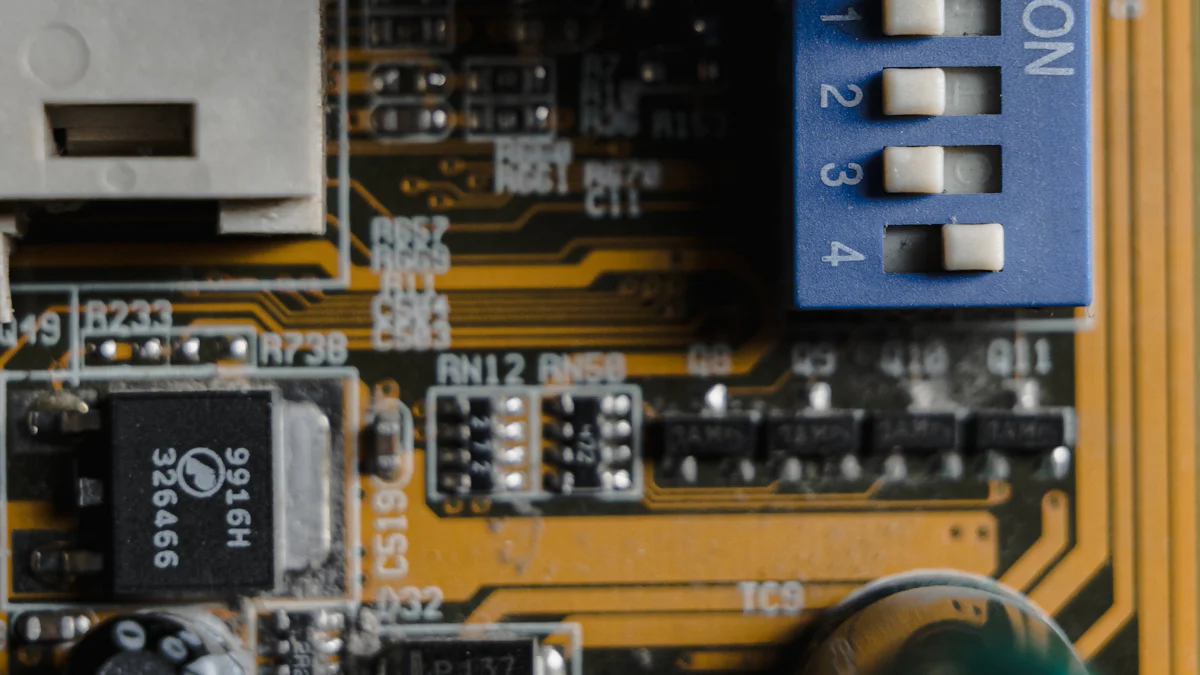
A wafer carrier serves as a vital tool in semiconductor manufacturing. It acts as a specialized container designed to securely hold and transport delicate semiconductor wafers. By cradling wafers at their edges, it prevents physical damage during handling. Its design also ensures wafers remain free from contaminants, which is critical in cleanroom environments. Materials like PTFE Teflon or fused quartz are often used to construct these carriers, offering resistance to high temperatures and chemicals. This combination of protection and cleanliness makes wafer carriers indispensable for producing high-quality semiconductor devices.
Key Takeaways
- Wafer carriers are essential for protecting semiconductor wafers from physical damage and contamination during manufacturing.
- Constructed from durable materials like PTFE Teflon and fused quartz, wafer carriers ensure cleanliness and withstand harsh conditions.
- Different types of wafer carriers, such as FOUPs and specialized carriers, cater to specific manufacturing needs and enhance automation.
- The design of wafer carriers minimizes direct contact with wafers, reducing the risk of scratches and ensuring high-quality production.
- By integrating with robotic systems, wafer carriers streamline handling processes, improving efficiency and reducing human error.
- Investing in high-quality wafer carriers can lead to significant cost savings by preventing defects and ensuring optimal wafer condition.
- As semiconductor technology advances, wafer carriers will continue to play a crucial role in supporting innovative manufacturing processes.
Understanding Wafer Carriers

Definition and Purpose
A wafer carrier is a critical component in semiconductor manufacturing. It serves as a secure container for holding and transporting semiconductor wafers throughout various stages of production. These carriers are designed to protect wafers from physical damage and contamination, ensuring their integrity remains intact. By holding wafers at their edges, they prevent scratches or cracks on the wafer surface, which could compromise the quality of the final product.
