making it suitable for chemically aggressive environments.
Rigid graphite felt offers exceptional chemical resistance, making it a preferred choice for industries dealing with corrosive substances. Its inert nature allows it to withstand exposure to acids, alkalis, and other aggressive chemicals without degrading. This property is particularly valuable in chemical processing plants, where materials are often subjected to harsh environments.
As highlighted in the Features and Applications of Rigid Graphite Felt study, this material’s resistance to chemical erosion ensures long-term durability and reduces maintenance costs in demanding applications.
For instance, in the energy sector, rigid graphite felt is used in fuel cells and battery systems, where it resists chemical reactions while maintaining structural integrity. This resilience ensures consistent performance over extended periods, even in challenging conditions.
Lightweight Properties
Low density allows for easy handling and installation, reducing overall system weight in industrial setups.
The lightweight nature of rigid graphite felt simplifies its handling and installation, making it a practical solution for various industrial applications. Its low density reduces the overall weight of systems, which is particularly beneficial in industries like aerospace, where minimizing weight is critical for efficiency.
The Carbon and Graphite Felt Market Analysis emphasizes the growing demand for lightweight materials in high-temperature insulation, driven by their ease of use and cost-effectiveness.
For example, in photovoltaic manufacturing, rigid graphite felt is used as an insulating layer in high-temperature furnaces. Its lightweight properties not only facilitate installation but also contribute to improved energy efficiency by reducing the thermal mass of the system.
Durability and Longevity
Maintains performance under extreme conditions, offering a long service life and reducing the need for frequent replacements.
Rigid graphite felt demonstrates remarkable durability, making it a reliable choice for industries that demand consistent performance under harsh conditions. Its ability to maintain structural integrity and thermal properties over extended periods reduces the frequency of replacements, which translates to lower maintenance costs and improved operational efficiency.
According to the Graphite Rigid Felts Market Potential Analysis, this material outperforms traditional insulation options in both thermal and mechanical stability, ensuring long-term reliability in high-temperature applications.
Industries such as aerospace and metallurgy benefit significantly from this longevity. For instance, in aerospace, rigid graphite felt is used in thermal protection systems for spacecraft, where it withstands extreme heat during re-entry without degradation. Similarly, in metallurgical processes, it endures prolonged exposure to molten metals and high-temperature environments, maintaining its insulating properties.
The material’s resistance to thermal shock and airflow erosion further enhances its lifespan. Unlike conventional insulation materials that may deteriorate under rapid temperature changes or abrasive conditions, rigid graphite felt retains its performance. This resilience makes it indispensable in applications like vacuum furnaces, where consistent insulation is critical for product quality.
The Global Rigid Graphite Felt Market Analysis highlights the growing adoption of this material in energy storage technologies, where its durability ensures stable performance over multiple cycles. For example, in advanced battery systems, rigid graphite felt serves as a key component, maintaining efficiency and reliability throughout the system’s lifecycle.
By choosing rigid graphite felt, industries can achieve a balance between performance and cost-effectiveness. Its extended service life not only minimizes downtime but also supports sustainable practices by reducing material waste and energy consumption.
Disadvantages of Rigid Graphite Felt
High Cost
The manufacturing process and raw materials make it more expensive than alternatives like ceramic fiber or mineral wool.
Rigid graphite felt stands out for its exceptional properties, but its high cost remains a significant drawback. The production process involves advanced techniques and premium-grade raw materials, which contribute to its elevated price point. Compared to alternatives like ceramic fiber or mineral wool, rigid graphite felt demands a higher investment.
According to market analysis, the Global Rigid Graphite Felt Market is projected to reach USD 1.15 billion by 2030, driven by its increasing demand in high-temperature industrial applications. However, this growth reflects the material’s premium pricing, which may limit its accessibility for cost-sensitive industries.
Industries such as aerospace and semiconductors often justify the expense due to the material’s unparalleled performance in extreme conditions. For instance, in high-temperature furnace linings used in metallurgy, rigid graphite felt enhances productivity and minimizes heat leakage. While the upfront cost is high, its durability and efficiency can offset long-term operational expenses.
Brittleness
Susceptible to cracking or breaking under mechanical stress, requiring careful handling during installation and use.
Despite its many advantages, rigid graphite felt exhibits brittleness, making it prone to cracking or breaking under mechanical stress. This characteristic necessitates meticulous handling during transportation, installation, and maintenance. Improper handling can compromise its structural integrity, leading to potential performance issues.
