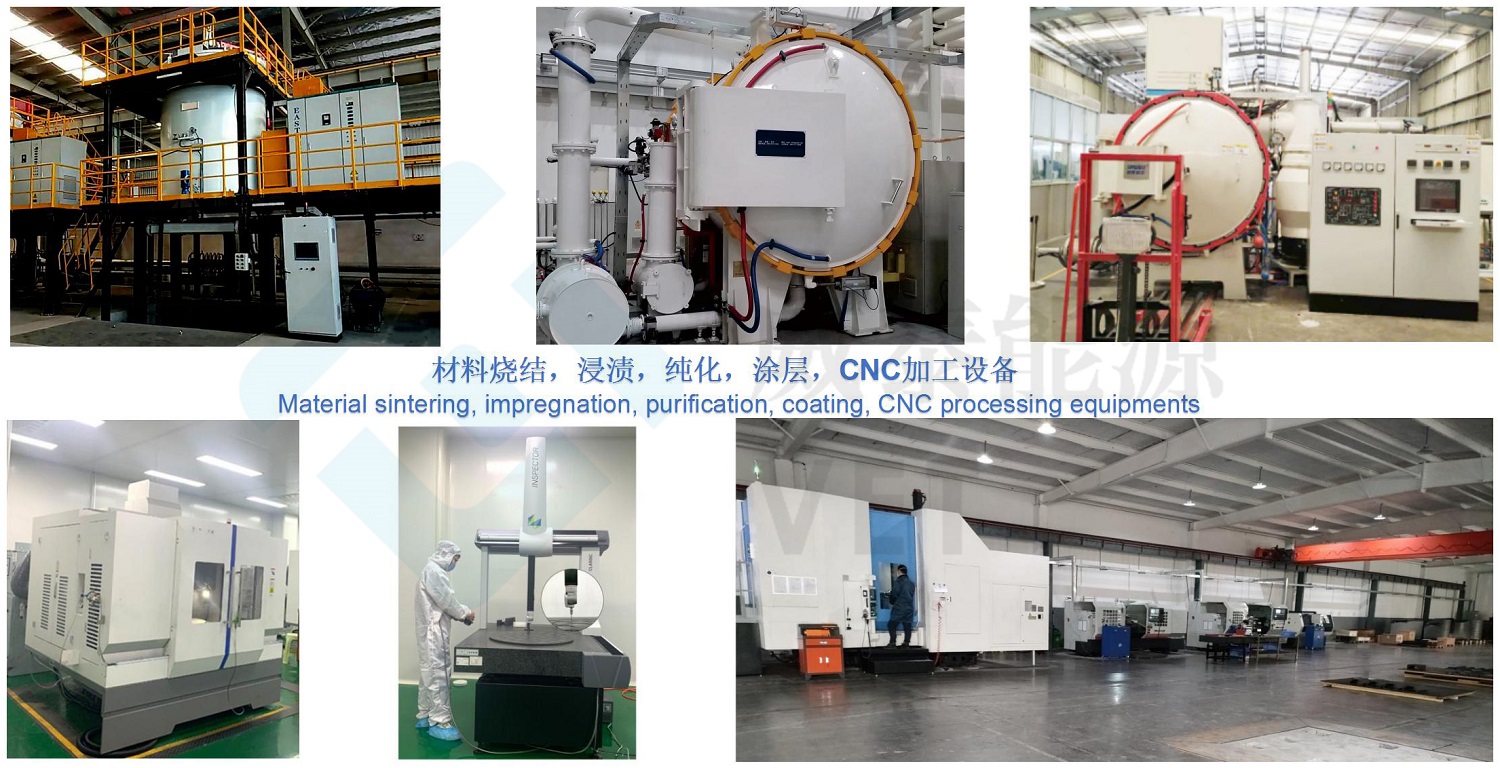
The VET Energy Wafer Susceptor with TaC Coating offers a cutting-edge solution for wafer processing applications. Its advanced design ensures high performance and reliability in demanding environments. The tantalum carbide (TaC) coating enhances the susceptor’s durability, thermal resistance, and chemical stability, making it a superior choice for precision-driven industries. This technology plays a vital role in sectors like semiconductors and energy systems, where resilience and accuracy are critical. By combining innovation with robust materials, the VET Energy Wafer Susceptor sets a new standard for operational excellence.
