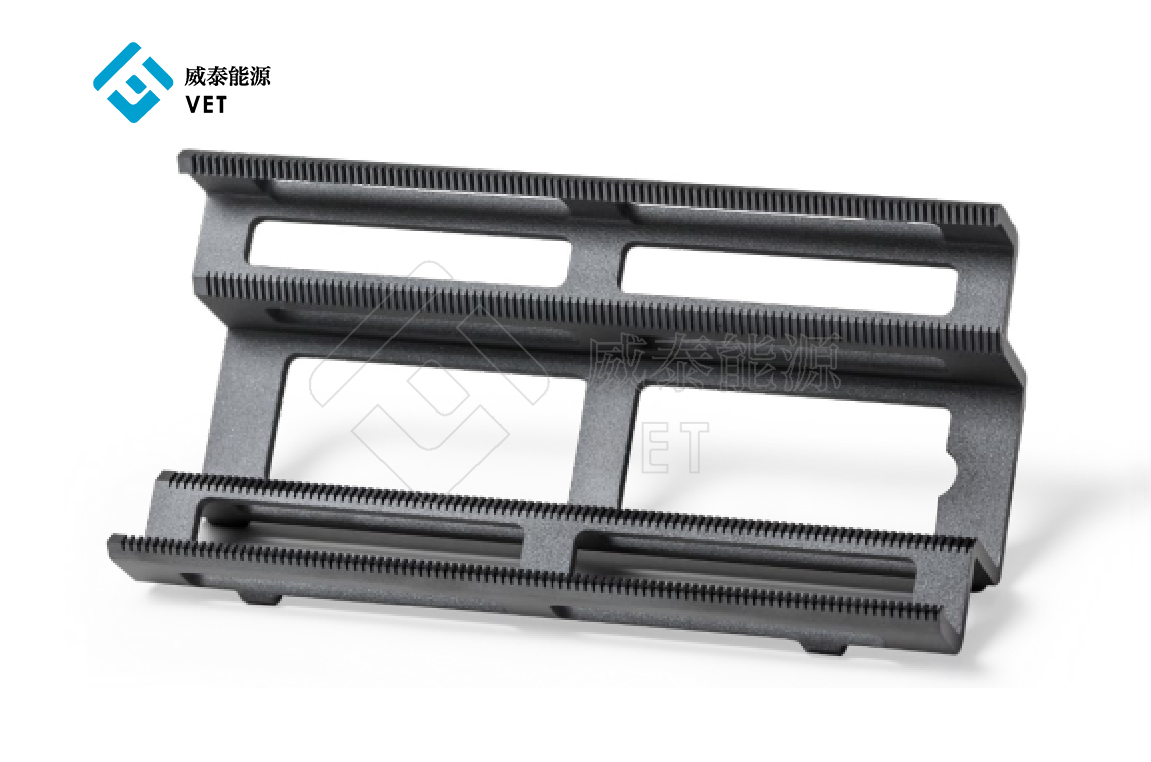
The Contiguous Wafer Boat from vet-china represents a breakthrough in semiconductor manufacturing. It delivers unmatched precision and efficiency in wafer handling. Its innovative design ensures wafers remain stable during critical processes, reducing the risk of damage. Built with high-quality materials, it withstands extreme temperatures and harsh environments. Manufacturers benefit from its ability to optimize throughput and improve yield rates. This advanced solution caters to the rigorous demands of modern fabrication facilities, making it an essential tool for enhancing operational performance.
Key Takeaways
- The Contiguous Wafer Boat enhances semiconductor manufacturing by ensuring wafer stability with self-locking mechanisms, reducing the risk of damage and improving yield rates.
- Quick-release designs streamline wafer handling, allowing for faster loading and unloading, which boosts operational speed and minimizes downtime.
- High-temperature resistance ensures the wafer boat performs reliably in extreme conditions, supporting critical processes like thermal oxidation and annealing.
- Customization options, including tailored designs and integrated sensors, empower manufacturers to optimize production lines for specific needs and enhance operational efficiency.
- Using high-quality materials like quartz and recrystallized silicon carbide (R-SiC) ensures durability, mechanical strength, and minimal contamination during wafer processing.
- Complementary tools, such as tweezers and vacuum wands, are essential for safe wafer handling, preserving wafer integrity and enhancing manufacturing precision.