In industries like chemical processing and high-temperature furnaces, where rigid graphite felt is widely used, specialized tools and techniques are often required to mitigate the risks associated with its brittleness.
For example, in the solar energy sector, rigid graphite felt plays a critical role in high-temperature insulation. However, its susceptibility to mechanical damage requires operators to implement strict handling protocols. This limitation can increase labor costs and extend project timelines, particularly in large-scale industrial setups.
Limited Mechanical Strength
Not suitable for applications requiring high structural integrity, often necessitating additional support or reinforcement.
Rigid graphite felt lacks the mechanical strength needed for applications demanding high structural integrity. While it excels in thermal insulation and chemical resistance, its limited load-bearing capacity restricts its use in environments with significant mechanical loads or vibrations.
In the metallurgical industry, rigid graphite felt is extensively used in furnace linings. However, additional support structures are often required to maintain its position and effectiveness under operational conditions.
For instance, in aerospace applications, rigid graphite felt provides excellent thermal protection but must be reinforced with other materials to withstand mechanical stresses during flight. Similarly, in advanced battery systems, it serves as a key insulating component but relies on external frameworks to ensure stability.
This limitation underscores the importance of evaluating application requirements before selecting rigid graphite felt. While it offers unmatched performance in specific scenarios, its mechanical constraints may necessitate alternative solutions or supplementary materials in certain industrial contexts.
Application Constraints
Performance may vary depending on specific industrial conditions, and it is not ideal for environments with high mechanical loads or vibrations.
Rigid graphite felt demonstrates exceptional performance in high-temperature and chemically aggressive environments. However, its application remains constrained by certain industrial conditions. The material’s effectiveness can vary based on the specific demands of the operating environment, particularly when subjected to mechanical stress or dynamic forces.
Industries requiring insulation in environments with significant mechanical loads or vibrations often face challenges when using rigid graphite felt. Its limited mechanical strength makes it unsuitable for applications where structural integrity is critical. For instance, in metallurgical furnace linings, rigid graphite felt provides excellent thermal insulation but requires additional support structures to maintain its position under operational stress. Without reinforcement, the material may fail to deliver consistent performance.
The Global Rigid Graphite Felt Market Report highlights that while the material excels in thermal stability, its brittleness and low load-bearing capacity restrict its use in high-vibration settings, such as heavy machinery or transport systems.
In high-end markets like solar energy and semiconductors, rigid graphite felt plays a vital role due to its thermal shock resistance and ablative properties. However, these industries often implement strict handling protocols and design modifications to mitigate the material’s mechanical limitations. For example, in solar panel manufacturing, rigid graphite felt serves as an insulating layer in high-temperature furnaces. To ensure stability, manufacturers incorporate external frameworks or protective casings.
Despite these constraints, rigid graphite felt remains indispensable in applications prioritizing thermal insulation over mechanical durability. Its use in chemical processing plants and aerospace systems underscores its value in environments where heat management and chemical resistance outweigh structural demands. In such cases, engineers often design systems that account for the material’s limitations, ensuring optimal performance without compromising safety or efficiency.
According to market projections, the global demand for rigid graphite felt will reach USD 1.15 billion by 2030, driven by its unmatched properties in high-temperature industrial applications. However, industries must carefully evaluate its suitability for specific conditions to maximize its benefits.
By understanding these constraints, industries can make informed decisions about integrating rigid graphite felt into their systems. Proper planning, combined with supplementary materials or reinforcements, allows businesses to leverage its advantages while addressing its limitations effectively.
Comparison with Alternatives
Rigid Graphite Felt vs. Ceramic Fiber
Compare thermal insulation properties, cost, and durability, highlighting scenarios where one material is more advantageous.
Rigid graphite felt and ceramic fiber are both widely used for thermal insulation, but their properties cater to different industrial needs. Rigid graphite felt offers superior thermal insulation due to its low thermal conductivity and high-temperature resistance. It performs exceptionally well in environments exceeding 2000°F, such as vacuum furnaces and aerospace applications. Ceramic fiber, on the other hand, provides adequate insulation for moderate-temperature applications, typically up to 2300°F, making it a cost-effective choice for industries like power generation and petrochemicals.
According to the Global Thermal Insulation Materials Report, rigid graphite felt demonstrates better thermal shock resistance and ablative properties compared to ceramic fiber. This makes it ideal for applications requiring consistent performance under extreme conditions.
