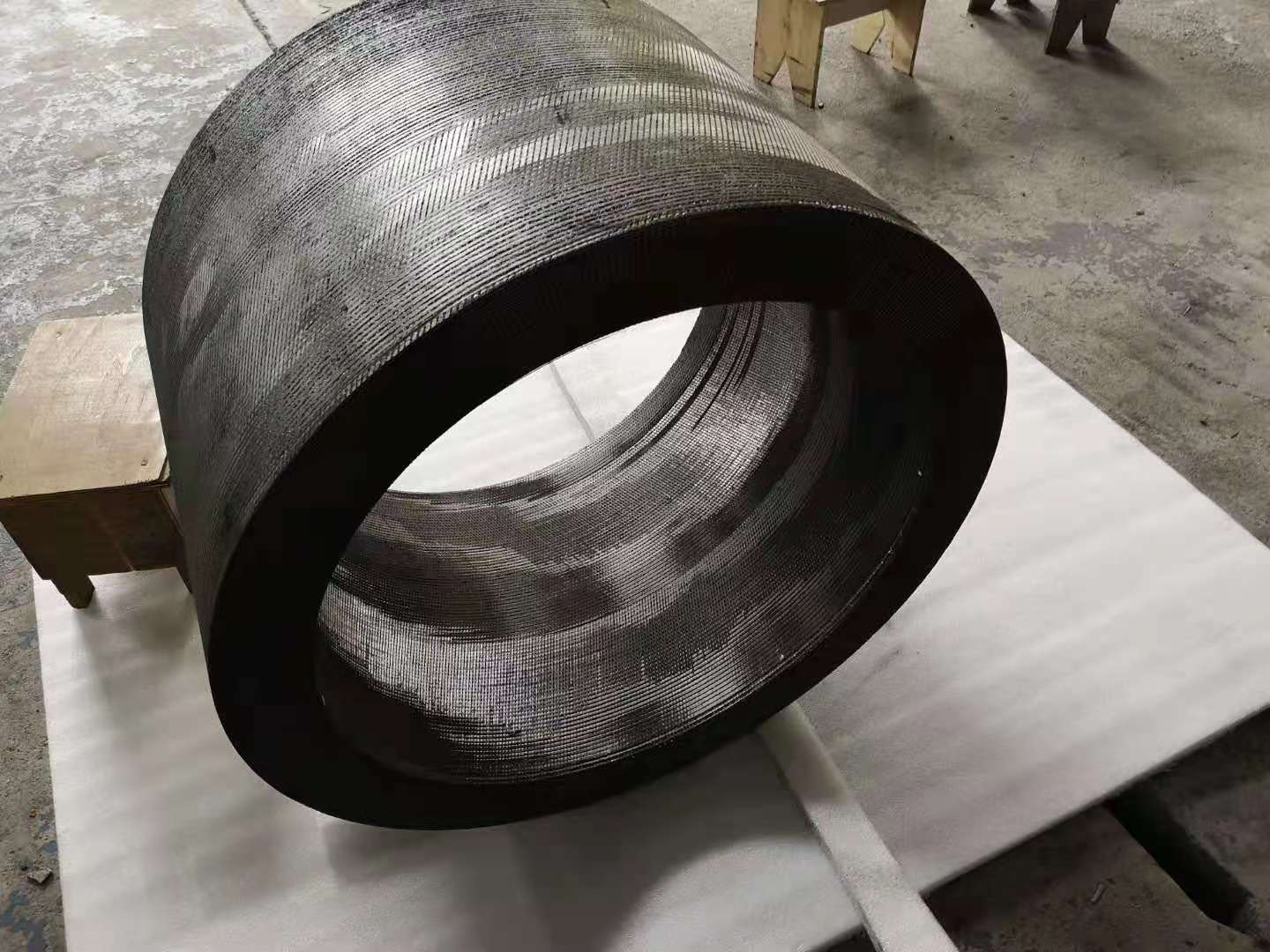
Carbon carbon composites stand out as materials with remarkable thermal and mechanical properties. Their high thermal conductivity ensures efficient heat transfer, while their low thermal expansion provides dimensional stability under extreme conditions. The superior strength of these composites results from the strong covalent bonds between carbon atoms. Advanced production techniques further enhance their performance. These attributes make carbon carbon composites essential for applications requiring durability and reliability in challenging environments.
