Tantalum carbide (TaC) coating significantly enhances the durability and longevity of graphite components. You benefit from its protective layer, which shields against wear and erosion. This improvement is crucial in industrial applications where extending the service life of graphite components can lead to increased efficiency and reduced costs. By choosing TaC coating, you ensure that graphite parts withstand harsh environments, maintaining their integrity and performance over time. This advancement not only boosts reliability but also supports sustainable practices by minimizing the need for frequent replacements.
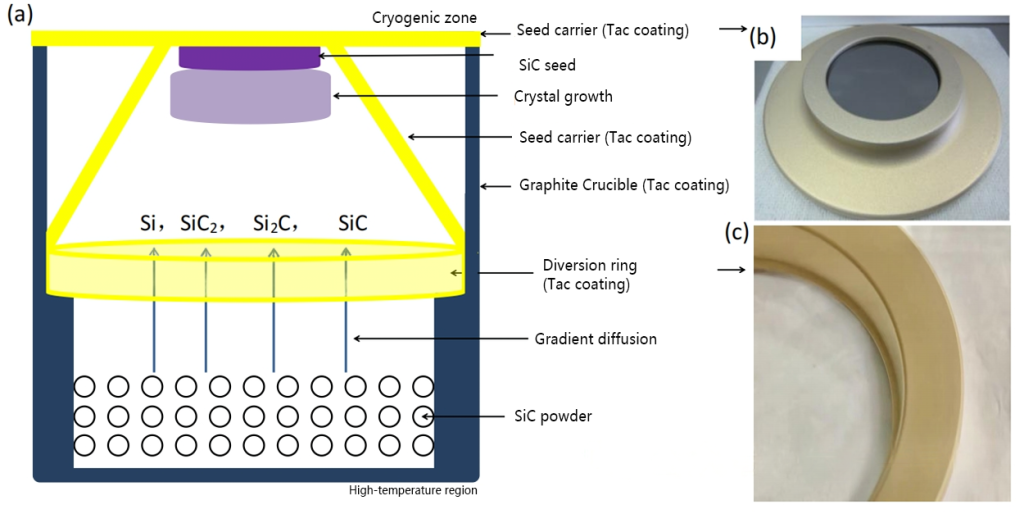
Key Takeaways
-
- TaC coating significantly enhances the durability and longevity of graphite components, making them more reliable in industrial applications.
-
- The coating provides exceptional resistance to wear, corrosion, and extreme temperatures, reducing the need for frequent replacements.
-
- Applying TaC coating leads to long-term cost savings by minimizing maintenance costs and downtime due to component failures.
-
- Proper surface preparation and quality control during the application process are crucial for maximizing the effectiveness of TaC coating.
-
- Industries such as aerospace, semiconductor manufacturing, and chemical processing benefit greatly from the protective properties of TaC coating.
-
- Investing in TaC coating supports sustainable practices by reducing waste and the consumption of raw materials through extended component life.
-
- Future trends in TaC coating technology include advancements in application techniques and emerging uses in renewable energy and medical devices.
Understanding TaC Coating
Composition and Properties of TaC
Tantalum carbide, or TaC, is a compound formed by tantalum and carbon. You find it in a crystalline structure that gives it remarkable hardness and strength. This compound exhibits a high melting point, making it suitable for extreme temperature applications. Its density and thermal conductivity also contribute to its effectiveness as a coating material. When you apply TaC coating to graphite components, you enhance their ability to withstand harsh conditions. The coating acts as a barrier, protecting the underlying material from damage.
Unique Characteristics of TaC Coating
TaC coating offers several unique characteristics that make it valuable in industrial settings. First, its exceptional hardness provides a robust shield against physical wear and erosion. You benefit from this when using graphite components in environments where abrasion is common. Second, the coating’s thermal stability ensures that components maintain their integrity even at high temperatures. This feature is crucial in industries like aerospace, where materials face extreme heat. Lastly, TaC coatingresists chemical reactions, which helps prevent corrosion. By choosing Tac coating, you extend the service life of graphite components, ensuring they perform reliably over time.
