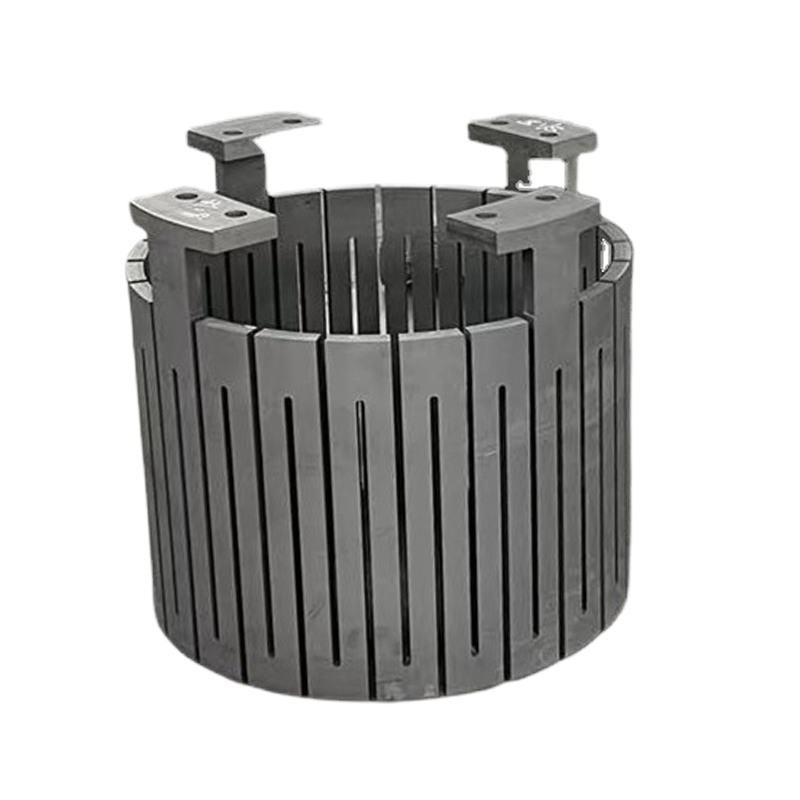
Nichrome, a nickel-chromium alloy, stands out as the preferred material for heating elements due to its exceptional properties. Its high electrical resistance allows it to convert electrical energy into heat efficiently, making it ideal for various applications. Nichrome resists oxidation and maintains stability even at elevated temperatures, ensuring durability and consistent performance. Industries and households rely on this alloy for devices like furnaces, toasters, and dryers. Compared to alternatives like the silicon carbide heating element, nichrome offers superior versatility and cost-effectiveness, making it indispensable in modern heating technologies.
Key Takeaways
- Nichrome is the preferred heating element due to its high electrical resistance, which allows for efficient heat generation.
- Its durability and resistance to oxidation ensure long-lasting performance, making it ideal for both household and industrial applications.
- Nichrome’s ability to maintain stability at high temperatures prevents degradation, making it reliable for devices like toasters, hair dryers, and industrial furnaces.
- Compared to alternatives like Kanthal and stainless steel, nichrome heats up faster and is more versatile, adapting to various designs and functionalities.
- To extend the life of nichrome heating elements, avoid overloading, maintain a stable operating environment, and perform regular cleaning and inspections.
- Understanding the properties of nichrome empowers consumers to make informed choices for their heating needs, ensuring efficiency and reliability.
What is a Heating Element?
Definition of a Heating Element
A heating element is a component designed to convert electrical energy into heat energy. This process occurs through Joule heating, where an electric current passes through a material with high resistance, generating heat. Heating elements are integral to various devices, including heaters, ovens, and industrial furnaces. Their design ensures efficient heat production while maintaining durability under high temperatures.
Role of Heating Elements in Heaters
Heating elements play a crucial role in heaters by serving as the primary source of heat. When electricity flows through the element, it heats up and transfers thermal energy to the surrounding environment. This mechanism allows heaters to warm spaces, objects, or even liquids. For example, in space heaters, the heating element generates heat that radiates outward, providing warmth to a room. In water heaters, the element heats water directly, ensuring a steady supply of hot water for household or industrial use.