The purpose of a wafer carrier extends beyond simple storage. It plays a vital role in maintaining the cleanliness required in cleanroom environments. Semiconductor wafers are highly sensitive to particles, moisture, and other impurities. Wafer carriers act as a shield, keeping these contaminants away. Additionally, they support the automation processes in modern semiconductor manufacturing by being compatible with robotic handling systems. This compatibility ensures smooth transitions between different production stages, reducing the risk of human error.
Key Features of Wafer Carriers
Wafer carriers come with several features that make them indispensable in the semiconductor industry. Here are some of the key characteristics:
-
Material Composition: Most wafer carriers are made from durable materials like PTFE Teflon, fused quartz, or polypropylene. These materials resist high temperatures and chemical exposure, making them ideal for the harsh conditions of semiconductor fabrication.
-
Secure Holding Mechanism: Many carriers feature precision-molded slots or grooves that hold wafers securely in place. For example, some models include conical bases that support wafers at their edges, minimizing contact with the wafer surface.
-
Capacity and Size Options: Wafer carriers are available in various sizes to accommodate different wafer diameters, such as 125 mm or 300 mm. Some carriers can hold a single wafer, while others are designed for multiple wafers, with capacities ranging up to 25 wafers per carrier.
-
Customizability: Manufacturers offer custom wafer carriers tailored to specific needs. These carriers can be optimized for unique processes, with features like adjustable silicone supports or specialized materials like PVDF and natural polypro.
-
Environmental Protection: Advanced wafer carriers often include seals or locking mechanisms to create a controlled environment. These features protect wafers from dust, moisture, and other impurities during storage and transport.
-
Transparency for Monitoring: Many carriers are transparent, allowing operators to visually inspect the wafers without opening the container. This feature ensures quick and efficient monitoring during production.
Wafer carriers are more than just containers; they are precision-engineered tools that ensure wafers remain safe and clean. Their thoughtful design and robust features make them an essential part of the semiconductor manufacturing process.
Types of Wafer Carriers
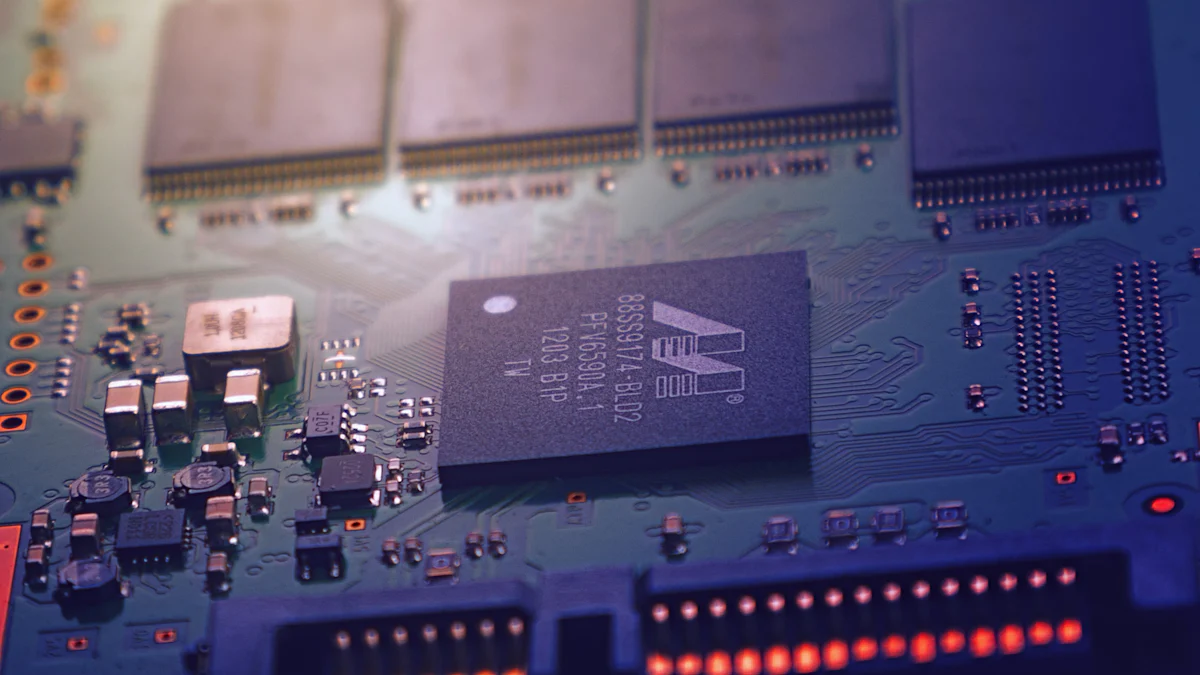
Wafer carriers come in various designs, each tailored to specific needs in semiconductor manufacturing. These carriers ensure wafers remain safe, clean, and ready for processing. Let’s explore the most common types.
