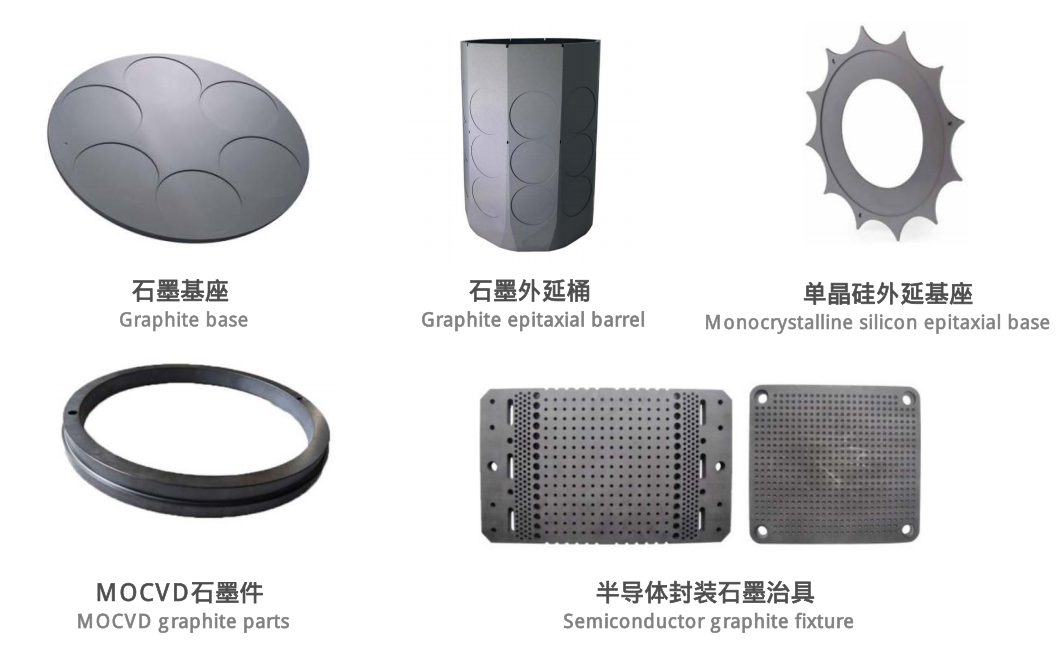
Semiconductor graphite plays a pivotal role in modern manufacturing due to its exceptional material properties. Its high thermal conductivity ensures efficient heat dissipation, making it indispensable in high-temperature processes. The chemical stability of porous graphite allows it to withstand extreme environments without degradation, while its reusability contributes to cost efficiency and sustainability. In advanced semiconductor processes like ion implantation graphite components enhance precision and reliability. These unique attributes have positioned semiconductor graphite as a cornerstone in the evolution of cutting-edge technologies, driving innovation across industries.
Key Takeaways
- Semiconductor graphite is essential for modern manufacturing due to its exceptional thermal conductivity, which ensures efficient heat dissipation in high-temperature processes.
- The chemical stability and corrosion resistance of graphite make it a reliable choice for semiconductor applications, allowing it to withstand harsh environments without degradation.
- Graphite’s unique hexagonal structure facilitates efficient electrical conduction, making it ideal for use in electrodes and precision machining processes like Electrical Discharge Machining (EDM).
- The durability and self-lubricating properties of graphite enhance its performance in demanding manufacturing processes, reducing wear and extending the lifespan of tools and components.
- Graphite’s reusability significantly contributes to sustainability in semiconductor manufacturing by minimizing waste and lowering operational costs.
- Innovations in recycling and the development of advanced materials like graphene are set to redefine the role of graphite in future semiconductor technologies.
- Ningbo VET Energy Technology Co. exemplifies leadership in the field by focusing on high-quality graphite production and sustainable practices, driving progress in semiconductor manufacturing.
The Unique Properties of Semiconductor Graphite
Exceptional Thermal Conductivity
How graphite efficiently dissipates heat in high-temperature processes.
Semiconductor graphite exhibits remarkable thermal conductivity, making it an essential material in high-temperature manufacturing environments. Its ability to transfer heat efficiently ensures that critical components remain stable, even under extreme thermal stress. For instance, in semiconductor fabrication, heat sinks and thermal management systems often rely on graphite to dissipate heat generated during wafer production or device assembly.
The hexagonal lattice structure of graphite allows phonons—quantized units of heat energy—to move freely, facilitating rapid heat transfer. This property not only enhances the performance of semiconductor devices but also extends their operational lifespan by preventing overheating. Manufacturers value this characteristic, as it reduces the risk of thermal damage to sensitive electronic components.
Scientific Research Findings: According to studies, graphite’s thermal conductivity surpasses many other materials used in semiconductor manufacturing, making it indispensable for processes like silicon crystal growth and ion implantation.