- Regular maintenance and cleaning of the wafer boat are crucial for extending its lifespan and ensuring consistent performance in semiconductor fabrication.
Key Technical Features of Contiguous Wafer Boats
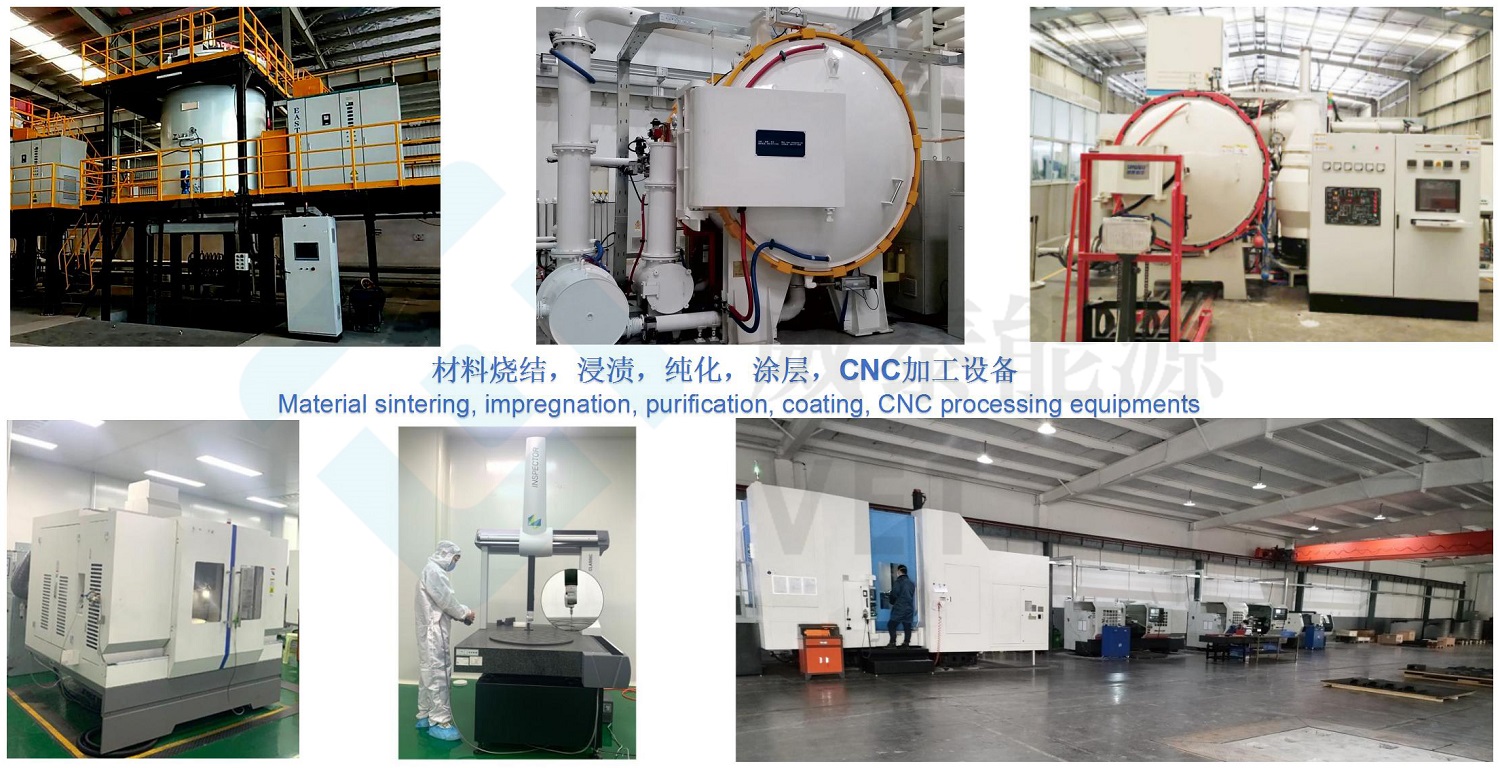
Self-locking Mechanisms
How self-locking mechanisms ensure wafer stability during operations.
The self-locking mechanisms in the Contiguous Wafer Boat play a crucial role in maintaining wafer stability. These mechanisms secure wafers firmly in place, preventing any unintended movement during critical manufacturing processes. By locking the wafers into position, they ensure precise alignment, which is essential for achieving consistent results in semiconductor fabrication. This feature enhances operational reliability and minimizes errors caused by misalignment.