Key Takeaways
- Carbon-carbon composites excel in thermal conductivity and dimensional stability, making them ideal for high-temperature applications.
- Their low coefficient of thermal expansion ensures minimal shape alteration under extreme heat, enhancing reliability in critical environments.
- The unique structure of carbon-carbon composites allows them to maintain mechanical strength and resist wear, making them suitable for demanding applications like aerospace and energy.
- Advanced production techniques, including pyrolysis and carbonization, significantly enhance the properties of these composites, ensuring optimal performance.
- Customization of fiber types and arrangements allows engineers to tailor carbon-carbon composites for specific applications, maximizing their effectiveness.
- Post-processing methods like heat treatment improve the strength and toughness of carbon-carbon composites, ensuring long-term durability under stress.
- Emerging applications in fields such as electronics and robotics highlight the ongoing innovation and versatility of carbon-carbon composites in modern engineering.
Thermal Properties of Carbon-Carbon Composites
High Thermal Conductivity
Role of carbon fibers and matrix in heat transfer
Carbon carbon composites exhibit exceptional thermal conductivity due to the synergistic interaction between carbon fibers and the carbon matrix. Carbon fibers, known for their high thermal conductivity, act as efficient pathways for heat transfer. The carbon matrix complements this by ensuring uniform heat distribution across the composite structure. Together, these components create a material capable of transferring heat effectively, even under demanding conditions.
Influence of density and microstructure on thermal performance
The density and microstructure of carbon carbon composites significantly influence their thermal performance. Higher density enhances thermal conductivity by reducing voids and improving the contact between fibers and the matrix. A well-optimized microstructure, characterized by uniform fiber alignment and minimal defects, further boosts heat transfer efficiency. Engineers often tailor these parameters to meet specific thermal requirements in advanced applications.
Low Coefficient of Thermal Expansion (CTE)
Mechanisms behind dimensional stability at high temperatures
Carbon carbon composites maintain dimensional stability at elevated temperatures due to their low coefficient of thermal expansion (CTE). The strong covalent bonds between carbon atoms resist thermal deformation, ensuring minimal expansion or contraction. This property allows the material to retain its shape and structural integrity, even when exposed to extreme heat. Such stability is crucial for applications requiring precision and reliability.
Comparison with other high-performance materials
Compared to other high-performance materials, carbon carbon composites demonstrate superior thermal stability. Metals like aluminum and steel expand significantly under heat, leading to potential structural issues. Ceramics, while stable, often lack the toughness required for dynamic environments. Carbon carbon composites combine low CTE with excellent mechanical properties, making them a preferred choice for high-temperature applications.
Thermal Resistance at Extreme Temperatures
Stability and performance above 3000°F (1650°C)
Carbon carbon composites excel in environments exceeding 3000°F (1650°C). Their unique structure, reinforced by strong carbon-carbon bonds, prevents degradation under such extreme conditions. Unlike many materials that weaken or melt at high temperatures, these composites retain their mechanical and thermal properties. This resilience makes them indispensable in industries requiring materials that can endure intense heat.
Applications in high-temperature environments
The ability of carbon carbon composites to withstand extreme temperatures has led to their widespread use in high-temperature environments. They are integral to aerospace components like rocket nozzles and heat shields, where thermal resistance is critical. In the energy sector, they play a vital role in nuclear reactors and solar thermal systems. Their unmatched performance ensures reliability in these demanding applications.