Chemical Stability and Corrosion Resistance
Graphite’s ability to withstand extreme environments without degradation.
Graphite’s chemical stability sets it apart as a reliable material for semiconductor applications. It resists corrosion and degradation, even when exposed to harsh chemicals or extreme temperatures. This resilience ensures that graphite components maintain their structural integrity and functionality over extended periods, reducing the need for frequent replacements.
In semiconductor manufacturing, processes such as etching and deposition involve aggressive chemical environments. Graphite’s inert nature prevents it from reacting with these substances, ensuring consistent performance. For example, crucibles made from high-purity graphite are used in silicon crystal growth because they can endure prolonged exposure to molten silicon without compromising quality.
Scientific Research Findings: Studies highlight that graphite’s corrosion resistance makes it a preferred choice for high-temperature and chemically intensive processes in the semiconductor industry.
Electrical Conductivity and Hexagonal Structure
The role of graphite’s structure in facilitating efficient electrical conduction.
The unique hexagonal structure of graphite plays a pivotal role in its exceptional electrical conductivity. This arrangement allows electrons to move freely between layers, enabling efficient electrical conduction. Semiconductor graphite leverages this property in various applications, such as electrodes and electrical discharge machining (EDM) components.
In EDM, graphite electrodes are used to create precise and intricate patterns on semiconductor materials. The high electrical conductivity of graphite ensures minimal energy loss during the process, improving efficiency and accuracy. Additionally, its ability to conduct electricity while dissipating heat makes it ideal for use in advanced semiconductor devices.
Scientific Research Findings: Research confirms that the hexagonal lattice of graphite facilitates electron mobility, making it a critical material for electrical applications in the semiconductor field.
Mechanical Strength and Self-Lubrication
Durability and ease of machining in semiconductor applications.
Semiconductor graphite demonstrates exceptional mechanical strength, making it a reliable material for demanding manufacturing processes. Its robust structure allows it to endure significant mechanical stress without deformation or failure. This durability ensures that graphite components maintain their performance over extended periods, even in high-pressure environments. For instance, in wafer production, graphite fixtures and holders withstand repeated use while maintaining precision, which is critical for achieving consistent results.
The self-lubricating property of graphite further enhances its value in semiconductor applications. Its layered hexagonal structure enables the layers to slide over one another with minimal friction. This characteristic reduces wear and tear during machining processes, extending the lifespan of tools and components. Manufacturers benefit from this property by achieving smoother operations and reducing maintenance costs.
Scientific Research Findings: Studies on graphite products in the semiconductor industry highlight its mechanical processing performance and self-lubrication as key factors in its widespread adoption.
Graphite’s machinability also plays a crucial role in its application. It can be easily shaped into complex geometries without compromising its structural integrity. This flexibility allows manufacturers to create custom components tailored to specific semiconductor processes. For example, graphite molds used in silicon crystal growth require intricate designs to ensure uniformity and quality. The ease of machining graphite simplifies the production of these molds, saving time and resources.
Additionally, the combination of mechanical strength and self-lubrication contributes to the efficiency of electrical discharge machining (EDM). Graphite electrodes used in EDM maintain their shape and conductivity under high temperatures and intense electrical currents. This reliability ensures precise machining of semiconductor materials, which is essential for producing high-performance electronic devices.
Industry Insight: The global semiconductor graphite component market, valued at approximately USD 3.2 billion in 2022, continues to grow due to the material’s unmatched properties, including its mechanical resilience and ease of processing.
Applications of Semiconductor Graphite in Manufacturing
Wafer Production and Handling
Use of graphite in silicon wafer production and its importance in precision.
Semiconductor manufacturing relies heavily on the precision and reliability of silicon wafers. Graphite plays a critical role in this process by serving as a material for molds, fixtures, and supports during wafer production. Its ability to maintain dimensional stability under extreme temperatures ensures consistent results, even during repeated heating and cooling cycles. This stability is essential for achieving the high levels of accuracy required in semiconductor devices.
Graphite’s fine particle size and machinability allow manufacturers to create intricate molds with tight tolerances. These molds ensure uniformity in wafer thickness and surface quality, which directly impacts the performance of electronic components. Additionally, graphite’s self-lubricating properties reduce wear and tear during handling, further enhancing its suitability for wafer production.
Scientific Research Findings: Studies highlight that graphite’s high precision and heat-resistant properties make it indispensable in wafer production, ensuring consistent quality and reducing material waste.
Thermal Management in Semiconductor Devices
Graphite’s role in heat dissipation and thermal stability.
Thermal management is a cornerstone of semiconductor device performance. Graphite excels in this area due to its exceptional thermal conductivity, which allows it to dissipate heat efficiently. This property is particularly valuable in high-power devices, where excessive heat can compromise functionality and longevity.