Challenges Faced by Uncoated Graphite Components
Wear and Tear in Industrial Environments
In industrial settings, graphite components often face significant wear and tear. You encounter abrasive forces that gradually degrade the material. This wear results from constant friction and contact with other surfaces. Over time, these interactions lead to surface damage and material loss. Without a protective coating, graphite components become vulnerable to scratches and gouges. This damage reduces their effectiveness and shortens their lifespan. You may find that uncoated graphite parts require frequent replacements, increasing maintenance costs and downtime.
Chemical and Thermal Degradation
Graphite components also face chemical and thermal degradation. In many industries, you expose these parts to harsh chemicals and extreme temperatures. Chemical reactions can corrode the graphite, weakening its structure. High temperatures can cause thermal expansion, leading to cracks and fractures. These conditions compromise the integrity of the components. Without protection, graphite parts may fail prematurely. You risk operational inefficiencies and potential safety hazards. Addressing these challenges is crucial for maintaining the reliability and performance of graphite components in demanding environments.
How TaC Coating Addresses Graphite Challenges
Enhanced Resistance to Wear and Corrosion
You face significant challenges when using graphite components in industrial environments. Wear and corrosion can quickly degrade these materials. Tac coating provides a solution by offering enhanced resistance to these issues. The coating forms a hard, protective layer over the graphite. This layer shields the material from abrasive forces. You will notice a reduction in surface damage and material loss. The coating also acts as a barrier against corrosive substances. It prevents chemical reactions that weaken the graphite. By applying TaC coating, you extend the lifespan of your components. This improvement leads to fewer replacements and lower maintenance costs.
Improved Thermal Stability
Graphite components often operate under extreme temperatures. Without protection, they risk thermal degradation. Tac coating enhances the thermal stability of these parts. The coating withstands high temperatures without losing integrity. You benefit from components that maintain their shape and strength. This stability is crucial in industries like aerospace. Here, materials face intense heat and pressure. TaC coating ensures that graphite parts perform reliably. You reduce the risk of cracks and fractures. This reliability supports safe and efficient operations. By choosing Tac coating, you improve the performance of your graphite components in demanding conditions.
Application Process of TaC Coating
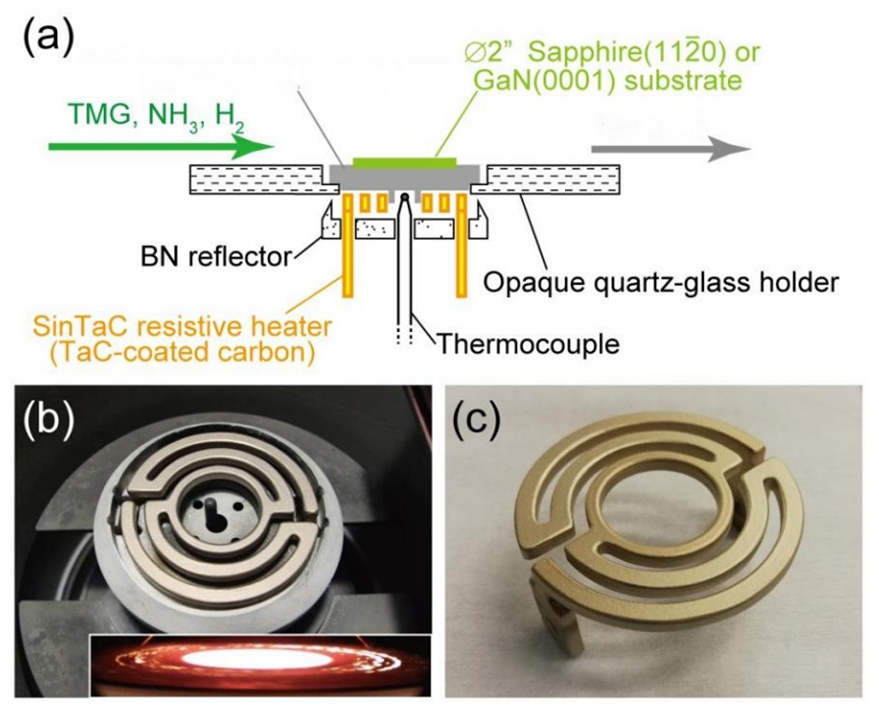
Techniques for Applying TaC Coating
Applying TaC coating to graphite components involves several techniques. Each method offers unique advantages, depending on your specific needs and the application environment. Here are some common techniques:
Chemical Vapor Deposition (CVD): This technique involves the chemical reaction of gaseous precursors to form a solid material on the substrate. You benefit from a uniform and high-quality coating. CVD is ideal for complex shapes and ensures excellent adhesion.