Benefits of reducing wafer movement and potential damage.
Reducing wafer movement significantly lowers the risk of physical damage. The self-locking design protects wafers from scratches, cracks, or other defects that could compromise their quality. This protection directly contributes to higher yield rates by preserving the integrity of each wafer throughout the production cycle. Manufacturers benefit from fewer rejected wafers, leading to cost savings and improved efficiency.
Quick-release Designs
Simplifying the loading and unloading process for wafers.
The quick-release design of the Contiguous Wafer Boat simplifies wafer handling. Operators can load and unload wafers with ease, reducing the time required for these tasks. This streamlined process eliminates unnecessary complexity, allowing workers to focus on maintaining smooth production workflows. The intuitive design ensures that even operators with minimal training can handle wafers efficiently.
Enhancing operational speed and reducing downtime.
By enabling faster wafer handling, the quick-release feature boosts operational speed. Reduced handling time translates to shorter production cycles, which increases overall throughput. Additionally, this design minimizes downtime caused by delays in loading or unloading wafers. Manufacturers can maintain consistent production schedules and meet tight deadlines without compromising quality.
High-Temperature Resistance
Ensuring durability in high-temperature environments.
The Contiguous Wafer Boat exhibits exceptional resistance to high temperatures. It remains stable and reliable even in extreme thermal conditions, making it suitable for demanding semiconductor processes. This durability ensures that the wafer boat performs consistently, regardless of the heat levels involved in manufacturing. Its ability to withstand such conditions extends its lifespan and reduces the need for frequent replacements.
Supporting processes like thermal oxidation and annealing.
High-temperature resistance is critical for processes such as thermal oxidation and annealing. These procedures require materials that can endure prolonged exposure to intense heat without degrading. The Contiguous Wafer Boat supports these processes by maintaining its structural integrity and performance. This capability ensures that manufacturers achieve optimal results in these essential steps of semiconductor fabrication.
Material Options and Their Benefits
Quartz
High purity and resistance to thermal shock.
Quartz offers unmatched purity, making it a preferred material for semiconductor manufacturing. Its ability to resist thermal shock ensures stability during rapid temperature changes. This property is vital for processes that demand precise thermal control. Quartz maintains its structural integrity even under extreme conditions, ensuring consistent performance.
Ideal for processes requiring minimal contamination.
The non-reactive nature of quartz minimizes the risk of contamination. This makes it ideal for environments where maintaining wafer purity is critical. Manufacturers rely on quartz to prevent impurities from affecting the delicate semiconductor fabrication process. Its high chemical stability further enhances its suitability for cleanroom applications.
Silicon Carbide (SiC)
Exceptional strength and thermal conductivity.
Silicon carbide exhibits remarkable strength, allowing it to withstand mechanical stress during demanding operations. Its superior thermal conductivity ensures efficient heat dissipation, which is essential for maintaining optimal processing conditions. These characteristics make SiC a reliable choice for high-performance applications.
Suitable for high-temperature and corrosive environments.
SiC thrives in environments with extreme temperatures and corrosive substances. Its resistance to chemical degradation ensures longevity, even in harsh conditions. Manufacturers benefit from its durability, which reduces the need for frequent replacements. This material supports processes that require robust and reliable components.
Recrystallized Silicon Carbide (R-SiC)
Enhanced mechanical properties, including higher strength and stiffness.
Recrystallized silicon carbide surpasses traditional materials in mechanical performance. Its enhanced strength and stiffness provide exceptional support for wafers during processing. This ensures precise handling and alignment, which are crucial for achieving high-quality results in semiconductor manufacturing.
High corrosion resistance and ability to withstand extreme temperatures.
R-SiC offers outstanding corrosion resistance, making it suitable for chemically aggressive environments. Its ability to endure extreme temperatures without compromising structural integrity ensures reliability in critical processes. This material’s advanced properties make it an excellent choice for manufacturers seeking long-lasting and efficient solutions.
Comparison of Material Properties
Quartz for purity and thermal shock resistance.