How Heating Elements Work to Generate Heat
Heating elements generate heat through a straightforward yet effective process. When an electric current passes through the element, the material’s resistance opposes the flow of electrons. This resistance converts electrical energy into thermal energy, producing heat. The amount of heat depends on the material’s resistivity, the current’s strength, and the element’s dimensions. Materials like nichrome are commonly used because they exhibit high resistance and can withstand extreme temperatures without degrading.
For instance, in an electric heater, the nichrome wire heats up as electricity flows through it. The heat then transfers to the air or surrounding medium, warming the space efficiently. This process highlights the importance of selecting materials with suitable thermal and electrical properties for heating elements.
Why Nichrome is the Most Commonly Used Heating Element
Properties of Nichrome
Nichrome, a nickel-chromium alloy, possesses unique properties that make it an ideal choice for heating elements. Its high electrical resistance allows it to efficiently convert electrical energy into heat, a critical requirement for any heating element. Nichrome also exhibits excellent oxidation resistance. When exposed to high temperatures, it forms a protective layer of chromium oxide, which prevents further degradation and ensures long-term durability.
Another notable property of nichrome is its ability to maintain mechanical stability under extreme heat. Unlike some materials that become brittle or deform, nichrome retains its structural integrity, making it reliable for prolonged use. Additionally, its non-magnetic nature and good ductility allow manufacturers to shape it into wires, ribbons, or coils without compromising its performance. These characteristics collectively position nichrome as a versatile and dependable material for heating applications.
How Nichrome Generates Heat Efficiently
Nichrome generates heat through the process of electrical resistance. When an electric current flows through the nichrome wire, its high resistance opposes the movement of electrons. This opposition converts electrical energy into thermal energy, producing heat. The efficiency of this process stems from nichrome’s high resistivity, which ensures significant heat generation even with a relatively small amount of current.
For example, in devices like toasters or hair dryers, nichrome wires heat up rapidly when electricity passes through them. The heat then transfers to the surrounding air or surface, enabling the device to perform its function effectively. Nichrome’s ability to heat quickly and evenly, combined with its resistance to oxidation, ensures consistent performance over time. This efficiency makes it a preferred material for both household and industrial heating applications.
Comparison with Other Heating Element Materials
When compared to other materials, nichrome consistently outperforms in key areas. For instance:
-
Nichrome vs. Kanthal: Nichrome heats faster due to its lower resistance and has better ductility, making it easier to shape into coils. Kanthal, on the other hand, offers higher resistance to rust and oxidation, which can be advantageous in specific environments requiring extreme durability.
-
Nichrome vs. Stainless Steel: Nichrome achieves higher temperatures more quickly and maintains stability at elevated heat levels. Stainless steel, while durable and corrosion-resistant, lacks the rapid heating capabilities and high resistivity of nichrome.
-
Nichrome vs. FeCrAl (Iron-Chromium-Aluminum): Nichrome demonstrates superior mechanical stability and can endure more power cycles before burnout. FeCrAl, however, has a higher melting point, which may be beneficial in certain high-temperature applications.
-
Nichrome vs. Ceramic Heating Elements: Nichrome often serves as the internal support structure in ceramic heating elements due to its ability to withstand high temperatures. While ceramics excel in insulation and heat retention, nichrome provides the necessary conductivity and heat generation.
These comparisons highlight nichrome’s balance of efficiency, durability, and versatility, making it the most commonly used material for heating elements across a wide range of devices.
Advantages of Nichrome as a Heating Element
High Electrical Resistance
Nichrome exhibits exceptionally high electrical resistance, which makes it an ideal material for heating elements. This property allows it to efficiently convert electrical energy into heat through the process of Joule heating. The high resistivity ensures that even a small amount of current passing through the nichrome wire generates significant heat. This efficiency is crucial in devices like toasters, hair dryers, and industrial furnaces, where rapid and consistent heating is required.