Physical Vapor Deposition (PVD): In this process, you use physical methods to deposit the coating material onto the substrate. PVD provides a thin, durable layer. It is suitable for applications requiring precise control over coating thickness.
Sputtering: This method involves ejecting material from a target and depositing it onto the substrate. Sputtering offers high precision and control. You achieve a dense and adherent coating, which is beneficial for components exposed to harsh conditions.
Thermal Spraying: This technique involves heating the coating material to a molten state and spraying it onto the substrate. Thermal spraying is effective for large surfaces. You gain a thick, protective layer that enhances durability.
Considerations for Effective Coating Application
To ensure the effectiveness of TaC coating, you must consider several factors during the application process:
-
-
Surface Preparation: Proper surface preparation is crucial. You should clean and roughen the graphite surface to enhance adhesion. This step prevents coating defects and ensures a strong bond.
-
-
-
Coating Thickness: The thickness of the TaC coating affects its performance. You need to determine the optimal thickness based on the application requirements. A thicker coating provides better protection but may affect thermal conductivity.
-
-
-
Application Environment: The environment in which you apply the coating can influence its quality. Control factors such as temperature, pressure, and humidity to achieve consistent results.
-
-
-
Quality Control: Implement rigorous quality control measures. You should inspect the coating for uniformity, adhesion, and defects. This step ensures that the coating meets the desired specifications.
-
By understanding these techniques and considerations, you can effectively apply Tac coatingto graphite components. This process enhances their durability and performance, making them suitable for demanding industrial applications.
Real-World Examples and Case Studies
Industry Applications Benefiting from TaC Coating
You find TaC coating in various industries due to its exceptional properties. In the aerospace sector, it enhances the performance of graphite components used in aircraft. These components face extreme conditions, and TaC coating ensures they remain reliable. The semiconductor industry also benefits from this coating. Graphite wafer carriers, essential in manufacturing processes, gain extended service life with TaC coating. This improvement reduces downtime and increases productivity.
In the chemical processing industry, you see TaC-coated graphite parts resisting corrosive substances. This resistance prevents material degradation, ensuring long-term functionality. The coating’s thermal stability makes it ideal for high-temperature applications. Industries like metallurgy and glass manufacturing rely on TaC-coated graphite for consistent performance. By choosing TaC coating, you enhance the durability and efficiency of graphite components across various sectors.
Case Study: Success Stories of TaC Coated Graphite
Consider a case study from the aerospace industry. A company faced frequent failures of graphite components in their aircraft engines. These failures led to costly repairs and operational delays. They decided to apply Tac coating to these components. The results were remarkable. The coated parts showed enhanced resistance to wear and maintained integrity under high temperatures. This improvement reduced maintenance costs and increased engine reliability.
Another success story comes from the semiconductor industry. A manufacturer struggled with the short lifespan of graphite wafer carriers. They implemented TaC coating to address this issue. The coated carriers exhibited superior etch resistance and durability. This change led to fewer replacements and improved production efficiency. The company reported significant cost savings and enhanced product quality.
These examples highlight the transformative impact of Tac coating. By applying this coating, you can achieve similar success in your industry. The benefits include extended component life, reduced maintenance, and improved operational efficiency.
Comparison with Other Coating Materials
TaC vs. Other Carbide Coatings
When you consider coating materials for graphite components, Tantalum carbide (TaC) stands out among other carbide coatings. Each carbide coating offers unique properties, but TaC provides distinct advantages.
Hardness and Durability: TaC exhibits exceptional hardness, surpassing many other carbide coatings. This hardness translates to superior wear resistance, making it ideal for environments with high abrasion. You benefit from components that last longer and require less frequent replacements.