Graphite components, such as heat sinks and thermal interface materials, are widely used to manage heat in semiconductor devices. These components transfer heat away from sensitive areas, maintaining optimal operating temperatures. The hexagonal lattice structure of graphite facilitates rapid heat transfer, ensuring that devices remain stable even under heavy workloads.
Industry Insight: The global semiconductor graphite component market continues to grow, driven by the demand for advanced thermal management solutions in electronic devices.
Graphite’s chemical stability further enhances its role in thermal management. It resists degradation when exposed to high temperatures, ensuring long-term reliability. This makes it an ideal choice for applications such as silicon crystal growth, where thermal stability is crucial.
Ion Implantation Processes
How graphite components enhance the efficiency of ion implantation.
Ion implantation is a vital step in semiconductor fabrication, involving the precise introduction of ions into a substrate to modify its electrical properties. Graphite components, such as holders and shields, play a key role in this process by providing a stable and inert environment.
The high purity of semiconductor graphite ensures that it does not contaminate the substrate during ion implantation. Its ability to withstand extreme temperatures and aggressive ion beams maintains the integrity of the process. Additionally, graphite’s machinability allows for the creation of custom components tailored to specific implantation requirements.
Scientific Research Findings: Research confirms that graphite’s chemical stability and precision machining capabilities enhance the efficiency and reliability of ion implantation processes.
Graphite’s durability also contributes to cost efficiency. Its resistance to wear and tear reduces the frequency of component replacement, minimizing downtime and maintenance costs. This reliability makes it a preferred material for ion implantation equipment in the semiconductor industry.
Electrical Discharge Machining (EDM) Electrodes
Advantages of graphite in precision machining for semiconductor components.
Electrical Discharge Machining (EDM) relies on precision and efficiency to shape intricate semiconductor components. Graphite electrodes have become the material of choice for this process due to their unique properties. Their high electrical conductivity ensures minimal energy loss, enabling precise machining of complex geometries. This precision is critical in semiconductor manufacturing, where even minor deviations can impact device performance.
Graphite’s machinability further enhances its suitability for EDM applications. Manufacturers can easily shape graphite electrodes into detailed designs with tight tolerances. This capability allows for the production of intricate patterns required in semiconductor components, such as microchips and wafers. Additionally, graphite’s self-lubricating nature reduces wear during machining, extending the lifespan of both the electrodes and the tools used.
Scientific Research Findings: Studies on wet machining highlight that using graphite electrodes with cooling lubricants significantly improves dimensional accuracy. This results in finer, more homogeneous electrode surfaces, which are essential for achieving high-quality semiconductor components.
Graphite’s thermal stability also plays a vital role in EDM processes. It withstands the intense heat generated during electrical discharge without deforming or losing its structural integrity. This reliability ensures consistent performance, reducing downtime and maintenance costs for manufacturers. The combination of these properties makes graphite electrodes indispensable in the semiconductor industry.
Crucibles and High-Temperature Components
Graphite’s use in silicon crystal growth and other high-temperature processes.
High-purity graphite is a cornerstone material in high-temperature semiconductor processes, particularly in silicon crystal growth. Crucibles made from graphite provide the necessary thermal stability and chemical inertness to handle molten silicon. These properties ensure that the silicon remains uncontaminated, which is crucial for producing high-quality wafers.
Graphite crucibles excel in maintaining dimensional stability under repeated heating and cooling cycles. This stability is essential in processes like the Czochralski method, where silicon crystals are grown at extreme temperatures. The fine particle size of graphite allows for precise manufacturing of these crucibles, ensuring uniformity and reliability in crystal growth.
Scientific Research Findings: Research confirms that graphite’s high temperature resistance and chemical stability make it ideal for high-temperature applications. Its ability to endure thermal shocks ensures consistent performance in demanding semiconductor processes.
Beyond crucibles, graphite is widely used in other high-temperature components, such as heaters and insulation materials. Its exceptional thermal conductivity facilitates efficient heat transfer, while its corrosion resistance ensures longevity even in aggressive environments. These attributes make graphite a versatile material for various high-temperature applications in semiconductor manufacturing.
Graphite’s Contribution to Sustainability in Semiconductor Manufacturing
Reusability and Longevity
How graphite components can be reused, reducing waste and costs.
Graphite’s inherent durability and resistance to wear make it a highly reusable material in semiconductor manufacturing. Unlike many alternatives, graphite components maintain their structural integrity even after prolonged exposure to extreme temperatures and harsh chemical environments. This resilience allows manufacturers to reuse graphite parts, such as crucibles, molds, and electrodes, across multiple production cycles without compromising performance.