Key Takeaways
- The VET Energy Wafer Susceptor with TaC Coating is engineered for high-performance wafer processing, ensuring precision and reliability in demanding industries.
- Tantalum carbide (TaC) coating significantly enhances the susceptor’s durability, thermal resistance, and chemical stability, making it ideal for extreme conditions.
- The susceptor’s design promotes optimal thermal uniformity, ensuring consistent results during wafer processing, which is crucial for semiconductor manufacturing.
- With a hardness rating of 2500 to 3000 HV, the TaC coating provides superior wear resistance, reducing maintenance and replacement costs over time.
- The susceptor’s versatility allows it to be used in various applications, including semiconductor manufacturing, energy systems, and advanced research, showcasing its broad utility.
- By minimizing wear and tear, the VET Energy Wafer Susceptor contributes to lower operational costs and improved efficiency for users in high-temperature applications.
- VET Energy’s commitment to innovation and quality positions the susceptor as a leading solution for industries requiring high-performance materials.
Technical Specifications of the VET Energy Wafer Susceptor with TaC Coating
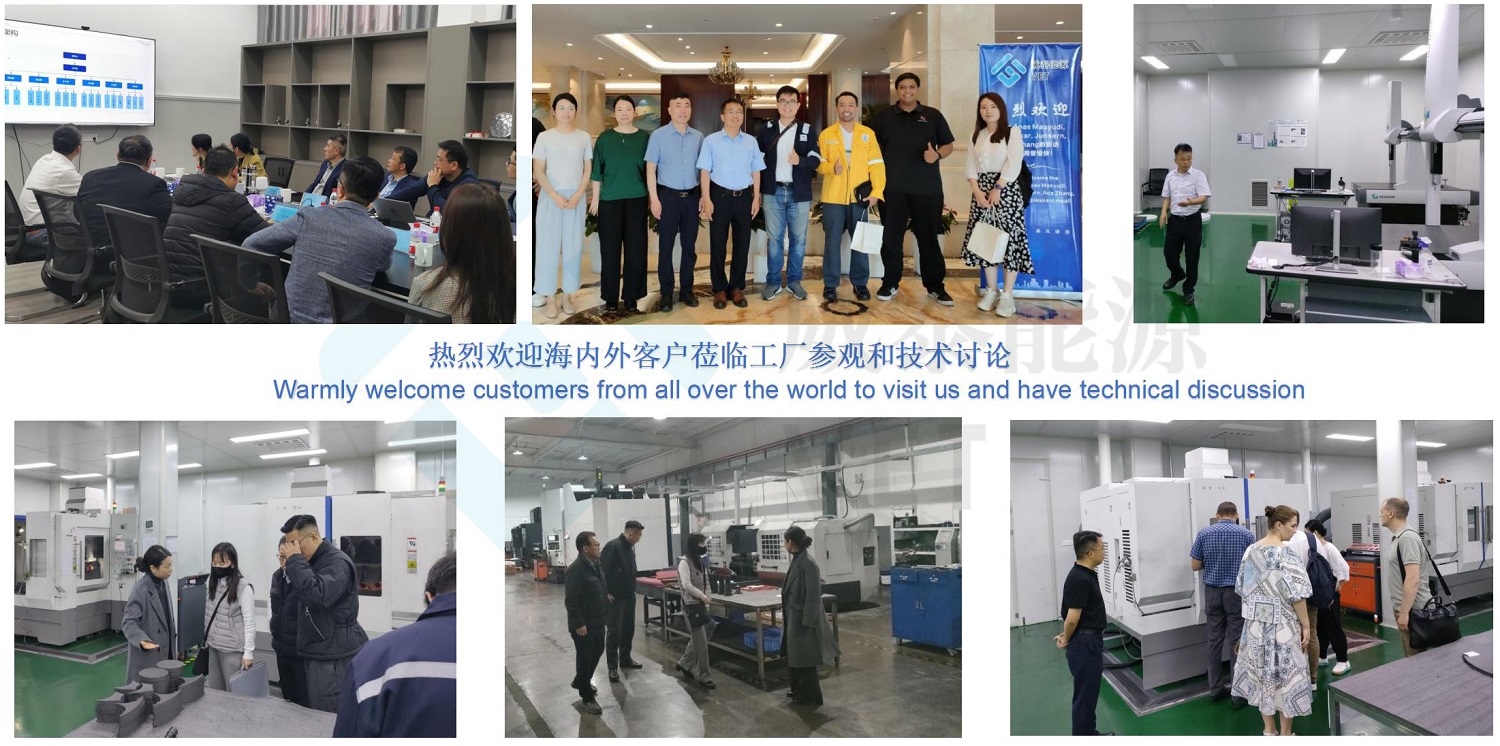
Material Composition
The VET Energy Wafer Susceptor incorporates advanced materials to ensure exceptional performance. The base material, often graphite or silicon carbide, provides a strong foundation for the susceptor. These materials are selected for their ability to withstand high temperatures and maintain structural integrity under extreme conditions.
The tantalum carbide (TaC) coating enhances the susceptor’s properties significantly. With a hardness rating between 2500 and 3000 HV, the coating offers remarkable resistance to wear and mechanical damage. This feature ensures the susceptor remains durable even in demanding applications. Additionally, the TaC coating exhibits excellent chemical stability, resisting reactions with acids, bases, and other corrosive substances. These characteristics make the VET Energy Wafer Susceptor a reliable choice for precision-driven industries.
Dimensions and Design
The VET Energy Wafer Susceptor is designed to meet the specific requirements of G5 and G10 wafer processing. Standard dimensions and tolerances are maintained to ensure compatibility with industry equipment. This precision in manufacturing guarantees seamless integration into existing systems.