The resistance of nichrome also contributes to its ability to maintain stable performance over time. Unlike some materials that degrade or lose efficiency with repeated use, nichrome retains its resistive properties, ensuring reliable heat generation. This characteristic makes it a preferred choice for both household and industrial applications.
Durability and Longevity
Nichrome stands out for its remarkable durability and longevity. Its ability to withstand high temperatures without deforming or breaking ensures that it remains functional even under extreme conditions. For instance, in industrial furnaces, nichrome heating elements endure prolonged exposure to intense heat while maintaining their structural integrity.
The alloy’s mechanical stability further enhances its lifespan. Nichrome does not become brittle or lose its ductility after extended use, which allows manufacturers to shape it into various forms, such as wires, ribbons, or coils, without compromising its performance. This durability reduces the need for frequent replacements, making nichrome a cost-effective solution for long-term heating applications.
Resistance to Oxidation and Corrosion
One of nichrome’s most valuable properties is its resistance to oxidation and corrosion. When exposed to high temperatures, nichrome forms a thin, protective layer of chromium oxide on its surface. This layer acts as a barrier, preventing further oxidation and protecting the underlying material from degradation. This self-healing property ensures that nichrome maintains its performance and appearance even after repeated heating cycles.
This resistance to oxidation makes nichrome particularly suitable for environments where other materials might fail. For example, in outdoor or high-humidity settings, nichrome heating elements continue to perform reliably without succumbing to rust or corrosion. This resilience not only extends the lifespan of the heating element but also ensures consistent performance in demanding conditions.
Cost-Effectiveness and Versatility
Nichrome offers a unique combination of cost-effectiveness and versatility, making it a preferred choice for heating applications. Its production involves relatively low manufacturing costs, especially when compared to other high-performance materials like molybdenum disilicide or carbon fiber. This affordability allows manufacturers to produce efficient heating devices without significantly increasing the overall cost of the product. For example, household appliances such as toasters and hair dryers utilize nichrome to deliver reliable performance at a reasonable price point.
The versatility of nichrome further enhances its appeal. Its ability to withstand high temperatures, resist oxidation, and maintain mechanical stability makes it suitable for a wide range of applications. Nichrome can be shaped into wires, ribbons, or coils, allowing it to adapt to various designs and functionalities. In industrial settings, it powers furnaces and kilns, while in households, it serves as the core component in electric heaters and ovens. This adaptability ensures that nichrome remains relevant across diverse industries and use cases.
Additionally, nichrome’s durability reduces the need for frequent replacements, which contributes to long-term cost savings. Its resistance to wear and tear ensures consistent performance over extended periods, minimizing maintenance expenses. This combination of affordability, reliability, and adaptability underscores why nichrome continues to dominate as a material for heating elements in both domestic and industrial applications.
Disadvantages of Nichrome as a Heating Element
Higher Cost Compared to Some Alternatives
Nichrome, while highly efficient and durable, tends to be more expensive than certain alternative materials. For instance, stainless steel and FeCrAl (iron-chromium-aluminum alloy) are often more cost-effective options for applications where extreme precision or rapid heating is not required. Stainless steel, known for its affordability and corrosion resistance, is frequently used in environments where cost is a primary concern. FeCrAl, on the other hand, offers a higher melting point and can handle extreme temperatures at a lower price point compared to nichrome.
The higher cost of nichrome stems from its composition, which includes nickel—a relatively expensive metal. This makes it less suitable for budget-sensitive projects or mass production of low-cost devices. For example, in industries producing inexpensive household appliances, manufacturers may opt for stainless steel or FeCrAl to reduce production costs. While nichrome provides superior performance in terms of heat generation and stability, its price can limit its use in applications where cost-efficiency outweighs performance needs.
Limited Use in Extremely High-Temperature Applications
Although nichrome performs exceptionally well in most heating applications, it has limitations when exposed to extremely high temperatures. Materials like FeCrAl and molybdenum disilicide surpass nichrome in such conditions due to their higher melting points and better thermal stability. FeCrAl, for instance, can withstand temperatures exceeding 1400°C, making it a preferred choice for industrial furnaces and kilns operating at extreme heat levels. Nichrome, in comparison, begins to lose its mechanical stability and efficiency at temperatures above 1200°C.
