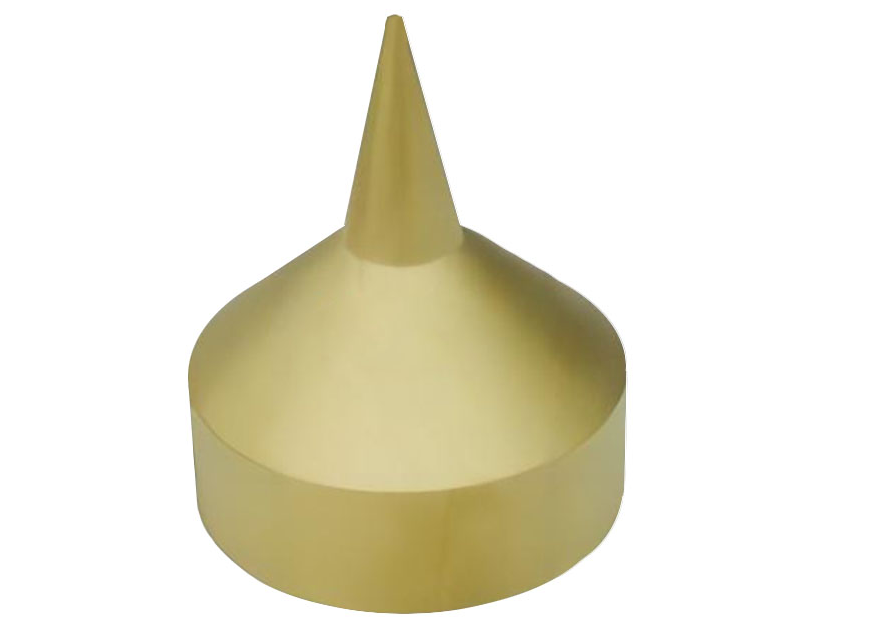
TAC coating chucks, featuring a specialized tic tac coating made from Tantalum Carbide, are essential tools in semiconductor processing. These chucks provide outstanding thermal stability and chemical resistance, making them perfect for wafer handling, etching, and deposition tasks. Their capability to maintain vacuum integrity significantly reduces contamination risks. By improving precision and efficiency, they enhance throughput and ensure superior product quality in manufacturing.
Key Takeaways
- TAC coating chucks help in making semiconductors by staying stable under heat and resisting chemicals, ensuring good results.
- These chucks work faster and lower contamination risks, which increases production and cuts down repair costs.
- They last long and resist damage, reducing the need for replacements and keeping performance steady.
Properties of TAC Coating Chucks
Hardness and Durability
TAC coating chucks excel in hardness and durability, making them indispensable in semiconductor processing. The tantalum carbide coating enhances wear resistance, ensuring the chuck performs reliably during repeated manufacturing cycles. This durability is critical for maintaining precision in high-temperature environments.
Key attributes include:
- Exceptional thermal stability.
- High resistance to chemical corrosion.
- Extended operational lifespan.
A comparison of TAC coating chucks with other materials highlights their superiority:
Metric | TaC Coating Chucks | Other Materials |
---|---|---|
Hardness | High | Variable |
Wear Resistance | Excellent | Moderate to Low |
Chemical Inertness | High | Low to Moderate |
High-Temperature Resistance | Excellent | Moderate |
The advanced hardness of the TAC coating ensures stable performance, even in demanding processes like epitaxy. This reliability reduces the need for frequent replacements, saving time and costs.
Thermal Conductivity
TAC coating chucks demonstrate excellent thermal conductivity, a vital property for semiconductor manufacturing. This feature aids in effective heat dissipation, preventing local overheating during high-temperature processes. The high melting point of tantalum carbide ensures the chuck withstands extreme temperatures without compromising performance.
Additional benefits include:
- Resistance to thermal shock.
- Consistent temperature distribution across the wafer.
- Reduced risk of delamination due to matched thermal expansion properties.
These qualities make TAC coating chucks a preferred choice over alternatives like uncoated graphite, which lacks similar thermal stability and durability.
Chemical Resistance
The chemical resistance of TAC coating chucks ensures their suitability for harsh semiconductor environments. The tantalum carbide coating is chemically inert, providing robust protection against acids, alkalis, and reactive gases. This resistance minimizes contamination risks and maintains the purity of processed materials.
Key advantages include:
- Protection against corrosive substances.
- Enhanced longevity of the underlying graphite substrate.
- Stable performance in epitaxial processes.
By resisting chemical corrosion, TAC coating chucks maintain their structural integrity, ensuring consistent results in semiconductor fabrication.