Thermal Stability: TaC maintains its integrity at extreme temperatures. While other carbide coatings may degrade or lose effectiveness, TaC remains stable. This stability ensures that your components perform reliably in high-temperature applications.
Chemical Resistance: TaC offers excellent resistance to chemical reactions. In contrast, some carbide coatings may not withstand corrosive environments as effectively. By choosing TaC, you protect your graphite components from chemical degradation.
Versatility: TaC coating adapts well to various industrial applications. Whether in aerospace, semiconductor manufacturing, or chemical processing, you find TaC suitable for diverse needs. Its versatility makes it a preferred choice over other carbide coatings.
Cost-Benefit Analysis of TaC Coating
Investing in TaC coating involves evaluating both costs and benefits. Understanding this balance helps you make informed decisions.
-
-
Initial Investment: Applying TaC coating may require a higher initial investment compared to other coatings. The cost reflects the advanced techniques and materials used. However, this upfront expense often leads to long-term savings.
-
-
-
Extended Service Life: TaC coating significantly extends the service life of graphite components. You reduce the frequency of replacements and maintenance. This longevity translates to lower operational costs over time.
-
-
-
Operational Efficiency: With TaC-coated components, you experience fewer disruptions due to part failures. This reliability enhances operational efficiency. You maintain consistent production levels and avoid costly downtime.
-
-
-
Quality and Performance: TaC coating improves the quality and performance of your components. Enhanced durability and resistance lead to better product outcomes. You deliver higher-quality products to your customers, boosting satisfaction and reputation.
-
By weighing these factors, you see that TaC coating offers substantial benefits. The initial cost is offset by the long-term advantages, making it a valuable investment for your industrial applications.
Practical Implications of Using TaC Coating
Long-Term Cost Savings
When you apply TaC coating to graphite components, you experience significant long-term cost savings. The coating extends the lifespan of these components, reducing the need for frequent replacements. You spend less on purchasing new parts and on labor costs associated with maintenance. This reduction in expenses contributes to a more efficient budget allocation.
Moreover, TaC coating minimizes downtime in your operations. With fewer component failures, your production processes run smoothly. You avoid costly interruptions that can impact your bottom line. The reliability of TaC-coated components ensures consistent performance, allowing you to maintain steady output levels.
Environmental and Operational Benefits
TaC coating offers notable environmental and operational benefits. By extending the service life of graphite components, you contribute to sustainability. Fewer replacements mean less waste, reducing the environmental impact of your operations. You support eco-friendly practices by minimizing the consumption of raw materials.
Operationally, TaC coating enhances the efficiency of your processes. The improved durability of coated components leads to fewer breakdowns. You maintain optimal production levels without frequent disruptions. This reliability boosts your overall productivity and helps you meet deadlines consistently.
In addition, TaC coating provides protection against harsh environmental conditions. You ensure that your components withstand extreme temperatures and corrosive substances. This resilience enhances the safety and effectiveness of your operations, allowing you to focus on achieving your business goals.
Future Trends in TaC Coating Technology
Innovations in Coating Techniques
You will witness exciting advancements in TaC coating techniques. Researchers and engineers constantly explore new methods to enhance the application process. These innovations aim to improve the quality and efficiency of TaC coatings.
Advanced Deposition Methods: You can expect the development of more precise deposition techniques. These methods will allow for better control over coating thickness and uniformity. Improved deposition ensures that your graphite components receive optimal protection.
Nanotechnology Integration: The integration of nanotechnology into TaC coatings is on the horizon. This approach enhances the coating’s properties at a molecular level. You benefit from increased hardness and resistance, making your components even more durable.
Eco-Friendly Processes: As sustainability becomes a priority, you will see a shift towards eco-friendly coating processes. These methods reduce environmental impact while maintaining high-quality results. You contribute to a greener future by adopting these practices.
Automation and Robotics: Automation in the coating process will become more prevalent. Robotics ensures consistent application and reduces human error. You achieve higher precision and efficiency in your operations.
Emerging Applications in New Industries
TaC coating technology is expanding into new industries. You will find its benefits being recognized in various sectors beyond traditional applications.