In applications requiring prolonged exposure to ultra-high temperatures, nichrome may degrade faster or experience burnout after fewer power cycles. For example, in high-temperature industrial processes like glass manufacturing or metal smelting, materials with greater heat tolerance, such as molybdenum disilicide, are often chosen over nichrome. While nichrome excels in moderate to high-temperature environments, its limitations in extreme heat scenarios make it less versatile for certain specialized applications.
Applications of Nichrome Heating Elements
Household Applications
Space Heaters
Nichrome plays a vital role in space heaters, where its ability to withstand high temperatures ensures consistent performance. The heating element in these devices generates heat efficiently by converting electrical energy into thermal energy. Nichrome’s high resistance allows it to heat rapidly, making it ideal for warming rooms during cold weather. Its durability ensures that space heaters remain reliable over extended periods, even with frequent use.
Hair Dryers
Hair dryers rely on nichrome wires to produce the heat necessary for drying hair. When electricity flows through the nichrome heating element, it heats up quickly and transfers warmth to the air blown by the dryer. Nichrome’s stability at high temperatures prevents it from degrading, ensuring the device’s longevity. Its non-magnetic nature also makes it safe for use in personal care appliances.
Toasters and Ovens
Toasters and ovens use nichrome wires to generate the heat required for cooking and baking. Nichrome’s ability to reach high temperatures without external heat transfer makes it an excellent choice for these appliances. In toasters, the nichrome wire heats up evenly, ensuring bread is toasted uniformly. In ovens, its high-temperature strength allows it to maintain consistent heat levels, essential for precise cooking.
Industrial Applications
Kilns and Furnaces
Nichrome is widely used in kilns and furnaces due to its high-temperature strength and resistance to oxidation. These industrial devices require heating elements that can endure prolonged exposure to extreme heat. Nichrome’s protective chromium oxide layer prevents degradation, ensuring reliable performance. Its workability also allows manufacturers to shape it into coils or ribbons, adapting to various furnace designs.
Heat Guns
Heat guns, used in applications like paint stripping and plastic welding, depend on nichrome for their heating elements. Nichrome’s rapid heating capabilities enable heat guns to reach the desired temperature quickly. Its durability ensures consistent performance, even in demanding tasks. This makes nichrome a preferred material for tools requiring precise and efficient heat generation.
Laboratory Equipment
Laboratory equipment, such as incubators and sterilizers, often incorporates nichrome heating elements. Nichrome’s stability at high temperatures ensures accurate and consistent heat delivery, critical for scientific experiments and processes. Its resistance to corrosion makes it suitable for environments where exposure to chemicals or moisture is common.
Other Nichrome Applications
Electric Blankets
Electric blankets use nichrome wires to provide controlled warmth. The heating element embedded within the blanket heats up evenly, ensuring comfort and safety. Nichrome’s flexibility allows it to be shaped into thin wires, making it ideal for use in lightweight and portable electric blankets.
Vape Coils
Vape coils, used in electronic cigarettes, often feature nichrome as the heating element. Nichrome’s ability to heat quickly and maintain stability at high temperatures ensures a smooth vaping experience. Its non-magnetic nature and resistance to oxidation make it a reliable choice for this application, where consistent performance is essential.
Alternatives to Nichrome Heating Elements
Kanthal: Properties and Applications
Kanthal, an iron-chromium-aluminum alloy, serves as a popular alternative to nichrome in specific heating applications. Its high resistance to oxidation and corrosion makes it suitable for environments requiring prolonged exposure to extreme temperatures. Kanthal can withstand temperatures exceeding 1400°C, surpassing nichrome’s limit of approximately 1200°C. This property makes it ideal for industrial furnaces, kilns, and other high-temperature equipment.