Mechanical Properties of Carbon-Carbon Composites
High Tensile Strength and Elastic Modulus
Contribution of carbon fibers and matrix bonding
The tensile strength and elastic modulus of carbon carbon composites stem from the robust interaction between carbon fibers and the surrounding matrix. Carbon fibers, known for their inherent strength, provide the primary load-bearing capability. The matrix, which binds these fibers together, ensures stress distribution across the composite. This synergy between the fibers and the matrix enhances the material’s ability to withstand significant tensile forces without deformation. Engineers often optimize the bonding process to maximize these mechanical properties for demanding applications.
Impact of fiber orientation and microstructure
The orientation of fibers within the composite plays a critical role in determining its mechanical performance. Aligned fibers exhibit superior tensile strength along their axis, making the material highly effective in specific load-bearing directions. Conversely, random fiber orientations provide more uniform strength but may reduce peak performance in targeted directions. The microstructure, including the density and arrangement of fibers, further influences the elastic modulus. A well-designed microstructure minimizes defects, ensuring consistent mechanical behavior under stress.
Fracture Resistance and Toughness
Resistance to cracking and impact under stress
Carbon carbon composites demonstrate remarkable resistance to cracking and impact, even under significant stress. The strong covalent bonds between carbon atoms prevent the propagation of cracks, maintaining the material’s structural integrity. Additionally, the matrix absorbs and redistributes energy from impacts, reducing the likelihood of catastrophic failure. This combination of properties makes the material ideal for applications where durability and reliability are paramount.
Factors influencing toughness and durability
Several factors influence the toughness and durability of carbon carbon composites. The quality of the fiber-matrix interface plays a pivotal role, as a strong bond resists crack initiation and propagation. The fiber type and arrangement also affect the material’s ability to absorb energy without fracturing. Post-processing techniques, such as heat treatment, further enhance toughness by refining the microstructure. These factors collectively ensure the composite’s long-term performance in challenging environments.
Fatigue and Wear Resistance
Long-term performance under cyclic loading
Carbon carbon composites excel in maintaining their mechanical properties under cyclic loading conditions. The material’s fatigue resistance arises from its ability to dissipate energy and resist microstructural damage over repeated stress cycles. Unlike many traditional materials, carbon carbon composites exhibit minimal degradation, even after prolonged exposure to fluctuating loads. This characteristic ensures reliability in applications requiring consistent performance over extended periods.
Resistance to wear in high-stress environments
The wear resistance of carbon carbon composites makes them suitable for high-stress environments. The material’s hardness and structural integrity prevent surface degradation, even under abrasive conditions. The matrix protects the fibers from direct contact with external forces, reducing wear and extending the composite’s lifespan. This property is particularly valuable in industries where components face continuous friction or mechanical stress.
Production Methods and Their Influence on Properties
Pyrolysis and Carbonization Processes
Formation of the carbon matrix and its impact on properties
The pyrolysis and carbonization processes play a pivotal role in forming the carbon matrix within a carbon carbon composite. During pyrolysis, organic precursors undergo thermal decomposition in an inert atmosphere, leaving behind a carbon-rich structure. This step establishes the foundation of the composite’s matrix. Carbonization follows, further refining the material by removing non-carbon elements and enhancing the carbon content. The resulting matrix provides the composite with its characteristic strength and thermal stability. A well-formed carbon matrix ensures uniform stress distribution and contributes to the material’s ability to withstand extreme conditions.
Influence on thermal conductivity and mechanical strength
The thermal conductivity and mechanical strength of a carbon carbon composite depend heavily on the quality of the pyrolysis and carbonization processes. High temperatures during these stages improve the alignment of carbon atoms, creating a more ordered structure. This alignment enhances heat transfer pathways, resulting in superior thermal conductivity. Additionally, the removal of impurities during carbonization strengthens the bonds within the matrix, increasing the composite’s mechanical resilience. Engineers carefully control these processes to optimize the composite’s performance for specific applications.