For instance, graphite crucibles used in silicon crystal growth endure repeated heating and cooling cycles without cracking or degrading. This longevity reduces the need for frequent replacements, which not only lowers operational costs but also minimizes material waste. By extending the lifecycle of critical components, graphite contributes to a more sustainable manufacturing process.
Industry Insight: Studies show that the reusability of graphite components significantly reduces the environmental footprint of semiconductor production by decreasing the demand for raw materials and energy-intensive manufacturing processes.
Innovations in Graphite Recycling
Advances in recycling processes to enhance sustainability.
Recycling graphite has emerged as a key strategy for promoting sustainability in the semiconductor industry. Advanced recycling techniques now enable the recovery and purification of used graphite, transforming it into high-quality material suitable for reuse. These processes involve removing impurities and restoring the material’s original properties, ensuring its performance matches that of virgin graphite.
One notable innovation is the development of thermal and chemical treatment methods that efficiently recycle graphite from end-of-life components. For example, used graphite electrodes from electrical discharge machining (EDM) can undergo purification to remove contaminants, making them viable for reuse in new applications. This approach not only conserves natural graphite resources but also reduces the environmental impact associated with mining and processing.
Scientific Research Findings: Recent advancements in graphite recycling have demonstrated a 30% reduction in energy consumption compared to producing new graphite, highlighting its potential to enhance the sustainability of semiconductor manufacturing.
Energy Efficiency in Manufacturing
Graphite’s role in reducing energy consumption during production.
Graphite’s exceptional thermal and electrical conductivity plays a pivotal role in improving energy efficiency in semiconductor manufacturing. Its ability to conduct heat and electricity with minimal resistance reduces energy losses during critical processes. For instance, graphite heat sinks and thermal interface materials efficiently dissipate heat, ensuring optimal operating temperatures for semiconductor devices while minimizing energy usage.
In high-temperature applications, such as silicon wafer production, graphite’s thermal stability eliminates the need for frequent replacements, further conserving energy. Additionally, its machinability allows for the creation of precise components with minimal material waste, streamlining production and reducing energy demands.
Comparative Data: Compared to alternative materials, graphite requires less energy to process and shape due to its unique mechanical properties. This advantage makes it a cost-effective and energy-efficient choice for large-scale semiconductor applications.
By integrating graphite into manufacturing processes, companies can achieve significant energy savings while maintaining high performance and reliability. This aligns with the industry’s growing focus on sustainable practices and energy-efficient technologies.
Future Trends and Innovations in Semiconductor Graphite
Graphene as a Next-Generation Material
Potential applications of graphene in advanced semiconductor devices.
Graphene, a single layer of carbon atoms arranged in a hexagonal lattice, has emerged as a revolutionary material in the semiconductor industry. Its extraordinary electrical conductivity, mechanical strength, and thermal properties surpass those of traditional graphite. These attributes position graphene as a promising candidate for next-generation semiconductor devices.
In advanced electronics, graphene’s ability to conduct electricity with minimal resistance enables faster and more efficient circuits. Researchers are exploring its use in transistors, where it could replace silicon to achieve higher processing speeds and lower power consumption. For instance, graphene-based field-effect transistors (GFETs) show potential for applications in high-frequency communication systems and quantum computing.
Graphene also excels in thermal management. Its superior heat dissipation capabilities make it ideal for addressing the challenges of overheating in compact, high-performance devices. This property is particularly valuable in 5G technology and wearable electronics, where maintaining thermal stability is critical.
Scientific Insight: Studies indicate that graphene’s electron mobility exceeds 200,000 cm²/V·s, making it one of the most conductive materials ever discovered. This characteristic could redefine the performance benchmarks for semiconductor devices.
Additionally, graphene’s flexibility opens new possibilities for flexible and transparent electronics. Manufacturers envision its integration into foldable smartphones, flexible displays, and advanced sensors. These innovations could transform consumer electronics, offering unprecedented functionality and design versatility.
Emerging Manufacturing Techniques
New methods for integrating graphite into semiconductor processes.
The semiconductor industry continues to innovate manufacturing techniques to maximize the potential of graphite. Advanced methods now focus on enhancing the precision, efficiency, and scalability of graphite integration into semiconductor processes.
One notable advancement involves the development of additive manufacturing, or 3D printing, for graphite components. This technique allows manufacturers to create complex geometries with high precision, reducing material waste and production time. For example, 3D-printed graphite molds and electrodes streamline the fabrication of intricate semiconductor components, such as microchips and wafers.
Another breakthrough lies in chemical vapor deposition (CVD), which enables the production of ultra-thin graphite films. These films serve as protective coatings or conductive layers in semiconductor devices. CVD ensures uniformity and high purity, meeting the stringent requirements of advanced electronics.