In terms of cost, ceramic fiber is significantly more affordable. Its lower price point makes it accessible for industries with budget constraints. However, rigid graphite felt justifies its higher cost with unmatched durability and longevity. For instance, in high-temperature furnaces, rigid graphite felt maintains its insulating properties over extended periods, reducing the need for frequent replacements. Ceramic fiber, while cheaper initially, may require more frequent maintenance due to wear and tear.
Industries must evaluate their specific requirements when choosing between these materials. For high-end applications demanding exceptional thermal stability, rigid graphite felt remains the preferred option. Conversely, ceramic fiber suits scenarios where cost-efficiency outweighs the need for extreme heat resistance.
Rigid Graphite Felt vs. Mineral Wool
Discuss differences in chemical resistance, weight, and application suitability, with examples of industries where each material is commonly used.
Rigid graphite felt and mineral wool differ significantly in chemical resistance and weight. Rigid graphite felt exhibits excellent resistance to acids, alkalis, and corrosive substances, making it suitable for chemically aggressive environments like chemical processing plants and energy storage systems. Mineral wool, while offering decent thermal insulation, lacks the same level of chemical resilience. It performs best in dry, non-corrosive environments, such as building insulation and HVAC systems.
The Carbon and Graphite Felt Market Analysis highlights that rigid graphite felt’s lightweight properties simplify handling and installation, especially in industries like aerospace and photovoltaics. Mineral wool, being denser, adds more weight to systems, which can be a disadvantage in applications requiring mobility or weight reduction.
For example, in the photovoltaic industry, rigid graphite felt serves as an insulating layer in high-temperature furnaces, where its lightweight nature enhances energy efficiency. Mineral wool, on the other hand, is commonly used in construction for fireproofing and soundproofing due to its affordability and ease of installation in static environments.
While mineral wool offers a cost-effective solution for general insulation needs, rigid graphite felt excels in specialized applications requiring chemical resistance and lightweight properties. Industries must consider these factors to select the most appropriate material for their operations.
Rigid Graphite Felt vs. Carbon Fiber Composites
Evaluate mechanical strength, brittleness, and cost, explaining why rigid graphite felt is preferred in high-temperature environments.
Rigid graphite felt and carbon fiber composites share similarities in their high-temperature capabilities, but their mechanical properties and costs set them apart. Rigid graphite felt provides exceptional thermal insulation and stability at extreme temperatures, making it indispensable in applications like vacuum furnaces and aerospace systems. Carbon fiber composites, while also heat-resistant, prioritize mechanical strength over insulation, making them suitable for structural components in automotive and aerospace industries.
The Features and Applications of Rigid Graphite Felt study emphasizes its superior ablative resistance and thermal shock performance, which are critical in high-temperature environments. Carbon fiber composites, though strong, lack the same level of thermal insulation and may degrade under prolonged exposure to extreme heat.
Cost is another differentiating factor. Rigid graphite felt, though expensive, remains more affordable than carbon fiber composites, which involve complex manufacturing processes and premium raw materials. For instance, in the semiconductor industry, rigid graphite felt is used to insulate reactors, ensuring consistent performance without the prohibitive costs associated with carbon fiber composites.
Brittleness is a limitation of rigid graphite felt, but its thermal advantages outweigh this drawback in high-temperature applications. Carbon fiber composites, with their superior mechanical strength, are better suited for load-bearing applications. However, for industries prioritizing thermal insulation over structural integrity, rigid graphite felt remains the material of choice.
Rigid graphite felt delivers unparalleled performance in high-temperature and chemically aggressive environments. Its exceptional thermal insulation, chemical resistance, lightweight design, and durability make it a cornerstone material in industries like solar energy, semiconductors, and metallurgy. From furnace linings to advanced battery systems, its ability to maintain stability under extreme conditions ensures reliable and efficient operations.
Ningbo VET Energy Technology Co. stands as a trusted provider of high-quality rigid graphite felt, offering solutions tailored to meet the demands of cutting-edge industrial applications. Their expertise guarantees consistent performance and long-term value for businesses seeking advanced material solutions.
FAQ
What is rigid graphite felt, and how is it used in industrial applications?
Rigid graphite felt is a high-performance insulation material made from carbonized fibers. It offers exceptional thermal insulation, chemical resistance, and durability. Industries use it in high-temperature environments such as vacuum furnaces, kilns, and reactors. Its lightweight properties make it ideal for applications requiring reduced system weight, such as aerospace and photovoltaic manufacturing.