The design of the susceptor prioritizes optimal wafer support and thermal uniformity. Its structure ensures even heat distribution across the wafer surface, which is critical for achieving consistent results during processing. The thoughtful engineering behind the susceptor’s design reflects VET Energy’s commitment to delivering high-quality solutions.
Performance Metrics
The VET Energy Wafer Susceptor excels in performance metrics that are essential for high-temperature applications. Its thermal resistance allows it to operate effectively in extreme environments without compromising functionality. This capability ensures reliable performance in processes that demand consistent heat management.
Durability is another key performance metric. The susceptor’s robust construction and wear-resistant coating contribute to its long lifespan. It withstands the rigors of continuous use, reducing the need for frequent replacements. This durability translates to lower operational costs and improved efficiency for users.
Advantages of TaC Coating
Thermal Resistance
The TaC coating on the VET Energy Wafer demonstrates exceptional thermal resistance, making it suitable for high-temperature applications. Its thermal expansion coefficient of 6.3 x 10^-6/K ensures stability under extreme heat conditions. This property minimizes the risk of structural deformation, maintaining the integrity of the susceptor during prolonged use.
Efficient heat transfer is another critical advantage of the TaC coating. Its enhanced thermal conductivity allows for uniform heat distribution across the wafer surface. This capability ensures consistent processing results, which is essential for industries that demand precision and reliability.
Durability and Longevity
The high hardness of the TaC coating, ranging from 2500 to 3000 HV, provides superior wear resistance. This feature protects the susceptor from mechanical damage, even in rigorous operational environments. The coating’s durability ensures that the VET Energy Wafer maintains its performance over extended periods.
Reduced maintenance and replacement costs are direct benefits of the coating’s longevity. The robust construction minimizes wear and tear, lowering the frequency of repairs or replacements. This durability translates into cost savings and improved operational efficiency for users.