Role of Fiber Preforms
Customization of fiber type and arrangement for specific applications
Fiber preforms serve as the backbone of a carbon carbon composite, offering opportunities for customization to meet diverse application needs. Engineers select fiber types based on desired properties, such as tensile strength or thermal conductivity. For instance, high-modulus fibers provide exceptional stiffness, while high-strength fibers enhance load-bearing capacity. The arrangement of these fibers, whether unidirectional, woven, or random, further tailors the composite’s performance. This customization ensures that the material meets the precise demands of industries like aerospace and energy.
Optimization for thermal and mechanical performance
The optimization of fiber preforms directly impacts the thermal and mechanical performance of a carbon carbon composite. Aligned fibers maximize heat transfer and tensile strength along specific directions, making the material ideal for targeted applications. Conversely, multidirectional arrangements offer balanced properties, suitable for environments requiring uniform performance. Engineers also focus on minimizing voids and defects within the preform to enhance overall durability. These efforts ensure that the composite delivers consistent results under challenging conditions.
Post-Processing Techniques
Heat treatment and densification for enhanced properties
Post-processing techniques, such as heat treatment and densification, significantly enhance the properties of a carbon carbon composite. Heat treatment involves exposing the composite to elevated temperatures, which improves the alignment of carbon atoms and reduces residual stresses. This process increases both thermal conductivity and mechanical strength. Densification, achieved through repeated impregnation and carbonization cycles, fills voids within the matrix. The result is a denser, more robust material capable of withstanding extreme environments.
Improvements in strength, toughness, and thermal stability
Post-processing methods contribute to notable improvements in the strength, toughness, and thermal stability of a carbon carbon composite. Heat treatment refines the microstructure, reducing the likelihood of crack initiation and propagation. Densification enhances the material’s resistance to wear and fatigue by eliminating weak points. These enhancements ensure that the composite maintains its integrity under high-stress and high-temperature conditions. Industries rely on these advanced techniques to produce materials that meet the rigorous demands of modern engineering.
Practical Applications of Carbon-Carbon Composites
Aerospace Industry
Use in rocket nozzles, heat shields, and re-entry vehicles
The aerospace industry relies heavily on carbon carbon composites for critical components. Rocket nozzles, which endure extreme temperatures and intense pressure during propulsion, benefit from the material’s high thermal resistance and mechanical strength. Heat shields, essential for protecting spacecraft during atmospheric re-entry, utilize these composites to withstand temperatures exceeding 3000°F (1650°C). Re-entry vehicles also incorporate carbon carbon composites to maintain structural integrity under severe thermal and mechanical stress. These applications highlight the material’s ability to perform reliably in the most demanding environments.
Advantages in lightweight, high-temperature components
Carbon carbon composites offer a unique combination of lightweight properties and high-temperature performance. Their low density reduces the overall weight of aerospace components, improving fuel efficiency and payload capacity. At the same time, their ability to retain strength and stability under extreme heat ensures durability and safety. This dual advantage makes them indispensable for modern aerospace engineering, where performance and efficiency are paramount.
Energy Sector
Applications in nuclear reactors and solar thermal systems
In the energy sector, carbon carbon composites play a vital role in advanced systems. Nuclear reactors use these materials for control rods and structural components due to their ability to resist radiation damage and maintain stability at high temperatures. Solar thermal systems, which concentrate sunlight to generate heat, rely on the material’s excellent thermal conductivity and resistance to thermal shock. These applications demonstrate the versatility of carbon carbon composites in addressing the challenges of energy production.
Benefits in thermal management and energy efficiency
Effective thermal management is crucial for optimizing energy systems, and carbon carbon composites excel in this area. Their high thermal conductivity ensures efficient heat transfer, reducing energy losses in critical processes. Additionally, their low coefficient of thermal expansion minimizes thermal stress, enhancing the longevity and reliability of components. By improving energy efficiency and system performance, these composites contribute to sustainable energy solutions.
Other Advanced Engineering Fields
Use in automotive racing, industrial tooling, and medical devices
Carbon carbon composites have found applications beyond aerospace and energy. In automotive racing, they are used for brake discs and clutches, where their wear resistance and thermal stability ensure consistent performance under extreme conditions. Industrial tooling benefits from the material’s strength and durability, making it ideal for high-precision manufacturing processes. In the medical field, carbon carbon composites are utilized in surgical instruments and prosthetics due to their biocompatibility and lightweight nature. These diverse applications underscore the material’s adaptability across industries.