Open Cassette Wafer Carriers
Open cassette wafer carriers are among the simplest designs used in semiconductor manufacturing. These carriers hold wafers securely at their edges, allowing easy access during manual or automated handling. Their open structure makes them lightweight and cost-effective. However, this design offers limited protection against contamination. Dust and particles can easily settle on the wafers, making these carriers less suitable for environments requiring strict cleanliness.
Despite their limitations, open cassettes remain popular for certain applications. They work well in processes where wafers need frequent access or when contamination risks are minimal. Their compatibility with various wafer sizes also adds to their versatility.
FOUP (Front-Opening Unified Pod) Wafer Carriers
FOUPs, or Front-Opening Unified Pods, represent a more advanced type of wafer carrier. These carriers are specifically designed to meet the stringent requirements of modern semiconductor manufacturing. FOUPs provide a sealed environment that protects wafers from contamination, including particles, moisture, and volatile organic compounds (VOCs). This makes them ideal for use in cleanroom environments.
One standout feature of FOUPs is their integration with automated systems. They allow seamless loading and unloading of wafers, reducing the need for manual handling. FOUPs are particularly suited for 300 mm wafers, which are common in advanced semiconductor processes. Their robust design ensures wafers remain secure during transport and storage, even in high-tech manufacturing facilities.
"FOUPs not only protect wafers but also enhance production efficiency by supporting automation," as noted by industry experts.
Specialized Wafer Carriers
Specialized wafer carriers cater to unique manufacturing needs. These carriers often feature custom designs or materials to handle specific challenges. For example, some specialized carriers are made from materials like PVDF or natural polypropylene, which offer enhanced chemical resistance. Others include adjustable supports to accommodate wafers of varying sizes.
Certain specialized carriers are designed for extreme conditions, such as high-temperature processes or environments with aggressive chemicals. These carriers ensure wafers remain intact and uncontaminated, even under demanding circumstances. Additionally, some models include advanced sealing mechanisms to create a controlled microenvironment, further protecting wafers during transport or storage.
Specialized wafer carriers play a crucial role in niche applications, offering solutions where standard carriers may fall short. Their adaptability makes them an essential tool in the ever-evolving semiconductor industry.
The Role of Wafer Carriers in Semiconductor Manufacturing
Contamination Prevention
Contamination poses a significant challenge in semiconductor manufacturing. Even the tiniest particle can ruin a wafer, leading to costly defects. Wafer carriers act as a protective barrier, shielding wafers from dust, moisture, and other impurities. Their design minimizes direct contact with the wafer surface, reducing the risk of scratches or contamination. Many carriers include advanced sealing mechanisms to create a controlled environment, ensuring wafers remain pristine during storage and transport.
Cleanroom environments demand strict cleanliness standards. Wafer carriers play a vital role in maintaining these conditions. For instance, materials like PTFE Teflon and fused quartz resist chemical reactions and high temperatures, making them ideal for cleanroom use. According to industry research, wafer carriers are essential for protecting delicate wafers from contamination throughout various manufacturing stages. By preventing impurities, they help ensure the production of high-quality semiconductor devices.
Compatibility with Automated Systems
Modern semiconductor manufacturing relies heavily on automation. Wafer carriers are designed to integrate seamlessly with robotic systems, enabling smooth transitions between production stages. This compatibility reduces the need for manual handling, which lowers the risk of human error and wafer damage. For example, FOUPs (Front-Opening Unified Pods) are specifically engineered to work with automated equipment, allowing precise loading and unloading of wafers.
Automation also improves efficiency. Robotic systems can handle wafer carriers with speed and accuracy, ensuring consistent results. Wafer carriers with standardized designs, such as those for 300 mm wafers, enhance this process by aligning perfectly with automated tools. As noted in industry studies, these carriers support the safe handling and efficient processing of thin wafers, which are increasingly common in advanced semiconductor applications.