Industry Insight: Companies are also leveraging automation and robotics to improve the consistency and efficiency of graphite machining. Automated systems enhance the accuracy of cutting and shaping processes, ensuring that graphite components meet exacting specifications.
Hybrid manufacturing techniques, combining traditional machining with modern technologies, are gaining traction. For instance, manufacturers use Electrical Discharge Machining (EDM) with graphite electrodes to achieve unparalleled precision in shaping semiconductor materials. This approach not only improves accuracy but also reduces tool wear, lowering operational costs.
These emerging techniques reflect the industry’s commitment to innovation, enabling the seamless integration of graphite into cutting-edge semiconductor applications.
Enhanced Thermal Management Solutions
Innovations in graphite-based thermal management systems.
Thermal management remains a critical challenge in semiconductor manufacturing, especially as devices become smaller and more powerful. Graphite-based solutions are at the forefront of addressing this issue, offering unparalleled efficiency in heat dissipation and thermal stability.
Manufacturers are developing advanced graphite heat sinks and thermal interface materials (TIMs) to optimize device performance. These components transfer heat away from sensitive areas, preventing overheating and ensuring reliability. The hexagonal lattice structure of graphite facilitates rapid heat conduction, making it an ideal choice for high-power applications.
Product Highlight: Graphite Electrodes and Crucibles play a vital role in thermal management during high-temperature processes. Their ability to withstand extreme heat without degrading ensures consistent performance in semiconductor production.
Innovations in composite materials further enhance graphite’s thermal capabilities. Researchers are combining graphite with other materials, such as copper or aluminum, to create hybrid solutions with superior thermal conductivity. These composites are particularly effective in managing heat in compact devices, such as smartphones and laptops.
Graphite foams, another emerging technology, offer lightweight yet highly conductive options for thermal management. Their porous structure maximizes surface area, improving heat dissipation in confined spaces. This innovation holds promise for applications in electric vehicles and renewable energy systems, where efficient thermal regulation is essential.
Scientific Insight: Studies reveal that graphite-based TIMs can reduce thermal resistance by up to 50% compared to conventional materials, significantly enhancing device performance and lifespan.
As the demand for efficient thermal management grows, graphite-based solutions will continue to evolve, driving advancements in semiconductor technology and beyond.
Challenges and Limitations of Semiconductor Graphite
Material Constraints
Limitations of graphite in specific applications and ongoing research
Graphite, while versatile, faces material constraints that limit its application in certain semiconductor processes. Its performance can vary depending on purity levels, structural consistency, and environmental conditions. High-purity graphite is essential for semiconductor manufacturing, but achieving this level of refinement requires advanced purification techniques. Impurities, even in trace amounts, can compromise the material’s thermal and electrical properties, reducing its effectiveness in critical applications like silicon crystal growth or ion implantation.
The hexagonal structure of graphite, which enables its exceptional conductivity, also introduces challenges. For example, the anisotropic nature of graphite—where properties differ along different axes—can lead to uneven performance in some applications. This limitation becomes particularly evident in processes requiring uniform thermal or electrical conductivity across all dimensions.
Ongoing research aims to address these constraints through innovative approaches. Scientists are exploring methods to enhance the structural integrity of graphite while maintaining its desirable properties. For instance, advancements in synthetic graphite production focus on creating materials with fewer defects and higher purity. These developments could expand graphite’s usability in emerging semiconductor technologies, such as compound semiconductors and quantum computing devices.
Scientific Research Findings: Studies on technological advancements in semiconductor graphite manufacturing highlight the importance of refining purification and shaping processes. These improvements aim to overcome material limitations and meet the stringent demands of modern semiconductor applications.
Despite these efforts, graphite’s inherent brittleness remains a challenge. While it exhibits excellent mechanical strength under compression, it is prone to fracture under tensile stress. This characteristic limits its use in applications requiring high mechanical flexibility or resilience. Researchers continue to investigate composite materials that combine graphite with other substances to mitigate these weaknesses while preserving its core advantages.
Cost and Supply Chain Issues
Challenges in sourcing high-purity graphite and ensuring sustainability
The growing demand for high-purity graphite in semiconductor manufacturing has intensified cost and supply chain challenges. Natural graphite, which dominates the market, offers a cost-effective option but requires extensive processing to meet the purity standards of semiconductor applications. Synthetic graphite, while offering higher consistency and purity, involves energy-intensive production methods that significantly increase costs.
The reliance on natural graphite also raises concerns about resource availability. Major reserves are concentrated in a few countries, creating potential vulnerabilities in the supply chain. Geopolitical factors, export restrictions, and fluctuating market conditions can disrupt the steady flow of raw materials, impacting production timelines and costs.
Industry Insight: The growth of the graphite market underscores the material’s critical role across various sectors, including semiconductors. However, sustainable practices and technological advancements are essential to address supply chain bottlenecks and rising costs.