Chemical Stability
The TaC coating offers remarkable resistance to corrosion and chemical reactions. It withstands exposure to acids, bases, and other corrosive substances, ensuring the susceptor’s reliability in diverse processing environments. This chemical stability is vital for maintaining operational integrity in industries with challenging conditions.
Compatibility with various processing environments further enhances the coating’s appeal. The TaC-coated VET Energy Wafer adapts seamlessly to different operational settings, providing consistent performance. This versatility makes it a valuable asset for industries requiring high-performance materials.
Applications of the VET Energy Wafer Susceptor with TaC Coating
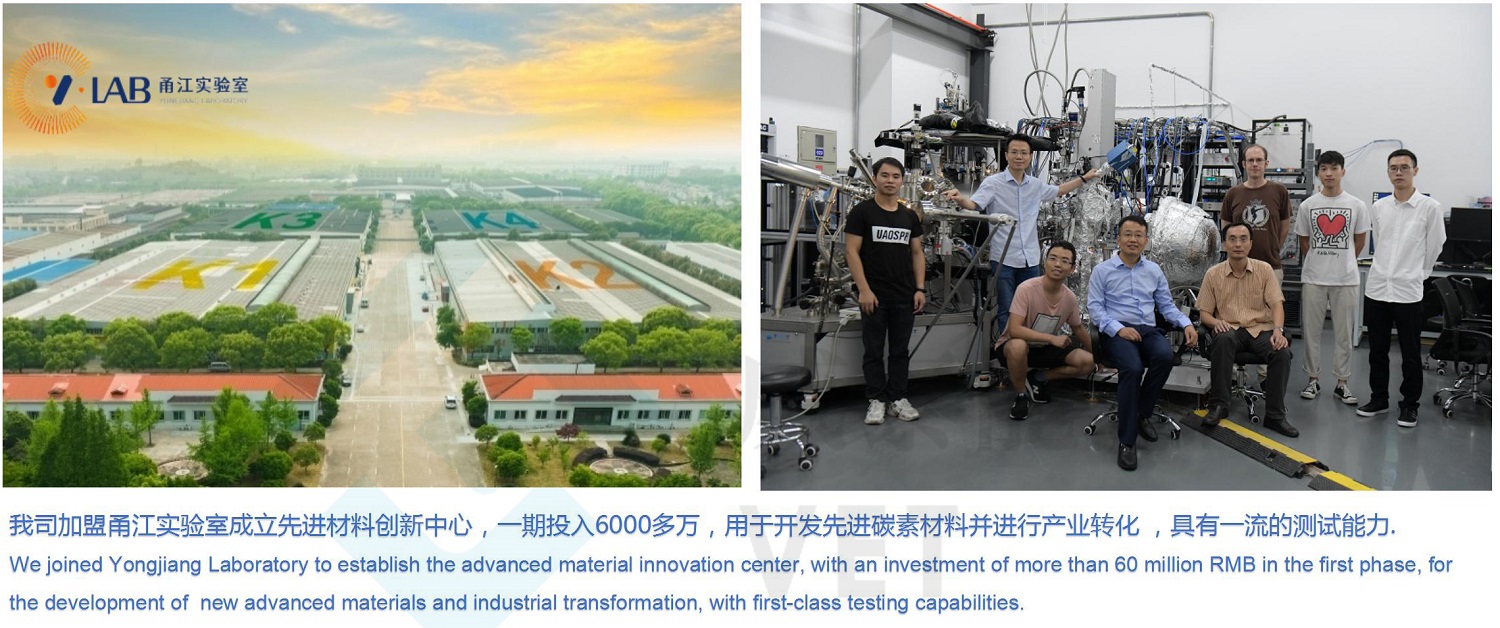
Semiconductor Manufacturing
The VET Energy Wafer plays a pivotal role in semiconductor manufacturing. It supports wafer processing techniques such as deposition and etching, which are essential for creating intricate microstructures. These processes demand precision and stability, both of which the susceptor delivers through its advanced design and material properties.