Renewable Energy: In the renewable energy sector, TaC coatings enhance the performance of components exposed to harsh conditions. You see improvements in solar panels and wind turbine parts, leading to increased energy efficiency.
Medical Devices: The medical industry is exploring TaC coatings for their biocompatibility and durability. You find these coatings in surgical instruments and implants, ensuring long-lasting performance and safety.
Automotive Industry: TaC coatings are gaining traction in the automotive sector. You benefit from enhanced wear resistance in engine components and improved thermal stability in exhaust systems. These advancements contribute to more reliable and efficient vehicles.
Electronics and Telecommunications: The electronics industry is adopting TaC coatings for their protective properties. You see these coatings in devices that require high thermal conductivity and resistance to wear, ensuring longevity and performance.
By staying informed about these trends, you position yourself to take advantage of the latest developments in TaC coating technology. These innovations and applications promise to enhance the durability and efficiency of your components across various industries.
You have seen how TaC coating significantly enhances the service life of graphite components. This coating provides exceptional resistance to wear, corrosion, and extreme temperatures. By choosing TaC coating, you ensure that your components perform reliably and efficiently in demanding industrial environments. Selecting the right coating is crucial for maintaining operational efficiency and reducing costs. TaC coating stands out as a valuable investment, offering long-term benefits and supporting sustainable practices. Make informed decisions to enhance the durability and performance of your graphite components.
FAQ
What is TaC coating, and why is it used on graphite components?
TaC coating, or Tantalum Carbide coating, is a protective layer applied to graphite components. You use it to enhance the durability and longevity of these components. The coating provides resistance to wear, corrosion, and extreme temperatures, making it ideal for demanding industrial applications.
How does TaC coating improve the service life of graphite components?
TaC coating forms a hard, protective barrier over graphite components. This barrier shields them from abrasive forces and corrosive substances. You benefit from reduced surface damage and material loss. The coating also enhances thermal stability, ensuring components maintain their integrity under high temperatures.
What industries benefit most from TaC-coated graphite components?
Several industries benefit from TaC-coated graphite components. You find them in aerospace, semiconductor manufacturing, chemical processing, and metallurgy. These industries require materials that withstand harsh conditions, and TaC coating provides the necessary protection and durability.
How is TaC coating applied to graphite components?
You can apply TaC coating using various techniques, such as Chemical Vapor Deposition (CVD), Physical Vapor Deposition (PVD), sputtering, and thermal spraying. Each method offers unique advantages, depending on your specific needs and the application environment.
What are the cost implications of using TaC coating?
While TaC coating may involve a higher initial investment, you experience long-term cost savings. The coating extends the service life of graphite components, reducing the need for frequent replacements. You also benefit from fewer maintenance costs and improved operational efficiency.
How does TaC coating compare to other carbide coatings?
TaC coating stands out due to its exceptional hardness, thermal stability, and chemical resistance. You find it more durable than many other carbide coatings. Its versatility makes it suitable for various industrial applications, providing superior protection and performance.
Can TaC coating contribute to environmental sustainability?
Yes, TaC coating contributes to environmental sustainability. By extending the lifespan of graphite components, you reduce waste and minimize the consumption of raw materials. This practice supports eco-friendly operations and reduces the environmental impact of your activities.
Are there any limitations to using TaC coating?
While TaC coating offers many benefits, you should consider factors like the initial cost and the specific application requirements. Proper surface preparation and quality control are essential for effective coating application. You must ensure that the coating meets the desired specifications for optimal performance.
What future trends can we expect in TaC coating technology?
You can expect advancements in deposition methods, nanotechnology integration, and eco-friendly processes. These innovations aim to improve the quality and efficiency of TaC coatings. Emerging applications in renewable energy, medical devices, and automotive industries will also expand the use of TaC coating.
How can I determine if TaC coating is right for my application?
To determine if TaC coating is suitable for your application, consider factors like the operating environment, required durability, and budget. You should evaluate the specific challenges your graphite components face and assess how TaC coating can address these issues. Consulting with experts in the field can also provide valuable insights.