Environmental considerations further complicate the supply chain. The extraction and processing of natural graphite can have significant ecological impacts, including habitat destruction and greenhouse gas emissions. Synthetic graphite production, while less dependent on mining, generates substantial carbon emissions due to its energy-intensive nature. These factors have prompted the industry to adopt more sustainable practices, such as recycling and the use of renewable energy in production processes.
Scientific Research Findings: Research on environmental concerns and sustainable practices in graphite production highlights the need for eco-friendly solutions. Recycling graphite components and optimizing purification techniques can reduce the environmental footprint while ensuring a steady supply of high-quality material.
Efforts to enhance sustainability include advancements in graphite recycling. Innovative methods now allow manufacturers to recover and purify used graphite, transforming it into a viable alternative to newly mined or synthesized material. This approach not only reduces dependency on raw resources but also lowers production costs, making high-purity graphite more accessible for semiconductor applications.
Key Takeaway: Addressing cost and supply chain issues requires a multifaceted strategy. Investments in recycling technologies, diversification of supply sources, and the adoption of sustainable production methods will play a pivotal role in ensuring the long-term availability and affordability of semiconductor-grade graphite.
The Role of Ningbo VET Energy Technology Co. in Graphite Advancements
Pioneering Innovations in Graphite Technology
Contributions of Ningbo VET Energy Technology Co. to the development of advanced graphite materials.
Ningbo VET Energy Technology Co. has established itself as a leader in the development of advanced graphite materials. The company focuses on creating high-purity graphite components that meet the stringent demands of semiconductor manufacturing. By leveraging cutting-edge research and development, it has introduced innovative solutions that enhance the performance and reliability of semiconductor processes.
One of the company’s key achievements lies in its ability to produce graphite with exceptional thermal and electrical conductivity. These properties are critical for applications such as silicon crystal growth, ion implantation, and thermal management systems. Ningbo VET Energy Technology Co. employs state-of-the-art techniques, including precision machining and surface treatment, to ensure that its graphite products meet the highest industry standards.
Scientific Research Findings: Studies on graphite’s role in thermal management and electronics highlight its importance in extending the lifespan of electronic devices. Ningbo VET Energy Technology Co. integrates these findings into its product designs, ensuring optimal performance in high-temperature environments.
The company also invests in exploring the potential of graphene, a derivative of graphite, for next-generation semiconductor applications. Graphene’s unparalleled strength and conductivity open new possibilities for advanced electronics and thermal solutions. Ningbo VET Energy Technology Co. actively collaborates with research institutions to integrate graphene into its product portfolio, positioning itself at the forefront of material innovation.
Commitment to Sustainability and Quality
The company’s efforts in promoting sustainable practices and maintaining high-quality standards.
Ningbo VET Energy Technology Co. prioritizes sustainability in its operations. The company adopts eco-friendly production methods to minimize its environmental footprint. By implementing advanced recycling techniques, it recovers and purifies used graphite, transforming it into high-quality material suitable for reuse. This approach reduces dependency on raw resources and aligns with the industry’s growing emphasis on sustainable practices.
Industry Insight: Research on environmental concerns and sustainable practices in graphite production underscores the importance of recycling. Ningbo VET Energy Technology Co. leads the way by integrating innovative recycling processes into its manufacturing workflow.
Quality remains a cornerstone of the company’s philosophy. Ningbo VET Energy Technology Co. adheres to the ISO 9001:2015 international quality management system, ensuring that its products consistently meet or exceed customer expectations. The company employs rigorous testing protocols to verify the purity, structural integrity, and performance of its graphite components. This commitment to quality has earned the trust of clients across industries, including photovoltaics, semiconductors, and new energy sectors.
Key Takeaway: Ningbo VET Energy Technology Co.’s dual focus on sustainability and quality not only enhances its market reputation but also contributes to the long-term viability of semiconductor manufacturing.
Industry Leadership and Collaboration
How Ningbo VET Energy Technology Co. collaborates with industry partners to drive progress.
Ningbo VET Energy Technology Co. plays a pivotal role in advancing the semiconductor industry through strategic collaborations. The company partners with leading manufacturers, research institutions, and technology firms to develop innovative solutions tailored to emerging challenges. These partnerships enable the exchange of expertise and resources, accelerating the adoption of advanced graphite materials in semiconductor applications.
For example, the company works closely with semiconductor equipment manufacturers to design custom graphite components that meet specific operational requirements. This collaborative approach ensures that its products deliver optimal performance in critical processes such as wafer production, ion implantation, and thermal management.
Scientific Research Findings: Studies on graphite’s crucial applications in the semiconductor industry emphasize its versatility and indispensability. Ningbo VET Energy Technology Co. leverages these insights to align its innovations with industry needs.