According to the Global Graphite Rigid Felt Board Market Report (2023), its thermal stability and chemical resistance make it indispensable in sectors like semiconductors, metallurgy, and energy storage.
How does rigid graphite felt compare to soft graphite felt?
Rigid graphite felt provides superior structural integrity and thermal insulation compared to its soft counterpart. While soft graphite felt offers flexibility and is easier to shape, rigid graphite felt excels in maintaining its form under extreme conditions. This makes it more suitable for applications requiring stable insulation, such as high-temperature furnace linings.
The Carbon and Graphite Felt Market Analysis highlights that rigid graphite felt’s higher density and strength make it a preferred choice for demanding industrial environments.
Why is rigid graphite felt considered expensive?
The production of rigid graphite felt involves advanced manufacturing techniques and high-quality raw materials, which contribute to its cost. Its unique properties, such as high-temperature resistance and chemical stability, justify the premium pricing. Industries often view it as a long-term investment due to its durability and reduced maintenance needs.
Market projections estimate the global demand for rigid graphite felt to reach USD 1.15 billion by 2030, reflecting its value in high-performance applications.
Can rigid graphite felt withstand chemical exposure?
Yes, rigid graphite felt exhibits excellent resistance to acids, alkalis, and corrosive substances. This property makes it suitable for chemically aggressive environments, such as chemical processing plants and energy storage systems. Its inert nature ensures long-term performance without degradation.
A study on Features and Applications of Rigid Graphite Felt confirms its ability to resist chemical erosion, reducing maintenance costs in harsh industrial settings.
What industries benefit the most from rigid graphite felt?
Industries that operate in high-temperature or chemically aggressive environments benefit significantly from rigid graphite felt. These include:
- Aerospace: Used in thermal protection systems for spacecraft.
- Semiconductors: Insulates reactors in high-temperature processes.
- Metallurgy: Serves as furnace linings for molten metal handling.
- Energy Storage: Plays a role in fuel cells and advanced battery systems.
Its versatility makes it a critical material across various advanced industrial sectors.
How does rigid graphite felt perform under extreme temperatures?
Rigid graphite felt excels in high-temperature environments, withstanding temperatures exceeding 2000°F. Its low thermal conductivity minimizes heat transfer, ensuring efficient insulation. This makes it ideal for applications like vacuum furnaces, kilns, and high-heat reactors.
The Global Thermal Insulation Materials Report emphasizes its unmatched thermal shock resistance, which ensures reliability even under rapid temperature changes.
Is rigid graphite felt environmentally friendly?
Rigid graphite felt supports sustainable practices by reducing energy consumption in industrial processes. Its durability minimizes material waste, as it requires fewer replacements compared to traditional insulation materials. Additionally, its lightweight properties contribute to energy efficiency in applications like aerospace and photovoltaics.
The Graphite Rigid Felts Market Potential Analysis highlights its role in promoting energy-efficient technologies, particularly in renewable energy sectors.
What are the handling requirements for rigid graphite felt?
Due to its brittleness, rigid graphite felt requires careful handling during transportation, installation, and maintenance. Specialized tools and techniques may be necessary to prevent cracking or breaking. Industries often implement strict protocols to ensure its structural integrity remains intact.
In high-temperature furnace setups, operators use protective measures to mitigate risks associated with its brittleness, ensuring consistent performance.
How does rigid graphite felt compare to ceramic fiber?
Rigid graphite felt offers superior thermal insulation and durability compared to ceramic fiber. It performs better in extreme temperatures and chemically aggressive environments. Ceramic fiber, while more affordable, is suitable for moderate-temperature applications and lacks the same level of chemical resistance.
The Global Thermal Insulation Materials Report notes that rigid graphite felt’s thermal shock resistance makes it ideal for high-end applications, whereas ceramic fiber suits cost-sensitive industries.
Where can businesses source high-quality rigid graphite felt?
Ningbo VET Energy Technology Co. provides premium rigid graphite felt tailored to meet the demands of advanced industrial applications. With expertise in graphite materials and a commitment to quality, the company ensures reliable performance and long-term value for its clients.
Certified under ISO 9001:2015, Ningbo VET Energy Technology Co. has earned recognition for its innovative solutions and customer-centric approach in industries like photovoltaics, semiconductors, and new energy.