Quartz stands out as a material of choice for semiconductor manufacturing due to its exceptional purity. Its non-reactive nature ensures that it does not introduce contaminants during wafer processing. This property is critical for maintaining the integrity of wafers in cleanroom environments. Manufacturers rely on quartz to achieve high-quality results in processes where even minor impurities can lead to defects.
Quartz also excels in resisting thermal shock. It maintains structural stability when exposed to rapid temperature changes, which are common in semiconductor fabrication. This capability reduces the risk of cracking or deformation, ensuring consistent performance. Its ability to endure such conditions makes it indispensable for processes requiring precise thermal control.
"Quartz’s unique combination of purity and thermal shock resistance makes it a cornerstone material in semiconductor manufacturing."
R-SiC for mechanical strength and chemical durability.
Recrystallized silicon carbide (R-SiC) offers unmatched mechanical strength, making it ideal for supporting wafers during demanding operations. Its rigidity ensures that wafers remain securely aligned, reducing the likelihood of misalignment or damage. This material’s superior stiffness enhances its ability to handle the mechanical stresses of modern semiconductor processes.
R-SiC also provides exceptional chemical durability. It resists corrosion even in environments with aggressive chemicals, ensuring long-term reliability. This property allows manufacturers to use R-SiC in processes involving harsh substances without compromising the wafer boat’s performance. Additionally, its ability to withstand extreme temperatures further solidifies its position as a preferred material for high-performance applications.
"R-SiC combines mechanical robustness with chemical resilience, offering a versatile solution for challenging manufacturing conditions."
By comparing these materials, manufacturers can select the one that best aligns with their specific requirements. Quartz excels in purity and thermal stability, while R-SiC delivers superior strength and chemical resistance. Both materials contribute to the efficiency and reliability of semiconductor fabrication processes.
Customization Options for Contiguous Wafer Boats
Design Flexibility
Tailoring the size and shape to fit specific wafer dimensions.
The Contiguous Wafer Boat offers unparalleled design flexibility, allowing manufacturers to customize its size and shape to accommodate specific wafer dimensions. This adaptability ensures a precise fit for wafers, reducing the risk of misalignment during processing. By tailoring the wafer boat to meet unique requirements, manufacturers can optimize their production lines for maximum efficiency and accuracy.
Adapting designs for unique manufacturing processes.
Manufacturers often face distinct challenges in semiconductor fabrication. The Contiguous Wafer Boat addresses these challenges by enabling design modifications that align with unique manufacturing processes. Whether it involves creating specialized slots or adjusting the configuration to support non-standard wafers, this customization capability enhances compatibility and streamlines operations.
Color and Coating Choices
Using color coding for easy identification and organization.
Color coding simplifies wafer boat management in complex manufacturing environments. The Contiguous Wafer Boat can be customized with various colors, making it easier to identify and organize specific batches or processes. This visual distinction reduces errors and improves workflow efficiency, especially in facilities handling multiple wafer types or production stages.
Applying specialized coatings for enhanced durability.
Specialized coatings further enhance the durability of the Contiguous Wafer Boat. These coatings protect the surface from wear and tear caused by repeated use in demanding conditions. They also provide additional resistance to chemical exposure, ensuring the wafer boat maintains its performance over time. Manufacturers benefit from reduced maintenance costs and extended product lifespan.
Additional Custom Features
Integrated sensors for real-time monitoring of wafer conditions.
Advanced customization options include integrating sensors into the Contiguous Wafer Boat. These sensors provide real-time data on wafer conditions, such as temperature and alignment. This feature enables manufacturers to monitor critical parameters during processing, ensuring consistent quality and reducing the likelihood of defects.
Custom branding or labeling for operational efficiency.
Custom branding or labeling adds a professional touch to the Contiguous Wafer Boat while improving operational efficiency. Manufacturers can incorporate logos, serial numbers, or other identifiers to streamline inventory management and traceability. This customization not only enhances brand visibility but also supports better organization within the production facility.