Improving Production Efficiency
Efficiency is critical in semiconductor manufacturing, where time and precision directly impact costs. Wafer carriers contribute to this efficiency by streamlining wafer handling and transport. Their secure holding mechanisms prevent damage, reducing the need for rework or replacements. Additionally, their compatibility with automated systems speeds up production, allowing manufacturers to meet tight deadlines without compromising quality.
The durability of wafer carriers also plays a role in boosting efficiency. Materials like graphite offer superior thermal stability and mechanical strength, ensuring carriers withstand the rigors of fabrication processes. This reliability minimizes downtime caused by equipment failures or damaged wafers. By maintaining wafer integrity and supporting automation, wafer carriers help manufacturers optimize their operations and stay competitive in a fast-paced industry.
"Wafer carriers not only protect wafers but also enhance production efficiency by supporting automation," as highlighted by experts in semiconductor manufacturing.
Why Wafer Carriers Are Essential to the Semiconductor Industry
Supporting Advanced Manufacturing Processes
The semiconductor industry constantly evolves, with advanced manufacturing processes driving innovation. Wafer carriers play a pivotal role in supporting these advancements. As technologies like IoT, artificial intelligence, and 5G continue to grow, the demand for high-performance semiconductor devices increases. Wafer carriers ensure that wafers remain pristine throughout production, enabling manufacturers to meet the rigorous standards of modern fabrication.
The shift toward 300 mm wafers highlights the importance of wafer carriers in advanced processes. These larger wafers allow manufacturers to produce more chips per batch, improving efficiency and reducing costs. However, handling such delicate and sizable wafers requires precision. Wafer carriers designed for 300 mm wafers provide the necessary support and protection, minimizing contamination risks and ensuring smooth transitions between automated systems.
Additionally, the trend of miniaturization in electronics has pushed manufacturers to adopt cutting-edge materials and designs for wafer carriers. For instance, advanced graphite wafer carriers offer enhanced thermal stability and chemical resistance, making them ideal for high-temperature processes. These innovations ensure that wafer carriers remain reliable even in the most demanding environments, supporting the industry’s push for smaller, faster, and more efficient devices.
"The evolution of wafer carriers since the 1990s reflects the industry’s commitment to meeting technological demands," as noted by industry experts.
Ensuring Cost-Effectiveness and Quality
In semiconductor manufacturing, balancing cost and quality is crucial. Wafer carriers contribute significantly to achieving this balance. By protecting wafers from damage and contamination, they reduce the likelihood of defects, which can be costly to rectify. A single contaminated wafer can lead to the loss of multiple chips, impacting both production timelines and profitability. Wafer carriers act as a safeguard, ensuring that each wafer reaches the next stage of production in optimal condition.
Modern automated wafer handling processes further enhance cost-effectiveness. Wafer carriers designed with tighter tolerances integrate seamlessly with robotic systems, reducing manual intervention. This not only speeds up production but also minimizes human error, leading to consistent quality across batches. For example, FOUPs (Front-Opening Unified Pods) are specifically engineered to support automation, making them a preferred choice for manufacturers aiming to optimize efficiency.
Regulatory and environmental standards also influence the design and use of wafer carriers. Compliance with these standards drives innovation, resulting in carriers that are both effective and sustainable. Materials like PTFE Teflon and fused quartz meet health and safety regulations while maintaining durability. By investing in high-quality wafer carriers, manufacturers can ensure long-term cost savings and maintain their competitive edge in a rapidly growing industry.
In summary, wafer carriers are indispensable in the semiconductor industry. They support advanced manufacturing processes, enhance automation, and ensure cost-effectiveness without compromising quality. As the industry continues to innovate, wafer carriers will remain a cornerstone of efficient and reliable semiconductor production.
Wafer carriers play a vital role in semiconductor manufacturing by safeguarding wafers from contamination and physical damage. Their innovative designs ensure wafers remain pristine, supporting the strict cleanliness standards required in cleanroom environments. By integrating seamlessly with automated systems, wafer carriers enhance production efficiency and reduce errors. These carriers not only protect delicate wafers but also contribute significantly to advancing semiconductor technology. As the industry evolves, wafer carriers will remain indispensable for maintaining wafer quality and driving innovation in manufacturing processes.