Emerging applications in cutting-edge technologies
As technology advances, new uses for carbon carbon composites continue to emerge. Researchers are exploring their potential in next-generation electronics, where their thermal and electrical properties could enhance device performance. The material is also being investigated for use in quantum computing and advanced robotics, where its unique characteristics could enable breakthroughs. These developments highlight the ongoing innovation surrounding carbon carbon composites and their expanding role in cutting-edge technologies.
Carbon carbon composites demonstrate exceptional thermal and mechanical properties, making them indispensable in modern engineering. Their high thermal conductivity ensures efficient heat transfer, while their low thermal expansion provides stability under extreme conditions. These attributes stem from their unique structure and advanced production techniques. Industries such as aerospace and energy rely on these materials for critical applications. As technological advancements progress, the demand for carbon carbon composites will continue to rise. Their role in high-performance engineering solidifies their importance in shaping the future of innovation.
FAQ
What are carbon-carbon composites made of?
Carbon-carbon composites consist of carbon fibers embedded in a carbon matrix. The fibers provide strength and stiffness, while the matrix ensures structural integrity and distributes stress. Both components are derived from organic precursors through processes like pyrolysis and carbonization.
How do carbon-carbon composites perform under extreme temperatures?
Carbon-carbon composites maintain their mechanical and thermal properties even at temperatures exceeding 3000°F (1650°C). Their strong covalent bonds and unique structure prevent degradation, making them ideal for high-temperature applications such as rocket nozzles and heat shields.
Why are carbon-carbon composites preferred over metals in certain applications?
Carbon-carbon composites outperform metals in several ways. They exhibit lower thermal expansion, ensuring dimensional stability under heat. Their lightweight nature reduces overall system weight, and their superior thermal resistance allows them to endure extreme conditions where metals may fail.
Can carbon-carbon composites resist wear and fatigue?
Yes, carbon-carbon composites demonstrate excellent wear and fatigue resistance. Their robust structure prevents surface degradation under abrasive conditions, and their ability to dissipate energy minimizes damage from cyclic loading. These properties ensure long-term reliability in demanding environments.
How does fiber orientation affect the properties of carbon-carbon composites?
Fiber orientation significantly influences the composite’s performance. Aligned fibers enhance tensile strength and thermal conductivity along specific directions. Random or multidirectional arrangements provide balanced properties, making the material suitable for applications requiring uniform strength.
What industries benefit the most from carbon-carbon composites?
Industries such as aerospace, energy, automotive racing, and advanced manufacturing benefit greatly from carbon-carbon composites. Their high-temperature stability, strength, and durability make them indispensable for applications like rocket components, nuclear reactors, and high-performance brake systems.
Are carbon-carbon composites environmentally sustainable?
The production of carbon-carbon composites involves energy-intensive processes, which may raise environmental concerns. However, their durability and long lifespan reduce the need for frequent replacements, contributing to resource efficiency in the long term.
How do post-processing techniques improve carbon-carbon composites?
Post-processing techniques like heat treatment and densification enhance the properties of carbon-carbon composites. Heat treatment aligns carbon atoms, improving strength and thermal conductivity. Densification fills voids, increasing density and toughness, ensuring the material performs well under extreme conditions.
What makes carbon-carbon composites suitable for aerospace applications?
Carbon-carbon composites combine lightweight properties with exceptional thermal and mechanical performance. They withstand extreme temperatures and pressures, making them ideal for critical aerospace components like rocket nozzles, heat shields, and re-entry vehicle structures.
Are there any emerging applications for carbon-carbon composites?
Yes, researchers are exploring new applications for carbon-carbon composites in fields like electronics, quantum computing, and robotics. Their unique thermal, mechanical, and electrical properties make them promising candidates for cutting-edge technologies.