Complementary Tools and Accessories
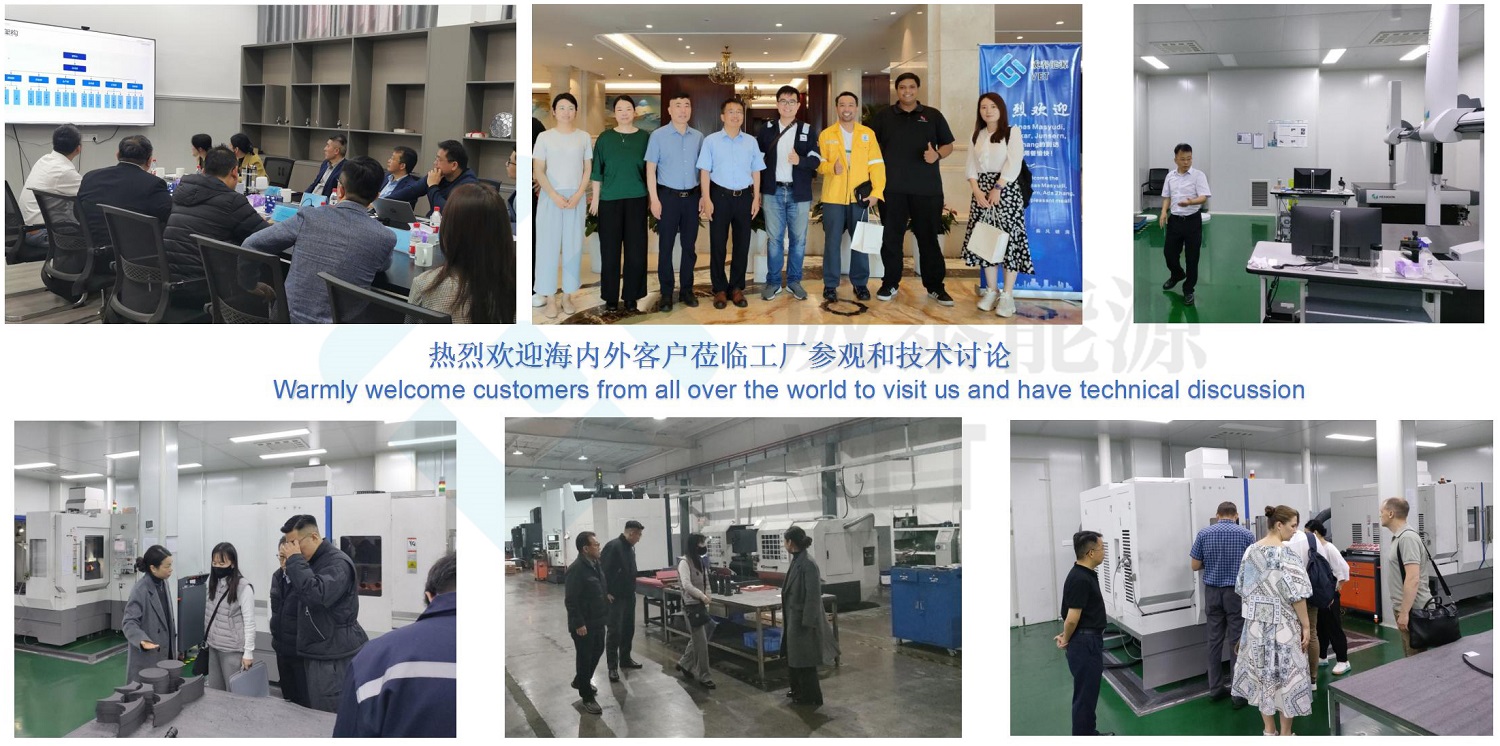
Wafer Handling Tools
Tweezers, vacuum wands, and other tools for safe wafer handling.
Wafer handling tools play a critical role in ensuring the safety and integrity of wafers during semiconductor manufacturing. Tweezers, vacuum wands, and similar tools are specifically designed to handle wafers delicately, minimizing the risk of physical damage. Tweezers with anti-static properties prevent electrostatic discharge, which could harm sensitive wafers. Vacuum wands provide a secure grip without applying direct pressure, reducing the likelihood of scratches or cracks. These tools enhance precision and reliability in wafer handling, making them indispensable for maintaining high-quality standards.
"Proper wafer handling tools are essential for preserving wafer quality and ensuring smooth manufacturing processes."
How these tools work in conjunction with wafer boats.
Wafer handling tools complement the functionality of wafer boats by facilitating seamless loading and unloading processes. Operators use tweezers or vacuum wands to place wafers securely into the slots of the wafer boat, ensuring proper alignment. These tools also assist in removing wafers without causing misalignment or damage. By working in tandem with wafer boats, handling tools streamline operations and reduce the risk of errors. This synergy improves efficiency and supports consistent production outcomes.