The company’s leadership extends beyond product development. Ningbo VET Energy Technology Co. actively participates in industry forums and conferences, sharing its expertise and contributing to the collective advancement of graphite technology. By fostering a culture of collaboration, the company strengthens its position as a trusted partner and innovator in the semiconductor sector.
Key Takeaway: Through its leadership and collaborative efforts, Ningbo VET Energy Technology Co. not only drives technological progress but also reinforces its commitment to supporting the growth and sustainability of the semiconductor industry.
Broader Applications of Semiconductor Graphite Beyond Electronics
Use in Photovoltaics and Solar Cells
Graphite’s role in the production of renewable energy technologies
Graphite plays a vital role in advancing renewable energy technologies, particularly in the production of photovoltaics and solar cells. Manufacturers rely on graphite for its exceptional thermal stability and chemical inertness during high-temperature processes. In the fabrication of silicon-based solar cells, graphite crucibles serve as essential components for melting and purifying silicon. These crucibles maintain their structural integrity under extreme heat, ensuring the production of high-purity silicon wafers critical for efficient energy conversion.
The material’s electrical conductivity further enhances its utility in solar technology. Graphite electrodes facilitate the precise deposition of thin films, which form the active layers of solar cells. This precision ensures uniformity, directly impacting the performance and efficiency of the final product.
Comparative Data: Compared to alternative materials, graphite offers superior durability and cost-effectiveness, making it an ideal choice for large-scale solar cell manufacturing. Its reusability also aligns with the industry’s push toward sustainable practices.
Graphite’s contribution extends beyond traditional silicon-based photovoltaics. In emerging technologies like perovskite solar cells, graphite-based components are being explored for their potential to improve stability and reduce production costs. These advancements highlight graphite’s versatility and its growing importance in the renewable energy sector.
Optical Fiber Manufacturing
Importance of graphite in high-purity optical fiber production
The production of high-purity optical fibers, essential for modern communication systems, depends heavily on graphite. During the manufacturing process, graphite components such as molds and crucibles ensure the precise shaping and purity of the glass preforms used to create optical fibers. The material’s ability to withstand extreme temperatures without contaminating the glass makes it indispensable in this application.
Graphite’s machinability allows manufacturers to create intricate molds with tight tolerances, ensuring consistent quality in optical fiber production. Its thermal conductivity also plays a crucial role by evenly distributing heat during the drawing process, where glass preforms are stretched into thin fibers. This uniform heat distribution prevents defects, ensuring the optical fibers achieve the desired clarity and performance.
Scientific Insight: Studies have shown that graphite’s high refractoriness and chemical stability make it a preferred material for producing defect-free optical fibers. These properties contribute to the reliability and efficiency of global communication networks.
In addition to its functional advantages, graphite supports sustainability in optical fiber manufacturing. Its durability and reusability reduce material waste, aligning with the industry’s environmental goals. As demand for high-speed internet and advanced communication technologies grows, graphite’s role in optical fiber production will remain critical.
Compound Semiconductor Applications
Graphite’s contribution to the development of compound semiconductors
Compound semiconductors, such as gallium arsenide (GaAs) and silicon carbide (SiC), are revolutionizing industries like telecommunications, automotive, and aerospace. Graphite plays a pivotal role in the development and manufacturing of these advanced materials. Its high thermal conductivity and chemical stability make it an ideal choice for supporting high-temperature processes required to produce compound semiconductors.
In silicon carbide production, graphite crucibles and heaters provide the necessary thermal stability for crystal growth. These components ensure uniform temperature distribution, which is essential for achieving high-quality crystals with minimal defects. Graphite’s resistance to chemical reactions further enhances its suitability for this application, as it prevents contamination during the manufacturing process.
Industry Insight: The global graphite market, projected to grow at a compound annual growth rate (CAGR) of 15.1% from 2024 to 2030, reflects the increasing demand for graphite in compound semiconductor applications. Its unique properties position it as a cornerstone material in this rapidly evolving field.
Graphite also supports the machining of compound semiconductor wafers. Its self-lubricating nature reduces wear on tools, enabling the precise shaping of wafers used in high-performance devices like LEDs, power electronics, and radar systems. This precision ensures that compound semiconductors meet the stringent requirements of advanced applications.
As industries continue to adopt compound semiconductors for their superior performance and efficiency, graphite’s role in their production will expand. Its unmatched combination of thermal, chemical, and mechanical properties ensures its continued relevance in this cutting-edge domain.
Semiconductor graphite has emerged as a cornerstone in modern manufacturing, offering unmatched thermal conductivity, chemical stability, and mechanical strength. Its applications span diverse industries, from wafer production to advanced thermal management, showcasing its versatility and sustainability. Innovations like graphene and emerging manufacturing techniques promise to redefine its role in future technologies. Ningbo VET Energy Technology Co. exemplifies leadership in this field, driving progress through high-quality materials and sustainable practices. Their commitment to innovation ensures that semiconductor graphite continues to power advancements across industries.