Kanthal also offers excellent durability and a longer lifespan in demanding conditions. Its ability to maintain structural integrity under thermal stress ensures consistent performance over time. Manufacturers often choose Kanthal for applications where longevity and resistance to harsh environments are critical. For instance, it is commonly used in ceramic kilns and glass manufacturing processes.
However, Kanthal heats up more slowly than nichrome due to its higher resistivity. This slower heating rate may not be suitable for devices requiring rapid heat generation, such as hair dryers or toasters. Despite this limitation, Kanthal remains a cost-effective and reliable option for high-temperature applications.
Ceramic Heating Elements: Pros and Cons
Ceramic heating elements combine ceramic materials with internal conductive components, such as nichrome or Kanthal wires, to generate heat. These elements excel in heat retention and insulation, making them highly efficient for applications requiring steady and uniform heat distribution. Ceramic’s natural insulating properties reduce energy loss, enhancing the overall efficiency of the heating system.
One significant advantage of ceramic heating elements is their ability to operate at lower surface temperatures while still delivering effective heat output. This feature makes them safer for use in household appliances like space heaters and hair straighteners. Additionally, ceramic elements resist oxidation and corrosion, ensuring durability in various environments.
However, ceramic heating elements have limitations. They are more fragile than metallic alternatives, making them prone to cracking or breaking under mechanical stress. Their production costs can also be higher due to the complexity of combining ceramic materials with conductive components. Despite these drawbacks, ceramic heating elements remain a preferred choice for applications prioritizing energy efficiency and safety.
Carbon Fiber Heating Elements: When to Use Them
Carbon fiber heating elements represent a modern alternative to traditional metallic heating materials. These elements consist of carbon fibers woven into a matrix, offering unique advantages in specific applications. Carbon fiber elements heat up rapidly and evenly, providing precise temperature control. Their lightweight nature and flexibility make them suitable for innovative designs, such as heated clothing and electric blankets.
Carbon fiber’s resistance to thermal shock ensures durability in applications requiring frequent temperature changes. Additionally, these elements operate efficiently at lower power levels, reducing energy consumption. This efficiency makes them an eco-friendly option for industries aiming to minimize their environmental impact.
Despite their benefits, carbon fiber heating elements have limitations. They are more expensive to produce than traditional materials like nichrome or Kanthal. Their lower maximum operating temperature also restricts their use in high-temperature industrial processes. Nevertheless, carbon fiber elements excel in applications where lightweight, rapid heating, and energy efficiency are essential.
How to Maintain and Extend the Life of Nichrome Heating Elements
Proper Usage Guidelines
To ensure the longevity of nichrome heating elements, users must follow specific usage practices. First, avoid exposing the element to excessive voltage or current beyond its rated capacity. Overloading can cause overheating, leading to premature wear or burnout. Manufacturers often provide detailed specifications for safe operation, and adhering to these guidelines ensures optimal performance.
Second, maintain a stable operating environment. Nichrome performs best in controlled conditions where temperature fluctuations are minimal. For instance, industrial furnaces using nichrome elements should avoid sudden cooling or heating cycles, as these can stress the material. Additionally, ensure proper insulation around the element to prevent heat loss and reduce unnecessary strain on the system.
Lastly, handle nichrome elements with care during installation or replacement. Bending or twisting the material excessively can weaken its structure, reducing its efficiency. Using tools designed for precision handling minimizes the risk of damage. By following these practices, users can maximize the lifespan of nichrome heating elements.
Cleaning and Maintenance Tips
Regular cleaning and maintenance play a crucial role in extending the life of nichrome heating elements. Dust, debris, or residue buildup on the element’s surface can hinder its performance. Cleaning the element periodically with a soft brush or compressed air removes these contaminants without causing damage. Avoid using abrasive materials or harsh chemicals, as these can degrade the protective chromium oxide layer.
Inspect the connections and terminals for signs of corrosion or loose fittings. Corroded terminals can disrupt the flow of electricity, reducing the element’s efficiency. Tighten any loose connections and clean corroded areas with a non-abrasive cleaner to restore proper functionality.