The susceptor ensures uniformity during wafer processing. Its thermal conductivity and chemical stability contribute to consistent results, reducing defects in semiconductor production. Manufacturers benefit from improved reliability, which enhances the quality of the final products. This makes the susceptor an indispensable tool for achieving high standards in semiconductor fabrication.
Energy Systems
High-temperature energy conversion systems rely on the VET Energy Wafer for optimal performance. The susceptor operates effectively in photovoltaic technologies, where it supports processes that convert sunlight into energy. Its ability to withstand extreme temperatures ensures efficiency and reliability in these applications.
New energy technologies also benefit from the susceptor’s advanced features. Its durability and thermal resistance make it suitable for demanding environments. By maintaining operational integrity, the susceptor contributes to the overall efficiency of energy systems. This highlights its importance in advancing sustainable energy solutions.
Advanced Manufacturing and Research
The VET Energy Wafer finds applications in cutting-edge manufacturing processes. Industries requiring high-performance materials, such as aerospace and automotive, utilize the susceptor for its exceptional properties. Its wear resistance and chemical stability ensure reliable performance in these advanced settings.
Research fields like metallurgy and material science also leverage the susceptor’s capabilities. Scientists use it in experiments that demand precision and resilience. Emerging applications continue to expand its utility, showcasing its versatility in both industrial and academic environments.
The VET Energy Wafer Susceptor with TaC Coating combines advanced materials and engineering to deliver exceptional performance. Its technical specifications, including high thermal resistance, durability, and chemical stability, make it a reliable choice for demanding applications. The advantages of the TaC coating enhance operational efficiency and reduce maintenance needs. Its applications span semiconductor manufacturing, energy systems, and advanced research, showcasing its versatility. This technology plays a crucial role in advancing high-temperature processes and improving manufacturing precision. VET Energy remains committed to innovation, paving the way for future advancements in material science and industrial solutions.
FAQ
What is the primary purpose of the VET Energy Wafer Susceptor with TaC Coating?
The VET Energy Wafer Susceptor with TaC Coating is designed for high-performance wafer processing applications. It ensures precision, durability, and reliability in industries such as semiconductors, energy systems, and advanced manufacturing.
Why is tantalum carbide (TaC) coating used on the susceptor?
The TaC coating enhances the susceptor’s properties by providing exceptional hardness, wear resistance, and chemical stability. These features ensure the susceptor performs effectively in demanding environments and extends its operational lifespan.
What materials are used in the construction of the susceptor?
The susceptor typically uses advanced base materials like graphite or silicon carbide. These materials offer high thermal resistance and structural integrity, making them ideal for high-temperature applications.
How does the susceptor ensure thermal uniformity?
The susceptor’s design prioritizes even heat distribution across the wafer surface. This ensures consistent processing results, which is critical for precision-driven industries like semiconductor manufacturing.
What industries benefit most from this technology?
Industries such as semiconductor manufacturing, photovoltaic energy systems, and advanced research fields benefit significantly. The susceptor’s durability, thermal resistance, and chemical stability make it a versatile solution for various high-performance applications.
Can the susceptor withstand exposure to corrosive substances?
Yes, the TaC coating provides excellent chemical stability. It resists corrosion and reactions with acids, bases, and other harsh substances, ensuring reliable performance in diverse operational settings.
What are the standard dimensions of the susceptor?
The susceptor is designed to meet the specific requirements of G5 and G10 wafer processing. It adheres to standard dimensions and tolerances to ensure compatibility with industry equipment.
How does the susceptor contribute to cost savings?
The susceptor’s durability and wear resistance reduce the need for frequent replacements or maintenance. This leads to lower operational costs and improved efficiency over time.
Is the susceptor suitable for high-temperature applications?
Yes, the susceptor operates effectively in extreme heat conditions. Its thermal resistance and stability make it an ideal choice for processes requiring consistent heat management.
What sets VET Energy apart as a manufacturer?
VET Energy combines advanced material expertise with innovative engineering. Their commitment to quality and tailored solutions ensures that clients receive high-performance products designed to meet specific industry needs.