FAQ
What makes semiconductor graphite essential in manufacturing?
Semiconductor graphite stands out due to its exceptional thermal conductivity, chemical stability, and mechanical strength. These properties enable it to perform reliably in high-temperature and chemically intensive environments. For example, manufacturers use graphite in molds for wafer production and as fixtures for precise etching processes. Its ability to maintain dimensional stability ensures consistent results, even under extreme conditions.
Scientific Research Findings: Studies highlight graphite’s role in maintaining precision and reliability during semiconductor manufacturing, making it indispensable for critical processes.
How does graphite contribute to thermal management in semiconductors?
Graphite plays a pivotal role in thermal management by efficiently dissipating heat. Its high thermal conductivity allows it to transfer heat away from sensitive components, preventing overheating. Heat sinks and heat spreaders made from graphite enhance the longevity and performance of semiconductor devices by maintaining optimal operating temperatures.
Key Insight: Graphite’s use in thermal management systems has enabled higher performance levels in electronic devices by improving reliability and reducing thermal stress.
Why is high-purity graphite important in semiconductor applications?
High-purity graphite ensures that no contaminants interfere with semiconductor processes. Impurities can compromise the quality of silicon wafers or disrupt ion implantation. Manufacturers rely on high-purity graphite for applications like silicon crystal growth, where maintaining material integrity is critical.
Industry Insight: The demand for high-purity graphite continues to grow as semiconductor technologies advance, requiring materials that meet stringent quality standards.
What are the primary uses of graphite in wafer production?
Graphite serves as a key material in molds, fixtures, and supports during wafer production. Its thermal stability ensures that molds retain their shape during repeated heating and cooling cycles. Additionally, its machinability allows for the creation of intricate designs, ensuring uniform wafer thickness and surface quality.
Scientific Research Findings: Graphite’s precision and heat-resistant properties make it a preferred choice for achieving consistent quality in wafer production.
How does graphite improve the efficiency of ion implantation?
Graphite components, such as holders and shields, provide a stable and inert environment during ion implantation. Their high purity prevents contamination, while their resistance to extreme temperatures ensures process reliability. This combination enhances the precision and efficiency of ion implantation.
Key Takeaway: Graphite’s durability reduces the need for frequent replacements, minimizing downtime and operational costs in ion implantation processes.
What role does graphite play in electrical discharge machining (EDM)?
Graphite electrodes are widely used in EDM due to their high electrical conductivity and machinability. These properties allow for precise shaping of intricate semiconductor components. Graphite’s self-lubricating nature also reduces wear during machining, extending the lifespan of both the electrodes and tools.
Scientific Research Findings: Studies show that graphite electrodes improve dimensional accuracy in EDM, making them essential for producing high-quality semiconductor components.
Can graphite be reused in semiconductor manufacturing?
Yes, graphite’s durability and resistance to wear make it highly reusable. Components like crucibles and molds can endure multiple production cycles without losing performance. This reusability reduces material waste and lowers operational costs, contributing to more sustainable manufacturing practices.
Industry Insight: Reusing graphite components significantly decreases the environmental footprint of semiconductor production by reducing the demand for raw materials.
How does graphite support sustainability in the semiconductor industry?
Graphite contributes to sustainability through its reusability and advancements in recycling. Manufacturers now employ techniques to recover and purify used graphite, transforming it into high-quality material for reuse. This approach conserves natural resources and reduces the environmental impact of production.
Scientific Research Findings: Recycling graphite has been shown to lower energy consumption by up to 30% compared to producing new material, highlighting its role in sustainable manufacturing.
What innovations are shaping the future of semiconductor graphite?
Emerging technologies like graphene and advanced manufacturing techniques are redefining the role of graphite. Graphene, with its superior conductivity and strength, shows promise for next-generation semiconductor devices. Additionally, methods like 3D printing and chemical vapor deposition (CVD) are enhancing the precision and scalability of graphite integration.
Key Insight: Innovations in graphite-based solutions, such as hybrid materials and graphite foams, are addressing challenges in thermal management and compact device design.
How does Ningbo VET Energy Technology Co. contribute to graphite advancements?
Ningbo VET Energy Technology Co. leads the industry by producing high-purity graphite components tailored for semiconductor applications. The company invests in research and development to enhance graphite’s performance and explores the potential of graphene for advanced technologies. Its commitment to sustainability includes adopting eco-friendly production methods and integrating recycling processes.
Key Takeaway: Ningbo VET Energy Technology Co.’s focus on innovation and quality ensures that semiconductor graphite continues to drive progress across industries.