For industrial applications, schedule routine inspections to monitor the element’s condition. Replace worn-out components promptly to prevent further damage to the system. For example, in kilns or furnaces, replacing a damaged nichrome coil ensures consistent heat distribution and prevents operational disruptions. Regular maintenance not only enhances performance but also reduces the need for costly replacements.
Recognizing Signs of Wear and Tear
Identifying early signs of wear and tear helps users address issues before they escalate. One common indicator is a decrease in heating efficiency. If the nichrome element takes longer to reach the desired temperature, it may signal internal degradation or increased resistance. In such cases, testing the element’s electrical resistance with a multimeter can confirm its condition.
Visible damage, such as cracks, discoloration, or deformation, also indicates wear. For instance, a nichrome wire that appears brittle or warped may have been exposed to excessive heat or mechanical stress. Replacing the damaged element prevents further complications.
Unusual noises or odors during operation can also point to problems. A buzzing sound or burning smell may result from loose connections or overheating. Addressing these issues promptly ensures the safety and reliability of the heating system. By staying vigilant and addressing signs of wear early, users can prolong the life of nichrome heating elements and maintain their efficiency.
Nichrome remains the most widely used heating element due to its exceptional properties. Its high resistance and ability to withstand extreme temperatures make it a reliable choice for both household and industrial applications. The protective chromium oxide layer it forms ensures durability and resistance to oxidation, further enhancing its performance. While alternatives like Kanthal or ceramic elements exist, nichrome’s balance of efficiency, versatility, and cost-effectiveness solidifies its position as the preferred material. Understanding its properties and applications empowers consumers to select the best heating solutions for their needs.
FAQ
What makes nichrome the preferred material for heating elements?
Nichrome stands out due to its high electrical resistance, stability at elevated temperatures, and resistance to oxidation. When heated, it forms a protective chromium oxide layer, which prevents degradation and ensures durability. These properties make nichrome ideal for applications requiring consistent and efficient heat generation.
Why does nichrome resist oxidation better than other materials?
Nichrome contains chromium, which reacts with oxygen at high temperatures to form a thin, protective layer of chromium oxide. This layer shields the underlying material from further oxidation, ensuring long-term performance even in demanding environments.
How does nichrome compare to Kanthal in heating applications?
Nichrome heats up faster due to its lower resistivity and offers better ductility, making it easier to shape into coils or wires. Kanthal, however, has a higher melting point and superior resistance to rust, making it suitable for extreme high-temperature applications like industrial furnaces.
Can nichrome be used in high-humidity environments?
Yes, nichrome performs well in high-humidity environments due to its resistance to corrosion. The chromium oxide layer protects it from moisture-induced degradation, making it reliable for outdoor or humid conditions.
What are some common household devices that use nichrome?
Nichrome is widely used in household appliances such as toasters, hair dryers, space heaters, and ovens. Its ability to heat quickly and maintain stability ensures consistent performance in these everyday devices.
Is nichrome safe for personal care appliances like hair dryers?
Yes, nichrome is safe for personal care appliances. Its non-magnetic nature and resistance to overheating make it a reliable choice for devices like hair dryers, where safety and efficiency are critical.
Why is nichrome more durable than other heating materials?
Nichrome retains its mechanical stability even after prolonged exposure to high temperatures. Unlike some materials that become brittle or deform, nichrome remains ductile and strong, ensuring a longer lifespan for heating elements.
Are there any limitations to using nichrome in heating elements?
Nichrome performs exceptionally well in most applications but has limitations in extremely high-temperature environments. Materials like FeCrAl or molybdenum disilicide may be better suited for applications exceeding 1200°C.
How does nichrome contribute to energy efficiency in heating devices?
Nichrome’s high electrical resistance ensures efficient conversion of electrical energy into heat. This minimizes energy loss and allows devices like toasters and ovens to operate effectively while consuming less power.
Can nichrome be recycled or reused?
Yes, nichrome can be recycled and reused. Its durability and resistance to wear allow it to maintain its properties even after extended use, making it a sustainable choice for heating applications.