Applications of TAC Coating Chucks in Semiconductor Processing
Wafer Handling and Stability
TAC coating chucks play a critical role in wafer handling by ensuring stability and precision during semiconductor processing. Their exceptional thermal stability and durability allow them to perform reliably under high temperatures. The high vacuum integrity of these chucks minimizes outgassing, reducing contamination risks and maintaining wafer purity.
Key advantages include:
- High-temperature resistance for extreme conditions.
- Chemical inertness that prevents contamination.
- Wear resistance, which extends the chuck’s lifespan and ensures consistent performance.
The coefficient of thermal expansion (CTE) of the TAC coating closely matches that of graphite. This compatibility reduces stress and prevents delamination, even during repeated cycles. These properties make TAC coating chucks indispensable for maintaining wafer stability in high-precision processes.
Etching and Deposition Processes
TAC coating chucks enhance the efficiency of etching and deposition processes in semiconductor manufacturing. Their ability to maintain high vacuum integrity minimizes contamination, ensuring superior material purity. The chucks accommodate various substrate sizes and geometries, making them versatile for different applications.
Key benefits include:
- Improved throughput and yield.
- Reduced costs due to extended chuck lifespan.
- Enhanced durability and stability under extreme conditions.
The high melting point of the TAC coating ensures the chuck withstands the intense temperatures of these processes without degrading. Its chemical inertness protects the underlying material from corrosive substances, leading to fewer replacements and higher yield rates.
Epitaxial Wafer Growth for SiC and GaN Devices
In epitaxial wafer growth, TAC coating chucks demonstrate exceptional performance, particularly for SiC and GaN devices. Their high-temperature resistance allows them to handle the extreme conditions of crystal growth and epitaxy. The chemical inertness of the TAC coating minimizes contamination, maintaining the purity of the materials.
Specific advantages include:
- Compatibility with the blue light GaN MOCVD process without introducing impurities.
- Comparable performance and uniformity to conventional SiC carriers in LED production.
- A significantly lower corrosion rate than SiC, enhancing the longevity of wafer carriers.
These features make TAC coating chucks a cost-effective and reliable choice for semiconductor manufacturers, improving throughput and reducing maintenance needs.
Benefits of Using TAC Coating Chucks
Extended Tool Longevity
TAC coating chucks significantly enhance tool longevity in semiconductor manufacturing. The advanced tantalum carbide coating provides exceptional thermal stability and resistance to chemical corrosion. These properties protect the chuck from oxidation and thermal stresses, ensuring a longer operational lifespan.
- The TaC coating enhances hardness and wear resistance, enabling the chuck to withstand extreme temperatures and corrosive gases.
- TaC-coated graphite components exhibit remarkable durability under demanding conditions, reducing maintenance requirements.
- The extended service life of these chucks results in fewer replacements and lower maintenance costs.
This durability minimizes downtime and ensures consistent performance, making TAC coating chucks a cost-effective solution for semiconductor manufacturers.
Enhanced Process Efficiency
TAC coating chucks improve process efficiency by maintaining high vacuum integrity and ensuring consistent performance under extreme conditions. Their chemical inertness reduces contamination risks, preserving material purity and enhancing device performance.
- Enhanced thermal stability ensures reliable operation during high-temperature processes.
- The versatile design accommodates various semiconductor substrates, maximizing productivity.
- Reduced maintenance requirements and fewer replacements lower overall costs.
These features contribute to higher throughput and improved yield rates, making TAC coating chucks indispensable for efficient semiconductor production.
Improved Product Quality and Yield
TAC coating chucks play a crucial role in improving product quality and yield. Their ability to maintain precise control and stability during processing ensures superior device performance.
“The TaC Coating Chuck addresses the critical need for precise control and stability during processing, ensuring exceptional thermal stability, durability, and resistance to chemical corrosion. This technology minimizes outgassing and contamination, ensuring the purity and quality of semiconductor materials, resulting in superior device performance and reliability.”
The durability and thermal stability of TAC coating chucks reduce defects and increase consistency in semiconductor products. These qualities make them a reliable choice for manufacturers aiming to achieve high-quality outcomes.
TAC coating chucks integrate advanced tantalum carbide coatings, ensuring exceptional thermal stability, durability, and chemical resistance. These properties make them indispensable for precise control in semiconductor fabrication. Their applications, including wafer handling, epitaxy, and deposition, highlight their role in advancing semiconductor technology. Ningbo VET Energy Technology Co. specializes in high-performance TAC coating chucks, offering reliable solutions for semiconductor manufacturing.
For inquiries, contact Ningbo VET Energy Technology Co. at:
- Tel: 86-1891 1596 392
- Email: yeah@china-vet.com
- Address: No. 777, Zhongguan West Road, Zhenhai District, Ningbo, Zhejiang, 315201, China
Visit their website at www.cnvetenergy.com for more information.