Cleaning and Maintenance Equipment
Tools and solutions for maintaining wafer boat cleanliness.
Maintaining the cleanliness of wafer boats is vital for preventing contamination during semiconductor fabrication. Cleaning tools such as ultrasonic cleaners, specialized brushes, and lint-free wipes effectively remove debris and residues. Cleaning solutions formulated for semiconductor applications dissolve stubborn contaminants without damaging the wafer boat’s surface. Automated cleaning systems offer an advanced option for thorough and consistent cleaning. These tools and solutions ensure that wafer boats remain in optimal condition for high-precision manufacturing.
"Regular cleaning of wafer boats safeguards wafer purity and enhances production reliability."
Importance of regular maintenance for optimal performance.
Regular maintenance extends the lifespan of wafer boats and ensures their consistent performance. Routine inspections help identify signs of wear or damage, allowing timely repairs or replacements. Proper cleaning prevents the buildup of contaminants that could compromise wafer quality. Maintenance schedules tailored to the specific demands of semiconductor processes optimize the performance of wafer boats. By prioritizing maintenance, manufacturers achieve higher yield rates and reduce operational disruptions.
"Investing in maintenance practices enhances the durability and efficiency of wafer boats, supporting long-term manufacturing success."
The Contiguous Wafer Boat from vet-china serves as an essential asset for semiconductor manufacturing. Its advanced features, such as self-locking mechanisms and quick-release designs, improve functionality and operational efficiency. High-quality materials like quartz and recrystallized silicon carbide ensure durability and adaptability for diverse manufacturing processes. Customization options, including tailored designs and integrated sensors, empower manufacturers to meet specific production needs. By incorporating this innovative solution and its complementary tools, manufacturers can enhance productivity, minimize downtime, and achieve superior yield rates, solidifying their competitive edge in the industry.
FAQ
What is the primary purpose of the Contiguous Wafer Boat?
The Contiguous Wafer Boat is designed to enhance precision and efficiency in semiconductor manufacturing. It ensures secure wafer handling, minimizes damage risks, and optimizes throughput during critical processes.
Which materials are used to construct the Contiguous Wafer Boat?
The Contiguous Wafer Boat is available in high-quality materials such as quartz, silicon carbide (SiC), and recrystallized silicon carbide (R-SiC). Each material offers unique benefits, including thermal stability, mechanical strength, and chemical resistance.
How does the self-locking mechanism improve wafer handling?
The self-locking mechanism secures wafers firmly in place, preventing movement during operations. This feature ensures precise alignment, reduces the risk of damage, and enhances overall manufacturing reliability.
Can the Contiguous Wafer Boat withstand high temperatures?
Yes, the Contiguous Wafer Boat exhibits exceptional high-temperature resistance. It performs reliably in extreme thermal environments, making it suitable for processes like thermal oxidation and annealing.
Are customization options available for the Contiguous Wafer Boat?
Manufacturers can customize the Contiguous Wafer Boat to meet specific requirements. Options include tailored designs, color coding, specialized coatings, and integrated sensors for real-time monitoring.
What are the advantages of using quartz in wafer boats?
Quartz offers high purity and excellent resistance to thermal shock. These properties make it ideal for processes requiring minimal contamination and precise thermal control.
How does recrystallized silicon carbide (R-SiC) benefit semiconductor manufacturing?
R-SiC provides superior mechanical strength, stiffness, and corrosion resistance. It performs well in chemically aggressive and high-temperature environments, ensuring long-term reliability.
What complementary tools work with the Contiguous Wafer Boat?
Wafer handling tools like tweezers and vacuum wands complement the Contiguous Wafer Boat. These tools ensure safe loading and unloading, preserving wafer integrity during manufacturing.
How should manufacturers maintain the Contiguous Wafer Boat?
Regular cleaning and maintenance are essential. Using ultrasonic cleaners, specialized brushes, and appropriate solutions helps maintain cleanliness. Routine inspections ensure optimal performance and extend the product’s lifespan.
Why should manufacturers choose the Contiguous Wafer Boat from vet-china?
The Contiguous Wafer Boat combines advanced features, high-quality materials, and customization options. It enhances operational efficiency, reduces downtime, and improves yield rates, making it a reliable choice for semiconductor manufacturing.